The Weldless Steel Tube Company
Limited, Waddens Brook Lane, Wednesfield was founded as
a private company in 1872 by three members of the Lloyd
family; William Ellis Lloyd, William Henry Lloyd and
Francis Henry Lloyd. The factory was in Ladywood,
Birmingham, alongside Icknield Port Road and Freeth
Street. The original process began by producing a steel
billet on one of the firm’s two Swedish barrel type
rolling mills. The seamless tubes were produced by
boring a single hole down the middle of a steel billet
and expanding it. Initially tubes were produced from 1¾
inches to 5½ inches in diameter. The firm was originally
called the Wellman Steel Tube Company and made tubes for
bicycle frames, boilers, hydraulic presses, and
shafting.
By 1894 there was a great demand
for bicycles, and much of the available tubing for cycle
frames was rapidly being acquired by American companies.
This led to shortages and so the company acquired a site
in Rotton Park Street, opposite the existing works and
alongside the canal, for the building of a second
factory. Production began there in about 1897. |
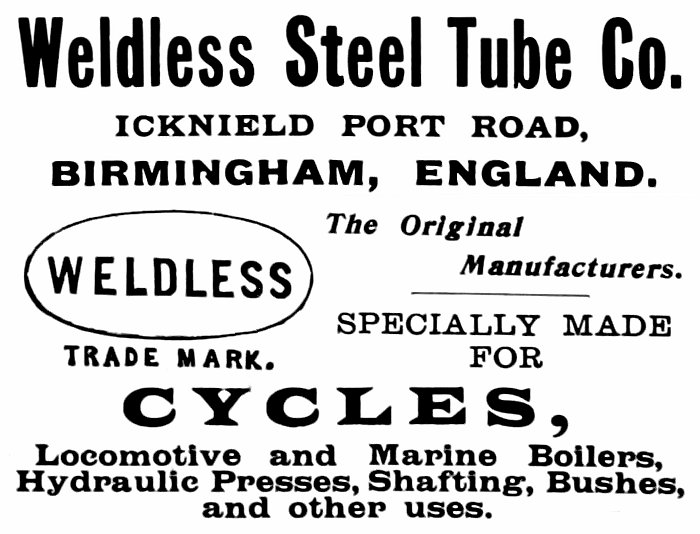
An advert from 1899. |
In 1899, on the death of William
Ellis Lloyd, and the retirement of William Henry Lloyd,
Weldless became a public limited company, with Francis
Henry Lloyd as Chairman. The company was valued at
£100,000 and at the time produced around 50,000 feet of
tube per month, up to 6 inches in diameter.
The Directors were Francis Henry
Lloyd J.P. of Stowe Hill, Lichfield, Chairman; George
Herbert Lloyd of Sutton Coldfield; John Wilson of 49
Lime Street, London; William Uprichard Jackson and
Francis Zachary Lloyd.
In 1901 the firm leased Reliance
Works in Wednesfield and purchased the factory in 1907,
followed in 1911 by the acquisition a steel mill at Hope
Works, nearby in Wednesfield. The mills at Reliance
Works were improved, so that by 1909 it was possible to
roll tubes with an outside diameter of 3½ inches. Hope
Works produced 2½ to 3 cwt. Ingots in all types of
carbon steel. During the First World War there was a
huge demand for tubes as part of the war effort. |
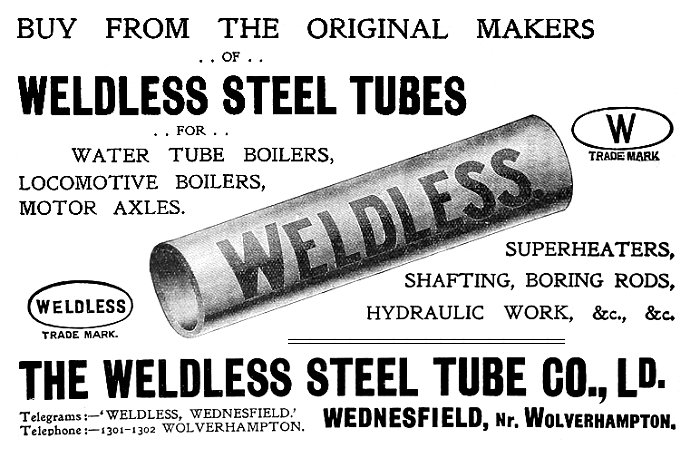
An advert from 1926. |
Francis Henry Lloyd had a terrible
shock in June 1915 when his youngest son, Major John
Francis Selby Lloyd of the North Staffordshire Regiment,
was killed in action. Francis never got over the shock.
