Sand, Clay, Bricks
and Pots George Ward (Moxley) Limited is a well
known firm which was a significant employer in the town.
It was the last in a line of manufacturers to exploit
the rich glacial sand and clay deposits in the Moxley
area. Some of the deposits were alongside the Walsall
Canal, which allowed heavy loads to easily be
transported at a time when many roads were simple dirt
tracks.
The fine-grained sand deposits were ideal for use in
moulding boxes in local foundries, making it possible to
produce accurately detailed castings. Sand from the sand
beds was used for casting as early as the late 18th
century by John Wikinson at his Bradley foundry and
ironworks.
For much of the nineteenth century the clay was used
for brick-making, at a time when there was a great
demand for bricks, because most of the local towns were
rapidly expanding. The many brick makers included the
Wood family (John Wood, Thomas Wood, and William Wood)
who ran Moxley Brickworks, alongside a small canal basin
in between Baggott's Bridge and Darlaston Road Bridge;
Hodgins and Bromley, brick and tile makers, and sand
merchants; Price's Brickworks; W. R. Price & Hewitt Lime
& Brick Works; Murby's Brickworks at Moorcroft Wood;
David Rose alongside the Albert and Moxley Ironworks;
Martin & Foster; and Baggott's Bridge Brick Works near
to Baggott's canal bridge.
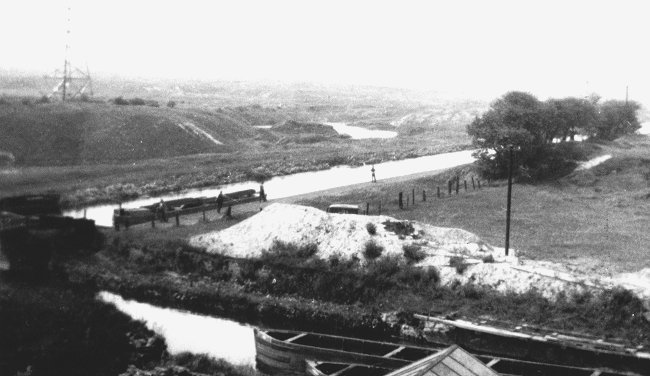
The canal basin that
ran into Wood's brick works. |
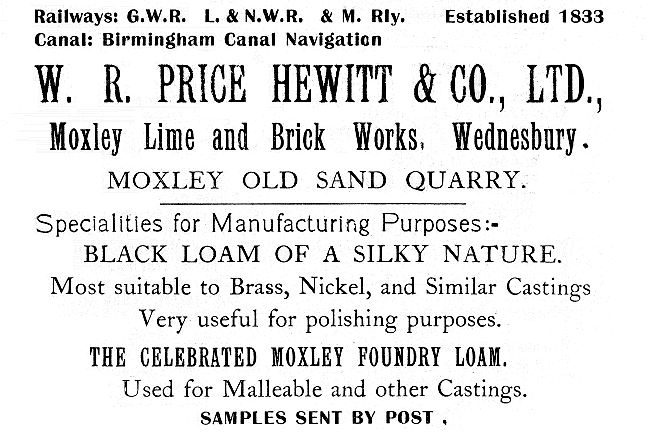
An advert from 1921.
Conditions in the early brickworks were
extremely basic, and work was hard. The report by the
Children's Employment Commission of 1864 includes the
following description of the girls who worked at Woods
Brickyard and David Rose's Brickyard:
At Mr. David Rose's Yard, Moxley.
Anne Wooley: I began when I was 15. I
mould now. I am 24. I am paid by the
thousand. I have 2 girls to carry clay.
One is going 16 and the other going 15.
I make about 2,000 bricks in a day. I
have to work the
whole time from 6 to 6 to do that. I
always stop half an hour for breakfast
and 1 hour for dinner.
The clay carriers at this yard had to
carry the clay from the bottom of the
pit to the tables at the top; the ascent
was about 10 yards in 70 yards.
At Mr. Wood's Yard:
In this yard the girls had to carry
the clay up a steep rise of about 12
yards in 50 yards.
