Apprenticeship
I joined Chubb as a student
apprentice on 4th September 1950, straight from
Wolverhampton Grammar School where I had specialised in
science. My original career ambition had been to go to
Sandhurst as a professional soldier, but I had failed
the medical due to slightly defective vision. The
Wolverhampton Juvenile Employment Bureau were most
helpful and on being advised that part of my reason for
a military career was "to see the world", suggested an
interview with Chubb, who were seeking young men to
train in security engineering and then to join the
Export Department. I was interviewed by Leonard Dunham,
the Sales Director and Leslie Tinkler who doubled his
job as chief estimator with that of apprentice
supervisor. |
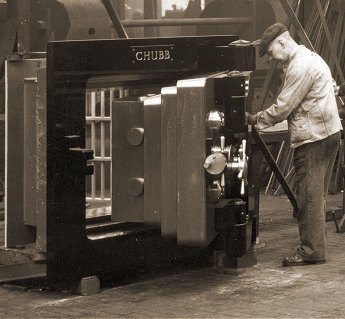
A strong room emergency exit door
nearing completion.
Courtesy of the Reverend Bill Enoch. |
Most apprentices started work in
the tool room where they were introduced to engineering
machinery, measuring instruments, and the basics of hand
fitting.
I was extremely fortunate to be
trained by Albert Ling, who was the model maker,
responsible for pre production safes etc, based on the
new drawings.
Our charge hand was a larger than
life character, Ron Brown who later progressed to the
Research Department, where amongst other things, he
handled the explosives used for testing safes, and the
weapons used in testing bullet resisting materials. |
At that time we
were working a forty four hour week, and during term
times apprentices were expected to attend Wolverhampton
and Staffordshire Technical College, later Wolverhampton
Polytechnic and then Wolverhampton University, for one
day a week and
as many evening sessions as demanded by our course.
Every six
months, apprentices changed their place of work, so as
to familiarise themselves with the whole factory and its
production.
My next place of
work was the Lock Shop, which consisted of a very large
number of repetition lathes, milling machines etc.,
mainly operated by women under male tool setters, and
the locksmiths benches at which the locksmiths, whose
apprentices underwent a separate course to the safe
works apprentices, produced the whole range of locks |
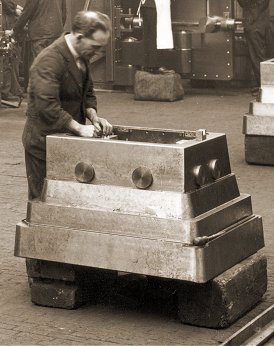
Assembling a strong room
emergency exit
door. Courtesy of the Reverend Bill Enoch. |
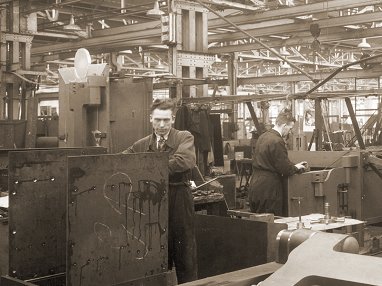
George Palmer constructing
a strong room door. Courtesy of
the Reverend Bill Enoch. |
My next area was the Light
Product Works, where fire resisting filing cabinets,
safe deposit lockers, metal deed and cash boxes were
produced.
Initially, I was based with Horace
Ward, the shop foreman, following which I had spells
with Walter Webb, charge hand of the fire resisting
filing cabinet section and then with Bill Stean on the
safe deposit locker section.
Bill had a sideline as a dance
band leader and was a popular figure at local dances. |
A spell in the
safe works followed, where I spent a fair amount of time
on the vault door section, although I was encouraged to
look over other sections such as safes, night deposit
traps, the foundry, and heavy machine bays. Most
interesting were the number of relatives who all worked
in the same areas. The Hamlin brothers, who made all the
night deposit safes with their apprentice, Dennis Unit,
who later became a senior manager. The Moore family were
welders and one of my fellow apprentices, also a Moore,
later became a first class welder. The Roberts family
were well represented and over the years were known as
"Old Cock", "Young Cock", "Bantam" and Chick", although
I remember only Chick Roberts. |
Whilst in the safe works, I was
seen again by Mr. Dunham, during one of his visits, who
enquired whether I still wished to go to the Export
Department. On receiving an affirmative answer he
arranged for me to transfer to the Drawing Office, under
David Tate, the Chief Draughtsman.
