Details of the lorry and engine are as follows:
The Guy two ton lorry chassis fitted with
Tulloch-Reading gas producer plant follows the accepted practice for
petrol-driven vehicles, and is identical with the firm's petrol two
ton lorry except in regard to the producer and fittings incidental
thereto, that the engine is, with the except of details mentioned
later, the same as that fitted to the three ton lorry.
[Then follows a description of chassis, etc.,
which is of orthodox type. - Ed. "A.M."]
5. Description of the
Tulloch-Reading Producer Gas Equipment
The following is a description of the
Tulloch-Reading producer gas plant:
No Interference with Load
The fuel is carried in a hopper incorporated in
the structure of the canopy, whilst the gas cleansing plant is
carried well out of the way, the scrubbers at the rear end of the
chassis and a centrifugal dust extractor under the off-side of the
body, behind the driver's cab. The blower is mounted just forward of
the dashboard, on the near side, where it is convenient to operate,
but does not interfere with engine accessibility. The whole of the
body space is therefore available for the load, and, whilst all
parts of the producer plant are easily reached, the accessibility of
the engine and transmission does not appear to have suffered.
A Large Fuel Valve
The fuel is fed by gravity from the hopper into
a bunker above the valve. The latter contains a hollow plug (or
barrel), which is slowly rotated by ratchet gear, so that an
aperture on the side periodically comes uppermost, and the barrel is
filled. Further rotation brings the aperture to the bottom,
releasing the fuel down a vertical chute to the fire chamber. When
the aperture is closing at the top the sharp edges cut through any
pieces of fuel that may be caught. The barrel is tapered and held on
its seating by a simple hinged spring clamp released by withdrawing
a cotter pin. The smaller end of the barrel is slotted to engage
with the driving member, worked by the ratchet gear; it is thus only
necessary to release the retaining spring to extract it.
A neat device is incorporated in the ratchet
gear that works the fuel valve. The pawl is retained in engagement
by a spring, which is utilised also to keep it out of engagement
when raised; thus, when approaching the end of a journey, the driver
has only a raise the pawl, when the fuel supply ceases, and he runs
home on that already in the generator. By experience the driver can
gauge fairly accurately when to shut off the fuel.
Actuating Mechanism
A distinctive feature of the Tulloch-Reading
Guy system is that the fuel regulating valves, the rocking camshaft,
which continually agitates the fire bars, and the water pump are all
continually worked from the engine by a very simple mechanism. A
small housing at the rear end of the engine crankcase contains a
worm wheel with which is engaged a worm on the end of the camshaft,
the gear reduction being 80 to 1. On the worm wheel shaft is a crank
connected by a rod to a lever fitted to a short horizontal shaft
mounted below the driver's seat, and to the right of the generator.
Rotation of the crank causes the shaft to rock, and, by a second
lever on the shaft, the motion is transmitted for working the fuel
valve and fire bar camshaft.
Water Supply to Vaporiser
Hand mechanism is provided for working the pump
independently temporarily to increase the water supply when
required. The pump delivers into a glass sight-feed vessel, which
may be placed in any position that enables the driver to see if the
pump is working properly. The outlet from the vessel is fitted with
a jet having a restricted orifice, so that the water is supplied to
the vaporiser at a slight pressure, and in a constant stream. The
water from the main supply tank does not pass through the pump, but
through a filter and ball valve into a chamber, from which
connection is made both to the pump and the sight feed vessel. As
the capacity of the pipe leading from this chamber to the pump is
greater than the quantity displaced at each pump stroke, a clean
water delivery is maintained, for the water in the pump, unavoidably
contaminated with oil, merely surges to and fro in the pipe,
propelling the clean water that passes through the filter and ball
valve. Thus the sight feed vessel inlets and outlets are kept clean.
Thermostatic Air and Steam Control
The function of the vaporiser is to supply hot
air and steam to the underside of the fire. Automatic regulation of
the air and steam supply is obtained by a thermostatic device. A
length of copper strip within the air and steam supply pipe has its
ends so secured that it is slightly buckled. From the centre of the
strip connection is made to a short arm of a bell crank lever, and
to the end of a long arm is connected a vertical rod, the upper end
of which bears against the underside of a hinged lid, closing an
outlet at the upper end of the pipe to the atmosphere. Thus when the
temperature within the pipe rises above a certain limit, the copper
strip expands, and, through the medium of the bell crank and
vertical rod, lifts the hinged lid and admits cold air. The length
of the rod is adjustable, so that the point at which the lid opens
can be advanced or delayed, whilst the position of the rod in
relation to the hinge can also be adjusted to vary the degree of
opening. The thermostatic device can, therefore, be set to suit any
working conditions.
