Archibald Kenrick &
Sons Limited
Archibald Kenrick
was born at Wrexham on the 12th November, 1760. In
1780 he moved to Birmingham, where he went into
business with a distant relation, Henry Witton,
making buckles. After acquiring some knowledge of
plating, he went into partnership in 1787 with
another buckle maker, Thomas Boulton, thanks to
financial support from his father. In 1790 Archibald
married Rebecca Smith.
|
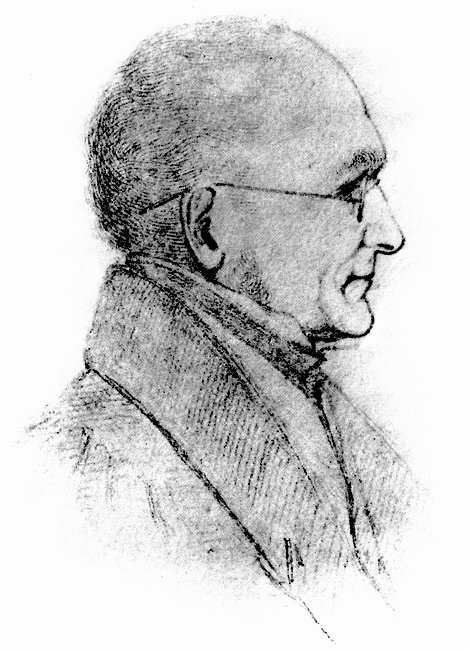
Archibald Kenrick. |
With the increasing use of shoe laces, it was
time to turn to other products. A year later, he
opened an iron foundry in West Bromwich, producing
cast ironmongery, including coffee mills, door
furniture, cast nails, and mole traps. The foundry
was built on a piece of land, covering over 4,000
square yards, which he leased from John Houghton, for
an annual rent of ten guineas. It was just to the
east of Spon Lane, stretching from Union Street to
the canal. The firm still occupies the same site
today.
Archibald and Rebecca moved into the Springfields,
a large mansion house at the top of Roebuck Lane.
Being quite close to the foundry, Archibald would
ride to and from the works on a mule.
In 1805, the firm began to produce cast-iron
hollowware, particularly for culinary use, and
Archibald developed and patented a new annealing
process. In 1812, steam powered machinery was
installed in the factory, which became the first
factory to manufacture saucepans with rims. |
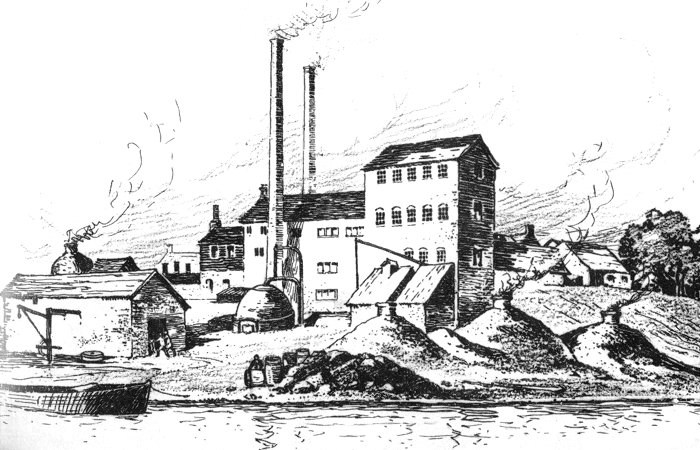
The factory in about 1800. |
At this time, Archibald’s nephew, Samuel Kenrick joined him
as a partner in the business, which became known as
Archibald Kenrick & Company. In 1807, Rebecca
Kenrick gave birth to a third son, Timothy Kenrick,
but sadly she died in 1809. Her other children were
Archibald, born in 1798 and George, born in 1803.
In 1812 Archibald married his second wife, Mary
Eddowes, who was 48 at the time. There were four
sons and three daughters from Archibald’s two
marriages.
|
The location of the factory, as it was
in 1902.
In 1818 and 1823, the company purchased land
adjacent to Spon Lane works and the factory was
enlarged. A tramway was built into the ovens which
saved time and heat, and the firm rapidly expanded.
