A Prefabricated Home of
Your Own
In the 1930s and 1940s the country
suffered from a severe housing shortage, which resulted
in large numbers of new houses being built. In the late
1940s one solution to the problem was to build
prefabricated houses consisting of a kit of parts that
were built in a factory, and taken to the building site
for rapid erection. Darlaston’s largest engineering
firm, Rubery Owen & Company Limited realised that a
lucrative market existed for cheap factory-built houses,
and so the company’s Structural Department began to
produce good quality houses for sale to local
authorities and building companies. |
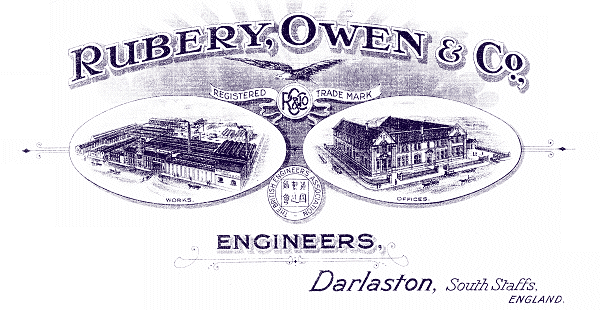
Background
In the late 1920s and early 1930s
large numbers of people still occupied old Victorian
slums, which had few modern amenities. The 1930 Housing
Act introduced a five year programme for the clearance
of slums, with designated Improvement Areas. Local
authorities were required to provide suitable housing
for anyone whose home was demolished in the slum
clearance. This led to the provision of council housing.
As a result of the Act a total of 19,840 houses had been
demolished by the summer of 1934.
Although many houses were built in
the 1930s, the problem still remained, and was made
worse by the increasing population. The building
programme temporarily came to an end at the outbreak of
the Second World War, and didn’t start again until the
war ended in 1945. During the war thousands of houses
were destroyed by enemy bombs, which made the problem
even worse. In 1945 it was estimated that around 750,000
new houses were required.
The post-war Labour Government
instigated a housing programme that relied on local
authorities to provide the much-needed housing, and
large building projects were soon underway. Part of the
solution lay in the large-scale construction of
‘prefabs’, a scheme that was instigated by the
government’s Temporary Prefabricated Housing Programme.
Most of the ‘prefabs’ were small
factory-built, single storey temporary bungalows with a
life expectancy of just 10 years. Although around
156,000 of them were built, there was still an acute
housing shortage. Local authorities still had to provide
a range of houses to cater for different sized families,
and so the conventional ‘prefabs’ could only fill part
of the housing gap.
The Rubery Owen houses, unlike the
basic ‘prefabs’, had a very long life expectancy, and
offered the inhabitants a more spacious, and comfortable
lifestyle. They were also ideal for larger families.
Rubery Owen Houses |
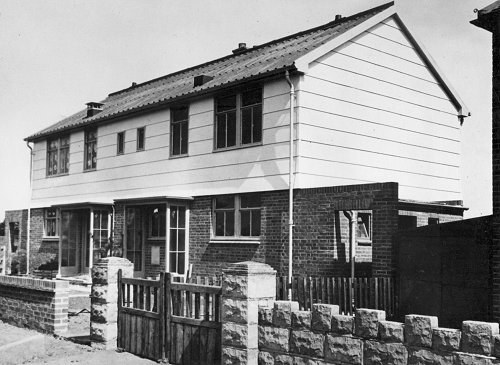
A Rubery Owen prefabricated house. |
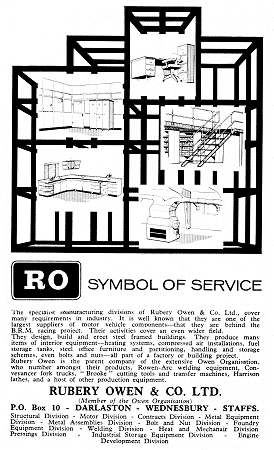
An advert from the mid 1960s. |
Rubery Owen was in an almost unique
position to produce factory-built houses. The company’s
Structural Department had been responsible for a number
of prestigious developments including the London
Passenger Transport Offices in Westminster (the tallest
building at the time in London); the Palace Court Hotel
in Bournemouth; and numerous factory buildings.
