The Bigwood
Pipe-Bending Machine
Many people criticise Britain’s ailing
industries, especially in these post Thatcherite days when
engineering has sadly become so unfashionable. Not that many
years ago Great Britain was at the forefront of many
technologies and this is often forgotten. What follows is an
example of just how good we were at developing cutting-edge
technology. Even if we no longer have the will, or inclination
to invest and build new factories in which to use our innovative
technology, others still do. This is the story of an important
machine that was built in Wednesfield between 1979 and 1981,
which is now surplus to our country’s industrial requirements.
The machine has found a new home in Canada where it will
hopefully have a long and productive future. Background
In 1980 Bigwoods in collaboration with Radyne Ltd and the
Babcock organisation, built one of the world’s largest induction
pipe-bending machines. It was built under contract to the
consortium of the British Steel Corporation and Vickers U.K.
This machine ended its U.K. life in Scotland and has recently
been transported to Canada to be re-assembled as one North
America’s most important large pipe-bending facilities. |
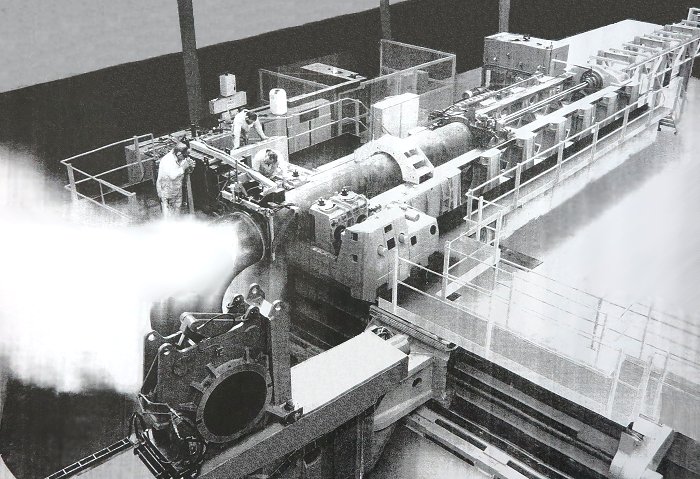
The pipe-bending machine in operation. |
A Brief History
In the 1980s the Romeo Vickers consortium
were developing nuclear power stations and equipment for Trident
submarines. For part of the work they required a large
pipe-bending machine and so a joint venture was set up between
Romeo Vickers and the British Steel Corporation at Tipton to
develop a suitable machine for the purpose. The design and
building work for the machine was contracted out to four
companies by the project managers at B.S.C. as follows:
