F. H. Lloyd & Company
Limited - The First Sixty Years The Darlaston based Bills & Mills
steelworks at The Green were purchased by the Lloyd
family for a quarter of a million pounds when its
owner Samuel Mills retired. |
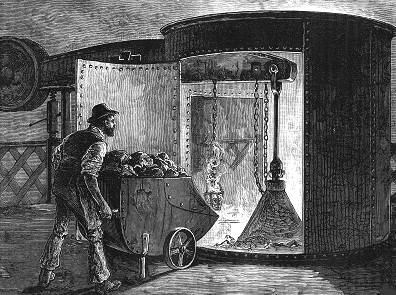
Charging a blast furnace. |
Mr. Sampson Lloyd of Wassel Grove, Stourbridge
became company Chairman and Mr. Francis Henry Lloyd, Managing
Director.
The name was changed to the Darlaston Iron & Steel
Company and rapidly expanded.
The number of puddling furnaces grew to 43 with 17
reheating furnaces, 8 rolling mills, a drawing-out
forge, 63 steam engines, including three 70hp.
blast engines for the blast furnaces. Rails were
laid to all parts of the works. |
The company's collieries and mines, mining a 12
yards thick seam, covered 850 acres, 350 of which were
freehold and 500 leasehold. Some of the seams produced
what was called "Brooch" coal, and others "Heathen" coal.
The company survived until the depression in the 1880's.
After the closure, Francis Henry Lloyd brought a disused
timber yard and brickworks at James Bridge, and established a small
foundry which eventually became F. H. Lloyd's James
Bridge Steel Works. The original
shareholders were: engineer, John William Hall junior,
of Bilston; solicitor, John William Hall, of Bilston;
engineer, John Hemming of Wednesbury; traveller, Alfred
Essington Hemming of Wolverhampton; engineer, Francis
Henry Lloyd of Wood Green, Wednesbury; manufacturer,
Sampson Z. Lloyd of Arley Hall, Stourport, (brother of
F. H. Lloyd); banker, George Braithwaite Lloyd of
Birmingham; and surgeon, Samuel Ashley Smith of Bilston.
|
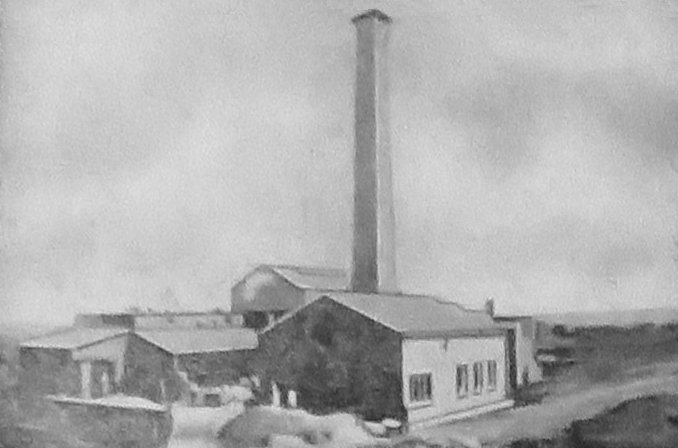
An early impression of James
Bridge Steel Works, from a long service award.
Courtesy of Wendy Marston. |
Soon after its opening in 1879, the factory consisted
of a steel foundry, three forges and a fitting shop.
Steel was melted and refined in a small gas-fired open
hearth furnace. A tilting machine was added for
drawing out steel and for making steel forgings. By 1900
the forges had been replaced by a machine shop and an
improved fitting shop.
