Foundries
West Bromwich lies on countless coal seems that played
an important role in the development of the town. When
the canal (the BCN) was built, heavy and bulky items
such as coal and iron ore, could be easily and cheaply
transported for the first time. Many ironworks and iron
foundries were built, close to the canal, where they
greatly prospered. This continued with road improvements
and the arrival of railways.
Many ferrous and non-ferrous foundries opened in the
town, along with essential patternmakers. The industry
was extremely successful until the disappearance of many
factories in the 1970s and 1980s.
T. Masters & Sons (Park Foundry)
Company Limited.
The firm was established in
Birmingham in 1896, before moving to the present site in
Glover Street, West Bromwich, in about 1924. It
originally specialised in ingot moulds, general engineering
castings and ingot casting equipment for the non-ferrous
industry.
The company developed an ingot
casting conveyor that was manufactured for the
non-ferrous and pig iron industries. It also exported
ingot moulds and casting equipment to many countries and
was widely known for its ingot moulds.
It now specialises in the design
and production of ingot casting machines and specialised
equipment for the non-ferrous and ferrous secondary and
primary metal refining industries.
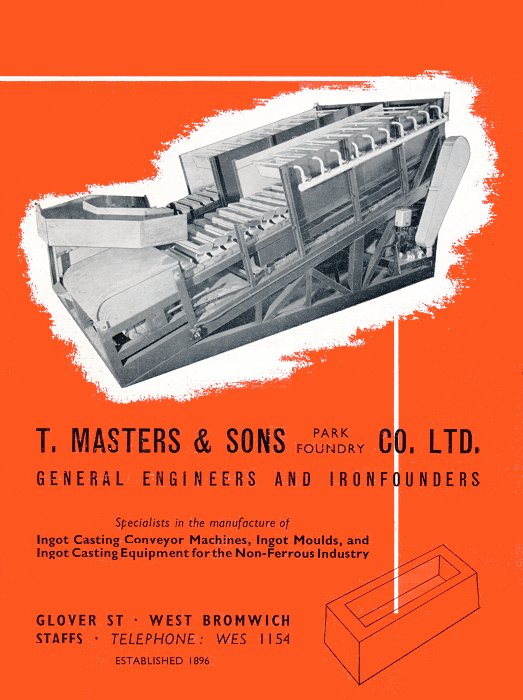 |
An advert from the
mid 1950s. |
William Mills Limited.
The firm was one of the oldest
established aluminium founders in the country. It had
around 500 employees and had up-to-date facilities for
sand casting, gravity die casting, and pressure die
casting. The firm had a laboratory with X-ray units and
analytical and tensile testing departments.
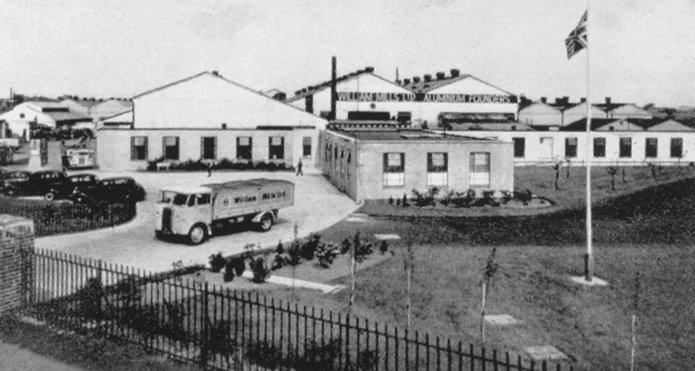
William Mills Limited.
Newby & Son (Ironfounders) Limited.
The business was started in 1882 by
Henry Newby. It became a limited liability company in
1938, manufacturing all types of castings for electrical
control gear, general engineering, and castings that
were suitable for vitreous enamelling. The company
began to specialise in high duty iron to BSS. Grade 17, which
is suitable for all types of pressure tight castings,
crank cases, water pump bodies, compressors and
air-cooled cylinders etc.
An airless shot-blast machine was
installed in the early 1950s for the efficient cleaning
of castings and the checking for any hidden defects. The
firm also began to construct pattern
equipment to customers' drawings. The firm now has
four sites in the West Midlands and employs around 240
staff.
