 |
The town stands on the edge of the
South Staffordshire coalfield, next to the Wenlock
limestone and shale that forms the high ground in
Dudley. It quickly falls away and underlies the coal
measures which in places are several hundred feet deep.
The layers of coal are separated by layers of sandstone
and shale that lie on an irregular, undulating surface,
so their depth varies considerably. There was also a
layer of fire clay and some surface deposits of clay
from the last ice age, which were both used for brick
making. The coal layers varied in thickness and had
several names. There was the Brooch Coal, often about
four feet thick; the Thick Coal, up to about 30 feet
thick; the Bottom Coal and in places the Heathen Coal,
both a few feet thick, and also some ironstone.
The coal mines greatly prospered
with the opening of the canal network in the 1770s,
which allowed large amounts of coal to be easily and
cheaply transported for the first time. The building of
local railways in the 1850s also helped the local
industry, but to a lesser extent.
|
In places where the coal was close to the surface,
bell pits were dug. They were just an unsupported shaft
around 20 to 25 feet deep, which was widened at the
bottom to remove as much coal as possible. This
continued until the shaft was in danger of collapsing.
The pit was then abandoned and a new one dug nearby.
People were lowered into the shaft, and the spoil
removed by a bucket that was wound up and down the shaft
by a windlass.
The larger mines, the deep mines, often
used a horse gin to lower the miners and raise the
spoil. They were sometimes several hundred feet deep.
Some of them, particularly the deeper ones had a steam
engine to raise or lower a cage and to pump out flood
water, which was always a problem. |
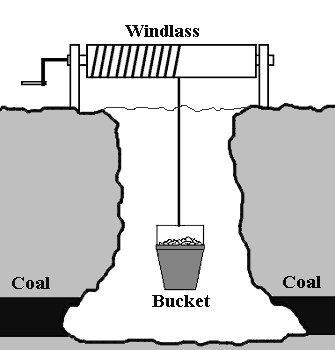
A typical bell pit. |
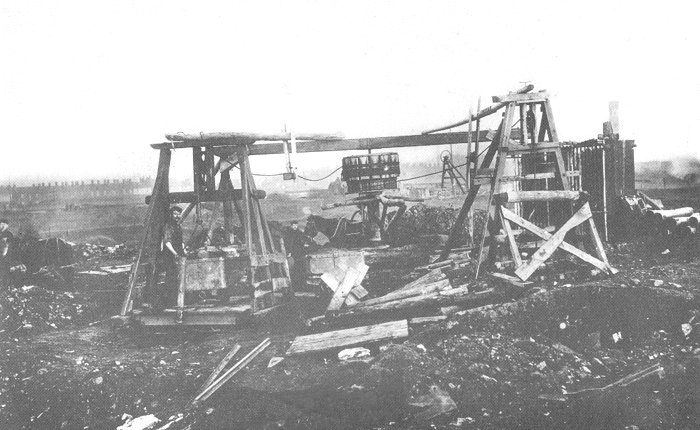
A gin pit, showing the horse and the gin. From
an old postcard.
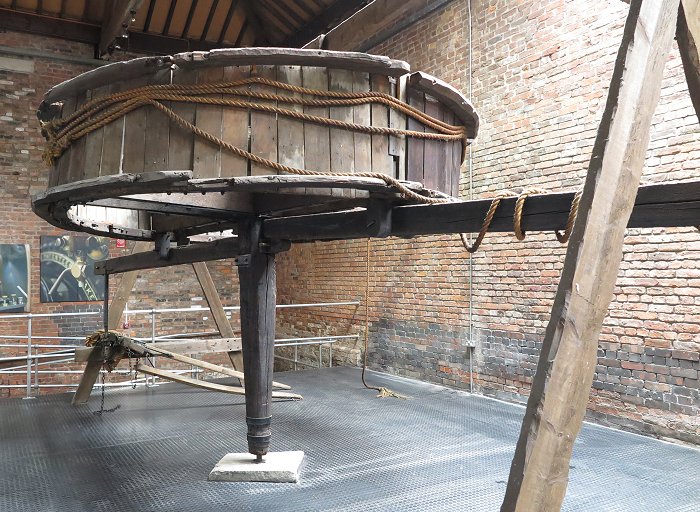
The horse gin that's on display at the Museum of
Science and Industry in Manchester.
In 1712 a Newcomen steam pumping
engine began to operate at the Coneygree coal mine and
the first commercial steam engine built by Boulton and
Watt began pumping water from Bentley and Company’s
Bloomfield Colliery in 1776.
There was a huge demand for coal to
fuel the local iron works and so large numbers of coal
mines operated in and around Tipton. Some of the blast
furnaces consumed 600 tons of coal per week. Mine spoil
heaps became a common sight. Thanks to the canals it was
a relatively cheap and easy matter to transport coal to
countless industries in the Black Country and
Birmingham. By 1835 the annual rent for coal mining land
was around £1,000 an acre.
