The Engineer, March 1st 1907. The
Generation of Power at Neasden
Through the kindness of Mr. Thomas
Parker, consulting engineer for the electrification of
the Metropolitan Railway, under whose guidance all the
arrangements at Neasden have been effected, we are
enabled to state the technical and economic results of
the working of this remarkable power station and to
describe the methods whereby these results are obtained.
The plan of the power house is a
rectangle about 325ft. long by 102ft. wide, with an
excrescence 70ft. by 114ft. on its south side containing
economisers and chimney, and with the condensers and
cooling towers standing also outside these limits on the
north side.
There is also a lake of 2½ acres
area and 7 million gallons capacity, and two artesian
wells yielding respectively 32 and 14 thousand gallons
an hour of clean water. The cooling powers of the lake
are not drawn upon except under stress of exceptional
load, because the scour of the water flow brings with it
a little troublesome mud, which is undesirable in the
circulating pumps. The boiler feed is wholly from the
wells.
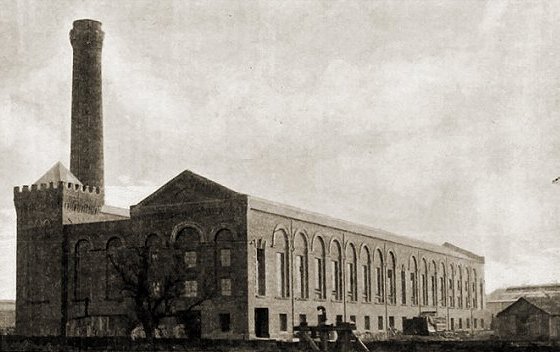 |
Neasden Power Station. It opened
in December 1904, and closed in 1968. It was
later demolished. |
The coal is brought by railway
sidings to the south west corner of the building where
the wagons are tipped direct into a large hopper 16ft.
square. From this it drops through crushing rolls when
of too large size for mechanical stoking, which rolls
are not, however, often in use. From the rolls a shoot
takes it straight on to the buckets of a great
chain-and-bucket conveyor, the buckets each carrying 28
lb. and being spaced 2ft. apart. This conveyor travels
at speeds up to 50ft. per minute and its full carrying
capacity is about 20 tons per hour.
This conveyor ascends vertically
between 50ft. and 60ft. to the top of the ‘hopper
tower,’ then travels horizontally the full length of the
building, distributing the coal into the bunkers over
the boilers, which bunkers have a combined capacity of
2,000 tons; descends vertically at the east end of the
building; and returns horizontally in front of the ash
doors. The conveyor is used alternately for feeding coal
to the bunkers and for the removal of ash. The ash is
raked by hand direct into the buckets of the conveyor
which in turn empty themselves into an ash bin situated
in the ‘hopper tower’ over the coal truck siding. This
conveyor chain, which has a total length of about 730ft.
has worked satisfactorily with only minor repairs since
the start.
From the bunkers the coal descends
by automatic weighing shoots to the mechanical stokers,
which are driven by eccentrics on a longitudinal shaft
with an electro-motor on each end of it. The shoots drop
the fuel evenly on travelling chain grates driven by the
same shaft. Roney grates were fitted in the first
place, but were replaced by chain-grates on account of
their being unsuitable for the kind of coal found to be
most economical, which is North Staffordshire
double-screened nuts. Preparations are now in hand for a
large extension of this building and of the plant it
contains.
The four turbo-generator sets at
present installed are served by fourteen water-tube
boilers designed for 200 lb. pressure and worked at 180
lb. to 185 lb. with 180 deg. Fah. superheat. They were
hydraulically tested to 300 lb. per square inch for one
hour. Each has 260 tubes, 18ft. long by 4in. diameter,
and two drums 23½ft. long by 4½ft. diameter. This gives
each boiler 5730 square feet of heating surface, and its
grate area is 100 square feet. Their guaranteed
evaporative power is 20,000 lb. per hour each, with 25
per cent. overload capacity; this corresponding to 3½ to
4⅜ lb. per square foot heating surface. The superheater
of each boiler contains 128 tubes, l½in. in diameter,
giving 894 square feet of external heating surface. Four
banks of economisers serve the fourteen boilers with a
total of 1760 tubes. These deliver the feed at an
average temperature of about 275 deg. Fah. The feed is
brought to them from the hot well through feed heaters,
which raise the temperature about 100 deg. Fah. by two
compound vertical double acting steam pumps, each of
which is equal to supplying three turbines at full load.