Archibald built houses to rent to a few key workmen
and the area was known locally as Kenrick village. Samuel Kenrick
initially had one fifth of the profits, which
rose to one quarter in 1814 and one third in
1820. The relationship between the partners
deteriorated and Samuel left the business in
1827 to establish Summit Foundry nearby, taking some
of the workmen with him.
Archibald was then joined in the business by his
eldest son, Archibald junior. He
had been educated at a private academy and studied
mechanics in Birmingham. On the 20th October, 1826
he married Anne Paget at Loughborough.
In 1827 Archibald Kenrick, Junior, became a
partner with his father Archibald Kenrick, in the
business, which became Archibald Kenrick and Sons. |
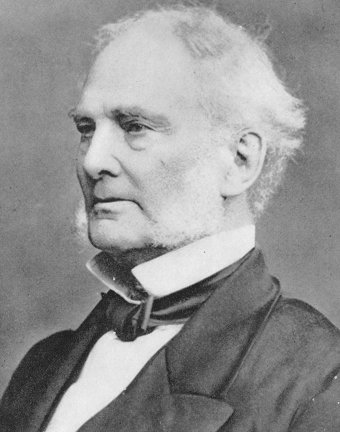 |
|
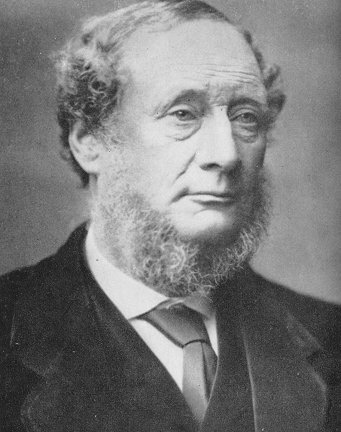 |
Archibald
Kenrick junior. |
|
Timothy
Kenrick. |
|
Timothy Kenrick, Archibald senior’s other
son, joined the firm in 1830. Archibald senior died in
1835. At that time there were several hundred
employees at the factory. When Archibald senior
died, his sons, Archibald and Timothy had equal
shares in the partnership. Timothy also served as
Chairman of Lloyds Bank and founded the Nurses'
Training Institution in Birmingham, for which he
purchased a home. Archibald junior began to
suffer from ill health, and so in 1847, his son John
Arthur Kenrick, left university to assist in the
family firm. John Arthur took responsibility for
production. In 1850, John Arthur's brother, William
Kenrick, joined the company and became responsible
for commercial management.
The company’s 1840 catalogue includes door
furniture, saucepans, a waffle iron and a humane man
trap. In 1844 the firm began casting hinges.
|
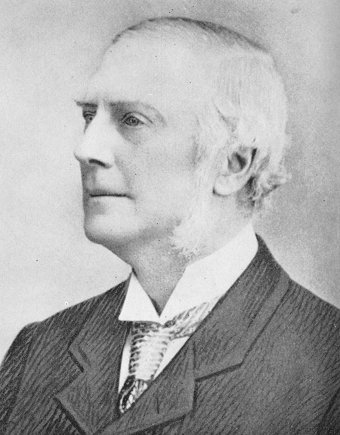 |
|
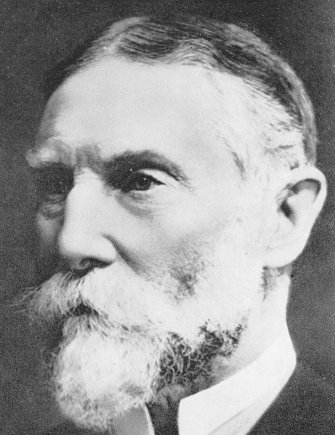 |
William
Kenrick. |
|
John Arthur
Kenrick. |
|
In 1846, Timothy had taken out a patent for
glazing and enamelling the metal surfaces of cast
iron, which led to the growth of sales, both at home
and abroad, and also a lot of investment in the company. In
1852 a new foundry was built next to the canal wharf
and in 1857 William became a full partner. In 1868, production management was
in the hands of Frederick Ryland, a professional engineer who was
also the first non-family manager employed in the
firm. Kenrick’s first travelling salesman was
appointed in 1872 and in 1873, George Hamilton
Kenrick, cousin of the two senior partners, John
Arthur Kenrick and William Kenrick, entered the
firm. He became responsible for the day-to-day
commercial management.
