Coal Mining
The Earls of Dudley made a massive
fortune from their mineral rights in Dudley and the
surrounding area. At the start of the industrial
revolution, coal and iron ore were in great demand. They
were in plentiful supply in the area and ready to be
exploited. When canals were built, the minerals could be
easily and cheaply transported from the mines to factory
sites.
When the first canal in the
vicinity, the Staffordshire and Worcestershire Canal
opened, John, second Viscount Dudley and Ward was
largely responsible for linking it to his estates via
the Stourbridge and Dudley canals. He was a shareholder
in four of the canals and introduced three of the Bills
into Parliament that allowed their construction. This
included the Dudley Castle Canal Tunnel that linked the
Dudley and the Birmingham Canals. After the Act was
passed in July 1785, the Dudley Canal Company recorded
its thanks to Lord Dudley for his "Unremitted Attention
to the Interests of the Company and for his very
powerful and successful exertion in Parliament in
support of the Extension of the Canal"
Viscount Dudley and Ward’s estates
in Dudley, Kingswinford, Rowley Regis, Sedgley, and
Tipton contained up to nine seams of coal, including the
rich thick coal or 30ft seam, along with deposits of
iron ore, limestone and clay. The Dudley family became
the leading mine owners in the Black Country, who
greatly intensified the exploitation of their estates.
This resulted in a greatly changed landscape in the area
around Dudley and has led to many cases of subsidence,
which still occur.
|
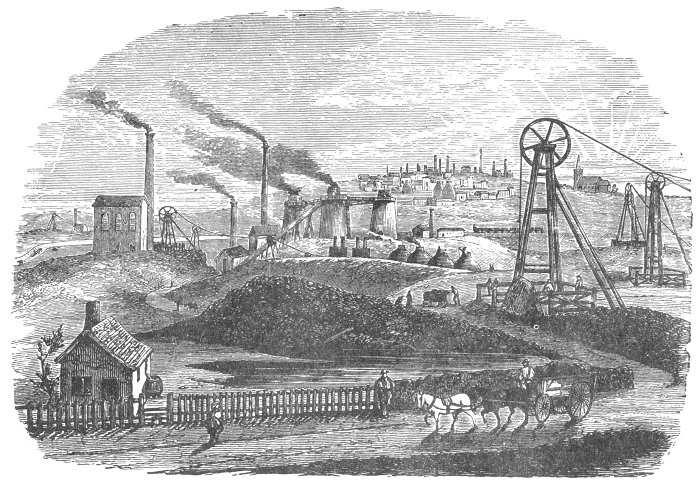
The Earl of Dudley's
coalfields. From Griffiths' Guide to the Iron Trade
of Great Britain. |
Lord Ward initially leased the
collieries to charter masters, who employed butty-colliers,
who in-turn employed middle men to employ the
colliers to mine the coal. In 1797 the system was
reorganised when Lord Ward employed Charles
Beaumont, who supervised the colliers himself and
stipulated how the mines would be run. The colliers
were now permanently employed, which didn't happen
with the old system. Every fortnight a minimum
amount of coal had to be brought to the surface.
Beaumont introduced a standard weight for the coal
so that the colliers knew beforehand how much they
would be paid. The standard rates were based on the
types of coal being cut, such as best coal, second
best coal, lump coal and slack.
In the 30 foot seam he started
a new system in which six foot layers had to be cut,
one at a time, to reduce waste. He also instigated
the use of one large shaft instead of two smaller
ones to carry air into the mine, with a stronger
draught. His work resulted in reduced costs and
higher profitability for Lord Ward. In 1803 the
annual profit was over £3,555 which in today’s money
is approximately £355,500.
In 1803 Lord Ward employed
Francis Downing as Mineral Agent for the Dudley
Estate, but by 1826 productivity was falling. So in
1836 he employed Smith and Liddell, mining
engineers, to improve matters. They recommended that
the business should be put in the hands of a mining
engineer and that the mines should be worked to
their full capacity, including the removal of the
thinner seams of coal and ironstone. They also
recommended that the pits should be leased on a 20
percent royalty on sales and that the coal masters
and ironmasters should meet all working costs.
Lord Ward appointed Richard
Smith as Mine Agent to work alongside Francis
Downing. Richard Smith greatly increased the profits
from the mines, which by the end of the century were
producing a lot of coal for domestic use.
In 1841 over a quarter of the
male population of Dudley were occupied in the coal,
iron and limestone mines which were run by 17 coal
masters. Bentley's Directory of 1840 lists that 1.2
million tons of coal and 150,000 tons of limestone
and ironstone were used to produce 24,000 tons of
iron in Dudley parish.
The collieries included the Parkhead and Dudley
Wood Collieries that served Parkhead Furnaces and
Woodside Works, also Shaw's and Badley's at Blowers
Green. At Netherton, the rich supply of easily
obtainable coal from the 30 foot seam contributed
enormously to Dudley's industrial development. It
was free from sulphur and with a characteristic long
flame that was ideal for the iron industry.
Netherton furnaces were well supplied by the New
Bufferies and Bumble Hole Collieries. There were
large coal and ironstone mines at Coneygre,
Russell's Hall, Himley, Knowle Hill and Saltwells.
