JOSIAH PARKES & SONS LTD. UNION WORKS, WILLENHALL
Greatly extended by Bev ParkerThe Parkes family were originally from Gornal. The
eldest brothers, William (born 1822) and Richard both served
apprenticeships as locksmiths in Willenhall. Josiah Parkes (born
1824) was apprenticed to Hickman’s Iron Works in Bilston.
It seems that the three brothers set up in the
ironmongery trade about 1840 in premises at 28, 29 and 30 Doctor’s
Piece. It seems that Josiah continued to work at Hickman’s, only
helping the firm in the evenings.
The trade done in those days
was considerable, as iron at the time was the material most commonly
used by lock and key makers throughout the land. The business grew
in volume and scope and new premises were taken in Union Street.
Old catalogues show that merchanting was done in iron and a great
variety of general goods, from mole traps to clothes' horses, from ash
pans to carpenters’ tool baskets .... and locks.
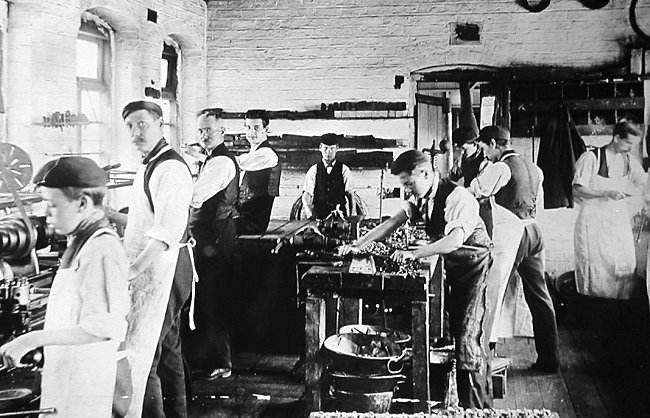
An early photograph inside the
factory. |
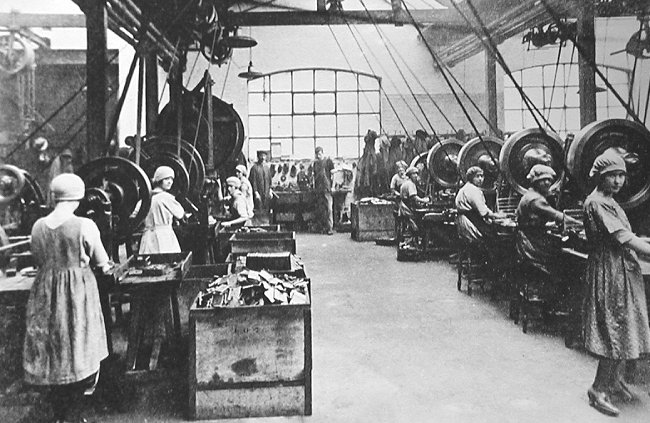
Another early photograph. |
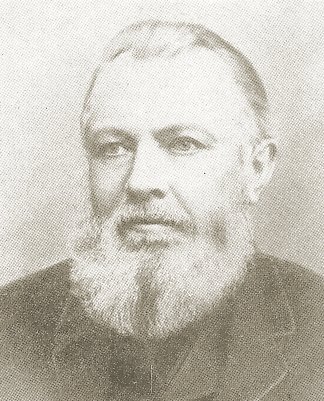
Josiah Parkes, 1823 - 1899. |
Richard did not stay with the firm but it is not known
when he left. William had an ironmongery business at 9 Union
Street. About 1850 Josiah and his wife, Catherine, moved to
premises at 3, Union Street and Josiah began working full-time with
Richard in the ironmongers.
By 1851 William and Josiah were in partnership and were advertising in
the local papers and trade journals as William and Josiah Parkes, Iron, Steel and Wire Merchants, Union Street. The partnership made
locks and other hardware but they also traded in those goods, acting as
factors. They would supply the raw materials to other locksmiths
and buy back the finished products from them, selling them on to
wholesalers and retailers. The brothers were obviously successful in this trade and in the
1850s were able to take on three apprentices. More tellingly they
acquired new premises in Union Street in 1852 and opposite in Wood
Street in 1883. |
In the 1860s the Parkes brothers began to concentrate more on
manufacturing and merchanting locks. An advertisement in the
Wolverhampton Guide of 1864 described them as "general merchants and
manufacturers of all kinds of rim, mortice, pad locks, bolts and
latches".
In 1861 the brothers were able to move their families to
better premises. William and his wife, Elizabeth, and
their four children, moved to 78 Union Street. Josiah
and his wife and five children moved to 77 Union St. The iron
warehouse and shop lay between the two houses.
The original business was dissolved in 1868 when his
son, William Edmund, joined Josiah. In 1885 James Harry, another
son of Josiah, joined the firm, when it became Josiah Parkes and Sons.
|
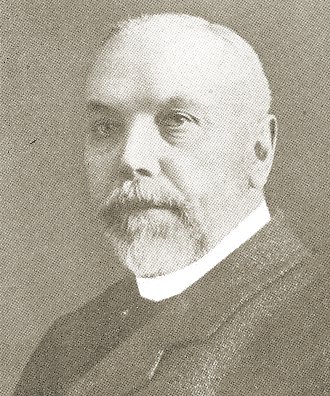
William Edmund Parkes, 1855-1920. |
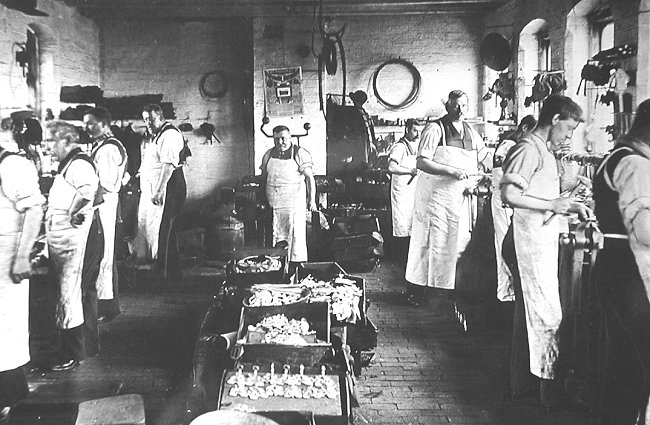
Locksmiths hard at work. |
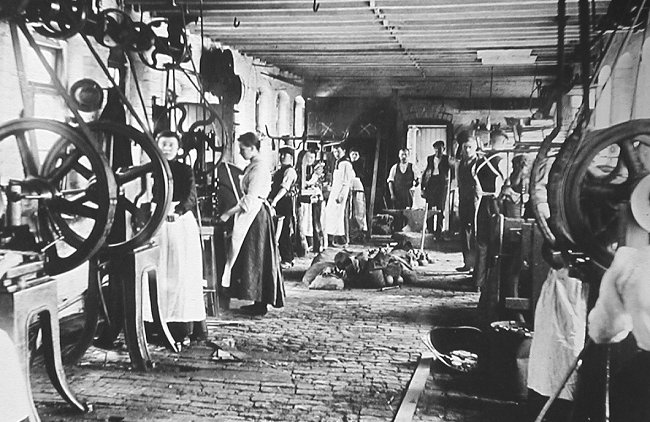
Making the parts. |
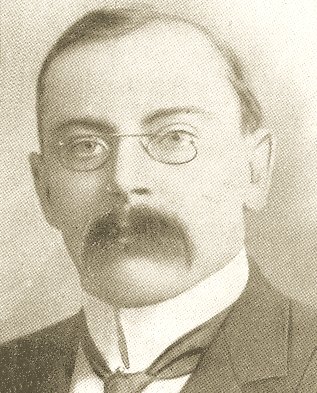
James Harry Parkes, 1867-1914. |
As the business grew the Parkes children came into the
Company. William had three sons: Samuel, Josiah and William Fletcher,
who all joined as iron merchants clerks. Josiah Parkes had five
sons, who were all younger than their cousins. Friction developed
between the two families about who was going to control the business. To resolve the problem William and Josiah dissolved the partnership
around 1873 and set up two separate businesses. William and his
sons became Parkes, Parkes and Company, but soon both Samuel and Josiah
started other businesses, Samuel as a hardware merchant in New Road and
Josiah as a brass founder in Wood Street.
