Joseph Sankey & Sons Limited
is well-remembered in Bilston, as one of the larger and most
successful manufacturers in the town. The firm’s factories at
Albert Street and Bankfield were once prominent landmarks,
overlooking the town centre.
The Early Years
Joseph Sankey was born in Bilston in 1827.
Unfortunately his father died in 1836 and so Joseph became a
pupil at the Royal Orphanage School in Wolverhampton. At the age
of 14 he was apprenticed to John Duncalfe, a tray blank maker of
Hall Street, Bilston, where he was taught design and mechanical
drawing. After his apprenticeship he was employed by the Birch
brothers, who made tinplate trays that were sold to japanners
for finishing.
The business failed, and two of the senior
employees, Charles Harthill and Samuel Jackson, set up their own
firm in Middlefield Lane, where they employed Joseph Sankey.
Charles Harthill died in 1854, at a time when the firm owed £800
to Jon Bates, a sheet iron merchant, who secured possession of
the plant and tools of the firm as security for the debt. He
recognised Sankey's skills and determination, and in 1854
persuaded Jackson to take him into partnership. The new firm,
with premises in Dudley Street, Bilston, concentrated on the
production of blank trays, stamped from tinplate, that were then
sold to japanners. Jackson & Sankey produced trays of many
different shapes and sizes, but struggled financially, having to
repeatedly re-mortgage the firm's premises to finance expansion.
In 1861, Joseph Sankey began to run the
business on his own, after buying-out Samuel Jackson, who
continued to work for the firm as a foreman in the blank tray
shop. In the early 1860s, Joseph went into partnership with
Richard Chambers and John Page in order to acquire a rolling
mill and ironworks at Stonefield, as a way of gaining control
over the firm’s supplies of tinplate and sheet iron. The
business became the Bilston Iron Company. |
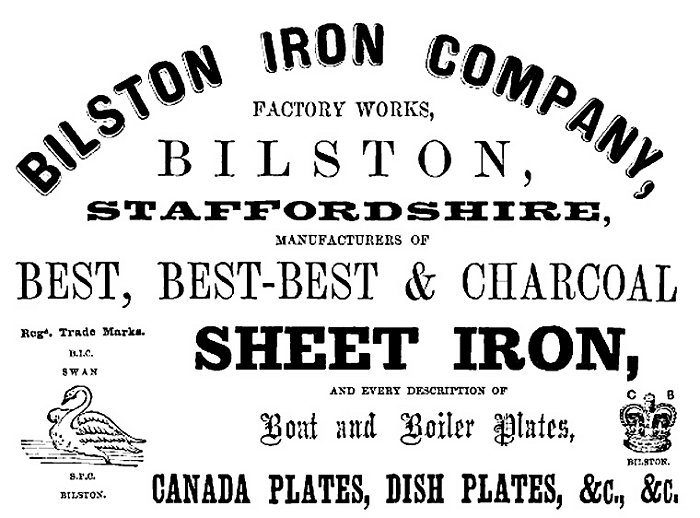
An advert from 1876. |
Expansion
Until the early 1860s, Joseph Sankey
appears to have lived on the Dudley Road site. In the early
1860s he had a new home built in Wolverhampton, which was called
Goldthorn House. It stood on the southern side of Goldthorn
Hill, next to where Coton Road stands today.
In 1867, Joseph Sankey acquired land in
Albert Street, behind the Dudley Street premises, where a large
workshop was built. Steam-powered stamping machines were
installed so that heavier gauges of metal could be worked. New
products included frying pans and kettles.
The firm began to concentrate on the
manufacture of a wide range of hollowware including chocolate
moulds, dish covers, lamps, lanterns, milk churns, tin boxes and
stamped or pressed metal products such as bath tubs, fire
shovels and metal life buoys. A significant export business also
developed. Cassada pans that were used to dry coffee beans were
exported to Brazil and bowls were exported to Ceylon, China and
India.
In 1871, Joseph’s eldest son, John William
Sankey, joined the firm and took over the accounting. In 1874
the firm had 65 employees. In 1878, John William Sankey became a
partner in the business and in 1884 his younger brother George
Herbert Sankey joined the firm. The company’s founder, Joseph
Sankey, died in 1886.
In December of that year, the company
started out in a new direction after being contacted by Robert
Jenkins, an iron merchant from London. He had been researching
into the possibility of making armatures for dynamos from
charcoal sheet iron discs. He thought that Sankey’s existing
stamping machines could be easily adapted for the manufacture of
electrical laminations and in 1887, persuaded Siemens to place
an order for laminations through an agency called Harold &
Jenkins. By 1890, contracts had been signed and production of
the laminations began. In the mid 1890s, Sankeys abandoned
charcoal iron in favour of a metal steel sheet.
Further Expansion
In July 1891, John William Sankey, went
into partnership with his two younger brothers, Frederick Ernest
Sankey and George Herbert Sankey, and the business became Joseph
Sankey & Sons. The firm acquired a number of smaller businesses
including Edward Morris & Sons, manufacturers of sugar-making
utensils; Huttons, manufacturers of nickel plated trays; the
Sanitary Bath Company, manufacturers of copper-clad steel; and
J. H. Hopkins & Sons of Granville Street, Birmingham,
manufacturers of hollowware and japanned products that had the
'Sphinx' trademark, which was adopted by Sankeys. The japanning
side of this business was sold, and stamping and pressing was
concentrated at Albert Street Works. |
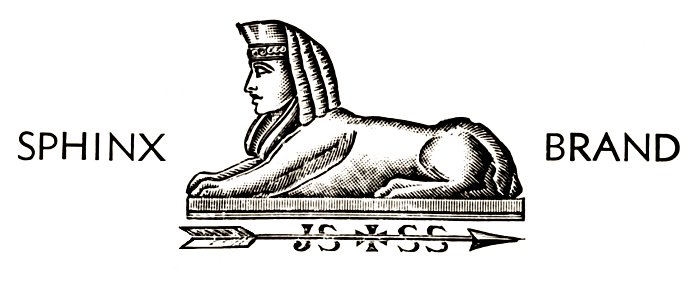
Sankey's trademark. |
In 1890, Sankeys patented a process called
'Neptune Ware' in which tinplate ran through colour rollers to
undercoat both sides. After being embossed and painted,
products, such as ash-trays, bread baskets, candlesticks, cups,
children's money boxes, cake baskets, and waiters' trays, were
blanked out to the final shape. The technique was a great
success and part of Albert Street Works had to be expanded to
cope with the growing demand. Also at this time, the firm
produced more kettles than any other British company, thanks to
the use of cheap steel that could easily be pressed into any
shape.
A New Factory
In 1893 the firm erected a large and
comfortable room for the use of the employees as a mess room and
a recreation room. A library was also built for the use of the
employees. Expansion continued in the early years of the new
century. In 1900 the derelict iron and tinplate works at
Bradley, established in 1833 by Thompson, Hatton & Company were
acquired for expansion. Most of the existing buildings were
demolished, and a new factory was built on the site for the
manufacture of electrical laminations. Slotting machines and
keyway cutters were acquired in order to transfer the
manufacture of laminations from Albert Street Works to the new
site, which was called Bankfield Works.
In September 1902, Joseph Sankey & Sons
became a limited company with an authorised capital of £200,000
divided into 10,000 ordinary shares of £10 each and 10,000
preference shares of £10 each. J. W. Sankey became Chairman and
George and Frederick Sankey were appointed as Directors, along
with John Chambers, who after working for the firm for many
years, had risen to Company Secretary.
To assist in the production of laminations
at Bankfield Works, Manor Rolling Mills at Ettingshall were
purchased from Stephen Thompson & Company Limited, in 1904. The
factory provided production facilities for the silicon steel
sheets that were needed for the electrical laminations.
Also in 1904, Sankeys began to manufacture
pressed body panels and wood and coach ironwork for cars. Within
two years, the firm was exporting body panels to Paris and New
York.
In 1906, Sankeys were granted an exclusive
licence from the Hadfield Steel Foundry of Sheffield for the
manufacture of a special electrical steel, known as 'stalloy'.
In 1909, Sankeys sub-licensed John Lysaght to roll sheets under
the Hadfield patents at their Orb Works, in Newport, South Wales
and also granted a licence to the Brymbo Steel Company, near
Wrexham, to make steel bars and blooms under the Hadfield
patent, which were to be sold to Lysaghts for rolling into
sheet. |
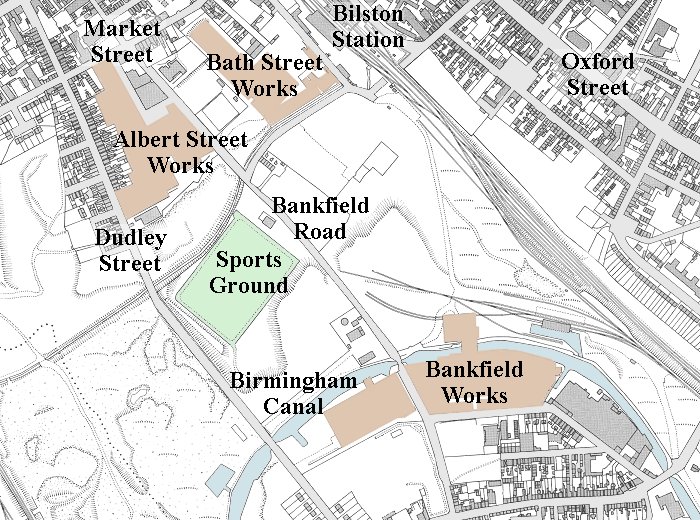
The Bilston factories. |
More Automotive Parts
Sankeys extended production of automotive
components at Albert Street after developing and patenting the
first pressed and welded, detachable motor car wheel, the 'All
Steel Wheel', in 1908. In the following year the company started
stamping steel body panels for Arrol-Johnston cars. Production
of automotive components increased again in 1910 when Sankeys
acquired the former factory of the Castle Car Company, at Hadley
Castle, near Wellington, which had produced tramcars. Some of
the machinery had remained in the factory, so production of
pressed steel car and charabanc body panels and the steel wheels
soon got underway there. The factory was also used for the
production of the range of Sankey-Sheldon office furniture and
agricultural implements.
