The Black Country was ideally
situated for the production of iron, especially from the late 18th
century, through to the 20th century. Demand was
extremely high in the many manufacturing industries that
soon appeared and the raw materials consisting of coal,
iron ore, and limestone were all available locally in
vast quantities. Thanks to the building of the large
canal network, some good roads, and the coming of the
railways, transporting heavy iron products was
relatively fast and cheap. Many people worked in the
ironworks. It was estimated that in Dudley alone, around
500 men and boys worked in iron production in 1852.
The main producers of iron in
Dudley
Blowers Green Iron Works was
established in 1800 by the Grazebrook family and by 1844
around 177 to 180 tons of iron were produced each week.
In 1851 the business was run by Michael and William
Grazebrook.
Buffery Furnaces had two ironworks,
Old Buffery Furnaces and New Buffery Furnaces. The
ironworks were located beside Bumble Hole Road,
Netherton and a short branch of the Dudley Canal that
ran north westwards from the Bumble Hole. Old Buffery
Furnaces was started by Samuel Ferriday who ran Ferriday
& Company. The business was declared bankrupt in 1817.
It was later run by Richard and Edward Salisbury. By
1855 it had been taken over by Joseph Haden, but had
closed by 1865. New Buffery Furnaces had opened by
1817 and were run by Wainwright and Jones. The factory
had closed by 1886. |
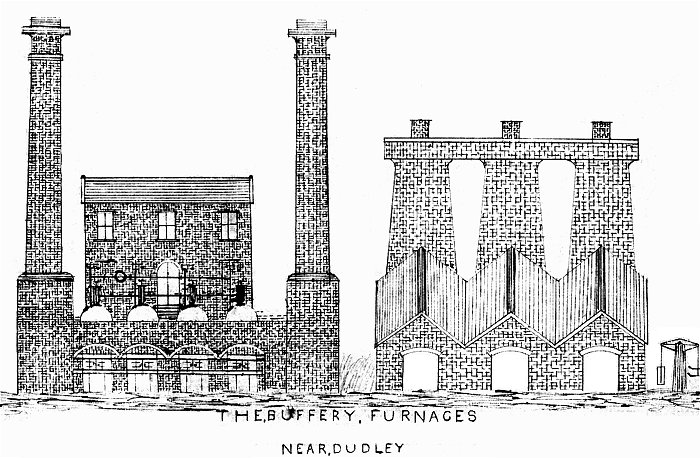
This drawing, made by J. N.
Onslow in 1913 was owned by the late David Evans.
David was unsure about the accuracy, but they are
the only images of the furnaces that are known to
exist. |
Dixons Green Ironworks was run by
William Haden from 1835 until 1867. It had only one
furnace and closed down in 1873. |
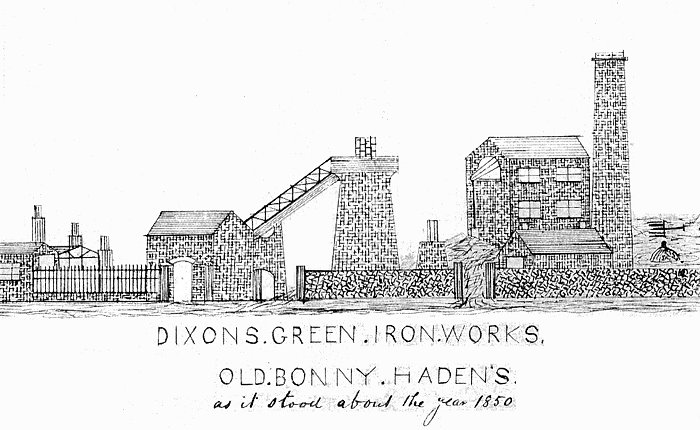
Another drawing, made by J. N.
Onslow in 1913 that was owned by the late David
Evans. |
Hingley & Smiths Ironworks was
opened in 1847 by William Jefferies at Harts Hill. In
1848 an iron boiler exploded, killing 40 men and boys.
In 1881 it became known as Hingley & Smiths when Noah
Hingley & Sons Limited acquired the business.
Old and New Netherton Iron Works. The Old
Netherton Iron Works was originally known as The
British Iron Company. The Old and New Works later
worked in conjunction and in 1844 were producing
around 180 to 190 tons of iron each week. In 1845
the business was run by Benjamin Best and by 1851
the agent was George Thompson. The business was
later taken over by Noah Hingley. The New Iron
Works produced around 18,000 tons of pig-iron per
year, which was sent to the Old Works for conversion
into the iron that was used at Hingley’s factory.