At
Kates Hill, coal could be found at the surface.
|
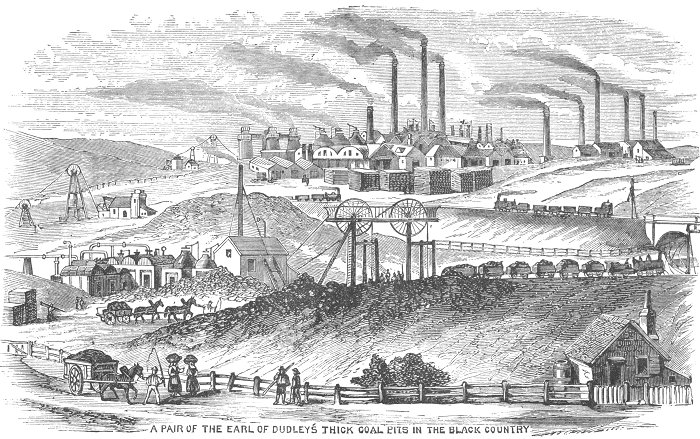
From Griffiths' Guide to
the Iron Trade of Great Britain. |
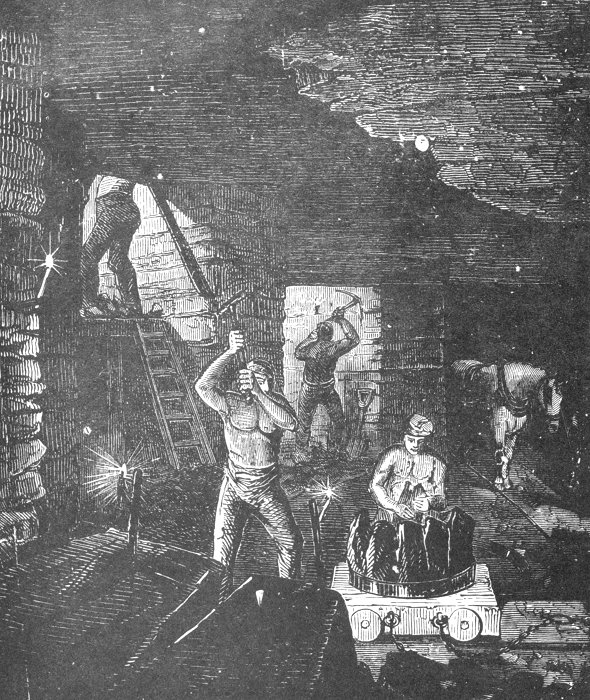 |
Underground work at
Saltwells Colliery.
From Griffiths' Guide to
the Iron Trade of Great Britain. |
Getting Coal at one of
the Earl of Dudley's thick coal pits.
From Griffiths' Guide to
the Iron Trade of Great Britain.
|
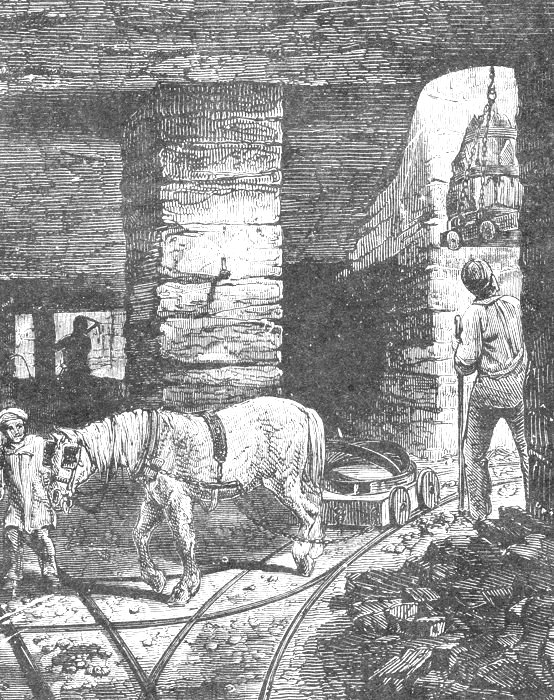 |
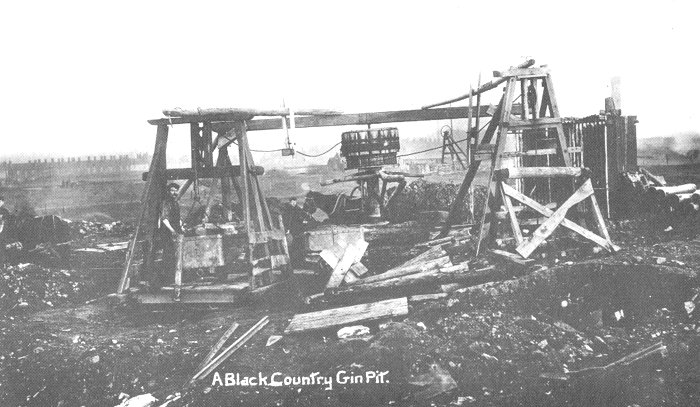
A once common
sight in the Dudley area, a horse-driven
gin pit. From an old postcard. |
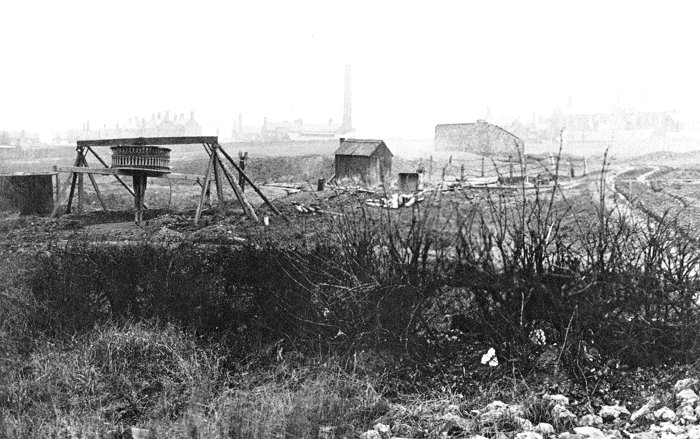
Another
typical view of a coal mining
area with a gin pit in the
foreground. From an old
postcard. |
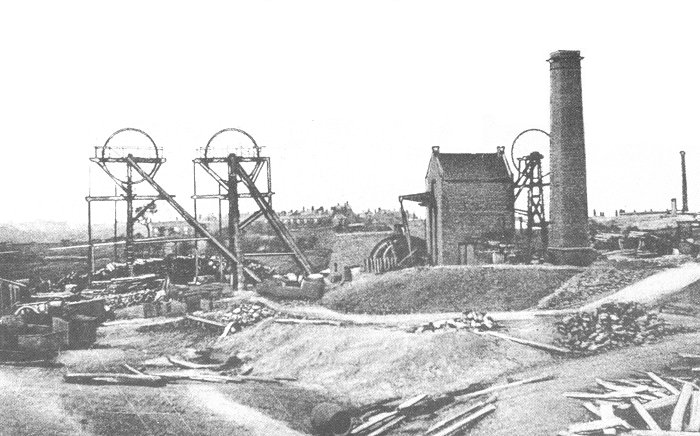
A mine with a
Newcomen steam engine operating a
water pump and the winding gear.
