 |
Ironworks
At the turn of the 19th century, Tipton and its
neighbouring Black Country towns were in an ideal
situation for the production of iron. The vast local
deposits of coal, iron ore and limestone, and cheap
efficient transport on the canal network meant that
the appearance of ironworks was almost inevitable,
especially because of the country’s growing appetite
for products made of iron.
Tipton’s iron industry began in
a relatively small way with the production of items
such as hinges, wood screws, awl blades, edge tools
and nail rods for the nail makers. At the time,
around one quarter of the local workforce were
involved in the production of nails. Whole families,
including several generations, from children to the
elderly, made nails.
Things began to change with the
development of steam engines, large machinery, iron
bridges, and the building of the railways.
|
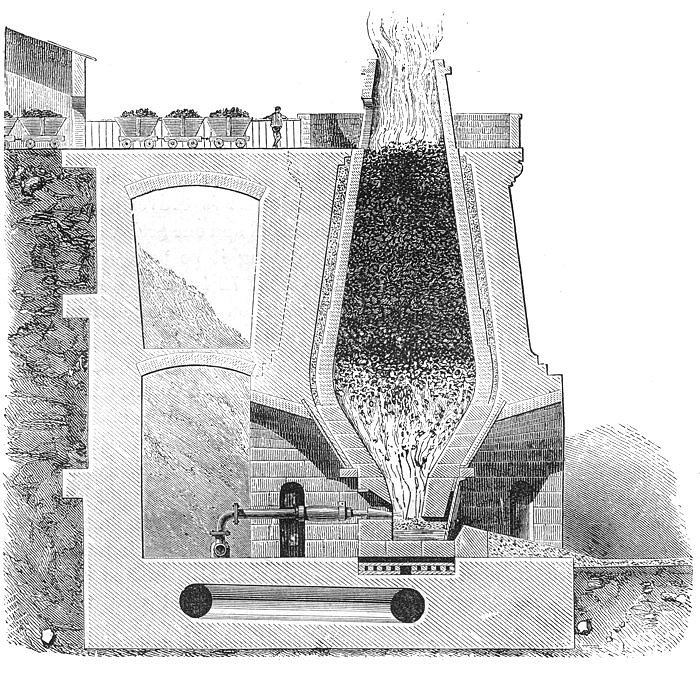
A 19th century blast furnace
which produced pig iron. |
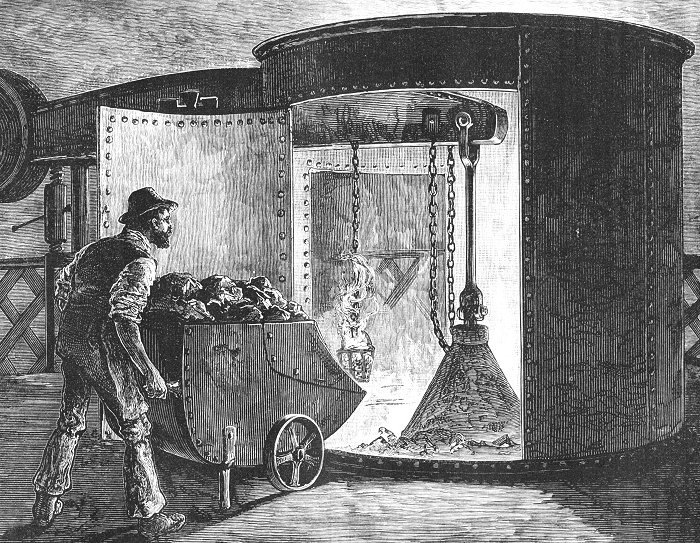
Charging a blast furnace. |
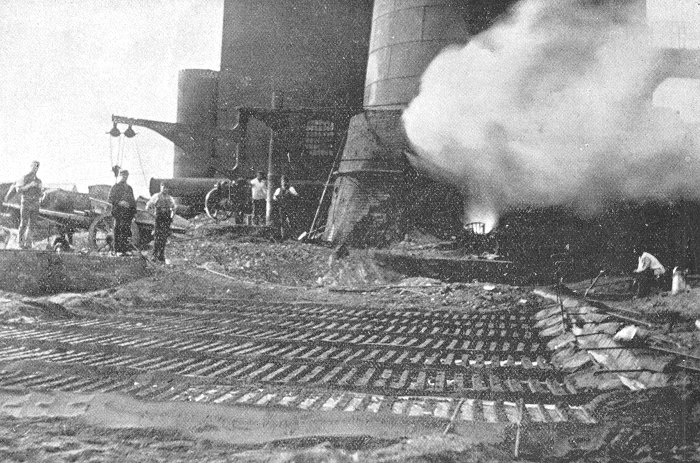
Tapping one of the
furnaces at Willingsworth Ironworks. The
molten iron was run into channels cut into
sand to produce iron ingots. This was known
as a pig bed. The iron was called pig iron
because during casting, the ingots were
likened to a piglet suckling milk from a
sow. |
The most common method of producing wrought
iron from pig iron in the 19th century was
puddling, invented by Henry Cort in 1784.
