Little is known about the company’s early years.
It was established in about 1850, the same date as the oldest
building on the site, which presumably was purpose built for the
company. Originally it was called the Crown Nail & Stamping
Company, as was seen on several brass clocking-in disks that
were found at the works in the 1950s.
The advert opposite is from the 1902 Wolverhampton Red Book
and lists many of the company's products. |
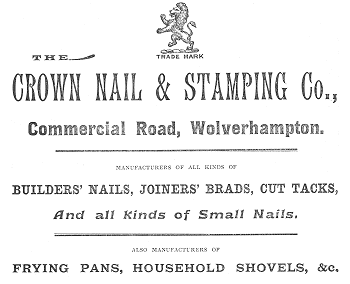 |
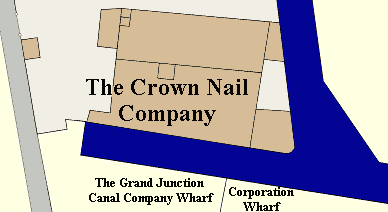
The works in 1871.
|
By 1884 the company was called the Crown Nail
Company, as mentioned in John Steen & Company’s Guide to
Wolverhampton.
Until the early 1950s the company was owned by the Lloyd
Family and it is believed that they were the founders. |
In the early years domestic holloware must have been produced on
the site because a number of frying pans, each bearing the name
“The Crown Stamping Company” were used in the works as tack
pans, until the 1950s.
Steen & Company’s directory of 1884 lists
four nail makers in Wolverhampton:
The Crown Nail
Company
The Patent Tip & Horseshoe Company
Messrs. Neve & Company
Danks, Walker & Company.
|
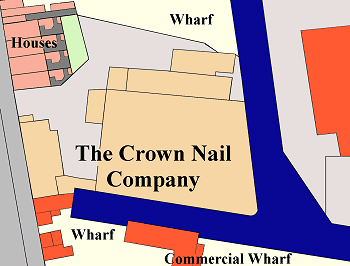
The works in 1901.
|
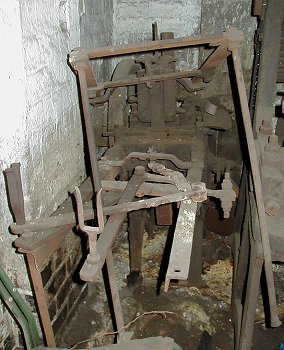
The old Elwell low-down nail machine that
was used in the early years. It still has the original pre 1910
seal to prevent the machine from being used at the time when the
industry was rationalised. The machine must have been in store
for nearly 100 years. |
Two of the companies, The Crown Nail Company and
The Patent Tip & Horseshoe Company were next door neighbours.
Several old machines were kept in store in the Commercial Road
factory, dating from around 1870 but unfortunately carrying no
manufacturer’s name. It has been suggested that they may have
come from The Patent Tip & Horseshoe Company, next door, which
stopped making nails in about 1883.
The Company was run by Paul Bedford Elwell who took out a
patent for nail making machinery in 1876. The patent is for a
low-down cut-nail machine that used a peculiar oscillating feed
arrangement for the steel strip. Instead of turning the strip
over in-between cuts, the strip moved through an arc and each
cut was parallel to the front of the machine.
The oldest machine that was in store at the works used an
identical arrangement and so is likely to be an Elwell machine.
This machine and the one below have been saved by the Black
Country Living Museum and will be on display in a few years
time. |
In the early years the Crown Nail Company was run
by John Lloyd and it seems that his wife Rose Lloyd took over at
a later date, her signature was found on an old indenture. She
was a rather strict and domineering woman and had two sons, who
later ran the business for many years. The Lloyds were Welsh and
lived at 3 Waterloo Road North before moving to “Hafren”
in Albert Road sometime during the 1930s. |
The company was probably founded by John Lloyd and so he must
have been much older than his wife, who lived until the mid
1940s. He had presumably died before 1902 because the family is
listed under the name of Rose Lloyd in the 1902 Wolverhampton
Red Book. The two children, Jack and Harry attended Rugby
School. They were very different, Jack being an extrovert and
Harry an introvert who kept himself to himself.
