At the works one gathers the impression
that success on a very large scale indeed has come somewhat unexpectedly,
for they are hard put to keep pace with the demand. There is not a square
foot of floor space to spare, not a single machine that is
not hard at work day and night, and not a man who is not
pulling his weight. There is no room for duds-mechanical or
human. Of course, with the cars being built on
such a very large scale a “flow" system of production is essential, and the
Clyno is singularly well adapted to the conditions of its
manufacture, for the design is ideal for rapid assembly.
This is apparent so soon as one enters
the works, for one can literally see the cars taking shape before one's eyes.
Almost the whole of the car is manufactured in the works at
Wolverhampton with the exception of the engine, which is made by a well-known firm of
specialists in the Midlands, and the bodies. Unlike most of the works engaged on
producing cars in very large numbers, no moving assembly
tracks or other “American" methods are adopted, although of
course a “flow" system is in force.
One is greeted at the entrance of the
works with a giant stack of chassis frames: these are taken
from the stack and first the springs, front axle and front
wheels are secured. The car is then pushed stage by stage
along the floor of the big assembly shop. The rear axle
unit, with the gearbox which has been previously assembled
in a different shop, is then run into place (with the road
wheels fixed), the engine with the clutch shaft in place
lowered on to the frame from above, the steering gear column
and connections assembled; the fitting of the radiator,
brake rods and so forth completes the assembling.
An engine being lowered onto the chassis frame
in the assembly shop.
All this happens in a remarkably short
space of time, the car finishing this first stage in its
career at the opposite end of the shop to the stack of
frames where it started. It is then turned round and the
body is dropped into place so that the car can be pushed
stage by stage to the original end of the big assembly shop
whilst the wiring up, trimming and fixing of hood and side
curtains and so forth are carried out.
The car is then turned round again and
progresses back down the shop to be elevated near the centre
on to a platform which allows mechanics to make sure that
everything is in order beneath it and that all parts needing
oil or grease are well supplied before it emerges from the
far end of the shop for a road test.
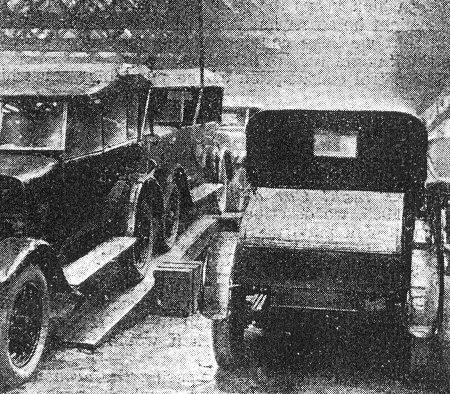
Final assembly.
The thing which impresses one
principally in the large assembly shop is the extraordinary
amount of space which so many manufacturers waste; for in
this single shop the whole of the actual building of the
cars is carried out in greater numbers and with less delay
than in many giant works equipped in a lavish manner and
planned on the most up-to-date lines. In the machine shops at the Clyno works
one observes the same unobtrusive efficiency that is
noticeable in the assembly shop, the work being carried out
very rapidly indeed and with no waste of time or material.
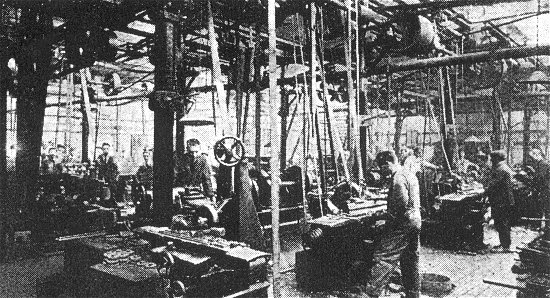
The machine shop.
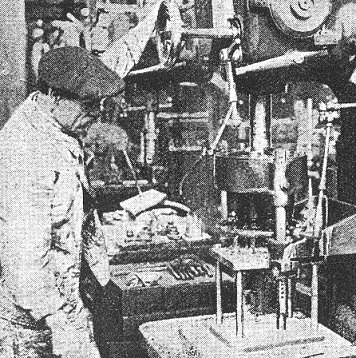
A multi-drilling machine, drilling 8 holes in one end of the axle.