From an old postcard. |
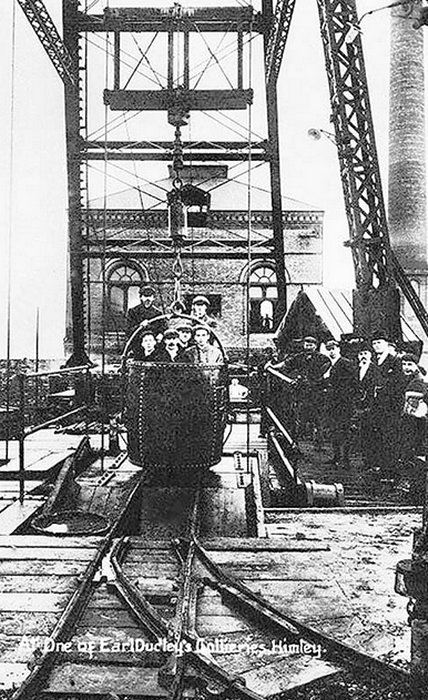
From an old postcard. |
Coal mining was hard and dangerous work. When
the demand for coal was high, miners were well paid,
but when demand fell, their wages were reduced. In
November 1831, many of them joined forces to form a
miners’ union, so wage reductions sometimes led to
strikes and even riots. In 1878 because of the
poverty caused by a wage reduction, a soup kitchen
was opened and 2,200 pints of soup were distributed
in Dudley, in under two hours. Unfortunately wages
continued to fall until the end of the century.
Accidents
There were many accidents including underground
explosions. Two men were killed at Saltwells Colliery when the explosive
firedamp (usually methane) came up from the sump of
the shaft and ignited in 1855.
Firedamp was common
in the Dudley pits, accumulating in pockets in the
coal. It sometimes collected in the underground
workings and could suddenly ignite, killing and
maiming miners. Work in a pit would have to be
stopped at least three times a day so that the gas
could be cleared by firemen who hung a candle from a
long rod and slowly raised it until an explosion
occurred.
|
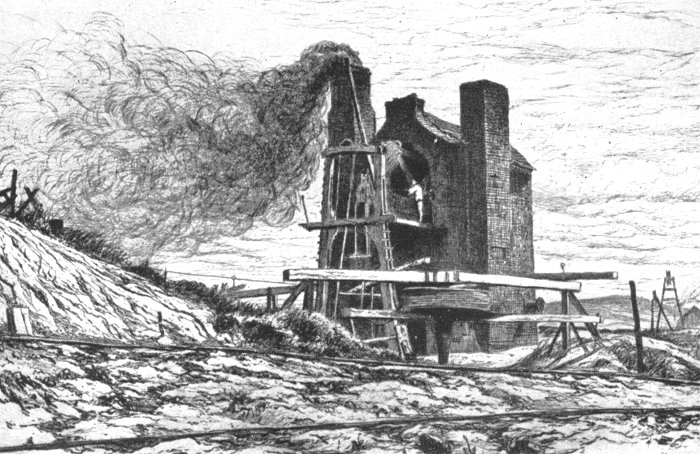
The pumping engine
at the Buffery Pit. From Chandler and
Hannah's 'Dudley as it was'. |
In 1808, James Ryan developed a system to safely
ventilate the thick coal at No. 16 Pit, Netherton,
in which passages were cut in the upper parts of the
workings and connected to air pipes running to the
surface. Within a very short time all the firedamp
was removed, which allowed the people underground to
work longer without having to resort to firemen
three times a day. This system was soon used
throughout the country.
|
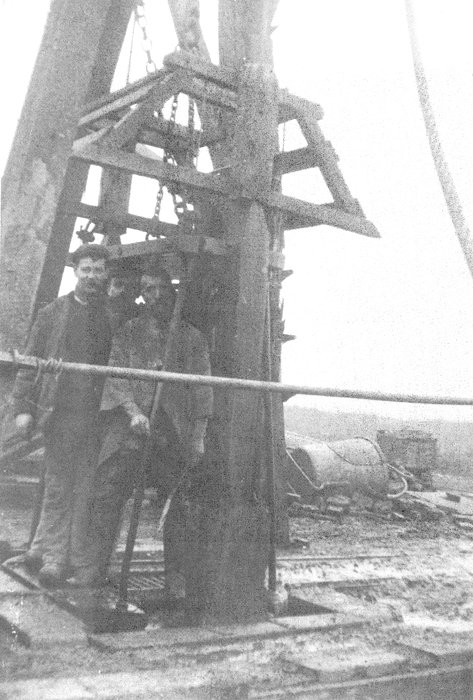
Coal miners leaving a pit
in about 1912. From an old postcard. |
An explosion occurred at Homer Hill Colliery, in
Cradley, owned by Messrs. Evers and Sons, on the 1st
November, 1866. The explosion occurred underground,
killing twelve men. On the 26th April, 1853, eleven men died in an explosion
at Old Park Colliery, Dudley, owned by Lord Ward, and another nine men died in
September 1857 at an explosion in Gwane Colliery,
Rowley Regis, owned by William Mills and Son.
The risk of an explosion could
be reduced by the use of a Davy lamp, which was
introduced into the Black Country in the early 19th
century.