Mr. J. Swindley, currier, Freeth
Street, Oldbury: I have lived in the
town 30 years. I am well acquainted with
the habits and conditions of the girls
employed in the brickworks. The
employment of young females at this work
is looked upon as a shame by all us
tradesmen. The girls have to do men's
work along with the men, I have often
been shocked to hear the language and
indecent talk among these girls when
they work. After their work is over
which is generally about six o'clock,
they dress themselves in better clothes
and accompany the young men to the beer
shops. They are a good deal in the habit
of spending their earnings in beer shops
with the men. They are ignorant of all
household work, and quite uneducated. |
|
|
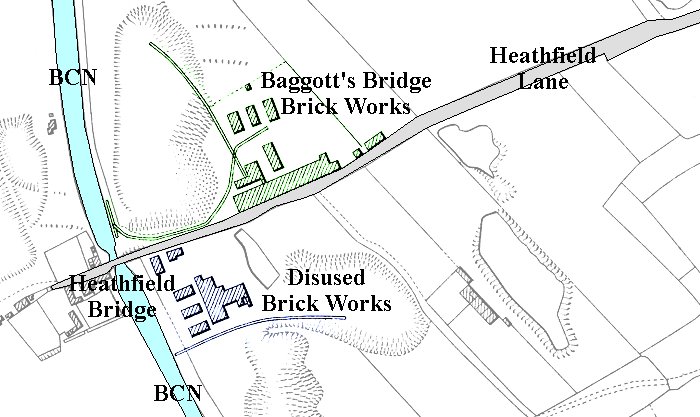
A map from 1901, based on the
Ordnance Survey map. At the time, Baggott's Bridge Brick
Works was run by Alfred Prosser, who is listed
as the owner in the Kelly's Staffordshire Directory of
1904 and again in 1912. Baggott's Bridge at the end of
Heathfield Lane, over the canal, was probably named
after the Baggott family who had a cottage and land on
the south side of the road, at its end. The owner in
1841 was Moses Baggott. The area was called Heathfield. |
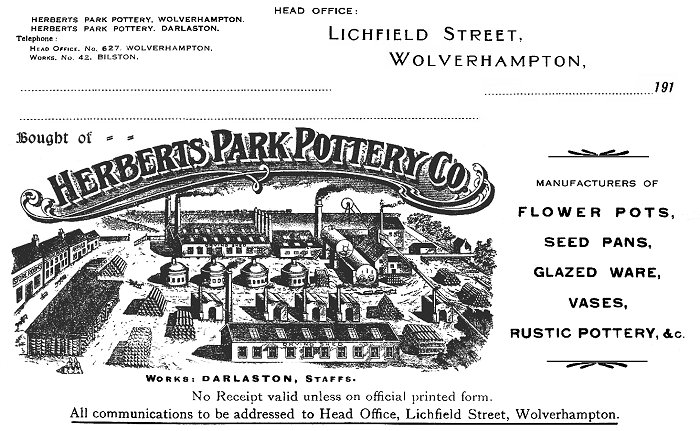
This bill head from 1910 to 1919
includes a good image of the site, with the canal and
Heathfield Bridge (also known as Baggott's Bridge) on the right. There were four kilns
and quite an extensive factory. In the 1921 Wednesbury &
Darlaston Blue Book and Directory, the site is listed
under two names, Prosser Brothers and George Ward. It
seems that George Ward initially purchased the disused
brick works on the southern side of Heathfield Lane and
later acquired the Herberts Park Pottery Company's site. |
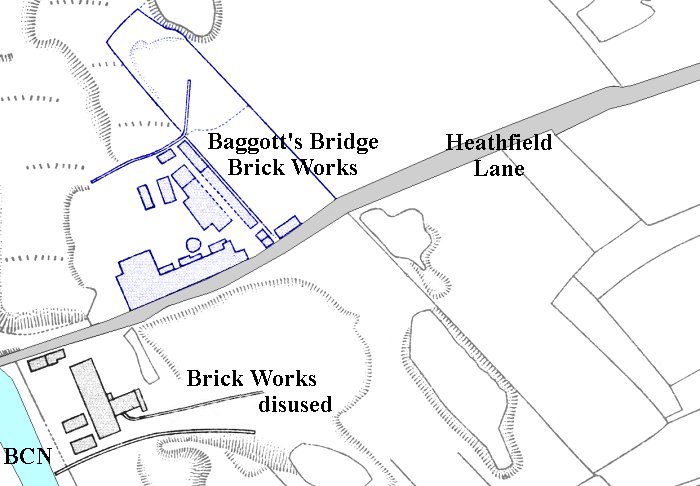
This map is based on the 1912
O.S. map on which the brick works to the south of