In the 1870s things started to go
wrong. A depression in the iron trade led to a fall in
the price of coal, which in turn led to the closure of
many mines. A long strike took place in the coalfield,
during which labour was withdrawn. Pumping engines were
not operated, and many mines flooded. In 1870 it was
estimated that around 150 million tons of coal, and 20
million tons of iron ore were under water in South
Staffordshire.
Some mine owners would not use a pumping engine because
they were also draining their neighbour’s pit at their
own expense. Pumping also altered surface drainage,
because the water was run into streams, which percolated
back into the mines. |
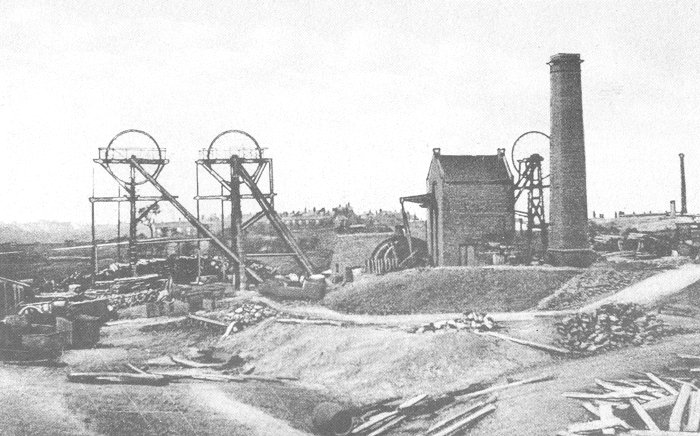
A local pit with a steam-powered hoist and
water pump. From an old postcard.
A petition to Parliament led to the
South Staffordshire Drainage Act of 1873. Under the
terms of the act, a Board of Commissioners was created
to raise money to fund pumping operations. A rate of one
penny per ton of coal, slack, and fire clay was levied
on the mine owners, but initially little progress was
made. In 1878 greater powers were granted to the
commissioners. During the next 10 years, £100,000 was
spent on pumping water out of the deeper mines. In 1886
the levy was raised to nine pence per ton of coal, slack
and iron ore, three pence per ton of fire clay, with an
addition of one penny per ton for surface drainage.
Water courses were straightened, and made watertight by puddling the beds with clay.
The Mines Drainage Commission
opened a pumping station off Moat Road, Summer Hill, on
part of the Moat Colliery site. It was powered by a
large beam engine that could pump water from a depth of
620 feet. The engine operated between 1893 and 1902 and
raised over 7.3 billion gallons of water during that
time. The operation cost over £2,500 annually, but in
spite of all the efforts, the drainage problem was never
solved. The Commission was largely ineffective. |

Working at the coal face. From an old
postcard.
Coal mines were dangerous places in
which to work. There were many accidents, some resulting
in fatalities. Underground gases such as methane
accumulated in pockets in the coal and adjacent strata.
The gases, known as firedamp, were flammable and could
easily explode. In 1849, an explosion at Moat Colliery
caused around twenty deaths (the exact number is
uncertain). There were 62 survivors. When mining
fatalities occurred, it was customary for the employer
to pay for a coffin and pay burial fees. Injured miners
usually received a coal allowance during their time off
work. Some of the local mines, including Horseley
Colliery, gave gifts of coal to the local hospitals that
looked after injured miners.
In 1890 the Mines Drainage
Commission wanted to know if it was still worth draining
mines in the South Staffordshire Coalfield and so
contacted mine owners to ask for an estimate of the
quantity of workable coal still in the ground. The
results showed that in the Tipton area alone, around 43
million tons of workable coal and ironstone were still
in the ground. By that time coal production had fallen
to half of what it was in 1874, and around £75,000 would
be required to completely drain the deep pits in the
area.
In 1896, W. Beattie Scott, H.M.