In 1911, the automotive body shop was
transferred from Bankfield Works to Hadley Castle, along with
the wheel shop from Albert Street Works. Production of
automotive components was now concentrated at Hadley Castle. By
1914 the demand for laminations for dynamos, motors and
transformers, as well as for small electrical stampings had
significantly increased.
|
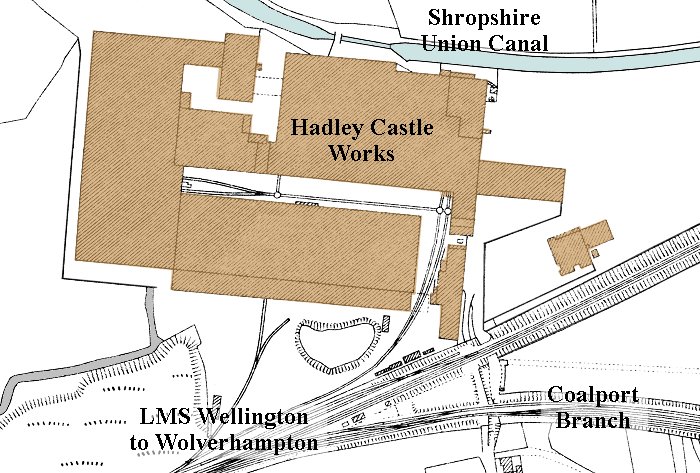
Hadley Castle Works in the 1930s. |
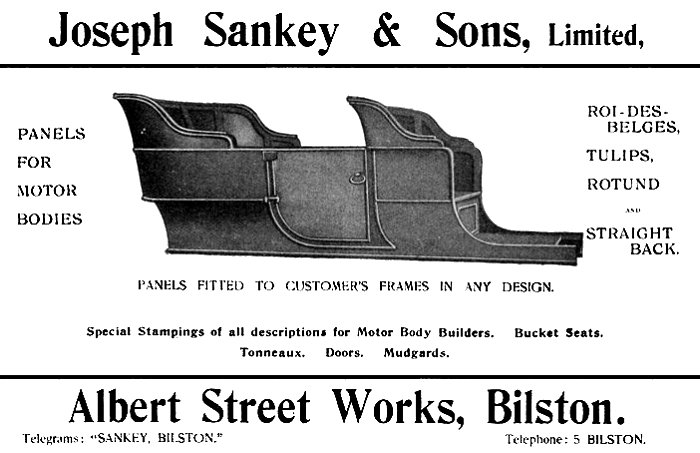
An advert from 1908. |
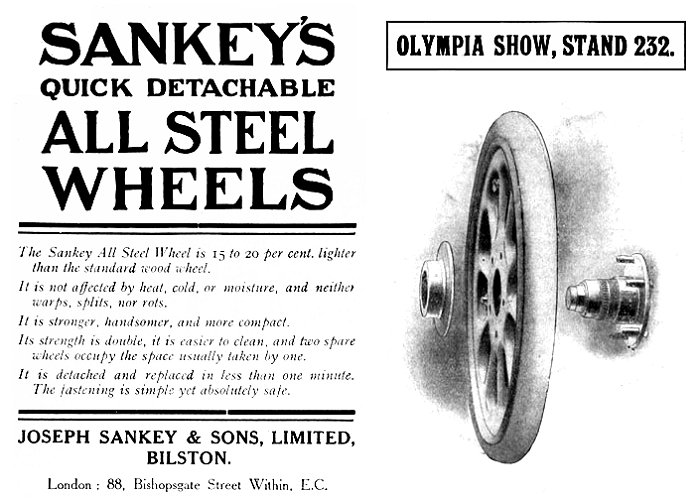
From the Autocar, 6th November, 1909. |
In 1913, after the death of John William
Sankey, his brother George became Chairman. At the outbreak of
war in 1914, a large number of employees went into the armed
forces, which greatly affected production. The firm received
large orders for war work from the Ministry of Munitions and in
November 1915, Albert Street Works became a Controlled
Establishment.
Products produced both at Albert Street and
Hadley Castle included aeroplane parts, bombs, field kitchens,
mine hemispheres, mortar bombs, rifle grenades, steel helmets,
anti-submarine bodies and shell bodies. A large number of female
workers were employed to replace the male factory workers who
had joined the armed forces. By the end of the war, 69 employees
had been killed, including Sydney Sankey, the eldest son of John
William Sankey.
Amalgamation
After the war, the company was still
profitable, but George Sankey had no desire to remain in charge.
There were few managers at board level and possibly some
uncertainty about the company’s future in the post war era. The
Sankey family decided to sell the business to one of their main
suppliers, John Lysaght & Company with whom they had strong
ties. In 1919, Lysaght’s Chairman, Henry Seymour Berry, also
became Chairman of Sankeys and Joseph Sankey & Sons Limited
became the sole subsidiary of John Lysaght Limited.
Henry Seymour Berry very much wanted to be
associated with Guest, Keen and Nettlefolds and planned to
takeover GKN. The two companies decided to amalgamate and so on
the 1st January, 1920, John Lysaght Limited and Joseph Sankey &
Sons Limited became subsidiaries of GKN. Sankeys retained its
identity and the company’s Registered Office remained at Albert
Street Works. Members of the Sankey family remained as managing
directors, until 1954.
By the 1920s, sales for the firm’s
hollowware had greatly declined. More goods than ever were
imported and plastic items were becoming more commonplace.
Sankeys decided to cease production of enamelled hollowware and
sold the excess stampings to Macfarlane & Robinson. The market
for 'Cassada' pans for Brazil remained buoyant, and large
numbers of casings for petrol pumps were sold to W. & T. Avery.
|
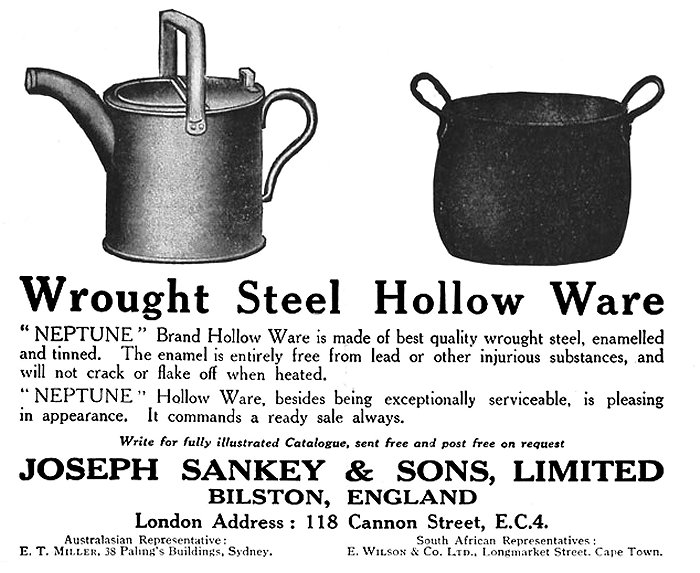
An advert from 1921. |
In the search for new products, an
agreement was made with the Asiatic Petroleum Company and the
Florence Stove Company, to make paraffin-burning heaters that
were sold by the Florence Stove Company. In 1929, Sankeys
purchased Bath Street Works, formerly occupied by Holcroft’s
Steel Foundry Company, and later by the Staffordshire Stainless
Iron Company. The buildings were next to the Albert Street
Works, and were used for the production of steel wheelbarrows.
|
The recession in the late 1920s and early
1930s led to a period of short time working and some
redundancies, which ended as the economy improved towards the
mid 1930s. At this time both Albert Street and Bath Street Works
were modernised. New presses and a new boiler house were added
along with toolmaking and repair facilities.
Investment was also made at Bankfield Works
due to the efforts of Mr. E. W. Richmond, who had been appointed
as general manager there in 1922. He convinced existing
customers to continue to purchase their electrical pressings
from Sankeys and to invest in new machinery to improve
production. By this time pressings were also being made for
wireless manufacturers.
Investment was also made at Hadley
Castle Works where three new rim-making machines were installed.
Production at the works included bath panels, metal trim,
radiators, steel barrels for the palm oil trade in Africa, steel
pulleys and steel roofing sheets.