A case in point is illustrated by the
accompanying photographs, which show a stub axle in the
rough and partly machined. For turning the two faces,
machining the spindle to two different diameters
and cutting the thread upon it six minutes are allowed;
actually this time allowance is on the generous side.
Another operation which typifies the efficiency of the
machine shop is the production of gearbox layshafts machined
complete from 1¾inch steel bar at the rate of four minutes
per shaft-a somewhat remarkable achievement.
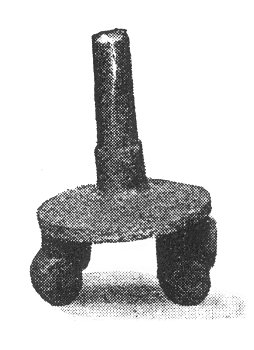 |
On the left is a
forged stub axle blank. It is shown on the right
after machining. An operation that took just 6
minutes to complete. |
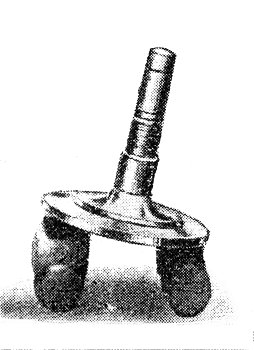 |
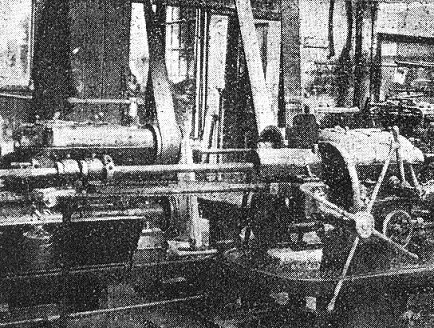
Machining a gearbox layshaft. It took
just 4 minutes.
With regard to the equipment, the Clyno
works are very well provided, the machines which are
installed being of the best, and in many cases designed
specifically for the work which they produce.
So far as the assembly of axles and
gearboxes is concerned, the gearbox of the Clyno is on the
front end of the torque tube. Little need be said except
that precision methods in the manufacture of the parts
ensure no delay in putting them together, whilst so
straightforward is the design that comparatively unskilled
labour can be employed.
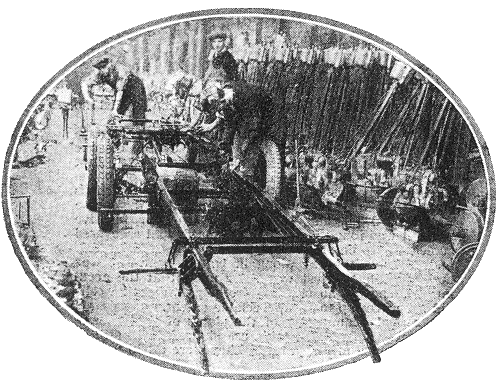
The chassis erection shop.
We understand that at the present time
there are something like a thousand men on the pay-roll at
the Clyno works, whilst, of course, many hundreds more are
busy in the production of the engines and the coachwork. The
company is a firm believer in the fact that a car to be
described as a British car must be British throughout,
therefore every detail of the Clyno is of British
manufacture.
From the Light Car and Cyclecar magazine, 12th March, 1926.
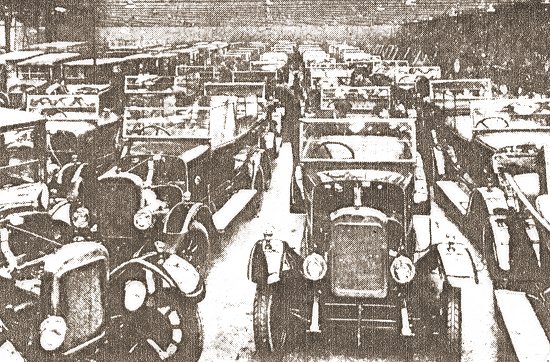
11hp. Clynos in the assembly shop. |