Beginnings
The family business was founded in 1910
by Thomas Partridge and two of his sons, Arthur and Joseph.
Thomas, who was born in Brierley Hill in 1858, had moved to
Darlaston by the turn of the century, working as a foreman
carpenter in an engineering factory, with a wife, four sons,
and a daughter. He became a Methodist preacher, and often
walked many miles each Sunday to preach at various churches.
He held strict religious opinions, had a well-developed
sense of humour, but had little patience with slow workers,
and contempt for sickness of any kind. |
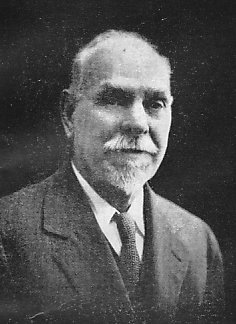
Thomas Partridge. |
By 1910 Arthur and Joseph had finished their
apprenticeships as carpenters and joiners, and were working
in Darlaston, constructing wooden buildings under their
father, who was the foreman. They often talked about, and
planned to start their own business.
The opportunity came through a new member of the family.
In 1910 Thomas’s widowed sister Maria Kelly married Richard
Delves Evanson, a carpenter and property repairer who had a
small business in Walsall. He got on well with Thomas,
Arthur and Joseph, and so it seemed to be a good idea to
form a partnership.
This led to the formation of Evanson, Partridge & Company
which came into existence on 7th March, 1910 with a capital
of £200. Unfortunately the venture was not a success. A few
months later Richard Evanson retired, and the partnership
was dissolved on 31st July, 1910. On that day the
partnership of Thomas, Arthur, and Joseph Partridge was
born. |
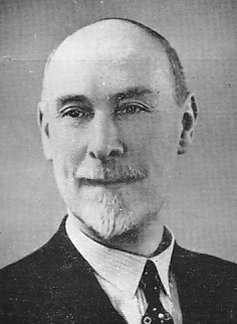
Arthur Partridge. |
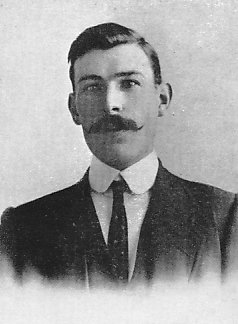
Joseph A. Partridge. |
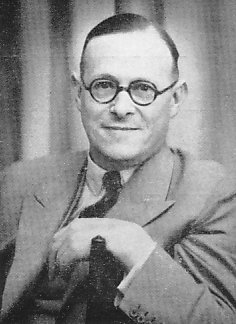
Bert Partridge. |
The New
Business
They purchased a small factory on the
corner of Darlaston Road and Pleck Road, Walsall, and set up
a joinery works. To begin with there were two or three
woodworking machines, powered by a gas engine. They employed
a young boy, A. Clement Kelly (known as Clement), who was
Thomas Partridge’s nephew, the son of his sister Maria, and
stepson of Richard Evanson. He would eventually become a
director of the company.
The business grew so rapidly that soon
a larger factory with more machinery became a necessity. In
1912 the firm purchased a piece of land in nearby Wallows
Lane, off Bescot Road, where a new factory was built. The
company built a wide range of timber-framed buildings
including bungalows, churches, boat houses, hospital
buildings, garages, and sports pavilions. The firm
specialised in the making of wide-span Belfast roofs for
industrial purposes including factories, aeroplane hangars,
warehouses, and dock sheds. All of the joinery was produced
in the factory by a team of experienced craftsmen. |
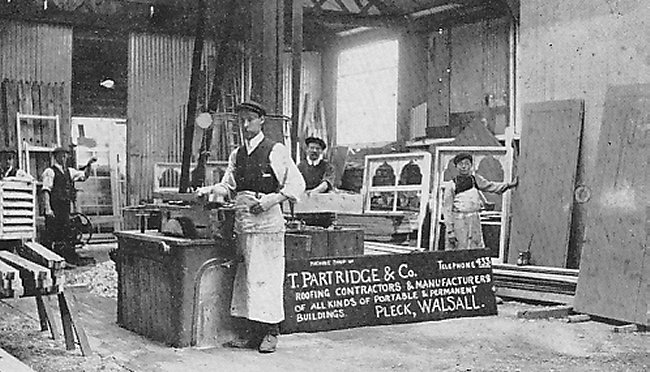
The woodworking machine shop in the
original factory on the corner of Darlaston Road and Pleck
Road. |
Around this time the firm developed,
and patented a putty-less roof glazing bar which was sold as
‘Elite’ leaded roof glazing. It became widely used in
factories, warehouses, and aerodromes throughout the
country.