Josiah set up a company with one of his sons, William Edmund
(1855-1920), trading as iron merchants and hardware factors. They moved
into 28 Doctor’s Piece. William Edmund concentrated on the hardware
section and Josiah looked after the iron merchanting. By 1880
business was doing well enough for them to employ three men and expand
the premises to 18, 29 & 30 Doctor’s Piece. |
Advertisements from
1884 refer to Josiah Parkes and Sons as "bolt, nut, screw, hinge, latch
and lock furniture manufacturers". Josiah Parkes Junior and John Parkes
both joined the firm. In 1887 Josiah Parkes Senior retired (Josiah died, aged 76, in August
1899 and was buried in the churchyard at Little London Baptist Church)
and in January 1888 a new partnership under the same name was
established between William Edmund, John and James Harry Parkes. Josiah
Parkes Jnr did not join this firm but carried on the iron merchanting
business by himself. The youngest son, Ebeneezer Thomas decided to go
into a career in banking. In 1889 the other brothers
decided to concentrate their firm’s attention on the manufacture
of locks and gradually ceased trading in iron and other goods. When more
factories for lock making appeared, as the lock industry grew in size
and importance, Josiah Parkes and his sons recognised the trend,
discontinued iron trading in 1896 and took up the manufacture of locks. The enterprise began in quite a small way and gathered pace in later
years. |
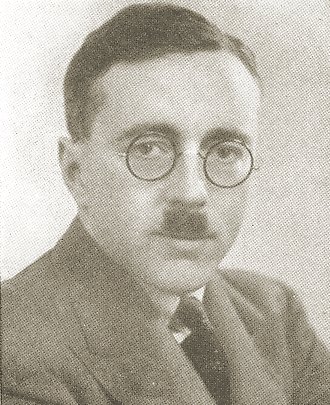
Harry George Parkes, 1896-1946. |
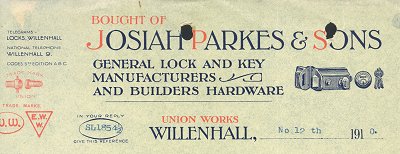 |
A letterhead from 1910,
showing three trade marks and still claiming to be in builders'
hardware. |
On their first products that they manufactured, the company stamped
the image of a hose coupling - a product that they also made - and
this image became the trade mark of Josiah Parkes even when they stopped
hardware trading. There was a lot of foreign competition in hardware goods
and iron products in the 1880s and 1890s. Despite this Josiah Parkes and
Sons were successful and they provided goods to shops and businesses all
over the country. But the Union Street business of Parkes, Parkes
& Co. faded out, as did the Samuel Parkes’ business. Josiah Parkes
and Sons were able to buy the old Union Street property and sold
the Doctor’s Piece property in 1890.
|
The 1910 letterhead above
shows three trade marks: the hose coupling; WW in an oval; and
EWW in a triangle. The hose coupling was their main mark in
their earlier days, reflecting their early trade in hardware.
The entry from a trade mark listing
(supplied by Trevor Dowson) also shows two versions of the word
"union", which became their usual trade mark.
|
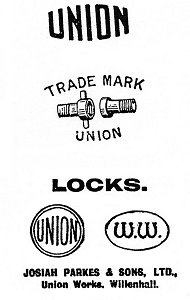 |
William Cyril Parkes, elder son of William Edmund Parkes, joined the
family business in 1903. In 1911 Harry George Parkes, son of James
Henry Parkes, joined the firm, and his younger brother, Arthur Joseph, joined in
1919. James Harry Parkes died in 1914.
In 1906 their employees totalled 35 but by 1913 they had
increased to 100. (In 1934 there were 550, the 1948 figure was
900, in 1958 it had reached 1300 and by 1971 it was over 1800, despite
increase mechanisation.)
|
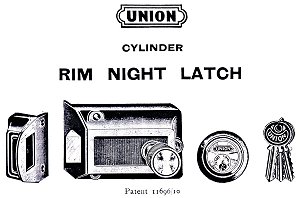 |
An important step was taken in 1911 company began the manufacture of
cylinder locks and latches started. At the time comparatively few
were being made in this country. |
In 1913 the company was able to expand and build a new
lock shop adjoining the original Union Street premises.
Just prior to the First World War the locksmiths union
had managed to establish itself and in negotiations with the Lock
Manufacturers Association (of which Josiah Parkes were members) had set
new wage levels:
Boys aged 16-17
3d per hour
Boys aged 17-18
4d per hour
Boys aged 18-19
5d per hour
Boys aged 19-21
6d per hour
Over 21
7d per hour
At the beginning of the war trade was depressed due to
few government contracts and the decrease in exports. But in due course
the factory was turned over to the production of a wide range of munitions
including grenades, shell fuses, bomb detonators, shrapnel tubes, rifle
rods, strombus horns, and turnbuckles.
|
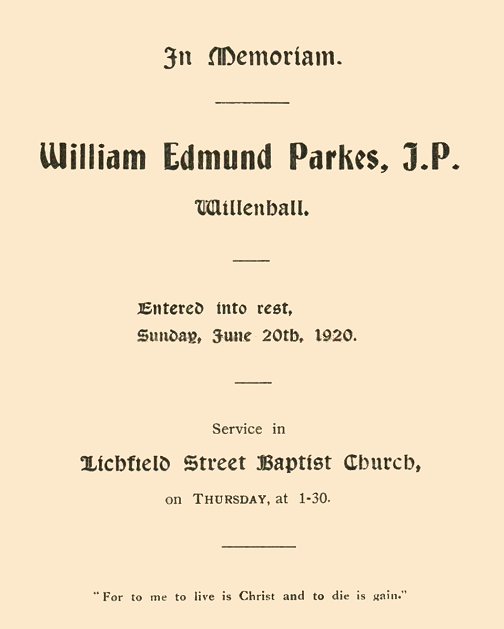
The front of the order of service. |
In 1916 Josiah Parkes & Sons was formed into a limited company with a
share capital of £25,000.