Each turbine is served by a
separate barometric condenser, the rising exhaust main
being 54in. in diameter and 34ft. in height. Each is
designed to condense normally 66,500 lb. of steam per
hour, and will deal satisfactorily with about 60 per
cent. in excess of this. The remainder steam, that is to
say, the steam that is not carried away as condensed
water with the circulating water, and the air are drawn
off by a steam-driven vacuum pump, its two pump barrels
being 24in. in diameter by 24in. stroke, while the one
steam cylinder is 10in. diameter by 24in. stroke, all
three being arranged tandem.
This pump runs at 100 double
strokes per minute. and consumes 55 horsepower. No
auxiliary jet ejector condensers are employed. The
circulating pumps are centrifugal, one 18in. pump to
each turbine, delivering 250,000 gallons per hour, or
not much short of forty times the weight of steam to be
condensed. There is also a 16in. hot water pump to each
turbine.
It is to be noted that the range of
boilers is not ring connected. One header connects the
whole set of fourteen. The main steam pipes to each
turbine from this header are 12in. in diameter. The
steam pipes are of steel, and exhaust pipes of cast
iron.
There are three duplex cooling
towers, each essentially composed of an immense number
of timber slats, which baffle and spray the water as it
falls through a height of about 20ft. Each can cool
400,000 gallons per hour down to at least 85 deg. Fah.
The hot water, after being pumped to the heads of these
towers, flows in a number of streams along wooden
troughs perforated with a large number of holes through
which it falls upon the topmost tiers of slats. These
towers are substantial well-braced timber structures,
which have withstood without any wracking or other
injury the winds of a somewhat exposed and elevated
locality. The hot well, from which the feed is taken
direct to the economisers, and from which also the bulk
of its contents, namely, the circulating water, is
pumped to the cooling towers, in a wide concreted trench
running along, and outside the north wall of the
station.
The four turbines, of
Westinghouse-Parsons pattern, are duplex, each of 3,500
kilowatt normal power, and capable of 50 per cent.
overload for one hour. There is a daily momentary peak
in the use of each of them of about 100 percent
overload. They run at 1,000 revolutions per minute, with
a permitted variation of 2½ percent; but 1½ percent
variation is very seldom exceeded. The steam consumption
is I7 lb. per kilowatt-hour at full load and 20¼ lb. at
half load. The vacuum maintained is about 1¼ lb. per
square inch absolute. The variations in load are
naturally heavy during daytime running from about 35
percent to 175 percent of normal, and after 7 p.m. from
little over 20 percent up to 100 percent of normal. The
governor, which is of the well known oscillatory type,
is electrically controlled, and the above figures prove
that it performs its function or maintaining approximate
constancy of speed very satisfactorily.
The gust admission of steam, which
is the peculiarity of this method of governing, is
practically the only cause of noise in the Neasden
station. The bearings are continuously water cooled and
are practically without appreciable tremor, while the
pedestals are always quite cool. The level of the
lubricating oil tank gives an available oil pressure of
15 lb. per square inch but not more than 10 lb. is found
to be necessary. The oil is cooled and filtered and
returned to the overhead tank by a steam-driven pump.
The consumption of lubricating oil in the whole station
for the four turbo-generators, the exciters, alternator
for donkey work, pumps etc. is under 100 gallons per
month. From each end of the casing of the turbine, which
is 11ft. in diameter by 13ft. long, the exhaust is led
off by a 40 inch pipe, the two branches joining in one
54 inch uptake to the condenser.
The alternators are three phase,
with 11,000 volts in each phase on a non inductive load.
The normal speed of 1,000 revolutions per minute gives a
frequency of 33⅓ cycles per second, the machines being
four-poled. They were tested with 20,000 volts across
the armature for half an hour; with a 30,000 volts flash
test; and with a dead short circuit under full
excitation maintained for one minute. There are three
100 kilowatt exciters installed. A small 100 kilowatt
alternator is run to supply power to various small
motors and for lighting the station and yards.
The switchboards occupy three
galleries in the west end of the generator house. The
bus-bars are on the ground and first floors; the
three-pole high tension oil switches on the first floor;
and the master control board upon the top floor. There
are two sets of bus-bars. Each generator and its main
switch can be isolated from the bus-bars; and each
feeder can be connected to either bus-bar, or to both,
or be isolated.