The two brothers took over the running of the company when
their mother retired. Harry Lloyd ran the office and his brother
Jack, an exceptional engineer, ran the factory. Jack enjoyed
mixing with the workforce but was a strict disciplinarian. Rose
never allowed her sons to marry, they were both dedicated to the
company and spent as much time as they could there. Jack’s only
luxury was his Bentley car, of which he was justifiably proud.
Once a year he would take a week’s holiday and drive off
somewhere. He would always return after about five days because
the factory was his life and he couldn’t stay away.
|
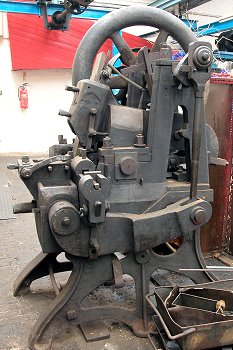
An old machine dating from the 1870s |
The factory started at the southern end of the
site where the bluing machine used to be. There were even power
presses upstairs on the wooden floor. The company seems to
have been doing well because in the early years of the 20th
century the central building with the Belfast roof was added. |
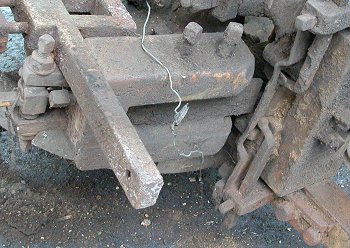
The surviving seal on the Elwell nail
machine. |
Nail production ceased in about 1910 and didn’t start again
until 1986. At the time too many nails were being produced and
in order to protect manufacturers and control prices, a form of
rationalisation was introduced. Many companies, including the
Crown Nail Company were paid a certain amount each year not to
produce nails and so only tacks were made. Seals were placed on
the moving parts of the nail machines to ensure that they were
not used. The Elwell machine that was in store still carries its
seal. |
Cyril Haydon, who later became Jack's right hand
man, started at the company in 1909 at the age of 14 as a
feeder. Most of the feeders were girls and they earned just
2s.6d a week and were very poor by modern standards, many only
owning a single set of clothes, which was common amongst factory
workers at the time. |
The feeders were a militant group who insisted
that any new recruit to their ranks must already have a relative
working at the company. Cyril had no relative there, but he did
have a distant relative who ran the pub that was used by the
feeders, and we believe this to have been "The Bradford" in
Commercial Road, where many of the local feeders used to drink.
Cyril's colleagues insisted that he went with them to the pub
and they said to the landlord "Do you know this boy" and he
replied "No". Unfortunately Cyril had not met the landlord
before and so the two relatives did not recognise each other. |
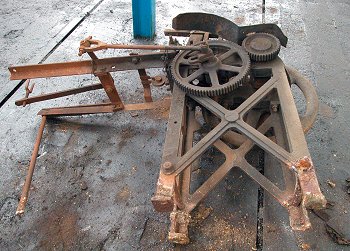
Another view of the Elwell machine showing
the peculiar oscillating feed arrangement. |
It was a closed-shop and in order to appease the feeders
Cyril had to leave, otherwise they would have come out on
strike. He left the Crown Nail Company and began an engineering
apprenticeship at Culwell Works in Wolverhampton.
Jack Lloyd must have taken a liking to
Cyril and regretted his departure, because two years later he
asked him to return to the company and join him in the fitting
shop. This was acceptable to the feeders and he returned in 1911
to continue his training under Jack. Cyril was known as Sid at
the works and he and Jack became close friends.
|
The Elwell machine
and another ancient nail machine in store at the works.
Sadly the machine on the right was scrapped. |
|
The 1914 Wolverhampton Red Book lists two
nail and tack makers:
The Crown Nail
Company, Commercial Road
G. Horobin, 76 Lower Villiers Street
The Crown Nail Company is also listed under
general stampers, and so stamped products were still produced in
1914.