Pig iron or scrap cast iron was melted in a
puddling furnace and stirred with a long pole,
which reduced the carbon content by bringing it
into contact with air, in which it burned. The
puddling furnace heated the iron by reflecting
the exhaust gases from the fire down onto it. In
the drawing below, the iron would be placed in
the central section. Because it was not in
contact with the fire, cheaper, poor quality
fuel could be used. After puddling, the iron was
hammered and rolled to remove the slag. |
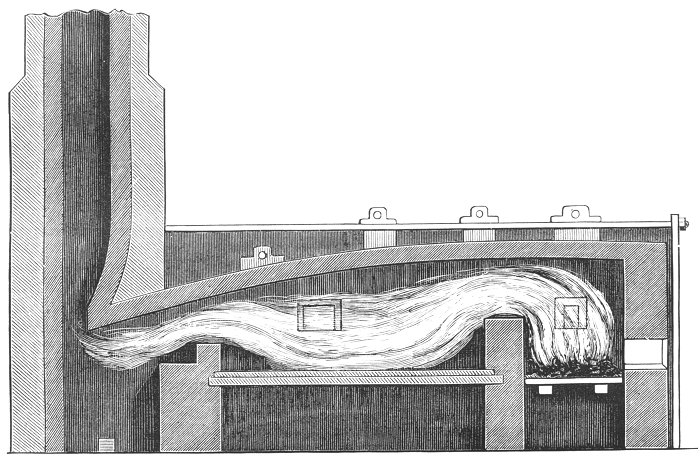
A puddling furnace. |
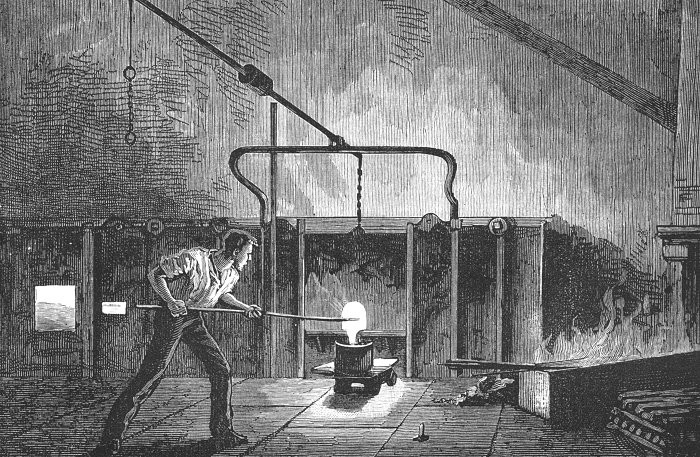
A puddler at work. |
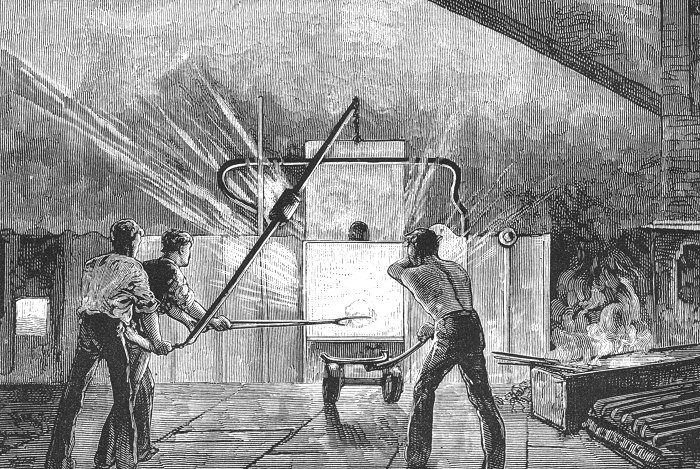
Puddlers at work. |
Some of Tipton's
Ironworks
Daniel Moore had a
water-powered slitting mill, with two undershot
water wheels and a steam engine. The firm produced a
wide range of nails and tacks, especially horse
nails, as well as shovels and tongs. Around 40
people worked there.