By the First World War the industry was
changing fast. More buildings were built with a steel frame,
and it became obvious that the firm had to move in that
direction. With this mind, Bert Partridge, Joseph and
Arthur’s younger brother, trained as a steel structural
engineer, and joined the firm in 1914 at the age of 21.
During the war the firm received many
government contracts for the making and fixing of ‘Elite’
roof glazing. Many millions of feet of glazing were fitted
to buildings of all kinds, which proved to be difficult
because of the shortage of skilled labour.
In 1917 Thomas, who had reached the age
of 59, decided to retire, and leave the business in the
capable hands of his three sons. |
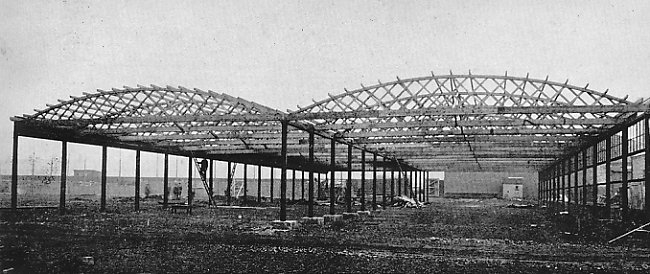
A Partridge two-bay Belfast roof. |
Inter-War Years
In January 1919 the company opened a
new office at Chamber of Commerce Buildings in New Street,
Birmingham, with S. H. Barrett, a 23 year old structural
engineer, in charge. In April of that year, Norman
Partridge, Thomas’s youngest son, joined the firm. He had
been trained as an accountant and so took over the
commercial side of the business.
The firm continued to be successful,
and became a private limited company on 27th January, 1920
with Arthur, Joseph, and Bert Partridge as directors. The
three brothers also started a new venture. They founded the
Walsall Wholesale Cabinet Company Limited, to manufacture
furniture. The new venture was so successful that Joseph
needed to devote all of his time to look after it. He
resigned from T. Partridge & Company Limited, leaving it in
the hands of Arthur and Bert.
In the early 1920s the demand for
steel-framed buildings rapidly grew. Up until this time the
company had been using steelwork that had been supplied by
outside contractors. For some time the directors had
considered the possibility of extending the company’s
operations to include the manufacture of structural
steelwork. The opportunity came in 1923 with the closure of
the Pleck Foundry Company Limited in Darlaston Road, and the
selling-off of the factory.
Arthur and Bert acquired the old
factory, and T. Partridge & Company Limited moved to the new
site. The much larger premises allowed the business to
expand, and with the installation of new plant, produce
structural steelwork. By 1927 a new company office had
opened at 8 Newall Street, Birmingham, and the business
continued to grow, receiving orders from many large and well
known British companies including the Austin Motor Company
Limited and I.C.I. |
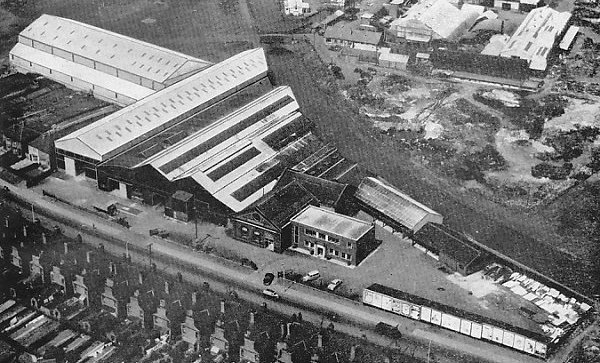
The new factory in about 1960. |
In 1927 the firm got its largest order
to date, a warehouse building for Austin, which covered two
and a half acres. The contract was completed in record time,
less than seven weeks after receiving the order. All of the
structural steelwork had been fabricated in the new
Darlaston Road factory.