The feeders are three core, paper
insulated, with a lead sheath, and steel armoured. They
are tested under water to 30,000 volts, and again to
22,000 volts after being laid in place. Four sizes are
used; of copper sections 0.1, 0.15, 0.2, and 0.25 square
inch. Three of the largest size lead to Baker Street sub
station, which is the distributing centre for the Circle
sub stations, and two each of smaller size lead from
Neasden to Harrow and Ruislip.
There are in all nine sub stations.
Most of these have in each three 800 kilowatt rotary
converters; but Charlton Street and Moorgate Street
stations have each three 1,200 kilowatt, and Baker
Street station four 1,200 kilowatt rotaries. In all
there are twenty eight sub station rotaries, of a total
normal capacity 25,200 kilowatts. These run at 375
revolutions per minute, and with 550 to 600 volts
between the outgoing terminals. Each can carry a 25
percent overload maintained for twenty four hours with
50 deg. Cent. rise of temperature, or a 50 percent
overload for one hour with 60 deg. Cent rise. Each
rotary converter is served by three static transformers
reducing from 11,000 to about 440 volts.
The conductor rails are of soft
steel of a conductivity equal to one seventh that of
copper. They are 100 lb. per yard in weight, or 10
square inches in section. They are copper-bonded, with
1½ square inch copper section. The insulators, placed
9ft. apart, are of highly vitrified porcelain, and have
plain cylindrical bodies, which are 5½ inches in
diameter by 4½ inches deep for the positive rail, and 3
inches depth with the same diameter for the negative or
return rail.
The present rolling stock comprises
twenty eight trains, each of a total weight of 180 tons
plus the passenger load, the passenger seated capacity
being 350. The motor coaches weight 40 tons and the
trailers 25 tons each. Each full train consists of two
motor coaches and four trailers.
The motors are rated at 150
horsepower, and there are four of these on each motor
coach, giving 1,200 horsepower to the full train. This
yields an acceleration of 1½ft. per second per second,
or 30 miles per hour in about half a minute. There are
in addition ten trains of a total weight 185 tons each,
the motor equipment being some. what heavier in these.
The turret controller which was at first used has been
substituted by a rectangular form, which weighs
considerably less and is also less bulky. Besides these
there are ten locomotives of 1,000 rated horsepower each
in four motors. These weigh from 45 to 50 tons, and are
capable of drawing 250 tons up a gradient of 1 in 40 at
10 miles per hour.
In November last; complete
systematic tests of the whole generating plant were
made. It is unnecessary to give here all the details of
these tests. Only the main results need be mentioned.
The boiler test lasted six hours, the gauge pressure
being 188 lb. per square inch, and the superheat 150
deg. Fah. The feed reached the economisers at 160 deg.
Fah. and left them at 253 deg. Fah. The water actually
evaporated was 3¼ Ib. per hour per square foot of
heating surface, the coal consumed being 23½ lb. per
hour per square foot grate area.
This corresponds to a steaming
power of 7.94 lb. actual superheated steam per lb. of
coal burnt. Apart from the action of the feed heater and
the economiser, which together raise the feed to 253
deg. Fah. the boiler proper and its superheater have,
therefore, an evaporative efficiency of 9.0 lb. water
from and at 212 deg. Fah. per lb. of coa1 burnt. (7 .94
x 1095.6/965.7 = 9.0). Taking the boiler along with the
feed heater and economiser, the whole plant has a
heating efficiency of 1263.6/965.7 x 7.94 = 10.4 lb.
from and at 212 deg. Fah. per lb. of coal. This means
84½ percent efficiency, since the coal used has 11.980
as its calorific value. The percentage efficiency of the
boiler and superheater separately is 73, deducting 12
percent of moisture contained in the fuel, the
consumption of dry coal per kilowatt-hour was 2.4 lb.
Considering that there was 8½ percent of ash as well as
12 percent of moisture in the fuel, these results are
very good.
The turbo alternator test was
carried out with 184½ lb. steam gauge pressure and 150
deg. Fah. superheat, the average vacuum pressure being
1¼ lb. per square inch absolute. During a six hour
full-load" run the actual variation of load was from
1,200 to 6,000 kilowatts and averaged 3,850 kilowatts.