Parkhead Furnaces was
run by Parks & Company in 1806. In 1843 the business
was taken over by Edward Evers. It was a small scale
affair producing just 70 to 75 tons of iron per
week, with one furnace that used the hot blast
system. The business was still in existence in 1851.
Russell's Hall Ironworks
was run by Samuel Holden Blackwell and his father
John Kenyon Blackwell in
1827. Russell's Hall Works was known as ‘The Dock’
and in 1844 was producing around 210 to 220 tons of
iron each week. John Kenyon
Blackwell retired in 1848 leaving his son Samuel in
charge. Samuel had been born in Worcester on the 8th
May, 1816 to John Blackwell and his wife Elizabeth.
In 1861 Samuel, a widower, was living in
Wellington Road, Dudley.
He owned numerous blast furnaces,
mills and forges in the Dudley area and collieries
in Monmouthshire, along with iron ore mines in the
Forest of Dean, Exmoor and elsewhere. He was greatly
interested in geology, particularly in the South
Staffordshire Coalfield and was a member of the
Institution of Mechanical Engineers and one of the
Vice-Presidents. In 1852 he read a paper to the
Institution about utilising the waste gas from blast
furnaces.
He died at Birmingham on the 25th
March, 1868, at the age of 51, after a long and
painful illness. On his death, Russell's Hall
Ironworks closed.
Withymore Iron Works was
run by Benjamin Best in 1844 and produced around 180
to 190 tons of iron per week. By 1851 it was being
run by Benjamin Best, Barr and Northall. Francis
Northall was the furnace manager.
Harts Hill Ironworks
opened in 1836 for the manufacture of hurdles and
fences, mostly for export to the colonies. Edward
Smith ran the ironworks, which by 1851, also
produced wrought iron forgings for steam engines. In
1860 the ironworks manufactured many miles of
continuous fencing for Queen Victoria's estates.
Edward Smith later ran the business with one of his
employees under the name of Hill and Smith. The firm
then manufactured gates and agricultural implements.
By 1883 the firm had around 400 employees.
|
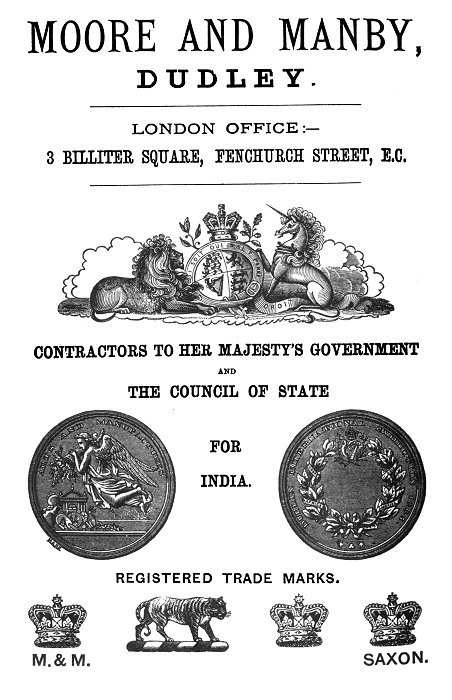 |
Moore and Manby,
ironmasters, Wolverhampton Street, Dudley.
One of the area's high
quality iron makers.
From Griffiths Guide to
the Iron Trade of Great Britain. |
Moore and Manby,
products. From
Griffiths Guide to the Iron Trade of Great
Britain. |
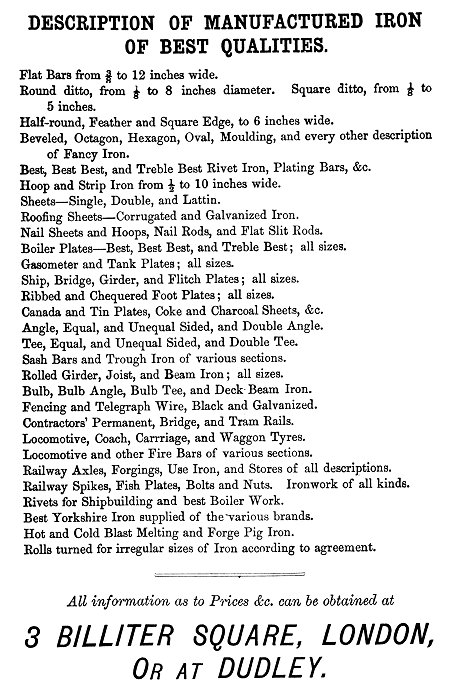 |
Woodside Iron Works was started in 1840
by Alexander Brodie Cochrane and his
son. The firm was also known as Alexander Brodie Cochrane and John
Joseph Bramah. Alexander Brodie Cochrane senior was
born in about 1786 in Eddlestone, Peebles, Scotland.
