Background
It all started in the 1820s when Absolom
Harper and his two sons, John and Edward, founded A. Harper & Sons, ironfounders, at Waddams Pool Works in Hall Street,
Dudley. They specialised in the production of
fenders and fire irons. Absolom’s daughter Mary married George Bean,
a bank clerk who grew-up in Stamford, Lincolnshire,
where he was born in 1855. He met Mary while working
for a bank in Dudley, and soon became financial
manager of Allen, Everitt & Sons of Smethwick. After
their marriage George left his job and joined the
family business. In 1901 he became the principal
shareholder. The name was changed to A. Harper, Sons
& Bean in 1907 when George became chairman. |
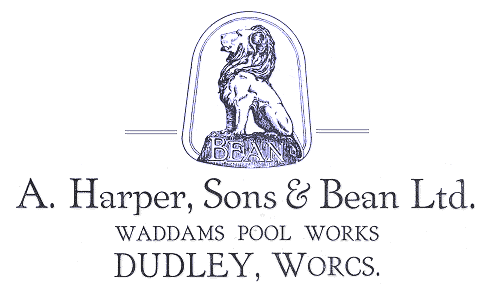
Drop hammers were installed at the
works in 1911 to produce forgings for the up and coming
motor industry. They were transferred to Smethwick in
1912 when the company established a forging plant there.
It still exists today as Smethwick Drop Forgings
Limited, now a part of GKN. There were 75 drop hammers
varying in size from 3 cwts to 3 tons, capable of
producing forgings up to 1½
cwts.
George Bean became Mayor of Dudley
in 1908, and again in 1911, and 1912. The business
greatly prospered during the First World War thanks to a
plentiful supply of ministry contracts for munitions.
The factory buildings were extended in order to increase
the production of shrapnel and shell cases. By 1916
around 21,000 shell cases were produced every week.
After the war George received a knighthood for his
services to the war effort, and his only son John, known
as Jack, who also worked in the business, was made a
CBE.
The Bean Car
At the end of hostilities the
lucrative munitions orders ceased and something had to
be quickly found to replace them, so that the business
could survive. At the time motor cars were becoming
increasingly popular, and so the decision was taken for
the company to become a car manufacturer.
At this time the jigs, patterns,
tools, and manufacturing rights for the Perry car were
up for sale and so A. Harper, Sons & Bean purchased them
in January 1919 for £15,000 as a way of quickly getting
into the industry by buying a tried and tested design.
The Perry car was made by the Perry
Motor Company at Tyseley, Birmingham. The business was
founded by James and Stephen Perry who made pen nibs in
London before moving to Birmingham to build bicycles. In
the late 1890s their business was purchased by James
William Bayliss, one of the owners of the Bayliss-Thomas
car company. Perry’s first car, the 8hp. Perry 8
cyclecar appeared in 1913 and remained in production
until 1915. It was designed by Cecil Bayliss, son of
James Bayliss. The car had an unusual two cylinder
engine in which both the cylinders rose and fell at the
same time.
About 800 Perry 8s were produced. In 1914
the company launched the Perry 11.9, a full-sized car
powered by a Perry four cylinder 1795c.c. engine.
Production continued until 1916 by which time over 300
had been produced. After the war Perrys decided not to
resume car manufacturing and so the design was put up
for sale. After their purchase, A. Harper,
Sons & Bean decided to manufacture the car and call it
the Bean.
Into Production
Jack Bean the company’s Managing
Director was an extremely ambitious man who planned to
produce vast numbers of the Bean car, to become one of
the country’s leading car manufacturers. With this in
mind he visited America to purchase the latest
machinery. As a result the company became one of the
first in the country to have twin moving track assembly
lines. |
Jack envisaged a large organisation
formed from a consortium of manufacturers that between
them could produce maybe 75,000 cars and 25,000 lorries
a year, something like the massive General Motors
combine in America.
He planned to take on the British
built model T Ford. Thanks to his drive and enthusiasm a
group of companies including vehicle maker Swift, car
and lorry maker Vulcan, Hadfield Steel Company of
Sheffield, the Regent Carriage Company, and radiator
makers Alex Mosses, and Gallay came together to Form
Harper Bean Limited in November 1919.
A newly built factory at Tipton began to produce
complete car chassis which were driven
to the Waddams Pool Works in Dudley for the bodies to be fitted. The Smethwick factory would provide all
of the forgings that were necessary.
The body shop at Waddams Pool Works occupied a site