By 1936 Sankey’s workforce had grown to
nearly 1,500. In 1938, Sankeys acquired a one-third interest in
the Florence Stove Company, which became the Florence Stove &
Hardware Company. The production of paraffin heaters became a
substantial part of production at Albert Street Works.
|
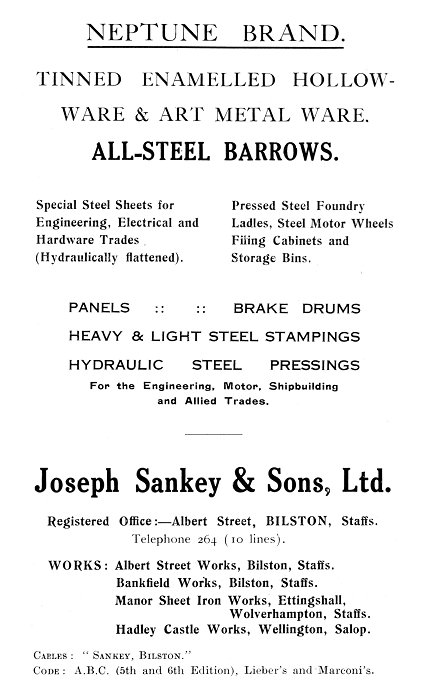
An advert from 1929. |
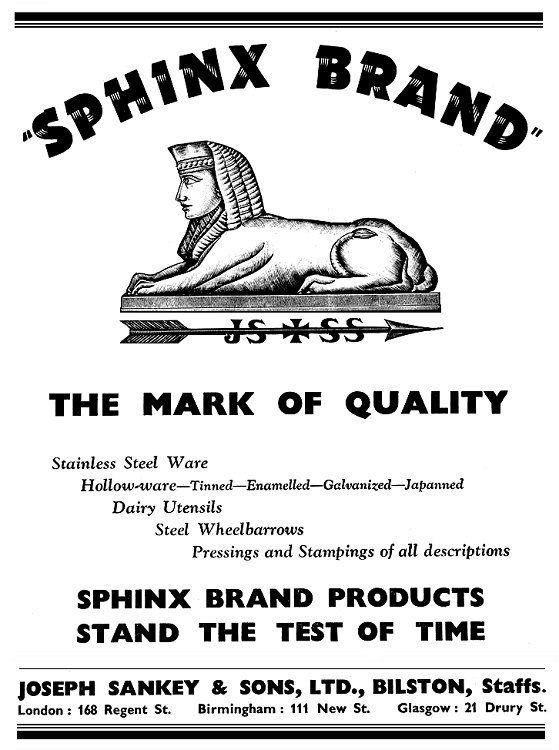 |
An advert from 1938. |
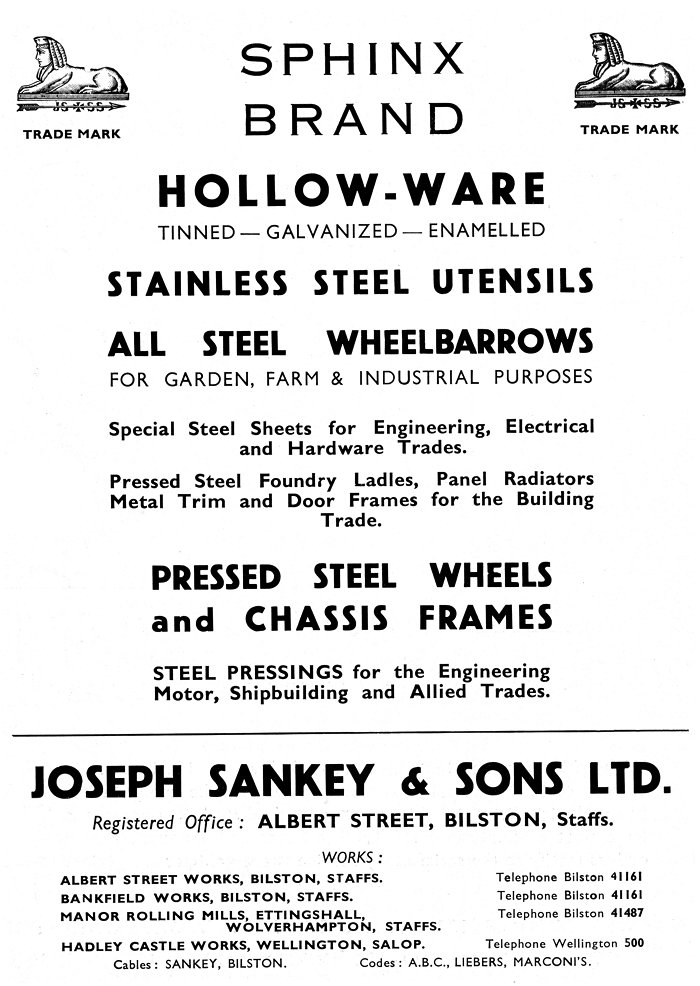
An advert from the early 1930s. |
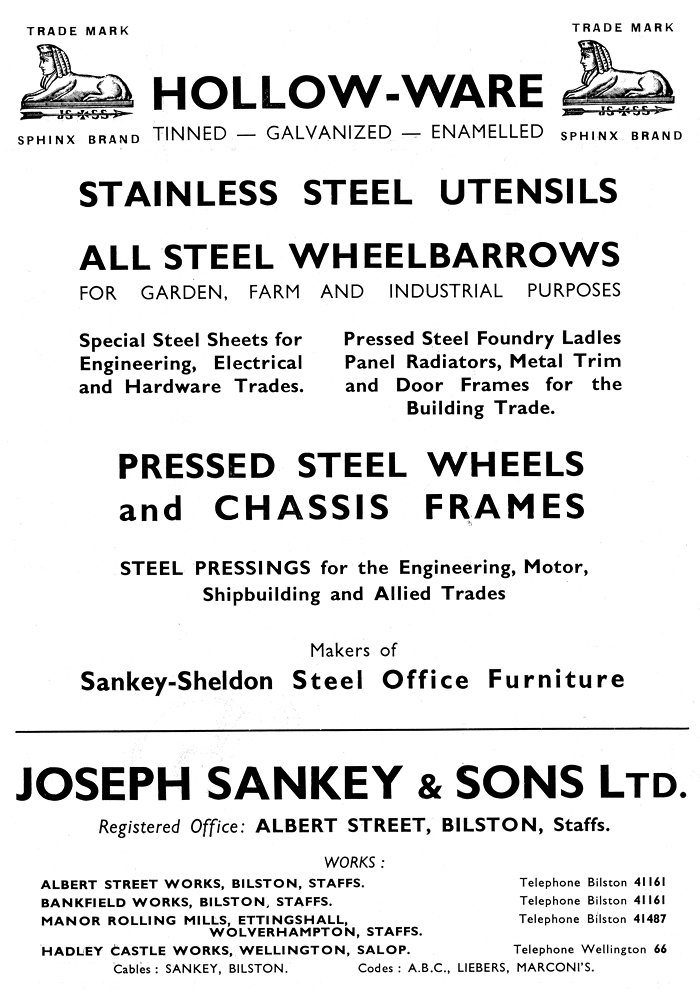
Another advert from the early
1930s. |
George H. Sankey died in 1934. By this time
his three sons, Harold B. Sankey, George Ronald Sankey and
Geoffrey B. Sankey had been in the business for some time.
Harold B. Sankey became Managing Director after his father's
death. Between 1942 and 1944 he was appointed Regional
Controller for the Midlands by the Ministry of Production.
Ronald Sankey then took over as Managing Director.
In the late 1930s, in readiness for the
outbreak of war, the government funded several new buildings at
Albert Street that would be used for war work. Products included
aeroplane spinners for De Havilland and Rotol, parts for jet
engines for the De Havilland DH1, heavy wheels for army
vehicles, ammunition boxes, bombs, depth charge cases, charges
and throwers, mines, steel helmets, complete spitfires, and
bridge sections and floats for the Admiralty. Other products
included electrical stampings for wireless sets and radar, and
steel furniture for the Royal Navy. By the end of 1940, 85
percent of the output was for war work. Orders eventually
declined after the end of hostilities in Europe in May 1945.
|
In 1946 a new wheel shop was built at
Hadley Castle Works that was further extended in 1955 and 1959.
In 1947 a range of agricultural implements was introduced there
including ploughs, seed drills, tractors, and trailers.
Expansion continued at the works for some time.
In 1958 a new
steel furniture factory was built, and in 1961 a new Commercial
Cab Shop opened. New plant was also installed for the production
of road wheels for buses, cars, tractors and trucks.
Hadley
Castle Works also produced mobility vehicles, armoured vehicles
including the 'Warrior' tank and automatic vending machines.
Sankeys acquired Universal Brewery
Equipment Limited in 1954, and began production of the ‘Sankey
System’, consisting of beer packaging, kegs, and combination
units for kegs to be washed, sterilised and refilled.
Plastic
mouldings for domestic appliances and office equipment became
important products along with steel furniture for marine cabins
and accommodation modules for oil rigs.