In 1930 another generation of the
family entered the business in the form of Raymond
Partridge, Arthur’s seventeen year old son, who started his
career in the drawing office at Birmingham. He then spent
some time in the Template Shop at Walsall, and later moved
to the Walsall drawing office where he gaining experience in
detailing. After his training he returned to the Birmingham
Office where he worked on detailing and estimating. In 1938
he became a company director.
By 1934 the firm had outgrown its
Birmingham office and so new and more spacious premises were
found in the newly completed Lombard House in Great Charles
Street.
There were several important changes in
1935. Arthur’s doctor advised him to retire on medical
grounds, which he reluctantly did. This resulted in a
reorganisation in which Bert Partridge became both Chairman,
and Managing Director. Two new directors were appointed,
Norman Partridge and S. H. Barratt. Around the same time
Clement Kelly became Site Manager.
In 1936 a new profit-sharing scheme was
launched, which was far ahead of its time. Initially it
applied to technical and commercial staff only, but would
soon be extended to manual workers, so that all members of
staff could benefit from the firm’s success.
In the late 1930s with war being almost
inevitable, the company worked on a large number of
contracts for the new factories that would be needed as part
of the war effort. While this work was in progress, steel
framework was deigned and built for four new Danilo cinemas,
at Cannock, Quinton, Stoke, and Stourbridge. |
The
Second World War
At the beginning of the war the threat
of aerial bombardment was paramount in many people’s minds.
Many local authorities were concerned about the effects of
the blast from high explosives on their air raid shelters.
This resulted in the introduction of a scheme to strengthen
existing underground shelters with structural steelwork.
Orders for suitable steelwork arrived
from municipal authorities in thirteen counties, which
involved the production and installation of over 1,300 tons
of structural steel.
Another form of air raid shelter was
introduced, called the Morrison Shelter, named after Herbert
Morrison the Home Secretary. It was a heavy steel box with
an opening side made of strong wire. Two or three people
could crawl inside for protection. It would stand in the
living room and double-up as a table. During the early years
of the war the company built over 2,000 of them. |
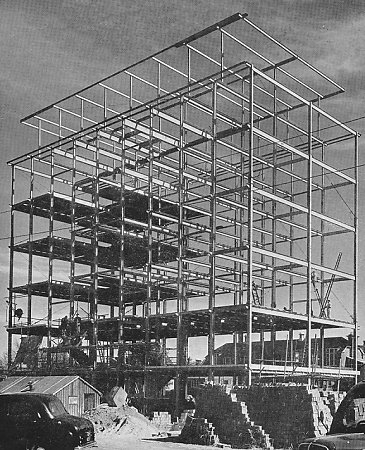
The structural steelwork for Slough
College. |
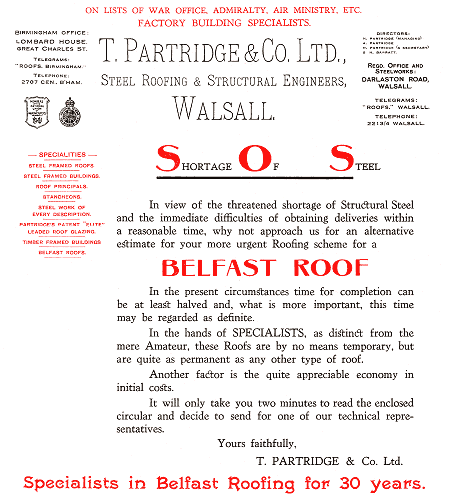 |
During the blitz the fire services in London increased
in size. A lot of extra garage space was needed for new
appliances. The company received orders for the building of
a large number of fire service garages in the London area,
and also carried out rapid repairs to factories that were
damaged during the bombing campaign.
Because of wartime shortages, every construction job
required a building license, and any purchase of steel had
to be authorised by a government department. The shortage of
timber led to the end of production of Belfast trusses, and
the patent ‘Elite’ glazing bar.
Birmingham was seen as a likely target
for the German bombers, and so most of the staff in the
Birmingham office moved to the Walsall site. The building
was sub-let to the Ministry of Works, apart from a small
room used by members of the design staff.
|
Other war work included the manufacture
of gun shields, machine gun brackets, gun pedestals, winch
casings for ships, davit frames, fulcrum brackets for tanks,
flail arms for mine destroying Scorpion tanks, and parts for
Bailey bridges. Over 1,000 tons of steelwork for power
stations was fabricated and shipped to Russia.
