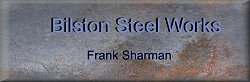
9. Elisabeth and Modernisation 1951 - 1964
The photos on this page were taken by Tim
Hadley when he was an apprentice with Stewarts and Lloyds from about
1947 onwards. They show the building of the Elisabeth furnace
and associated works.
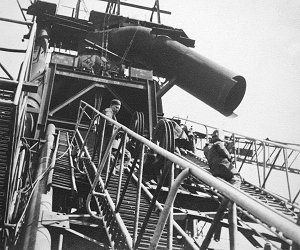
Elisabeth. |
To continue the narrative, we now revert to our anonymous source: "When the decision was taken in 1951 to build a new blast furnace,
the first in the country to be designed from the start to operate on
high‑top pressure, the modernisation of the works as a whole really
began.
Steelmaking capacity was more than trebled with vastly
improved methods of handling and with fixed furnaces capable of as
high rates of output as the quality of steel would permit." |
I take it that the furnace referred to is the
famous "Elisabeth". Mary Mills and Tracey Williams, in their "Images of England: Bilston, Tettenhall and Wednesfield", say that
it replaced three smaller blast furnaces and was first lit in 1954.
"By tradition, after relining, the furnace had to be relit by a
young girl. The only time it was lit by a man, the furnace went
out". Ron Davies, who worked for E. N. Wright Ltd., the
maintenance company, confirms this tradition and know of several
instances where attempts were made to light the furnace by a man,
all of which failed.
So this furnace was lit by Elisabeth (so spelled, with a s,
not a z), the little daughter of one of the senior managers of the
works. |
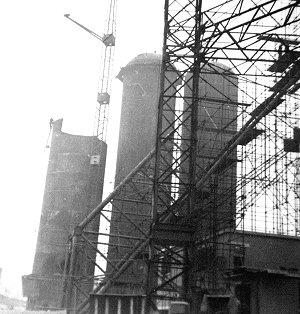
Elisabeth in the course of
construction. |
Ron Davies also recollects that, so new and innovative was the
Elisabeth furnace, that it took them two years to get it running at
its best.
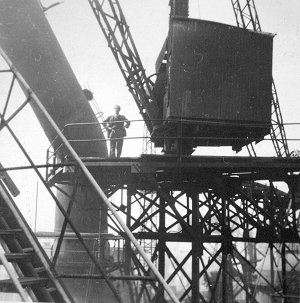
Elisabeth. |
W. K. V. Gale in his “The Black Country Iron
Industry” (The Iron and Steel Institute, London, 1966) comments on
Elisabeth and the Bilston steel works generally in 1965:
"There is now only one
blast furnace left in the area where once there were 200, but it is
a large modern one and unique in that it was the first
high‑top-pressure furnace to be built, ab initio, in Great
Britain to operate in this way.
This is the Elisabeth furnace,
built in 1954 at the Bilston Steelworks of Stewarts and Lloyds Ltd
(formerly Alfred Hickman Ltd). Of 27 ft hearth diameter, Elisabeth
provides molten iron for the steelworks, which have also been
completely rebuilt."
|
Gale continues: "The new furnace, incidentally, is far from
being the only pioneer installation at the Bilston Works. Among the
others was the Ward-Leonard-Ilgner set provided by the Electric
Construction Company when the former 36 inch mill was electrified in
1907; this was probably the first in a British steelworks.
Bilston
Steelworks now have two 1000ton inactive mixers, seven open‑hearth
furnaces of 100-120 tons capacity, a 40inch two-high reversing
blooming mill, and a 32 inch two-high reversing bar and billet mill.