Inspector of mines for the South Staffordshire District,
compiled a list of working mines. The mines in Tipton
were as follows: |
Name |
Owner &
Address |
Manager |
Under
Manager |
Underground
Workers |
Surface
Workers |
Minerals
Worked |
Bunn’s Lane |
Joseph Marsh,
Dixon’s Green, Dudley |
|
|
6 |
2 |
household
coal |
Coneygre (part) |
Wilkinson &
Vaughan, Park Lane, Tipton |
|
|
9 |
4 |
coal and ironstone |
Coneygre (part) |
J. Kirkham,
Coneygre, Tipton |
|
|
10 |
4 |
coal and ironstone |
Coneygre (part) |
J. and S.
Baggott, Sedgley Road, Tipton |
|
|
5 |
2 |
fireclay |
Coseley Moor |
Wones Brothers,
Coseley Moor, Tipton |
A. P. Taft |
|
36 |
7 |
manufacturing coal |
Foxyards (part) |
G. G. Wilkinson
& Co., Foxyards, Dudley |
|
|
11 |
4 |
coal and fireclay |
Foxyards (part) |
G. Powell,
Foxyards, Dudley |
|
|
2 |
2 |
manufacturing coal |
Foxyards (part) |
Flavell
Brothers, Foxyards, Dudley |
|
|
3 |
2 |
manufacturing coal |
Foxyards and
Rounds Hill |
The Earl of
Dudley Priory Offices, Dudley. Gilbert
Claughton agent |
A. W. Grazebrook |
H. Rickward |
276 |
97 |
cement-stone, coal,
ironstone, fireclay |
Gospel Oak |
Gospel Oak
Colliery Co., Dudley |
C. A. Clarke |
V. A. Wilks |
191 |
36 |
coal, ironstone, pyrites |
Gospel Oak
(part) |
William
Barnbrook, Great Bridge |
|
|
6 |
4 |
household
coal |
Groveland |
Joseph Marsh &
Sons, Kate's Hill, Dudley |
|
|
9 |
3 |
manufacturing coal |
Horseley (part) |
Thomas
Fieldhouse, Horseley, Tipton |
T. Roper |
T. Fieldhouse |
12 |
4 |
coal, ironstone, pyrites |
Horseley (part) |
W. J. Hayward &
Co., Horseley, Tipton |
C. A. Clarke |
Luke Roberts |
102 |
19 |
coal, ironstone, pyrites |
Hurst Lane |
Hurst Lane
Colliery Co., Tipton |
|
|
22 |
5 |
coal and ironstone |
Jubilee |
Joseph Marsh,
Tividale, Tipton |
|
|
|
|
manufacturing coal |
Moat |
Mines Drainage
Commission, Trindle, Dudley |
E. Howl, Agent |
|
|
|
pumping
station |
Moat |
Moat Colliery
Co., Tipton Moat, Tipton |
Thomas Roper |
W. Tudor |
54 |
15 |
manufacturing coal |
Moat |
Ben Southan &
Son, Tipton Moat, Tipton |
|
|
12 |
5 |
Abandoned |
Park Lane
(part) |
George Wellings,
Park Lane, Tipton |
|
|
6 |
2 |
manufacturing coal |
Wednesbury Oak |
Phillip
Williams & Sons, Wednesbury Oak, Tipton |
A. Wilks |
E. Bowen |
284 |
59 |
coal and ironstone |
|
|
Number of workers |
1,056 |
276 |
|
|
By 1896 most of the local collieries had closed,
although a few of the larger ones remained, bringing the
total mining workforce to 1,332. By this time, most of
the easily workable coal had gone, and within 25 years
so had the local mining industry. Some mines, such as