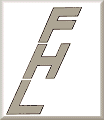 |
Read an
illustrated article about
F. H. Lloyd & Co. Ltd. from the
"South Staffordshire Institutions and Trades
Illustrated" of about 1900. |
The business was extremely successful and a
foundry for producing small castings was
added in 1909. By 1912 the factory produced
2,000 tons of steel castings each year, and
during the 1914-18 war, production
concentrated on cast steel shells. |
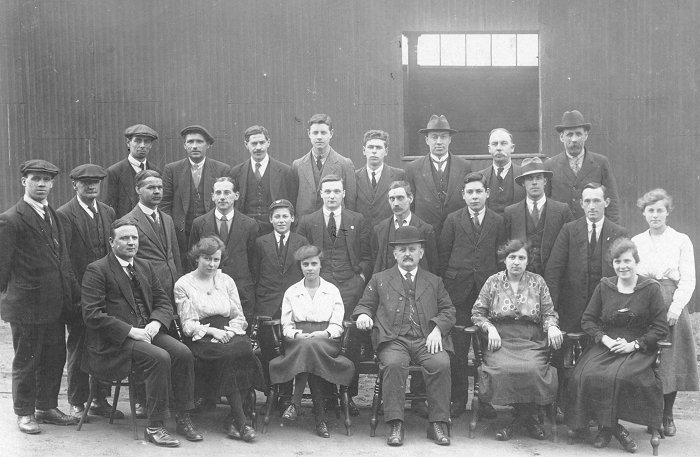
Some of the staff
during World War One: back row left to
right: number 3- Billy Fisher, number 4-
M. H. Dale, number 6- Joe Davies, number
8- Jack Chorley. Middle row left to
right: number 1- Arthur Crawford,
number 2- ? Blakesly, number 3-
Billy Dudley, number 6- Teddy Walker,
number 7- Harry Sanders, number
10-Walter Clifford. Front row left to
right: number 1- ? Griffith, number 4-
Mr. Clifford senior, number 5- Lizzie
Long (Horace Morgan's wife). Courtesy of
Wendy Marston. |
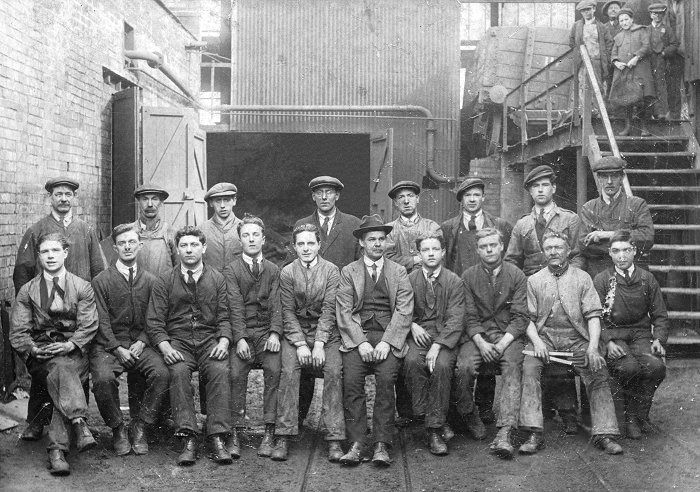
Another group of
staff from around World War One. Front
row left to right: number 2- Jack
Davies, number 3- Harry Parsons, number
6- Billy Dudley. Courtesy of Wendy Marston.
|
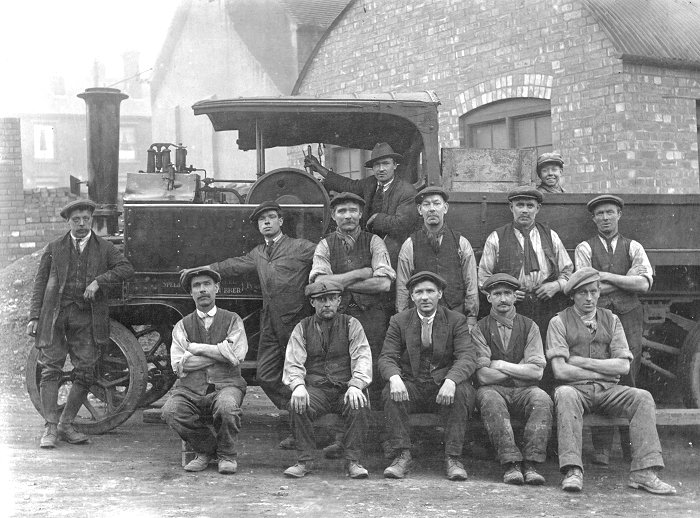
Another photo from World War
One. The building in the background on the right is
the old canteen. Wilf Brown is at the controls of
the steam lorry. Courtesy of Wendy Marston.
|
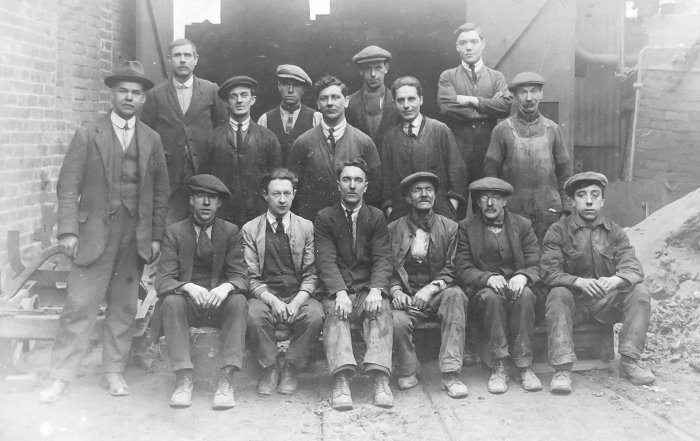
Another group from around the
same time. Middle row left to right: Billy Dudley,
Jack Davies, Harry Parsons. Courtesy of Wendy Marston.