The company was incorporated on 13th
December, 1916 with William Edmund Parkes as Chairman and Managing
Director, and William Cyril Parkes as assistant Managing Director.
In
the following year several large bays were added to the factory.
With
the death of his father, William Edmund Parkes, in 1920, William Cyril Parkes became Chairman
and joint Managing Director with his brother, Arthur Josiah Parkes who
had joined the firm twelve months earlier.
|
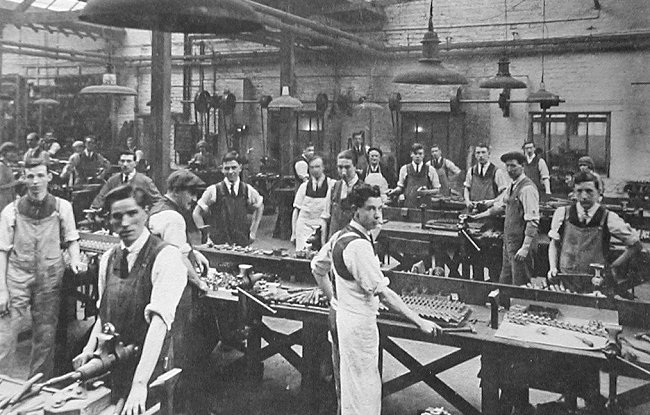
One of the many workshops. |
In 1917, William Cyril Parkes became a majority
shareholder in the Crane Foundry, Wolverhampton, taking control
of the company from the Crane family. The foundry became part of
Josiah Parkes & Sons and began to specialise in castings for the
engineering industry, and Parkes' lock cases. It remained under
the control of Josiah Parkes & Sons until the 25th June, 1945,
when the foundry was sold to Qualcast for £9,200.
By 1917 so many men had enlisted that Parkes, like most other
manufacturers in the area, had to employ women workers. When the
war ended the women did not automatically lose their employment.
Conditions were not easy for women employees - they were not allowed to
speak at work and had to meet together to walk home at the end of the
day, to avoid attracting men’s attention. Two members of staff lost
their lives whilst serving in the armed forces. They were E.
Ashbrooke, and R. Highway.
The Union
Engine
The two-stroke engine was developed in 1918
to supply the many motorcycle manufacturers who would cater for
the expected surge in demand for motorcycles after the war. An
initial version of the engine was patented by Mr. R. S. Whaley.
It could deliver 2¾ hp. and had a bore of 69 mm. and a stroke of
78 mm. Further development took place in early 1919, after which
it was optimistically claimed that the engine could deliver 5
hp. with a fuel consumption of 125 mpg. The bore was now 70 mm.
with a 76 mm. stroke.
It was available with a C.A.V., E.I.C. or
Runbaken side-mounted magneto, and an A.M.A.C. or Brown Barlow
carburettor. It also had a special lubrication system where oil
was fed to the moving parts through pipes on either side of the
crank case.
The engine was successfully tested at the
Camarthen Hill Climb on 4th August, 1919, and appeared in
countless adverts. It was also exhibited at the November 1919
Olympia Motor Cycle Show.
A number of manufacturers purchased the
engines, including Autoglider, Baron, Coulson, De Luxe, Macklum,
Priory, Romper, and Sirrah. Production continued in Willenhall
until about 1926 when the engine and manufacturing rights were
acquired by Wiseman’s of Glover Street, Birmingham, who built
Sirrah motorcycles. Before the year was out, production at
Wiseman’s ended, so it seems likely that no Union engines were
ever made in Birmingham. Engine production at Willenhall
probably came to an end because Union engines could not compete
with the cheaper and superior Villiers engines with flywheel
magneto. |
New Buildings and Another War In 1921 the firm began to rent fifteen acres of land in
Portobello on which to build a sports ground. Two years later the first
sports pavilion was erected there. In the 1930’s the Union Street premises in Willenhall
were modernised and a new office block was completed in 1933. A year
later the small houses where the firm started making locks, and later
used as offices, were demolished. In 1935 the freehold was acquired for
the land at Portobello with a view to building a new factory there. |
An architect's drawing of the
proposed new offices in Gower Street, built in 1933. |
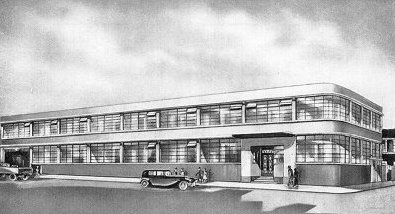 |
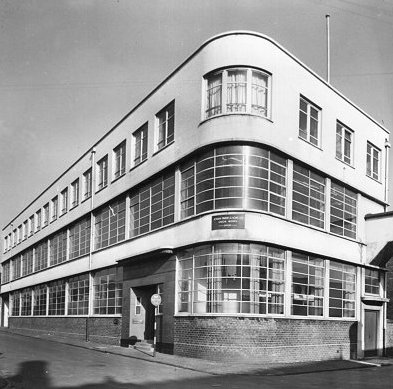 |
The new offices as built in
1933. The building had a floor area of 16, 056 square feet. It
contained a warehouse for finished goods, the wrapping, packing
and despatch departments, offices for three of the directors,
and for the sales, and accounts staff, the printing office,
telephone exchange, the showroom, and a museum.
A pendulum conveyor continuously carried
finished products across a bridge over Wood Street, from the
factory to the warehouse. |
The Union Works, on the corner
of Gower Street and Union Street, built as an extension to the
existing works, and in a style matching the new office building. |
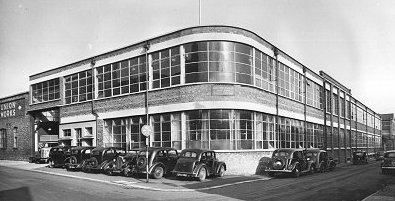 |
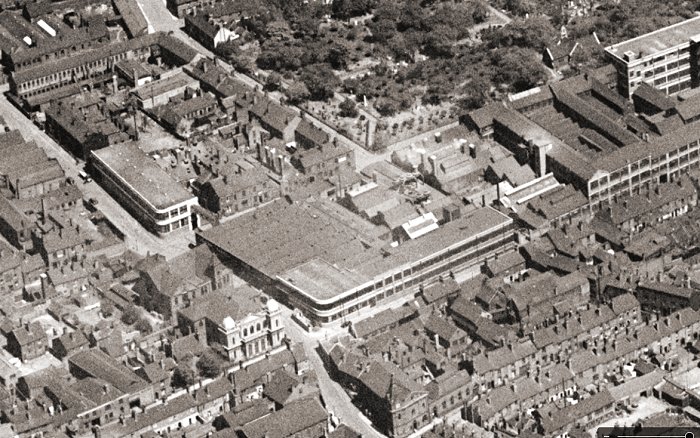
Union Works in 1939.
The company was converted into a public company under
the name of Josiah Parkes & Sons Ltd, on 28th November, 1936,
taking over J. P. and Sons (Holdings) Ltd (formerly Josiah Parkes & Sons
Ltd). The directors were C. W. Parkes (Chairman and joint MD), A.
J. Parkes (joint MD), W. E. Egar (Secretary) (Stock Exchange Yearbook
1946). The new company had a paid up share capital of
£200,000.
