The Engineer. 2nd July, 1880.
The Walsall Boiler Explosion.
On the 15th of May, a Rastrick
boiler exploded at the Birchills Ironworks, near
Walsall, in Staffordshire, and twenty five persons
were killed. A coroner's jury was of course
empanelled to inquire into the circumstances under
which these lives were lost, and a great deal of
evidence was taken. All parties were well
represented.
Mr. A. A. Fletcher, the
coroner, was assisted by Mr. F. B. Marten, C. E.,
Stourbridge. Mr. A. Young appeared for the Home
Office; Mr. W. F. Traill, engineer surveyor in
chief, and Mr. T. J. Richards, his assistant, for
the Board of Trade; M. Gillespie for the Mayor,
ex-Mayor, and authorities having with him Mr. H.
Bewlay ; Mr. Williams, with Mr. Davis, C.E.,
Wolverhampton, for the owners of the works; and Mr.
Edge, barrister, and Mr. McDougall, chief engineer
for the Boiler Insurance and Steam Power Company,
Manchester.
There were also present Mr. H.
Hiller, National Boiler Insurance Company,
Manchester ; Mr. Thompson, Manchester Steam Users
Association; Mr. Longridge and Mr. C. Longridge,
Engine and Boiler Insurance Company, Manchester; Mr.
W. Brownhill, managing director of the Birchills
Hall Company and others. Everyone likely to throw
any light on the matter has been examined. Indeed,
we cannot call to mind a boiler explosion the
circumstances of which have been more carefully
investigated.
The jury delivered their
verdict on Saturday, the 26th inst.; and we regret
to add that it is not entirely satisfactory. It ran
thus :- “That the twenty five persons came by their
deaths through the explosion of No. 4 boiler at the
Birchills Hall Ironworks, and we find that the hard
firing to which the boiler was subjected day and
night together with the weakening of several of the
plates by corrosion, and the many times it had been
repaired, brought the boiler into too weak a state
to withstand the working pressure, which we think
exceeded 30 lb. per square inch, and probably at
times rose from 40 lb. to 60 lb. to the square inch,
and somewhere about that pressure we think the
boiler exploded; the safety valve area being too
small for so large a diameter boiler.
The Birchills Hall Iron Company
were much to blame in using the boiler in the manner
they have done after the repeated cautions of the
Boiler Insurance Company; also that the boilers have
not been managed by a competent engineer; and,
seeing the want of steam and water indicators upon
the boiler and the incorrectness of those that were
in use, together with the load upon the safety valve
more than the boiler was strong enough to bear with
safety, we are of the opinion that it shows the
necessity of the Government instituting certain
regulations for the management of steam boilers in
general, and we respectfully request the gentlemen
they have deputed to watch this inquiry to lay this
request of ours before them."
We have no intention of
reproducing even a summary of the evidence on which
the preceding verdict was based; but we can give our
readers an opportunity of attaching their own value
to it. The accompanying engraving shows the boiler,
and gives a ground plan of the works; it is so
complete in itself that it needs no special
description. For certain general information
concerning Rastrick and other boilers in ironworks
we would refer our readers to The Engineer for June
4th. The question we have to consider is, why did
the boiler explode? The jury say that the boiler was
too weak to withstand the working pressure, but they
add that because the safety valve was too small a
pressure of as much as 60 lb. might have been
reached, and that at about this pressure the boiler
exploded. Concerning this latter point there is no
evidence whatever.
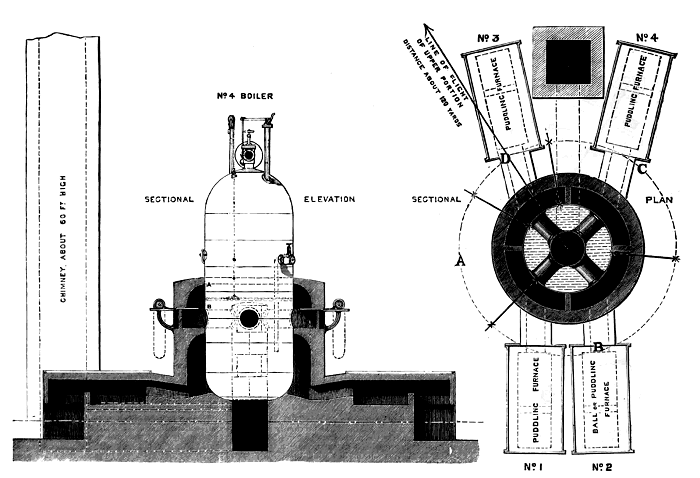
Sectional elevation and plan of No. 4 boiler,
Birchills Hall Iron Works.