covering 327,000 square feet. It had a capacity of
twenty cars per day.
Departments included the body assembly department,
the paint shop, the sawmill, the trimming shop, the
experimental department, and the cushions and hoods
department.
|
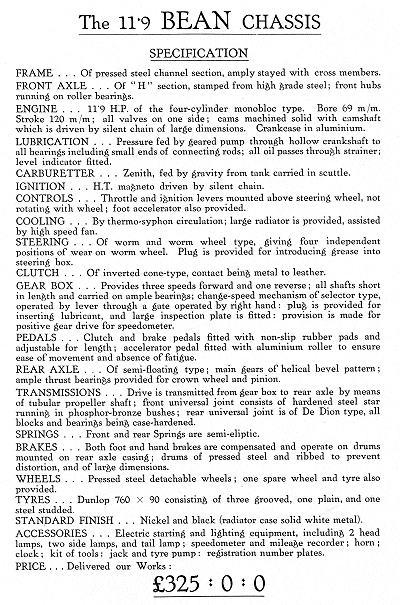 |
The company’s first car, the Bean
11.9, a slightly updated Perry design, was launched at
the 1919 Motor Show. The models on display consisted of
a 2 seater tourer priced at £425, a 4 seater tourer
priced at £450, and a complete chassis. The range was
soon augmented by the addition of a 2 seater coupé
priced at £500, and a 4 seater coupé priced at £550.
Harry Radford was employed as Chief Designer to oversee
the initial modifications that were made to the Perry
design, and Tom Conroy an American production engineer
took charge of the Tipton factory. |
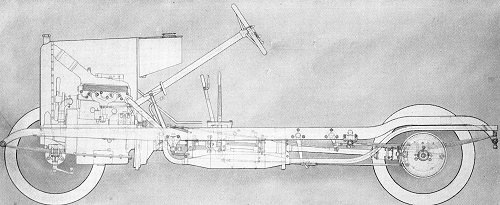
From the 1919 Bean catalogue. |
The Bean 11.9 chassis that was built at
the Tipton factory. |
Another view of the 11.9 chassis.
|
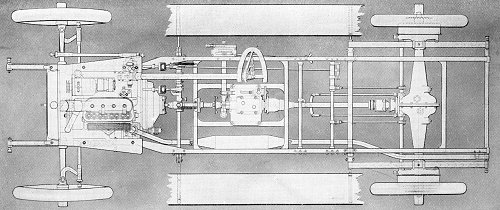
From the 1919 Bean catalogue. |
Production began in earnest in
January 1920 and soon 80 chassis were
completed each week. Unfortunately the Dudley factory
couldn’t produce enough bodies and so an order for 2,000
bodies was placed with Handley Page of Cricklewood. In
1920 around 2,000 Beans were produced. |
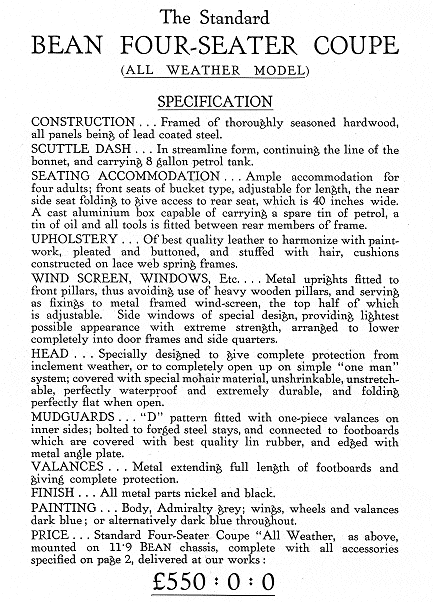
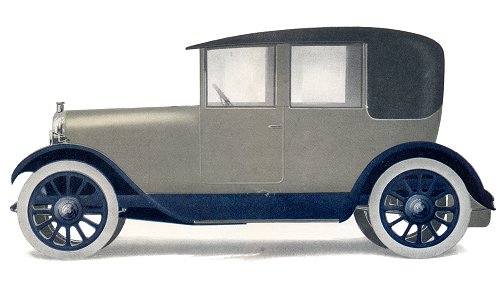
From the 1919 Bean catalogue. |
The Bean 11.9 four seater coupé
with the hood up. |
A side view of the Bean four seater coupé. |
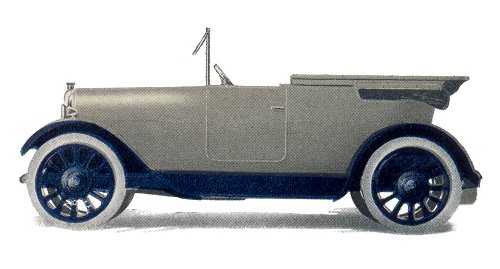
From the 1919 Bean catalogue. |
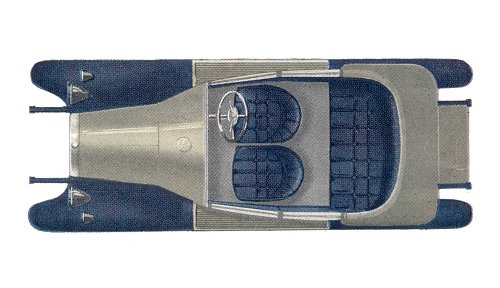
From the 1919 Bean catalogue. |
A plan view of the Bean four seater coupé
showing the seating arrangements. |
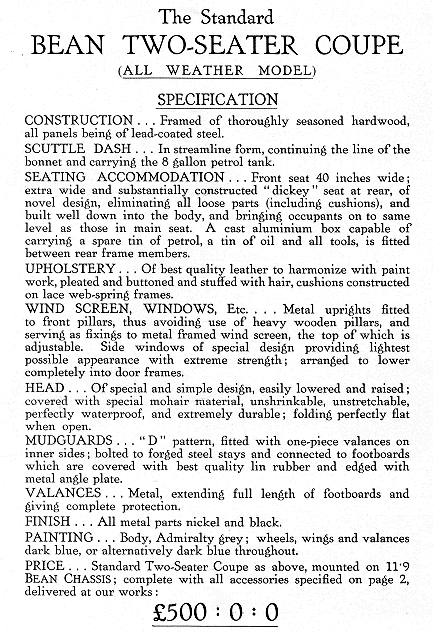
The Bean 11.9 two seater coupé
with the hood up. |
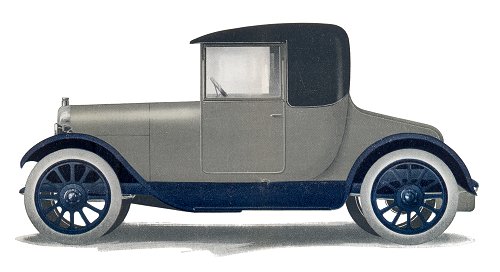
From the 1919 Bean catalogue. |
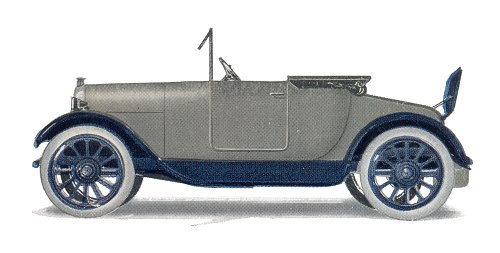
From the 1919 Bean catalogue. |
A side view of the Bean two seater coupé
showing the dickey seat. |
A plan view of the Bean two seater coupé
showing the seating arrangements. |
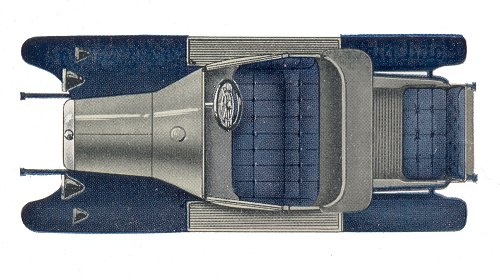
From the 1919 Bean catalogue. |
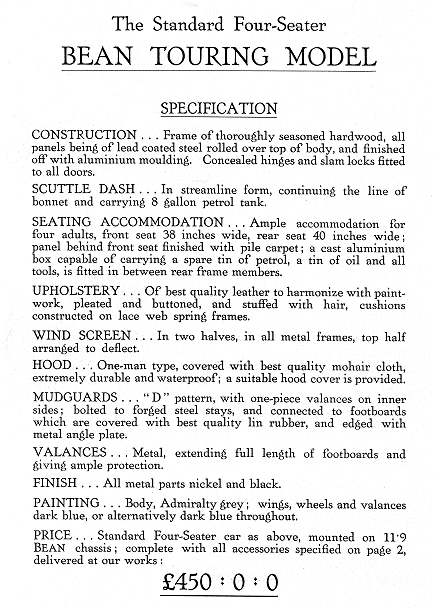

From the 1919 Bean catalogue. |
The Bean 11.9 four seater touring model with the
hood up. |
A side view of the Bean four seater touring
model. |
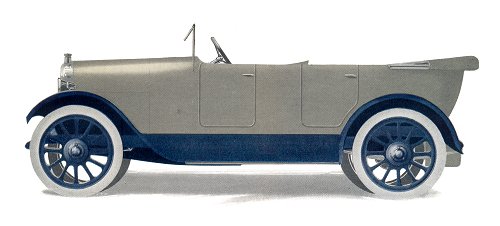
From the 1919 Bean catalogue. |
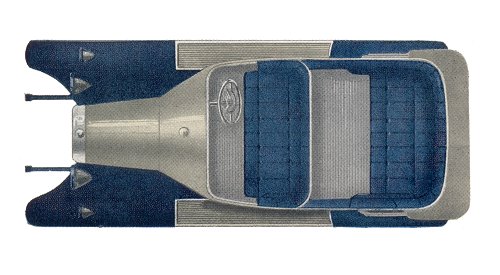
From the 1919 Bean catalogue. |
A plan view of the Bean four seater touring
model showing the seating arrangements. |
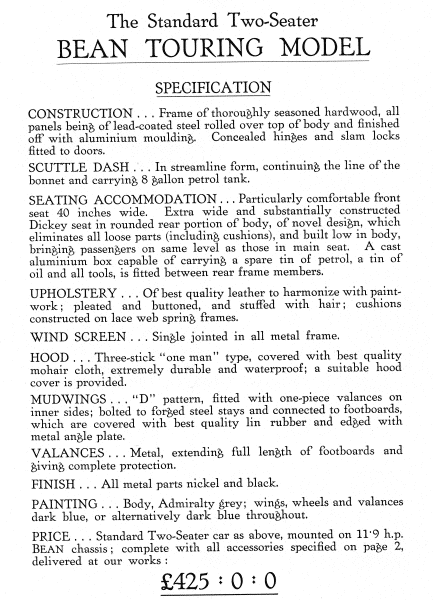
The Bean 11.9 two seater touring model with the
hood up, showing the dickey seat. |
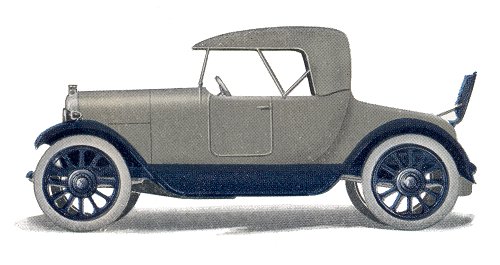
From the 1919 Bean catalogue. |
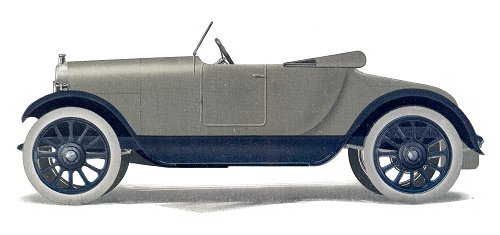
From the 1919 Bean catalogue. |
A side view of the Bean two seater touring
model. |
A plan view of the Bean two seater touring model
showing the seating arrangements. |
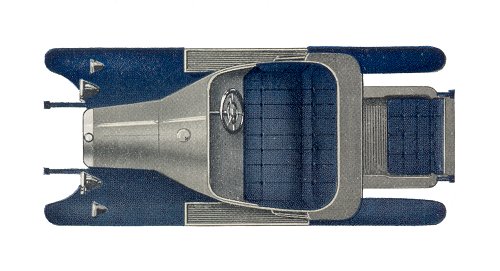
From the 1919 Bean catalogue. |
The Tipton factory covered a large
site alongside Hurst Lane and the canal. The foundry
covered 122,000 square feet, with four 360 ft. long
bays, five cupolas, overhead cranes with capacities
ranging from five tons to fifteen tons, and an output of
250 tons of castings per week.
The main factory was extremely well
organised, with electric trucks conveying materials from
one part of the factory to another. The machine shops
were organised on a 'flow system' so that materials and
components progressed in an orderly fashion to the
assembly lines. The shops were fitted with the most
up-to-date machinery including a large plane miller
capable of machining twelve sets of cylinders at a time.
There were seven multi-spindle drilling machines which
could drill seventy two holes in one operation. Three of
them were used to tap the forty four holes in the
cylinder blocks and crankcases. There were twenty gear
cutting machines, automatic machines to machine front
and rear hubs, and a machine to drill and ream big ends
and connecting rods, four at a time.
There was an array of grinding
machines in the grinding department, and seventeen
gas-fired furnaces in the heat treatment section. All
completed engines were thoroughly tested with a
dynamometer and had to develop at least twenty one
horsepower.
