The following photographs were taken on
a busy day at the foundry in July 2005. Production was
in full swing with everything operating in its normal
efficient manner. It is always an impressive sight to
see a foundry in operation and sad to think that so few
now survive in the UK.
In the distance is the
filtration equipment and chimney for the cupolas and in
the foreground is the scrap metal that forms part of the
furnace charge. |
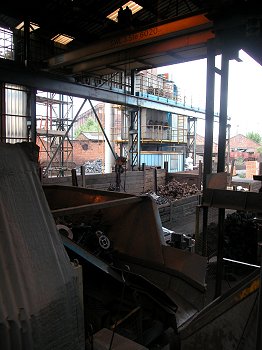 |
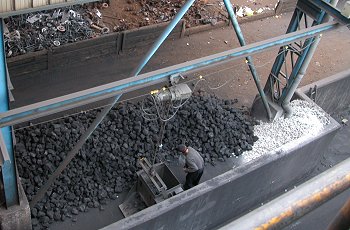 |
The raw materials - scrap
iron, coke and limestone. |
Molten iron from the cupola
flows into the electric induction furnace below. |
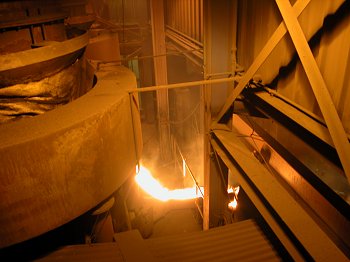 |
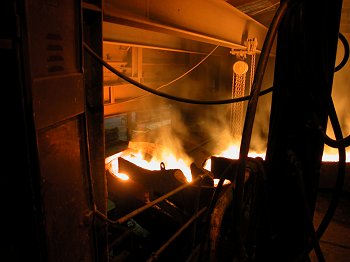 |
Another view of the flowing
iron from the cupola. |
The Birlec
electric induction melting furnace. Above is the track
that carries the large ladles that collect the molten
iron. |
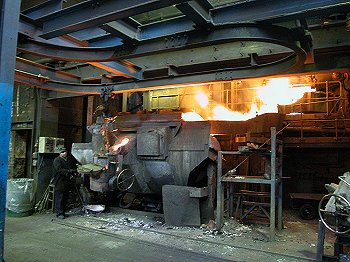 |
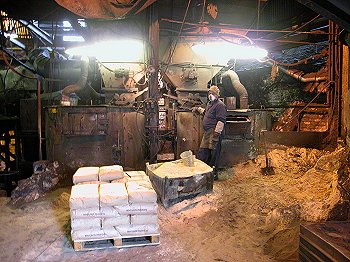 |
The two sand mixing machines. |
Finished cores awaiting
their journey into the foundry. |
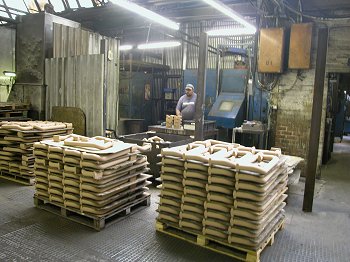 |
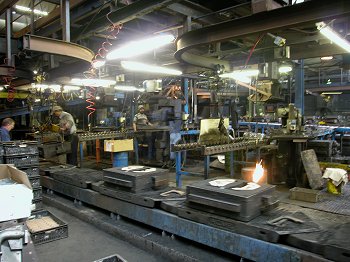 |
Manufacturing
locomotive brake blocks on the foundry's
moulding line. The bottom half of each mould is
prepared and put on the track. |
Another view of the moulding
line, where the top half of each mould is prepared in
readiness to join the completed bottom half on the
track. |
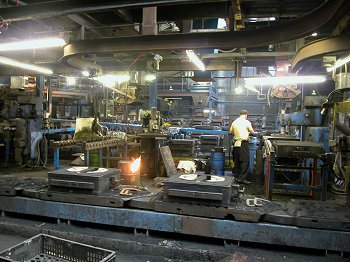 |
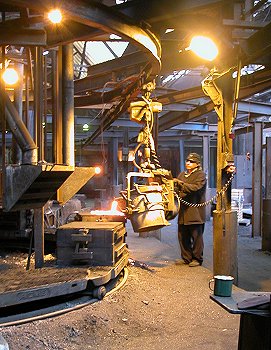 |
The two halves are joined
together and cast by hand. |
When cast, the brake blocks
cool as they travel towards a cubicle at the end of the
line, where they are removed from the mould. |
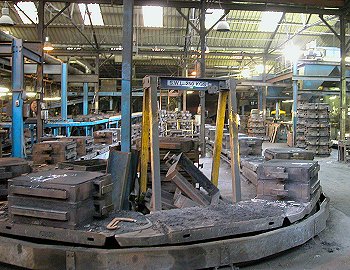 |
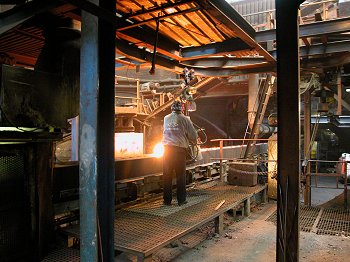 |
Casting on one of the
Disamatic machines. |
A sandblasting machine for
cleaning the castings. |
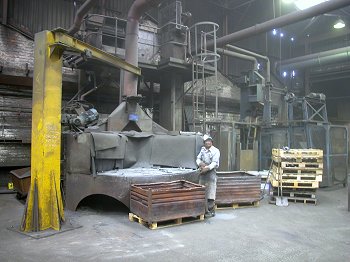 |
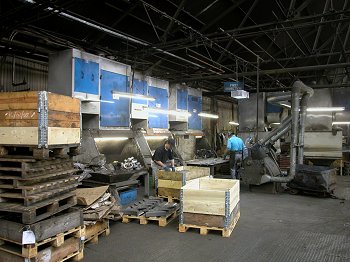 |
Grinding surplus metal
from the finished castings. |
One of the company's delivery
vehicles. |
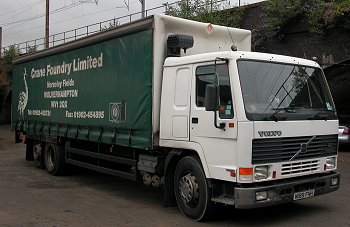 |
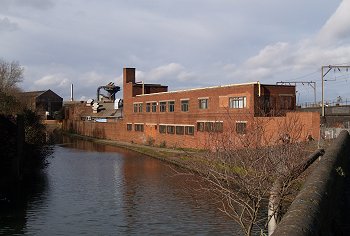 |
A view of the works alongside
the Wolverhampton canal. |
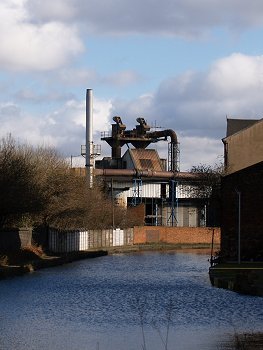
The cupolas as seen from the canal.
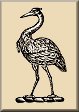 |
Return to
the
previous page |
|