During a subsequent two hour half load run it varied
from 800 to 3,400 kilowatts, and averaged 2,175
kilowatts. The actual steam consumption per
kilowatt-hour was 18.3 at full, and 22.2 at half power;
but with the allowance made on account of the above
large variation and for other reasons, the full load
consumption is within the guaranteed 17 lb. per
kilowatt-hour. If 85 percent be taken as the mechanical
and electrical efficiency of the combined turbine and
alternator, this figure of 17 means 14½ lb. per
kilowatt-hour, or 10.8 lb. per horsepower hour of
mechanical work done by the steam on the turbine blades.
During the test of No.4 turbine the
condensing water passed over the measuring weir was 3¼
million pounds per hour, and it was raised in
temperature from 60¾ deg. to 84¼ deg. Fah. in passing
through the condenser. This condensing water was 46½
times the weight of steam it condensed. Since 84¼ - 60¾
= 23½ and 23½ x 46½ = 1060, this last is the units of
heat extracted from each pound of exhaust steam. Adding
84 - 32 = 52 to this, we find 1,112 British thermal
units as the total heat from 32 deg. Fah. of the
condensed steam, which corresponds to slightly under l
lb, per square inch absolute pressure in dry saturated
steam. Some of the steam, however, is withdrawn by the
vacuum pumps without mixing with the above water, and it
is also not certain that the exhaust is quite dry steam.
The exhaust also loses heat, of course, from the surface
of the large 54in. uptake pipe, and these items amply
account for the difference between this 1 lb. pressure
and the actually measured l¼ lb. per square inch, the
latter corresponding to a total heat of 1,115, or an
excess of three units only above that resulting from
direct measurement. This small difference points to
great accuracy in the measurements made in these tests.
Table 1. gives a complete return of
the coal consumption and power generated and work done
for each week during the last four months of 1906. The
chief contents of this table for three months are also
given in diagram form in Figs. 1, 2, 3, and 4.
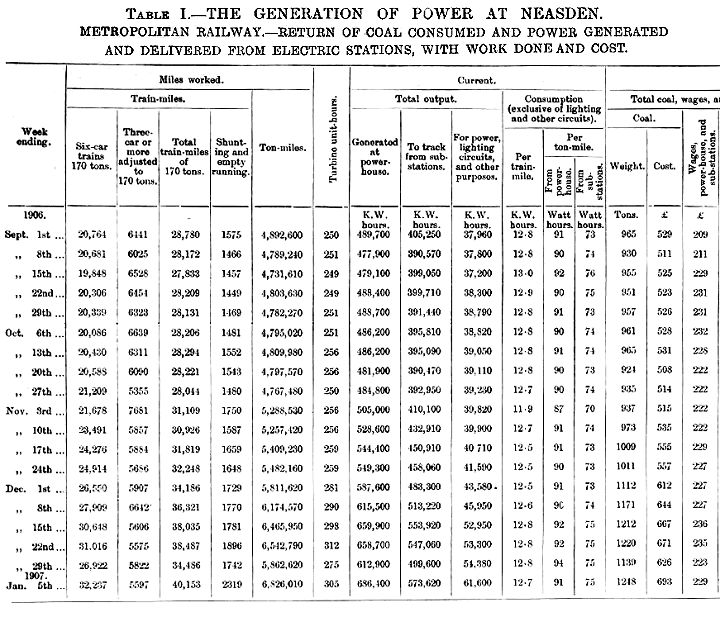
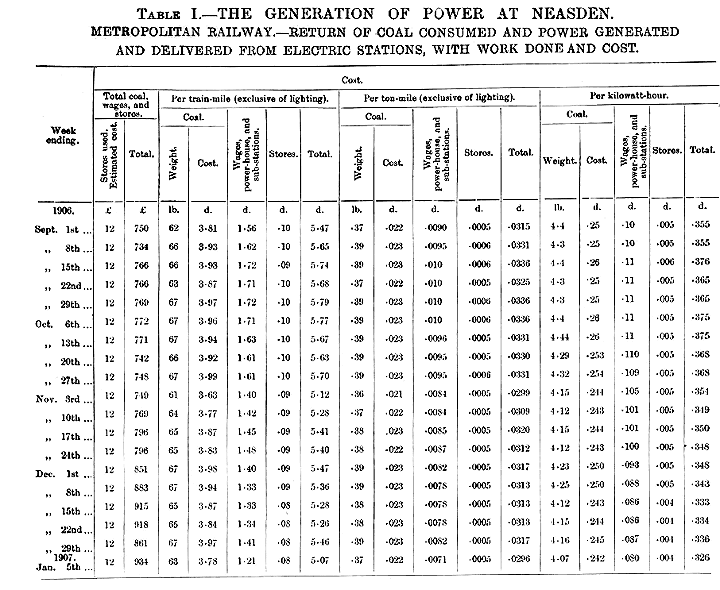
For the purpose of obtaining a
definite figure for train-miles all the trains have been
reduced to equivalent trains of 170 tons weight,
although many of the trains are three-car or ‘half’
trains, and also the real weight of a full train
approximates more nearly to l80 tons than to 170 tons.
