The Mechanical and
Electrical Engineering Company (Walsall) Limited
|
The company was founded in about 1907 by Henry J. Webb,
an experienced and practical engineer. The premises were
at 62 and 63 Bradford Street, Walsall, and consisted of
a retail shop on the ground floor, with an office,
stockroom, and workshops above. In the shop, all kinds of
electrical items were for sale, ranging from electric
light fittings, electric lamp holders and shades, lamps,
wires, switches, telephones, electric bells, electric
novelties, hand lamps, torches, carbons for arc lamps,
etc. The firm specialised in lighting and power
installations, and stocked all components for the
lighting of country houses. The firm carried out
electrical installations in large or small factories,
and fitted electric lighting to cars and other vehicles.
In later years, all kinds of repairs were made to
electrically powered industrial machines, and power
installations were carried out. Other services included
the rewinding of electric motors, and the building to
order of transformers, geared motors, and variable speed
motors.
By the 1950s the firm had a factory in Rollingmill
Street, Walsall called Robust Works, while still
retaining the Bradford Street premises.
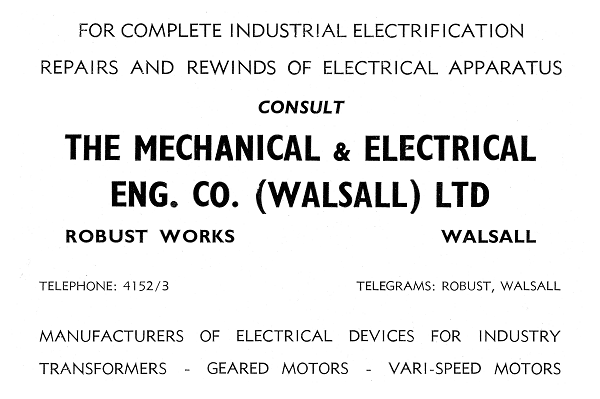
An advert from 1954. |
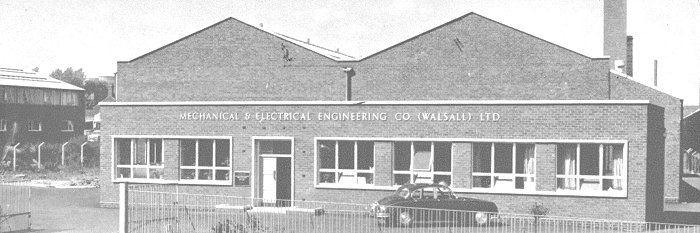
The factory in Rollingmill
Street. From 'The Steel Casting', courtesy of Wendy Marston. |
The Managing Director Mr.
Francis Webb. From
'The Steel Casting', courtesy of Wendy Marston. |
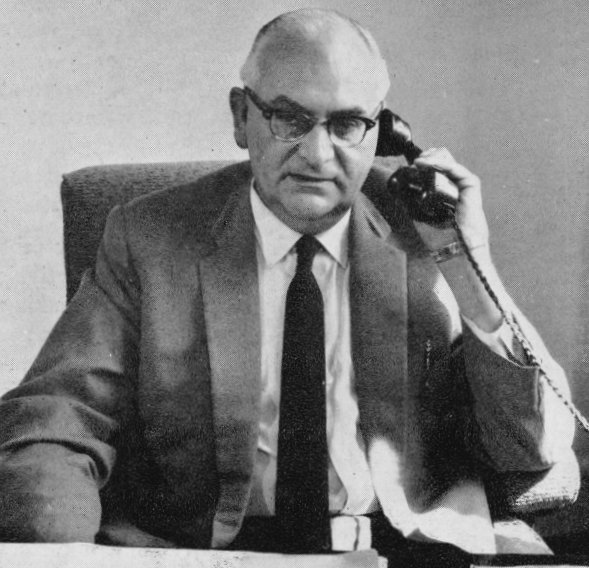 |
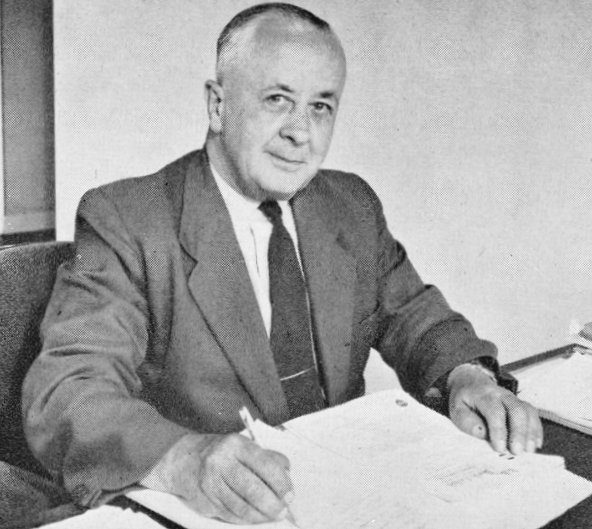 |
General Manager Mr. W. T.