The foreman of the jury, Mr.
Davis, however, in the course of the examination,
asked Mr. Niel McDougall, chief engineer to the
Boiler Insurance and Steam Power Company, if he
thought the area of the valve sufficient, and on Mr.
McDougall saying that he considered the valve large
enough, Mr. Davis replied, "I differ from you very
much." We do not think that Mr. Davis knows as much
about boilers as Mr. McDougall, for in a little
speech which he made before the verdict was given he
announced that he had recently, after making come
inquiry into the subject, "found that every time the
diameter of a boiler was doubled its strength was
halved.'' He had also found that "although spherical
ends were twice the area of flat ends, the pressure
was only equal to flat ends." It seems evident that
Mr. Davis only began to learn the first principles
of boiler making during the course of the inquiry,
so could not therefore speak with much authority;
but no doubt Mr. Davis put the paragraph about the
safety valve into the verdict. It will be remarked
that the boiler was in communication with others so
that it did not always rely on one safety valve.
This valve was 5½ in. in diameter, which ought to be
ample for a boiler with only 550 square feet of
heating surface. However, as no proof was put in
that 60 lb. pressure had ever been reached, we need
say no more on this point.
The boiler either exploded at
the working pressure, about 41 lb., or at some
pressure above or below that. At the time of the
explosion the safety valve was blowing off; not
hard, but certainly blowing. The pressure could not
therefore have exceeded save for a moment or two at
the most about 43 lb. on the square inch. Now, it is
a noteworthy fact that a short time before, this
boiler had plates in it less than one sixteenth of
an inch thick, and was worked at the time, and the
safety valve blew off steam. These defective plates
were all taken out and new plates were put in, and
the repaired and ostensibly stronger boiler burst
under a pressure readily withstood by the boiler in
its ostensibly weaker condition. Mr. McDougall
handed in a report, in which we find the following
words :-
"In seeking to arrive at a
conclusion as to the cause of the explosion, one
fact worth considering is that a boiler which in
November of last year was actually worked at a
pressure of about 33 lb. to the square inch up to
the time our inspector examined it, with plates in
the bottom only one sixteenth of an inch thick,
should now, after extensive repairs, have burst,
although the thinnest part of the thinnest plate
which can now be found in the bottom is four times
the former thickness. In connection with this, it
should be borne in mind that one sixteenth of an
inch of solid plate, of a tensile strength of 18
tons to the square inch, is sufficient to stand a
pressure of over 40 lb. to the square inch in a
boiler of this diameter."
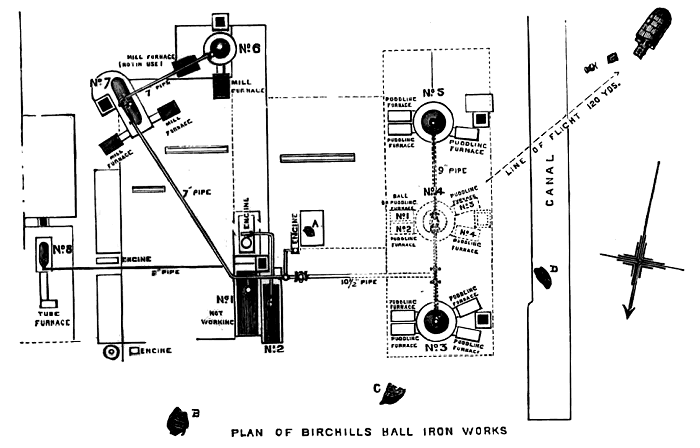
It would appear therefore that
the repairing of the boiler, or something which was
done at or about the time of repair, modified the
conditions under which it worked in such a way as to
bring about the explosion. So far as could be known
the boiler was the better, very much the better for
the repairs; but, as a matter of fact, the repaired
boiler was not so strong as the unrepaired boiler.
By reasoning in this way, and sifting facts a
little, we gradually narrow the field of inquiry.
Let us turn now to the boiler itself, as shown in
our engraving, and see what it has to say for
itself.