Francis Henry Lloyd (born in 1844)
also founded Europe's largest steel foundry, F. H. Lloyd
& Company Limited, in Wednesbury. He lived at Wood
Green, Wednesbury until 1890 when he and his family
moved to Stowe Hill Mansion at Lichfield. Francis sadly
died in January 1916 after being hit by a train whilst
taking a short cut to the railway station at Darlaston,
before catching his train home. He was succeeded as
Chairman by Francis Zachary Lloyd, who in 1920 decided
to close the Birmingham factory in order to concentrate
production at Wednesfield.
Francis Zachary Lloyd (born in 1869
in Wednesbury) died at his home, Areley Hall near
Stourport, in 1920. He was awarded a C.B.E. for his work
on the organisation of supplies during the First World
War, and became a member of the Iron and Steel Institute
in 1920. After Francis Zachary Lloyd’s death, W. V.
Jackson became Chairman and R. E. Moynihan became
General Manager. The other Directors were Daniel Charles
Lloyd (son of Francis Henry Lloyd) and Mr. J. Wilson. |
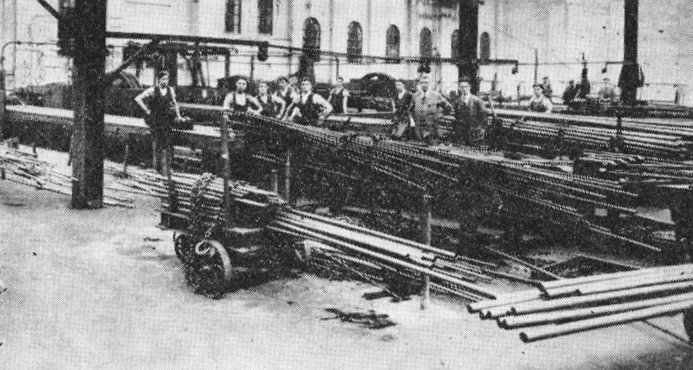
Cold drawing in Hope Works. |
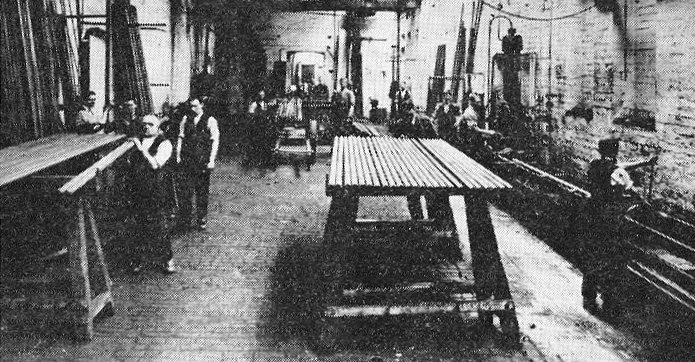
Hydraulic drawing in
Reliance Works. |
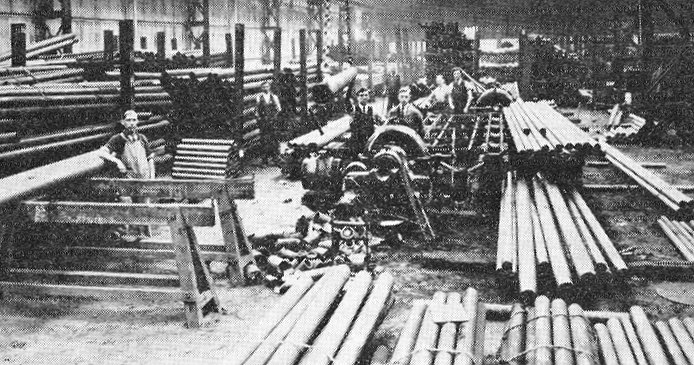
Tube cutting
equipment. |
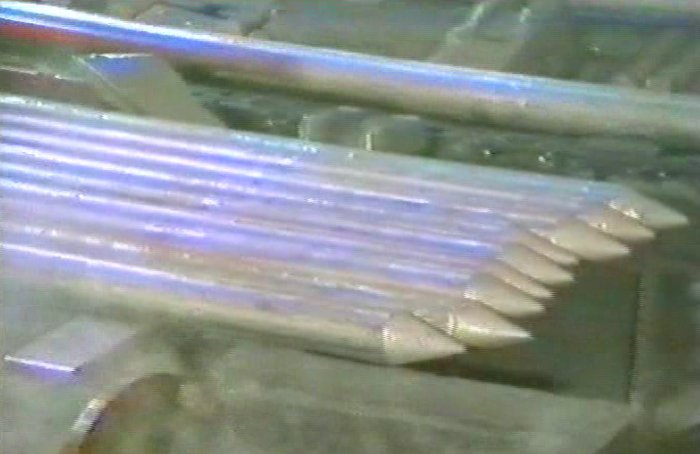
Mandrel Bars. |
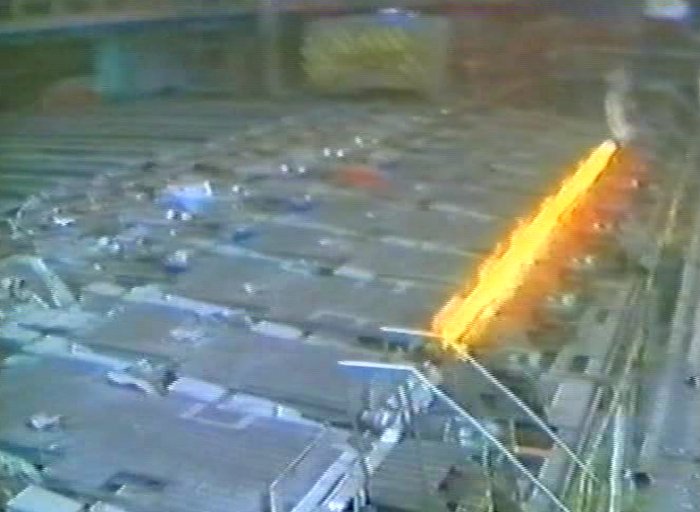
A corner of the rolling mill. |
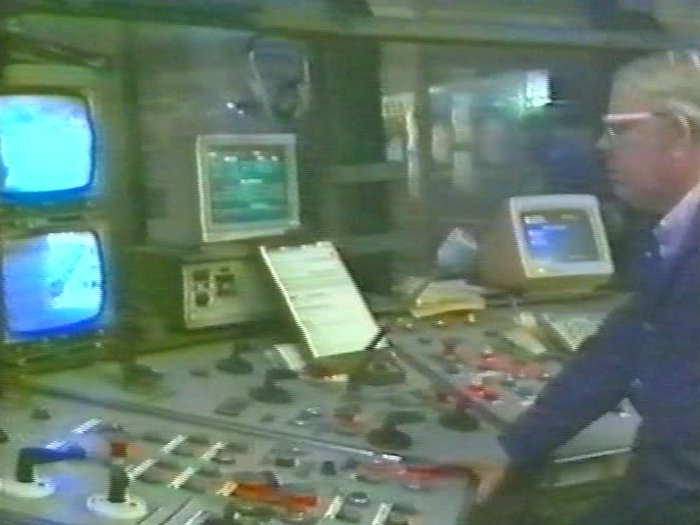
Operating part of the complex
computer control system. |
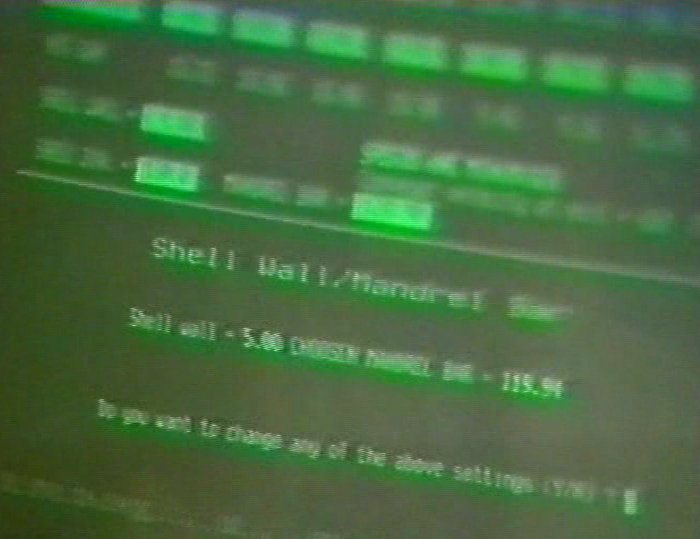
One of the computer displays. |
The firm began to suffer from the
effects of the global depression in the early 1920s
which resulted in the closure of the factory from around
1922 until 1924. It became part of Tube Investments
Limited in 1929, but closed again in the early 1930s
because of the great depression. The factory opened
again in 1934 and in the Second World War concentrated
on the production of aircraft gas cylinders and barrage
balloons.