Petrol is used for starting up, and an
ingenious type of valve is fitted to the intake pipe to control the
admission of petrol or producer gas mixtures either separately or
together. The valve is of the tapered barrel type, held on its
seating by hinged spring clamps, like that used for the fuel control
valve, so that jamming is prevented. The barrel is formed with a
passage, which, in the vertical position, is a continuation of the
intake pipe, though sealing the petrol mixture pipe from the
carburettor. One side of this passage, however, is cut away, so that
when the barrel is turned to cut off the producer gas, petrol
mixture can be drawn into the engine. Within the barrel is an
ordinary butterfly valve mounted on a spindle, with level so
interconnected with the carburettor butterfly valve that both are
controlled by the same accelerator pedals. Movements of the barrel
do not affect the butterfly valve inside, consequently the producer
gas or petrol mixture control is independent from the accelerator
pedal control, which regulates only the quantity of either mixture
supplied to the engine.
The gas, after leaving the furnace, passes to a
cyclone scrubber, where most of the dust is deposited, and thence
through a light gauge drawn-steel pipeline, zinc treated, to a
series of four tubular sheet steel scrubbers situated transversely
at the rear of the chassis. These scrubbers, which are provided with
easily detachable ends, are divided by baffle plates into
compartments, which are filled with wood wool. From the scrubbers
the gas passes to the special conical valve (referred to in the
previous paragraph), placed between the carburettor and inlet
manifold, which admits the fuel air mixture and controls the ratio
of the gas-air to petrol-air mixture.
The engine is started on petrol, and changed
over as soon as the gas generated in the producer is of the required
value.
6. Tests
In May, 1928, one of these vehicles was made
available to the producer gas sub-committee by Messrs. Guy Motors
Ltd. for observation and test.
The lorry was operated under service conditions
by the Postmaster General's Department, and, during the month, a
total distance of 842 miles was travelled, using 2023 lb. of
charcoal, 35 gallons of water, and 12 gallons of petrol. This
represents a consumption of 2.4 lb. of charcoal per mile; but, as a
considerable amount of time was spent in idling and empty running in
the city and suburbs, this cannot be regarded as an average
consumption for the vehicle when operating on the type of transport
for which it is most suitable.
A good indication of the performance is given
by a trip to Mt. Dandenong on June 20, when members of the
sub-committee travelled with the lorry in order to observe its
behaviour.
The lorry was loaded with scrap iron, and,
including passengers, the total load was 2 tons 11 cwt. The tare of
the lorry being 3 tons 3 cwt., the gross load was 5 tons 14 cwt.
From the Postal Garage to the Fiveways, Mt. Dandenong North, a
distance of 26.5 miles, the total rise is 1,460 feet. This distance
was travelled in 2 hours and 18 minutes, the average speed being
11.5 miles per hour, and the amount of charcoal consumed 81 lb. The
return trip was made in 1 hour 37 minutes, at an average speed of
15.9 miles per hour, and for a fuel consumption of 71.5 lb. of
charcoal. The average speed over all was 13.5 miles per hour, and
the amount of fuel used was 152.5 lb. of charcoal, two gallons 'of
water, and a quarter of a gallon of petrol was used for starting
purposes only.
This represents a fuel consumption of 1.13 lb.
of charcoal per net ton mile, and a consumption of 0.13 lb. of water
per lb. of charcoal.
The hill at the end of the run has a length of
3.4 miles and an average grade of 1 in 22.4 (maximum, 1 in 20), and
the average speed in third gear at this point was 7 miles per hour,
with a maximum speed on a 1 in 20 grade of 7.6 miles per hour.
Assuming 56 lb. per ton as the resistance to
motion, the horse power required to maintain this performance would
be 19.4. If the losses in the gearbox, etc., be assumed as 6
percent., the brake horse power of the engine would then be 20.6.
Considering the large amount of climbing
encountered on the journey, the machine can be regarded as having
performed very satisfactorily.