The boiler was 26 ft. long and
a little over 10 ft. in diameter, the internal tube
was 4 ft. in diameter and 11 ft. high, and into it
opened four cross tubes, each 2 ft. in diameter and
3 ft. long. The circumference of a boiler l0 ft. in
diameter is 377 in. From this let us deduct about
100 in. for the metal removed at the four cross tube
holes, and we have left 277 in. The thickness of the
shell plates at the time of the explosion was
probably under seven sixteenths the original
thickness; we shall not be far wrong if we call it
0.37 of an inch. There were in consequence 102.5 in.
holding the top and bottom of the boiler together.
The plates were made up in this boiler with the
fibre running lengthways of the boiler. We may from
the tests taken assume that they were equal when
cold to 18 tons on the square inch. This being so,
it would require a longitudinal strain of 1845 tons,
or 4,132,800 lb. to tear the boiler asunder.
There are 11,300 square inches
in a circle 10 ft. in diameter, and it is readily
seen that the pressure on each square inch must be
in round numbers 365 lb. to pull the boiler asunder.
But it so happened that just where the cross tubes
were inserted a rivetted seam ran round the boiler.
Under no circumstances could this ring have had more
than 56 percent of the actual strength of the
plate. Let it be borne in mind that it had been
severely caulked, that it had been exposed to
intense heat for years, and that it was not of first
rate workmanship to begin with, and we think it may
be conceded that its strength did not exceed 40 per
cent. of that of the plate. The longitudinal
bursting strength of the boiler was thus about 136
lb. on the square inch but it must not be forgotten
that there were many patches on this seam about the
orifices of the cross tubes.
If matters rested here, it
might be granted at once that the boiler was quite
strong enough, and during the earlier part of the
career of the boiler there is no reason to think
that it was deficient in longitudinal strength.
There was, however, evidence tendered, which was not
rebutted, to show that at some time recently the
position of the float which showed the water level
bad been altered, with the effect of lowering the
water level by about 2 ft. This had been probably
done to cure priming, but the effect of the change
would be to permit the over heating of a ring of
plates round the middle of the boiler, between A and
B, as shown in the engraving. The whole top of the
boiler flew away from the bottom, the parting taking
place at the circular seam of rivets to which we
have referred, and the parting was we believe due to
the overheating of which we speak. Mr. McDougall in
his evidence says:-
"With the water worked at a low
level, the effect of a few seconds of priming, with
a 10 in. stop valve open 2½ in., as appears to have
been the case in this boiler, would be to lay a band
of metal bare to the flames all round the shell,
immediately above or down to the four branch tubes.
From the attachment of these tubes to the shell at
this part, which owing to the extent the shell is
cut away at four places to provide for the branch
tubes, is the weakest part of the boiler, the plates
and angle irons are subject to excessive strains
from the unequal expansion of the tubes and the
shell.
There is ample evidence of this
action in the patches which have been required in
the plates around the branches, and the result of
excessive heating of the plates around these parts
would be to intensify the strains to
such an extent that rupture might easily take place
before the plates were hot enough to show strong
indications of heating. The reduction in strength
and ductility of iron when subjected to a
comparatively low heat is now understood, and iron
of the character used in the construction and
repairs of this boiler, as shown by the tests to
which the samples have been subjected, would no
doubt be peculiarly susceptible to this action."
A careful examination of all
the circumstances leads us to very nearly coincide
with Mr. McDougall's explanation of the explosion,
which is that the fatal rent began around the branch
tube fronting the furnace marked No.2 on the plan;
and that it ran round the horizontal seam, the
fragment B being blown out bodily; the other pieces
being blown right and left from the joint between A
and D, which probably parted as the boiler left its
seat.
The statements made by the
witnesses concerning the thickness of the scale on
the floor, its tendency to prime; the indifferent
quality of the plates; and the frequent repairs, all
tend to the same end. They show that all the proper
conditions of safety were violated. Had all the
instructions of Mr. McDougall and his men been
carefully and rigorously carried out, the boiler
could probably have been worked in safety for twelve
months, the time for which it was insured; but the
margin of safety was so small that no room was left
for departures from the instructions of the boiler
company. This was the weak point in the company's
action. It would, however, hardly have been
justified in refusing the boiler. Indeed, it is one
of the most useful functions of such companies to
take under their charge boilers which are not in
first class condition. The line of risk must be
sometimes approached, and in this case it seems to
have been overstepped. |