the Toll End Colliery Company, run by William and
William T. Field, used the local clay deposits to
produce bricks. They were producing bricks before 1864.
One successful brick maker was Thomas Bayley, whose
family ran the Great Bridge Brickworks, at Golds Hill,
for at least 80 years. Bricks were still made there in
1932.

Trade Mark.
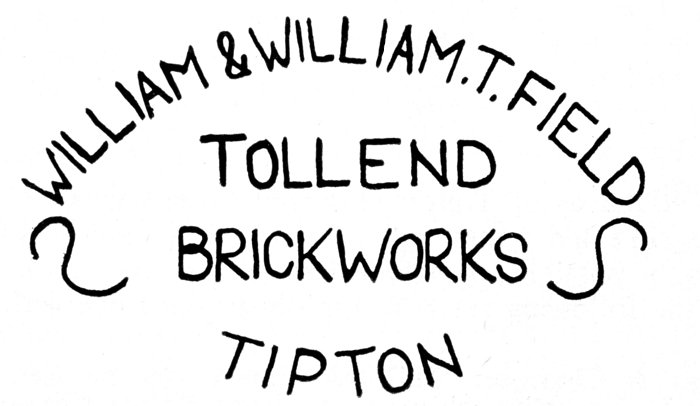
Trade Mark. |
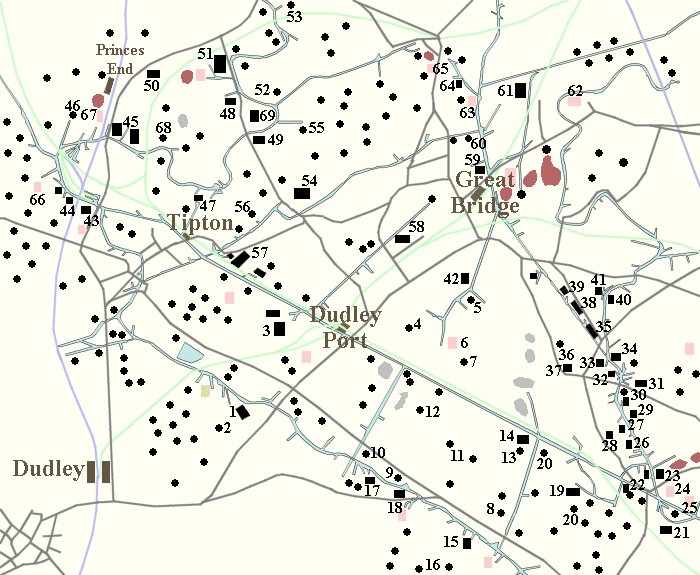
 |
1. |
|
Coneygre Furnaces |
24. |
Albion Brick &
Tile Works |
47. |
Tipton Green
Furnaces |
2. |
|
Coneygre
Colliery |
25. |
Piercy Brick
Works |
48. |
Summer Hill
Works |
3. |
|
Wellington Works |
26. |
Vulcan Foundry |
49. |
Hope Works |
4. |
|
Denbigh Hall
Colliery |
27. |
Vulcan Tube
Works |
50. |
Tibbington
Foundry |
5. |
|
Cophall Colliery |
28. |
Brush Farm
Ironworks |
51. |
Gospel Oak
Works |
6. |
|
Pumphouse Brick
Works |
29. |
Nelson Ironworks |
52. |
Moat
Colliery |
7. |
|
Pumphouse
Colliery |
30. |
Woodlane
Ironworks |
53. |
Schoolfield
Colliery |
8. |
|
Peartree Pit |
31. |
Royal Eagle Tube
Works |
54. |
Horseley
Furnaces |
9. |
|
Victoria
Colliery |
32. |
Eagle Ironworks |
55. |
Hope
Colliery |
10. |
|
Hullbridge
Colliery |
33. |
Staffordshire
Works |
56. |
Horseley
Colliery |
11. |
|
Waterloo
Colliery |
34. |
Ryders Green Tar
Works |
57. |
Gas Works |
12. |
|
Groveland
Colliery |
35. |
Atlas Ironworks |
58. |
Horseley
Ironworks |
13. |
|
New England
Colliery |
36. |
Whitehall
Colliery |
59. |
Great Bridge
Iron & Steel
Works |
14. |
|
Bradeshall
Furnaces |
37. |
Dunkirk Foundry |
60. |
Eagle
Colliery |
15. |
|
Hange Furnaces |
38. |
Dunkirk
Ironworks |
61. |
Golds Hill
Ironworks |
16. |
|
Hange Colliery |
39. |
Nelson Foundry |
62. |
Golds Green
Brick Works |
17. |
|
Tividale Sheet
Mills |
40. |
Ryders Green
Tool Works |
63. |
Crownmeadow
Colliery & Brick
Works |
18. |
|
Etna Iron Works |
41. |
Crown Bridge
Works |
64. |
Crown Iron
Works |
19. |
|
Union Furnaces |
42. |
Sheepwash
Ironworks |
65. |
Toll End
Blue Brick Works |
20. |
|
Union Colliery |
43. |
Tipton Hall
Works |
66. |
Foxyards
Fire Brick Works |
21. |
|
Izons Foundry |
44. |
Coseley Moor
Furnaces |
67. |
Bloomfield
Brickworks |
22. |
|
Gas Works |
45. |
Bloomfield
Ironworks |
68. |
Tibbington
Colliery |
23. |
|
Albion Ironworks |
46. |
Roundhill
Colliery |
69. |
Mines
Drainage Pumping
Station |
|
|
Ironworks and coal mines in the 1880s. |
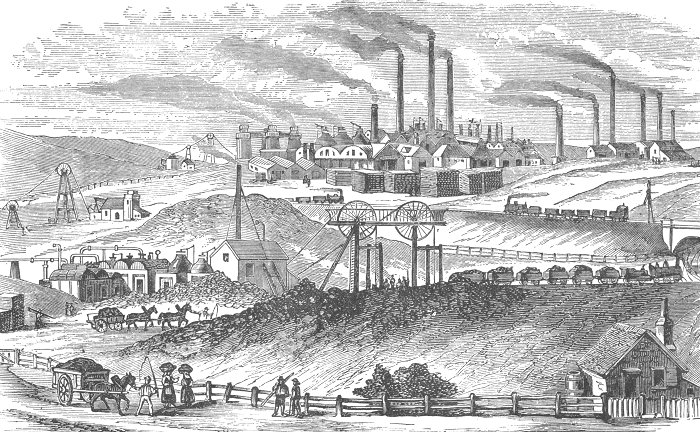
The
industrial scene in the middle
of the 19th century. A mixture
of coal mines and ironworks. |
|
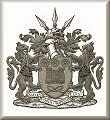 |
Return to
the
previous page |
|