I must confess I was not a good
draughtsman but was greatly helped by David Tate who
allowed Ron Swift and myself to carry out many fire
resisting tests on his behalf as he strove to develop
better fire resisting materials. We also made a number
of small prototypes which were most interesting,
particularly when they entered production, based on my
drawings. Ron Swift went on to become a first class
designer and was responsible for many of the later
security features for high grade safes. |
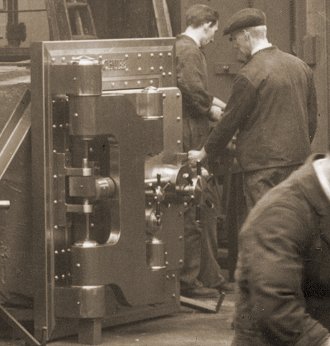
A nearly completed strong room
door. Courtesy of the
Reverend Bill Enoch. |
For a short period I spent time
with the Time Study department who were responsible for
deciding how long the various items of equipment should
take to make (and therefore the labour cost). This
background was extremely useful in estimating production
time and cost when I joined Export Department, and non
standard items were called for. |
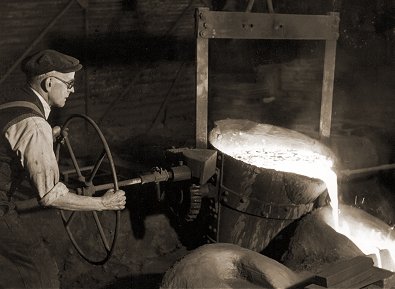
Casting anti-blowpipe alloy
in the early 1950s. Courtesy of the
Reverend Bill Enoch. |
After a further brief spell with
John Jeavons and Charles Grainger, who dealt with the
programming of orders for Chubb products, I was
transferred to Birmingham sales office, then based in
Newhall Street to start learning the basis of selling
Chubb products.
I was extremely fortunate in that
Frank Hall, the sales manager, let me deal with the
showroom and also go out on calls from time to time, and
also assist Peter Dewey, a first class engineer who
dealt with repairs and breakdowns. |
Peter and I became close friends
and in later years I was able to recommend him for
Overseas Installations, which until then had been
carried out by one or two works engineers, notably, Les
Minshall. Finally in September 1955, my indentures came
to an end and I awaited call up for National Service at
the age of twenty two. |
Back From
National Service
Following my National Service in the RAF, I resumed work
at Wolverhampton on 1st January, 1956. I was attached to
Mr. Reg Hoye, manager of the Lockworks and given a
refresher course.
I was involved in the early
attempts to manufacture certain locks without all the
hand fitting by locksmiths. This work was carried out at
Leyton, in East London, at the former Hobbs Hart factory
The experiment was not altogether successful but it gave
an insight on what was required to manufacture locks in
this way.
For the final month of my time at
the factory, I was allowed to spend time on the
locksmiths benches, not usually granted to any except
lock apprentices, where I spent time hand fitting locks
and dealing with three and four wheel combination locks.
Finally, in August 1958, I
transferred to London sales to take up my career. |
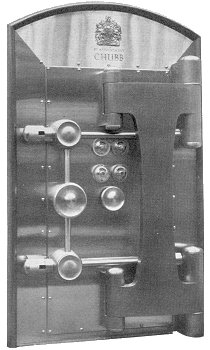
A Chubb
Treasury Vault door. |
Since joining the Company in
1950, rapid expansion had taken place and in this
period, Chatwood-Milner, itself formed by the
amalgamation of Chatwood and Milner, was taken over.
Hobbs Hart, Josiah Parkes (Union locks), Burgot Alarms,
Rely a Bell, Pyrene, Read and Campbell and others were
acquired to form the rapidly growing security group.
Additionally, a company had been set up in Canada and
the existing operations in Australia and South Africa
expanded. |
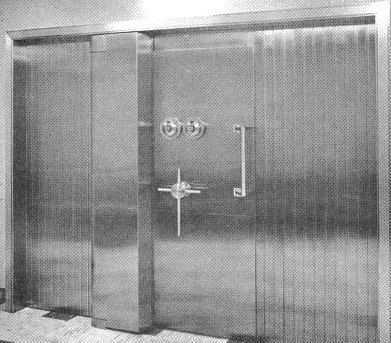
Another Chubb
Treasury Vault door. |
In addition to this rapid growth,
much development work was taking place in the
construction of safes and vault doors to counter a large
number of burglary attacks.
Many men had been trained in the use
of explosives, cutting equipment and modem tools during
their military service and as much security equipment in
use dated back to the early parts of the twentieth
century, the contest between modern explosives and
cutting equipment, and obsolete safes, was very one
sided. |
The banks especially, were keenly
aware of the problems posed and instituted large
upgrading programs in their branches, which kept the
security companies, Chubb included, at full stretch.
