Tack Manufacturing: The Later Years
The manufacturing process had now been
perfected and no further changes to the
machines were necessary. A girl could now feed 15
machines and a fitter could look after 15 machines. After
bluing, the tacks were put into pans and transported up an
elevator to the floor above, where they went around a gravity
fed roller conveyor to cool. After cooling they were weighed and
put into the appropriate packaging as requested by the
customer. The company’s brands were “Lion Brand” and “Bugle
Brand”.
|
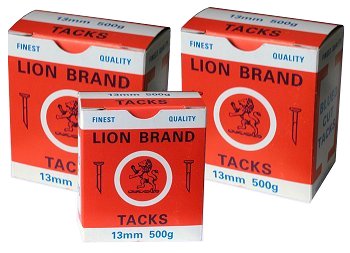 |
The tacks were noted for their quality, clean finish and sharp
points. Tacks were also available in a zinc-plated finish or
made from copper or aluminium, for use in boats and roofing.
Most of the tacks were exported to many countries including:
America, Hong Kong, Malaysia, Germany, Switzerland, West Indies,
Panama and Malta. Requirements varied from country to country.
Some wanted lighter tacks or smaller heads and these differences
had to be catered for. |
In the 1970s the Crown Nail Company broke into
the American Market and between 10 to 15 tons of tacks at a time
were sent to one customer alone. At this time the Chinese tack
manufacturers started supplying cheap tacks to North America and
the Americans started buying them in preference to the more
expensive British variety. This was a blow to the Crown Nail
Company and as a result the factory went on short time for a
while. About 18 months later the Americans once again started
buying the superior Wolverhampton product in preference to the
cheap Chinese tacks, because of a large number of complaints
from customers. One of the Crown Nail Company’s last production
runs was for an American customer. It was for 13 tons of special
stake tacks with a dimple in the head, and tip nails to hold
steel shoes on foundry boots. |
In later years it became difficult to attract
young people into the industry, which was perceived as being
dirty, with a lot of heavy manual labour. In the mid 1980s there
was a price war. |
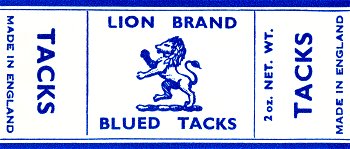 |
The company’s main competitor drastically
reduced the price of its tacks and everyone else followed. A
little while later production ceased at the competitor’s works.
The Crown Nail Company’s efficient production techniques had
paid off yet again.
The tacks were produced in a size range of
6mm to 32mm and were packed in 500gm, 2.5kilo and 10kilo boxes.
Most tacks are now sold in bubble packs and small cartons in
D.I.Y. stores. In later years about 99 per cent of the Crown
Nail Company’s tacks ended up this way. This resulted in a three
fold increase in the price of the tacks after they were sold to
the distributor who could purchase them in bulk 25 kilo and 10
kilo cartons.
|
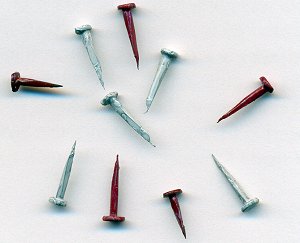
Gimp Pins.
|
One of the Crown Nail Company’s products was gimp pins,
which are used by upholsters. They have a thin head and are
coloured to match the furniture. The colouring is done by
placing 25 kilos of the tacks in a rotating barrel with internal
metal vanes. Paint is poured in and the tacks are coloured. It
is essential that the paint is lead-free, because many
upholsterers put the tacks in their mouths and so cellulose
paint is used. Gimp pins are rapidly disappearing because of the
introduction of staple guns and today they are only used on
hand-made furniture. A similar tack was also produced for
shoemakers. |
Next door to the works, in
the front room of one of the old houses was Crown Stores. The
shop was owned by one of the company's employees and run by his
wife. They sold sandwiches, bread, sweets, cigarettes and
tobacco.
Photograph courtesy of Mary Ashleigh. |
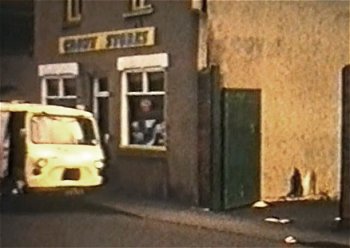 |
|