The
moulding and casting process
Sadly very few working foundries
still survive in the UK and the once familiar moulding
and casting skills are rapidly disappearing. The
manufacturing processes and terminology were well known,
but are now alien to many people. The following section
describes the processes that go into producing a casting
from beginning to end. |
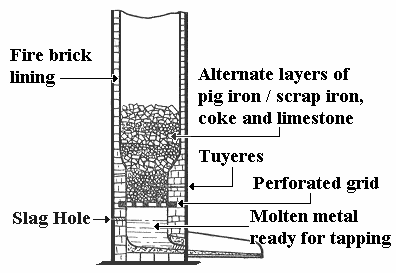
An early type of cupola. |
The molten iron is usually
produced in a cupola furnace. This is a vertical
cylindrical steel shell with a “well” at the bottom to
collect the molten metal.
The inside can be made of fire
bricks, but is normally constructed of steel, with a
water jacket for cooling and lined with clay. The well
at the bottom is lined with sand and the furnace is
charged through a door at the top with pig iron or scrap
iron, coke and limestone. |
Air is necessary
for combustion and this is blown into the furnace
through several tuyeres (blast holes) near the base.
There are cold blast cupolas where the air enters at
atmospheric pressure and hot blast cupolas where the air
is preheated by the heat from the exhaust gases. This
type of cupola has an increased melting rate, produces
hotter metal, and uses less coke.
The coke burns
fiercely thanks to the air blast and the metal soon
melts. The limestone acts as a flux, reacting with the
sand and ash etc. to form slag, which floats on top of
the molten metal. This is removed through a slag hole
below the tuyeres.
The cupola
extends above the charging door to produce a chimney
where the exhaust gases are removed and cleaned before
entering the atmosphere. The coke can be fired directly
to start the combustion process, but electricity, oil or
gas are often used with carbon being added to the
charge. |
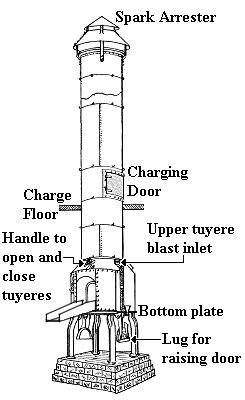
A more modern cupola. |
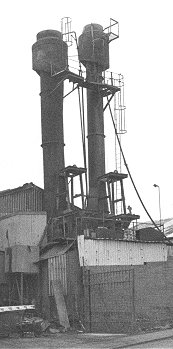
Cupolas at Hermit Industries in
Upper Gornal. |
Iron is usually
cast in sand into which an impression of the item to be
cast is made. The impression is made by a pattern, which
is produced from the original drawing and is slightly
larger than the final casting. Patterns were originally
produced in wood, with several special types being used
including jelutong from the Philippines, cherry wood,
mahogany, maple, and white pine. Pattern making is an
extremely skilful occupation; the patterns must be
precisely shaped and accurately finished.
As the molten
metal cools it shrinks, and to allow for this the
pattern must be larger than the finished product.
Pattern maker’s rules are used, which are scaled to
allow for shrinkage in various metals. Although
traditionally made of wood, many patterns today are made
in resin that is shaped on a milling machine. The
machines can be computer controlled and work directly
from the original drawing data. In the past, every
foundry had at least one pattern maker but today many
buy their patterns from specialist companies. |
If the casting is hollow, a core
is inserted in the mould to shape the interior. Cores
are made from silica sand (with a low clay content) and
held together with a bonding agent such as sodium
silicate, which can be bonded by passing carbon dioxide
through the mixture. Such a mixture is very strong and
has good dimensional stability. Cores were originally
made in a core box but today they are usually formed by
machine. The mould is made
in two halves, one forming the bottom and the other the
top. Each half consists of a box into which sand is
tightly packed around the pattern. When the pattern is
removed its impression is left in the sand and this
forms the mould. |
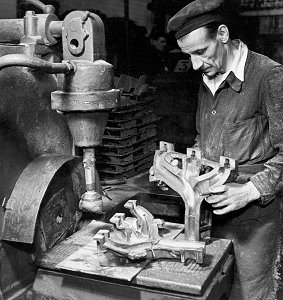
A core box and filling machine. |
Different types
of fine sand are used with chemical additives that bind
the sand together to give an accurate and detailed
impression of the pattern. The sand is recycled and soon
blackens from its contact with the molten iron.
|
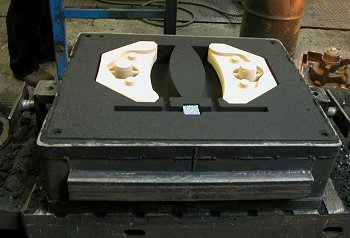
The bottom half of a moulding box
with 2 cores in place. |
When the two halves of the mould have
been prepared and any cores inserted they are fastened
together in preparation for casting.
The mould will include a network of
small flow channels that lead the metal into all of the
corners of the impression in the sand.
Provision is also made for the
escape of the hot gasses that are released when the
molten metal enters the mould. |
When the casting
has solidified and cooled it is knocked out of the mould
and taken to be dressed (cleaned up). Metal will have
solidified in the flow channels and this will be
attached to the casting and must be removed. Any
extraneous pieces are cut off and ground flat using
grinding wheels. Shot blasting can also be used to give
a clean finish. Precision castings are often accurately
machined and may be tested for unwanted cracks or flaws.
Crane Foundry
products are made of grey cast iron, in which silicon
causes the carbon to come out of the molten solution as
graphite, to leave a matrix of pure soft iron. This type
of iron produces sharp castings and has a high
resistance to corrosion and wear. It also has a good
thermal conductivity and so is ideal for saucepans and
casseroles etc. and is easy to machine. |
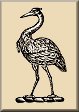 |
Return to
the
previous page |
|