In 1776 Joseph Carver went into business as a saddle,
collar, and whip thong manufacturer, based in Upper Rushall
Street. It is believed that he purchased his premises, which
had previously been a warehouse, from John Cotterill senior
and John Cotterill junior after they became bankrupt. The
yard adjoining the building became known as Carver's Yard. By 1789 the business was being run by John Carver,
Joseph's son, who was twenty four years old. At the time he
had just four employees, but the business slowly grew. John
had a short life, which ended in 1813. After his death, his
eldest son Joseph took charge of the business, which
continued to expand, and began to specialise in whip thongs.
|
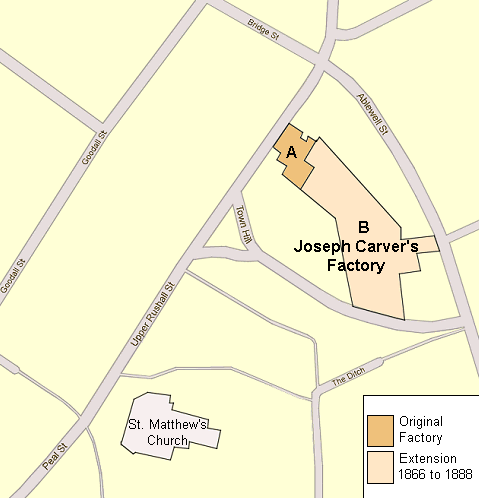 |
A second premises was acquired at Town End Bank, between
Wolverhampton Street and the canal, in an area known as
Wharf Yard. Possibly because of the nearness to the canal,
Joseph began to sell coal which was easily transported to
the site from the many pits that were alongside the canal.
In William White's 1851 History, Gazetteer, and Directory of
Staffordshire, Joseph Carver is listed as a coal merchant,
and whip thong maker.
After Joseph's death in 1866 the business came under the
control of his eldest son, also called Joseph. He ended the
coal business and vacated the Town End Bank site. He also
acquired a premises at 84 Ablewell Street which adjoined the
back of the original building in Upper Rushall Street to
greatly extend the factory. |
Around this time a range of custom-made whips was
produced for the very well to do. An engraver from
Birmingham was employed to add monograms, mottoes, crests of
arms and such like to the intricate silver-plated caps and
ferrules. Other products included watch guards, walking
sticks, hearth rugs, bedside mats, and a variety of brass
collars for waggon whips. The firm had an important export
market which included Kangaroo Thongs for Australian
customers. Thanks to its high quality exports, the firm
received several awards including a gold medal in Chicago in
1883, another in New Orleans in 1885, gold and bronze medals
in the International Exhibition in Jamaica in 1891, and a
bronze medal at the World Columbian Exposition in Chicago in
1893 which
celebrated the four hundredth anniversary of the voyages to
the Americas by Christopher Columbus between 1492 and 1503.
In the early 1880s Joseph Carver invented the steel whip,
made of fine tempered steel instead of traditional
whalebone. The new whips were being sold by 1884. |
Another
innovation was the Carver unbreakable stick gig whip, made
from a special wood which could be bent into the shape of a
rainbow, and finished to resemble holly, hew, or thorn etc.
By the late 1880s the firm also produced the usually more
expensive American style glued whips at the same price as
the cheaper English counterparts. In 1886 the firm launched
a range of braided goods including worsted cords, blind
cords, and sash cords. In the 1887 catalogue, Joseph Carver describes his
entirely new process for manufacturing whips, as follows:
The old system, the one used by all other whip makers, is
to put the pieces of cane and bone together with wax, which
upon a hot day naturally becomes soft, and in frosty weather
brittle; paper is also put on the stock in the hand part to
make the whip tapered.