Heathfield Lane are marked as disused. |
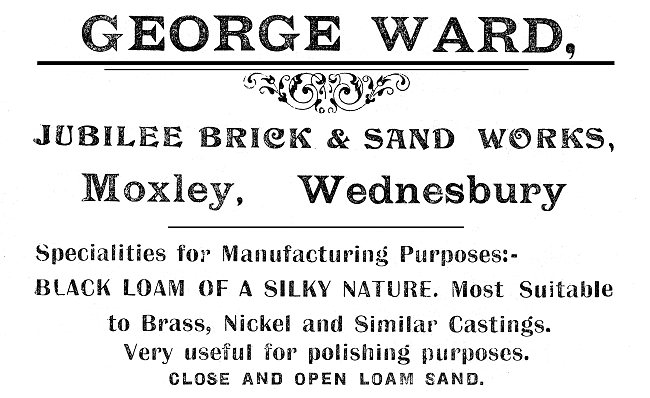
This advert is from 1921 when
George Ward ran the Jubilee Brick and Sand Works at
the site of the disused brick works on the map
above. |
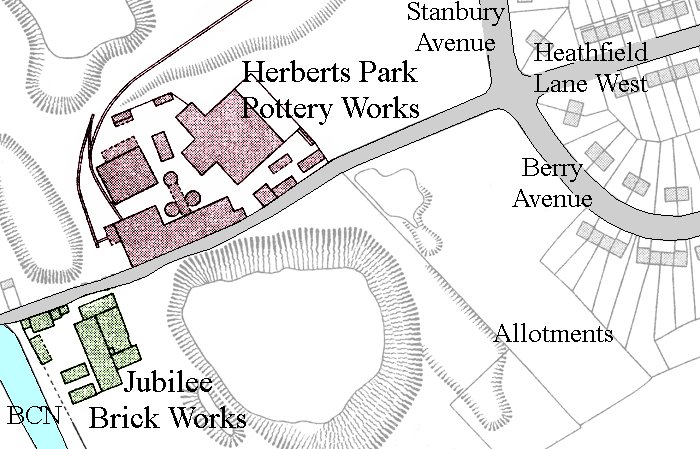
This map, based on the
1938 O.S. map, shows the Jubilee Brick Works and the
Herberts Park Pottery Works, both run by George Ward. |
Some time before 1920, George
Ward took over the disused brick works on the southern
side of Heathfield Lane and opened the
Jubilee Brick & Sand Works, producing bricks and
supplying sand to foundries, and for polishing.
This part of Heathfield Lane became Heathfield Lane West
when the council houses were built. |
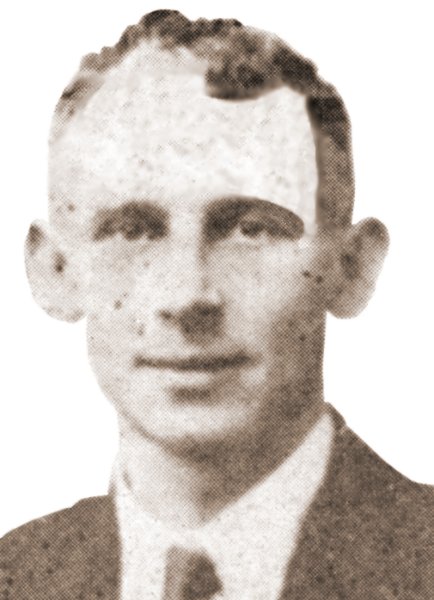
Edgar Ward. |
In 1920, George Ward was joined by his son Edgar, when
he had finished his schooling, first at Dorsett Road
Council School, then Queen Mary's Grammar School,
Walsall.
In the early 1920s the demand for bricks fell, and so
in 1921 Edgar developed a method of producing flowerpots
from the Moxley clay. Something that had been
unsuccessfully attempted previously.
The firm then began producing flowerpots, which were
very popular and sold in large quantities.
Edgar was also a member of Darlaston Council. He
represented the Catherine's Cross Ward, and lived at
Marlborough House, 59 Moxley Road, Darlaston.
In the late 1930s the family moved to 8 Ednam Road,
Wolverhampton and called their new house 'Darlas'. |
In 1927 Edgar returned to his old school in
Dorsett Road to ask the headmistress if one of
the forthcoming school leavers would be suitable
to work for him and his wife as a housekeeper,
who would also look after his son, Edgar. My
mother got the job and worked for the Ward family for many
years, also looking after Edgar's younger
brother Malcolm.
She later worked at Ward's factory making
pots.