Williams who joined the company in 1913 after
leaving school. From
'The Steel Casting', courtesy of Wendy Marston. |
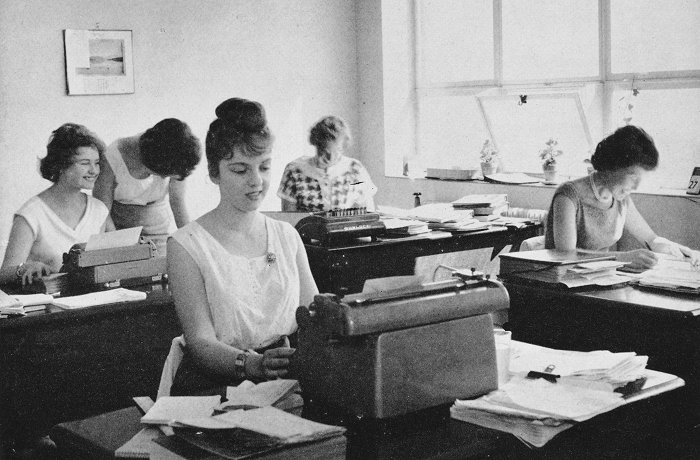
Some of the secretarial staff
in the office. From 'The Steel Casting', courtesy of
Wendy Marston. |
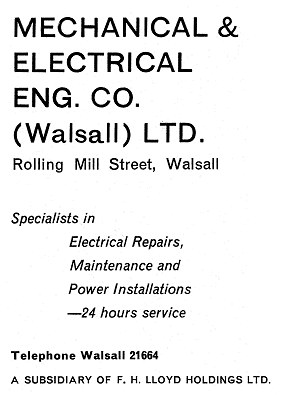
An advert from 1976. |
In about 1960 the firm became part of the Lloyd Group
and a new up-to-date factory was built in Rollingmill Street
which included a wide range of equipment to improve the
efficiency of the electrical repair department, and to
speed-up repairs. The new equipment included an
electrically-heated stove with a loading capacity of 400
cubic feet. It had two powerful fans to circulate hot air,
ensuring an even temperature throughout, and accurate
temperature control. It was mainly used to dry windings that
had been impregnated with insulating varnish.
The installation included heavy duty coil winding
machines which had been designed and built in-house, and
could handle the large high frequency coils used for the
melting and heat treatment of metals.
Metal spraying equipment was also installed along with a
heavy duty hydraulic press to deal with the extraction and
fitting of rotor shafts.
|
The works department had the facilities to repair all
kinds of electrical tools, and a large stockroom for
replacement parts, enabling an almost 'repair while you wait
service' to be carried out. By 1961 the firm employed
over 100 skilled men, some of whom started as apprentices in
the company's training scheme in the Bradford Street
workshops.
There were also contracting and maintenance departments,
and a subsidiary company EMCO Limited that provided a 24
hour maintenance service for all kinds of electrical and
electronic plant throughout the Midlands.