Partitioning was also
produced for general office and factory use.
|
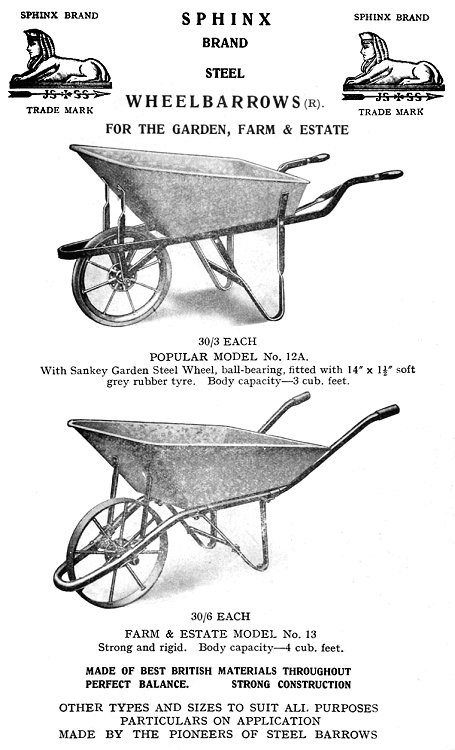
An advert from 1938. |
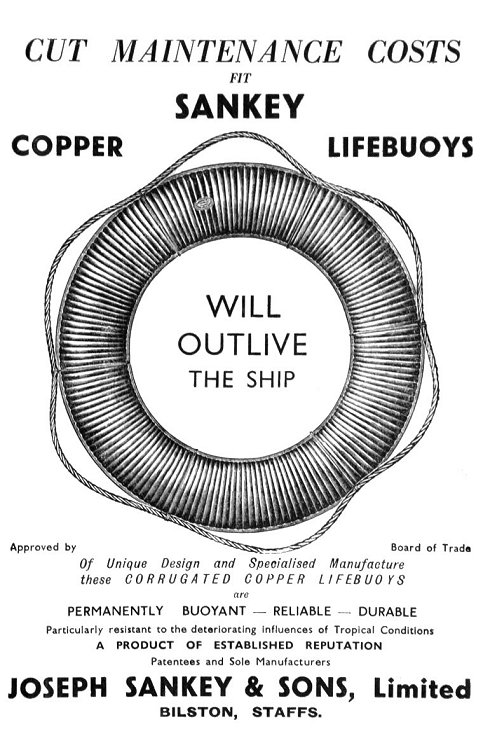
An advert from 1951. |
Albert Street and Bankfield Works were
rebuilt in 1957 to 1958, along with a new
head office. In 1968, Joseph Sankey & Sons Limited became GKN
Sankey Limited, and by 1970, Hadley Castle Works became the main
centre of operations, employing a much larger workforce than at
Bilston.
In 1971, the company took over the production of heavy
wheels for earth moving equipment etc. from Dunlop, who took
over production of Sankey car wheels.
By the 1970s the company was divided into
the following divisions: wheel; pressings; Bankfield; plastics;
brewery; unistrut; Sankey Sheldon; and automatic vending.
The
Sub-Group headquarters was at Hadley Castle Works.
|
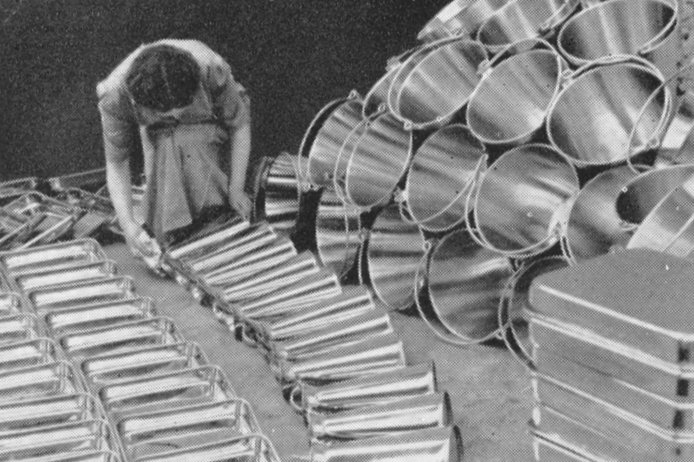
Stainless steel hospital ware made at
Albert Street in 1953. |
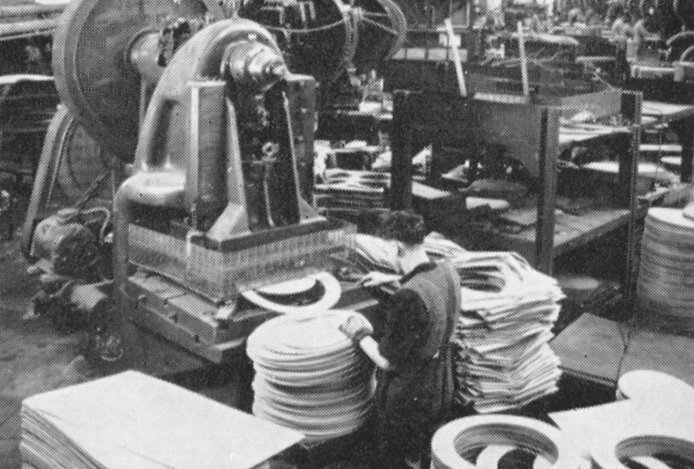
Electrical laminations made at
Bankfield in 1953. |
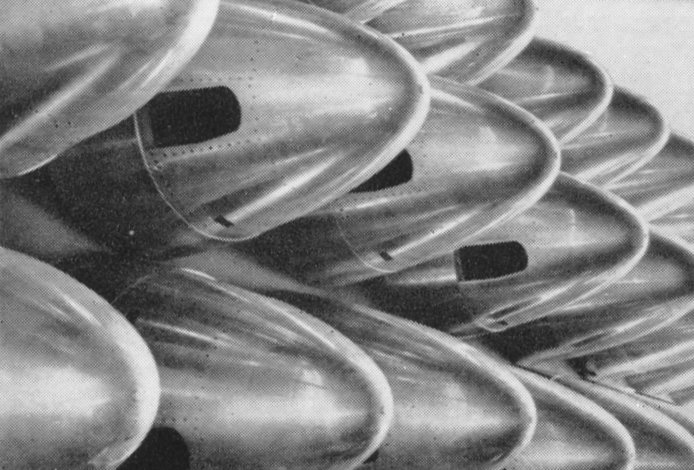
Aircraft propeller components made
at Albert Street in 1953. |
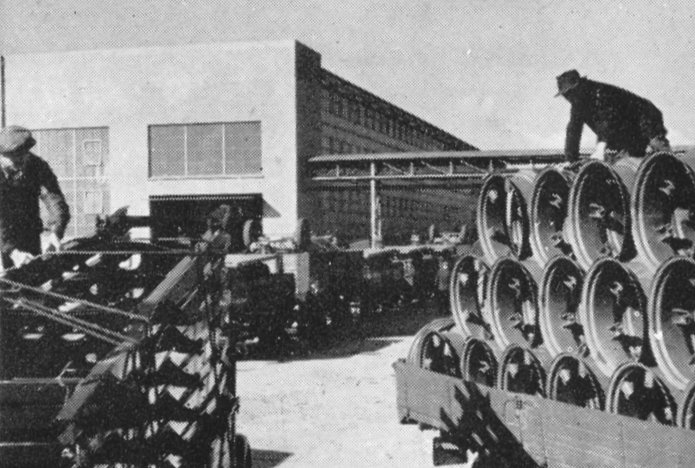
Chassis, tractor wheels and
trailers made at Hadley Castle in 1953. |
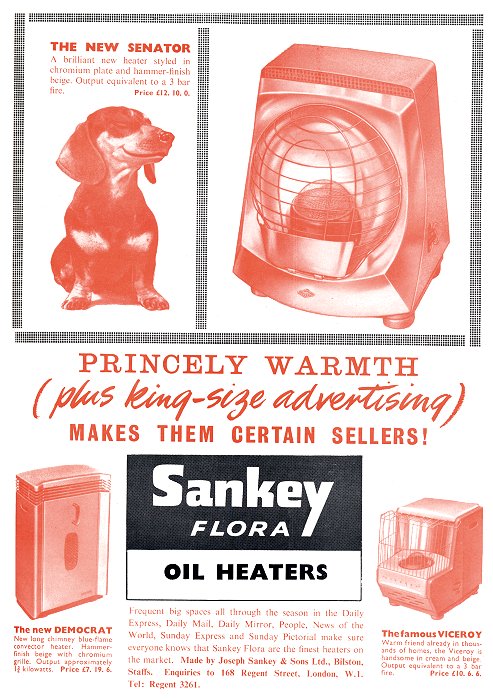
An advert from 1958.
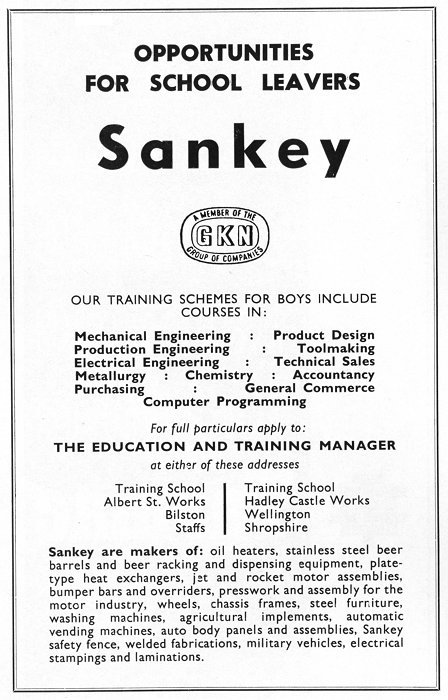
An advert from 1965.
