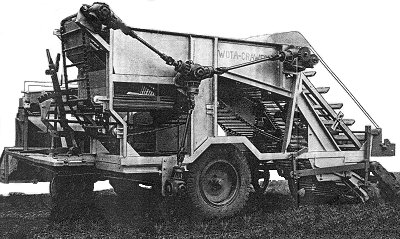
The Wota - Crawford Potato Harvester.
|
The harvester was designed to harvest the maximum
crop with the minimum amount of damage and constructed to handle
many hundreds of tons of soil, stones, potatoes and haulms every
working day.
Three acres of potatoes could be handled daily, scrubbed free
of soil, sorted and automatically bagged. Alternatively they
could be directly loaded into a cart running alongside. |