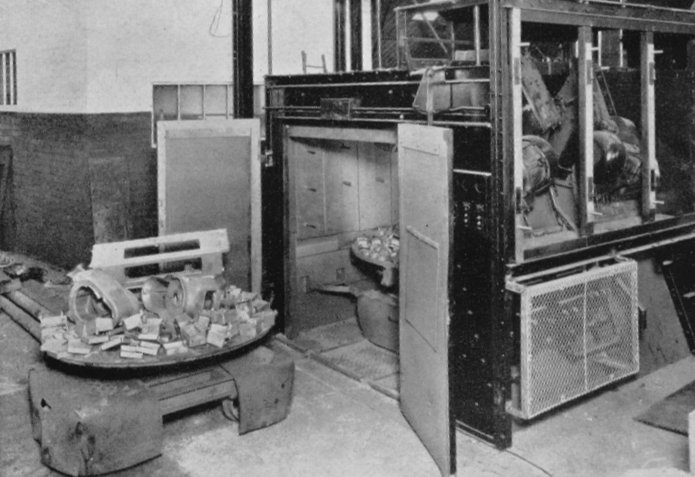
An airless shot blasting machine
at Newby & Son.
An advert from the
mid 1950s. |
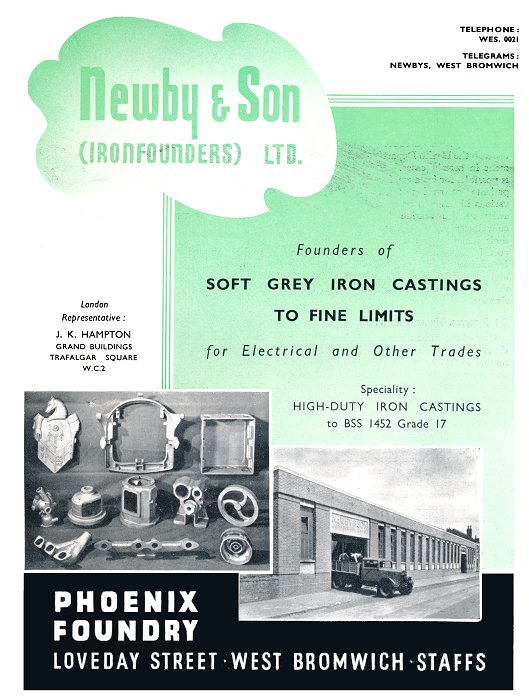 |
The Sandwell Casting Company.
The company, formed in 1928,
originally supplied its parent company, Sanbra Limited,
with sanitary brass castings, but in 1939 it began
making general engineering castings in copper and
aluminium alloys. From the late 1940s the business
expanded and the factory covered an area of over 100,000
square yards, with a staff of 400.
In the core shop, forty operators
were employed, mostly women. Cores of all sizes were
manufactured, weighting up to several hundredweights.
State of the art core-blowers were installed along with
a central steel band conveyor which took the cores to
the drying ovens.
The firm's five foundries operated
as follows in the 1950s: Small
orders were executed in the copper-base jobbing foundry,
along with complicated work unsuited to moulding
machinery. In the mechanised copper-base foundry the
greater part of production was brass castings, such as
valves, stopcocks and plumbers' fittings for Sanbra
Limited. Large orders were quickly undertaken thanks to
the use of modern machinery and furnaces. The aluminium
sand foundry made accurate castings, particularly for
the aircraft industry. About thirty workers were
employed in gravity die-casting in aluminium, brass and
bronze, specialising in precision castings. High quality
castings in aluminium and brass were mass produced in
the pressure die-casting section, where the latest
machinery turned out brass castings up to 6½ lb. in
weight and aluminium castings up to 3¼ lb. in weight.
In the shot-blasting department,
copper-base castings were first cleaned, inspected and
dressed on electric grinding machines. Aluminium
castings were not as a rule, sand blasted. The surplus
metal was usually removed in the aluminium dressing shop
by abrasive grinding wheels. All dies used on the
premises were manufactured in the die-sinking section.
The very
modern machine shop employs highly qualified technical
staff, producing mainly patterns in metal, but also in
wood, if required. There was a metal recovery plant
which handled about 25 tons of foundry residues each
week and a heat-treatment section.
In the laboratory, all raw
materials can be analysed before processing, and finished
castings checked to ensure that specifications are
met. Moulding sand used in the foundries was checked at
15-minute intervals and a close check was kept on the
temperature of the metal in the foundries before each
casting was poured. There was a well-planned despatch
department and a fleet of lorries and vans, so that
countrywide deliveries could be quickly and efficiently
made.