By 1878 Kenricks employed over 700 people and so
new offices and warehouses were built. At that time,
more than 30 percent of products were sold
overseas. In 1883 the firm became a limited company,
with John Arthur Kenrick in charge. On the 23rd
February,1885, Timothy Kenrick died, at Maple Bank,
Birmingham.
|
Kenricks' factory.
1886 was a momentous year. The firm acquired the
Birmingham Hollow-ware Company and Kenricks
amalgamated with a principal competitor, A & E
Baldwins, to become the largest supplier of cast
iron butt hinges in Britain. In 1889 Kenricks acquired the bedstead castor
business of Parry & Wythes of Birmingham and in the
following year, new offices were opened in Glasgow,
Dublin and Leeds. Expansion continued in 1898 when
Kenricks acquired brassfounders, Thomas Pemberton,
and increased the workforce by a further 400 people.
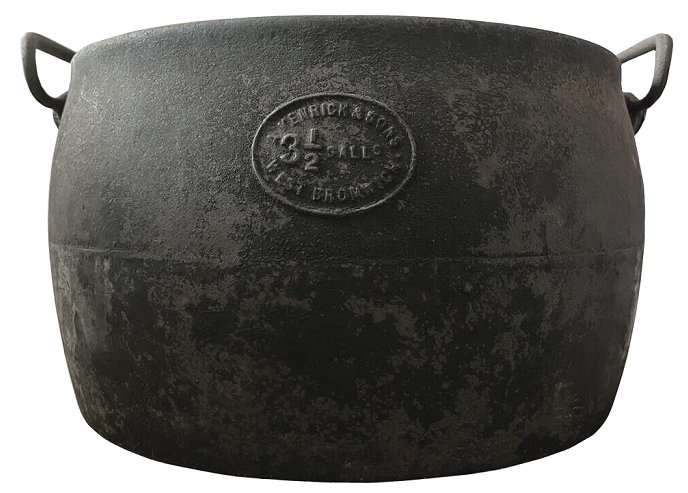
A cooking pot.
In 1895,
19 acres of land was given to the town by
John Arthur Kenrick and William Kenrick as the site
for Kenrick Park.
In 1898, John Arthur Kenrick JP., resigned as
company chairman and in 1904, Kenricks began to
manufacture cylinder door locks. By this time, the
company controlled several steel hinge businesses
which were amalgamated in 1910 to form United Hinges
Limited, with premises adjacent to Kenricks’
factory. |
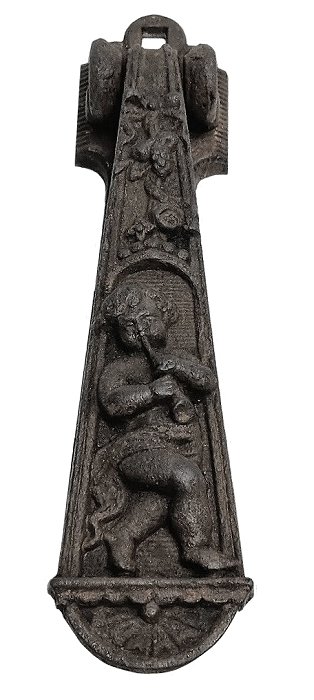
A cast-iron door knocker. |
By 1911 there were over 1,200
employees and John Archibald Kenrick had taken over
as managing director. The firm was listed as
ironfounders, enamellers and lock manufacturers,
specialising in cast iron hollowware, household and
builders' ironwork, malleable ironwork and castings. In 1912, during his time as Mayor of West
Bromwich, John Archibald Kenrick presented the
Kenrick Clock in Dartmouth Square, to the Borough.
It still stands there today.
At the outbreak of the First World War, civilian
production ceased and the business relied on
government contracts for work as part of the war
effort. Products included grenades and shells and
fulfilling a
large number of military contracts.