This period saw the development of the new relocking
devices from the pre-war "static" varieties which could
be beaten by preloading the bolt throwing handle during
an explosive attack, to the final version of the Chubb
"live" re-locker which operated every time the safe was
locked, which together with the handle clutch mechanism,
which disconnected the handle from the mechanism when
locked, effectively closed this avenue of attack. As a
result, explosive attacks became very rare during the
final years of my service. |
Oxy acetylene metal cutting
equipment had been available to safebreakers since the
late 1800's and Chubb had developed a ferrous based
material which we called A.B.P. (anti blow pipe) which
was practically impervious to attack by oxy acetylene,
and this material which was cast in thick slabs was used
in heavy bankers safes and vault doors.
In the late 1950's however a new
cutting device utilising both the electric arc and
oxygen was produced to cut up the complex alloys which
had been used in the manufacture of military tanks etc.
This was the oxy arc cutter. The first successful attack
using this new tool was carried out on a London bank in
the late 1950's. The perpetrators were caught as the
tool was so new that the manufacturers kept records of
all purchasers. It quickly became obvious that Chubb
A.B.P. could be penetrated by this new weapon and after
much research a material comprising copper and extremely
hard inclusions which Chubb called Anti Arc was
produced. |
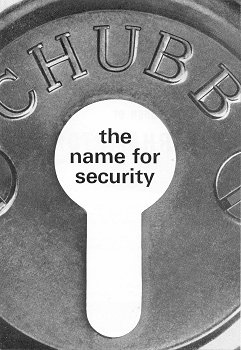
An advert from 1968. |
This material not only protected
against penetration by oxy arc but also effectively
countered the threat posed by the new tungsten carbide
tipped drills, and the percussion drilling machine which
could bore through most hardened steels and concretes.
A further version of this protective
material was developed using aluminium in lieu of
copper, which was found to be ideal for the protection
of the bodies of safes. Very soon a process was
developed using the aluminium based material, which
enabled the foundry to cast a five sided "bell" on a
heavy steel inner shell, and this system quickly
replaced the old iron based protection used in the
bodies of high grade safes, and remained in use until
the closure of the Wednesfield Road plant.
This form of protection, allied
with a highly sophisticated drill protection, which
covered the vulnerable points of the Chubb "isolator"
bolt locking mechanism, was used in the highest grade
production safe produced at Wolverhampton, "The
Sovereign". |
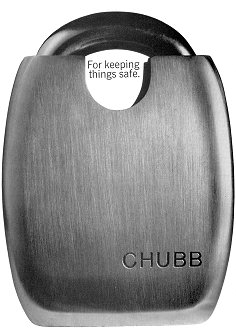
An advert from 1972. |
Until my retirement from the
Company at the end of 1991, no successful attack was
ever recorded on this type of unit. For cheaper
range safes, special concrete protective layers were
developed by the Research Department, which gave
incredibly high levels of protection. These
concretes utilised metal and synthetic fibres to
prevent the shattering, which normal concretes are
subject to, and strict quality control enabled
concretes having extremely high crushing strengths
to be produced. The
early attempts to produce locks more cheaply than by
the traditional hand fitting by locksmiths
eventually bore fruit. Whilst domestic locks (those
for use on company products) were still manufactured
by skilled locksmiths, those sold to the general
public for household and commercial use were
manufactured by a process of extremely accurate
machining which enabled semi skilled fitters to
assemble them without compromising security. |
The Later Years
The vastly enlarged company fortunes
prospered until the early 1970's when a further addition
to the Chubb group was made. The Gross company
manufactured a range of mechanical cash registers, which
had been extremely popular with many large chain stores.
Unfortunately, insufficient research had been undertaken
to move from mechanical machines to the coming
electronic and computer controlled systems. It became
obvious that unless something could be done to remedy
this situation, Gross would go out of business with the
loss of a large number of jobs.
Naturally this prospect horrified
the Labour government of the day and a high level search
was instituted to seek a rescuer for the ailing company.
Chubb was one of the possible companies approached and
finally it is said after certain government inducements,
Chubb made an offer which was accepted. It quickly
became obvious that Gross was beyond saving, in spite of
large amounts of capital being injected in an attempt to
catch up on the neglected research work.
Finally the cash register business
was closed causing a loss of the capital which had been
denied to the core businesses of the Group. This
financial blow had a severe effect on the stock market
standing of the Chubb Group, as dividends paid to
investors suffered and also reduced funds for the
development of the group. |
Chubb quickly became a target in
the financial press, as the likely victim of a take over
bid themselves and on many occasions G.E.C. were said to
be the likely predators.
In fact, a senior director assured me
that no take over bid was ever received from G.E.C. or
anyone else, but over a period of time, the drip, drip,
drip of rumour had the desired effect. |

A final view of a
Chubb Treasury Vault door. |
Racal, headed by Ernest Harrison
was a long time competitor of G.E.C.; in fact it was
reported that there was considerable rivalry between
Arnold Weinstock of G.E.C. and Harrison. Eventually,
Racal launched a bid for Chubb, some said to spite
G.E.C. and as Harrison had something of a cult status in
the City, as a financial wizard, the bid succeeded.
