Chris Heath's Memories
of the Company
Chris Heath has been extremely helpful in producing this history of E.C.C.
He worked for the company for twenty two years, after following his father,
Gilbert, into the business. Gilbert did his apprenticeship at Siemens in
Stafford and after several moves, ended up at the E.C.C. Bushbury works. He
started the design of truck switchgear, which was to become an important
product for the company. Truck switchgear is built on wheels, so that it can
easily be moved to allow access for servicing or modifications.
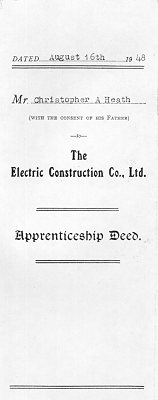 |
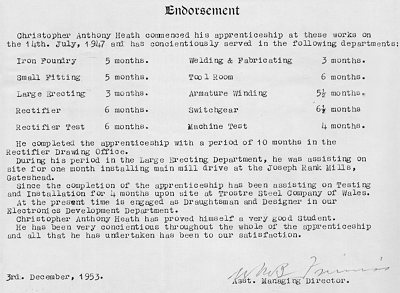
Part of Chris's
Apprenticeship Deed of 1948. |
Chris started his E.C.C. apprenticeship on the shop floor. Here he
learned many aspects of electrical equipment manufacture and also
went to the local technical college, where he got his Higher
National Certificate. In the summer of 1949, Chris helped with the
installation of the mill motor at Joseph Rank Limited's new flour
mill at Gateshead. The fitters included Arthur Jeavons and Sammy
Ball.
|
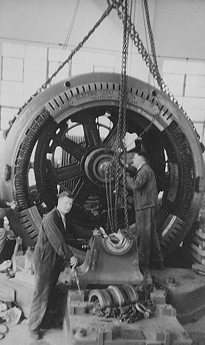
Installing the mill motor.
Photo courtesy of Chris Heath. |
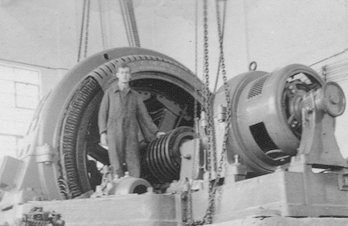 |
The Flour Mill motor nears
completion.
Photo courtesy of Chris Heath. |
The completed motor and the
installation team.
Photo courtesy of Chris Heath. |
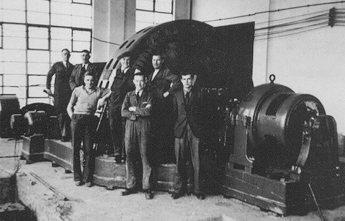 |
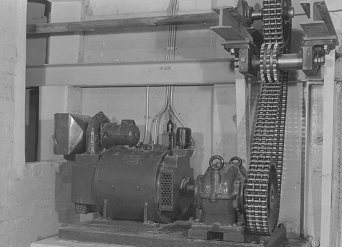
One of the motors and chain drive.
Photo courtesy of Chris Heath. |
In 1952, after completing his apprenticeship, he
joined the commissioning team, who installed the motors and control
gear for the tinplate line at the Steel Company of Wales, Trostre,
Llanelly. This was a continuous tinning process, on a large
scale, which involved the use of large motors and heavy duty control
gear. The control gear supplied two lines, each of which operated at
a current of 120,000 amps. |
Chris built the rectifiers for the control gear,
during his apprenticeship, and spent nearly twelve months travelling
between Wolverhampton and Wales.
The front view of the control board.
Photo courtesy of Chris Heath. |
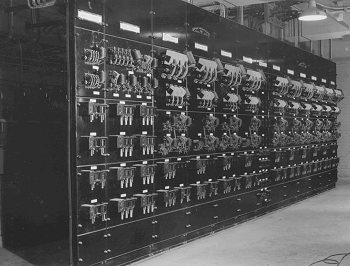 |
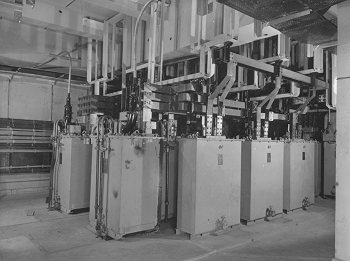 |
Transformers and rectifiers.