Edward and James Fisher and
James Bate employed around 100 people in the
manufacture of iron hinges. Zachary Parkes and
Company at Dudley Port had a single furnace that
produced between 20 to 25 tons of iron per week.
They also had a forge and a slitting mill.
George Parker & Company had
two furnaces that produced 20 or 25 tons of pig iron
per week at Coneygre Ironworks, Dudley Port,
established in 1794 by Zachariah Parkes. They had
three forge hammers and a rolling
and slitting mill. One of their products was boiler
plates. Another furnace was added and the business
was acquired by
the Earl of Dudley. The three furnaces then produced around 200 tons of iron per week.
George Parker & Company also owned Tipton Furnace,
also known as 'Parker's New Furnace'. It was later
called Coseley Moor Furnace.
Read, Banks, and Dumaresq had a
forge and a single furnace producing around 25 tons
of iron per week. Richard Hawkes and Company also
had a single furnace which produced around 20 tons
of iron per week. At Toll End was Taylor's Foundry
where heavy items such as parts for steam engines,
whimseys and machinery were cast.
The Great Bridge Iron & Steel Company Limited was
founded by James and Neal Solly, who traded as Solly
Brothers and were one of the oldest and largest
suppliers of puddled steel. There were two forges,
two merchant mills, and two sheet mills that could
produce up to 320 tons of iron and steel per week.
Another successful enterprise was the Crown Iron &
Galvanising Works at Toll End, run by Edward Bayley,
who also operated two blast furnaces at Eagle Works.
Crown Works were established in 1870 and were later
extended with the addition of two sheet mills and a
galvanising factory. There were ten puddling
furnaces and three mill furnaces, with a total
capacity of nearly 100 tons per week. The factory
employed around 200 men and produced best quality
black sheet iron and galvanised corrugated iron
sheet.
|
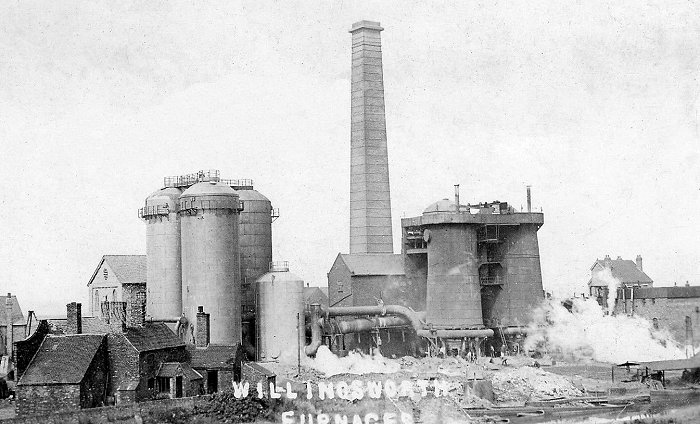
The two blast furnaces at
Willingsworth Ironworks that produced good forge
iron. From an old postcard. |
Eagle Works, founded in about 1800 by Richard
Hawkes, once stood on a site that was later occupied
by Great Bridge Railway Station, alongside Eagle
Road. Around 1844 Eagle Works were put-up for sale
and the site was acquired by the South Staffordshire
Railway, in readiness for the building of the railway
station. The
factory had two blast furnaces, a double refinery
and a
large foundry capable of producing 100 tons of
castings per week. There was a boring mill, capable of boring
cylinders ten feet in diameter,
blast and boring mill engines, a
smiths shop, a fitting shop, a carpenters shop, plus
a manager’s house and three workmen’s cottages.
