 |
Backyard Industries
In the late seventeenth and early
eighteenth centuries, Darlaston town must have reverberated
to the sound of industry for the first time when nail makers
began hammering in their small backyard workshops.
The industry was made possible by the
invention of the slitting mill in 1565. This was a watermill,
where bars of iron were slit into rods which were passed to nailers, who made them into nails by adding a point and a
head. The slitting mill was probably invented in Belgium,
and first appeared in England in 1590 at Dartford in Kent.
The first local slitting mill was built on Cannock Chase in
about 1611, and others soon followed along the River Stour
between Stourbridge and Stourport, where they used iron
transported along the River Severn to produce rods for the
Black Country nailers.
|
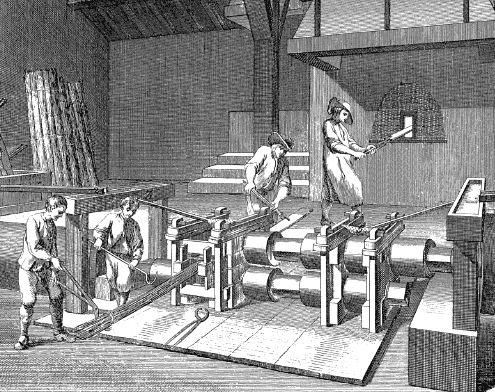
An early slitting mill. |
The slitting mill had two sets of
water-powered rolling mills to convert flat bars of iron,
about three inches wide and half an inch thick, into rods.
Pieces were cut-off the bars by shears powered by a
waterwheel, then heated in a furnace before passing between
flat rolls to produce a sheet of the required thickness.
The
sheet then passed through the second rolling mill where
cutters with intersecting grooves slit it into rods. |
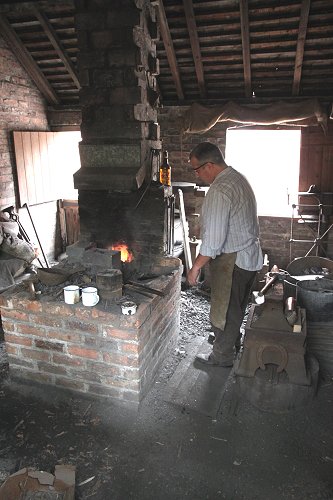 |
|
 |
An
impression of a local backyard nail shop can be
obtained from the the nail shop at the Black
Country Living Museum. It has a typical hearth,
but the nails are hand-forged without the use of an
'oliver'. |
|
By 1710, Darlaston had 23 nailers
producing a wide range of nails including brads, tacks,
spriggs, dog-eared frost nails, sheath nails, and sparrables.
The rods were advanced to nailers, who converted them into
nails, and then returned them to the mill for payment. A
bundle of rods weighed sixty pounds and was usually four
feet six inches long. The nails were characterised according
to the number produced from a given weight of iron. Long
thousand (1,200) nails weighing 4 pounds, were known as four
penny bundles. Larger nails were called ‘one hundred work’,
and were priced by the hundred. They were more profitable
than the smaller ones, as less work was required to
manufacture them, and less waste produced. |
This was the first type of mass
production in the town. Large quantities of nails could be
simply made by unskilled people, who often had a second
occupation such as farming.
Frederick Hackwood, the local
historian, stated that in 1780 there were between 35,000 and
40,000 nailers in the Black Country.
A typical workshop was
only just big enough to house the hearth, bellows, and
‘oliver’ hammer. It usually had an open widow with bars, and
a low ceiling, just high enough to accommodate the return
spring pole of the treadle-operated hammer.
The introduction of machine nailing in
1810 led to a further increase in the number of people
employed in the industry, but by 1888 there were no nailers
left in Darlaston, because of the preference for light
engineering. |
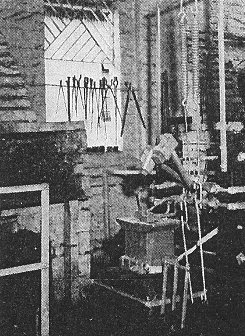
An 'oliver' with two
hammers. |
Gunlocks
The town also had a large number of
small backyard workshops used for the production of gun
locks and barrels, which were supplied to the gun
manufacturers in Birmingham. This was the first large-scale
skilled occupation in the town. It was very much a family
affair with skills being handed down from father to son.
Gunlock makers usually supplemented their income by doing
other types of work, because the gun trade suffered from
periods of depression. In the late 1750s there were between
300 and 320 gunlock filers, 50 to 60 gunlock forgers, and
250 boys employed as filers, gunlock forgers, cock stampers,
and pin forgers.
A 14 hour working day was usual, and
the truck method of payment often used. During the
Napoleonic wars, the Birmingham gun trade supplied over 3
million gun barrels, and 2.8 million gunlocks to the British
Government. The largest recorded production in a single year
was 490,838 gun barrels, and 457,616 gunlocks, in 1813.
After the Napoleonic wars had ended in
1815, demand fell and Darlaston went into a severe
depression, which lasted until 1839. The remaining trade was
mainly confined to the export market and sporting guns. By
about 1870 the development of machine made locks had
virtually eliminated the trade in Darlaston, which had
however, produced a skilled pool of metalworkers. This can
be seen in the 1818 edition of Parson & Bradshaw's Directory
which lists the following products that were made in the
town: bridle bits, buckles, bullet moulds, carpenter's
tools, dog collars, files, fire irons, guns, gunlocks,
handcuffs, harness buckles, hasp locks, nails, padlocks, and
trunk locks.
|
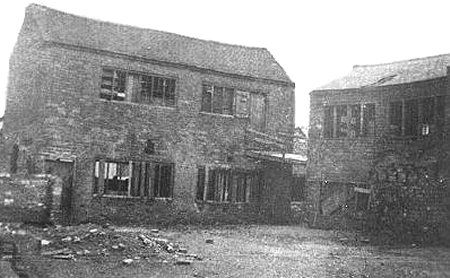
One of the last remaining gunlock
workshops in the town. |
By 1801 the population of 3,812
included 1,325 people employed in trade, manufacturing, and
handicrafts, and 2452 people in other employment.
Only 35
people still worked in agriculture. |
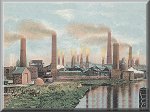 |
|
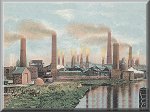 |
|
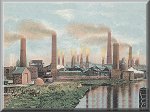 |
Return to
Early Iron-Making |
|
Return to
contents |
|
Proceed to
Heavy Industry |
|