Towards the end of the war the company
made parts for the two top secret Mulberry artificial
harbours that were taken across the English Channel to
offload cargo on the beaches during the Allied invasion of
Normandy. |

Structural steel in the main stockyard
bay at the factory. |
After
the War
In the late 1940s large numbers of new
schools were built. The company supplied and usually erected
the structural steelwork for over one hundred and thirty of
them. On 16th January, 1947 one of the company’s founders,
Thomas Partridge died, after a long and enjoyable
retirement. He was greatly missed because he had always been
on hand to offer advice whenever needed. In the same year,
Bert’s only son Malcolm, joined the business after spending
five years in the army. He trained in the factory and the
drawing office, and went-on to become a company director in
1952. |
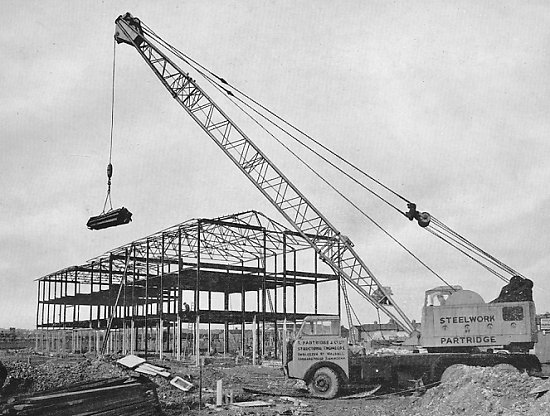 |
One of the company's mobile cranes
working on a building site. |
The mid 1950s was a sad time for the
family. Arthur died in September 1954 at the age of seventy
two, and Joseph died in March 1956 at the age of sixty nine.
In 1955 Bert resigned as Managing Director due to ill
health, and died in November 1956 at the age of sixty three.
After Bert’s death the management consisted of:
Norman Partridge – Chairman and Company
Secretary
S. H. Barrett – Contracts Director
Clement Kelly – Site Director
Raymond Partridge – Sales Director and Joint
Managing Director
Malcolm Partridge – Works Director and Joint
Managing Director |
|
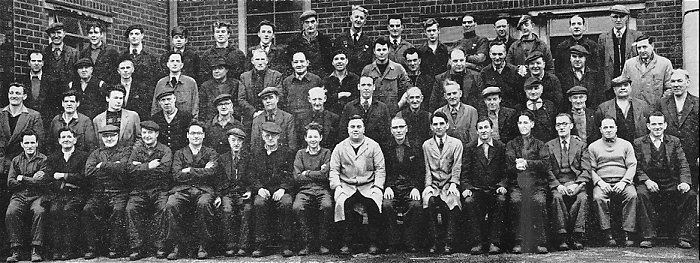
Some of the factory staff in the late
1950s. |
Part of the welding shop which
covered around 14,000 square feet. |
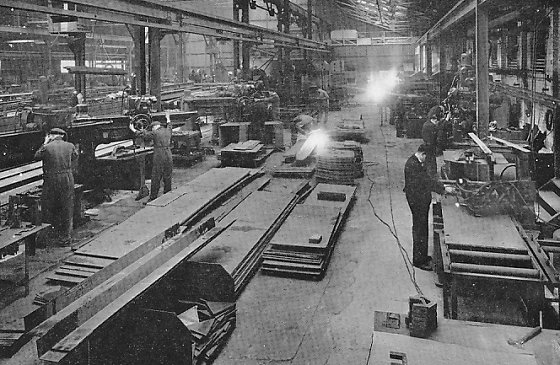 |
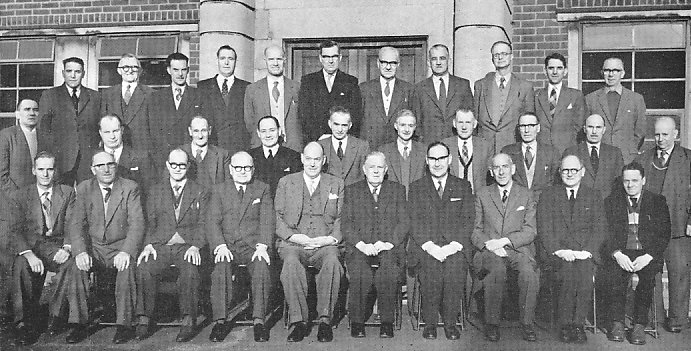
A group of employees, all with
over 25 years service.