|
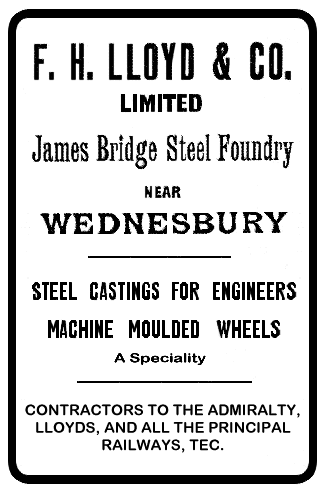
An advert from 1913. |
Francis
Henry Lloyd (born in 1844) died after a railway accident
in 1916 and was replaced by his son, Daniel Charles
Lloyd, who lived at Tettenhall, Wolverhampton. He would leave home at a
quarter to eight each morning and catch the
tram to Wolverhampton, the train to Wednesbury,
and presumably the tram to James Bridge via
Darlaston. After the return trip each
afternoon, he arrived back
home around 6 p.m.
The senior partner,
John Hemming, died in the early 1920s. After
his death, Daniel Charles Lloyd became
Chairman and Managing Director. Daniel's wife
Hilda was convinced that Francis Henry Lloyd
got leukaemia from standing too close to the new X-ray machine,
bought to detect faults in castings.
Francis
Henry Lloyd also founded the Weldless Steel
Tube Company at Wednesfield, which was taken
over by Tube Investments in about 1927. |
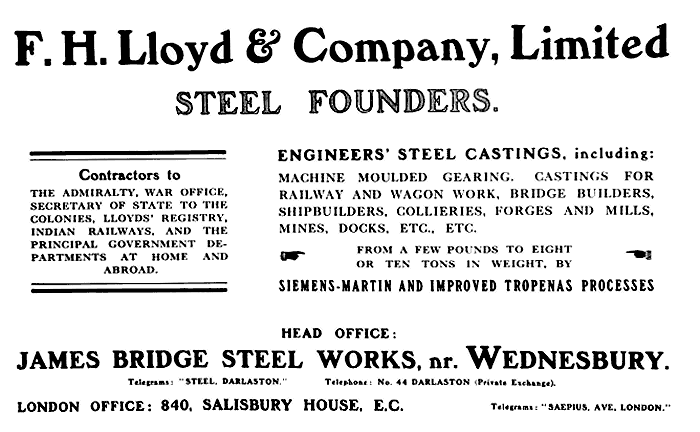
An advert from 1916. |
In 1919 a new heavy foundry was built and output
increased to about 6,000 tons of castings a year. At the
time there were nearly 600 employees. After the
depression of the late 1920s production greatly
increased with over 13,000 tons of steel products being
produced annually.