My grandfather also worked there in the
1930s, in the clay pit. |
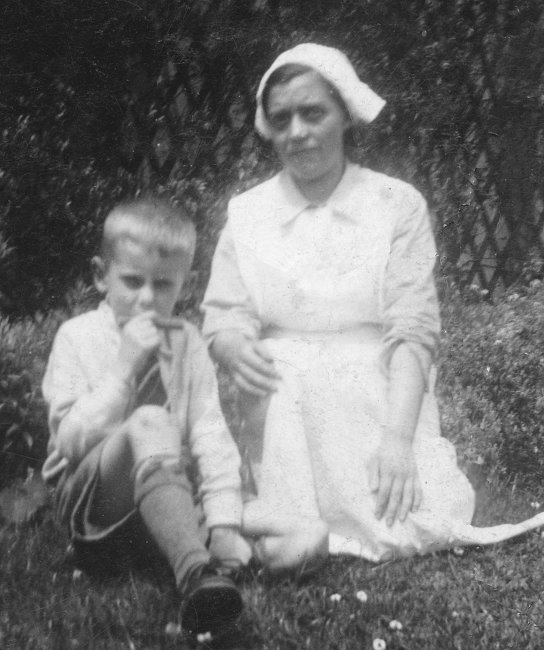
Young Edgar Gordon Ward,
playing his harmonica. Sitting next to my
mother, Daisy. |
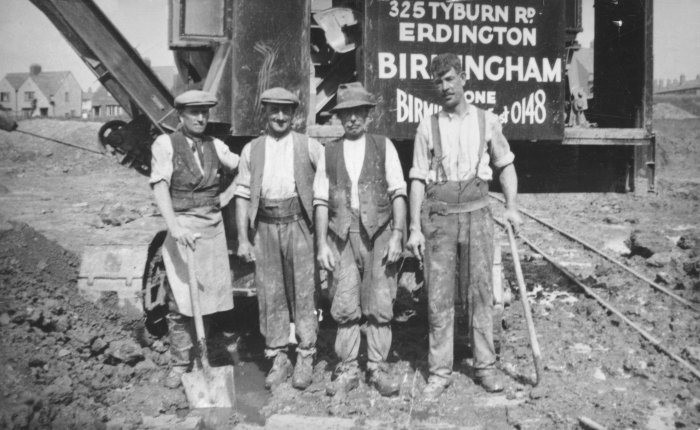
Digging clay in the clay
pit. Second from the right is my grandad Henry
Flavell. On the far right is the foreman, Jack
Kimberley. The crane was known as 'The Devil".
The houses in the background are in Berry
Avenue. |
On the 29th October, 1973, some members of the
Ward family founded a private limited company called
Topfpots Limited. The company manufactured plastic
products including plant pots. The directors were
Edgar Ward, Muriel Ward (Malcolm Ward's wife), and
Peter Ward. The nature of the business quickly
changed. Clay pots continued to be produced for a
while, but were slowly phased out. At the end there
were only eight employees in the factory. Edgar
Ward retired in 1994 and spent his last day at work
with my mother as a guest at the factory. He settled
down to retirement in Trevean Way, Newquay, Cornwall
and eventually returned to the West Midlands, living
in Sunrise care home in Wergs Road, Tettenhall.
Sadly he died on the 28th May, 2020, at the age of
93.
His younger brother Malcolm Beverley Ward, born
in May 1931, became a Circuit Judge and lived with
his wife, Muriel, in Lothians Road, Tettenhall. He
was also a director of Wolverhampton Grammar School
Limited. Sadly he died on the 1st March, 2020, at
the age of 88. His wife Muriel Winifred Ward, died
on the 19th December 2018, at the age of 87. |
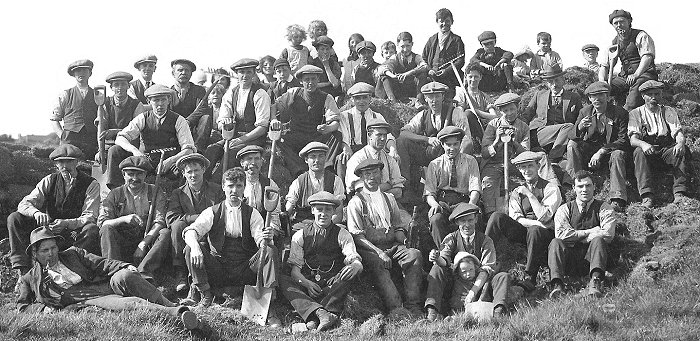
Workers at Ward's clay pit in the
1930s. Courtesy of John & Christine Ashmore. |
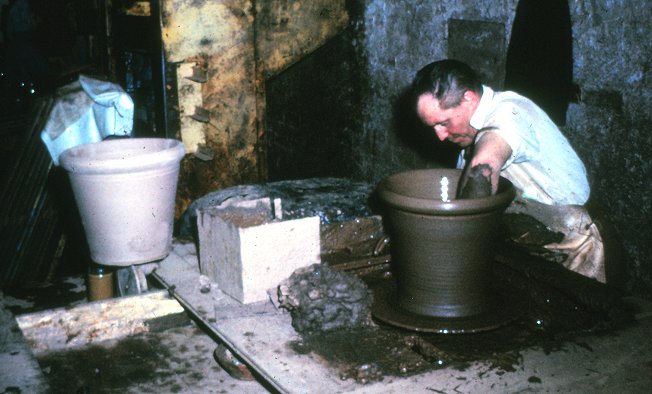
Producing a large pot on the potter's
wheel.