It was not liked in
Dudley because the lamps did not give enough light
and the gauze which made the lamps safe, would
clog-up with coal dust, so that the miners could
hardly see what they were doing.
Men also died in accidents
while being lowered or raised from the pit. On the
20th June, 1856, eight men fell to their deaths
while being lowered down the shaft at number 20 pit,
Old Park Colliery, Dudley, when a chain broke.
|
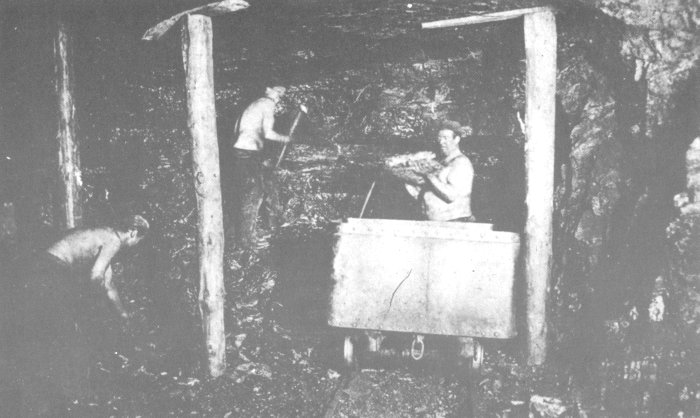
Dangerous working
conditions at the coal face. From an old
postcard. |
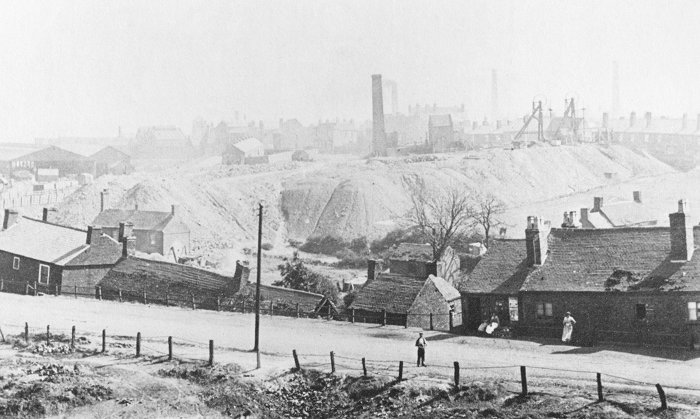
Mining subsidence in
Northfield Road, Netherton. From an old
postcard. |
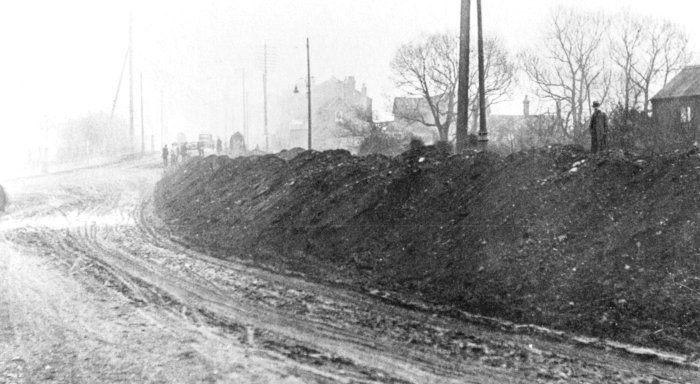
Mining subsidence in
Scotts Green Road on 13th November, 1922. From
an old postcard. |
At Bridge End Colliery in Pensnett, run by Mr. Raybould,
six men were killed on the 11th. January, 1864 when
a pit horse fell down the shaft onto the men who
were being lowered into the mine. At Woodside
Colliery in 1893, three men were killed when the
winding machine broke while bringing them to the
surface.
At number 10 pit, at Saltwells on the 9th. February, 1865, around fifty
tons of coal fell around seventeen feet at one of
the openings, killing six men. On the 18th.
March, 1929 at Coombs Wood Colliery, in Halesowen,
managed by Mr. H. J. Newey, eight men died after an
underground fire. In another underground fire at the Old Buffery Colliery in
1875, four men died.