Their success was no doubt helped by
the excellent management-employee relations that always
prevailed at the works. A training scheme for young men
began at the factory, and by the time the recession had
ended, the firm had a large number of skilled workers. |
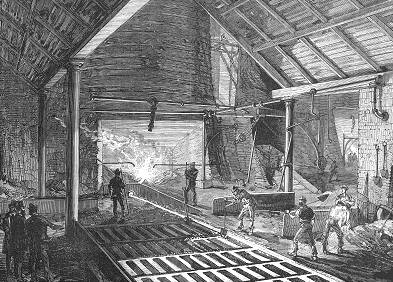
Tapping a furnace to produce pig
iron. |
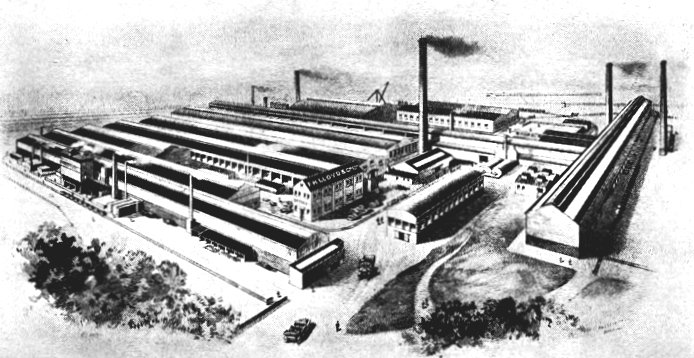
The factory in 1919. From 'The
Steel Casting'. Courtesy of Wendy Marston. |
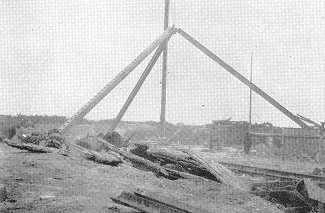 |
|
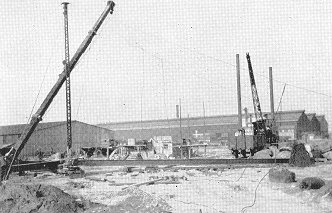 |
In 1933
the breaking area where scrap steel and steel
castings could be broken up, was moved to a less
restricted area. The derrick on the left is
being dismantled before being rebuilt at the new
location on the right. |
|
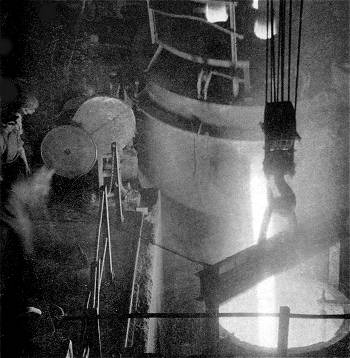
Tapping an electric arc furnace at
F. H. Lloyd.
|
In the early 1930s the company
started to produce heavy castings for mechanical
excavators and earth-moving machines for an engineering
firm in Lincoln.
The company's staff magazine "The
Steel Casting" appeared in 1938, around the same time as
many operations in the factory were reorganised.
Mr. A. B. Lloyd made an exploratory
visit to America to discover how large American
engineering companies were organised. He visited Bucyrus
Erie Company, manufacturers of surface, and underground
mining equipment, including steam shovels, draglines,
hydraulic excavators, and mining trucks. He also talked
to engineering consultants.
|
On his return to Wednesbury he
carried out a preliminary survey of operations at the
works, and appointed a firm of engineering consultants
to produce a plan to make the factory operate more
efficiently. The consultants began their investigation on April
1st, 1938, which resulted in the formation of a central
production department to take responsibility for the
coordination of production throughout the works.
A
standards department was also created to oversee and
standardise production times. Internal order forms were
redesigned, and a printing machine was installed to
print them.
Before the reorganisation, productive effort was
measured by tonnage produced, which was misleading, due
to the increased use of intricate steel castings with
lighter sections.
Under the new scheme, man hours were taken into
account when considering the efficiency and output of
each department.
The reorganisation ensured that every department was
kept fully employed without congestion, and an improved
standard of service was given to customers. |
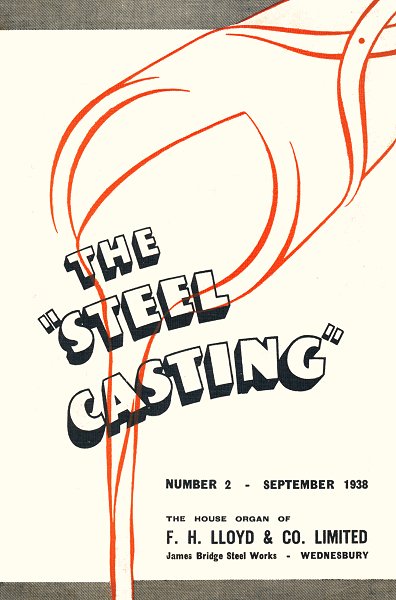
The staff magazine. |
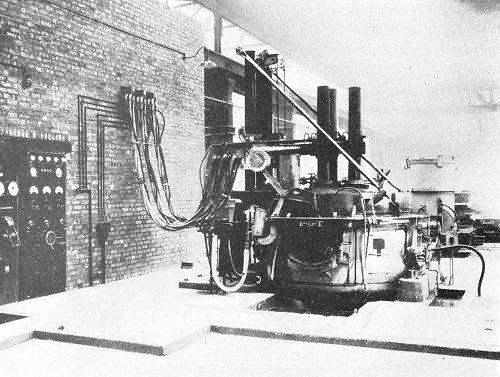
The electric furnace, charging
bucket and control board. |
In 1938 a new electric arc furnace was installed
to increase the steel-making capacity at the works.
In 1914 Mr. D. C. Lloyd acquired the company's
first electric furnace, for experimental purposes. The 5 cwt. furnace proved to be
uneconomical due to high running costs.