There were also collieries mining Heathen Coal, New
Mine Coal, and New Mine Ironstone, with two winding
and pumping engines, and three winding engines. Other large concerns included
the Portfield Works near Dudley Port, owned by James and
Charles Holcroft, which could produce almost every size,
shape, variety and section of iron, and had a large
galvanising department. Another sizeable ironworks
was the Church Lane Works run by George Gadd &
Company. There were 14 puddling furnaces, 2 mill
furnaces, and one ball furnace, with a total
capacity of 180 tons of bar iron and 200 tons of
puddled iron per week.
The Hope Iron, Steel and
Tinplate Company Limited at Summerhill had 4 mills. Plant and Fisher at Dudley Port Works produced
250 tons of iron per week from 20 puddling furnaces
and 3 mills. The Gospel Oak Iron & Galvanised Iron &
Wire Company had 24 puddling furnaces and 6 rolling
mills, and the Dudley Port Furnace Company, run by
James Roberts and Fred Deeley had a single blast
furnace with a capacity of 250 tons of pig iron per
week.
The Gospel Oak Iron Works, which
was founded by Samuel Walker and William Yates in
1817, began making cannon in 1822, but the business
failed. The sons of the owners took over and started
to produce ironwork for all kinds of building
projects, including Hammersmith Bridge, in London,
in 1825, and the cast iron columns for the Albert
Dock, Liverpool, in 1846. Similar columns were later
produced for the Gladstone Dock, also in Liverpool. In
1848 the business was taken over by John and Edward
Walker, who employed around 350 people, producing
large amounts of wrought-iron cannon
and tinplate. The business failed for a second time
in about 1860 and cannon manufacture was taken
over by three ex-employees who founded the Hope
Company. Around 1900 the Blackwall Galvanised Iron
Company acquired the Gospel Oak Company and exported
galvanised sheets to many parts of the world using
the product names Poplar, Blackwall and Gospel Oak.
Tubes were produced in Great Bridge by Wellington
Tube Works Limited at Wellington Tube Works. The
firm, founded by Joseph Aird started making tubes in
1861. Products included mild steel and wrought iron
tubes and fittings for gas, water and steam, along
with coated
and wrapped tubes, loose flanged tubes, grilled
metal tubes and special pipe work of all kinds.
Other locally made iron
products included cast iron grates and stoves
produced at the Moat Foundry, Summerhill by Charles
Lathe & Company, established in 1877. There were
also boiler makers, hurdle and iron fencing makers,
anvil makers and manufacturers of vices and hammers.
Bloomfield Ironworks
It all began when a local Tipton man invented
a process that revolutionised puddling,
throughout the country and much of the world.
His name was Joseph Hall, who was born in 1789.
In about 1811 he noticed how his employer,
carefully saved old scraps of iron for use at
the refinery, where large quantities of iron
were lost in the wasteful process of making it
into wrought iron by refining and puddling. He
began to follow his employer’s example and saved
all the odd bits and pieces of iron that were
lying about the works. Around 1816 he noticed
that the cinder from puddlers' boshes (the water
tanks where the puddler cooled his tools)
contained a quantity of iron, and so he began to
save this also.
Some time later, he tried adding some of the
bosh cinder to a puddling furnace and found,
rather to his alarm, that a violent boiling
occurred, the contents of the furnace running
out in all directions. He feared that the
furnace would be damaged, but the boiling ceased
and when he looked in the furnace he saw that
pieces of iron were present. When he gathered
them into a ball and hammered them together, he
was surprised to find that iron was the best he
had ever seen.
He had accidentally discovered an ideal
method of working a puddling furnace. The cinder
that he used consisted of small pieces of iron,
brought out of the furnace by the tools, mixed
with a rich iron oxide. When heated, the oxygen
had united violently with the impurities in the
iron, making the contents of the furnace boil,
leaving behind, high quality wrought iron.
He formed a partnership with Thomas Lewis and
in 1830 they bought a piece of land at
Bloomfield, where they built a small ironworks
with three puddling furnaces beside the canal.
The site was later connected to the main railway
line by sidings. Hall continued his experiments
to improve the process. There was a serious
problem with the cast-iron bottom plates of his
furnaces, which were attacked by the bosh
cinder. He overcame the problem by roasting the
cinder, which became known as bull-dog and was used for the furnace bottoms.
Bull-dog was
patented in 1838.