In the Second World War (as in the First) the skill and
machinery of the company were put to essential munitions manufacture,
notably grenades, fuses for shells and landmines, detonators for aero
bombs, and bomb release mechanisms etc. as well as locks to
secure the spinners of aeroplanes, switches for booby traps, wireless
aerials for tanks, and thousands of padlocks to secure
kit bags and numerous other purposes. Over five million units and
assemblies were produced in the factory for the armed forces. During the
war, 152 male employees, and 8 female employees joined the armed forces.
Sadly, six of them were killed in action. They were H. Barker, D.
Dudley, D. Johnson, L. Ray, T. Rowley, and S. Ward.
|
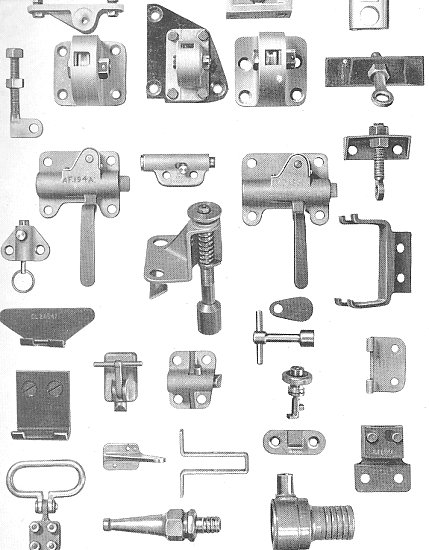
Some examples of the company's war work. |
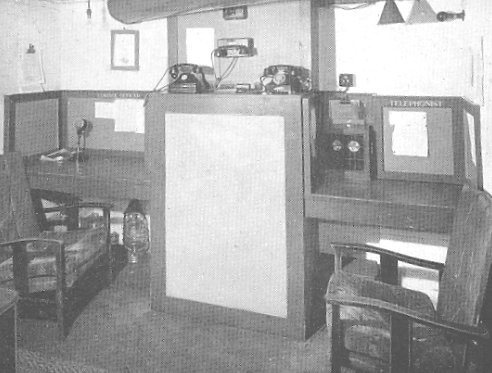 |
The Air Raid Precaution Control Room
that was in the company's air raid shelters between 1940 and
1945. |
The Air Raid Precaution Equipment
Store, and the Control Officer's sleeping quarters in the air
raid shelters. |
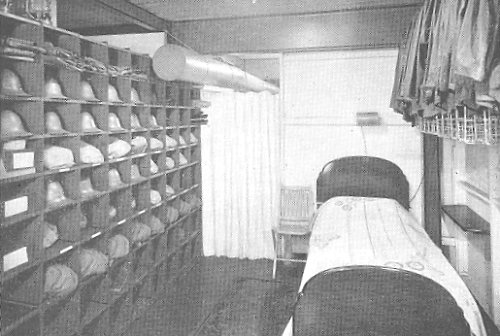 |
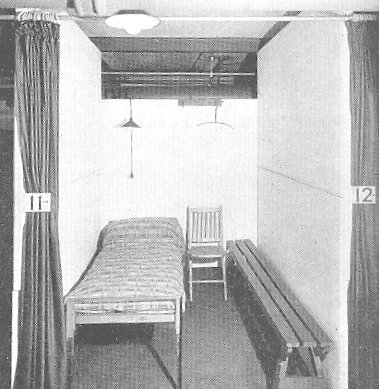 |
The Fire Guard's sleeping cubicle in
the company's air raid shelters. |
In 1945 at the end of the war, work started on building a new factory, covering
150,000 square feet, on the company's land at Portobello. A year later
the factory opened and began producing lock parts.
|
|
|
View some photographs
of the
interior of the factory |
 |
|
|
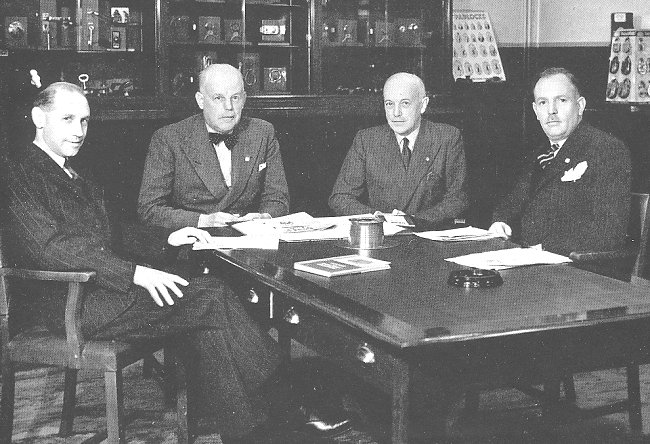
The Board of Directors. Left to right:
W. E. Egar, Director and Secretary; C. W. Parkes, J.P.,
Chairman and Joint Managing Director; A. J. Parkes, Joint
Managing Director; and E. C. Fryer, Works Director. |
Josiah Parkes & Sons Limited had built up a thriving export
business over the years. In 1928 Cyril William had toured
Australia, New Zealand and Canada to explore the possibilities of
expansion. By the late1940s there were representatives and agents in
over 50 countries worldwide.
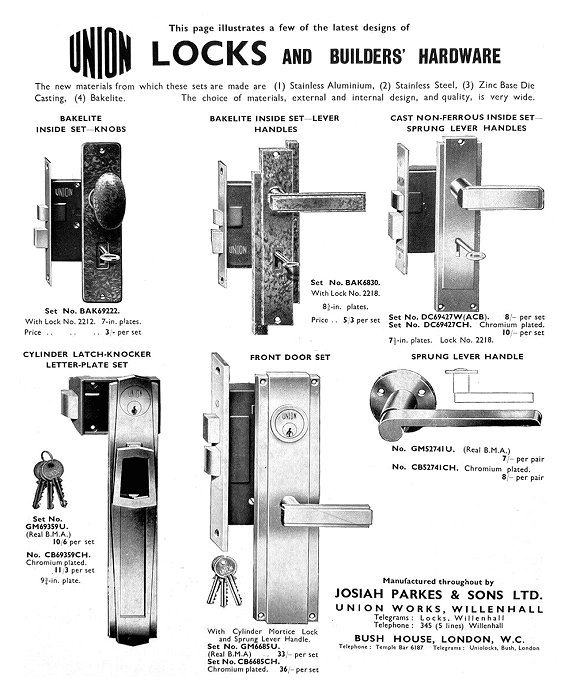
An advert from 1936.
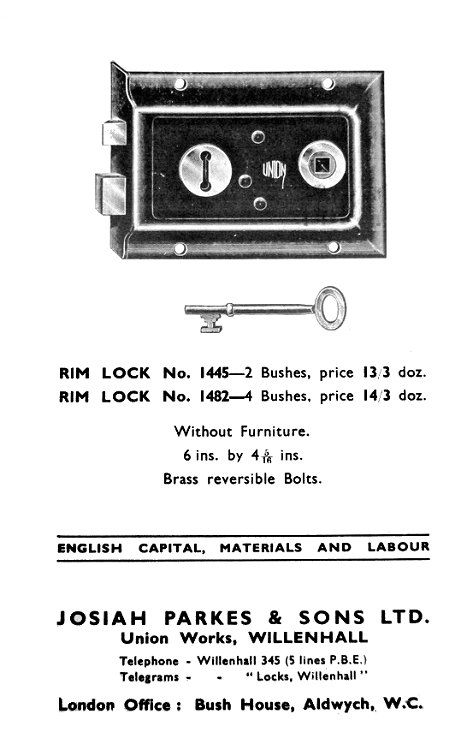
A postcard from 1936.