The company also produced a
considerable number of domestic items such as stainless
steel and vitreous enamelled sinks, and cupboard units.
The company’s wealth of technical
knowledge and practical experience came together to
produce a good-sized building that struck a balance
between the sound methods of traditional building, and
the ease and speed of erecting factory produced units.
The architects were A. T. and
Bertram Butler of Dudley and Wolverhampton who were
responsible for many of the area’s landmark buildings
including Dudley’s Technical College, Station Hotel, and
the Guest Hospital. |
The houses were built around a rust-proof light
steel frame with stanchions, trusses, and beams of a
substantially rectangular form.
To simplify and speed-up the building process, the
design included simple forms of attachment for almost
any suitable building material.
The individual members of the steel structure were
produced by bending, pressing or rolling, and the
individual components were welded together at the
factory. |
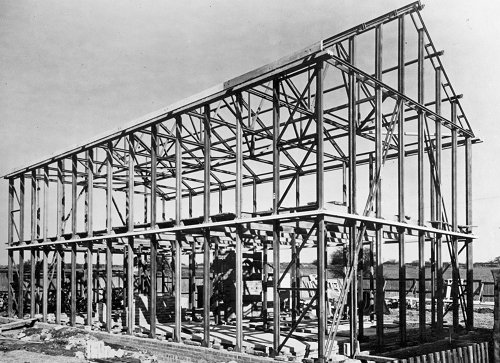
The light steel frame. |
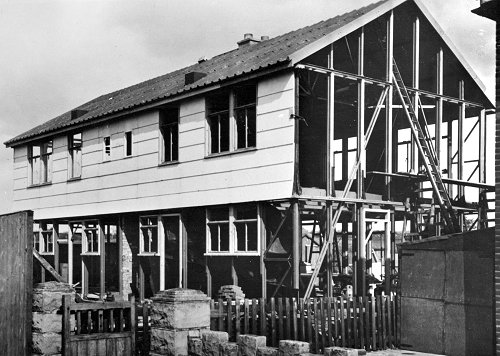
A partially-built house showing
the steel frame beneath the external cladding. |
On the building site the individual and lightweight
sections of the steel frame could be simply bolted
together, and the large floor, wall, ceiling, and roof
panels quickly added, so that the building could be
assembled in a very short time.
The total weight of the steel frame was 1¾ tons per
house, and the maximum weight of each section was 80
lbs.
As a result there was no difficulty in transporting
the various parts to the building site. |
Several versions with minor differences were
produced. The type 'B' and the type 'C' are shown below: |
The type 'B' has a downstairs
toilet and a fuel bunker on the side of the house. |
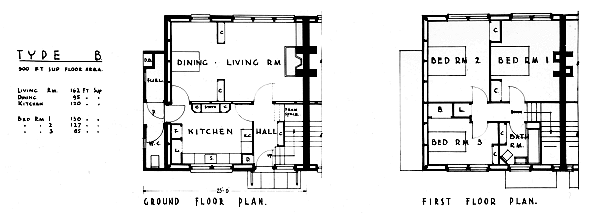 |
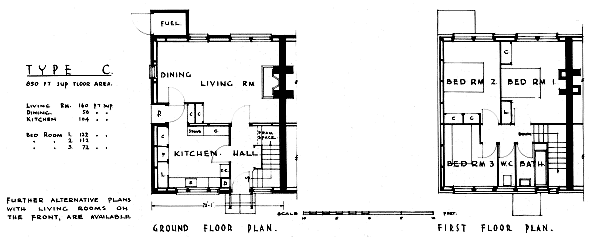 |
The type 'C' has an upstairs
toilet, a slightly shorter third bedroom, and a fuel
bunker on the back of the house. |
The type 'B' ground floor plan
showing the open-plan living room and dining area, the
kitchen with its built-in cupboards, the compact
staircase, and outside toilet. |
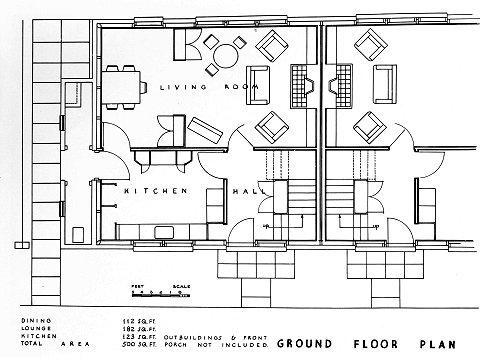 |