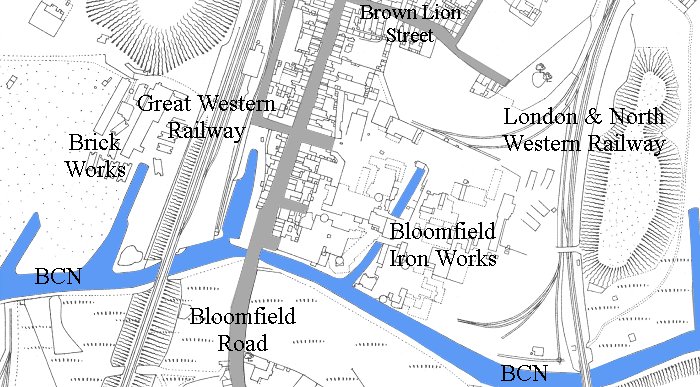
Bloomfield Ironworks in
1884.
He also discovered that a small addition of
some hammer cinder and mill scale (the iron
oxide that breaks off the surface of the iron as
it is rolled and hammered) fully protected the
furnace bottom plates. His process was now
perfect. Pig iron was charged into the furnace
in the usual way, the fettling or lining of
bull-dog and scale being repaired before
charging as required. The metal was then melted
down and in due course it began to work, as the
oxygen from the fettling united with the carbon
in the iron. The reaction was violent, and for
about half an hour the surface of the metal
boiled, with bubbles of carbon monoxide breaking
through, and burning with little blue flames or
puddlers' candles. Because of this violent
reaction, the process became known as pig
boiling or wet puddling.
Hall's patent greatly reduced the amount of
waste from puddling furnaces so that by 1900,
only 21 cwt of pig was needed to make a ton of
wrought iron. Since the furnace bottom was
formed of oxide, the supply of oxygen for the
elimination of carbon was assured. The amount of
silica was strictly limited to that in the sand
adhering to the pigs, plus the silicon in the
pigs themselves, so there was no build-up of an
acidic slag. The slag remained basic; as this
combines with phosphorus, the removal of that
unwanted element was facilitated. Furthermore,
the violent reaction of the oxides with the
carbon in the pig iron, by agitating the charge,
helped to ensure a thorough mixing and reduced
the time required to complete the process, which
also
reduced the amount of manual labour needed.
Thomas Lewis soon left the firm and Joseph
Hall was joined by two new partners, Richard
Bradley and Mr. Welch, who left in 1834 and was
replaced by William Barrows. The firm became
Bradley, Barrows and Hall. The factory was
greatly extended and the iron was sold under the
brand name B.B.H.
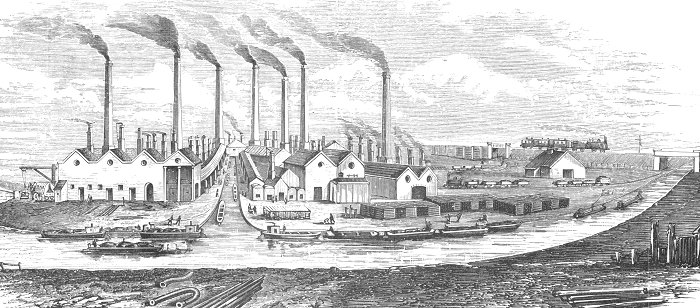
Bloomfield Ironworks in
1872.
Richard Bradley retired in 1844 and was
succeeded by Mr. Bramah, who lived at
Kingswinford. Mr. Bramah died in 1846 and the
firm became Barrows and Hall, William Barrows
and Joseph Hall being equal partners. In 1851
the firm employed 1,000 men.
In 1849 Joseph Hall moved to Bloomfield
House, in Holyhead Road, Handsworth, where a
Farmfoods shop now stands. He died there on the
18th January, 1862 at the age of 72 and was
buried in a family vault at Key Hill Cemetery,
Birmingham.
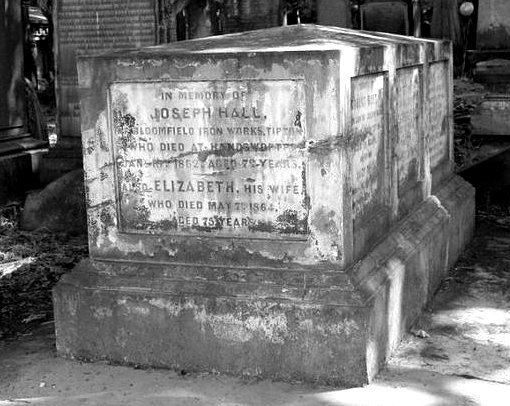
Joseph Hall's family vault
at Key Hill Cemetery, Birmingham.