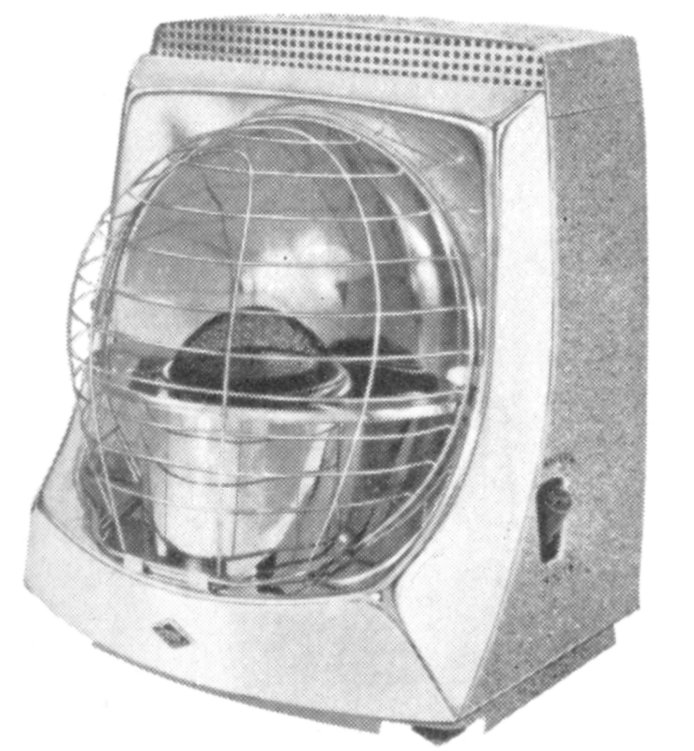
A Senator domestic heater
made at Albert Street in 1968. |
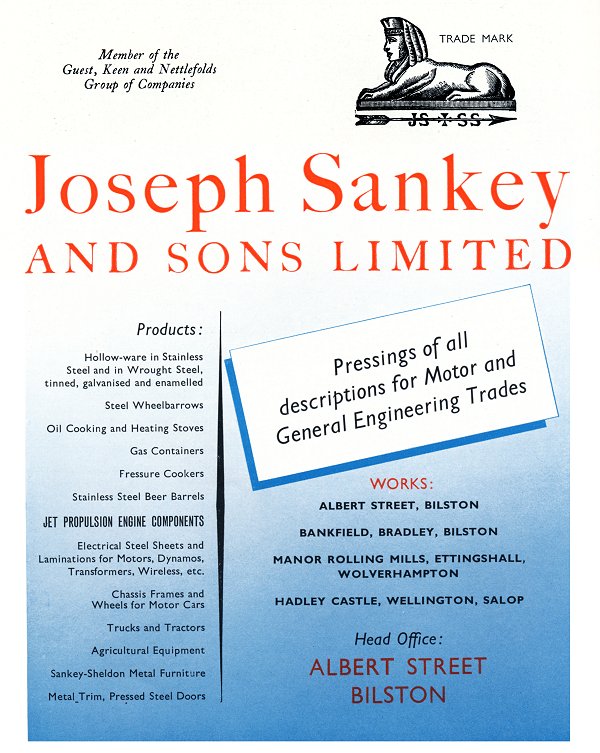 |
An advert from 1953. |
An advert from 1955. |
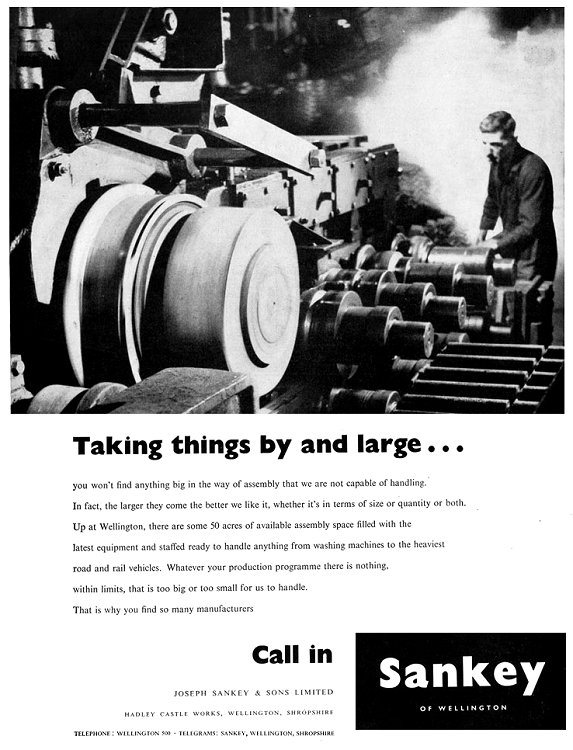 |
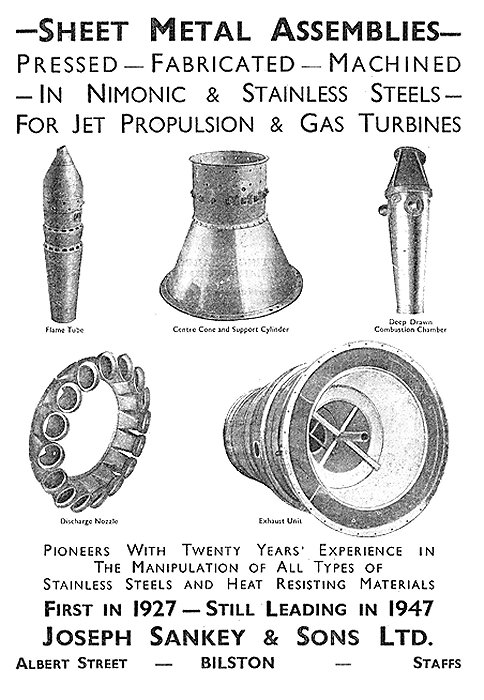
An advert from 1947. |
By the 1980s the company was suffering as a
result of the general decline of UK manufacturing. In 1980 and
1981 there were redundancies at Hadley Castle Works and Bilston,
due to losses in the wheel and pressing divisions.
Albert Street
Works closed in 1988 and buildings on the site were demolished.
The brewery business was sold and presses were moved to the
Hadley Castle Works in order to produce body pressings in a
joint venture with Jaguar.
Hadley Castle Works was divided into
four units consisting of light fabrications, making telephone
kiosks; agricultural products, supplying tractor cabs for Ford
and Massey Ferguson; engineering products, producing car
components; and the wheel division, concentrating on tractor and
off road wheels.
The venture with Jaguar failed after Jaguar was
taken over. |
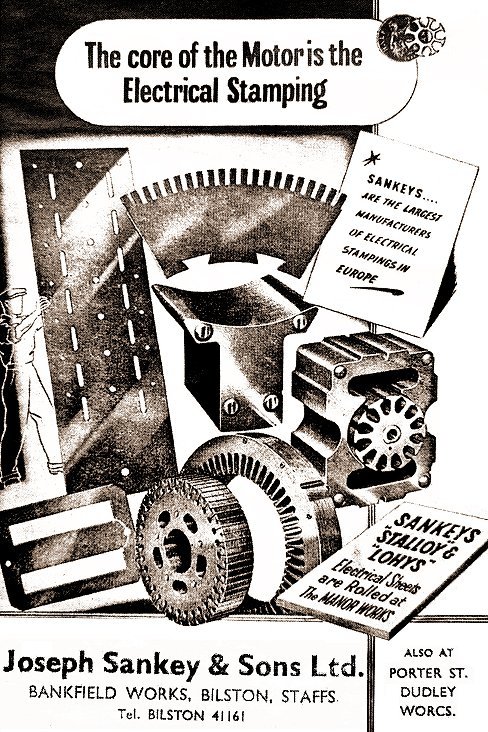
An advert from the 1960s. |
Photos from 1988 and 1989, when Albert Street Works
closed.
The lovely photos that follow, were kindly sent by David
Clare. They were taken by Sam Skitt, before and during the closure of
Albert Street Works and so must be some of the last photos
taken there. It was a sad time, when Sankeys vacated Bilston
after running the business for 134 years. During that time,
the firm had grown and had previously been one of the town's
largest employers. |

The front of the offices.
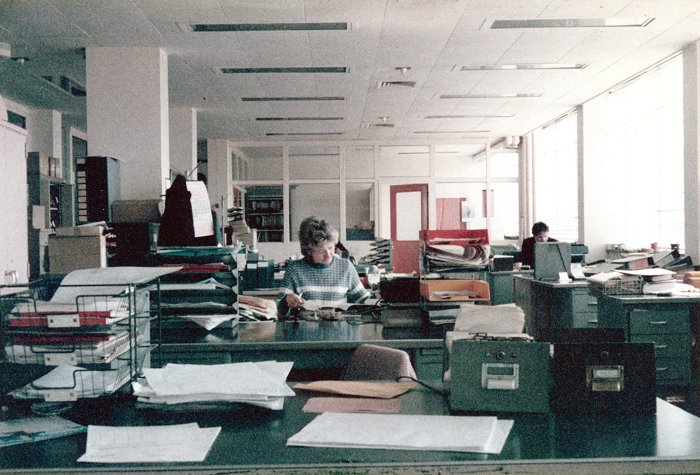
Inside one of the offices.
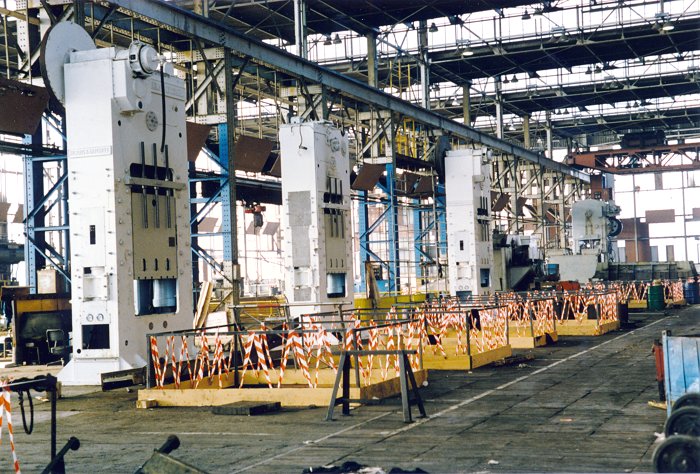
A row of locally made Wilkins and Mitchell presses
in one of the press shops.
