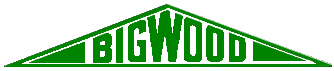
Joshua Bigwood & Son
Limited
Straightening
Machines
Bigwoods designed and
constructed plate straightening machines for many years. The
machines were grouped into two categories. The first was for dealing
with plates or sheets up to three sixteenths of an inch thick. These
machines were usually equipped with thirteen or seventeen
straightening rolls. The second category was for machines dealing
with greater thicknesses. These were usually provided with seven or
nine straightening rolls. The largest of the machines could deal
with plates up to 2.5 inches thick and any width. |
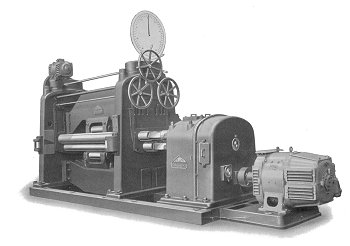
A plate straightening
machine for dealing with thick plates
|
The bearings on both the straightening and
supporting rollers had water cooled bearings and the top rolls
were operated by an electric motor which was push-button
controlled. Precision hand adjustment was provided for the inlet
and outlet rollers and the degree of adjustment was precisely
registered on a large dial. The drive from the motor was via a
totally enclosed, self-lubricating gearbox and other bearings
were equipped with a pressure grease system. The strong
construction was reinforced with steel tie rods. |
In the smaller machines the straightening rollers
have an extra large diameter to avoid any undue deflection when
straightening thin and narrower plates. The rollers were driven
from a simple, reliable gear drive and were easily and
accurately adjusted using a graduated indicator dial. The use of
a gear drive with double helical teeth ensured smooth and
vibration-less running. |
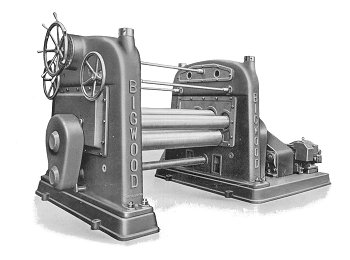
A smaller plate straightening machine
|
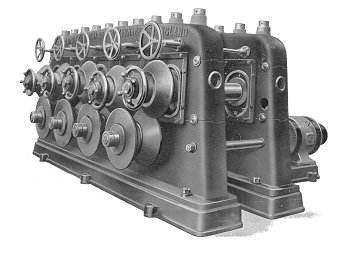
The S.M.16 shape and section straightening
machine with 9 rolls.
|
The shape and section straightening machine was
designed to straighten large quantities of bars in a large-scale
production system. The top rollers were vertically adjustable to
deflect the material to be straightened and horizontally
adjustable to enable complicated sections to be dealt with. Each
machine was supplied with a set of rollers to suit the
customer's own requirements and all gearing was of cast steel
and all bearings had bronze bushes. The speed of straightening
depended upon the shape of the section and the nature of the
material. |
The S.G.5 shape and section
straightening machine with 8 rolls. |
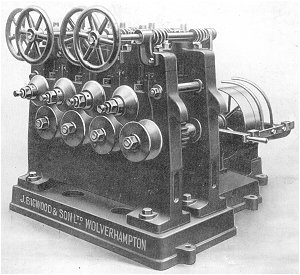 |
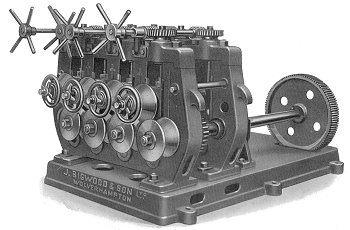 |
The S.H.8 shape and section
straightening machine with 8 rolls. |
The S.K.10 shape and section
straightening machine with 8 rolls. |
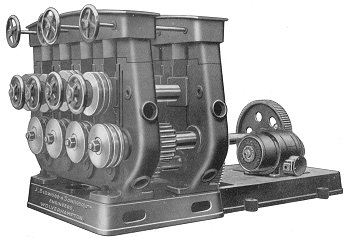 |
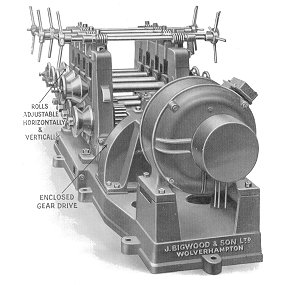 |
A motor-driven S.H.8. |
The Bigwood high efficiency multiple roller sheet
straightening machine could perfectly flatten buckled and dished
sheets and remove all rolling and stretcher strains. The machine
was easily adjustable using the hand wheels on the front of the
machine, each of which was provided with an indicator.
Lubrication was centrally provided by a pressure grease system
and finger guards were provided to safeguard the operator. |
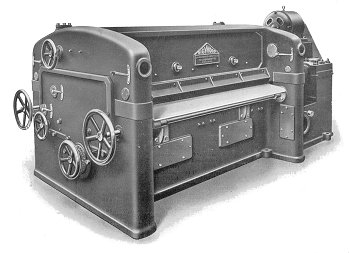
A high efficiency 17 roll sheet
straightening machine
|
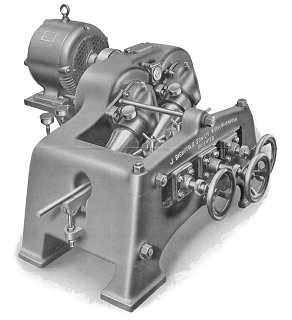
No. OA tube and bar straightening machine
|
The No. OA tube and bar
straightening machine could straighten any bar up to seven
eights of an inch diameter and any tube up to one inch in
diameter at a speed of 300 feet per minute. The rollers were
adjustable both horizontally, vertically and in an angular
direction to ensure that alloy heat treated steels could be
straightened in a perfect manner. All bearings were covered to
prevent the entry of dirt and a special flood lubrication system
and oil bath was included. The machine could be driven from a
belt or electric motor. 7 hp. was required for dealing with
tubes and 10 hp. for bars.
|
A hand operated
straightening machine. |
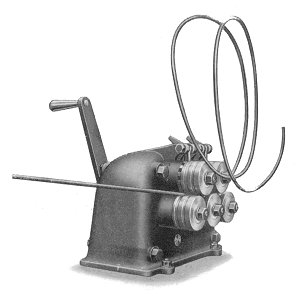 |
The following four photographs were kindly sent by
Terry Pringle. They show a working M.R.L. 4 plate
levelling machine that is still in use. As can be seen,
it is a typical heavy-duty, well-built Bigwood product,
designed to have a long and reliable life. It is lovely
to see a well looked-after Bigwood machine, still doing
what it was designed to do. Sadly the business closed
in the middle of 2022 and the machinery was auctioned
off. Unfortunately no one was interested in buying the
machine, so it will now be scrapped.
I must thank Terry for his excellent photos and
details of the machine's sad demise. |
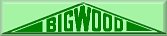 |
Return to
the
Bigwood section |
|