By my new process the canes are all
spiced to each other and to the bone by a waterproof cement,
which will not give in any weather; there is no paper
stuffing in the handle, and the whip, before braiding is in
one solid piece. This process enables me to make a much
lighter whip, with more elasticity and durability, of better
appearance, and not affected by heat, cold, or wet.
|
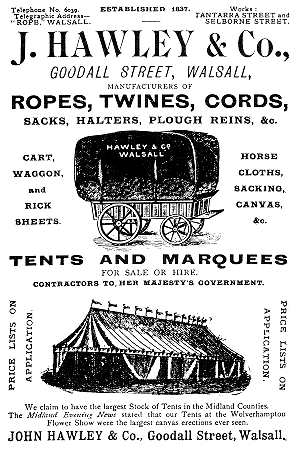 |
New Premises In the late 1880s work began on a new purpose-built
factory on the western side of Eldon Street, which became
known as the Steam Whip Works, the only one of its kind in
the country. The buildings, which still survive, are now
called Eldon Court. After the new factory came into
operation in 1889, production greatly increased and first
class bridle cutters who had worked for the best
manufacturers in London, Birmingham, and Walsall were
employed.
|
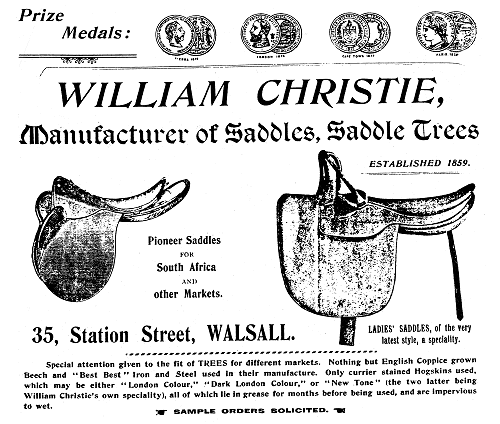 |
In August 1892 Carvers had a set-back when a fire broke
out in the new factory. It was spotted at lunchtime, and the
fire brigade soon arrived. Unfortunately the water pressure
was too low for the water from the hoses to reach the top
two floors, which were badly damaged.
The fire caused nearly
five thousand pounds worth of damage, a great deal of money
in those days. Luckily most of the plant was saved, along
with a large stock of holly bush shafts which were used as
handles for the whips. |
In 1893 Joseph Carver and a number of employees went to
the Great Chicago Exposition to display over 700 types of
whips to potential customers. In February of that year,
before leaving for America, customers were invited to a
private viewing of the exhibits in the Eldon Street factory.
When Joseph returned to Walsall in December, he was presented
with an attractive brass-bound writing companion case by his
employees, to thank him for his efforts in promoting the
firm's products in Chicago. Three years later, Carver's whips were being produced for
the Cape and Transvaal markets in South Africa, just before
the outbreak of the Boer War. In 1903 the company was
offering special cheap lines of bridles, head collars,
saddle bags, and money belts to the South African dealers.
The early years of the twentieth century must have been a
worrying time for the firm because of the introduction of
motorised vehicles. Horses were rapidly being replaced by
more modern forms of transport. Carver's salesmen travelled
far and wide to find orders for their many products, but the
writing was on the wall, as it was for all of the
manufacturers of saddles, harnesses and bridles.
Joseph's second son, John David Carver joined the
business in 1895 at the age of 17. After a short spell in
the factory he went to Spain to learn Spanish in order to
fully exploit the export market in South America. He spent
eighteen months in Madrid, living with a family of
engineers, and became interested in engineering. On his
return home he told his father that whip-making was a dying
trade and so he intended to become an engineer. Although his
father was greatly dismayed, it would eventually lead the
family business into new areas, and allow it survive after
the inevitable decline in the demand for whips.
David became an apprentice at Siemens in
Stafford, and towards the end of his apprenticeship in 1902
he built a car, one of the first to be seen on the streets
of Walsall. He greatly wanted his father to acknowledge him
as a skilled engineer and to realise that he had no
intention of returning to the old business. David rented a
small workshop from his father, in the Eldon Street factory,
and began to trade as J. D. Carver. He built machines for
many Walsall companies, including some for his father, to
automate the production of whips. In 1910 he built a boat
called 'The Endeavour' which was powered by the engine from
his 1902 car.
|
Joseph refused to believe that the whip trade was dying
and informed customers that he could now make whips better,
and cheaper due to the installation of up-to-date machinery.