Babcock Power Limited, Research Centre,
Renfrew carried out design and development work.
Bigwood & Company of Wolverhampton carried
out the mechanical, structural and hydraulic work and did the
final assembly.
Lightwood Engineering produced the
electrical layout.
Radyne of Wokingham, Berks designed and
built the necessary electronic control equipment. |
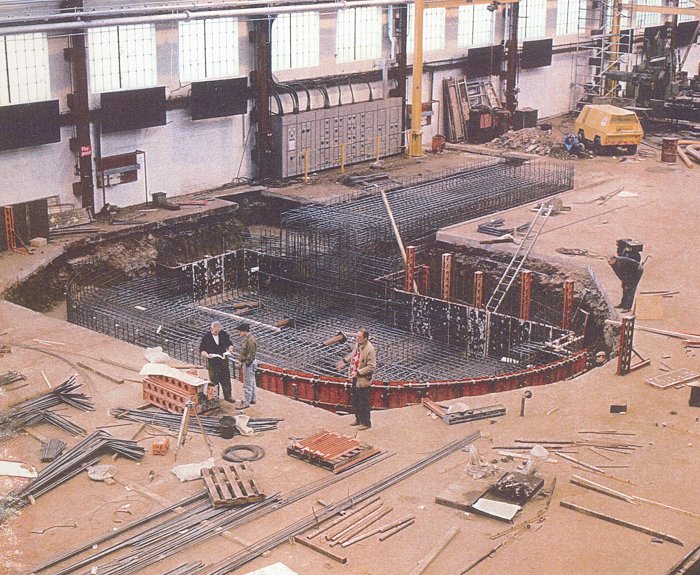
Preparing the site, in readiness for
the installation of the machine. |
The machine has an impressive specification. It is
capable of bending a 36 inch diameter pipe with 4 inch thick
walls and can equally handle a 6 inch diameter pipe with quarter
inch walls. The machine includes an induction heater to heat the
pipe and a water and air cooling system to cool the pipe after
bending. The temperature is accurately controlled and the water
system filters and recycles the water for reuse. There is a
triple axis movement of the rolls and coils, with forward,
backward, up and down control of the pipe and independent
adjustment of the heating coils. A 65 ton hydraulic ram with a
30 foot stroke transports the pipe through the machine at speeds
from 38mm per minute for large bore heavy wall pipe to about
250mm per minute for small bore light wall pipe. |
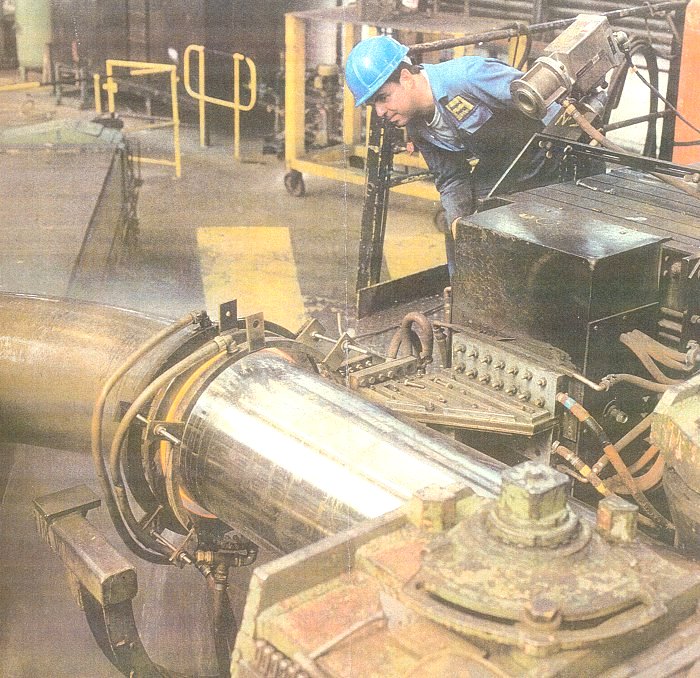
An operator keeps an eagle-eye on a large
bend. |
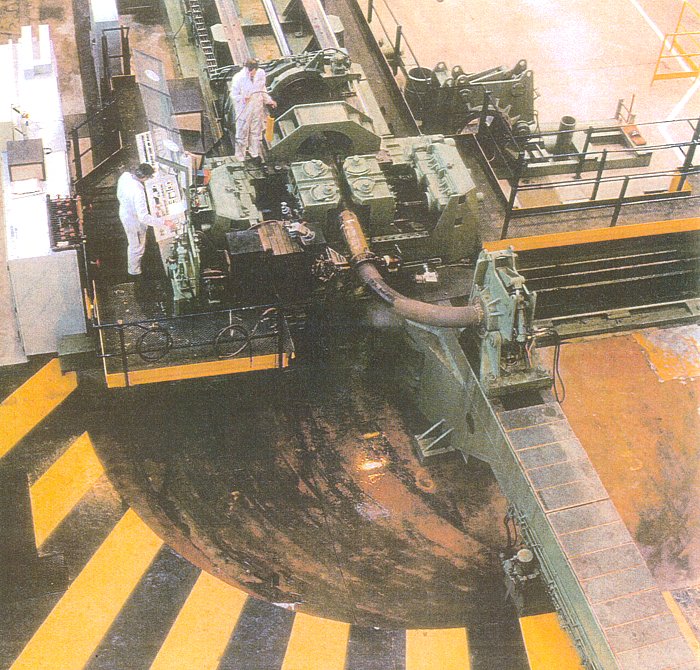
An aerial view
showing the machine in operation. |
The operator has light finger-touch controls which
allow for a large degree of control and latitude to perform an
excellent pipe bend.
The machine was assembled by Bigwoods and put into service in
the Birmingham area in about 1982. It originally accommodated
the pipe-bending requirements of Britain’s Trident nuclear
submarine program at Vicker’s U.K. yard.