During the First World War the company
supplied all of the tacks that were used to hold the fabric to
the wooden framework of the early military aircraft, which
proved to be extremely lucrative for the Lloyd family. During
the war Cyril Haydon went into the army where he worked in a
field ambulance and was a batman to the Colonel. He didn't enjoy
his new role and when he heard that the army was looking for
engineers for its workshops, he applied and after easily passing
a test became an army engineer. After the war Cyril returned to
the Crown Nail Company and continued to assist Jack Lloyd in the
fitting shop.
|
The tack machines always ran from overhead line
shafting. Works Manager Ken Farrington remembered one of the old
employees, Frank Edwards describing how it used to be. The
shafting was originally driven by two gas engines, one located
in the old part of the works and another in the fitting shop.
After the second engine’s removal, a slight quarter-circle was
left on the floor where the engine’s flywheel ran. The engines
were replaced by a 50h.p. E.C.C. electric motor that was itself
replaced in 1972. There was also a spare that remained in the
storeroom until the works closed. |
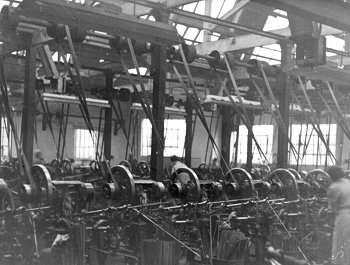
An old view of the tack shop showing the
overhead line shafting that drives the machines. |
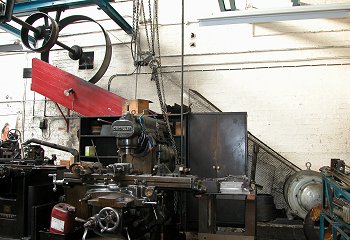
The 50h.p. motor driving the overhead line
shafting. |
The spare was dated 1926 and so presumably that’s when
the gas engines were replaced. The line shafting proved
to be extremely reliable. It originally used leather belts and
if one broke it would simply follow the pulley and drop to the
floor. In later years the belts were made of nylon and leather,
with a layer of nylon on the outside for strength and a thin
layer of leather on the inside for grip. Older belts were joined
by a riveted steel plate that was eventually replaced by a steel
gripping system called a “clincher”. |
If the electric motor failed it would take no more than half a day to exchange
it for the spare. It’s incredible to think that the whole factory was
efficiently running from just one 50h.p. motor. |
Expansion
In the 1920s tack production centred around
a number of low-down machines. Towards the end of the decade the
Lloyd brothers decided to expand production and greatly increase
the number of machines. They purchased an American Blanchard and
a British low down machine which were typical of the day, but
Jack was not satisfied with them.
|
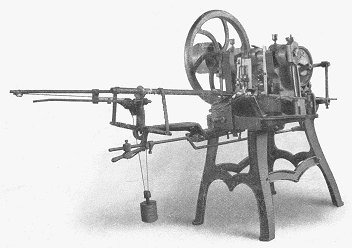
An American Blanchard machine.
|
He decided to take the best parts from both
machines and with the help of Cyril, use them in a machine of
their own design that would out-perform the commercially
available machines at the time.
With his in mind he fully equipped an enlarged fitting shop,
where he and Cyril designed and built the new tack machines.
Many of the parts were made in-house, but such things as
castings had to be brought-in. |
Two types of machine were developed; a standard machine and a
heavy duty machine for longer tacks. Many of the parts including
the tools were fully interchangeable between the machines, which
proved to be very successful. Reliability was foremost in Jack’s
mind. For simplicity they used plain phosphor bronze bearings
(bushes) where possible. All of the bearings in each machine
were of this type except for a pair of big double self-lining
roller bearings, which were brought in to fit the machines. This
technique has worked well because none of the bearings have had
to be replaced for many years, only an occasional machining has
been necessary during normal preventative maintenance.
Jack was extremely pleased with Cyril's contribution in the
development of the new machines and rewarded him with a large
toy car for his young son. They became firm friends and Jack and
Cyril would go together to visit other companies. Jack even gave
Cyril a suit to wear for these occasions. |
One of the standard
tack machines that were designed by Jack Lloyd and
Cyril. |
|
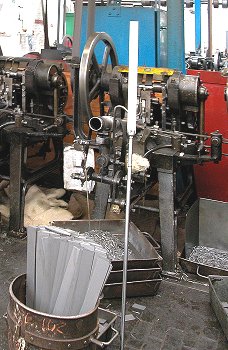 |
A large Lloyd tack machine
in the tack shop. Leaning against the rest is the steel strip,
attached to the feed-rod, ready for inserting into the barrel.