In the early 1960s EMCO carried out the installation and
wiring of the controls for the radar dishes (including the
one in the photograph opposite) at the Royal Radar
Establishment at Defford near Malvern. |
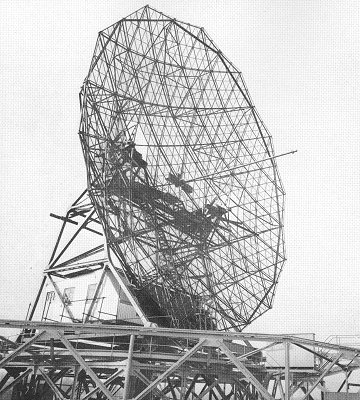 |
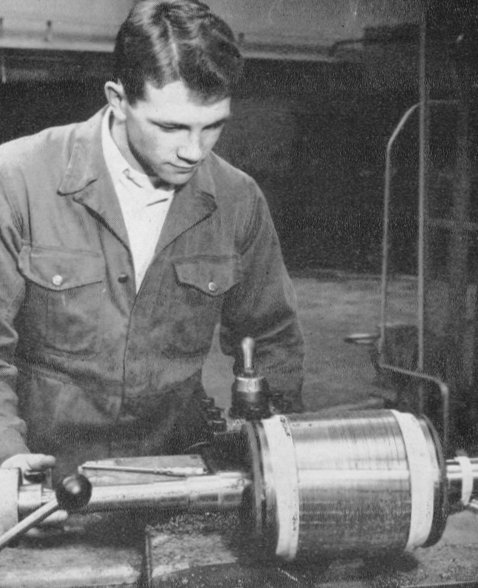 |
Mr. J. Morrell at work, machining a rotor core in
1961. From 'The Steel
Casting', courtesy of Wendy Marston. |
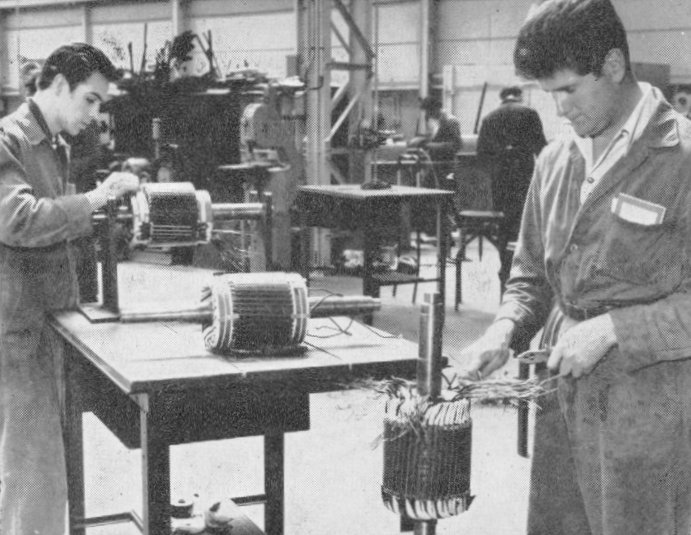
Pat Clift and Alan Rose winding
and connecting rotors. From 'The Steel Casting',
courtesy of Wendy Marston. |
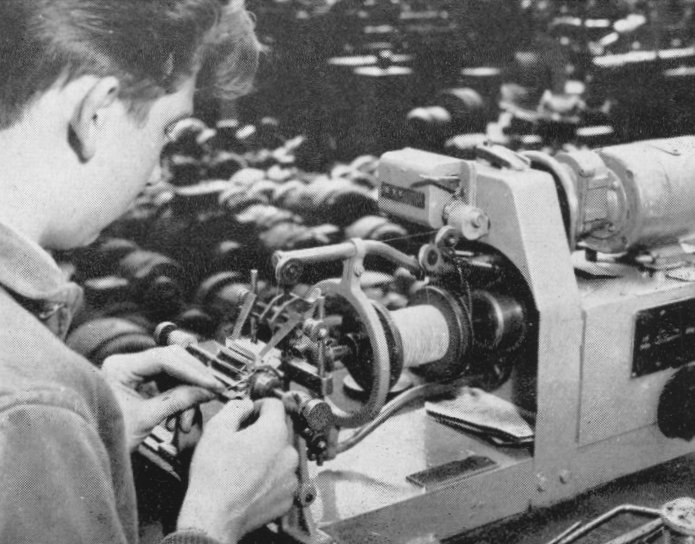
Mr. J. Davies, winding an armature
for a small electric motor in 1961. From 'The Steel
Casting', courtesy of Wendy Marston. |
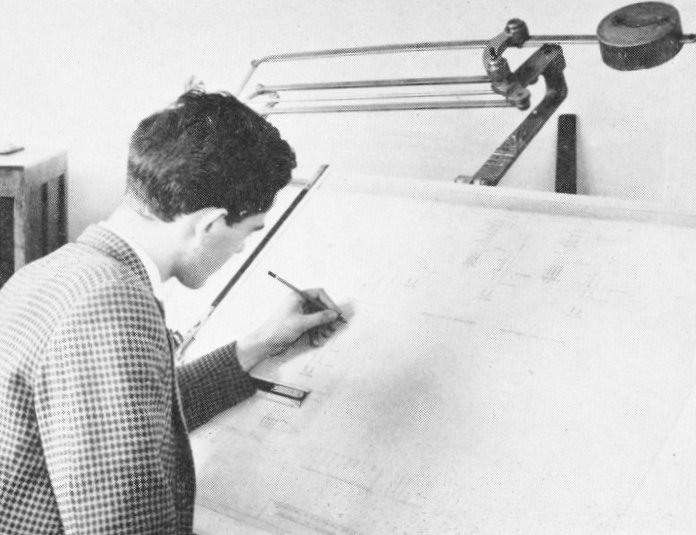
Colin Webb, son of the Managing
Director at work on a drawing board. From 'The Steel
Casting', courtesy of Wendy Marston. |