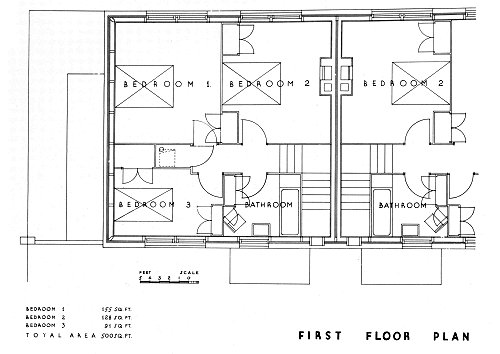 |
The type 'B' first floor plan
showing the reasonably sized bedrooms and bathroom, with
fitted cupboards, and the landing cupboard; presumably
an airing cupboard. |
Conventional concrete and brick
foundations were used with pockets to receive the
holding-down bolts for the steel stanchions. The bolts
were positioned using a steel template that came with
the kit of parts. The base of the steel frame was
mounted on a slate damp-proof course, set in
cement. The wooden sub-frames and steel casements for
the windows were bolted to the stanchions, and an 11inch
brick cavity wall was added to provide the necessary
sound insulation.
The roof could be covered
immediately after the frame was erected with coloured
combined asbestos sheeting, and the pre-formed
light-gauge steel staircase quickly added. The staircase
was fitted with wooden treads and risers at the factory,
and transported to the building site in three sections.
The plumbing and electric wiring
were also pre-fabricated in the factory. Every room had
at least one power point, and each house came complete
with a wireless earth and aerial. The kitchen and main
bedroom had points for extension loudspeakers, and fixed
electric fires were fitted in the dining recess, bedroom
number 2, and high-up in the bathroom. |
The kitchen included the following
fittings:
A slow combustion stove.
An electric cooker.
A refrigerator.
A wash boiler.
A sink and double drainer unit with cupboards below.
A larder.
A china and dry store.
A cupboard for a broom and cleaning materials.
The slow combustion stove provided
hot water, and heated bedrooms 1 and 3 via hot air
ducts.
It also heated the dining recess
and living room via a coil that was fitted in the dining
recess area. |
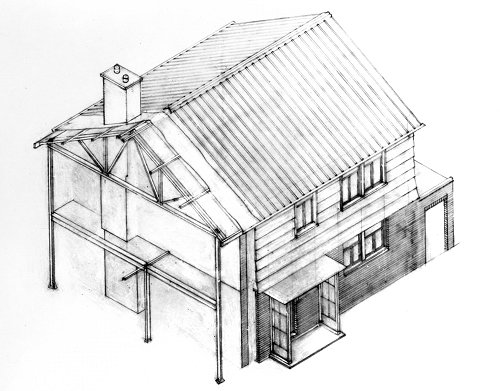
A partially completed house
showing the roof covering, with the garden gate and wall
on the right. |
Wet construction processes were
kept to a minimum to ensure that assembly could be
undertaken in all weathers.
The end result was a comfortable,
reasonably sized family home that was much faster to
build, and far cheaper than a traditional house, and more
spacious than a conventional ‘prefab’. |
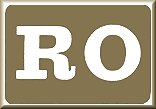 |
Return to
the
previous page |
|