The following table gives a summary of some
individual results obtained by the sub-committee with a two-ton Guy
lorry while under trial for one month:
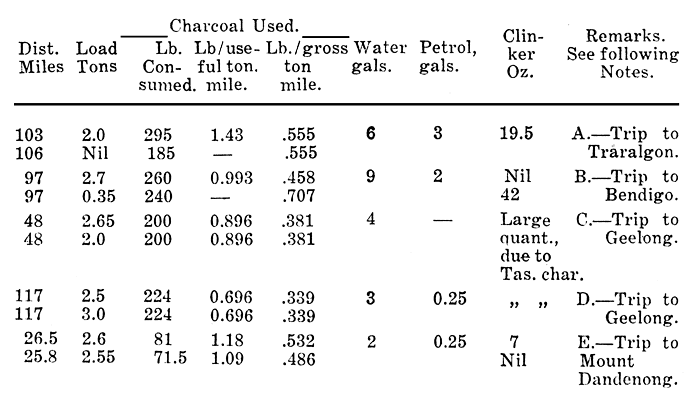
Remarks:
A. Trip to Traralgon, May, 1928
During this run demonstrations of the machine
were given at all towns en route to Traralgon; this caused a larger
petrol consumption than normal, due to frequent starting of the
engine.
Of the 480 lb. of charcoal used on the whole
trip of 209 miles, 420 lb. was obtained from Queensland, and 60 lb.
was English charcoal (believed to have been made from W.A. kauri
timber), which had been supplied with the vehicle.
The Queensland charcoal had been obtained from
iron bark timber at Darra. It was ordinary commercial ungraded
charcoal, the analysis of which had revealed 3.5 percent of ash
containing a large percentage of calcium carbonate, which it was
considered would, to a large extent, prevent the fusion of the ash
and modify difficulties due to clinkering. Clinker formed during the
run, however, amounted to 19.5 oz., possibly due to the presence of
foreign matter in the charcoal. No operating trouble was experienced
with the clinker owing to the action of the rocking grate, which
prevented the clinker from clogging up the firebars.
During the run two fuel blockages were caused
by large lumps of charcoal choking the lead from the hopper to the
fuel valve. Otherwise no fault was found with the running of the
machine.
B. Trip to Bendigo, May, 1928
Demonstrations during the run again accounted
for a higher petrol consumption than would otherwise have occurred.
On the outwards run 260 lb. of Western
Australian pit-burnt Jarrah charcoal, obtained from Chidlow, near
Perth, was consumed. No clinker was formed with this charcoal, the
analysis of which gave an ash residue of 0.12 percent, having an
alkalinity of 5 percent of the ash content, calculated as potassium
carbonate, K2CO3.
On the return journey, 240 lb. of Victorian
grey box charcoal, obtained at Bendigo, was used. On arrival at
Melbourne, it was found that 42 oz. of soft clinker had formed in
the furnace of the producer.
C. Trip to Geelong, June 12, 1928
Tasmanian charcoal, obtained from blue gum
timber, at Neika, near Hobart, was used on this trip. The fuel
contained a considerable amount of incompletely charred wood, which
the rotary feed valve was unable to shear through; this caused
stoppages and loss of time, especially on the return journey.
The fuel also proved to contain a considerable
amount of foreign matter and as a result large quantities of clinker
were formed, but trouble was averted by the rocking action of the
grate.
An analysis of this charcoal gave an ash
residue of 0.32 percent, having an alkalinity of 28 percent of the
ash content calculated as potassium carbonate, K2CO3.
D. Trip to Geelong, June 15, 1928
On this trip Tasmanian charcoal was again used,
and, as in the previous trip, large quantities of clinker were
formed, without serious detriment to the operating efficiency of the
plant.
On the return journey the vehicle, although
operating on defective fuel, satisfactorily carried 50 percent,
excess of its classified load capacity.
The greater mileage of the total trip was due
to the vehicle being diverted from the direct route in order to
deliver stores at another depot.
E. Trip to Mount Dandenong, June 20, 1928
On the trip to Mount Dandenong, previously
referred to, the fuel used on the outwards run was retorted charcoal
obtained from Mr. Holmquist, at Gisborne, Victoria, and that used on
the return journey was charcoal imported to Australia with the
vehicle, and believed to have been made from Western Australian
kauri timber.