The main casualties were most of
Chubb's senior management, including Lord Hayter, W.E.
Randall, and W.G. Bannochie, all of whom had
considerable service with Chubb and had been successful.
Their replacements under the Racal regime were of a much
lower quality and many employees, including me, could
not understand why Racal had bought the group and for
what purpose. Initially, Chubb were amalgamated into the
Racal Group, but the promised increase in value failed
to occur and eventually Chubb were de-merged from Racal
and set up again as a stock market quoted company.
In the early years of Racal
ownership, many in Chubb, myself included, wondered why
we had been taken over. |
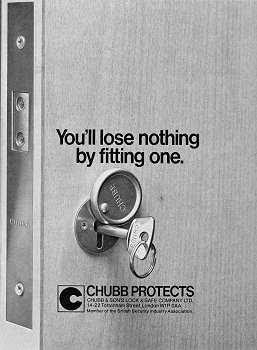
An advert from 1974. |
One explanation given to me
whilst on holiday in the West Indies, occurred during a
lunch with two Racal directors, who happened to be
visiting the island where we shared a common agent. The
managing director of our agent, having mentioned my
presence on the island to the Racal men, acted as the
host. During lunch I was quizzed about many aspects of
Chubb and the reaction of Chubb staff to the take over.
I answered to the best of my ability and towards the end
of a very good lunch, one of the Racal men asked if I
had any questions of my own.
I enquired the reason for the take
over when nothing appeared to have changed. "We believed
that you had a very sophisticated electronics
department", I was told. I protested that within the
Group we had alarm and fire companies but really their
work comprised standard electrical fitting rather than
specialised electronics. To this I received the amazing
answer, "Yes, we know that now". |
It appeared that an error had
been made and it was believed that all towns where a
Chubb Super Centre sticker was displayed - which
indicated a major lock stockist, in fact had an alarm
control centre. I was simply staggered and to this day I
cannot believe that such an elementary mistake could
have occurred. But if it had then at least there was
some sense in the take over.
As time passed and Racal desperately
attempted to provide the "value" which Harrison had
frequently told the City that he could provide, the
accountants resorted to what had become a very popular
measure at this time; discarding staff as a company's
greatest expense, in order to improve the "bottom line".
These voluntary redundancies were
a very fashionable way forward in many businesses at the
time and Chubb were no exception. Gradually, any staff
who might have been considered as excess left and as
further redundancies took place, the staff involved were
vital for production at Wolverhampton. More and more
redundancies were called for until finally in 1991, it
was decided that not only production personnel but also
management and sales must also be "downsized".
In an attempt to save the
positions of some of our younger and very promising
staff, I volunteered to go, on the basis that after
forty one years service, I had very few more years to go
until the official retirement age of sixty five. On
December 31st, 1991 I left the office for the
last time. Unfortunately, this did not save the
prospects for many of our younger staff, who were
dismissed, which I felt to be extremely unfortunate as
they were the future life blood of the company. |
Shortly after my retirement,
Racal sold the Chubb business to Williams, who owned the
Yale lock company. There had been rumour for some years
that Williams were seeking to acquire Chubb; presumably
to consolidate their lock business.
After a few years however, Williams
decided to break up and sell off their security
business. Fire Alarms and manned security were bought
out by United Technologies, an American concern, whilst
the locks and safes were purchased by Assa Abloy, a
Finnish security organisation, who then sold on the safe
operations to Gunnebo, another Finnish concern.
The Wednesfield Road factory was
closed down and the lock manufacture moved to Willenhall
for Commercial locks, and to a new smaller manufacturing
plant for the high security (prison) locks. |
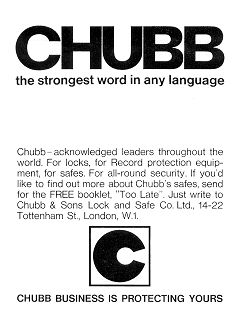
An advert from 1970. |
There was great
sadness amongst many of the former staff, that after
almost one hundred and seventy years, the safe making
skills, in which Chubb had been world leaders, were
finally lost.
It has often
been said that in this modem age, where cash is not so
significant, such skills were no longer required. One
has only to recollect however, that precious metals,
jewels and other valuable commodities still need
protection from theft and that cash is still vitally
necessary for many transactions, to realise that there
is still a place for high grade security products. It is
a pity that the house of Chubb no longer exists to meet
these requirements.
©
D. R. E. Ibbs. August 2007. |
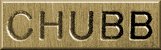 |
Return to
the
Chubb menu |
|