A. G. Sutherland Limited was founded in 1912, and run by
Mr. A. G. Sutherland, and Mr. J. G. Sutherland.
The original factory in Pritchett Street, Birmingham was
opened for the production of dry gas meters, gas pressure
governors, and gas main taps. In 1913 Mr. A. E. Owen
acquired a controlling interest in the company, and two
years later the firm purchased the Standard Stamping &
Forging Company Limited run by Mr. J. E. Beaver. |
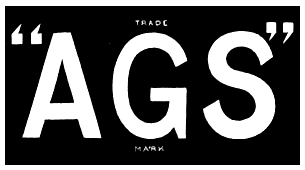
Trade mark. |
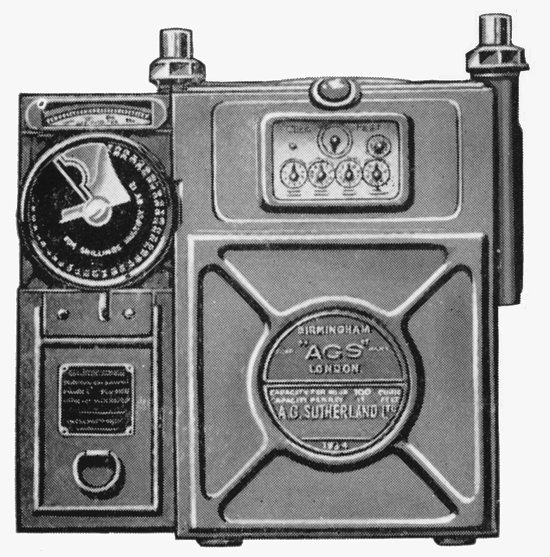 |
Three years later the business moved to
a new, purpose-built factory in Warwick Road, Greet,
Birmingham to produce domestic and industrial gas meters.
Mr. B. E. Mace became Managing Director
in July 1922, and remained in this role until December 1946
when he retired.
In 1920 another factory was built at
Battersea, in London. Soon larger premises were required and
so in 1928 a new factory was built at Summerstown, near
Wimbledon. The London operation was managed by Mr. A. G.
Sutherland.
|
Mr. Ben E. Mace in
the 1930s when he was Managing Director.
The photo was kindly sent by his
grandson, Peter Mace. |
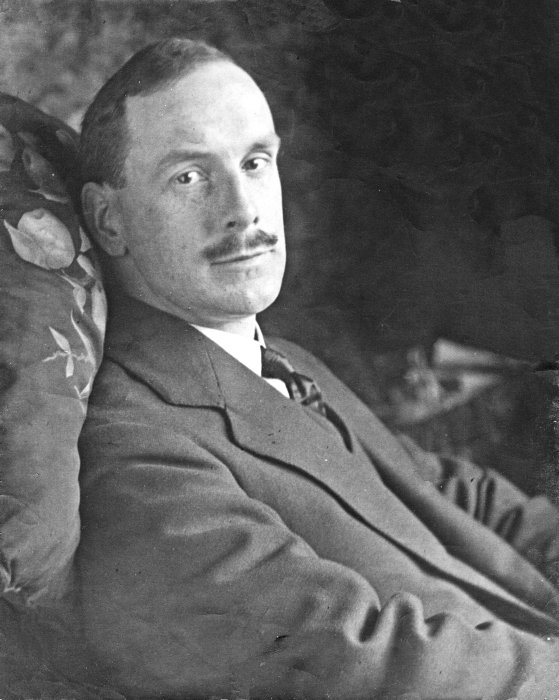 |
In 1937 the firm exhibited its range of
‘A.G.S.’ dry gas meters and meter components at the British
Industries Fair. |
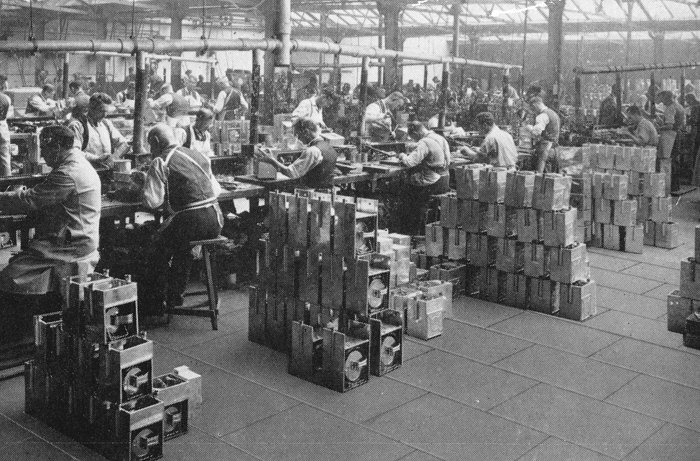
The meter assembly shop at Birmingham. |
Expansion continued with the building
of a new factory in Nottingham, which opened in 1938, and a
depot at Manchester in 1939.