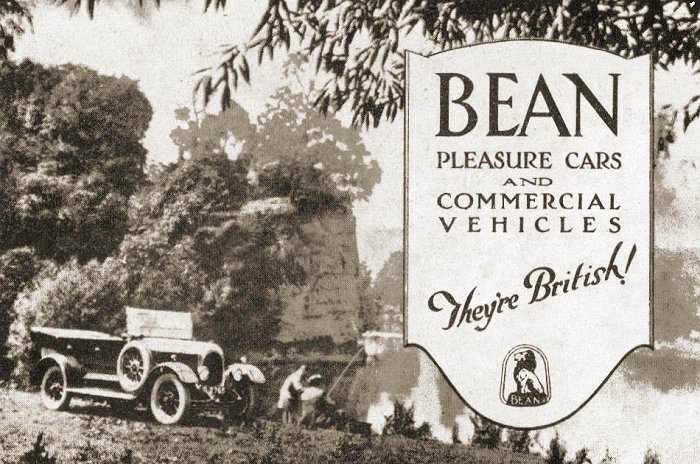
The assembly shop covered an area
of 450 ft. by 90 ft. and had a long constantly moving
assembly track on which the chassis frame was drilled,
and all of the components were added in sequence. The
engines were lowered into place with a pneumatic hoist
to minimise handling, and groups of fitters alongside
the track carried out the assembly work. At the end of
the track, the completed chassis ran down a slope to the
test track, where they were driven, and any necessary
adjustments made before starting their journey to
Waddams Pool Works, where the bodies were fitted.
During the
early summer of 1920 the selling prices rose dramatically,
mainly because of wage rises. The price of the 2 seater
tourer increased to £600, and the 4 seater tourer
reached £650, both models costing considerably more than
the competition. As a result the company was forced to
slash the prices in order to undercut the competition,
in readiness for the Motor Show that autumn. At the show
the 4 seater was on offer at £545.
To add to the company’s troubles,
the post war boom in the car industry had come to an end
and the following recession rapidly saw the end of the
Harper Bean conglomerate. The company owed around
£475,000 to trade suppliers and so a receiver was
appointed. Production ended at Tipton in October 1920
and in the following month Jack Bean resigned from the
company.
Rejuvenation
During November 1921 a huge
investment of capital by Sir George Bean, Barclays Bank,
The National Provincial Bank, and Hadfields enabled them
to buy a 55% controlling interest from Harper Bean and
repay the creditors. This allowed A. Harper, Sons & Bean
to manage their own affairs again, but would have
serious financial implications five years later.
Production of the Bean 11.9
restarted early in 1922. The car had an improved clutch
and was available as an open 4 seater tourer, and a 2
seater with dickey. Production slowly increased,
reaching 100 cars a week by August. |
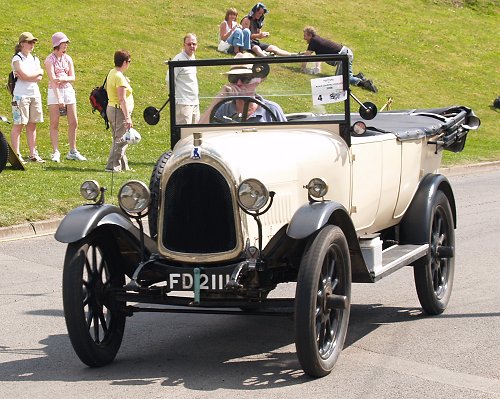 |
Maurice Luscot Evans' Bean
11.9 tourer from 1926. |
Another view of Maurice
Luscot Evans' Bean car. |
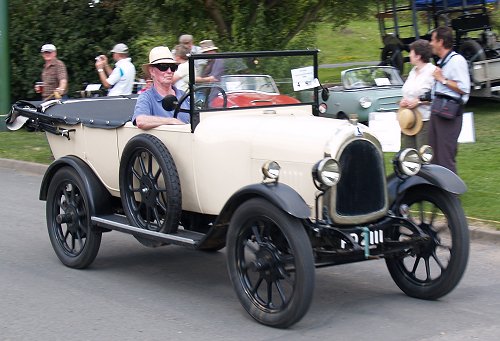 |
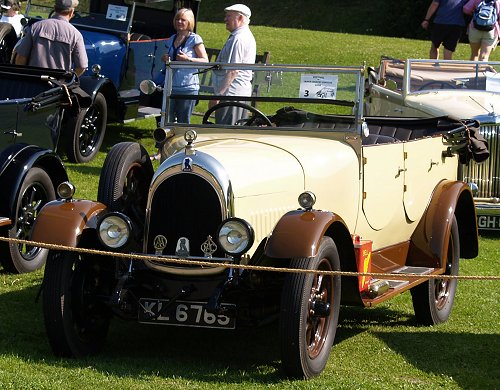 |
The 1925 Bean 11.9 tourer
that belongs to Mrs. D. Thomas. |
Stuart Gray's Bean
tourer from 1924. |
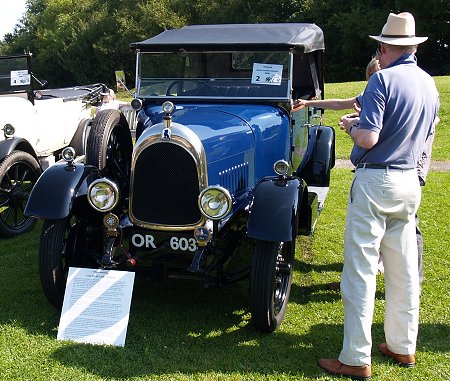 |
October 1923 saw the launch of a
new car, the much larger Bean 14, powered by a 13.9hp.
engine and fitted with a 4 speed gearbox. Several
different bodies were available ranging from a tourer, a
3 seater with dickey, a coupé, a four door saloon, to a landaulette. The car sold particularly well in
Australia, partly due to the exploits of Francis Birtles
who made the first double crossing of the continent by
car. He drove a Bean 14 from Sydney to Darwin and back.
The Bean 12, a smaller version of
the Bean 14 was launched in May 1924. Four models were
available, ranging from a 2 seater plus dickey, a coupé,
a 4 seater tourer, to the top of the range brougham.
In November 1924 the company
launched the first Bean commercial vehicle, a 25 cwt.
chassis based on the 13.9hp. engine and gearbox. The
vehicles mainly appeared as a lorry, but vans,
ambulances, coaches and light buses were also made.
Sadly the company’s chairman Sir
George Bean died in 1924 at the age of 68. He was
replaced by Major Augustus Clerke, Hadfield’s Managing
Director, and a director of Bean since 1921. |
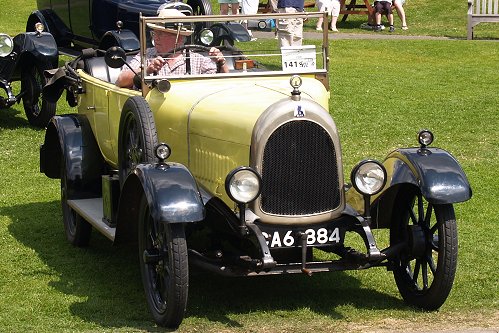 |
Malcolm Knowles and his
Bean 14 tourer. |
Another view of Malcolm
Knowles' car. |
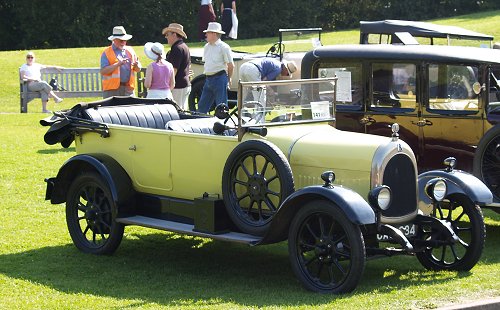 |
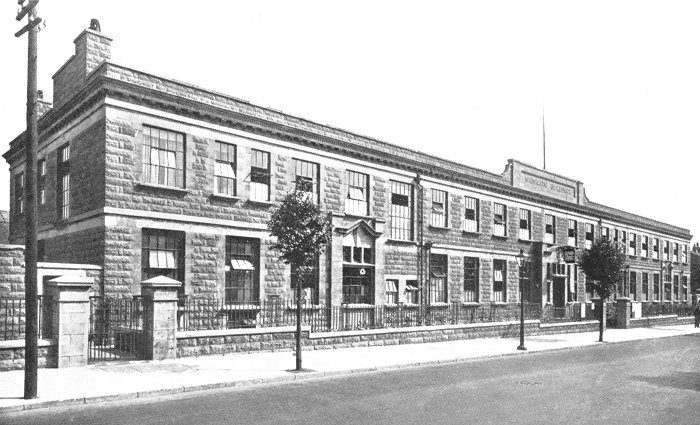
The company's offices in
Sedgley Road West. The building was sold to Tipton
Council in 1935. |
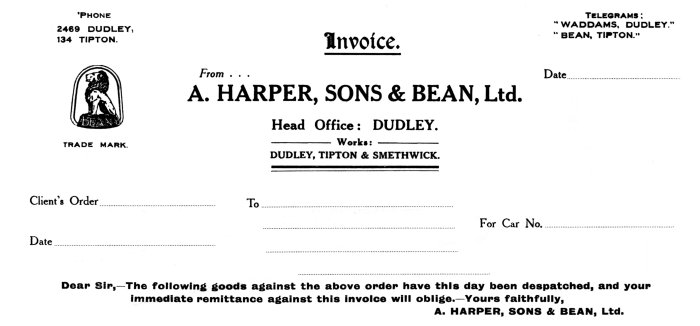
An invoice from the mid 1920s.