Today, Sandwell Castings is capable
of producing a wide variety of cylinder heads,
manifolds, crankcases, covers, cases, water pipes,
housings and sumps, all of which are used extensively in
the manufacture of diesel engines.
Sandwell Castings produce a wide
variety of products for various applications and
environments, including components used in the
manufacture of light passenger vehicles, such as
manifolds, steering boxes, covers, housings, water
connections and pipes, engine mounts, sumps, water pump
bodies and a variety of mounting brackets.
Sandwell Castings is capable of
producing high integrity parts for use in air
compressors and also castings that are subject to high
pneumatic pressures. The firm can also produce castings
in copper based alloys and in aluminium, that are used
in safety critical areas and hostile environments for
the water and gas supply industries.
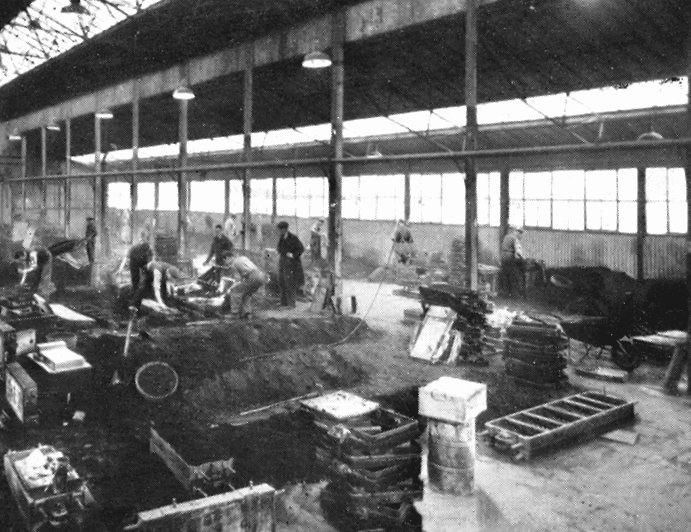
One of the Sandwell Casting
Company's foundries.
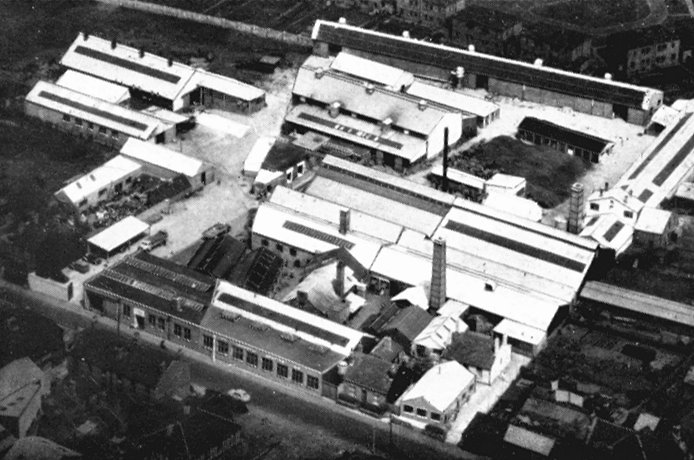
The Sandwell Casting Company's
Factory.
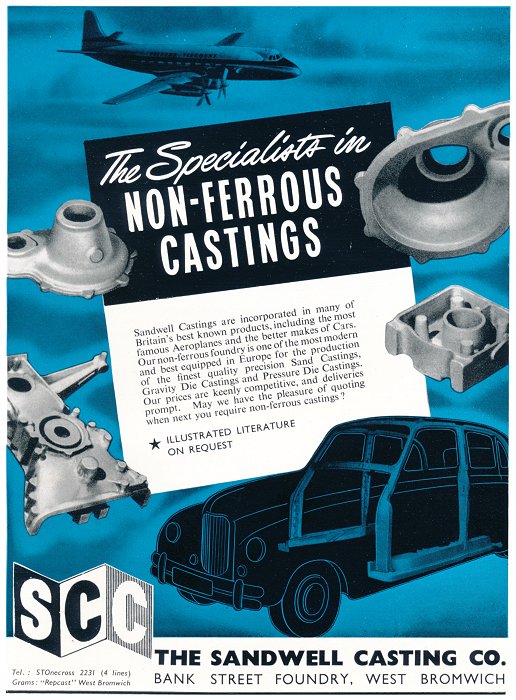 |
An advert from the
mid 1950s. |
|