They remained in operation until 1941
when they were both taken-over by the Government. |
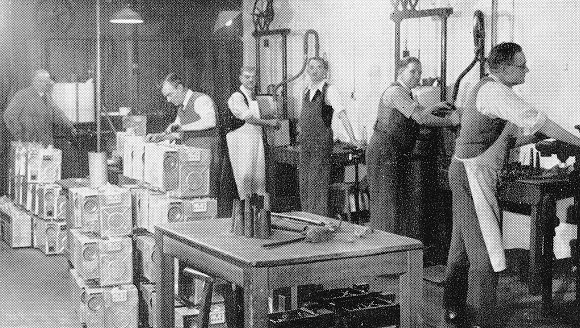
The final test shop in Birmingham.
Left to right: A. Francis, T. Reynolds, S. Slim, W. Tarpley,
and A. Davies. From the spring 1950 edition of the staff
magazine "Goodwill". |
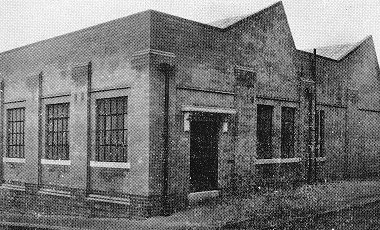
The Nottingham factory. From the
spring 1950 edition of the staff magazine "Goodwill". |
The firm constructed most of the
component parts for the gas meters including the sheet metal
work, the pressings, the hot forgings, and carried out its
own tool making and wheel cutting.
In the Second World War the firm undertook war
work, mainly for the Admiralty, producing ammunition boxes,
aircraft petrol tanks, light pressings, and forgings. |
After the war the firm returned to gas
meter production. All gas meters had to comply with the Gas
Meter Regulations as specified by the Ministry of Fuel and
Power. Each meter had to be officially tested and stamped
before or during installation.
Many of the meters were pre-payment
types, with a coin mechanism. Meters were produced to measure
from a few cubic feet per hour to 3,000 cubic feet per hour. |
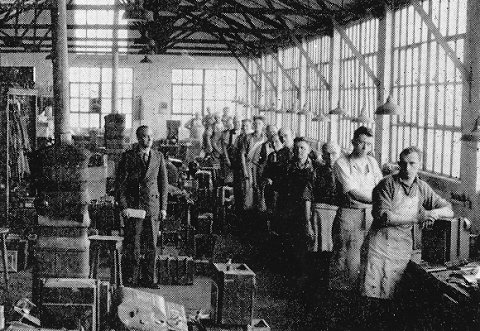
The repair depot in London. From the
spring 1950 edition of the staff magazine "Goodwill". |
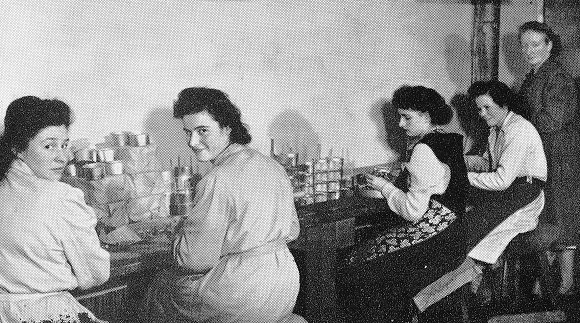
Assembling coin mechanisms in
Birmingham. Left to right: Rita Bradford, Lily Hill,
Barbara Baldwin, Dorothy Dyer, and Edie Roddy. From the
spring 1950 edition of the staff magazine "Goodwill". |
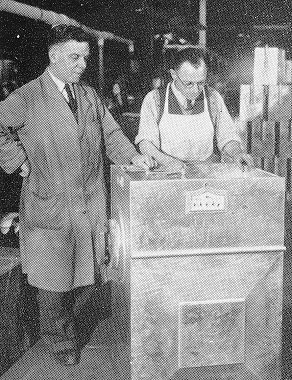
J. Bullivant and H. Lees
examining an industrial gas meter at Birmingham.
From the spring 1950 edition of the staff
magazine "Goodwill". |
|
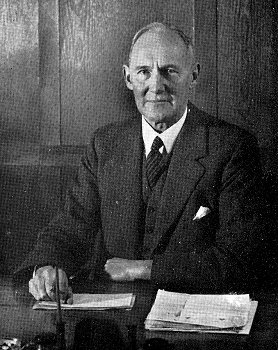
Mr. W. D. Cheshire,
Managing Director.
From the spring 1950 edition of the staff
magazine "Goodwill". |
|
The firm also produced copper electric cable soldering
sockets in a wide range of sizes, and hot stamped brass wing
nuts. By the 1950s the Managing Director was W. D. Cheshire. |
 |
Return to
the
previous page |
|