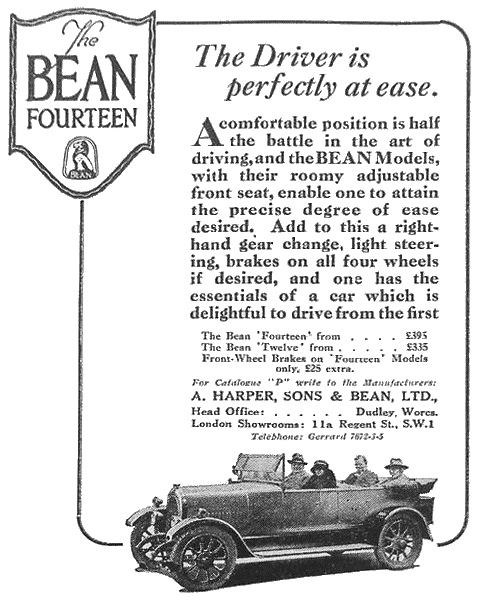
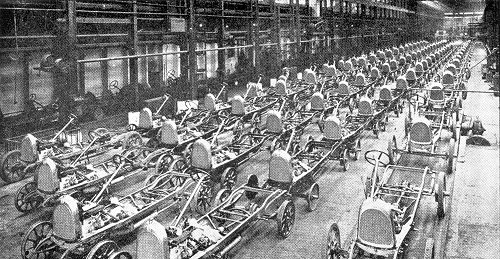
The Tipton factory in 1925.
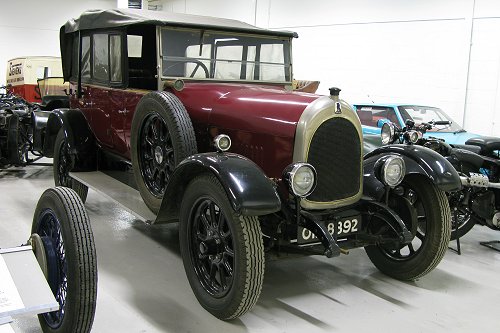 |
The 1925 Bean
14 that's on display at the Black Country Living
Museum, Dudley. |
Another view of the Black
Country Living Museum's Bean 14. |
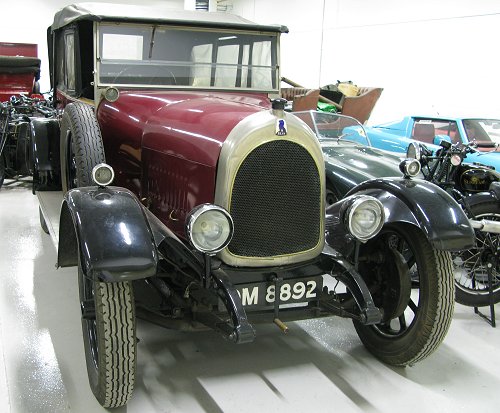 |
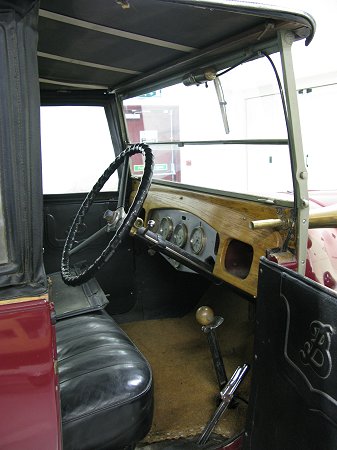 |
The interior of the
Black Country Living Museum's Bean 14. |
Unfortunately the company suffered
from an acute shortage of cash with debts totalling £1.8
million, mainly due to the restructuring in November
1921. As a result Hadfields the Sheffield steel
producer rescued the company and renamed it Bean Cars
Limited, in June 1926.
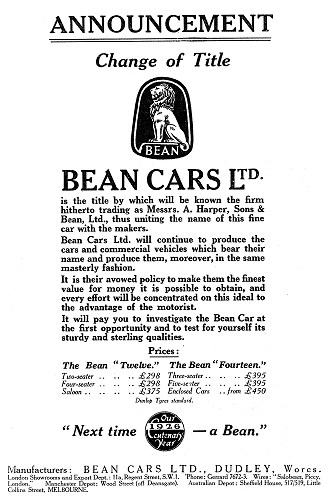
An advert from June 1926.
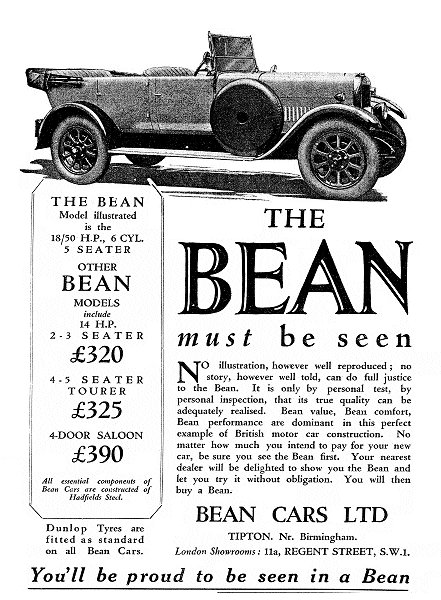
An advert from 10th June,
1927.
The Hadfield Era
Initially little changed after
Hadfields’ takeover. The same models continued in
production, but there were changes in management. Hugh
Kerr Thomas became a director and took over as General
Manager, and Jack Bean left Dudley in April to go on a
world tour to promote the company’s products. He
returned in March, 1927 and promptly resigned as
Managing Director to join the Board of Guy Motors.
To reduce overheads, some of the
Bean factories, including the Dudley site were sold.
From now on production would be concentrated at the
Tipton site, where a new body shop was completed in
1927.
|
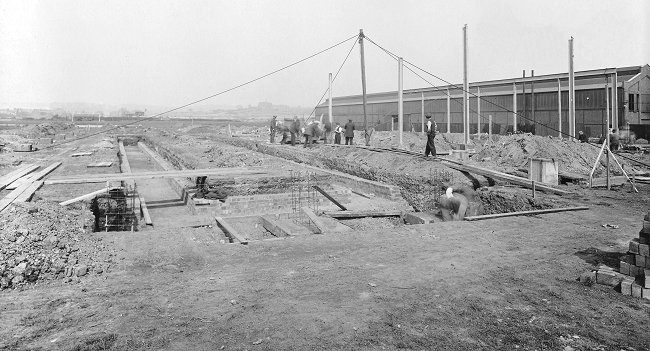
Work on the new body shop was
well underway by 13th May, 1927. |
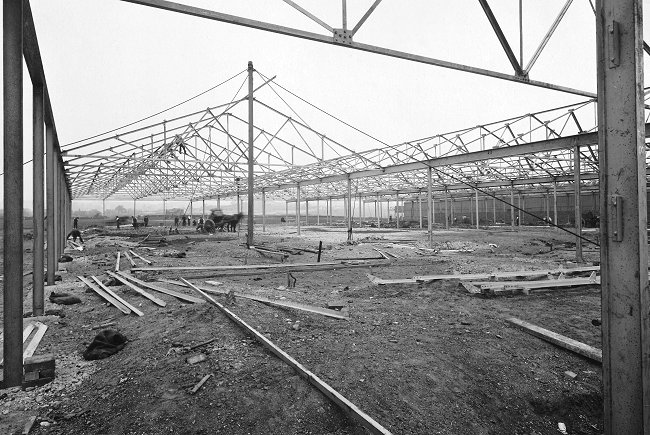
Work on the new body shop
progresses rapidly. By 26th May much of the
structural steelwork was in place. It was made by,
and installed by Wilfred Robbins Limited of Golds
Hill Ironworks, Great Bridge. |
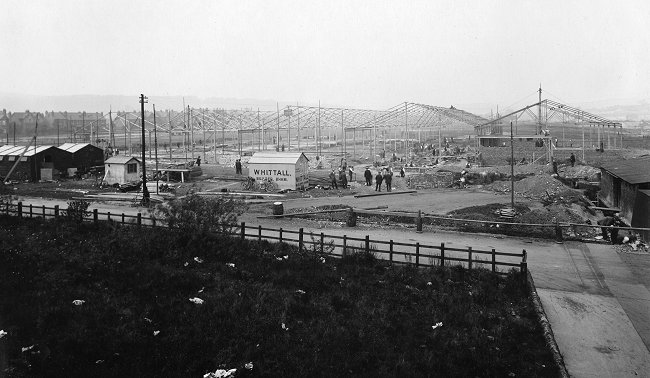
Within a few days the
structural steelwork was complete. The remainder of
the building was built by Whittall of Birmingham.
|
1927 saw the introduction
of the 18/50 that was powered by a 2.7 litre, overhead
valve Meadows engine with a Meadows gearbox. They also produced a
similar car called the “Imperial Six”. Francis Birtles
attempted to drive one of the early prototypes from
England to Australia, but gave up in India after the
second failure of the car’s back axle. The car never
made it into production. Undaunted, he returned in
October to have another go, this time in his faithful
Bean 14 called “The Sundowner”. He achieved his goal by
reaching Melbourne nine months later.
