Background
It all started when Absolom
Harper and his two sons founded A. Harper & Sons,
ironfounders, at Waddams Pool Works in Hall Street,
Dudley. Absolom’s daughter Mary married George Bean,
a bank clerk who grew-up in Stamford, Lincolnshire,
where he was born in 1855. He met Mary while working
for a bank in Dudley, and soon became financial
manager of Allen, Everitt & Sons of Smethwick. After
their marriage George left his job and joined the
family business. In 1901 he became the principal
shareholder. The name was changed to A. Harper, Sons
& Bean in 1907 when George became chairman. |
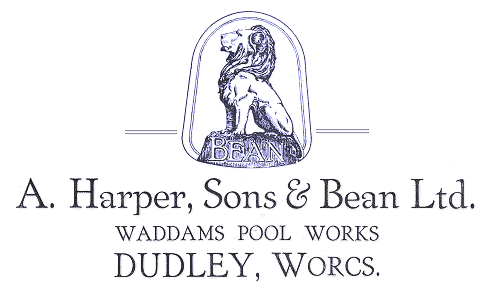
The business
greatly prospered during the First World War thanks to a
plentiful supply of ministry contracts for munitions.
The factory buildings were extended in order to increase
the production of shrapnel and shell cases. After the war George
Bean received a knighthood for his
services to the war effort, and his only son John, known
as Jack, who also worked in the business, was made a
CBE.
The Bean Car
At the end of hostilities the
lucrative munitions orders ceased and something had to
be quickly found to replace them, so that the business
could survive. At the time motor cars were becoming
increasingly popular, and so the decision was taken for
the company to become a car manufacturer. At this time the jigs, patterns,
tools, and manufacturing rights for the Perry car were
up for sale and so A. Harper, Sons & Bean purchased them
in January 1919 for £15,000 as a way of quickly getting
into the industry by buying a tried and tested design.
The company’s first car, the Bean
11.9, a slightly updated Perry design, was launched at
the 1919 Motor Show.
Harry Radford was employed as Chief Designer to oversee
the initial modifications that were made to the Perry
design, and Tom Conroy, an American production engineer
took charge of the Tipton factory. Production began in
earnest in January 1920 and soon 80 chassis were
completed each week, at a newly built factory in Tipton,
using the latest machinery and twin moving track
assembly lines. The
complete car chassis were driven
to the Waddams Pool Works in Dudley for the bodies to be
fitted.
Unfortunately sales were not good, because the vehicles were sold at
a higher price than the competition. Although prices were
slashed, the recession in the car industry in 1920
rapidly led to spiralling debts. A receiver was
appointed, and production ended at Tipton in October
1920. In November Jack Bean resigned from the company.
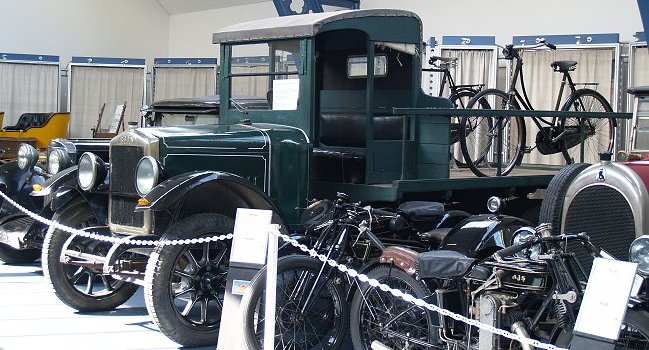
The 20/25 cwt. lorry from 1926,
that's in the collection at the Black Country Living
Museum.
Rejuvenation
During November 1921 a huge
investment of capital by Sir George Bean, Barclays Bank,
The National Provincial Bank, and Hadfields enabled them
to buy a 55% controlling interest from Harper Bean and
repay the creditors. This allowed A. Harper, Sons & Bean
to manage their own affairs again, but would have
serious financial implications five years later.
Car production started again in 1922,
and slowly increased to 100 cars a week by August. October 1923 saw the launch of a
new car, the much larger Bean 14, powered by a 13.9 hp.
engine, and fitted with a 4-speed gearbox. The engine and
gearbox would prove to be ideal for the company's
first commercial vehicles. |
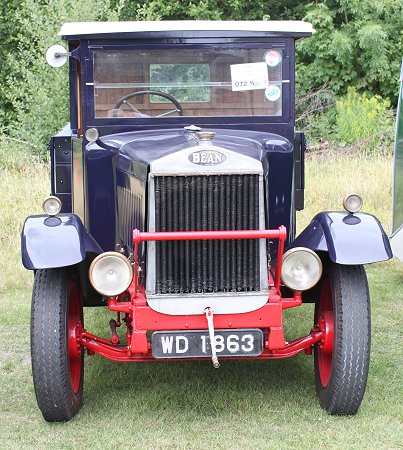
The Type 'W' 30
cwt. lorry from 1930, that belongs to Daniel
Batham and Son Limited. As seen at the Black
Country Living Museum in 2010. |
|
Commercial Vehicles In November 1924 the company
launched the first Bean commercial vehicle, a 25 cwt.
chassis based on the 13.9 hp. engine and gearbox. The
vehicles mainly appeared as lorries, but vans,
ambulances, coaches and light buses were also made.
The engine and gearbox were mounted on a separate
chassis, and initially, the vehicle only had rear wheel
brakes. The 20/25 cwt. chassis sold for £265. From 1926
front wheel brakes were available for an extra £20.
Unfortunately the company suffered
from an acute shortage of cash, with debts totalling £1.8
million, mainly due to the restructuring in November
1921. As a result Hadfields, the Sheffield steel
producer, rescued the company and renamed it Bean Cars
Limited, in June 1926.
