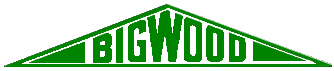
Joshua Bigwood & Son
Limited
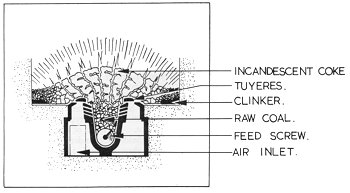
An underfeed stoker, located beneath the
fire.
|
Underfeed stokers are a British
invention which was used as early as 1838. It is an ideal way of
firing bituminous coal in a small automatically controlled unit.
The stokers have been used for such diverse purposes as the
firing of central heating boilers, steam boilers, kilns and
almost every type of industrial furnace. They provide an
efficient way of firing which uses the minimum amount of fuel
and requires less labour than traditional methods. |
Bigwoods offered a range of underfeed
stokers for various types of boilers. There was the 'Unicalor'
stoker and the 'Unidrive' stoker.
In the 1980s both models were replaced with
the Bigwood angle feed stoker. This was basically a bunker to
boiler stoker but with the pick up screw capable of being angled
through 180 degrees. In the 1960s Bigwoods were the largest
underfeed stoker manufacturers in the country, with an annual
production in excess of 600.
In addition, Bigwoods made screw elevators,
turf burners for burning peat and trickle feeders for the top
firing of brick kilns.
Unicalor coal stokers |
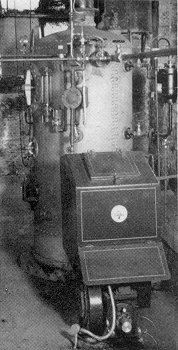 |
The ‘Unicalor’ stoker was available as
a bunker to boiler model. A screw inserted in the base of a coal
bunker brought the coal forward to a transfer box, where a second
screw collected the coal and delivered it to a retort set in the
base of the boiler, where combustion took place. The stoker was
available for coal feed rates of 220 to 750lb. per hour for firing
tubular flue boilers. A similar design, suitable for installing in
cast iron sectional and vertical steam boilers was available for the
full range of 20 to 750lb. per hour.
The ‘Unicalor’ stoker was also available as a hopper model,
which had a hopper for the coal situated over the transfer
screw.
The photograph shows a Bigwood Unicalor
screw type standard hopper stoker, applied to a small vertical
boiler. |
The Unicalor bunker-feed
stoker |
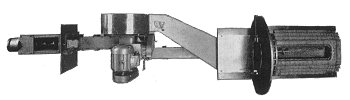 |
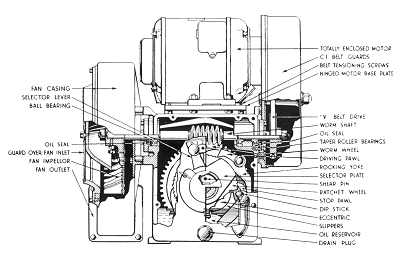
The Unicalor Drive
|
A 'V' belt drive transmits the drive from a totally
enclosed electric motor to a worm reduction gear, from which the
final reduction is obtained through an adjustable pawl and ratchet
mechanism. This gives the choice of a range of feeds by adjustment
of the selector plate or mask. All parts were interchangeable and a
slipping clutch protected the mechanism from an overload. The gears
were contained in an oil bath. |
This is part of a Bigwood's
advertisement that appeared in the programme of the St. Peter's
Church Bazaar of 1938, which was held in the Civic Hall.
It shows Unicalor stokers in the then new
Civic Hall and refers to another recent installation in St.
Peter's itself. |
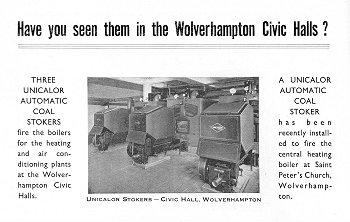 |
Unidrive coal
stokers
After World War 2 Bigwoods offered a lower priced
‘Unidrive’ range of bunker to boiler and hopper models. |
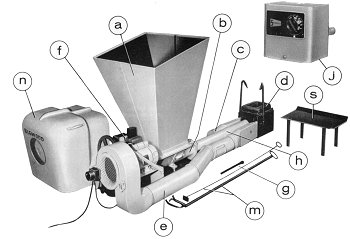
A Bigwood Underfeed Unidrive Hopper Coal
Stoker
|
Parts:
a. Hopper
b. Hopper base
c. Cleanout duct
d. Retort
e. Air duct
f. Drive unit and
control gear
g. Spanner
h. Coal tube (first
section)
j. Thermostat
m. Clinker tongs and
dust rake
n. Cover
s. Clinker tray |
The coal is fed by means of a screw into the base
of the retort, from where it rises into the combustion zone. The
retort is surmounted by a row of tuyeres through which air is
introduced. The fuel and air move together vertically upwards to
produce efficient combustion. The fuel and air flow are
automatically controlled to suit the requirements of each
individual installation. |
An underfeed stoker shown during fire
cleaning. |
|
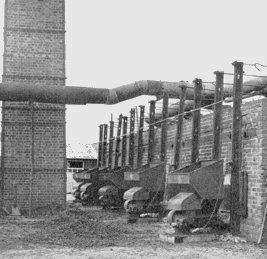
A bank of Bigwood Unidrive
Hopper Coal Stokers in operation. |
The stoker was supplied with
everything that was necessary for the installation, including
fireclay, firebricks, sealing cement and electrical cable and
fittings. The coal feed into the boiler is adjustable in
multiples of 20lbs per hour and there is a fire kindling control
that can be set to operate for several minutes every hour. The
stoker also has a thermostat and a fan to control the fire.
|
A close-up view of the air
duct and the driving wheel at the back of the stoker. |
 |
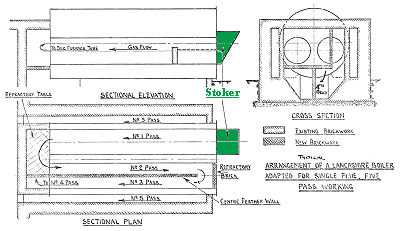 |
A Bigwood drawing of the
arrangement for converting a Lancashire boiler into single flue, five
pass working, which increased the boiler efficiency but reduced the
output to 60% of the original rating. |
We would like to thank David Evans for his help
in producing this page. |
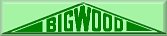 |
Return to
the
Bigwood section |
|