In the mid 1940s the company described itself as a
manufacturer of locks and builders' hardware including lock and door
furniture (bolts, knobs, handles, postal knockers, finger plates, and
catches), cupboard door fastenings, coat hooks, and gate fittings. In
1946 Harry George Parkes died, Mr. D. S. Maitland joined the firm, and
Mr. William Ewart Egar joined the board. In the following year he was
joined on the board by Mr. Edward Camden Fryer.
|
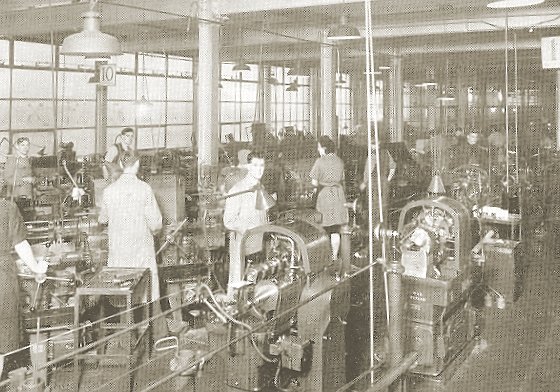
The Capstan Shop. |
By the late 1940s locks were produced on a large scale,
by a sizeable workforce with a wide range of skills. In addition to
skilled locksmiths and keysmiths there were male and female operators of
power and hand presses, capstan and automatic lathes, drilling
and milling machines, and key-cutting machines. Other members
of staff carried out brass finishing, and electric welding. |
The all-important tool room which produced the essential
tools for production employed highly skilled people to operate
numerous kinds of precision machines, and to precisely fit and
harden the tools. In the factory there were foremen, charge hands, store
keepers, routers, progress chasers, and the maintenance staff who looked
after the various buildings and the machines. Their team included
bricklayers, carpenters, painters, millwrights, and electricians. The
warehouse and despatch departments employed cardboard box makers,
wrappers and packers. There was also the laboratory, staffed by
qualified chemists who regularly tested and analysed the materials and
chemicals that were used in production, and carried out trials on new
finishes and processes. There was also a test room where the strength,
performance, and durability of all the products were checked, and an
experimental shop for the development of new products.
|
The factory had its own printing department for the
production of all office and works stationary, forms, pamphlets,
notices, and many of the advertising leaflets. In the office
there were calculating machines, and a punch card system that
was used to record sales, purchases, payments, wages, and for
analysis. |
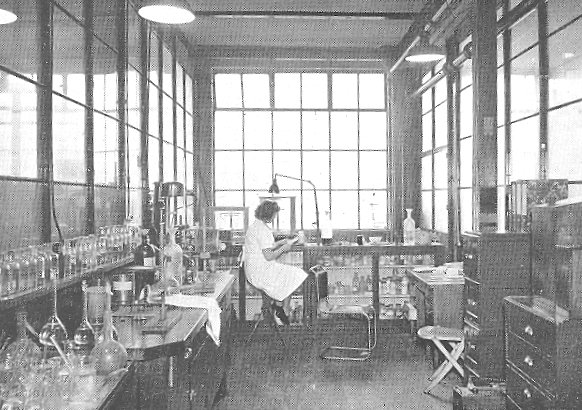
The Laboratory. |
There was also the drawing office where draughtsmen designed
the various products and the tooling needed to make them.
Employees worked for 40 hours each week from Monday to Friday,
which included a short tea-break each morning and afternoon. The
only people who were at work on a Saturday were the maintenance
staff who could carry out important work without affecting
production. |
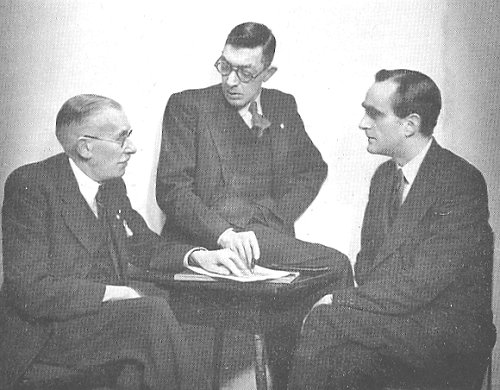
Left to right: E. J. Foster, North West
Coast Representative; T. Dudley, Tool Room Superintendent; and
J. Williams, Home Sales Manager. |
All
employees had one week's paid holiday plus six days leave, with pay each
year.
After twenty years service, all employees were given a long
service award consisting of a silver badge for men, and a silver brooch
for women. After thirty years service a silver gilt badge or brooch was
presented, and after forty years service a gold badge or brooch was
presented.
When the business was founded in 1840, people worked a
fifty-five hour week, which was reduced to fifty hours around 1900, then
to forty seven hours after the First World War. |
Left to right:
E. F. Ordidge, Development Officer; L. Blakemore, Purchasing
Officer;
F. J. Butter, Chief Designer; A. J. Morris, Tool Engineer; D. S.
Maitland (seated), Planning Engineer; and
L. Southall, Production Controller. |
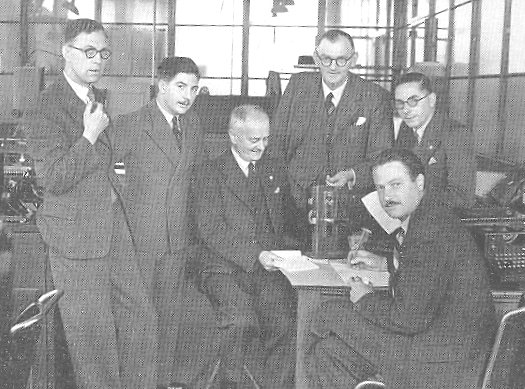 |
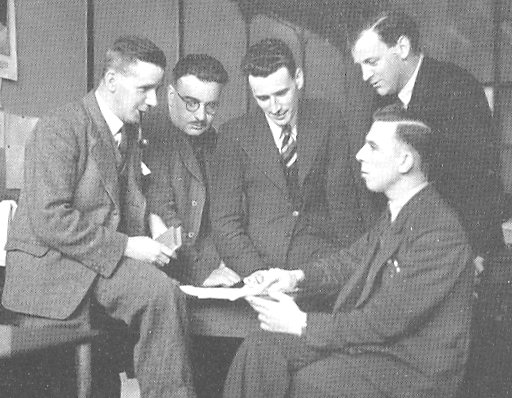 |
Left to right:
L. Mable, Plating Shop Superintendent;
K. P. Stanworth, Training and Educational Officer; M. Lloyd,
Maintenance Engineer;
F. M. Campbell, Time Study Officer; K. Moran (in front)
Electrical Engineer. |
The company's welfare department assisted and advised
employees on all matters connected with their work, and with
personal problems. The department had a welfare supervisor,
and a fully equipped ambulance room and surgery staffed by a
qualified nurse, who could treat minor injuries and complaints.