By the late 1930s, the advent of the national grid
and cheaper electricity, together with improvements
in furnace design and operation, made an electric furnace a
practicality, and led to the purchase of a direct
arc furnace. |
The direct arc furnace had a capacity of 4 to 5 tons
and was supplied by Birmingham Electric Furnaces
Limited, which had the manufacturing rights for the
Moore Rapid Lectromelt Furnace, made by the Pittsburgh
Lectromelt Furnace Corporation of America. The
installation went well. Within 14 weeks of the initial
order the furnace was in operation. The furnace was
charged by a swing roof, actuated by a hydraulic ram,
which also swung the electrode gear. The steel scrap
used to charge the furnace was loaded into a bucket
with drop-bottom doors, secured with a hemp rope. |
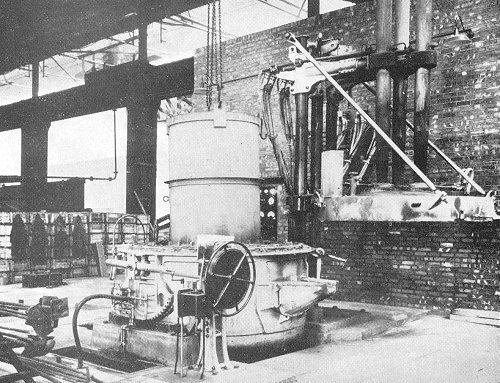
The bucket is swung into position
in readiness for charging. |
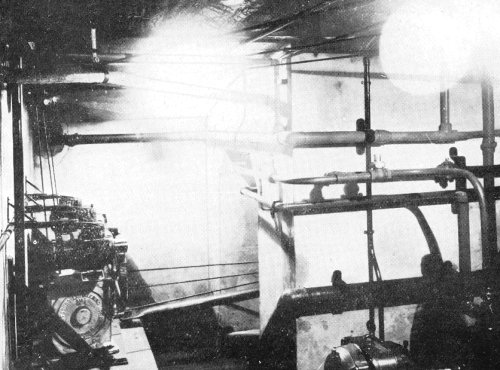
The winch motors controlling the
electrodes. |
After lowering the bucket into the furnace, the rope
quickly burnt away, allowing the scrap to fall. The
whole charging operation only took a few minutes. The
roof, the body of the furnace, the electrode holders,
the doors, and all metal parts exposed to heat were
water-cooled.
The hearth was lined with refractory material to
remove as much sulphur and phosphorus from the charge as
possible. |
The 7,000 volt supply that fed the furnace sub-station
was stepped down by an oil-filled transformer with a
tapped secondary winding supplying up to 215 volts to
the furnace. The charge was heated by the current
flowing through the graphite electrodes, arcing across
the gap between the electrodes and the charge.
The gap had to be precisely maintained to supply the
correct amount of heat. |
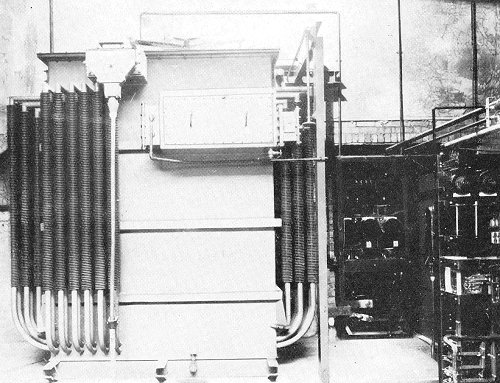
The transformer and automatic
electrode control. |
This was accomplished by a Westinghouse automatic
regulator which operated each electrode independently
through a winch and motor to lower or raise the
electrodes and maintain a steady operating current. |
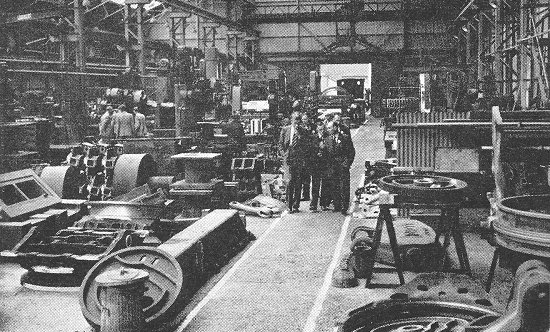
The machine shop. |
The average time taken from
charging to tapping was about three hours, giving an
output of one ton per hour.
The furnace was mainly used for the
production of carbon steels, but also for the alloy
steels which were being developed at the factory.
|
In 1938 the company opened Lloyds
(Burton) Limited at Burton on Trent, which would
eventually be the last part of the business to survive. |
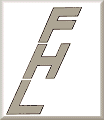 |
|
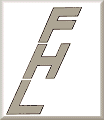 |
Return to
the contents |
|
Proceed to the
early 1930s |
|