|
Coalmines in Dudley
in 1896: |
Colliery |
Manager |
Minerals |
People Underground |
Surface
Workers |
Bournehills, Netherton. |
J. Williams |
Coal, Ironstone |
76 |
28 |
Brettell Lane, Brierley Hill. |
George King Harrison |
Coal, Fireclay |
13 |
3 |
Bridge End, Brierley Hill. |
J. W. Grocott |
Coal |
51 |
11 |
Brickhouse, Rowley Regis. |
G. H. Dunn |
Coal |
37 |
8 |
Brockmoor, Brierley Hill. |
R. Mills & Company |
Coal, Ironstone |
44 |
17 |
Bromley, Brierley Hill. |
J. W. Growcott |
Coal, Ironstone |
57 |
20 |
Bromley Lane, Pensnett. |
J. A.
Fullwood |
Coal |
83 |
17 |
Coneygre, Rowley Regis. |
H. W. Hughes |
Coal, Ironstone |
301 |
111 |
Corbyns Hall, Kingswinford. |
Bennett & Bradley |
Coal |
10 |
7 |
Delph, Brierley Hill. |
Hickman & Company |
Coal, Fireclay |
9 |
4 |
Fly, Old Hill. |
W. B. Keen |
Coal |
21 |
6 |
Granville, Old Hill. |
W. B. Collis |
Coal |
|
|
Knowle, Rowley Regis. |
R. Mason |
Coal, Ironstone |
80 |
25 |
Merry Hill, Brierley Hill. |
Firebrick Works, Stourbridge |
Coal |
11 |
3 |
Oak Farm, Dudley. |
J. Walker |
Coal, Fireclay |
12 |
4 |
Old Hill, Old Hill. |
Noah Hingley & Sons |
Coal, Ironstone |
133 |
51 |
Pearson, Old Hill, |
H. Johnson |
Coal |
22 |
14 |
Saltwell, Cradley. |
C. F. E. Griffiths |
Coal, Ironstone |
167 |
59 |
Scotwell, Rowley Regis. |
Hawes Hill Colliery Co. |
Coal |
10 |
4 |
Shut End, Kingswinford. |
D. Rogers |
Coal, Ironstone |
113 |
67 |
Stour, Cradley Heath. |
David Parsons |
|
45 |
27 |
Stourbridge Extension,
Kingswinford. |
Himley Firebrick Company |
Coal, Fireclay |
15 |
6 |
Straits Green, Lower Gornal. |
J. W. Newey |
Coal, Ironstone |
26 |
7 |
Thorns, Brierley Hill. |
Gilbert Claughton |
Coal, Fireclay |
18 |
18 |
Tiled House, Kingswinford. |
R. S. Dodd |
Coal |
86 |
32 |
Timbertree, Cradley Heath. |
W. H. Chapman |
Coal |
40 |
25 |
Turners Lane, Brierley Hill. |
Harris & Pearson |
Coal |
15 |
9 |
Upper Gornal, Dudley. |
A. P. Taft |
Coal, Fireclay |
32 |
5 |
|
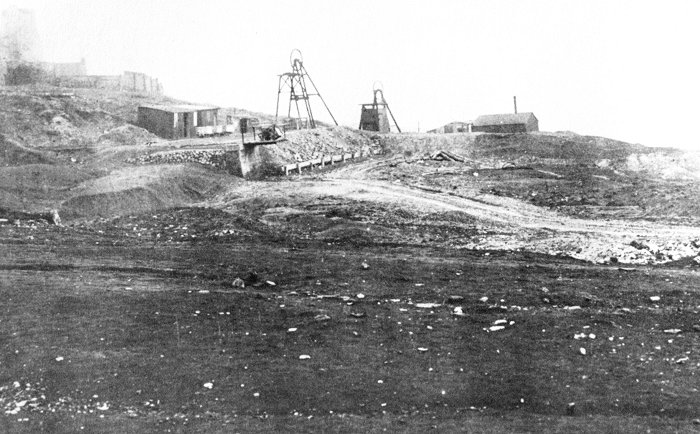
Salop Street No. 2