Back Row left
to right: J. Bissell, H. Gwinnett, C. A. Troman, J.
T. Finney, E. T. Hayward, L. J. Martin,
W. H. Smith, C. Griffiths, H. J. Troman, W. A. Raybould,
and A. J. Lovatt.
Middle Row left
to right: W. E. Worrallo, J. T. Whitehouse, R.
Poynton, E. Maull, W. Booker, A. O. Troman,
C. Stackhouse, G. Dabbs, G. Manning, and G. W. S. Dixon.
Front Row left
to right: W. Coyne, G. W. James, D. Salt, S. H.
Barrett, N. Partridge, A. C. Kelly,
R. A. Partridge, G. E. Hallam, H. Smart, and F. H.
Phillips. |
Building techniques were rapidly
changing. Structural steelwork had always been held together
by rivets, but with improved methods, welding was rapidly
taking over. Portal frame construction was also becoming
standard, especially for wide span buildings.
In order to keep abreast of the times,
new machinery had to be installed in the factory, including
a large brake press, large guillotines, plate rolls, and a
massive bending machine. Over £100,000 was spent on new
machinery and plant.
Some of the company’s largest orders
included extensive building projects for I.C.I., a new power
house for Courtaulds at Grimsby, Equipment for Stewarts &
Lloyds Minerals Limited at Wirksworth, and buildings and
extensions for the John Thompson (Wolverhampton) Limited
group of companies.
T. Partridge & Company Limited closed
