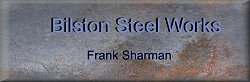
11. Nationalisation: 1966
When
Labour won the 1945 general election it was committed to a programme
of nationalising many basic industries, including iron and steel.
This proposal was hotly contested by the Conservatives who argued
that there was no point in taking over an industry that was running
profitably. The government’s first priority was nationalising coal
and they did this while trying to finalise their plans for iron and
steel nationalisation. So it as not until 1949 that they brought
forward the Iron and Steel Act. Because of delaying tactics in the
House of Lords the Iron and Steel Corporation of Great Britain did
not come into operation February 1951. It was a different form of
nationalisation from that used for coal and the railways. Instead
of acquiring the whole undertaking of the numerous iron and steel
companies, the Corporation only acquired the share capital of the
firms concerned. This gave them effective control whilst allowing
for the fact that many of the companies had many ancillary
activities outside the production of iron and steel. So Stewarts
and Lloyds became nationalised.
Almost
immediately the Labour party lost a general election and the new
Conservative government repealed the nationalisation of iron and
steel. The from that nationalisation had taken enabled them to do
this by privatising – selling off the share capital – of all the
companies they controlled. This they succeeded in doing (with the
exception of Richard Thomas and Baldwins) and Stewarts and Lloyds
re-entered the private sector. It was not until 1966, when a new
Labour government under Harold Wilson, renationalised the industry,
that Stewarts and Lloyds finally became part of a fully nationalised
industry as part of the British Steel Corporation.
Our anonymous source takes up the story again:
"Together with all other large steelworks, the
Combine was nationalised in 1966. With re‑organisation Bilston,
Wolverhampton and Birchley Works became part of Special Steels
Division, Carbon Group, of the British Steel Corporation.
"With the advent of nationalisation, the
Finishing End was increased in size to allow for bars to be
carefully cooled, straightened, shot‑blasted or peeled and then
dressed by either chipping, grinding or oxy‑propane scarfing, to
meet the high quality requirements of B.S.C. grading system.
"Most steel leaving Bilston Works was
guaranteed internally sound and therefore the ultrasonic testing of
material was carried out extensively. To increase the speed of
inspection, the Divisions Research Laboratories of Swinden at
Rotherham created a method known as M.I.D.A.S.. This was developed
at Bilston. Working on magnetic principles, any surface defect
disturbs the pattern of eddy currents, which can therefore be
detected and marked with a paint spray for subsequent dressing.
"Methods of improving production techniques
were always being sought and extensive trials were carried out with
Open Hearth Furnaces, using atomised fuel oil and oxygen. By
charging scrap at both ends and firing with both burners together,
by‑passing the re‑generator chambers, charging times are drastically
reduced and tap‑to‑tap times of three hours should be possible.
"The 14‑inch Mill at Wolverhampton Works was
extensively modified. A larger re‑heating furnace was to be
installed and the mill stands altered and re‑positioned to increase
both the product size range and its output."
At this point our
anonymous source concludes.
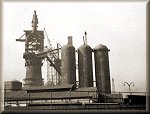 |
|
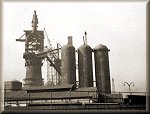 |
|
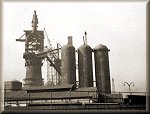 |
Return to
Photos |
|
Return to
the
beginning |
|
Proceed to
Memories |
|