Bentley Hall Brick
Company Limited The company, founded on 28th
October, 1933, leased 80 acres of land from the Bentley Hall
Estate, on which to build a brick works, using the plentiful
supply of available clay. Production began in 1934, soon
after the completion of the kiln. In the following year the
company purchased the land from the Bentley Hall Estate,
plus an additional 3½ acres for
£10,000. |
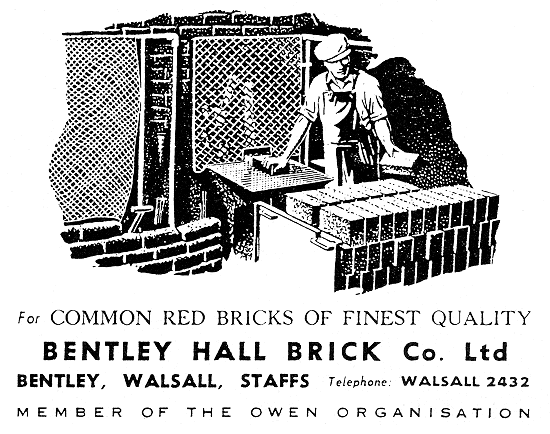
Production slowed during
World War 2 because of a shortage of labour, and the
reduction in house building. In July 1943 the works were
closed by order of the Ministry of Works as part of a
plan to concentrate production. In November 1944 Rubery
Owen & Company Limited acquired the business as part of A.
G. B. Owen's plan to build a garden village at Bentley. The
works reopened after the war, and the manufacturing process
was mechanised in order to increase production. The works
were situated to the north of the main Willenhall to Walsall
Road, beside where the M6 stands today. The manager was Mr.
G. Williams, and the company claimed to produce the finest
red bricks in the West Midlands. |
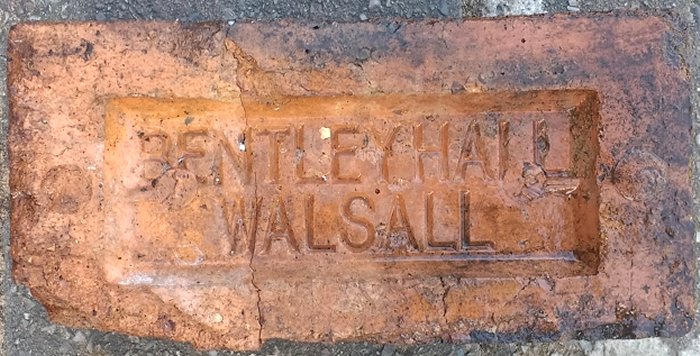
A Bentley Hall brick. Courtesy of
Paul Robinson. |
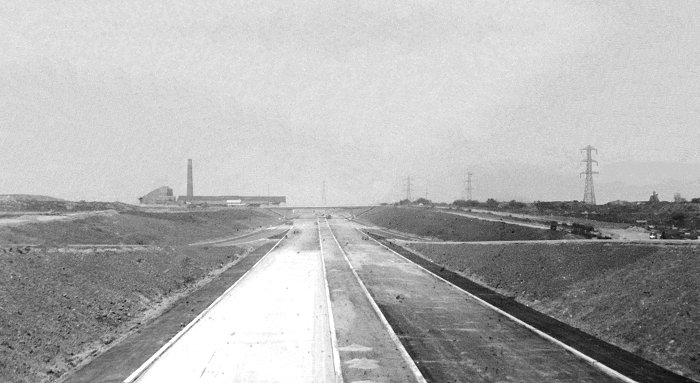
This photo, taken during the
building of the M6 Motorway at Bentley, includes the
once familiar view of the brickworks, that overshadowed
the motorway. |
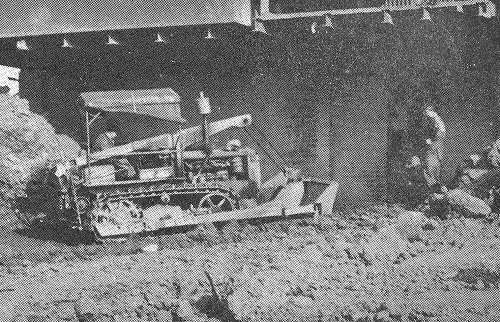
The bulldozer. From the Christmas 1947
edition of the staff magazine "Yuletide". |
The clay from which the bricks were made was delivered
to the works by a tractor, bulldozer, and scraper.
There were four automatic brick-making machines, each
capable of producing 1,150 bricks per hour.
The site also contained fine china clay which was also
exploited.
|
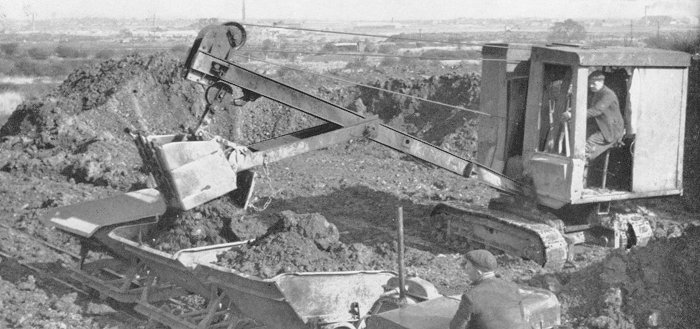
Another view of the bulldozer. |
There was a continuous Hoffman kiln with twenty two
chambers, capable of producing 170,000 bricks per week, and
two Scotch type open kilns, each capable of producing 20,000
bricks per week.
The drying and baking process in the electrically-powered
kilns took around twelve days. |
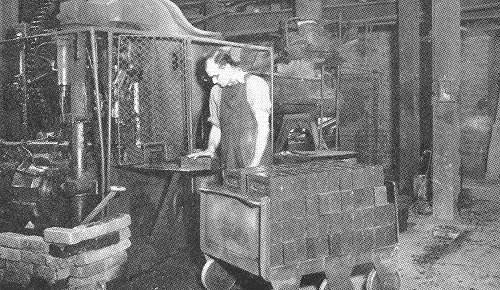
A brick-making machine. From the
Christmas 1947 edition of the staff magazine "Yuletide". |
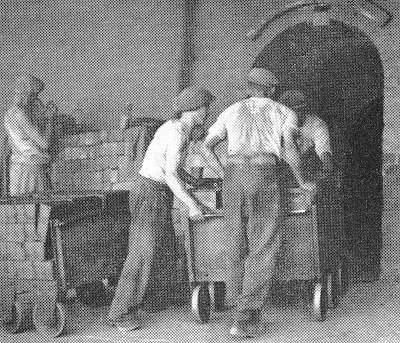
Loading a kiln. From the
Christmas 1947 edition of the staff magazine "Yuletide". |
Each chamber in the Hoffman kiln held around 18,500
bricks, each of which contained around one pint of water
which had to be completely dried-out before firing.
This was done by blowing them with hot air. The final
baking temperature was 960 degrees Fahrenheit. The total
output in a good week was around 210,000 bricks per week.
At the time, the bricks were the cheapest and most
efficient building material produced. They sold (ex-works)
for less than one penny each, or around one pound per ton. |
 |
Return to
the
previous page |
|