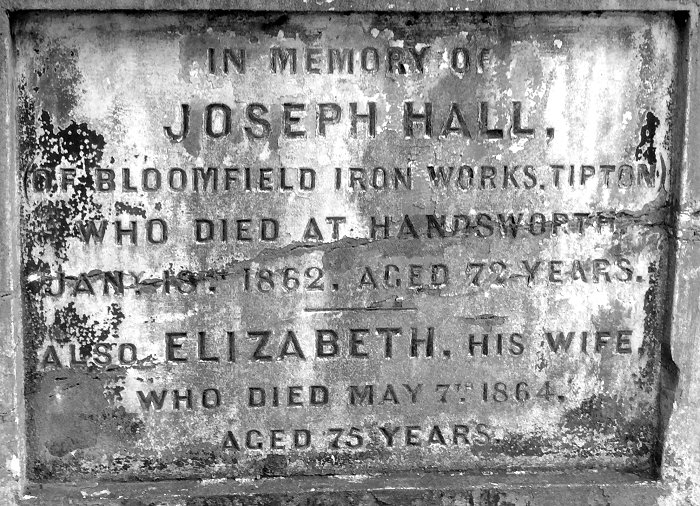
Joseph Hall's memorial stone, on the family
vault at Key Hill Cemetery, Birmingham.
|
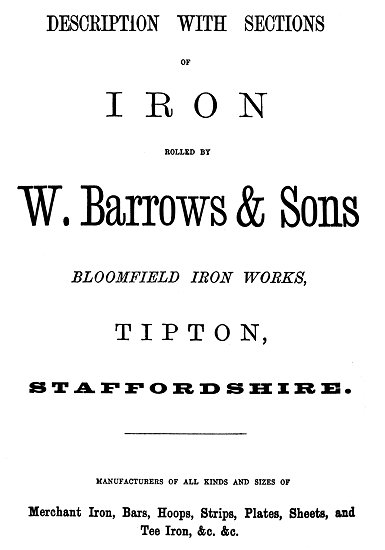
From Griffiths' Guide to
the Iron Trade of Great Britain. 1873. |
In 1848 two men were killed in a boiler
explosion at the ironworks. They were Mr.
Millington and William Perry. Several people
were injured. The boiler, weighing 7 to 8
tons was thrown about 70 yards across the
canal. After Joseph Hall's death the
company became W. Barrows & Sons. William
Barrows was born in Birmingham in 1800 or
1801. In the 1830s he lived in Hampstead
Row, Handsworth, before moving to
Springfield House, Dixon's Green, Dudley.
In 1861 he was living at Himley House,
Himley, (now a pub and restaurant) with his
wife Martha and four servants. Their sons
Thomas and Joseph were both ironmasters.
William Barrows died on 10th December,
1863 at Stafford Railway Station. In 1867
the firm had 58 puddling furnaces and eight
mills.
By 1872 there were 100 puddling furnaces
and 10mills and forges. There were around
800 employees producing approximately 800
tons of iron sheets, plates and bars per
week. Their iron was second to none. |
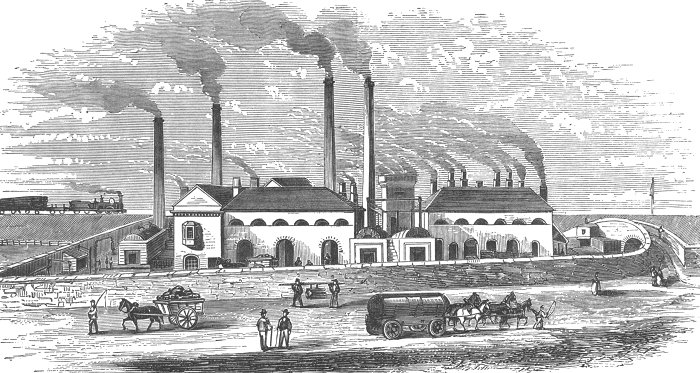
W. Barrows & Sons,
Bloomfield Ironworks.