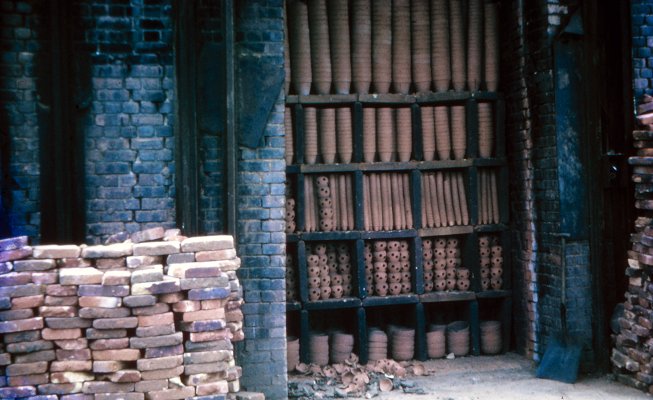
The fully-loaded kiln.
Over the years, Wards produced all kinds of traditional clay pots
and became well known for their high quality products.
Eventually the firm moved with the times, adding plastic
pots to the product range. They were a
cheaper product and finally-took over from the clay
pots.
Wards had three rotational moulding machines, and
around 20 injection presses, mostly Windsor machines.
Most of the products were made from polypropylene or
high density polyethylene.
The later product range consisted of moulded
plastic plant pots, planters, propagators and watering
cans, much of which was exported.
The firm was finally taken over by Plysu in 1997.
After which production at Darlaston ended. The site
has now been redeveloped into a housing estate. |
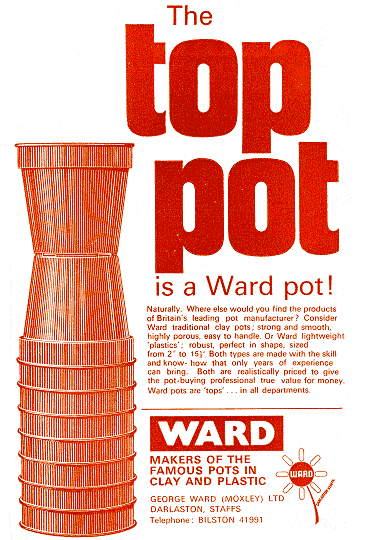
An advert from 1972. |
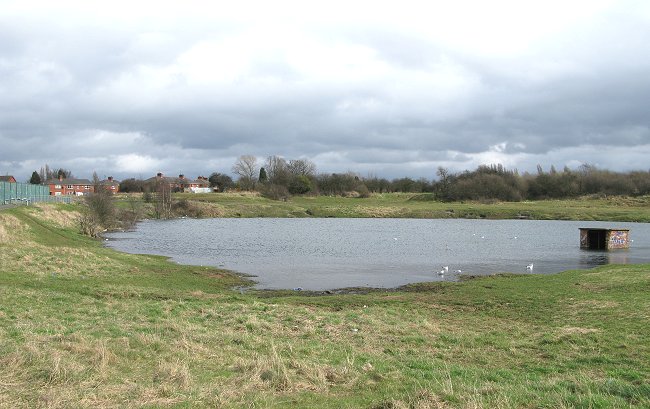
Ward's clay pit in 2008. |
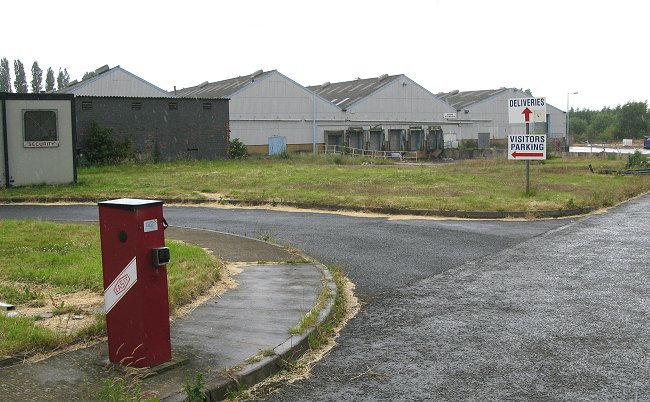
The factory in 2008. |
 |
Return to
the
previous page |
|