In 1927 a number of changes were
made to the existing product range. Bean 12 production
ended, around 3,000 had been built. The Bean 14 became
the Long 14, and the Short 14 was introduced. This
consisted of a Bean 12 chassis, powered by a 14 engine.
The Long 14 had a relatively short life. It was
discontinued in 1928.
|
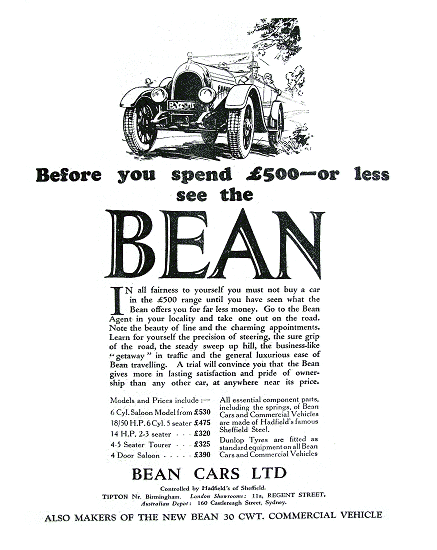
An advert from 1927.
In January 1928 the Hadfield Bean
14/40 designed by R. P. Turner went into production.
Powered by a 2,297c.c. engine, it had a top speed of
nearly 60m.p.h. Several versions were available, ranging
from a 5 seater tourer priced at £325, a saloon priced
at £495, to the Sunshine saloon with a folding roof.
March saw the introduction of the
Hadfield Bean 14/45, one of the worst car designs to
ever go into production in the UK. It had a top speed
of 65m.p.h., Dewandre servo brakes, powerful beam
headlights, and wide doors. The saloon sold for £435, and a
5 seater tourer was priced at £325. Fabric bodied
versions were also available as the Hadfield Bean 14/70.
The car went into production before the design had been
fully tested and developed. It resulted in a long
catalogue of faults which soon became apparent. Amongst
the problems were frequent back axle failures, and an
extremely heavy clutch. |
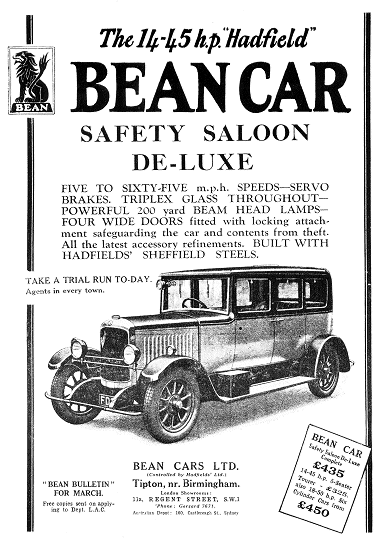
An advert from 1928.
Bean cars had gained a reputation
of being average, but reliable performers. The
14/45 put an end to all that. The company soon got a
bad reputation, and sales fell to around 25 cars a week.
By March 1929 the number of new cars with faults that
were returned to the factory, was higher than the number
of cars being produced. Returns also included some
faulty 30 cwt. commercials. As a result car
production ended in 1929, and efforts were made to
improve the reliability of the commercials, which continued
in production for another two years. In June
1931 the company went into voluntary liquidation and
vehicle production ended.
Cars
Produced |
Title |
Factory Model No. |
Years
in Production |
11.9 |
1 |
1919
to 1922 |
11.9 |
2 |
1923
to 1924 |
14 |
3 |
1923
to 1928 |
12 |
4 |
1924
to 1927 |
Short
14 |
6 |
1927
to 1928 |
18/50 |
7 |
1927
to 1928 |
14/40, 14/45, 14/70 |
8 |
1928
to 1929 |
|
Commercial Vehicles
In November 1924 the company launched the first Bean
commercial vehicle, a 25 cwt. chassis based on the
13.9 hp. engine and gearbox. The vehicles mainly
appeared as lorries, but vans, ambulances, coaches
and light buses were also made. The engine and
gearbox were mounted on a separate chassis, and
initially, the vehicle only had rear wheel brakes.
The 20/25 cwt. chassis sold for £265. From 1926
front wheel brakes were available for an extra £20.
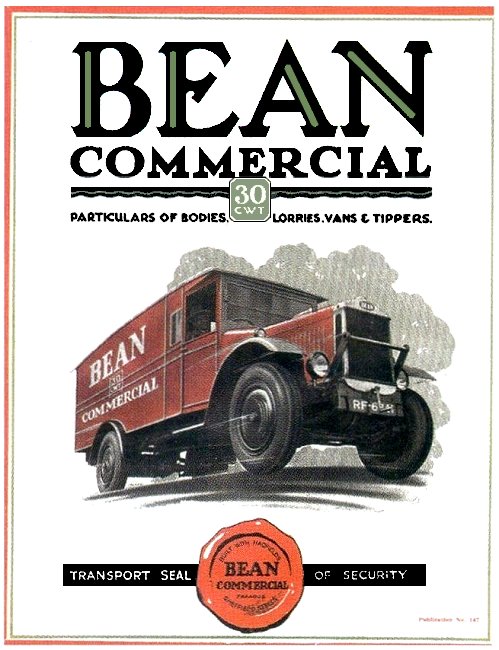 |
In June 1927 the chassis was
replaced by a 30 cwt. model designed by
Hugh Kerr Thomas. It had a 2.3 litre
Ricardo high turbulence cylinder head
engine, and sold for £325.
By this time the commercial chassis
accounted for about 60% of the total
production at Tipton.
The 30 cwt. chassis continued in
production until 1929 when it was
replaced by the 'Empire' model, powered
by a 3.6 litre Ricardo high turbulence
cylinder head engine.
It only remained in production for about
18 months, when it was replaced by an
updated version of the original 20/25
cwt. chassis, powered by a 2.3 litre
Hadfield engine.
The new chassis was only manufactured
for just over three months, before Bean
Cars Limited went into receivership. |
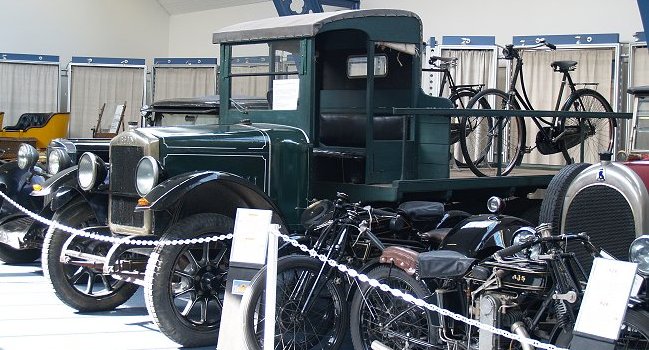
The 20/25 cwt. lorry from
1926, that's in the collection at the Black Country
Living Museum.
The Type 'W'
30 cwt. lorry from 1930, that belongs to
Daniel Batham and Son Limited.
As seen at the
Black Country Living Museum in 2010. |
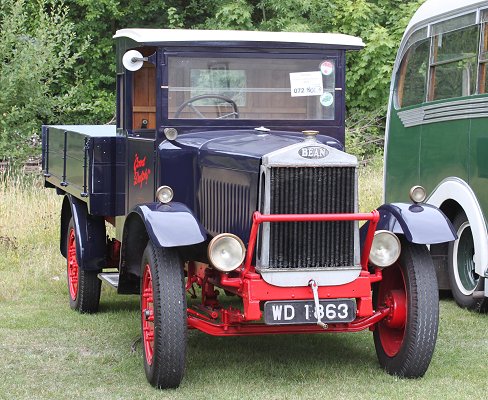 |
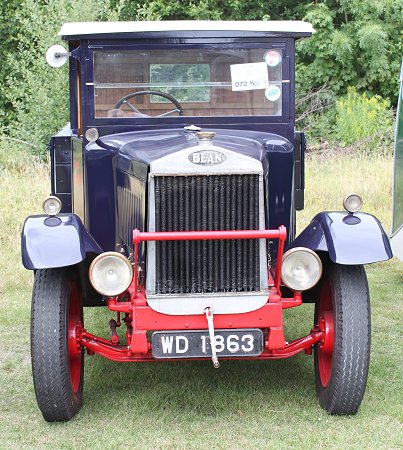
Another view of the Type
'W' 30 cwt. lorry.
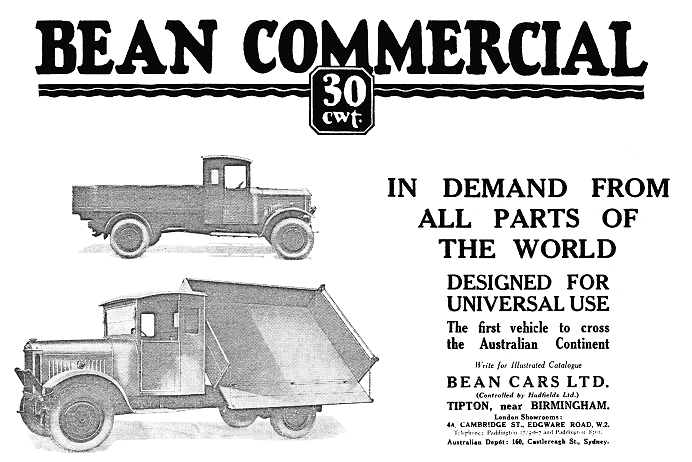
An advert from The Times Trade
& Engineering Supplement, 25th May, 1929.