Fireclay Pit in the London Fields area. From an
old postcard. |
Fireclay
Mines in Dudley in 1896: |
Mine |
Manager |
Minerals
|
People
Underground |
Surface
Workers |
Brettell Lane, Brierley
hill. |
Trotter, Haines &
Corbett |
Fireclay |
14 |
5 |
Clattershall, Brettell
Lane, Stourbridge. |
Bowens Limited |
Fireclay |
15 |
4 |
Crown, Amblecote. |
E. J. & J. Pearson |
Fireclay |
15 |
2 |
Dibdale, Lower Gornal. |
T. E. Jackson |
Fireclay, Pyrites |
38 |
15 |
Freehold, Lye. |
William Cox |
Fireclay |
3 |
1 |
Moor Lane, Brierley
Hill. |
John Hall & Company |
Fireclay |
17 |
9 |
|
The Dudley family’s last pit, Baggeridge Colliery,
began life after the first shaft was sunk in 1902 to
reach a thick coal seam, 1,800 feet below the
surface. Two further pit shafts were sunk in 1910
and full production began in 1912. It was served by
a branch of the Earl of Dudley's Pensnett Railway
and in its heyday employed 3,000 men who produced
around 12,000 tons of coal per week. The pit closed
on the 2nd March, 1968 and was the last remaining
pit in the Black Country. |
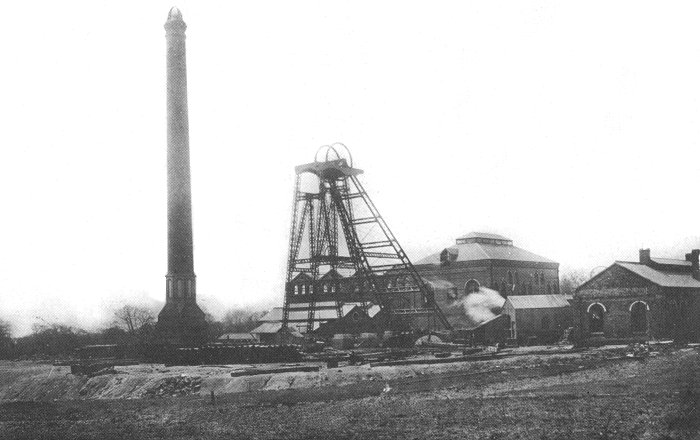
Baggeridge Colliery. From an
old postcard. |
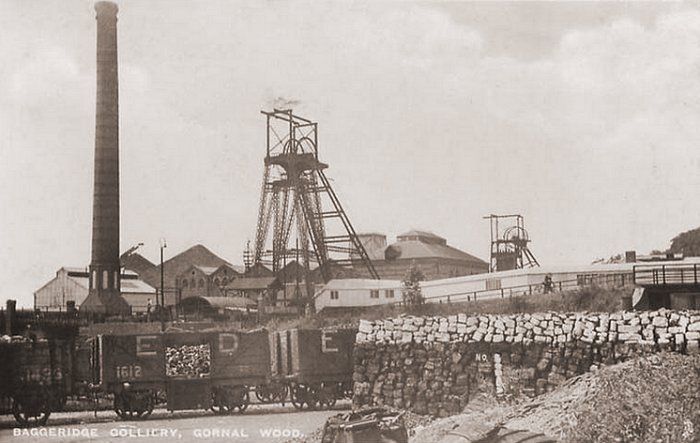
Another view of Baggeridge Colliery. From an
old postcard. |
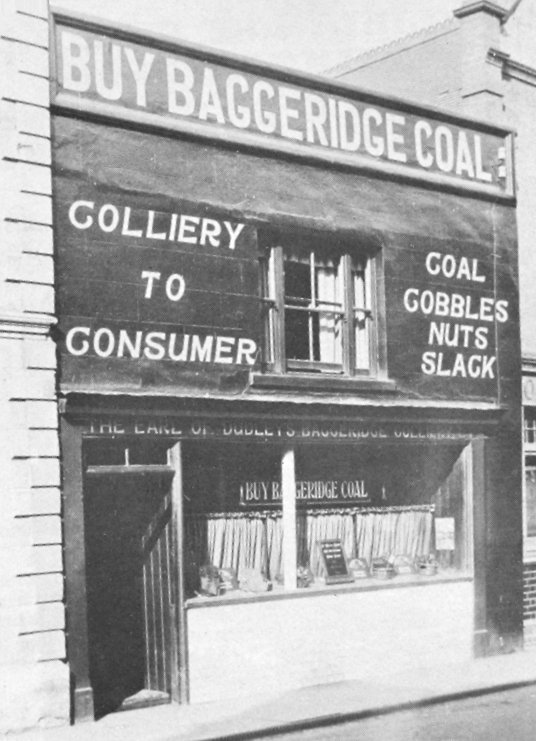
One of the many
Baggeridge Colliery shops that sold coal
directly to members of the public. |
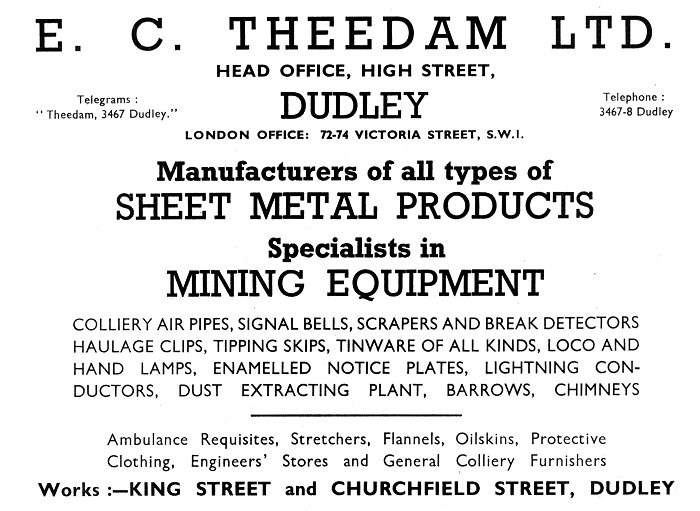
An advert from 1958. |
Limestone Mines From the end of the 18th century, limestone was
in great demand due to the opening of many ironworks
and the ease of transportation on the newly built
canals. It was used as a flux that was essential to
iron making. Silurian limestone, outcrops in a series
of faults in the Dudley area that form Castle Hill,
Wrens Nest Hill and Hurst Hill.
|
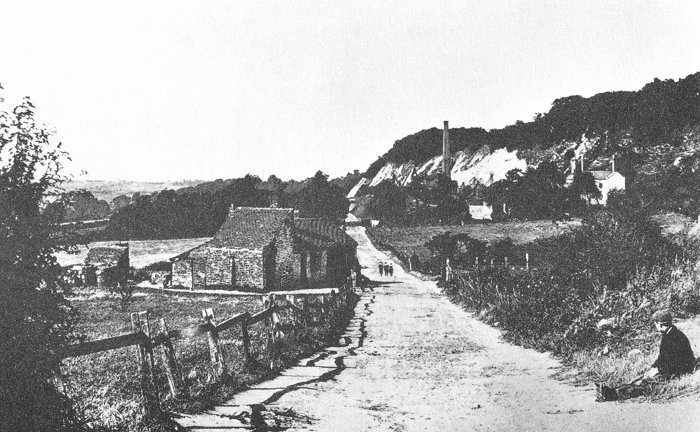
Limepit Lane that ran
alongside Wrens Nest Hill, as seen in the
1920s. In the distance is the chimney and
pithead gear of one of the limestone mines. |
The limestone
outcrops were mined for hundreds of years, initially