Sometime in the late 1980s it was moved to the premises of
Mitsui Babcock in Renfrew and used to bend pipes for Babcock
built power stations throughout the world and North Sea oil
installations. |
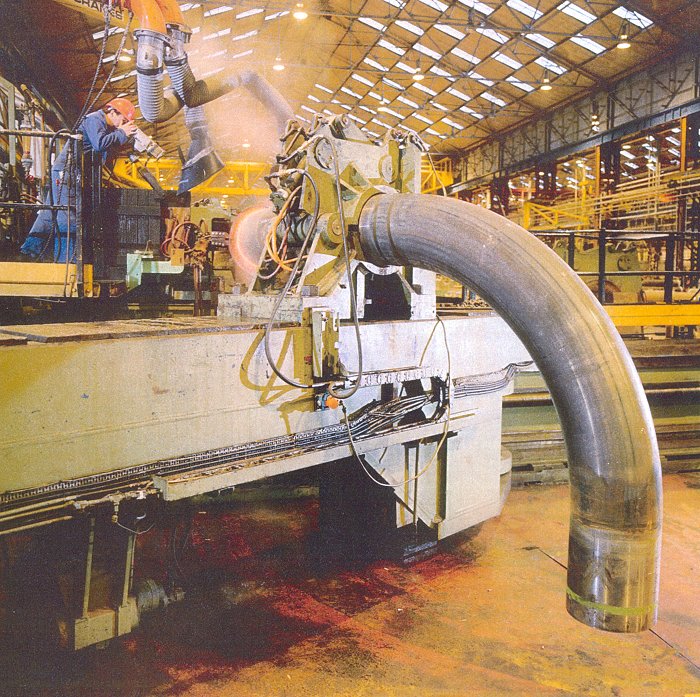
A large pipe leaving the machine with the
operator monitoring the induction heating. |
Rebirth
In 1998 the Babcock plant closed and was turned into a glass
storage warehouse. The pipe-bending machine was purchased by
Triple DDD Bending of Calgary, Alberta, Canada. It was
decommissioned, disassembled and transported to Canada under the
watchful eye of Project Manager Syd Maskey. The company is
building a new plant to house the Bigwood machine and a draw
bending machine on land at Glenmore Trail and 48th
Street, Calgary. The now outdated induction heating and control
system will be replaced with modern technology and the Bigwood
Induction Bender will be housed in a purpose built 70ft x 200ft
factory at 4715 Glenmore Trail S.E., Calgary, Alberta, where it
will hopefully have a long and useful life. |
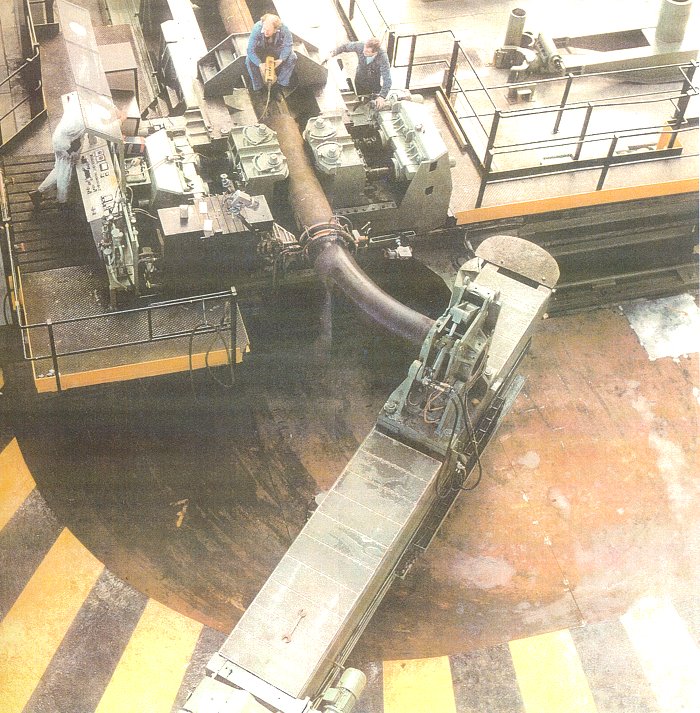
A final view of the machine in
operation. |
I would like to thank Mr. Syd Maskey and Mr. Pat Jordan for
their help in producing this history of an important
Wolverhampton-made product.
|
Return to the
previous page |
|
|