The First World War gave a short reprieve to the industry
because large numbers of horses were used by the army, and
orders flooded-in.
David also greatly benefitted from war work. He produced
shell fuse carriers and devised many new production
techniques that were adopted by other makers of munitions.
His workshop greatly increased in size as orders grew, and
he employed over one hundred people, working in three
shifts.
|
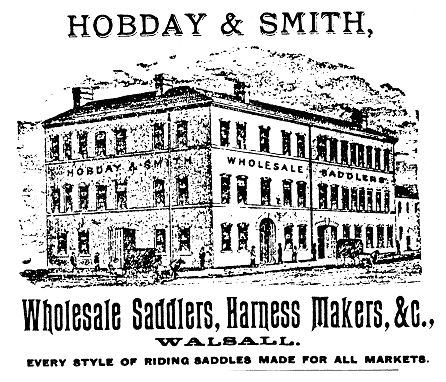 |
At the end of hostilities all munitions contracts were
immediately cancelled, and David was left with over two
hundred tons of partly finished, and completed components,
with no compensation. After the war David's workforce dwindled to two or three
people, and he concentrated on making special purpose
machines and mechanisms for local companies. He also took
out a series of patents for everyday domestic articles
ranging from a pair of coal tongs to a self-locking
gramophone lid.
Joseph's business was in a serious position. Motorised
vehicles were superseding all forms of horse-powered
transport, and in order to survive, the firm had to develop a
new range of products. Joseph felt that he was too old for
this task, and so in 1920 at the age of 75 he retired, and
appointed Mr. C. A. Williams as Production Manager. In 1922
new products included a range of rim locks under the
'Supreme' name, brass box locks, cupboard locks, hasps,
staples, and shelf brackets. Two years later the firm
launched the 'Torpedo' brand of golf clubs which were sold
to wholesalers.
In 1924 Joseph's son-in-law Mr. Charles Brazier became
Managing Director. He introduced a range of walking sticks,
and drains and chimney cleaning apparatus, which were widely
exported.
World War 2
The Second World War revitalised the almost dead whip
trade. It was like old times again. For a short while large
Ministry orders for horse whips to the 1914 pattern
flooded-in, and production returned to its previously high
level.
David's company again became involved in the armament
industry after receiving an order for the same shell noses
that had been produced in World War One. Sadly David was
taken ill in February 1940. His son Joseph, who was only sixteen years old,
took the business over during his father's absence. Sadly David
never recovered and died in June 1942. Joseph had been
studying engineering at the time, but his college had closed
due to a lack of fuel.
Charles Brazier also died in 1942. He was replaced by his
brother-in-law, Frederick Charles Hall.
Reorganisation and Changes
In 1944 the engineering section was registered as Carver
& Company, and in 1948 Joseph's eldest brother Leonard John
Carver, known as John, joined the company as Technical
Manager. History repeated itself in 1950 when Joseph and
John decided to build their own car, a four-seater Tourer,
known as 'The Bomb'. For many years it was used in hill
climbs and trials events.
|
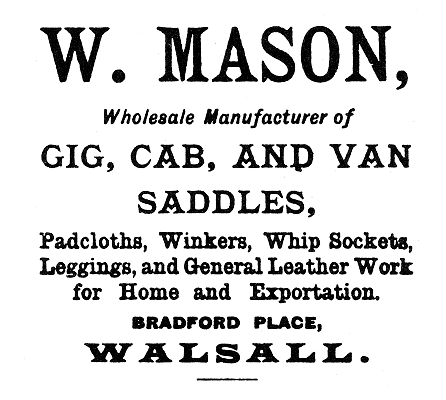 |
Although whip making continued in a small way, it came to
an end in 1958 after the death, in close succession, of three
of the company's oldest employees, William Musgrove, Frank
Owen, and William Smith. Their combined service amounted to
over 150 years. In the 1950s the main products were cleaning rods for
drains, and chimney sweep brushes, along with a wide variety
of machines and mechanical devices including mechanised golf
tees, moulding machines, shell moulding machines, and
precision flame cutters, with a cut of up to eight inches.