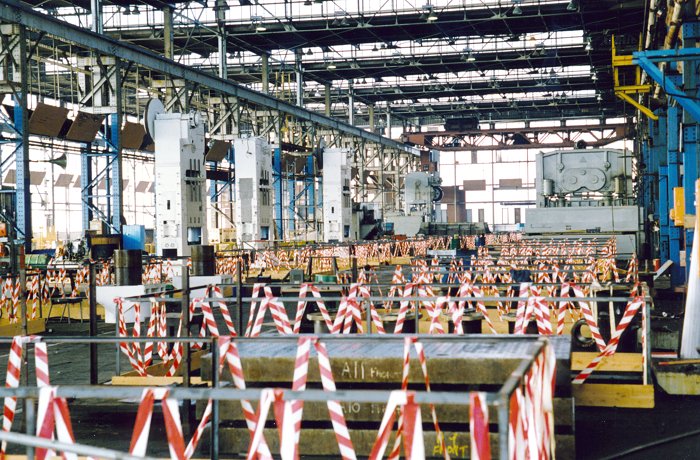
Another view of the press shop.
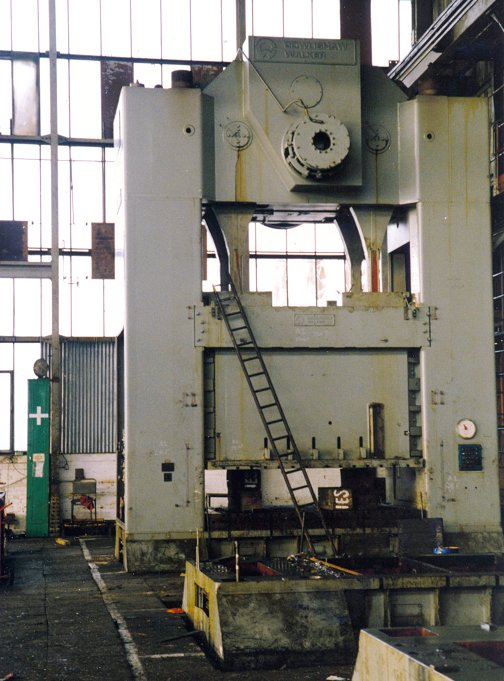
A Cowlishaw Walker press, which is about to be
dismantled.
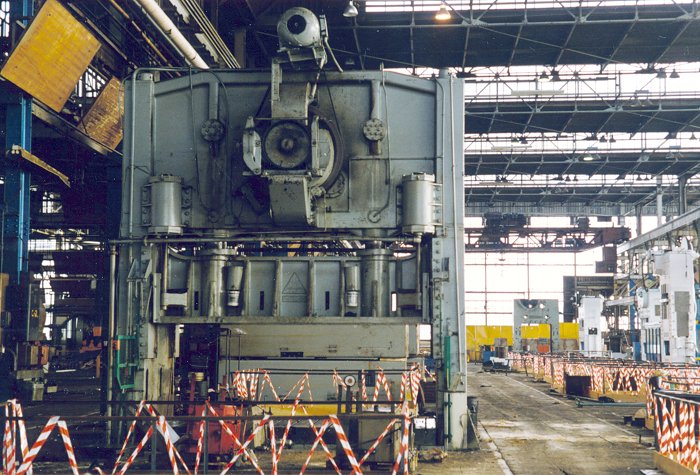
Another press awaits its fate.
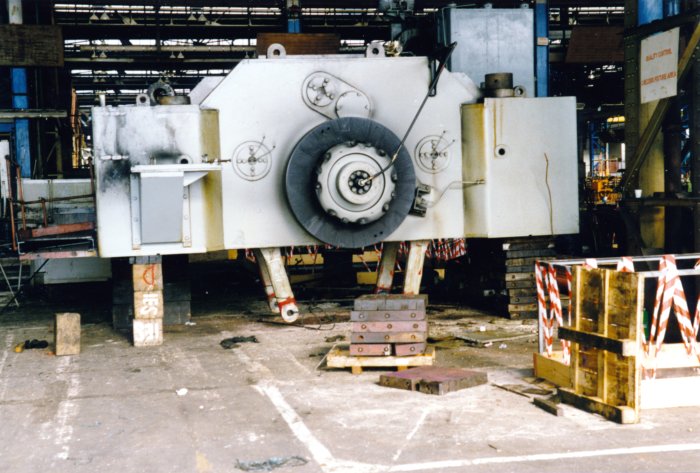
Another machine is dismantled.
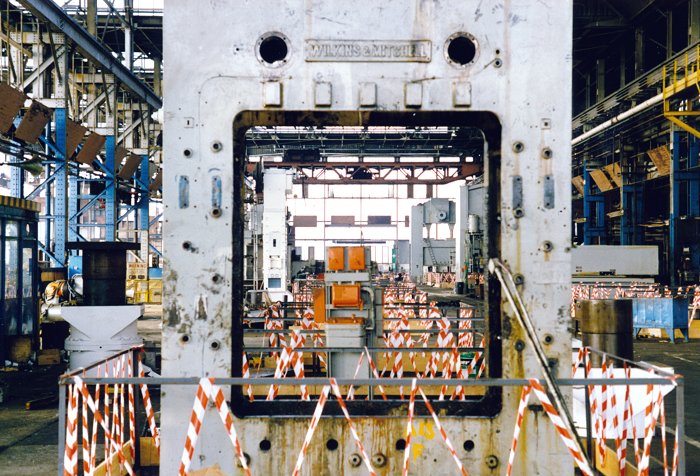
A final view of the press shop.
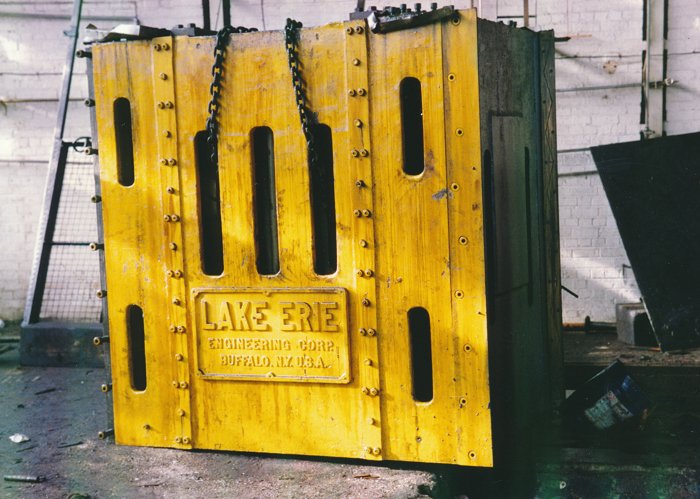
Part of a Lake Erie hydraulic press.
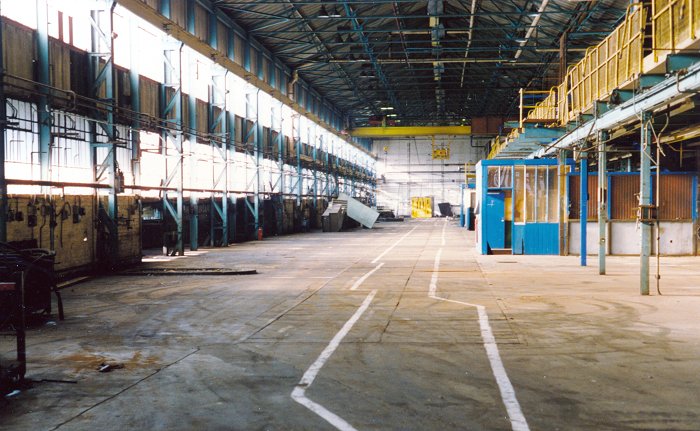
The press in the previous photo, now stands in an
almost empty shop.
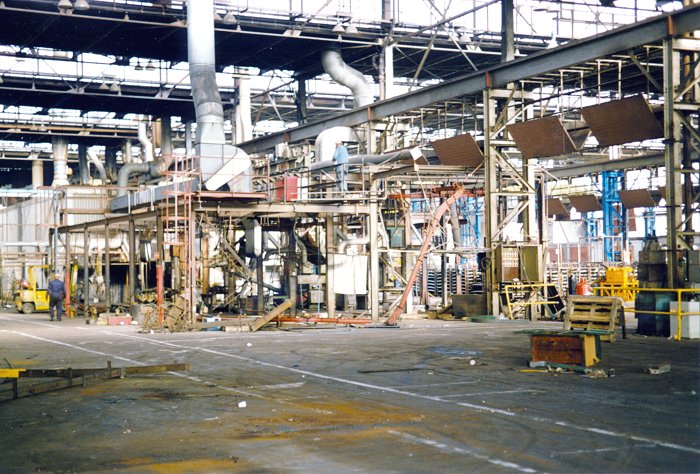
A general view, as the factory is dismantled.