In calculating the ton-mileage the passenger load has
been neglected. The seating capacity gives a full
passenger load of about 20 tons, and seeing that during
certain hours there is a great deal of strap-hanging, 10
tons of passengers per full train is probably an under
estimate of the average. This is 6 percent of 170 tons,
and this ought to be remembered in considering the other
figures of the table. For instance the average of the
column giving energy from sub stations per ton-mile is
74 watt-hours, but reducing this by 6 percent, the real
figure, taking into account passenger load, is only 70
watt-hours.
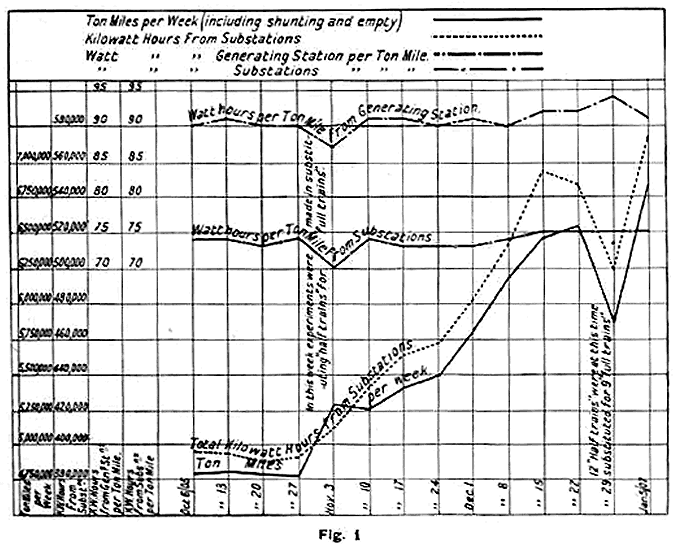
During these four
months the ton-mileage has steadily increased from under
5 to over 6½ millions. This is also shown by a diagram
line on Fig. 1. The only deviation from regularity is
the great drop in the week ending 29th December. This is
due to the withdrawal of a considerable number of ‘full’
trains, and the substitution of ‘half’ trains for them.
Experiments in this direction were made at the end of
October, and the disturbances thus caused at these two
particular periods account for the only marked
irregularities in the curves of the diagrams in Figs. 1
and 2. Fig. 2 gives the costs per ton-mile, and apart
from the above-mentioned disturbances no cost curves
could be more satisfactorily steady. Fig. 4 gives the
cost per unit generated in the power house. Here the
coal cost keeps perfectly uniform, and wages and
consequently the total costs exhibit a slow steady
decrease.
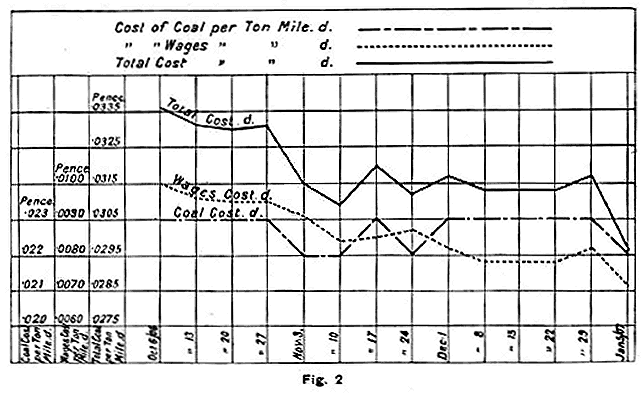
During the 24 hours there is on the
average one unit at work during 1.85 hours, two units
during 13.75 hours, and three during 5.15 hours, The
seventh column in Table 1. gives the turbine unit-hours
used per week. Near the end of the year this was about
280, or 40 per day. Averaged over the twenty-four hours,
this means 1⅔ turbines at work continuously. Averaged in
the same way, the output of each is somewhat over 2,000
kilowatts, or about 60 percent of their rated power.