|
In 1952 the company name was changed to Carver & Company
(Engineers) Limited, and five years later John and Joseph
became joint managing directors. In the same year John
designed a 'C' clamp for use in welding, initially for the
company's workshops, but its sales potential soon became
apparent, and large numbers were produced. Customers
included Rolls Royce at Derby, and many engineer's
merchants. Within a short time a whole range of clamps was
introduced including the 'Buttress Clamp' for use on shallow
work pieces, the 'Snap Clamp' for the DIY market, and the 'Flexitool'
range of clamps for various craft industries. The clamps
sold well at home and abroad. By 1964 the demand in the
U.S.A. alone led to the formation of a distribution and
service company in Florida.
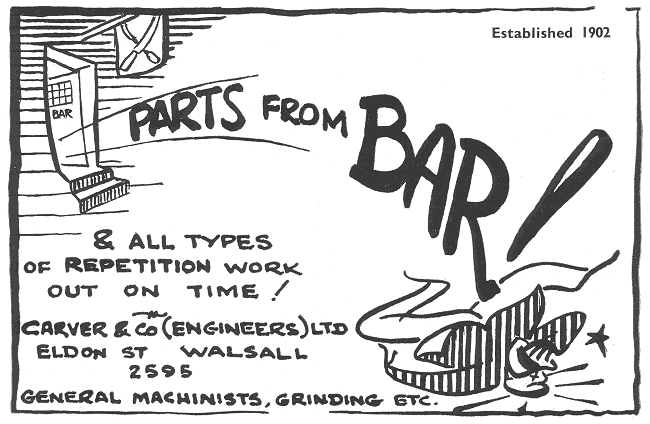
An advert from 1954.
In the mid 1950s the company's range of capstan,
combination turret, automatic, and copying lathes, and also
their vertical and horizontal milling machines were used for
repetition work such as light aircraft components,
In 1958 the company acquired the Guy Electrical Company,
formerly based in Broughton Street, Birmingham. They
manufactured flexible shaft grinding and polishing machines,
rotary burrs, and small tools. The manufacture of these
machines continued for several years under the Carver name,
and the Guy Electrical Division became a distributor of
portable industrial tools made by Bosch and Duplex.
Another important development took place in 1962 when
John Hawley & Company of Walsall asked Carvers to build a
tube bending machine for the manufacture of garden
furniture. This led to the development of a whole range of
bending machines for tubes and flat strip steel, featuring
hydraulic and numerical control. Carvers also produced a
range of light alloy drain plugs in standard sizes up to 36
inches.
New Premises
In order to increase production, more factory space
was needed. The Eldon Street site was fully occupied and no
suitable land could be found in the immediate area. The
decision was taken to purchase a two and a half acre site,
at Coppice Side Industrial Estate, in Brownhills. A new
factory and offices were built at a cost of £75,000. The
move to Brownhills took place over two days in November
1967, and went so smoothly that it had little impact on
production. The extra space was soon fully utilised, and the
workforce, and production increased accordingly.
In 1971 the bending machine part of the business was sold
because it had become too vulnerable,
depending upon the whims of the largest customers in the
motor trade. It was replaced by the manufacture of caravan
and boat heating appliances, manufactured under licence from
Phillip Kreis of Munich. A year later John Carver became
Chairman and Joseph Carver became sole Managing Director.
The number of heater products continued to grow, and
within a few years there were seven liquid gas heaters in
Carver's 'Trumatic' range. Carvers eventually
sold the product range to Truma. Some years ago the business moved to its present
location at Stoke Prior, Bromsgrove where clamps are still
made.
Much of the information came from "200 Years of Carvers
Walsall", published by the company in 1976.
|
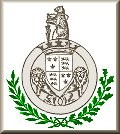 |
Return to
the
previous page |
|