By 1930, George Hamilton Kenrick
(1850–1939), was chairman of the company. The 1930s
were a bad time for the cast-iron hollowware and
hardware trade, which had been in permanent decline
for a decade or so. Most of the holloware produced
at that time was made from aluminium and so Kenricks
had started to produce different cast-iron products
including electric and gas irons, but without
success. Their best selling cast-iron products were
baths and so the firm concentrated on their
production. Bath sales accounted for 39 percent of
turnover by 1935.
Around this time, Wilfred Byng
Kenrick became chairman and he appointed his son
William, as head of the sales department.
In 1939 at the beginning of the
Second World War, the firm had to rely again on
government contracts for war work. The manufacture
of hollowware ended and the many highly profitable
government contracts, rescued the company from its
decline. The firm began moving from iron-casting to
die-casting. During the war, the company
manufactured seven million hand grenades and 1.5
million, 2-inch mortar bombs.
|
At the end of the war, in 1945,
Wilfred Byng Kenrick’s, son, William, was promoted
to managing director. In 1949, G. F. Shepherd, a retired engineer
living in Australia, agreed to license the company
to manufacture and sell his patented furniture
castor, which led Kendricks into a new area.
The first set of Shepherd castors were produced in
1950 at the time when the bath department closed and
pressure die casting replaced traditional sand die
casting in the factory. Wilfred Byng retired in 1953 and Arthur Wynn
Kenrick, a distant relative, formerly joint managing
director of Kenrick and Jefferson, was appointed
Chairman, and John Donkin, an engineer, who formerly