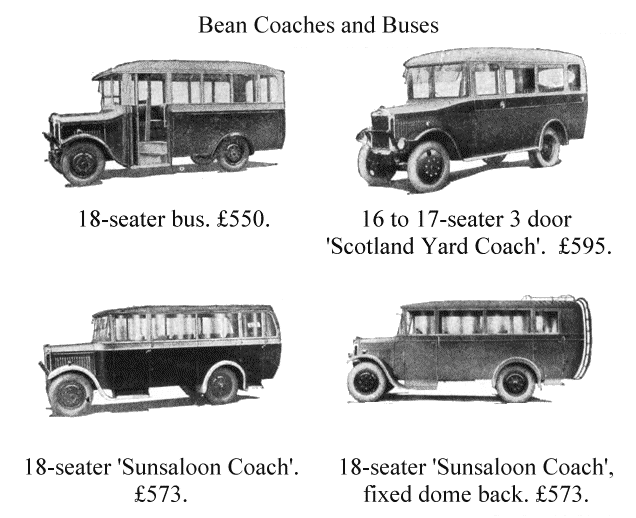
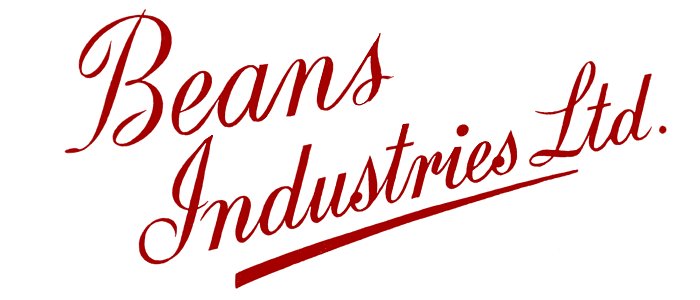
A new chapter started in November
1933 when Hadfields re-launched the business as Beans
Industries. The new company would produce castings for the motor
industry.
The business soon became profitable again, and
in 1936 the drop forging business at Smethwick became
Smethwick Drop Forgings Limited, later becoming part of
GKN.
In 1937 Beans Industries became a public company. |
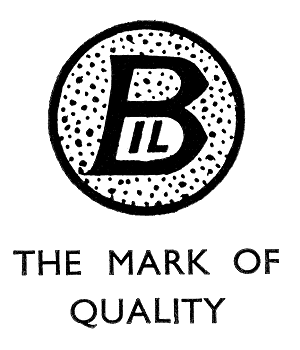
Trademark. |
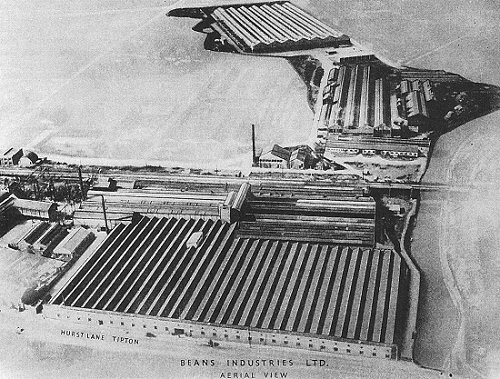
Record Breaking
In 1937 a final car was built at
the Tipton works when the company obtained the contract
to build George Eyston’s world land speed record
breaking car the ‘Thunderbolt’. The car, powered by two
Rolls Royce V12, 36.5litre engines, each delivering 2,350b.h.p.,
weighed 7 tons. One of the engines had previously
powered a Schneider Trophy winning aircraft.
There were three axles and eight wheels.
The two leading axles steered, and were of varying track.
The driven rear axle had twin tyres to spread the
weight.
At the rear was a large triangular tail fin to provide
directional stability, and on top were the engine
air intakes, and the exhaust outlets. The driver sat
ahead of the engines, behind the second pair of
front wheels. |
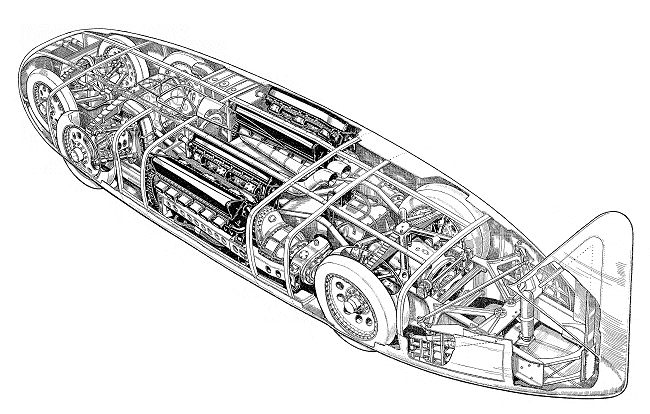
The 'Thunderbolt', as originally built.
The air intake pipes for the superchargers were
brought to the top of the body to avoid sucking-in
the salt spray from the dry Utah lakebed, where the
record attempt was to take place. Each engine had
its own clutch, with a drive to the 3 speed gearbox.
From the gearbox the drive was taken to the
differential-less rear axle via a bevel and crown
wheel. The dimensions of the car were as follows:
length - 30ft. 5inches; height
- 46 inches; width - 7ft. 1½
inches
|
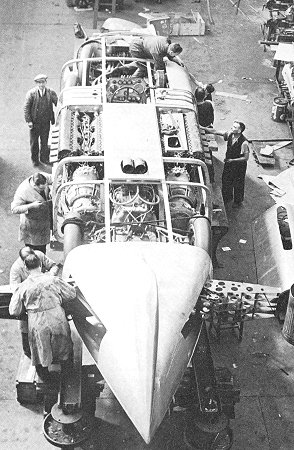
The Thunderbolt; under
construction at Tipton. |
Eyston and his team took the car to
the Bonneville Salt Flats in America for the record
attempt. The team arrived in October 1937 but
proceedings were delayed for a fortnight due to clutch
problems and bad weather. During a couple of trial runs the
car easily reached 230m.p.h.
The first attempt on 28th October
ended in failure. On the first run of the 10 mile
course the car reached 310m.p.h. but during the
return run the dog clutches that coupled the two
engines failed. Another attempt a week later ended
with same result,
the car achieved 310m.p.h. on the first run, but the
clutches again failed during the second run.
As a result new clutch parts
made to Eyston's design were hurriedly produced by
two racing engineers in Los Angeles. The parts
arrived on 17th November and two days later the car
was ready for another attempt on the record.
On the first run the car
achieved 305.59m.p.h. and reached 319.11m.p.h. on
the return run. The average speed for the kilometre
was 312m.p.h., and for the mile, 311.42m.p.h. George Eyston
had broken Sir Malcolm Campbell’s existing record by 11m.p.h.
|
In 1938 the car returned to the
salt flats for another attempt at the record. Several
modifications had been made to the car. The streamlining
was improved with a rounded nose, and a fully enclosed
cockpit was added with a respirator for the driver. The
first attempt on the record took place on 24th August
and Eyston and the car performed superbly reaching
347.155m.p.h. on the first run. Unfortunately things
went wrong on the equally fast second run when the time
keeping equipment operated by Art Pillsbury failed to
register the time. It seems that the sensor failed to
register the shiny car against the white salt
background. As a result a black arrow with a yellow disc
was painted on the side of the car to cure the problem.
On 27th August the car returned
for another attempt on the record. This time
everything went well, and the car achieved a new
record of 345.49m.p.h.
On 12th September Eyston's
rival John Cobb made an attempt on the record in his
Napier-Railton car, reaching 342.5m.p.h. Three days
later he took the record at 350.2m.p.h. |
Undaunted, Eyston prepared to
have another go at the record. After his last
success he hurriedly made some improvements to the
car. He completely covered the nose after removing
the radiator and replacing it with a tank cooling
system, and also removed the tail fin. On 16th
September he was ready for another attempt on the
record. After a wonderful performance the
Thunderbolt re-took the land speed record after
achieving 357.5m.p.h. |
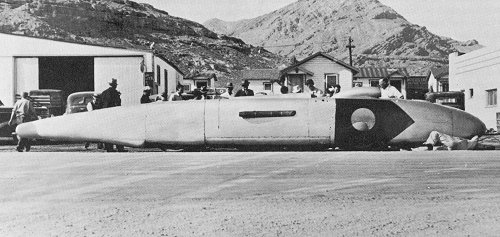
The Thunderbolt in its final
form. |
Unfortunately the car was
eventually destroyed by fire during a tour of New
Zealand in the early 1940s. The remains of the engines
can be seen in the Museum of Transport and Technology,
Western Springs, Auckland.