By the 1950s, orders were in
plentiful supply and in the late 1950s the company
claimed to have produced the world's longest rolled
stainless tube, which was over 55 feet long, with an
outside diameter of 6 inches. New machinery installed in
1954 included two Pilger mills of the latest design,
with ancillary plant, including gas producers.
A big development took place in
1969 when a £10 million continuous tube mill was installed,
consisting of a three roll piercer, a mandrel mill to
elongate the pierced billet, and a stretch reducing mill
to produce the final size of tube required. The new
plant could produce more than 100,000 tons of seamless
tubes each year in the continuous mill. There was also a
specialised finishing plant at Corby. Products included
boiler tubes, and tubes for process plant, power
generation, pipelines, vehicles, construction equipment,
oil wells, mineral exploration, and sporting goods such
as golf clubs and bicycles. |
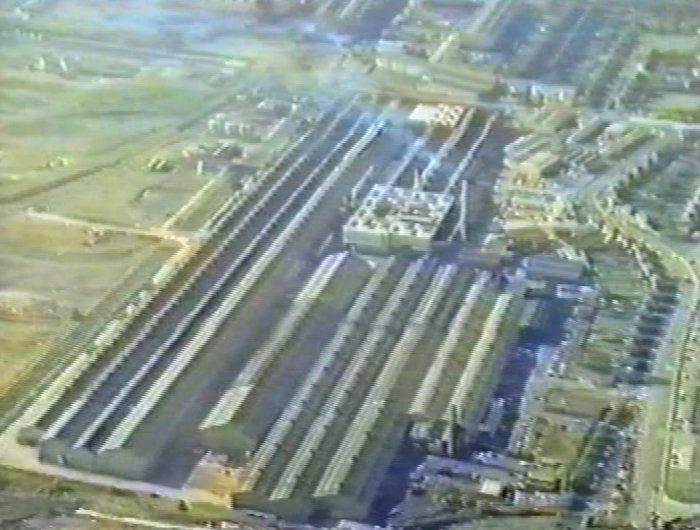
An aerial view of the factory. |
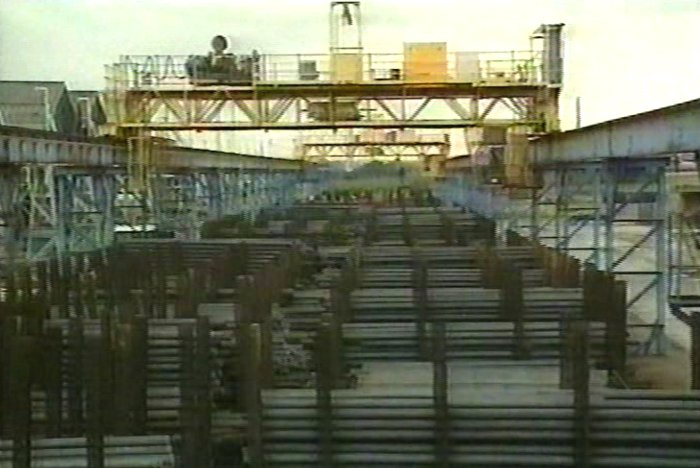
The outside storage area. |
Tubes were produced in three
stages. Initially a solid billet was pierced on the
unique three roll rotary piercer, followed by
elongation over a mandrel bar to achieve a
controlled wall thickness, before rolling to a
finished diameter on a stretch reducing mill. The
continuous process was accurately monitored and
controlled by a sophisticated computer system, with
quality control forming an integral part of
production. Many of the firm’s products went abroad,
to countries including Burma, Cuba, Jamaica, New
Zealand and Norway.