On December 11, 1928, a second run to Mount
Dandenong was observed by the sub-committee in order to test the
effect of certain minor alterations, which had been made by the
makers. The engine started easily from cold, and changed over to gas
eight minutes after starting to prepare the fire. The lorry behaved
very well, and made a more satisfactory showing than on the previous
occasion. Its performance on the long hill at the end, obtained from
the two tests:
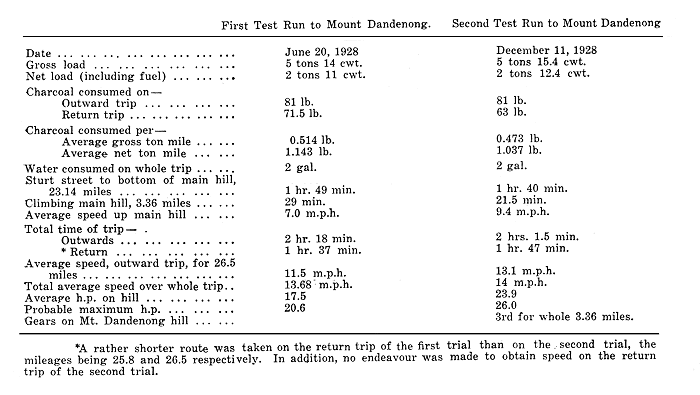
7. Operation Under Service Conditions
In May, 1929, the vehicle was taken over by the
Postmaster-General's Department (Transport Section), and has since
formed one of the regular units of the Melbourne fleet.
During the period from June 17 to November 15,
1929, the lorry ran 1943 miles, being chiefly used for city and
suburban work, carrying heavy engineering stores. At times fairly
long periods of waiting were involved at wharves or store yards, and
during these times the fire was necessarily kept alight, with the
result that the fuel consumption per mile was heavier than would
have been the case on long runs.
The lorry has given satisfactory service in
spite of the fact that producer gas vehicles are more suited to
long, continuous hauls than to short runs in heavy traffic. In
traffic it is difficult to distinguish the performance of this
vehicle from that of a petrol-engined lorry, except for the fact
that the idling speed on producer gas is somewhat high.
During one period of service, a test was made
of "carbonite" (pelleted charcoal), instead of the ordinary
commercial charcoal, but it was found that these very hard pellets
were liable to stop the rotation of the rotary fuel admission valve.
It was also found that in using carbonite, very bad clinker was
formed on the grate, which was exceedingly difficult to chip off
wh2n cold. While this form of charcoal may give excellent results in
down-draught producers, and is in many ways preferable to ordinary
charcoal owing to its greater cleanliness and decreased bulk, it is
not suitable for producer plants of the updraught type, such as the
Tulloch-Reading.
At another period considerable trouble was
experienced through the fuel containing incompletely charred wood,
which caused the rotary feed valve to jamb. Trouble was also
experienced owing to badly graded charcoal causing blockage in the
feed pipe.
In the following table, a summary is given of
the results obtained with the lorry during the period under review:
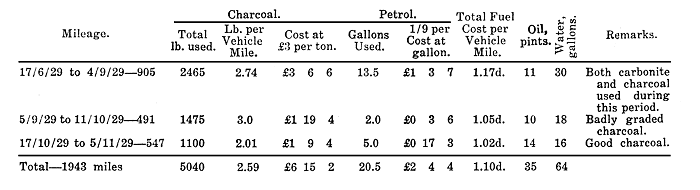
In the above table the price of charcoal has
been taken at £3 per ton, this figure being based on quotations and
estimates obtained from recognised charcoal suppliers.
It is clear that the relative economy of
producer gas vehicles compared with petrol vehicles depends largely
upon the price of charcoal. This aspect of the investigation will be
fully dealt with in the sub-committee's fourth interim report, which
will be submitted shortly.
It is estimated that the fuel consumption of a
petrol-driven vehicle doing similar work would be 7 mpg., which, at
1/9 per gallon, gives a fuel cost of 3d. per mile. It may,
therefore, be concluded that the fuel costs for the Guy lorry,
equipped with a producer gas plant, are approximately one-third of
those of a petrol lorry of similar capacity.
The time required to prepare the vehicle for
the road, including cleaning the scrubbers and lighting the
generator, is approximately 30 minutes, compared with an average
time of 20 minutes for a similar capacity petrol vehicle.
8. Maintenance, Repairs and Depreciation
On January 10, 1930, the cylinder heads were
removed, and an examination made of the cylinders and valves. The
deposit on the cylinder heads and valves was light, dry and brittle.
The deposit was not excessive, and did not exceed that to be
expected in an average good petrol lorry engine operated for a
similar period.