worked for GEC, was appointed as joint general manager to work with William.
At the same
time, an Australian inventor offered William the
option of using a patent for producing Shepherd's
furniture castor, by die-casting. William
recommended this to the board and production soon
began.
Thanks to the great success of the castors and
William's insistence that from then-on, the
number of sales, and
what the consumer wanted, would determine product
policy and investment, rather than the plant's
capacity to produce items, enabled the firm to
survive.
|
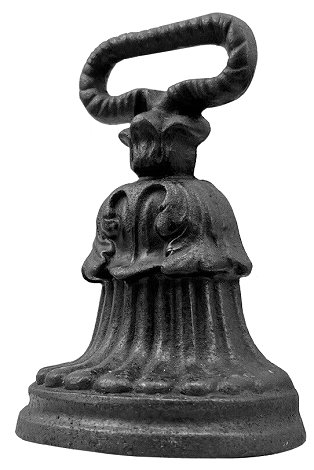
A cast iron door stop. |
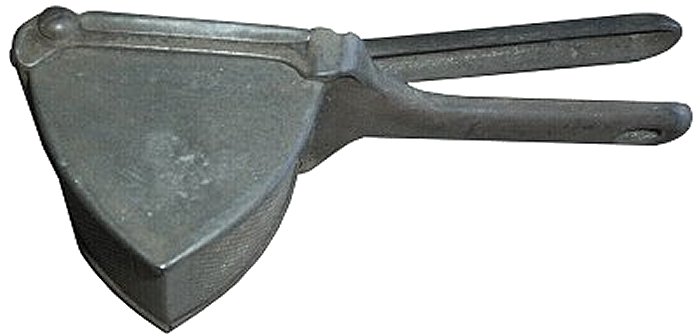
A Kenrick potato
masher. |
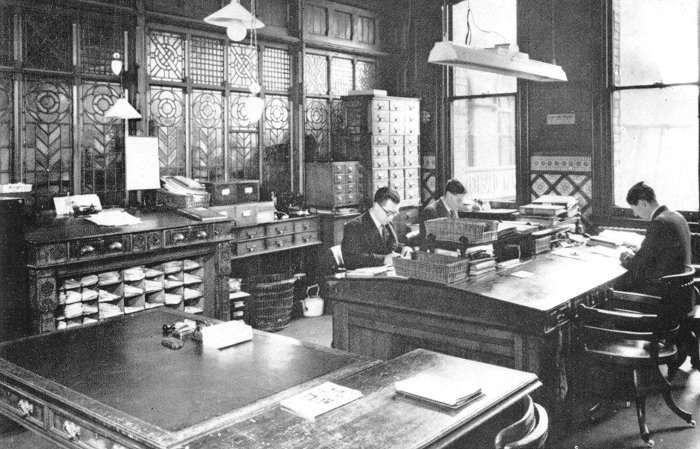
The private office
in 1952. |
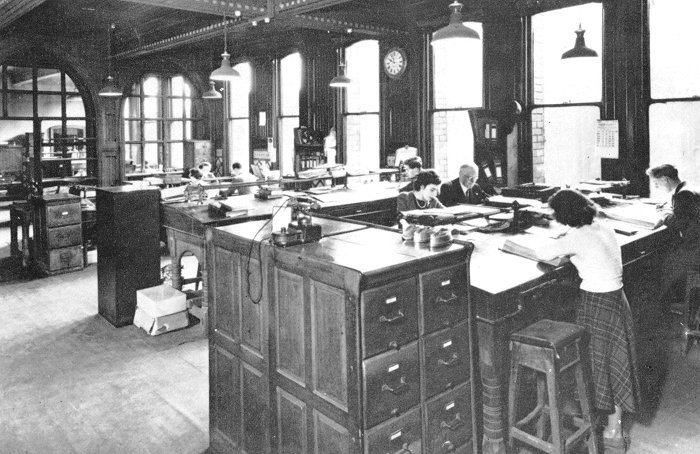
The public
office in 1952. |
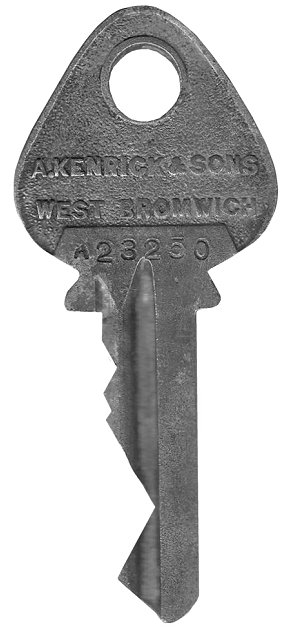
Locks and keys have
been important products. |
In
1956, the Kenrick tinning department closed and
thanks to a successful promotional campaign, the
1,000,000th set of Shepherd castors was made in Feb
1958. Castor sales then amounted to 64 percent of
total sales and so the inventor was presented with a
gold plated set of castors. In 1959, the land that had been used for the
Kenrick recreation ground was sold to West Bromwich
Albion Football Club. Two years later the Shepherd
Minicastor was introduced, and the firm had 420
employees.
In 1962, Kenrick’s first plastic castor,
the Meteor, was manufactured under license, then in
the following year, William became chairman as well
as Managing Director.
In 1964, his son Martin,
joined the company and in 1965 the iron foundry
closed. At that time, die cast products accounted
for 80 percent of total output, and Kenrick’s were
described as zinc alloy die-casters and hardware
manufacturers.
