From 'The Engineer'. 14th January, 1966.
Heavy Steel Castings Foundry
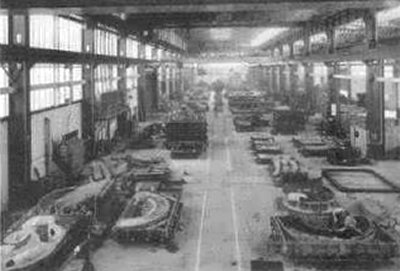 |
A further step in the modernisation and expansion of
F. H. Lloyd and Company Limited, James Bridge
Steelworks, is the recent opening of a new heavy foundry
for the production of steel castings up to 50 tons in
weight. A new dressing shop has also been provided
with specialised equipment to deal with large castings. |
The steel castings industry is only just over a century old and the
firm of F. H. Lloyd and Company Limited has been engaged in making
steel castings for all but fourteen years of that period. It was
founded in 1879 by the grandfather of the present chairman, Mr. F.
N. Lloyd, who with his brother Mr. M. C. Lloyd is also joint
managing director.
Making steel castings was a new departure for the Lloyds in 1879,
but to be connected with iron and steel was not, for there have been
members of the Lloyd family actively engaged in one branch or
another (and often in several) of the industry since late in the
17th century.
Both the output and the products themselves were small in the early
days, but growth has been continuous and at present some 25,000 tons
of steel castings of all sizes are produced at James Bridge
Steelworks annually and the area now occupied is 36 acres. The range
of casting sizes has also grown and the James Bridge works now make
steel castings ranging from less than a pound each to 50 tons.
Extensive modernisation has been carried out in recent years in all
departments and particularly in steel melting, pattern making,
non-destructive testing and machining. In recent years the demand
for steam turbine and other heavy castings has outgrown the capacity
available at James Bridge, and the new heavy foundry and its
associated dressing shop have been built on a site hitherto
unoccupied, near to the existing light foundries and other
departments.
The new foundry is in two bays, one, the larger of the two, for
moulding and casting and the other for core making and for storing
scrap and furnace materials. The larger bay is 420 ft long and 70
ft wide, while the smaller one is 390 ft long and 48 ft wide.
From the floor to the eaves of the larger bay is 56 ft and to the
apex, 67 ft; in the smaller bay the dimensions are 41ft and 46ft
respectively. Lifting beams are incorporated in the roof structure
for crane maintenance.
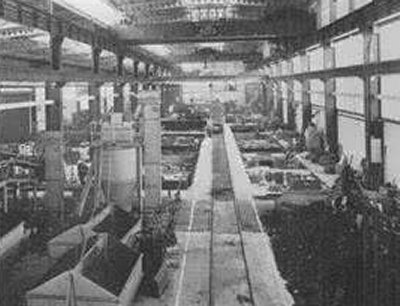
The foundry from the sand preparation bay.
Lifting facilities comprise four overhead electric travelling
cranes, two of 60 tons main hoist and 20 tons auxiliary hoist
capacity, running on rails, 70ft span and 40ft above floor level;
and two of 10 tons capacity and 68ft 2¼in span, at 27ft 3in
above floor level. In the secondary bay there are two cranes, each
of 20.7 tons capacity on a span of 48ft and 30ft above floor level.
As is customary in heavy foundries, there is ample provision of deep
moulding pits, but the conventional arrangement, with a number of
pits of fixed size, which was used in the former foundry at James
Bridge, has not been provided in the new one. Instead, the pits,
which are in the larger of the two bays, are arranged in two
parallel lines, one on each side of a Speedslinger track, and each
pit is continuous over its length of 130 ft. One pit is 22ft wide
by 16ft clear depth and the other is 16ft wide by 12ft clear depth.
Both are constructed in reinforced concrete, with recesses of 5ft
pitch to accommodate prefabricated dividing-wall sections which can
be lowered into place by the overhead cranes. It is thus possible to
modify the length of any pit in 50 increments to suit the work in
hand. Very heavy top and bottom bearers, with steel connecting ties,
are provided, and these too can be spaced at 5ft intervals. Portable
steel handrailing can be fixed in floor sockets to fence-off the
pits as required.
The Speedslinger running between the moulding pits has a radius of
28ft which enables it to reach any part of the pit moulding area; it
has its own crane-handled sand hopper in the normal way. Its rail
track is carried on a steel structure, below which is a belt
conveyor leading to the sand reclamation and preparation plant, and
the space between the rails is occupied by a steel grid. Sand
spillage from the Speedslinger and sand from the moulding pits as
they are emptied, are cleared by this conveyor. The Speedslinger
track extends beyond the pit area, and the machine can thus be used
for box moulding, for which there is ample space available.
Molten metal is provided at present from existing electric furnaces
in other parts of the works, and transported to the new foundry by
rail ladle car, but provision is made in the heavy bay layout for
the installation there, in the near future, of a 25/30 ton electric
arc furnace. For most purposes the foundry will then be
self-contained, but it will still be able to call on additional
melting capacity when necessary.
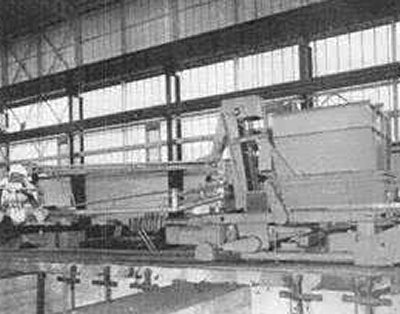
Speedslinger between moulding pits.
Fettling and Dressing
Castings lifted from the pits or taken from moulding boxes are
roughly cleaned of sand in the heavy foundry and then transported by
rail to the adjacent heavy dressing shop. This is structurally
similar to the foundry, but is 450ft long and has crane rails at
75ft span and 32ft above ground level. In this shop there are two
cranes, each of 50 tons capacity, with 15 ton auxiliary hoists. The
roof is 46ft 6in to the eaves and 58ft 3in to the apex. There is
an annex 98ft long and 90ft wide.
All the dressing equipment normally used in a foundry, such as
portable grinders and chipping hammers is provided and there are
numerous items of specialised plant, appropriate to the size and
complexity of the castings produced. Primary cleaning of castings is
catered for by a hydraulic fettling plant which has a water-jet
capacity of 47 gallons per minute at 2,300 lb/in. Castings to be
cleaned are carried on a 15ft diameter turntable, capable of taking
a load of 100 tons. The equipment is housed in a steel cabinet, 24ft
long, 24ft wide and 23ft high. Control of the plant is from the
outside.
Two items of shot blasting equipment are provided, a shot blast box
and a Wheelabrator. The shot blast box is 27ft long by 24ft wide by
20ft high and is arranged for loading and unloading by crane through
an opening roof section. The Wheelabrator is 20ft long by 20ft wide
by 18ft high and has 5 shot wheels. It has a 15ft turntable of 50
tons capacity.
For pickling there are two tanks side by side, both 24ft square and
12ft deep, one for acid and the other for a lime neutralising
solution. Both are of reinforced concrete with a 9in blue brick
lining backed by rubber. Both are sunk in the floor to a distance of
9ft. Acid-holding tanks and boiler are housed close to the tanks.
Completely fettled and dressed castings can be despatched from the
end of the shop by road or rail, or they can be heat treated first.
For this purpose there are two heat treatment furnaces, both gas
fired. One of the pit type is 30ft long by 20ft wide by 15ft 6in
deep (it is actually above floor level and the latter dimensions
could perhaps better be given as 15ft 6in high). The second furnace
of the bogie type, has internal clearance dimensions of 22ft 6in
long by 16ft 6in.
|