By the late 1870s the industry was in
decline. Bloomfield Ironworks closed in 1902
and were offered for sale in local
newspapers. By that time trade was bad and
so no one offered to buy the site. Joseph
Barrows, the principal partner, died in
1903, and the works were again offered for
sale, but again no purchaser could be found.
In 1904, the site was sold privately for the
coal which was plentiful there. The factory
was demolished to clear the way for mining
operations at what became known as Bloomfield Colliery.
The final sale catalogue shows a large
site, covering just over 18 acres, but only
a small part of the site was occupied by
buildings, which had all been erected in a fairly
haphazard way. The various rolling mills lay
clustered together and were at all angles,
as were the puddling furnaces. The rolling
mills were under cover and roofs were
provided for departments that had valuable
machinery, such as lathes. Quite a
number of the puddling furnaces had no
protection from the weather at all. There
were bull-dog kilns, foundry and fitting
shops for maintenance purposes, and
extensive roll-turning equipment. Several of
the puddling furnaces still had their little
individual chimney stacks, and were not
connected to a boiler. There were several
boilers of the cylindrical egg-ended type,
which were coal-fired. It was in every way a
typical 19th century factory, which probably
couldn't have survived much longer without
being modernised.
Bloomfield Colliery was purchased by
British Rolling Mills Limited and their
subsidiary, Brymill in the 1930s. Rolling
mills and a steelworks were built on the
site. Later Corus Steelworks constructed
their Firsteel Cold Mill and Service Centre
there. Most of the site is now occupied by
houses.
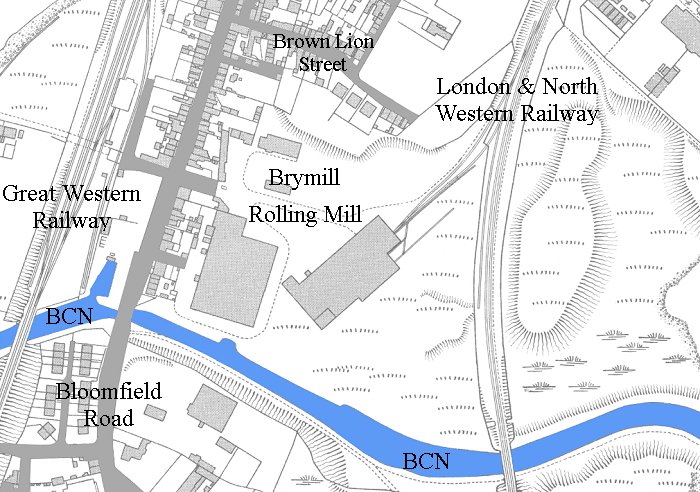
Brymill in 1938. |
Wednesbury Oak Ironworks The business was founded in
1820 by Philip Williams and Sons, who were from an
old Shropshire family who moved to the area in 1776.
Philip started in business in about 1800. After
working for several companies, became a partner in
Gibbons, Whitehouse, and Williams, who built their
first furnace at Wednesbury in 1814. His partners
soon left the business and he purchased the
foundation timbers for a forge and mill from the
Government authorities at Woolwich, in 1818.
In 1820 the forges and mills
were built at Wednesbury Oak Ironworks and
manufacture of ‘Mitre Brand’ iron began. The factory
was extended and modernised in 1847 and 1880 for the
production of cold-blast pig iron. In 1829 Philip
Williams and his family founded and ran the Union
Furnaces at West Bromwich and also acquired the
Albion Works, and the Union Works at Smethwick,
along with Birchills Collieries and Furnaces, Mabbs Bank
Colliery, and
Bunker's Hill Colliery. By 1846 they were
employing over 5,000 men.
Philip Williams died in 1864
and the business continued to be run by members of
his family. One of his nephews, Walter Williams
became honorary secretary to a scheme that
encouraged ironworkers and colliers to keep their
children at school in the days before School Boards
were formed. He also anonymously wrote about the
value of education to the labouring classes and was
Chairman and President of the Mining Association of
Great Britain, Chairman of the local Mines Drainage
Commission, and Chairman of the Birmingham, Dudley,
and District Bank. He was also a Justice of the
Peace for Staffordshire and High Sheriff of
Staffordshire in 1880 to 1881. He lived at Sugnall
Hall, Eccleshall.