In June 1927 the chassis was replaced by a 30 cwt.
model designed by Hugh Kerr Thomas. It had a 2.3 litre
Ricardo high turbulence cylinder head engine, and sold
for £325. By this time the commercial chassis accounted
for about 60% of the total production at Tipton. |
The 30 cwt. chassis continued in production until
1929 when it was replaced by the 'Empire' model, powered
by a 3.6 litre Ricardo high turbulence cylinder head
engine.
It only remained in production for about 18 months,
when it was replaced by an updated version of the
original 20/25 cwt. chassis, powered by a 2.3 litre
Hadfield engine.
The new chassis was only manufactured for just over
three months, because Bean Cars Limited went into
receivership on the 19th June, 1931, when vehicle
production ended. The cars had not been selling well,
and soon gained a bad reputation as a result of many
problems with the company's latest model, the 14/45.
|
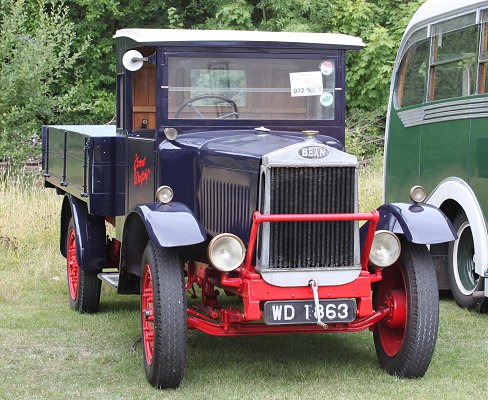
Another view of Batham's Bean
lorry. |
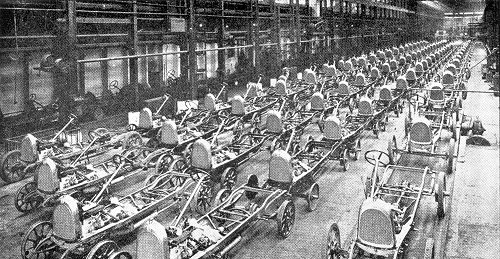
The Tipton factory in 1925.
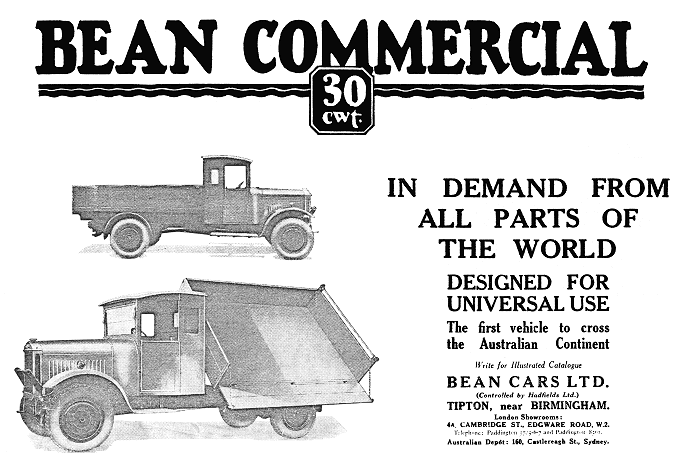
An advert from The Times Trade &
Engineering Supplement, 25th May, 1929.
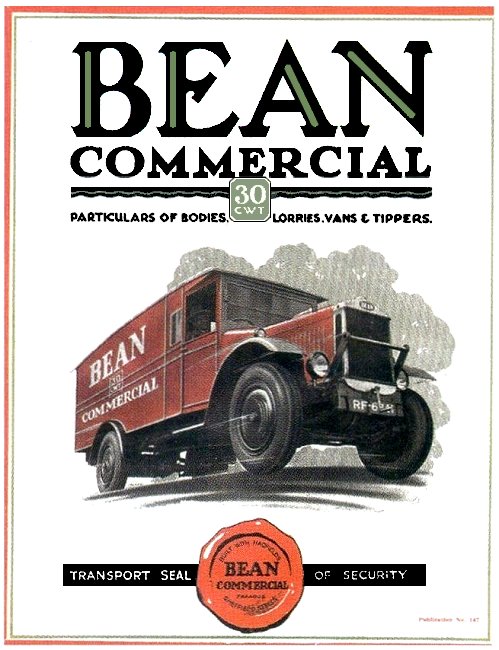
Later Years
A new chapter started in
November 1933 when Hadfields re-launched the
business as Beans Industries. The new company would
produce castings for the motor industry, and soon
became profitable again. In 1937 Beans Industries became a public
company.
During World War 2 the company
produced lorry engines and parts for army trucks. In
1956 the company was taken over by Standard-Triumph to
produce castings for their vehicles, and in 1960 became
part of British Leyland, producing castings for their
lorries and coaches. In 1975 it became known as Beans
Engineering.
In 1988 when the Leyland group was
privatised and broken-up by the Conservative Government,
Beans Engineering was acquired by its management team,
and after the buyout it acquired Reliant. Things went on
much as before until Reliant failed in 1995 and took
Beans into receivership.
The Tipton factory was purchased by
the German engineering group Eisenwerk Bruhl who made a
large investment at the works, where 40,000 tons of
cylinder blocks could be produced each year. The
business became known as Bruhl UK but suffered from
financial problems because the large investment had left
the company in debt. For a second time the management
team purchased the business which then became Ferrotech.
The factory had one of the most modern and efficient
foundries in Europe and became a large supplier of
castings to Rover. Unfortunately Rover went into
administration in 2005, and Ferrotech failed to find a
replacement customer. As a result the story ends in
September 2005 when Ferrotech closed its doors for the last
time.
|
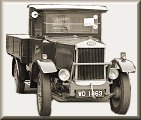 |
Return to
the list
of manufacturers |
|