His son of the same name was born in Dudley
on the 10th February, 1813.
Alexander senior moved to Ironbridge from Scotland
where he went with Lord Dundonald who
developed the tar works there. In about 1830
Alexander senior became manager of Grazebrook’s
colliery and furnaces, near Dudley, where his son,
Alexander junior also worked and learned about iron
production. In 1838 Alexander
Brodie Cochrane junior, went into partnership with
John Joseph Bramah and opened a small iron foundry
in Bilston.
In 1840 Alexander and his son, founded Woodside
Iron Works in partnership with John
Joseph Bramah. They leased land at Woodside next to
the canal and built the ironworks and a foundry
alongside the canal. The partnership was dissolved
in 1842 when Alexander Brodie Cochrane senior,
retired. By 1844 Cochrane and Bramah were
producing around 9,100 tons of iron per year.
|
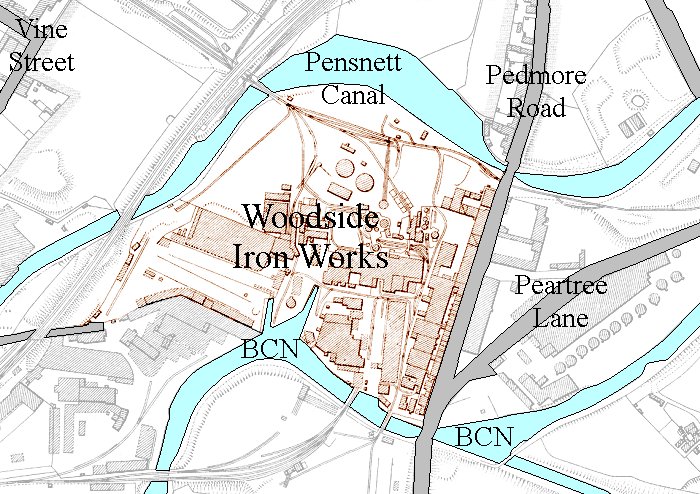
The location of Woodside
Iron Works. |
In 1846 John Joseph Bramah died
and Mr. Charles Geach and Mr. Archibald Slate became
partners. The business then became Cochrane and
Company.
Woodside Iron Works was a great success,
producing large amounts of iron and many products
from the foundry. One of the large orders came from
Fox Henderson of Smethwick, who subcontracted the
work for the manufacture of the huge cast columns
for the Crystal Palace in Hyde Park, in readiness for
the Great Exhibition of 1851.
In 1851 Alexander Brodie Cochrane
junior, lived in Kingswinford, with Esther
Cochrane age 40, Mary Cochrane age 12, George
Cochrane age 6, Ellen Cochrane age 3, Donald Alice
Cochrane age 2 and Alfred Cochrane, age 7 Months.
Alexander Brodie Cochrane senior
died on the 8th December, 1853, in Netherton. 1853
had been a time of expansion because the company
acquired several collieries in Northumberland
and Durham, and established the Ormesby Iron Works
at Middlesborough. In 1854 Mr.
Charles Geach died and Mr. Archibald Slate left the
firm. In the same year an order was received
from Australia for 20,000 tons of iron piping for
the Melbourne Waterworks.
In 1855, Alexander Cochrane's
son, Charles, aged 20, went to work at Ormesby
Ironworks and in 1856 became a partner with his
father, both at Woodside and Ormesby. Woodside had
many large orders including ironwork for several
important building projects in London. Including the
large caisson and dock gates for the Victoria docks,
which opened in 1855, ironwork for the new
Westminster Bridge, ironwork for the Charing Cross
Railway bridges, ironwork for Cannon Street Railway
Bridge and railway station and ironwork for the
Holborn Viaduct, which opened in 1869. |
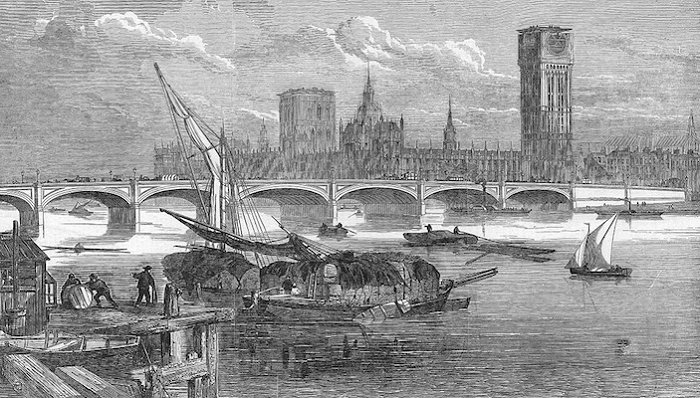
The New Westminster Bridge.