In the 1970s the firm became T
I Weldless Limited, by which time around 1,500
people worked in the factory. On the 22nd December,
1983, the company became Seamless Tubes Limited. By
the early 1990s the firm was finding it difficult to
compete with cheaper foreign competition and began
to make a loss, which by the mid 1990s had increased
to around £2 million annually. By this time it was
part of British Steel Seamless Tubes and mainly
produced oil and gas pipes, and axles for lorries. |
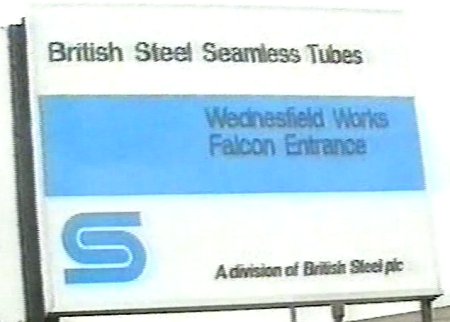 |
Because of the annual loss, British
Steel decided to close the factory in 1995 and
commissioned Connell Brothers Limited, of Salford,
Manchester to demolish the buildings and make the 37
acre site safe. The closure resulted in the loss of 520
jobs.
The site then became part of Wednesfield Steelpark,
which was opened by the deputy Prime Minister, John
Prescott in 1999. |
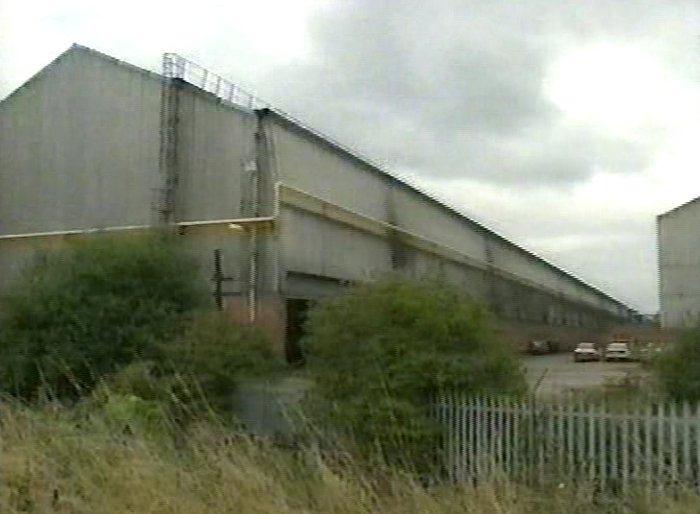
Part of the factory. |
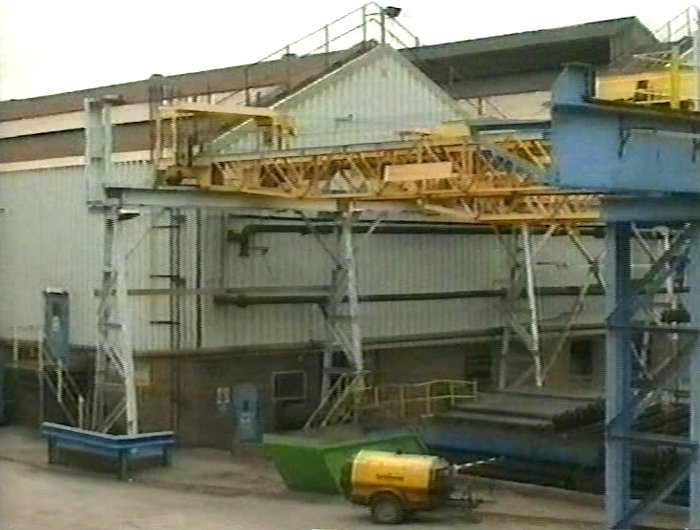
A final view of the factory. |
 |
Return to
the
previous page |
|