Back to Tipton
During World War 2 the company
produced lorry engines, parts for army trucks, and parts
for aircraft.
|
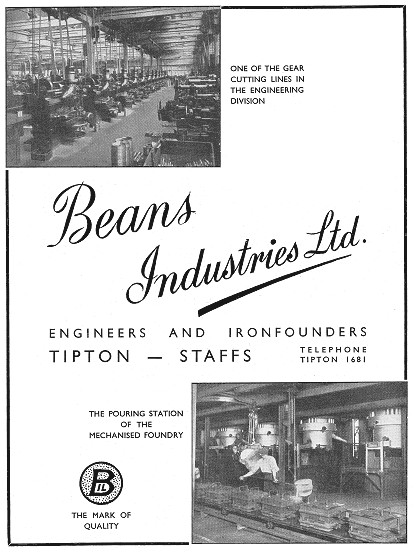
An advert from 1954. |
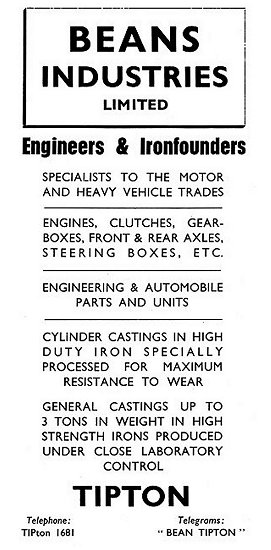
An advert from 1947. |
In the early 1950s the business went from
strength to strength. By this time, the foundry
alone covered an area of around 297,000 square feet,
and could produce five hundred tons of iron castings
each week. The foundry had a large number of
up-to-date machines, used to manufacture automotive
components and assemblies of all kinds. It had a
sand handling plant, moulding machines for medium
repetitive work, and a traditional floor moulding
section for jobbing work. Production included castings of almost every kind
for numerous industries, and castings for
vehicle manufacturers including flywheels, brake
drums, manifolds, and gearboxes. The cylinder section produced over 1,000 castings
a week, for all kinds of cylinder blocks, heads, and
crankcases. The general section produced large
numbers of high quality engineering castings from a
few pounds up to five tons in weight. They included machine tools, press castings,
cylinders for marine oil coolers, steam jacketed
tube moulds, tractor transmission cases and axle
sleeves, diesel engine beds, columns, motor
gearboxes, oil engine parts, hydraulic cushion
cylinders, etc., etc. |
Precise control of everything from pig iron,
sand, and all materials, through to the finished
cast metal was carefully maintained. Each ladle of
metal was individually tested to ensure that the
correct composition was used for each casting, to
guarantee high tensile strength, combined with good
machineability.
The firm gained a high reputation for the quality
of its castings, and for providing an efficient and
reliable service to customers. |
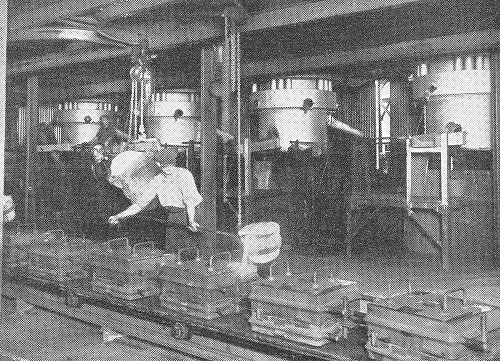
Casting in the foundry. |
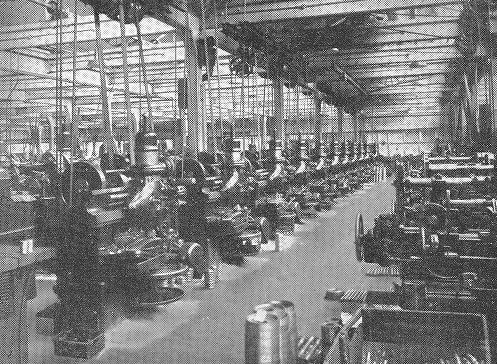
One of the gear cutting lines. |
The Engineering Division manufactured precision
engineering components and assemblies for vehicle
manufacturers, railway locomotive builders, tractor
builders, and marine industries. Products included
vehicle transmissions, axle assemblies, machined
cylinder blocks, cylinder heads, crankcases, and
gearboxes.
The up-to-date machinery and plant ensured that
work was produced to the highest standards, and to
fine tolerances.
Skilled operators were used, and their work was
closely supervised and inspected at every stage. |
There were facilities for efficient heat
treatment, and a modern tool room which produced all
the essential jigs, tools, and equipment needed for
production. The extensive experience gained in the
factory enabled the firm to produce a vast range of
components for a large number of industries. |
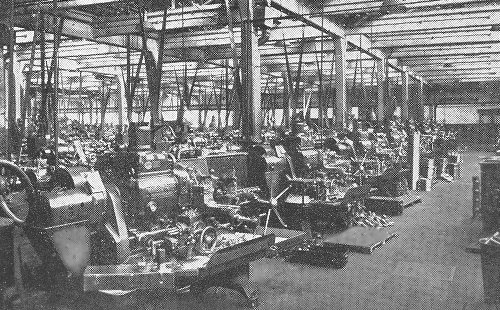
A row of capstan turret
machines. |
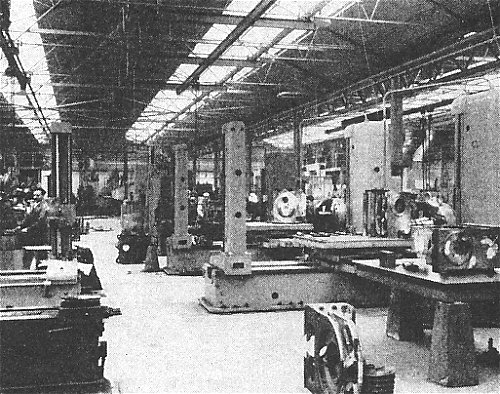
Horizontal and vertical boring
machines. |
In
1956 the company was taken over by Standard-Triumph to
produce castings for their vehicles, including cylinders
made from "Bilchrome" a special cylinder iron
developed in-house. |
The fully mechanised foundry concentrated on the
production of a wide
range of vehicle castings, including flywheels,
brake drums, manifolds, and gearboxes, ranging in weight
from a few pounds to 60 lbs. The main products,
castings for cylinder blocks, cylinder heads, and
crankcases were produced up to a weight of 1,000
lbs., and over 1,500 such castings were produced each
week.
At this time the foundry produced around 600 tons
of castings a week. |
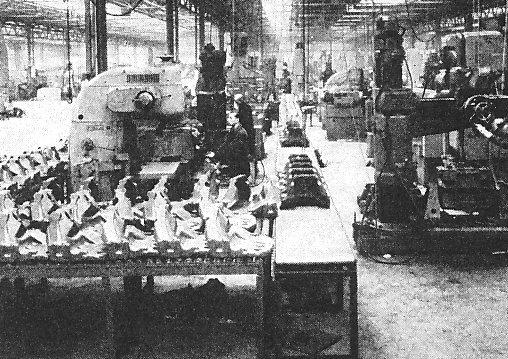
The production line for
tractor front axle supports. |
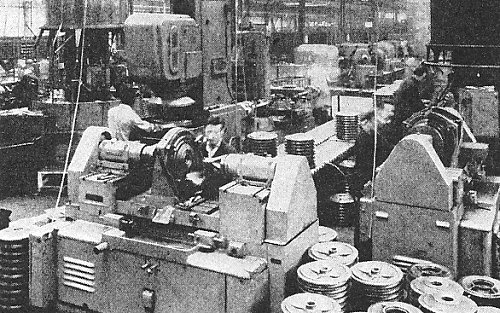
The production line for
tractor differential carrier plates. |
The castings were machined in the engineering
division where components and complete assemblies
were produced for vehicles, tractors, locomotives,
and boats. The division had 500,000 square feet of
floor space, and had the most modern machine tools
including capstan and turret lathes, Bullards and
automatics, vertical turning and boring machines,
centre lathes, and Fischer copying lathes. |
There were also Plano and duplex vertical and
horizontal milling machines, multi-drillers and
tappers, gear grinders, rotary surface grinders,
gear shapers, and hobbing machines for straight
bevel gears. Spiral bevel gears could be produced
up to twenty one inches in diameter. |
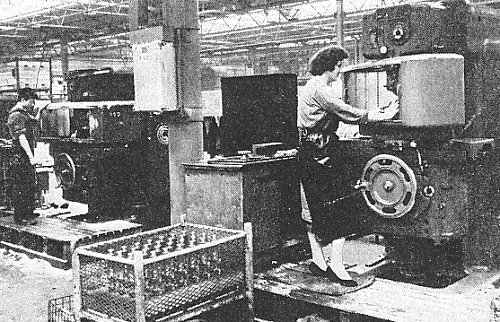
The gear shaving line. |
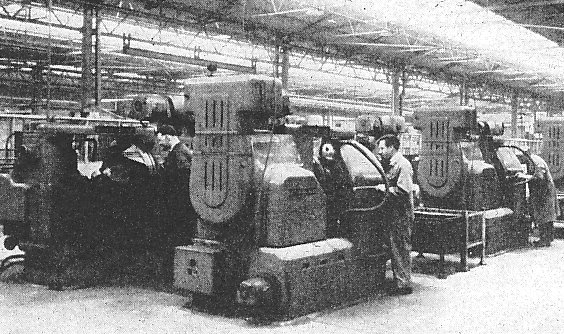
The spiral bevel gear section. |
The division's main products were machined
cylinder blocks, heads, crankcases, flywheels, fuel
pump valves, fuel accumulators, motorcycle
components, complete transmission units for
agricultural and commercial vehicles, locomotive and
marine gearboxes, textile and printing machinery,
axles, shock absorbers, test rigs, gun mounts,
turbines, heading machines, record presses, wire
drawing machines, hydraulic buffers, and
coal-cutting machinery. |
In 1960 the company became
part of British Leyland, producing castings for their
lorries and coaches. In 1975 it became known as Beans
Engineering. |
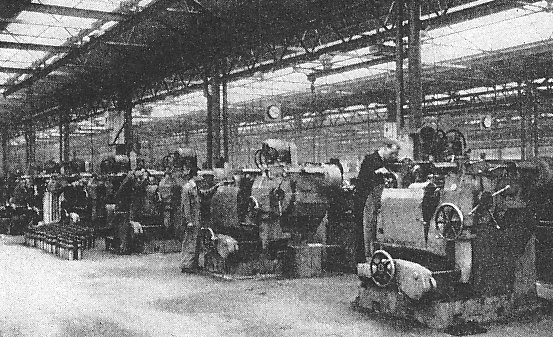
The gear cutting section. |
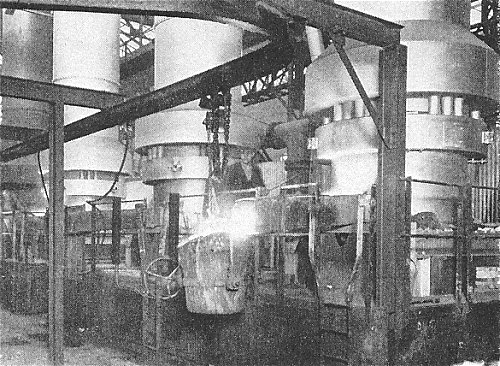
The foundry cupolas. |
In 1988 when the Leyland group
was privatised and broken-up by the Conservative
Government, Beans Engineering was acquired by its
management team, and after the buyout it acquired
Reliant. Things went on much as before until Reliant
failed in 1995 and took Beans into receivership. |
The Tipton factory was purchased by
the German engineering group Eisenwerk Bruhl who made a
large investment at the works, where 40,000 tons of
cylinder blocks could be produced each year. The
business became known as Bruhl UK but suffered from
financial problems because the large investment had left
the company in debt.