The barrel can be seen to the left of the feed rod.
In the foreground is a keg containing a
supply of steel strips. The finished tacks are collected from
the pan on the right. |
A close-up view of one of
the machines in the fitting shop during repair. On the left is
the flywheel that is attached to the pulley for the overhead
belt. The flywheel is attached to one end of the cam shaft that
operates the tool-holders, which can be seen in the centre of
the photograph. This machine is currently in-store at the Black
Country Living Museum and will be on display in the future. |
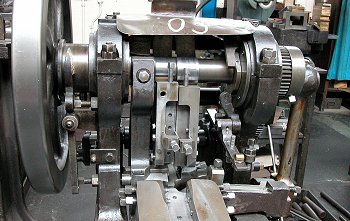 |
The tacks are cut from a strip of steel that’s
hand fed into a long barrel by the operator. Each strip is
clamped to the end of a feed-rod and inserted into the barrel.
It is gravity fed into the machine by a “leather” and a cord
that is attached to a weight. The barrel rotates through 180
degrees before each nail is cut from the strip to minimise
waste. |
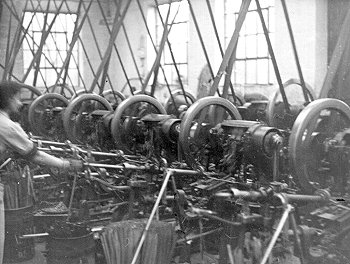
An old photograph showing the machines in
operation. |
The machines were a great advance on anything else
that was available at the time and between 1931 and 1964 a total
of 104 were built as required.
The smaller machines could produce 280 tacks a minute and
the larger machines 240 tacks a minute.
The first machine went into production on 30th
November, 1931 and was set up by Mr. T. Hitch. |
The machines were built as follows:
Year |
Number Built |
Year |
Number Built |
Year |
Number Built |
1931 |
5 |
1938 |
12 |
1950 |
1
|
1932 |
8 |
1939 |
6 |
1952 |
4 |
1933 |
4 |
1940 |
4 |
1959 |
3 |
1934 |
12 |
1946 |
6 |
1960 |
2 |
1935 |
6 |
1947 |
2 |
1961 |
3 |
1936 |
10 |
1948 |
5 |
|
|
1937 |
9 |
1949 |
2 |
|
|
|
Four of the machines would be overhauled at any
one time. The machines were taken out of service for
preventative maintenance on a five year cycle, irrespective of
whether or not it was needed. The machines were stripped down
and given a full overall before being returned to the tack shop.
The new machines were
installed in rows of ten, with a girl hand-feeding five
machines, so there were two feeders on each row. For every two
feeders there was a spare feeder who would take over if a girl
wanted to leave her machines. |
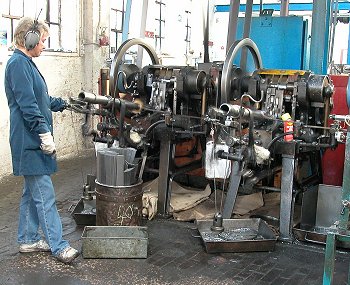
One of the last hand-feeders was Dawn
Sambrooks, who is seen here at work. |
If one of the feeders wanted
to go to the toilet she couldn’t leave her machines until the
spare feeder took over. This was done to maintain production.
The feeders were paid a production bonus, but not the spare
feeder who was on a lower salary. The bonus was calculated from
the number of tacks produced and was a few pence per 100,000.
When the tacks left the machines they were put into pans and
each girl’s output was weighed twice a week. Each tack was made
to a specific weight to ensure that the customer had a
guaranteed number of tacks per lb.
As well as the feeders there were setters. A setter
would look after 7 to 10 machines and keep a close eye on them,
because in those days the tools had to be taken out and reground
frequently due to the inferior quality of the steel. |
|
|
 |
|
|
Return to
Industrial Growth |
|
Return to
the Contents |
|
Proceed to
Shearing & Bluing |
|