A sample of the deposit was submitted to the
Commonwealth Analyst, who reported upon its analysis as follows:
The low percentage of silicious mineral matter
indicates that the scrubbing apparatus was operating efficiently.
The amount of iron present in the ash is normal to a new engine that
is being run in.
Taken on the whole, the sample of deposit could
be regarded as comparable with that in a good average petrol engine
operated under similar conditions.
The pistons were not withdrawn, but very little
movement could be detected by rocking them; variation in the bore of
the cylinders did not exceed two-thousandths of one inch, indicating
that there had been very little, if any, wear in this direction. The
exhaust valves were of a decided red colour, and the inlet valves
the usual grey colour.
Generally speaking, the examination of the
engine failed to disclose any variation in condition other than
would be expected from the examination of a good type of petrol
engine operated for a like period and under similar conditions.
The Tulloch-Reading producer gas equipment was
not dismantled, but a general inspection of the plant revealed no
undue wear or need for repair.
Minor repairs carried out from time to time
since the lorry entered the service of the Postmaster-General's
Department did not include any part of the producer gas plant, with
the exception of the conical change-over valve, which was not
gastight, and was reground.
In consideration of these facts, it appears
that the maintenance charges are not likely to be heavier than with
a similar type of petrol lorry.
9. Charcoal
The sub-committee desires to lay particular
emphasis upon the importance of the charcoal being retort burnt, and
absolutely free from earth, stone or any other foreign matter. The
introduction of only a very small amount of this foreign matter is
likely to cause trouble from clinker formation, and although the
rocking grate of the Tulloch-Reading producer gas plant tends to
prevent the clinker adhering to the firebars, the presence of
clinker must detract from the efficiency of the plant. It is,
therefore, recommended that charcoal for producer gas motor vehicles
should be procured from timber entirely free from earthy or other
foreign matter, and that great care should be exercised in the
bagging of the charcoal to avoid the inclusion of this foreign
matter at that stage of charcoal production.
10. Conclusions
The sub-committee is of opinion that the Guy
motor vehicle, equipped with a Tulloch-Reading producer gas plant,
as tested, is an effective producer gas motor vehicle, capable of
economical operation, provided the added first cost of the complete
vehicle does not counteract the economy which undoubtedly can be
effected in fuel costs.
Owing to the fact that the vehicle has only
been operated under producer gas for a total distance of about 2,785
miles, it is not possible for the sub-committee to express an
authoritative opinion regarding depreciation of the producer gas
equipment; this can only be determined after prolonged use. It is,
however, an important aspect of the economic use of producer gas
plants for the propulsion of motor vehicles in Australia. The
sub-committee strongly recommends that the vehicle now under review
be used continuously as a producer gas motor vehicle, and its
performance closely watched by the Postal Department, so that a true
record of its durability and life can be obtained.
The sub-committee also recommends that, if
possible, the vehicle be used on long-distance work for the
department, so that it may be utilised under conditions most suited
to the use of producer gas, and obtain as big a mileage aggregate as
possible in the shortest time.
As a result of trials carried out with the Guy
lorry equipped with a Tulloch-Reading producer gas plant, the
sub-committee considers that the use of producer gas obtained from
Australian charcoal does offer an economic and effective alternative
fuel to petrol for commercial motor vehicles more especially in
those parts of the country far removed from the seaboard, where
imported liquid fuels are dear, but where waste wood for the
production of charcoal may be plentiful and cheap.
This class of vehicle also offers attractions
to farmers, who, by the expenditure of a small outlay on equipment,
should be in a position to supply their own retorted fuel for their
motor lorries.
11. Acknowledgments
The sub-committee desires to place on record
its appreciation for the cooperative assistance rendered by the
Postmaster-General's Department in keeping the sub-committee
informed regarding the performance of the Guy lorry and facilitating
observation of its operation when necessary.
The sub-committee also desires to refer
appreciatively to the keen interest taken in the investigations by
Mr. C. Florant, the driver of the vehicle, whose careful observation
of the performance of the lorry has been of material assistance.
The Producer Gas Sub-committee of the
Committee on Mechanical Transport:
Edward J. C. Rennie, Chairman
G. Baghel, Member.
C. K. Bromell, Member.
G. A. Cook, Member.
A. E. Dawkins, Member.
C. J. Kirkbride, Member.
Thomas E. Moorhouse, Secretary.
February 12th, 1930. |