|
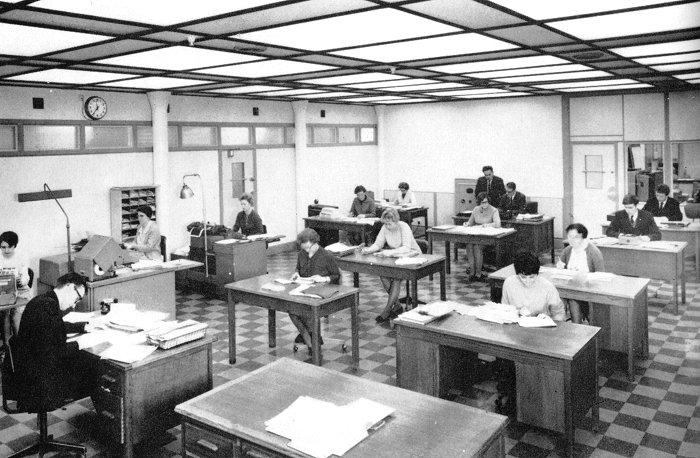
The accounts
office in 1968. |
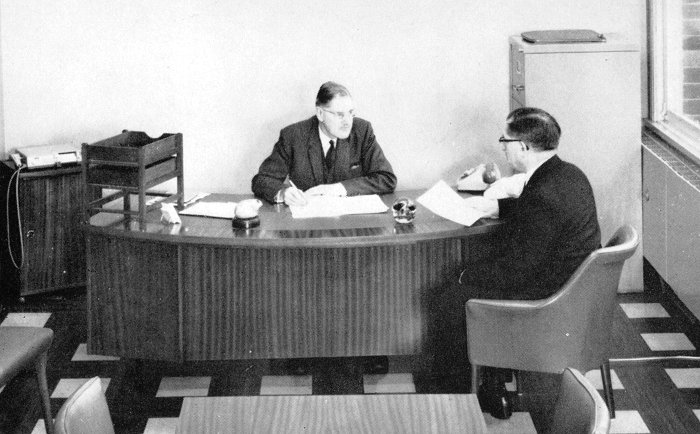
The chairman's
office in 1968. |
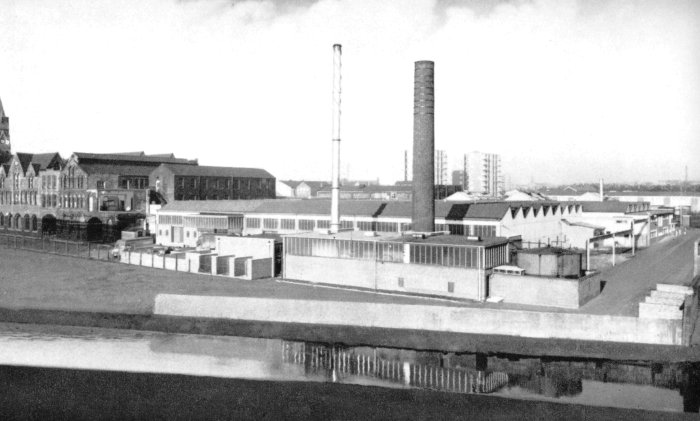
The factory in
1968. |
In 1978, William retired as Managing Director and
Chairman, and Martin Kenrick became chairman. The
firm introduced more new products including
aluminium extruded hardware, such as window handles
and letter plates, aluminium racking systems and
aluminium twin wheel castors. A new range of
bathroom accessories was introduced in 1984. By
1986 the workforce had been reduced to 120 and the
company was trading profitably. In 1988, new die-cast products included phone box
casings, socket covers and engine mountings. More
castors were introduced in the form of the Suroy
industrial castor in 1990 and the Textile castor in
1991, along with the Sabre Lock shootbolt for
windows.
In 1993 the popular Sentri Lock
system was launched and Kenrick’s Window Test Centre
opened. Since then, Kenricks have continued to
develop new and innovative products and the firm has
celebrated its 230th anniversary. Which is quite an
achievement. |
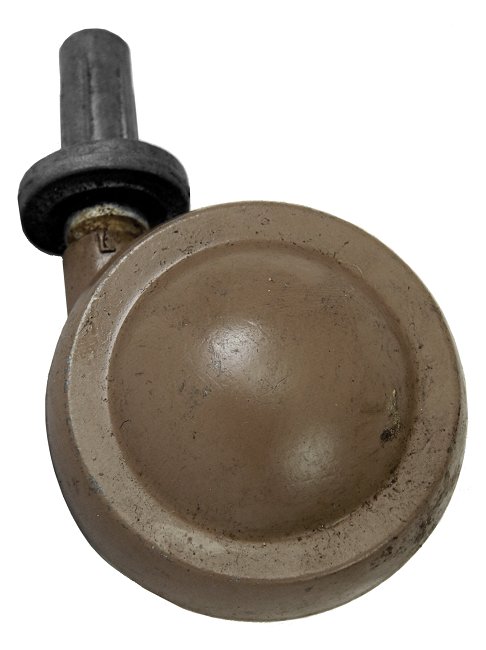
A Shepherd castor. |
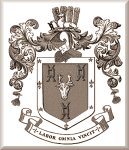 |
Return to the
previous page |
|
|