There were ten units, each consisting of 2 transformers, feeding
twelve 1,000 amp rectifiers.
Photo courtesy of Chris Heath. |
Chris then worked in the Electronics Department for 18 months. This was a
new department, which was housed in a part of the works, that used to
contain the old world war 2 mustard gas de-contamination plant. Here he
worked on electronic controls for use with motors and switchgear. After two
years in the R.A.F. he returned to the Electronics Department and then moved
to the machine design department, where he stayed for six years.
The company was interested in computers, and Chris
attended the first computing course that was held at the local
technical college, using the old 'Witch' computer,
which stood for Wolverhampton Instrument for Teaching Computing from
Harwell. Chris did some computing work at E.C.C. and then ended up
in management. |
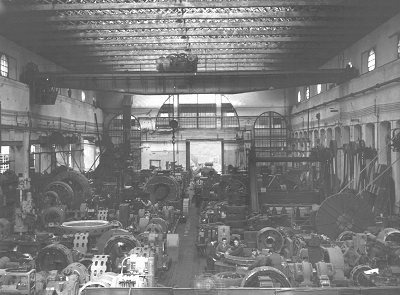
The Large Erection Shop in 1949. It was built
around the first world war and had two 60 ton cranes, one of which
can be seen in the photograph. These had cast gears which made a
terrific noise when they ran at speed. Photo courtesy of
Chris Heath. |
At this time the company was producing hundreds of automatic power
supplies for knitting machines and power supplies for electronic
telephone exchanges. Some of the many products made at E.C.C. were
centrifuge motors, for separating sugar from hot syrup in sugar
manufacturing. On 23rd June 1964 Chris took out a patent for
an accurate fan-hub tachometer.
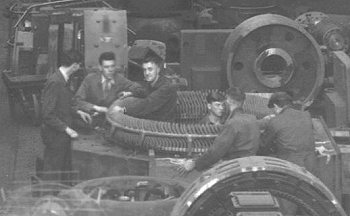 |
This enlargement from the
photograph above shows work in progress on a 33KV alternator for
English Electric at Stafford. The people are, from left to
right:
?, Johnny Howel (tester), Frank Hall, Brian Haddock
(Apprentice), Ken Hall, ?
Frank and Ken Hall were twins. Brian Haddock went on to become
the Plant Supervisor at E.C.C. Moulded Breakers. |
Chris remembers from his apprenticeship days, 'hammering in' colleagues,
who arrived late for work at Bushbury Works. Outside the timekeeper's office
was a rack, on which hung the metal tokens, each of which contained an
employee's works number. On arrival at the works, you picked up your token
and threw it through a rectangular hole in the timekeeper's office wall.
Behind the hole was a chute, and the tokens fell into a box at the bottom.
When the works hooter sounded, the timekeeper closed a gate at the bottom of
the chute, to catch any tokens that were handed in late.
If you were late, you were 'hammered-in' on arrival at the shop. Everyone
would pick up a hammer or a piece of metal and start banging it, to make a
noise. Adjacent shops would often join-in, and the sound could be heard in
most of the works. When the noise started, the foreman would come to see
what was going on, although of course he would realise what was happening.
It was all done in a light-hearted manner, but it meant that if you were
late, you couldn't sneak in to your bench. The works manager used to do his
rounds every morning and woe betide anyone who was late during his rounds.
This enlargement from the
Large Erection Shop photograph, shows Chris Heath at work during
his apprenticeship days. |
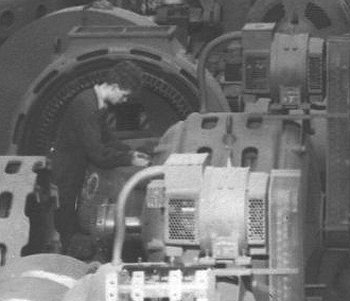 |
The E.C.C. was run like a family business and cared for its employees. If
there was an accident in the works and someone was hurt as a result, the
company would help out by finding a job for the man's wife, until he could
return to work. There were several generations of some families at work
there.
Chris left E.C.C. in 1969 and moved to Britool, where he worked on their
computer system.
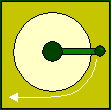
|
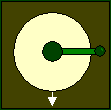
|
|
Return to the
Final Years |
|
Return to the
list of manufacturers |
|