A doctor attended once a week, and sunray treatment was given
free of charge providing it had been approved by a doctor. |
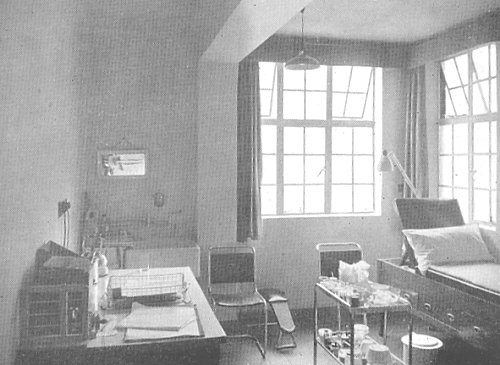
The Ambulance Room. |
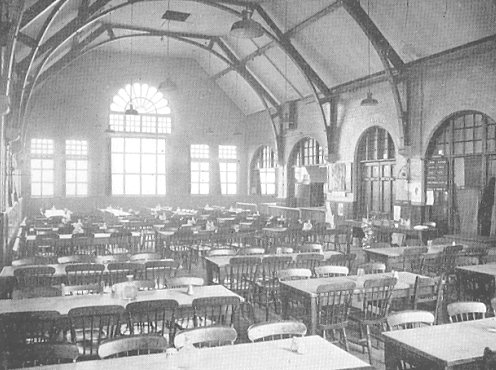
The Canteen. |
As part of the general welfare scheme, the Union Locks
Welfare Society was formed. All staff were eligible for
membership, which included access to the Benevolent Fund to
financially help members in cases of illness, or accident.
There was also a Sick and Dividend Club that provided its
members with sick pay and funeral benefits. |
A contributory pension scheme was introduced in 1943 for
the benefit of all the permanent staff. It provided a pension that was
payable on retirement age. In 1949 it was extended to provide pensions
for hourly-paid workers. The company ran an apprenticeship scheme that
included training by skilled instructors in the various departments in
the factory, and attendance at a technical college during working hours
and one or two evenings a week.
The firm's Sports Club oversaw the sporting activities
of the various football, tennis, cricket, and bowling clubs, and the
sports club refreshment rooms, and any entertainment that took place in
the canteen, or the sports pavilion. The canteen could seat around 300
people and served hot lunches, tea, and refreshments that were provided
by a firm of professional caterers. There was also a company safety
officer who made sure that all the safety equipment required by
the Ministry of Labour was provided and that regulations were observed.
The firm had a trained works fire brigade, and fire appliances which
were provided at various points in the factory.
|
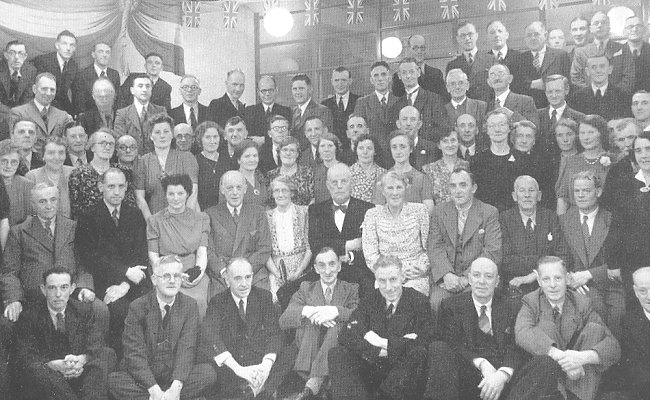
A group of long service employees in
1946. |
The non-ferrous foundry at Portobello opened in 1948, by
which time the main products were still locks, latches, and keys, which
were produced in numerous sizes and qualities. At this time the firm
described itself as a manufacturer of locks and builder's hardware, so
other products included lock and door furniture, such as knobs, handles,
postal knockers, catches, fastenings of all kinds, and hat and coat
hooks. For a time the company also made door bolts, window fasteners,
stays, openers, drawer handles, finger plates, gate fittings, hinges,
and kicking plates. The policy was to make articles that were in the
greatest demand, so locks were also produced for ships, motor cars,
filing cabinets, and clothes lockers. The firm produced a considerable
percentage of the twenty million or so locks and latches were produced
annually in the UK in the late 1940s. The general range of products was
distributed through builders' merchants and ironmongers, and the
specialised products were supplied directly to manufacturers. In 1948 Josiah Parkes & Sons (South Africa)
Limited was formed with W. F. Boustred as Chairman, for the purpose of
manufacturing Union locks and architectural furniture in South Africa.
It had a starting capital of £50,000, and was based at Fordsburg,
Johannesburg. The manager was Mr. F. G. W. Sutton from Union Works. In the 1960s Josiah Parkes & Sons Rhodesia Ltd. and Josiah Parkes & Sons Nigeria Ltd. were
formed. Two further factories were established in Singapore and Kenya to
manufacture and assemble Union products in their respective countries.
The company had agents in Buenos Aires, Melbourne,
Sydney, Brussels, La Paz, Nairobi, Barbados, Trinidad, Demarara,
Rangoon, Winnipeg, Montreal, Las Palmas, Colombo, Santiago, Punta
Arenas, San Jose, Havana, Copenhagen, Guayaquil, Cairo, Dublin, Asmara,
Addis Ababa, Helsinki, Djibouti, Athens, Guatemala City, Port Au Prince,
Amsterdam, Tegucigalpa, Bombay, Karachi, Madras, Baghdad, Kingston,
Beirut, Madeira, Valletta, Mexico, Casablanca, Managua, Oslo, Tel Aviv,
Peru, Lisbon, East Africa, Rhodesia, San Salvador, Saudi Arabia, Cape
Town, Johannesburg, Khartoum, Istanbul, Montevideo, Caracas, and Lagos.