For a second time the management
team purchased the business which then became Ferrotech.
|
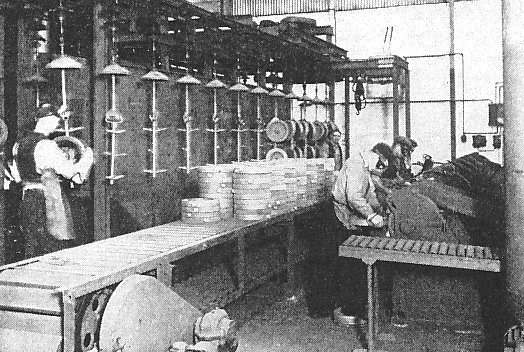
The foundry grinding section. |
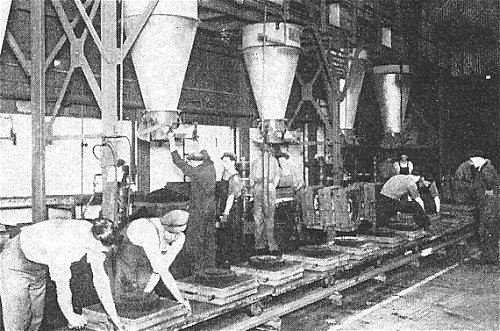
The foundry moulding section. |
The
factory had one of the most modern and efficient
foundries in Europe and became a large supplier of
castings to Rover. Unfortunately Rover went into
administration in 2005, and Ferrotech failed to find a
replacement customer.
As a result the story ends in
September 2005 when Ferrotech closed its doors for the last
time. |
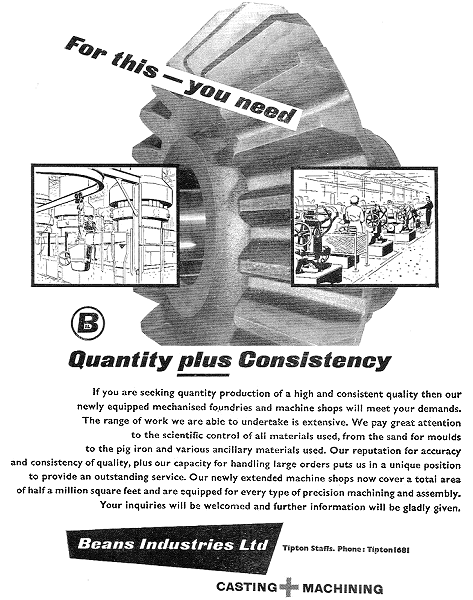
An advert from 1957.
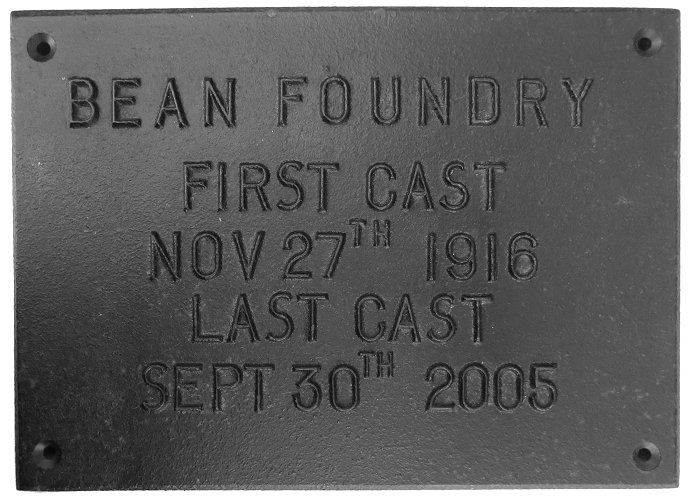
A cast-iron plate, cast to
commemorate the closing of the foundry. Courtesy of
Nigel Martin.
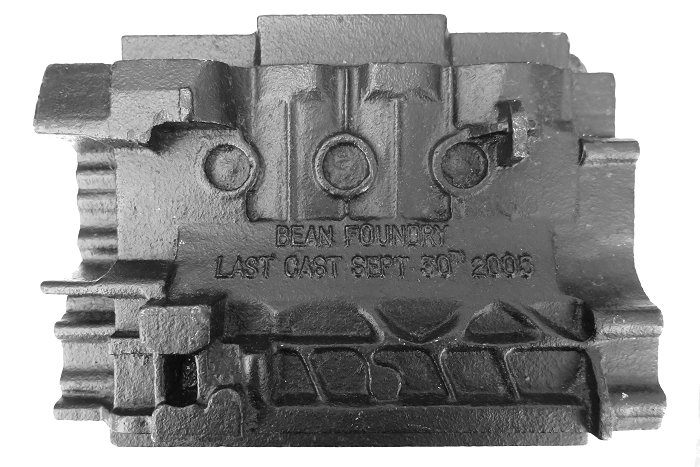
Another casting, cast to
commemorate the closing of the foundry. Courtesy of
Nigel Martin.
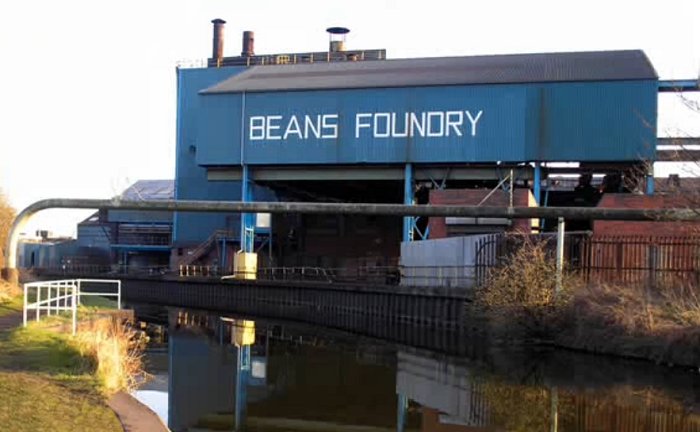
The empty foundry awaiting
demolition.
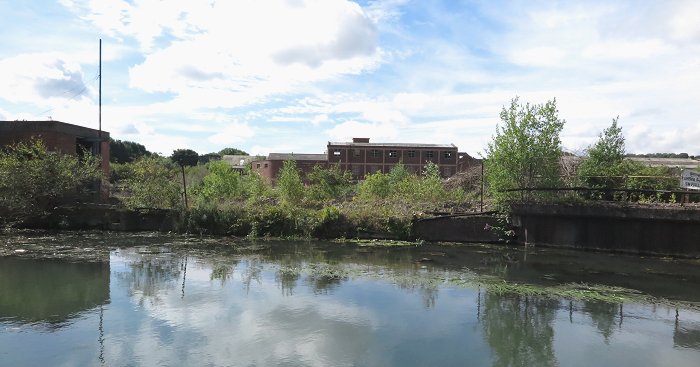
The remains of the old
factory, as seen from the canal in 2017.
|
 |
Return to
the
previous page |
|