for building stone and mortar, then with the coming
of iron making, it was in great demand for use as a flux. During the
height of the industrial revolution, up to 20,000
tons of local limestone was quarried annually. It
was laid down in a shallow sea and was known for its
wide variety of fossils including large numbers of
trilobites. Because they were so common, they became known as the ‘Dudley Bug’. |
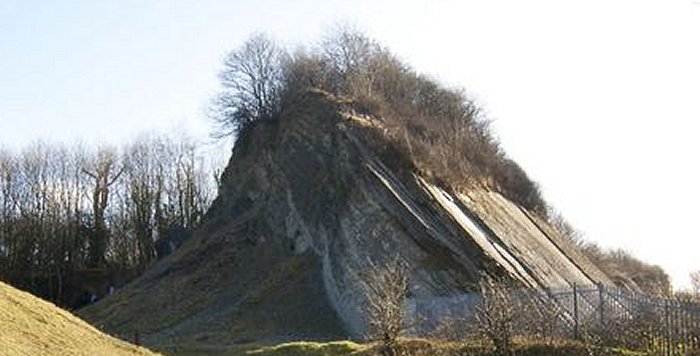
Wrens Nest, from where
most of the good quality limestone was quarried. |
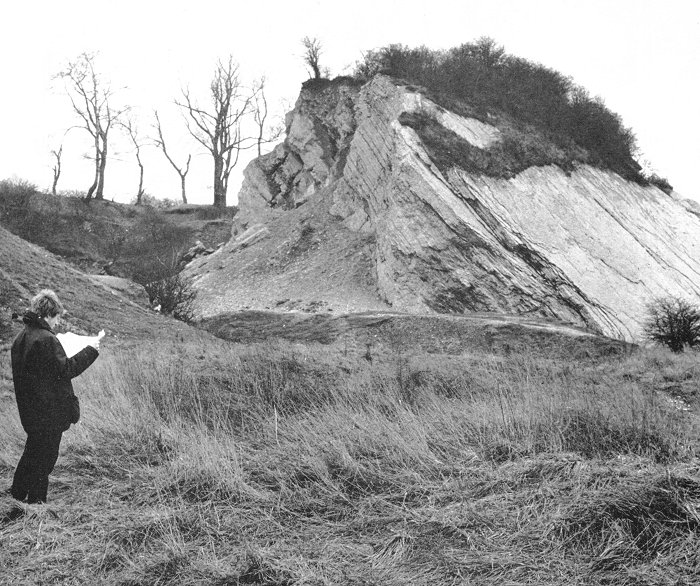
Wrens Nest in the mid
1970s. |
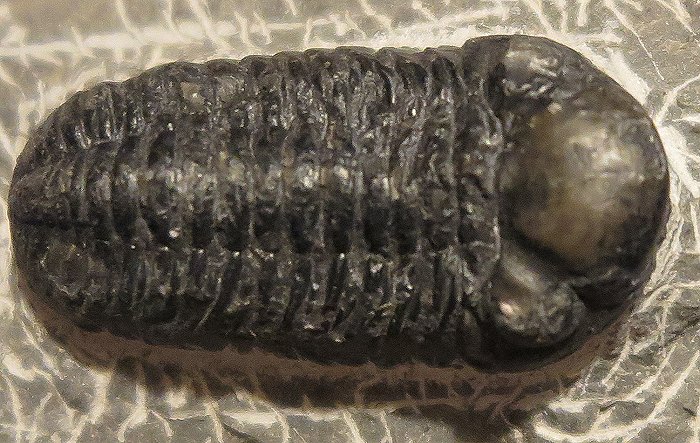
A trilobyte. |
The first part of Lord Ward’s canal tunnel was
built to help transport the limestone that was
extracted from the mines inside Castle Hill, through
which the tunnel runs.
A branch from the main tunnel
that runs to Parkhead, went under Wren's Nest to two
underground basins, east basin and west basin, to
transport limestone from the underground workings.
This is now blocked off.
Wrens Nest was well known for its large surface
cavern known as the ‘Seven Sisters’ which is more
than 100 metres long.
Quarrying ended in 1925 and
the site was abandoned. In 1956 it became a national
nature reserve.
In 2004, Wren's Nest and the nearby
Castle Hill were declared Scheduled Ancient
Monuments, because they represented the best
surviving remains of the limestone industry in the
area.
The Seven Sisters Cavern had to be filled in
with loose sand after a major roof collapse in 2001. |
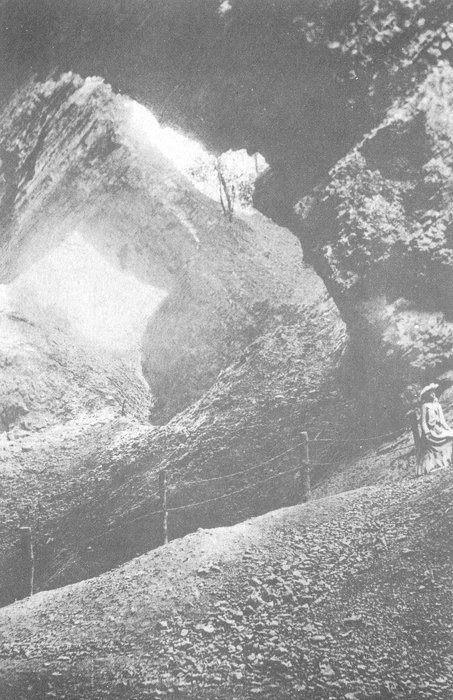
Seven Sisters Cavern. From
an old postcard. |
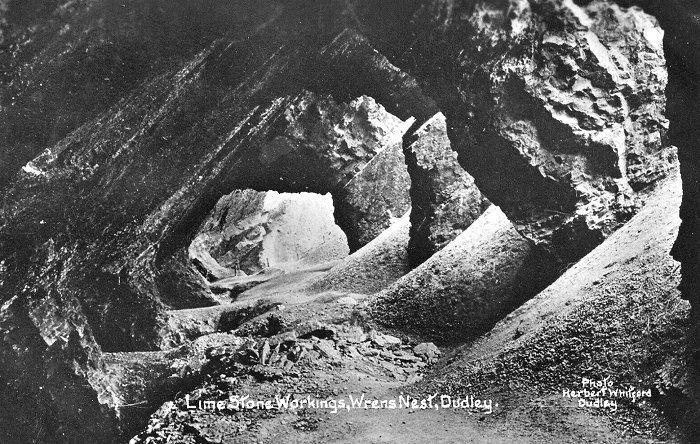
The Seven Sisters
Cavern. From an old postcard. |
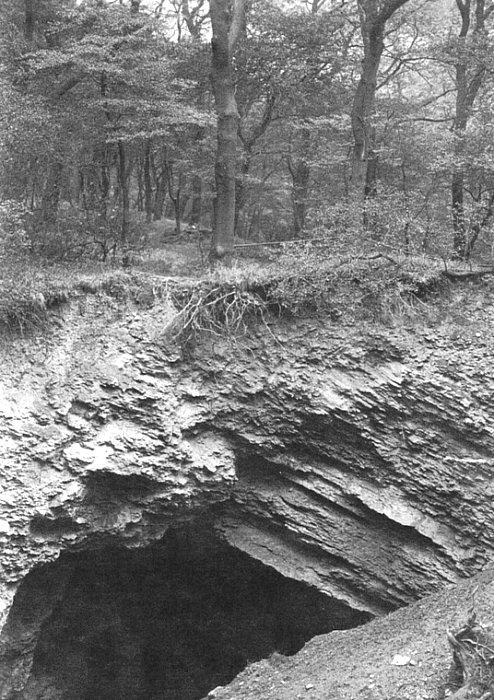
Old limestone
workings on Castle Hill. From an old
postcard. |
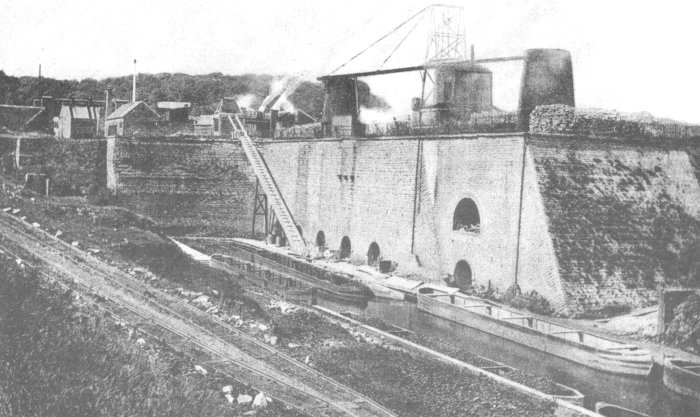
Visitors to the Black Country Living Museum can
see the remains of lime kilns beside the canal. A
reminder of the once-important limestone industry.