some years ago. The Pleck site is now occupied by Whittalls
Wines Limited. |
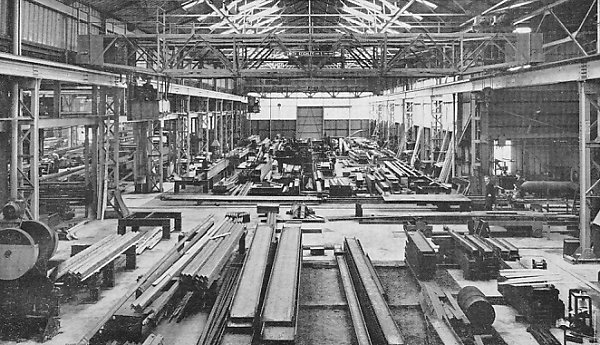 |
The new fabricating bay built in
1956. |
A bending and straightening
machine. |
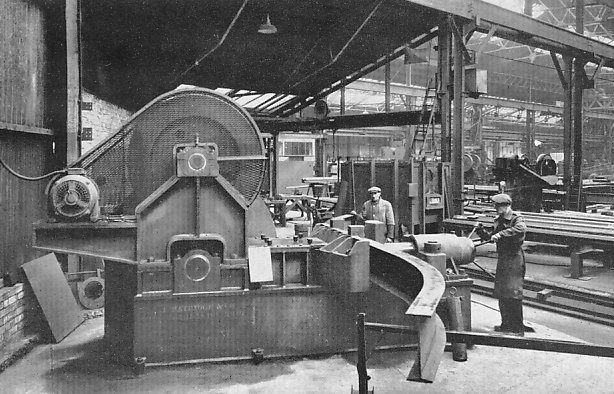 |
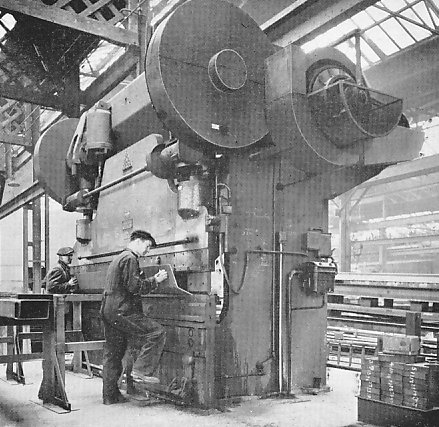 |
A 240 ton brake press for
flanging plates up to 10 feet in length. |
One of the plate rolls. |
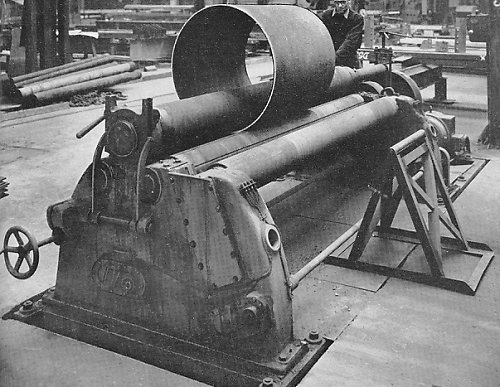 |
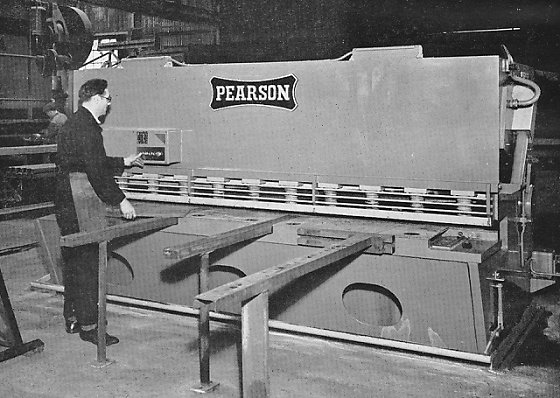 |
A large guillotine, capable of
shearing steel plate up to 10 feet long and
½ inch thick. |
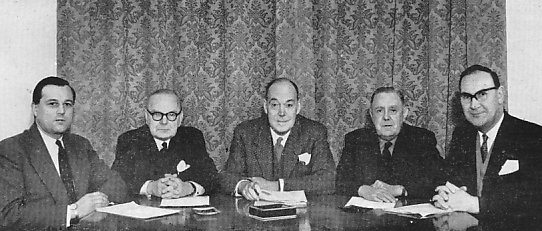
The company directors.
Left to right: Malcolm
H. Partridge (Works Director), S. H. Barrett (Contracts
Director), Norman Partridge (Chairman and Secretary), A.
C. Kelly (Site Director), and A. Partridge (Sales
Director). |
Members of the drawing office
staff. |
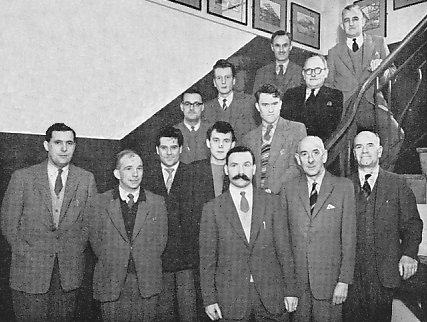 |
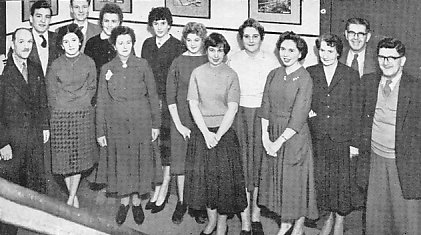 |
Members of the commercial
staff. |
Members of the works staff. |
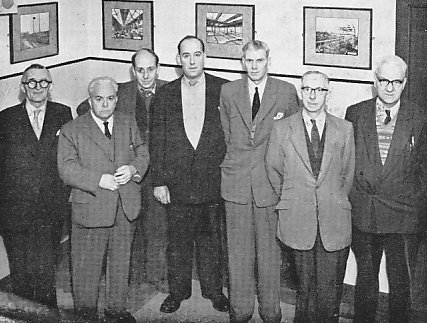 |
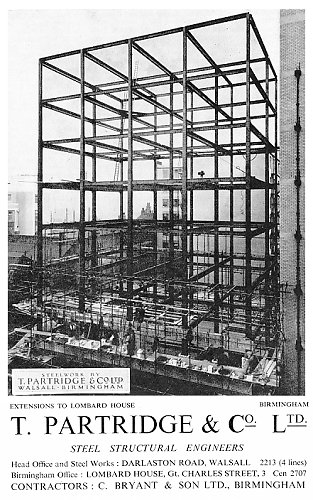
An advert from 1953.
The information and factory photographs are taken from 'The
Partridge Story 1910 - 1960' which was published by the
company. |
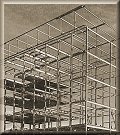 |
Return to
the
previous page |
|