A vacuum degassing plant is also installed. The principal products
of Bilston Steelworks are tube-making ingots, billets 22 to 72 inch
square, slabs 5-15 inches wide, and rounds 34 inches in diameter. All the
rolled products can be produced in finished lengths up to 30feet." |
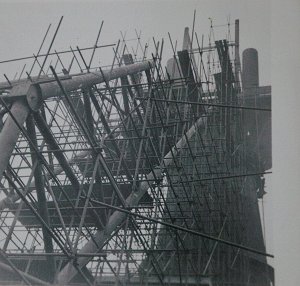
Elisabeth in the course of
construction. |
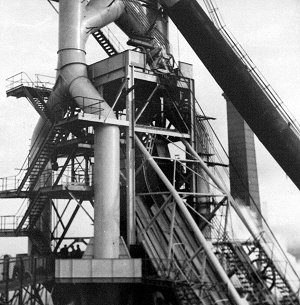
Elisabeth. |
This passage appears in a chapter ominously
entitled "Epilogue" but which does open with the words:
"It seems
that cast iron will continue to be made in the Black Country for
some time". And that was written in 1966, making no mention of the
nationalisation that was to take place that year. |
Reverting to our anonymous source: "The
completion of the modernisation programme in 1964, meant that the
plant consisted of a high‑top pressure Blast Furnace capable of
producing up to 7,000 tons of pig iron per week, using a variety of
ferrous bearing materials available in the West Midlands, as well as
the conventional iron ore burden now arriving from world wide
sources as well as the Northamptonshire deposits. |
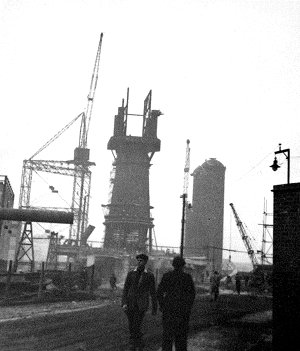
Workers leave at the end of
the day with Elisabeth, under construction, in the
background. |
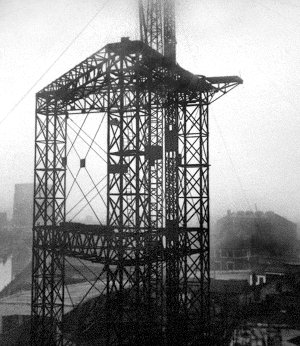
Elisabeth in the course of
construction. |
"The Melting Shop contained two 1,000 ton
inactive mixers, for storing molten pig iron. Seven all‑basic
Magnesite lined Open Hearth Furnaces, each with a capacity of 120
tons, were capable of making all the range of carbon steels,
together with a range of low alloy steels up to 4% Chromium. The
furnaces were now fired with heavy fuel oil atomised with steam;
oxygen enriched the pre-heated air, enabling them to reach
temperatures of 1660 degrees centigrade, and reducing tap-to-tap times to an average of
seven hours". |
"The addition of a Ruhrstahl Heraeus
Degassing Plant allowed for the removal of hydrogen and nitrogen
gases and, more importantly, non‑metallic inclusions.
This enabled
steel to be made to a very high standard of cleanliness". |
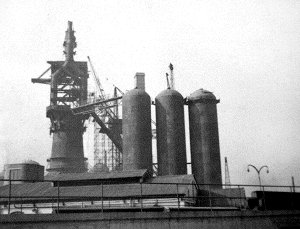
Elisabeth completed. |
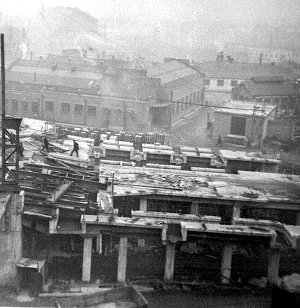
Elisabeth casting side
foundations. |
"The pit‑side had been modified to cast all
mill ingots in casting bogies, with facilities to cast forging
ingots up to 42 tons in a special bag, and Rotary Forge ingots for
tube making in the North and South Side Shops. A separate Mould
Preparation Shop had been constructed to prepare ingot moulds and
casting plates to ensure that all the steel could be bottom poured". |
"A new mill constructed by Schloemann
completed the redevelopment on the Bilston site and this enabled an
extensive range of rounds to be rolled. But blooms, billets anal
slabs could also be produced to absorb the extra production from the
steelworks, and this lead to the making of steel for engineering
uses". |
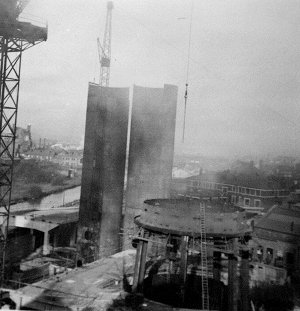
Elisabeth base and copper
stoves. |
|