From an old postcard. |
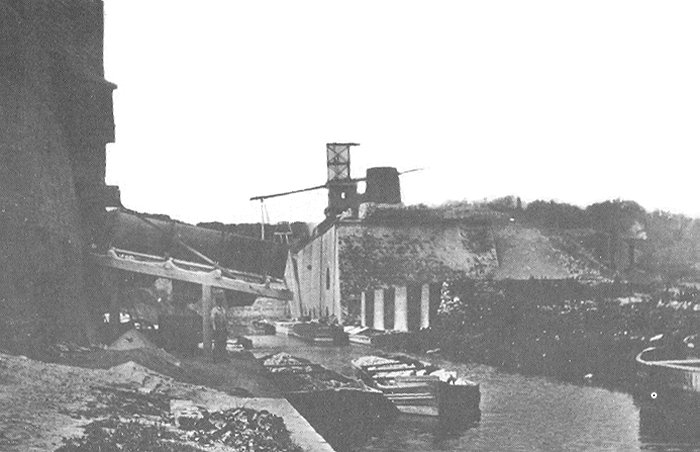
Another view of the lime
kilns at the Black Country Living Museum. From
an old postcard. |
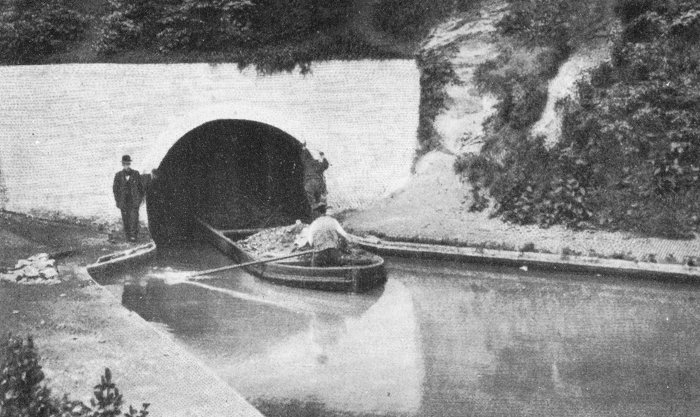
A canal boat leaving the
Dudley tunnel. From an old postcard. |
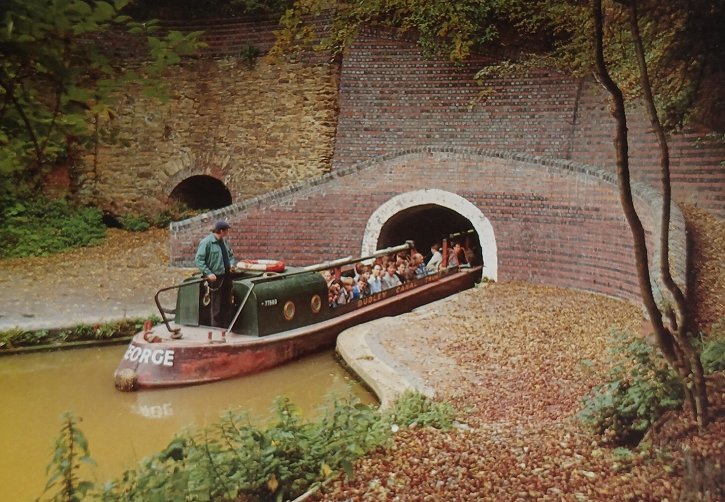
A boat full of
tourists entering the canal tunnel in modern
times. |
Clay has also been extensively mined in the area, for use in
brick making and for industrial furnaces. Vast clay
deposits have been found all around Dudley, where a large
number of fireclay mines and brick and tile works
formed part of the local landscape. |
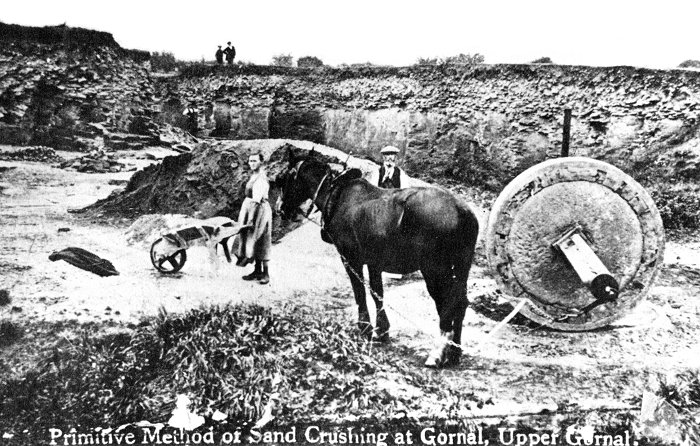
Local
sand deposits were well-worked for glass-making. From an old
postcard. |
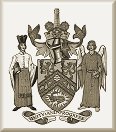 |
Return to the
previous page |
|