From the Illustrated London News, 3rd February,
1855. |
In 1859 the firm received a large order
for the manufacture of the once-familiar cast
iron pillar boxes, where letters were posted. Sadly, Alexander Brodie Cochrane
died on the 23rd June, 1863, at the age of 50,
after a long and severe illness, at his residence in
Stourbridge. In 1847 he became a member of the
Institution of Mechanical Engineers and for some years
before his death was one of the Vice Presidents. He was
also a member of the Institution of Civil Engineers,
which he joined in 1850 and was a magistrate for the
counties of Worcester and Stafford.
In his later years at Woodside he experimented with
the use of the slack coal for firing ovens and continued
to actively manage the company until several years
before his death, when he became seriously ill. He was
joined by his brother John Cochrane, who devoted much of
his time to the engineering side of the establishment.
Thanks to his efforts, the firm became well known for
the manufacture of cast iron pipes, and supplied nearly
all the principal water and gas companies in the
country, and also many on the continent in the colonies.
In 1868 the firm produced girders for the Runcorn
Bridge over the River Mersey and the Farringdon Street
Viaduct in London. There were many other orders
including ironwork for the Rochester Road Bridge and
Swing Bridge over the River Medway and ironwork for the
Clifton Suspension Bridge.
In 1874 Woodside produced a magnificent wrought iron
bridge for New Street Railway Station in Birmingham.
Charles Cochrane and Joseph Bramah Cochrane took over
the business in 1875 after other family members left. It
was then called Cochrane and Company. In 1890 it became
a limited company.
On the 27th July, 1894, one man was killed and
several were injured as a result of a boiler explosion
on the Woodside site.