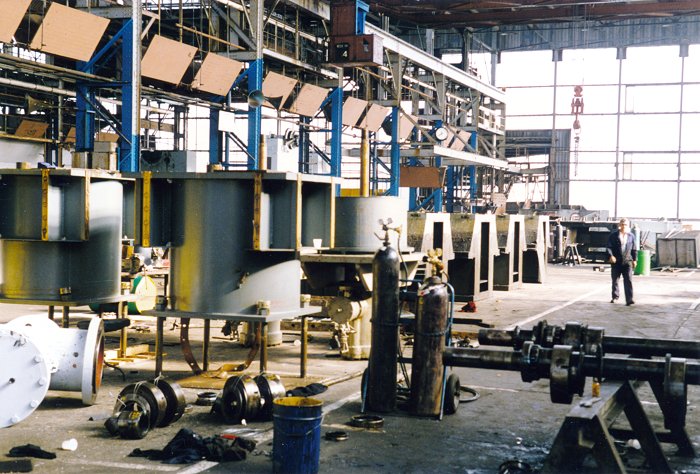
More machines are broken-up.
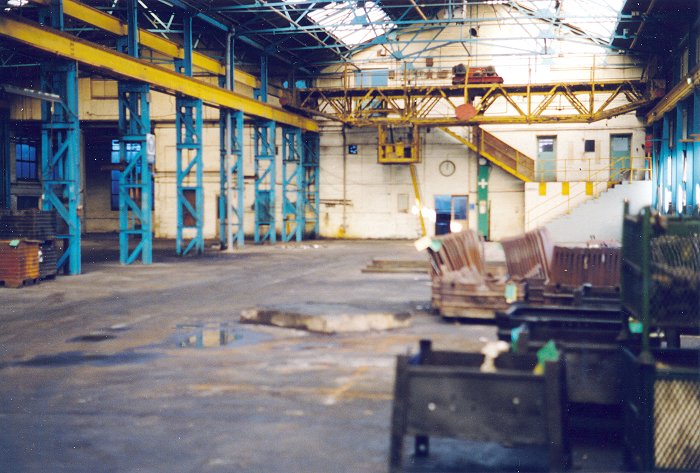
The overhead crane in another nearly empty shop.
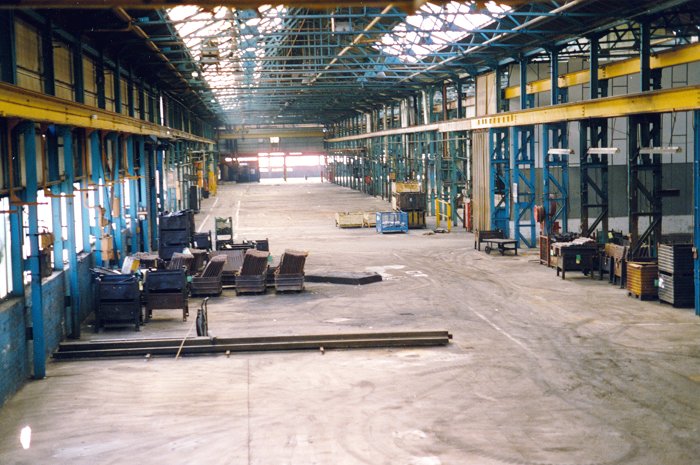
Another view of the same shop.
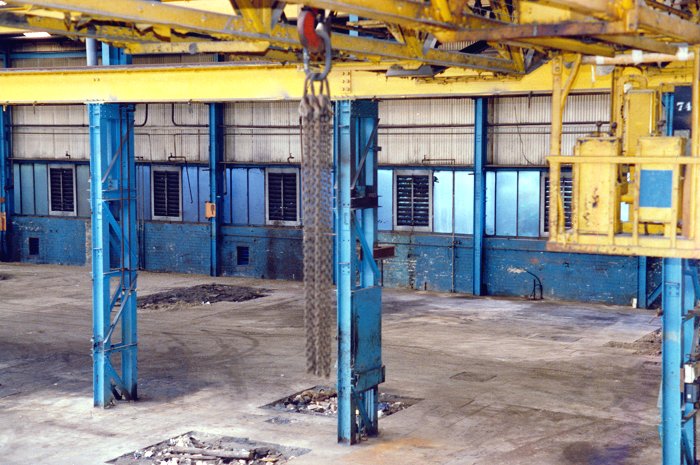
The end of the shop with part of the crane on the
right.
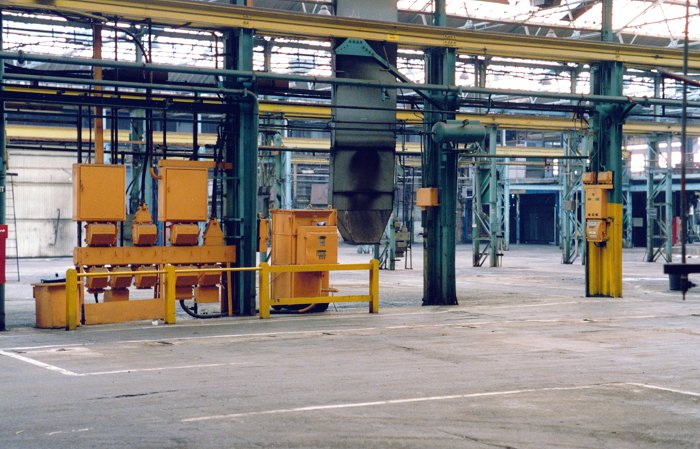
Some of the switchgear that once supplied power to
the machines.
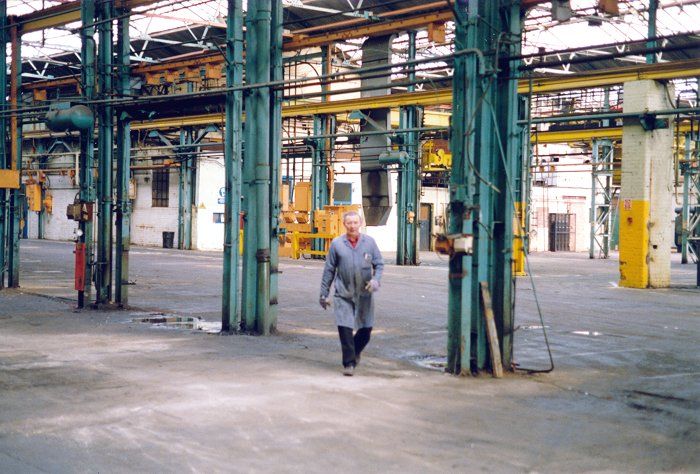
Another view of the shop and the switchgear, that
would soon be gone.
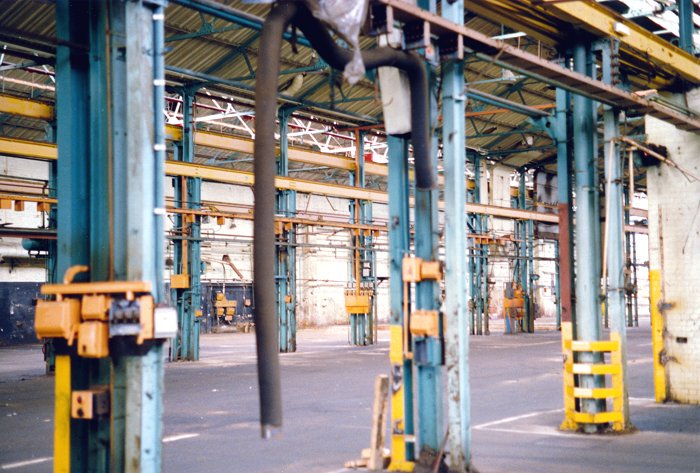
One of the other empty shops.
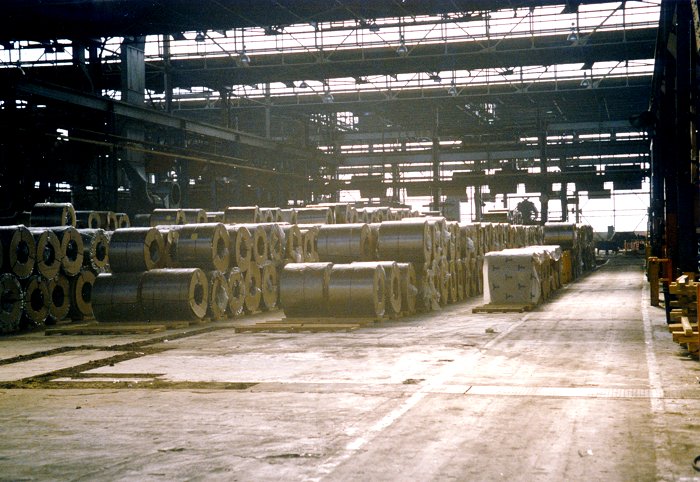
Steel rolls awaiting transportation.
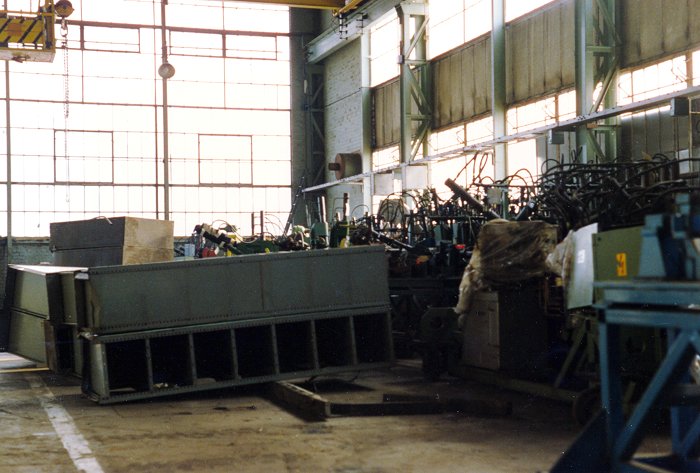
A pile of scrap awaits removal.
