The Periflex Era
Sir Kenneth began to
think about the possibility of producing a camera. The initial idea
was to produce a subminiature version of a 35mm camera using a 16mm
film cassette. A lot of development work was carried out, but it
became obvious that the concept was wrong. Such a camera would only
sell in comparatively small numbers and only a few dealers would
stock, or even print from, the film in the unique format. The
project was dropped, but the seed had been sown, and soon thoughts
turned towards a camera using 35mm film.
The initial concept was
to produce an economically priced, high quality 35mm camera body
with a focal plane shutter and a Leica lens mount, so that Leica
owners could purchase one for use as a second body. Another
consideration was that at the time there were a lot of second hand
Leica lenses on the market. This would make it possible for someone
to purchase the camera and a Leica lens, and end up with a high
quality camera at an economical price. In the early 1950's, import
restrictions meant that new Leica equipment was in short supply in
the shops. A lot of manufacturers were producing all kinds of
accessories for Leica cameras, as it was often very difficult to
obtain the genuine article . It was possible to purchase almost any
accessory, but this was the first time that anyone had attempted to
offer a cheaper alternative to the camera body itself.
Work quickly got
underway. Many of the parts were made from aluminium instead of the
usual brass, as this was both cheaper and easier to manufacture. The
shutter was designed to work from a thirtieth to a thousandth of a
second using a fixed tension blind with a variable slit. It was made
from rubberised fabric. A glass film pressure plate was incorporated
as it was easy to polish and avoided film scratches. Another
innovation was the sprocket-less film transport which simplified the
wind-on mechanism and avoided jamming. It had been decided to
include some kind of reflex focussing system. The difficulty was to
fit it in the small confined space above the shutter. Sir Kenneth's
solution was to use a small periscope which could be lowered behind
the lens for focussing. This would allow the user to view the
central part of the image through the lens and so focus the image.
The periscope was then retracted and the photograph taken. A
separate conventional viewfinder was provided to compose the image.
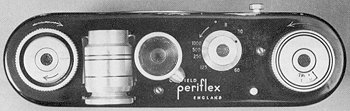 |
The camera top plate with the periscope in the
centre. The lever to lower and raise the periscope can be seen
just above the letter 'p'. |
The Corfields were
delighted with their new camera. The final design was so good that
it could easily compete with the competition as a product in its own
right. To sell it as just a camera body would severely limit its
potential in the marketplace, and so it was now time to find a
suitable lens. Initially the leading UK lens manufacturers were
contacted, but not one of them could produce a quality product at
the right price. The next step was to contact the European
manufacturers, but this became unnecessary after Sir Kenneth was
introduced to Frederick Archenhold. He was an experienced optician
who worked for the British Optical Lens Co. in Walsall. He suggested
that Corfields could make the mount and his company could make the
lenses. They had just installed new lens coating equipment and could
easily mass produce lenses to a high standard. After some thought
Sir Kenneth decided that this was a good option, and gave Frederick
the go ahead to design the optics and provide Corfields with a
specification for the mount. The lens mount and body were made of
aluminium which could be polished to provide a similar finish to the
satin chrome finish which was popular at the time. The new lens was
called the Lumar and initial prototypes performed extremely well.
New production
facilities were now required to manufacture the camera and lens.
Luckily the company was able to purchase one of its immediate
neighbours in Merridale Works to provide the much needed extra
space. New machinery was soon installed and everything was made
ready for production to begin. The first cameras had black anodised
top and bottom plates, and were finished in pigskin. The camera was
named after its unique periscope focussing mechanism and was called
the Periflex. John's workload was lightened during this
expansion as he appointed Eric Isles as technical assistant, and
Gerry Whitton as toolmaker. Prior to this John had personally
designed, drawn and dimensioned every component, and made all of the
tools for the various products.
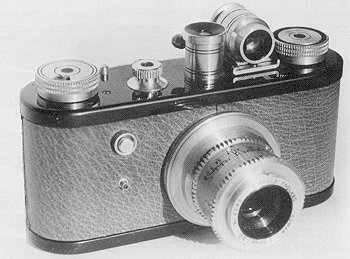 |
The original Periflex with black top and bottom
plates, and pigskin covering. Only the first 200 or so were
covered in pigskin. It was replaced by black leathercloth which
was easier to handle and more fashionable. |
The black leathercloth version. The ring around
the shutter release can be unscrewed to allow the fitting of a
Leica-type cable release. The flash socket is now recessed into
the camera body instead of standing proud. |
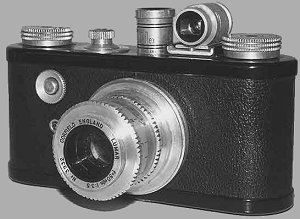 |
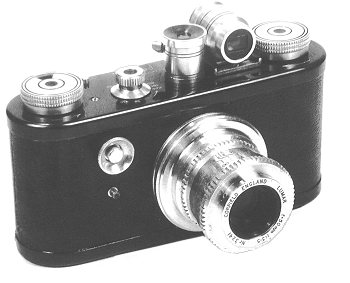 |
The first the
public heard of the camera was a pre-launch article which
appeared in the January 28th, 1953 edition of Amateur
Photographer. It consisted of advance details supplied by
Corfields and looked forward to the appearance of the camera.
The edition of May 20th was the first to announce the arrival of
the new camera. |
The write-up included
the following:
The camera has a
somewhat Leitz body style, but different in having the periscope
eyepiece and the unusual tan pigskin covering. The body is
constructed of 16 s.w.g. light alloy, has a removable back and base.
Equipped with a Leica thread lens mount, collimation had been
carried out to a high degree of accuracy to suit the widest
apertures - plus or minus 0.0004in from flange to the face of the
film plane. The camera was very comfortable in the hand, with the
shutter release being placed on the front of the body in a natural
position for the index finger of the right hand. Around the shutter
release was a removable collar which, when unscrewed, would allow
the fitting of a Leitz cable release. Flash synchronisation was
provided by the standard 3mm co-axial socket. The prices were quoted
as: body only £19.19.6d, with 50mm f3.5 Lumar lens - uncoated,
£29.18s.6d, or coated £32.19s.6d.
The write-up was a
great success. As soon as the magazine reached the shops orders
started pouring in. It had only been planned to initially produce
between 25 to 30 units each week, and so the sudden demand came as a
bit of a shock. It took sometime to build up production,
particularly as the employees had to be trained in a lot of new
skills.
|
After approximately 18 months the camera underwent some cosmetic
changes. The top and bottom plates were silver anodised
aluminium and the lens barrel was simplified. Black leather
strips were added to the adjustment rings to allow the user to
firmly grip them. These changes brightened up the appearance of
the camera, and gave it a more modern look. |
 |
|
|
|
 |
Back |
|
Return to
the contents
|
|
Continue |
|