Charles and Joseph ran the business until 1896, when
Joseph’s son Walter took over. In 1921 the factory
closed after a strike and was bought by John Cashmore’s
Limited and used to manufacture a number of products
including street lamps. It closed in 1939.
|
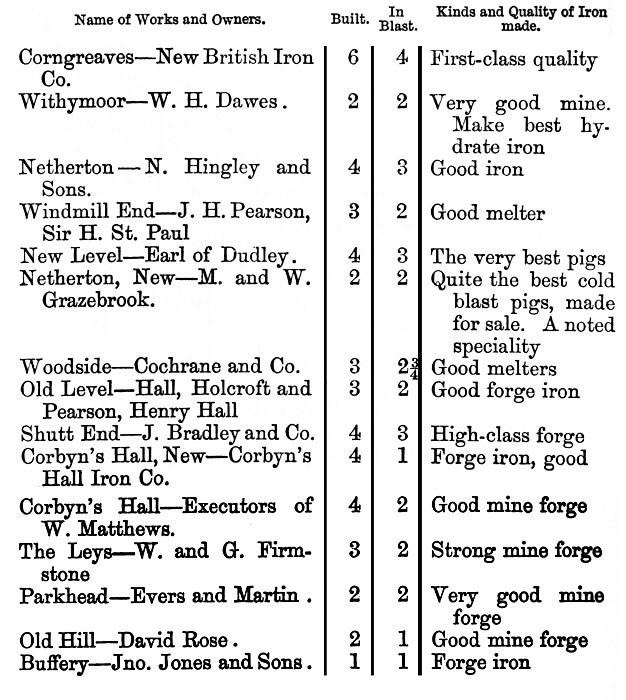
List of blast furnaces in the
area in 1872. From Griffiths Guide to the Iron Trade
of Great Britain. |
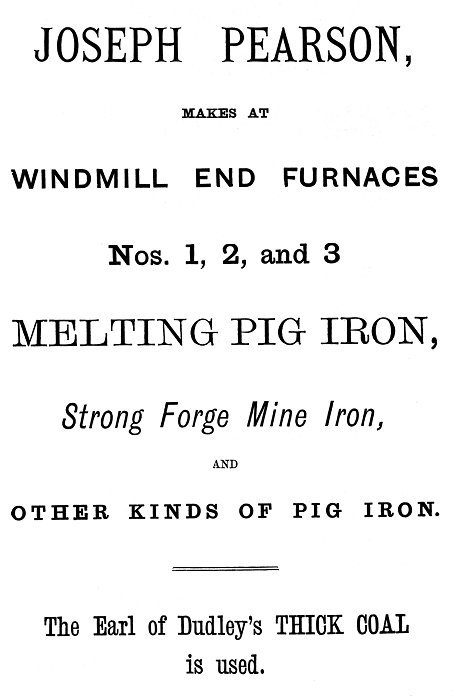
From Griffiths Guide to the
Iron Trade of Great Britain. |
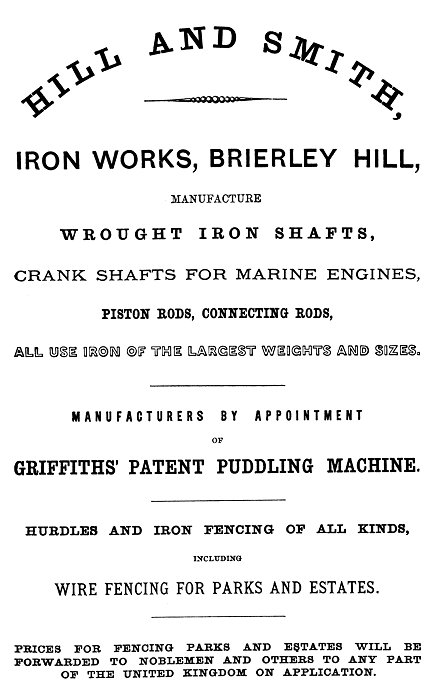
From Griffiths Guide to the
Iron Trade of Great Britain. |
Hill and Smith was established in 1824 and
became known as Hill's Ironworks. Henry Smith
began working for his brother-in-law, Edward
Hill, which led to a partnership. Henry Smith
died in September 1906 at the age of 82 and was
succeeded by his eldest son, Joseph H. Smith,
who was killed in a carting accident in 1909 at
the of 54. After his death, the firm became Hill
and Smith, a private limited company. Early
products included harrows, cultivators,
chaff-cutting machines, puddling machines,
hurdles, gates and fencing, wrought iron shafts,
crank shafts, piston rods and connecting rods.
Structural steel was also produced for
factories, warehouses, roofs, footbridges and
walkways.
The firm also supplied many miles of fencing
for Queen Victoria in 1860, Ornamental Gates and
parapet railing for the Royal House of Siam,
steelwork for the Sydney Harbour Bridge, the
Royal Dockyard at Simonstown, South Africa,
gates for Hong Kong market and the steelwork for
the dome at Birmingham University.
In 1982 the business became Hill and Smith
Holdings plc. The firm now designs and
manufactures products for the construction and
infrastructure industries. |
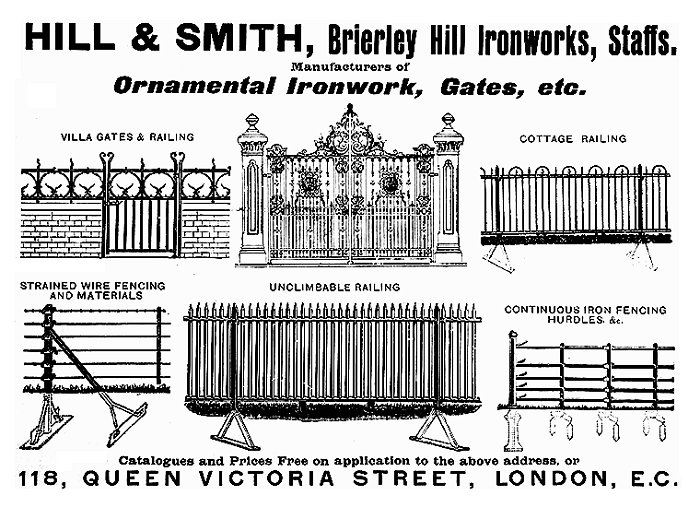
An advert from 1907. |
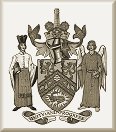 |
Return to the
previous page |
|