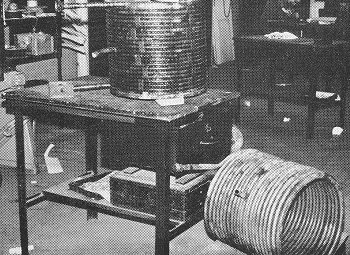 |
|
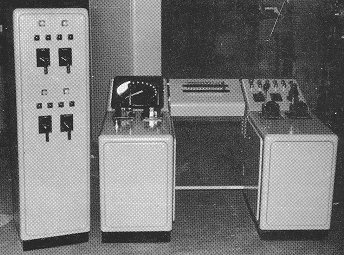 |
A newly
wound replacement high frequency coil, and the
control panel on one of the automatic machines. |
|
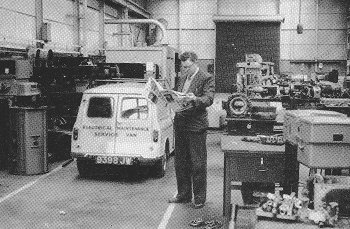 |
|
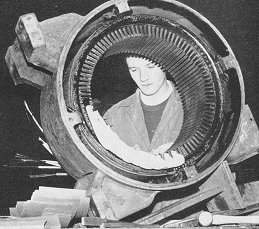 |
The
maintenance department, and a partly completed motor
rewind. |
|
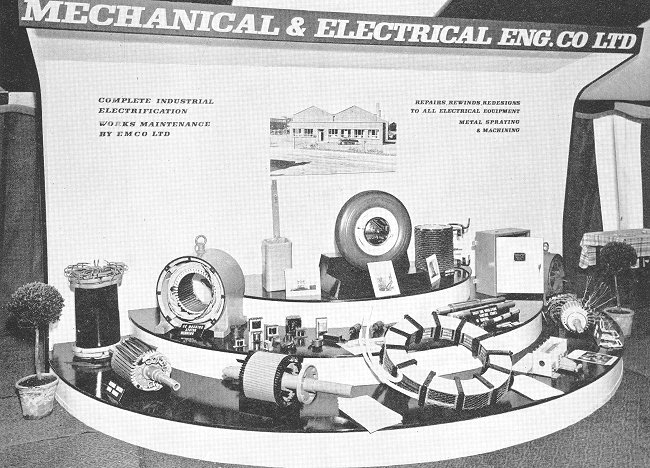
The company's stand at the
exhibition at James Bridge Steelworks to celebrate the
British Steel Foundry Year, in 1962. |
Some typical motor rewind
jobs: |
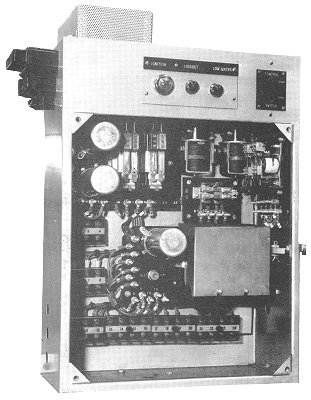 |
In 1963 the company opened an electronics section to
produce control equipment for a wide range of industrial
applications. The photograph opposite shows a control
panel for train heating boilers which provided
fully-automatic control from the driver's cab. The panels
were fitted to diesel locomotives by Spanner Boilers
Limited.