Around 1875 Wednesbury Oak
Ironworks were managed by George MacPherson who
became a partner in about 1890. The other partners
at the time were Philip A. Williams, Walter
Williams, and Joseph W. Williams. There were 3 blast
furnaces, 32 puddling furnaces, 5 mills and forges,
extensive collieries, saw mills, carpenters and
pattern makers' shops, foundries, millwrights,
engine fitters’ shops, blacksmiths’ shops, and
boiler makers' sheds. Finished products included bar
iron, angle iron, strips, nail rods, sheets, etc.
Summer Hill Iron Works
Summer Hill Iron Works was
founded by Thomas Millington in about 1820.
|
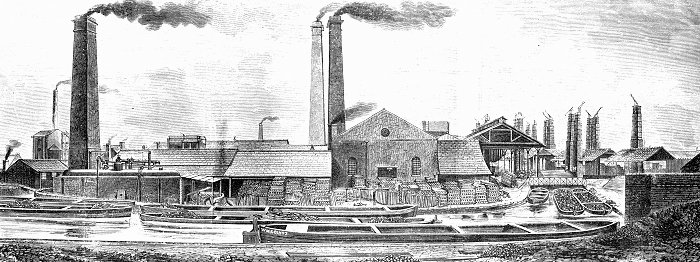
Summer Hill Iron Works. |
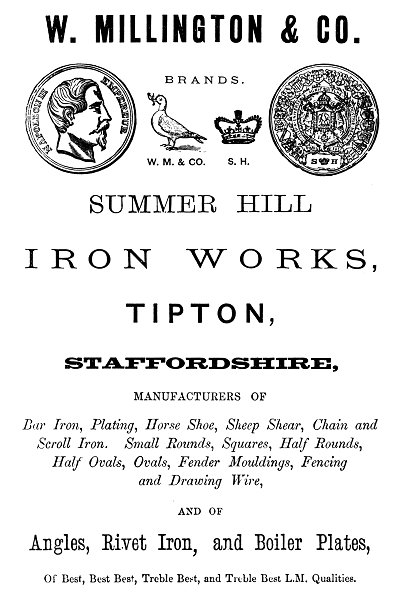
An advert from 1872. |
The firm was run by several generations of
the Middleton family, beginning as Thomas
Middleton, then Thomas Middleton & Son, followed
by T. Middleton & Sons, William and Isaiah
Millington, and finally W. Millington and
Company. By the 1870s it was run by Samuel
Millington.
There were 16 puddling
furnaces, 4 mills and forges, an annealing furnace,
a forge and up-to-date machinery.
Products included
boiler plates, merchant bar iron, plates, strips,
angle iron, shoe tip iron, horseshoe and rivet iron,
cable and chain iron of nearly every size, shape,
and variety.
The average production was around 200
tons per week and 150 men were employed at the
factory. |
Tipton Green Furnaces
The original two furnaces were
built in 1808 by Bradburn, Scott, and Foley, and in
the 1840s were let to Benjamin Gibbons, junior, of
Corbyn's Hall, who started to operate them in 1847.
He also rented the adjoining Tipton Green Colliery.
In 1848 he was joined by William Roberts who became
an equal partner in 1851. The furnaces originally
produced about 30 tons of iron per week using cold
blast, but they were enlarged and hot blast stoves
and winding engines were added to increase
production to 100 tons of iron per week.
In 1848 there were three furnaces,
which gave their name to a public house in Wood
Street. The old furnaces were demolished and
replaced by two new ones in the late 1850s and a
further two in 1860. In 1858 Benjamin Gibbons left
the firm, and in 1869 Alfred Roberts joined William
Roberts, and Mr. E. A. Spurgin joined in 1882.
Cowper stoves were added in 1889 and one of the
furnaces was rebuilt to include all of the latest
developments. The firm’s main customers were steel
works at Wednesbury, Bilston, and Round Oak. By the
1890s only two furnaces were in operation producing
200 tons per week of ‘Roberts' Tipton Green Iron’.
|
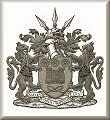 |
Return to
the
previous page |
|