|
In 1956, the old established business of Edwin Showell & Sons of
Stirchley, Birmingham, was acquired. Showells was founded around
1830 and manufactured door springs and architectural brass ware. The
principal object of the amalgamation was to enable Parkes to offer
builders' merchants, the architects, and the building trade, a
comprehensive range of builders' hardware. |
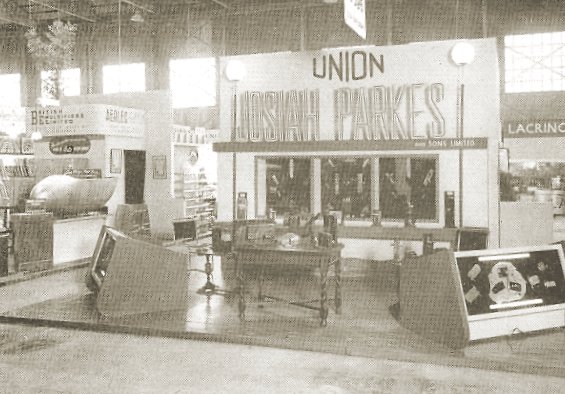
The company's stand at the 1948 British
Industries Fair. |
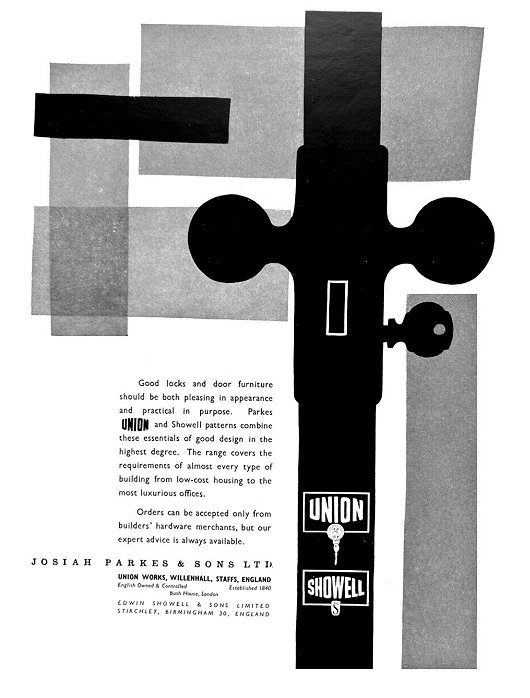
An advert from 1961.
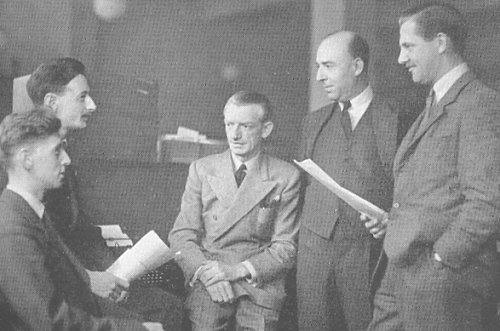 |
Left to right:
E. R. York, Home Sales Executive; R. J. Jesson, Director and
General Manager of Josiah Parkes & Sons (South Africa) Limited;
J. H. Adcock, London Manager; W. J. T. Baker, Warehouse Manager;
and
R. G. McKay, Export Sales Manager. |
Left to right:
F. V. Murtagh, Midland and
West Country Representative;
D. J. Fowler, Southern Counties Representative; H. W. Pritchards,
East Coast Representative; and
E. Hewitt, Northern Representative. |
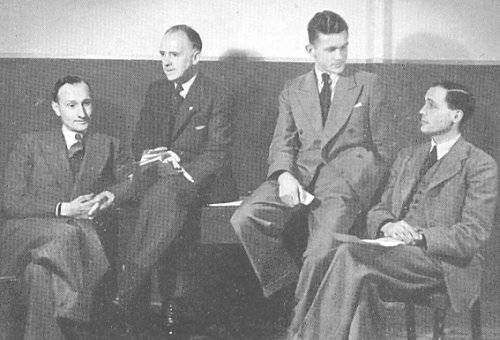 |
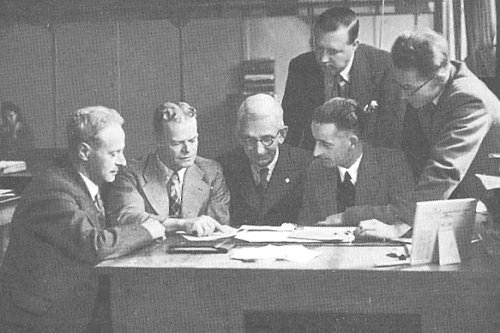 |
Left to right, seated:
F. Nicklin, Chief Inspector;
E. W. Morgan, Works Manager; A. R. Corbett, Departmental
Superintendent; and F. Smith, Machine Shop Superintendent.
Left to right, standing:
B. E. Cooke, Portobello Factory Superintendent; and J. Robb,
Assembly Department Superintendent. |
During the ten years, 1948 to 1958 the firm's capital increased from
£389,876 to £1,300,046 and the firm's annual profits before tax
increased from £89,882 to £295,007. During the decade the number of
employees had more than doubled to nearly 1,800, more than half of whom
were women and girls. In 1958 the company
produced its authoritative encyclopaedia of the lock trade, by which
time the firm's factories covered around six acres..
In 1964 Cyril Parkes retired as chairman and was
succeeded by his brother Arthur, who himself retired in 1967. On
Arthur's retirement William Ewart Egar became Chairman, and Mr. D. S.
Maitland became Managing Director. Cyril Parkes died in 1966.
|
|
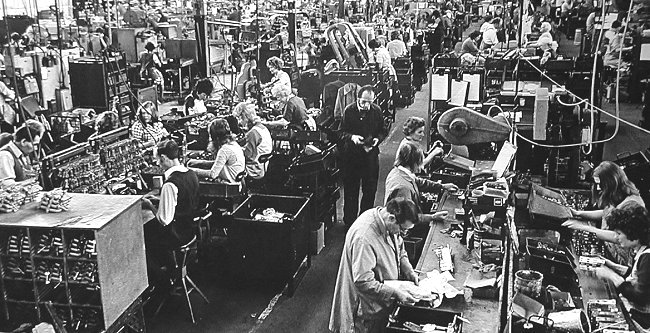
The factory in later days. |
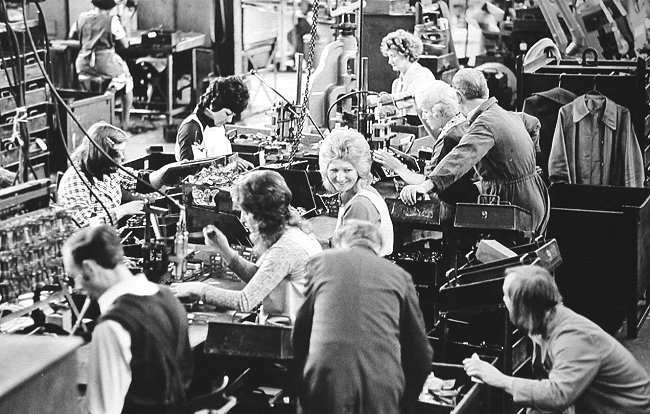
A final view of the assembly area. |
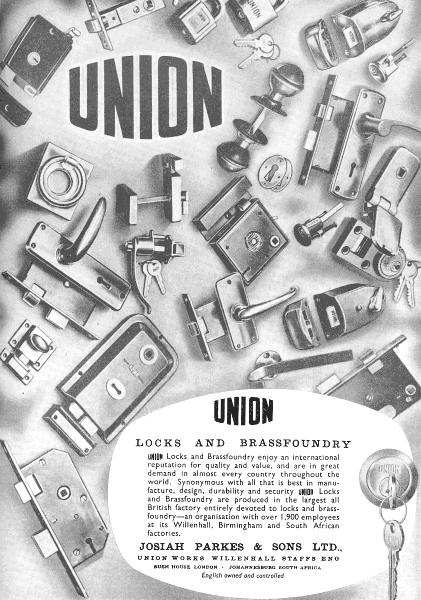
An advert from 1958. |
The business was acquired by the Chubb Group of security
companies in 1965 and became a member of the Racal Group of companies in
1984 on the acquisition of Chubb & Son plc by Racal Electronics plc.