Other products manufactured by the section included an
electronic timer unit, timing from 0 to 100 seconds, and
temperature control units. |
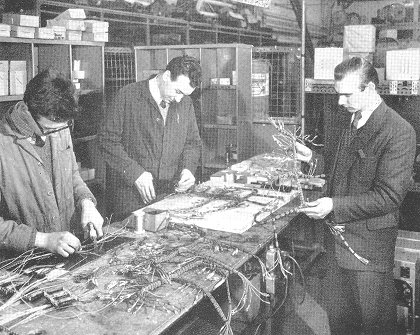 |
|
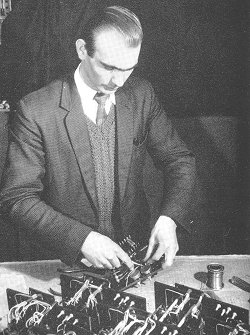 |
Producing
wiring looms, and wiring small control units. |
|
All kinds of electrical equipment
was overhauled in the company's workshops, including the
200hp. Sulzer-Haywood Tyler 150,000 gallons per hour
submersible pump opposite. It was used to lift water into a
canal from an underground reservoir, via 170 ft. of 12
inch diameter steel pipes. |
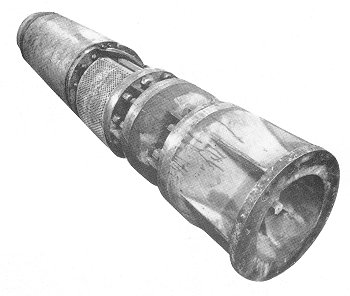 |
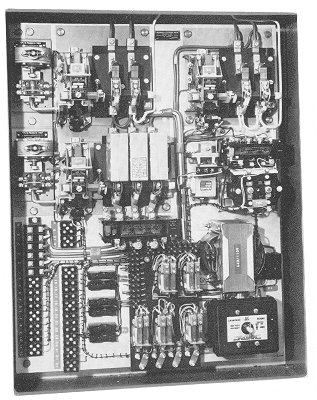 |
|
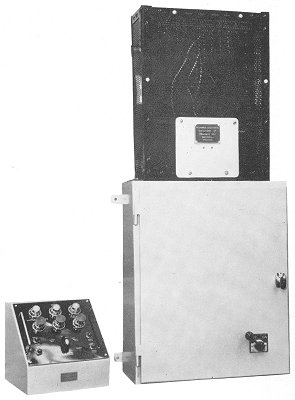 |
Examples of
the company's electronic control units. |
|
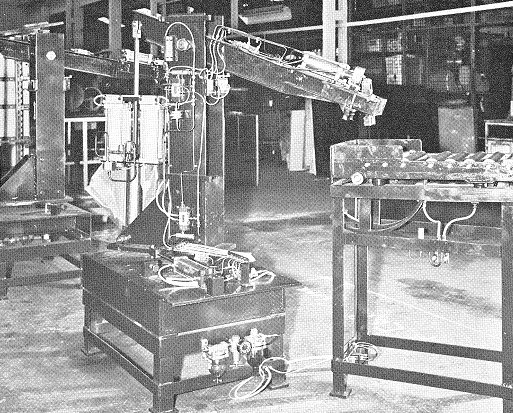 |
In 1971 the firm completed its
first export order to Yugoslavia.
It was for the 2-billet
pneumatically operated handling arm shown opposite. |
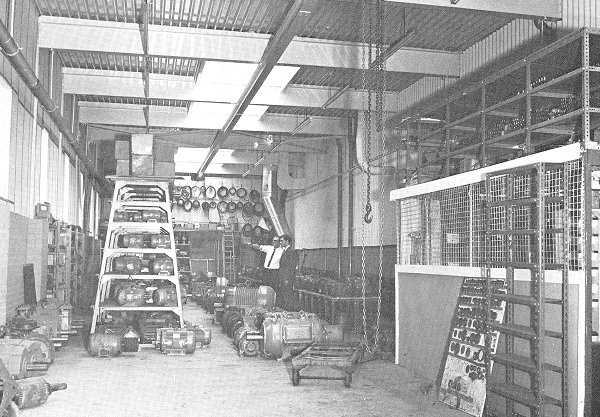
The new 3,600 square feet storage
bay, designed and installed by E. C. & J. Keay in 1971.
Keays also built a new works canteen with vending
facilities. |
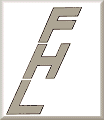 |
Return to the
previous page |
|