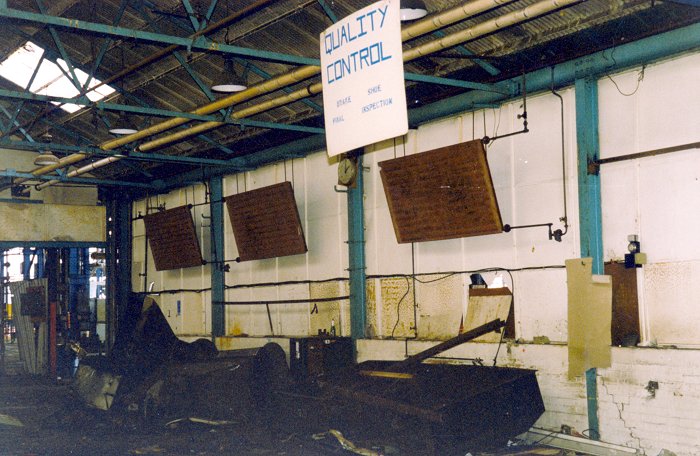
Another pile of scrap.
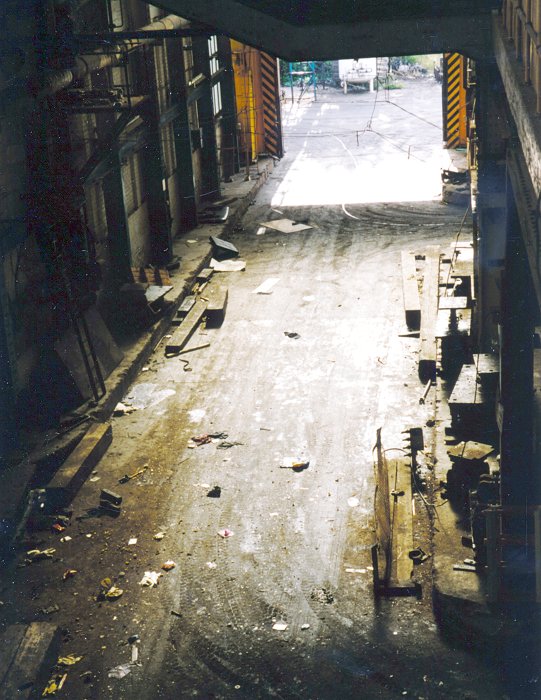
A final view of the almost derelict building.
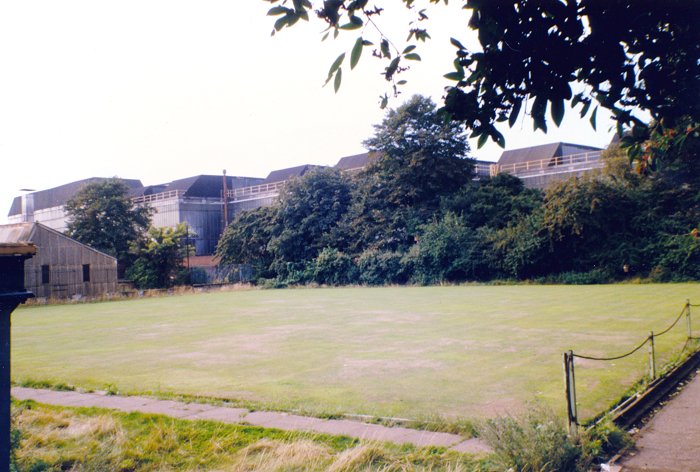
The exterior of the factory in its last days.
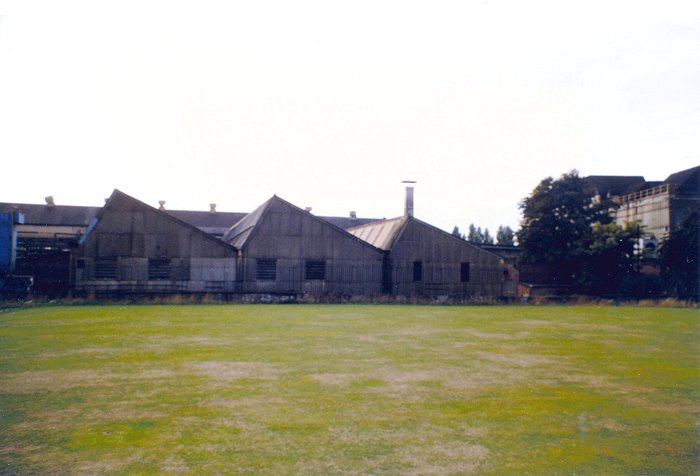
A final view of the factory, which awaits
demolition.
In 2001, Hadley Castle Works became GKN
Auto Structures.
In 2002, Ford and Massey Ferguson ceased to
produce tractors, so the main agricultural business came to an
end and GKN cabs division closed.
A small celebration was held
at Hadley Castle Works in 2004 to commemorate the 150th
anniversary of the founding of Sankeys.
At the time, around
1,600 people still worked on the site. The factory still
survives (December 2019) and is now part of GKN Aerospace.
In 2005 Corus closed the laminations
factory at Bilston with a loss of 190 jobs. |
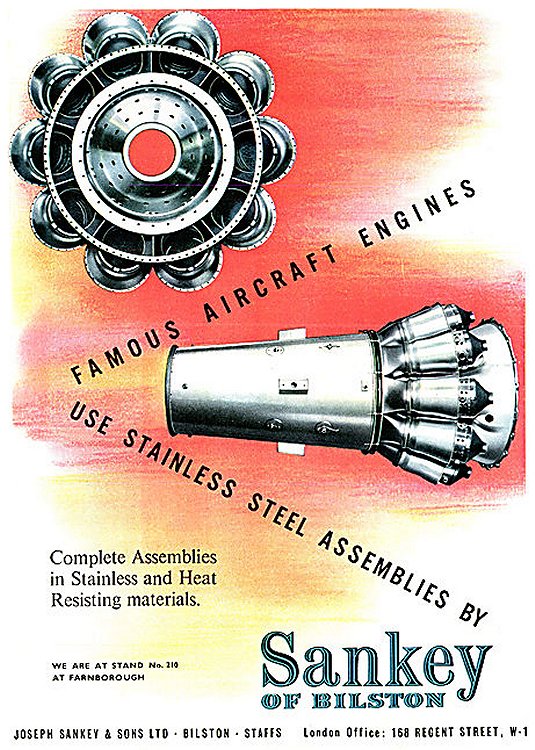
An advert from 1953. |
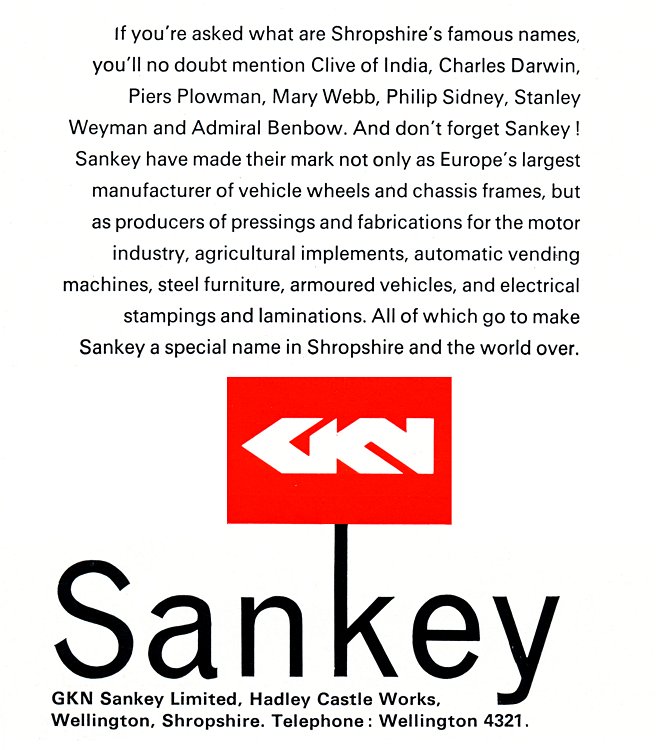
An advert from 1970. |
Social Activities
Sankeys had a good relationship with the
local communities in both Bilston and Wellington. Annual outings
were organised for employees and the staff canteen at Albert
Street opened in 1893. The firm contributed £25 a year to a sick
benefit club and a sports club was first founded in 1893. In
1935 land between Albert Street and Bankfield Works, that had
been purchased in 1921, was levelled for a sports field with a
pavilion for the Sankey Social and Sports Club, which opened on
the 6th June 1936. Entry to the social club was not restricted
to employees and so it became very popular with the local
population. There were dances with live bands, bingo, and social
groups including choirs, ballroom dancing groups, music groups,
and clubs focused on hobbies and leisure interests. Sadly the
Social and Sports Club closed in 1988 and the buildings were
demolished. The company had its own St. Johns Ambulance section
and a fire brigade. |
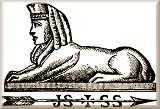 |
|
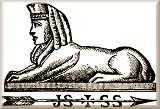 |
Return to
the
previous page |
|
Read
about Sankey's
art metalware |
|