In 1971 the company opened a new metal finishing factory
at Portobello, consisting of three buildings. The first, a single storey
building, 18ft. high, 150 ft. long, and 100 ft. wide, housed the
production department and the plating department. To the west stood the
two storey effluent and chemical storage building, measuring 75 ft. by
40 ft. To the east were the polishing department, laboratory, offices,
stores, and toilets in a two story building measuring 50 ft. by 115 ft.
The plant included automatic chrome plating machinery, automatic, and
hand polishing machinery, barrel burnishing machinery, and machinery for
barrel plating in copper, nickel, zinc, brass, and bronze. The factory
cost £500,000.
The automatic chrome plating plant was designed to process
zinc die castings to B.S.S. 1224 service condition 2. It could
handle up to 4480 components per hour. |
The automatic polishing plant was of the latest
design. The polishing compound was supplied to the machines via high
pressure supply lines, and injected into the mops in controlled
quantities at regular intervals, resulting in a more economical usage of
polishing compound. There were efficient extractors to remove all
noxious fumes, which regulated the temperature of the incoming fresh
air, and a closed pipe network to carry away all of the waste process
liquids to an effluent treatment plant that purified the waste. After
treatment the solids were drawn off, and the purified effluent was
discharged into the local authority's sewer.
By the late 1970s the company exported locks to eighty
four countries, representing 45% of the country's lock exports. Each
week around forty tons of locks and hardware were despatched from the
firm's factories in Willenhall to various ports for shipment abroad. In
1970 the exports exceeded £1,500,000 in value.
In 1977 the company’s excellent record in the export
trade was rewarded by their becoming the first lock manufacturer to be
honoured by the Queen’s Award for Export Achievements.
|
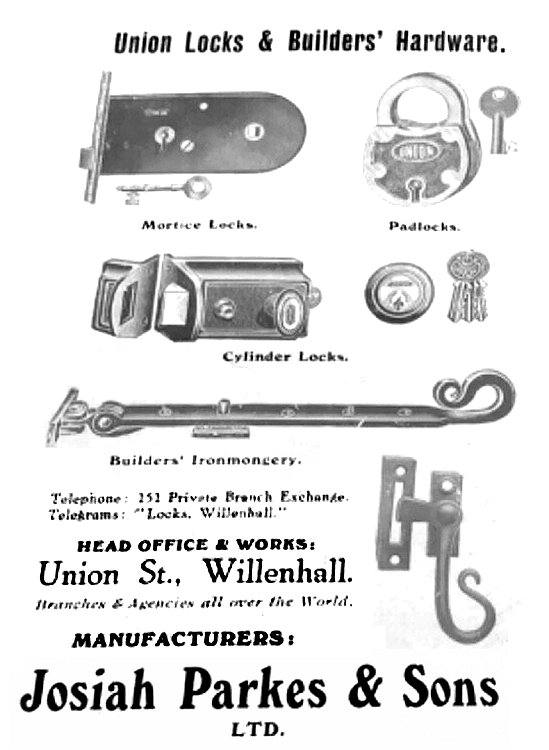
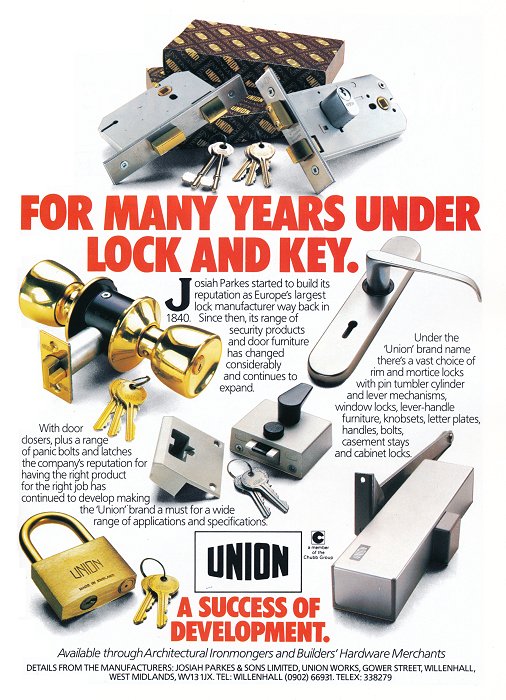
An advert from 1985.
The company was acquired, along with Chubb Locks, by
Williams Holdings 1997. In October 1997 William’s Holdings
announced changes to the organisation of their Security Products Group.
They planned to close the Union factory in Wood Street, the Yale factory
in Temple Bar (this was the Yale Die Casting Division on the site of the
old Enoch Tonks factory, and had been due for closure before the
William’s take over). They also closed the Planetary Road
Warehouse, which had been used as a warehouse following the move of
Chubb Lock making to Portobello; this was the old Albert Marston
factory.
The Yale Wood Street site was planned to become the company
headquarters and manufacturing unit for all cylinder and padlocks locks. The Parkes Portobello site would concentrate on all mortice production
and become the sole distribution site. The proposals would create
240 redundancies over the next 15 months. (Express & Star, 9-10/10/97).
|
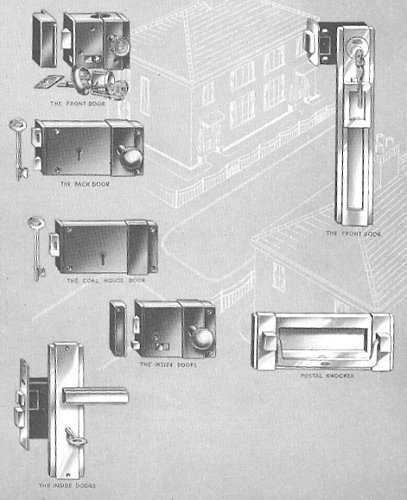
Union locks and door furniture. |
The change over to produce all cylinder locks and
padlocks at Wood Street took place in May 1998 . The production of
the Union Cylinder locks ceased and all locks were made to the Yale
design but were marked both Yale and Union. The move to produce
all mortice locks at the Portobello site was completed in July 1998,
when they ceased to make Yale mortice locks and only made the Union
range, although they were sold branded Yale and Ingersoll.
At this point (April 1999) the whole of the Williams
Group lockmaking side was reorganised under the name Yale Security
Products UK Limited,
with offices in Wood Street, Willenhall. All the administration,
sales and purchasing etc. took place from there.
Early in 2000 it was announced that Williams were
selling this division off to Assa-Abloy, a Swedish lockmaking company.
The official take over did not take place until the end of August 2000.
For further information on this company after the Assa
Abloy takeover, see the entry for Chubb.
|

The derelict office building in 2009. It
was demolished in 2013. |
References:
Walsall Archives note on the history of Parkes, prepared
by them from reports received from the company in 1994.
Catalogues and brochures issued by the company, and a
photo collection, all in the Lock Museum, Willenhall (undated but about
1950s and 1960s).
Union, published in 1949 by Josiah Parkes & Sons
Limited.
We are grateful to Yale Security Products for permission
to reproduce images which are still in their copyright.
|
|