This rate of generation of 280 turbine-hours per week
corresponds to about 590,000 B.T. units generated, and
to 1,100 tons of coal consumed, costing £600, or between
0.24d. and 0.25d. per B.T. unit. This coal consumption
includes all banking-up time and losses on
uneconomically small loads. The output from the sub
stations is between 82 and 83 percent of that generated.
Of this latter output between 9 and 10 percent is spent
on lighting, machine driving etc. etc. Thus about 75
percent of the power generated is used for actual
traction work upon the track. It is this last
consumption that is dealt with in columns 11 and 13,
headed ‘Consumption per train-mile and per ton-mile from
sub stations.’ Per train-mile of 170 ton trains the
average is 12,800, and per ton-mile 74, watt-hours. Per
ton-mile ⅜ lb. of coal are used, costing 0.23d. The cost
in coal consumed varies very uniformly in proportion to
the output, while the other costs in this station are
phenomenally low, being only about 0.008d. for labour,
and 0.0005d. for lubricant and stores. The total cost
thus comes to only 0.0315d. on the average per ton-mile.
Per kilowatt-hour generated the average figures are: 4¼
lb. coal, costing ¼d.; wages, 0.1d.; stores, 0.005d.;
total, .0.355d. This figure includes no depreciation or
repairs, nor does it cover interest on capital outlay.
Nevertheless, it is hardly needful to point out that it
is remarkably low, probably the lowest figure that has
yet been well authenticated.
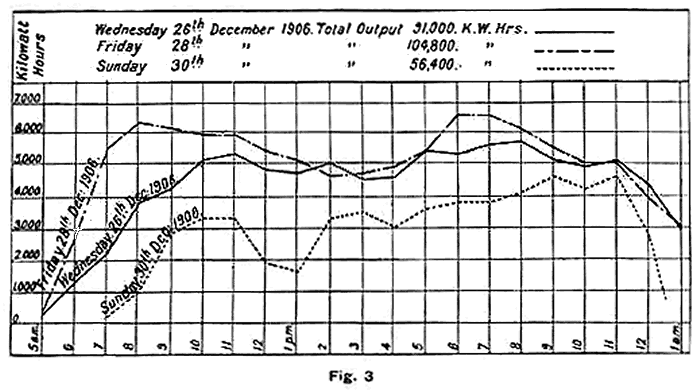
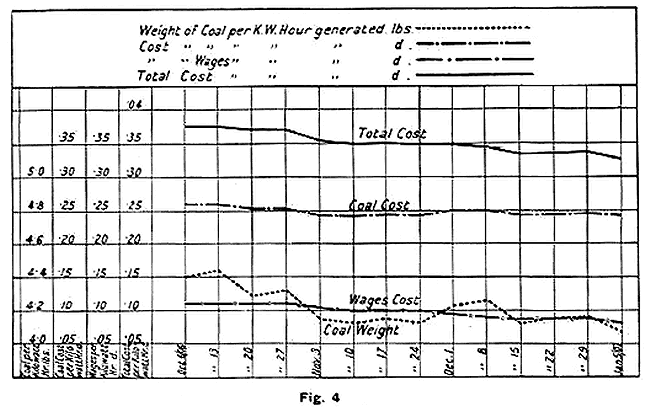
In the diagrams Figs. 1, 2, 3, and
4 the scales have been chosen very open in order to show
the variations from week to week very markedly; but
those who are accustomed to read and consider such
diagrams will recognise that the uniformity of running,
allowing, of course, for the gradual increase of work
done, has been unusual. The installation is fortunate in
the fact that the morning and evening demand peaks are
not nearly so pronounced as they are on very many
electric traction systems. This is shown in Fig. 3 which
gives the hourly output throughout three typical days.
The Metropolitan Railway is used as a means of business
communication right through all the mid-day hours. Also
for at least at night there are no passenger trains
running, and for three out of every twenty-four hours
none of the big turbo-generators are at work. The load
factor is thus high, being about 42 percent, reckoned on
the normal capacity of the four units installed.
The chief element in the economy of
this station is however, undoubtedly the completeness
and steady reliable working of the arrangements for
almost entirely automatic working. The staff works in
three shifts, and over its eight hours, each shift has a
low load factor of employment. Considering that over
half a million B.T. units are sent out on it per week,
the place has at all times a weirdly lonesome aspect.
The three shifts all told of high and low degree, number
42 persons, or 0.0030 of an individual per rated
kilowatt. The total number of stokers is 14 to take
charge of boilers whose normal duty is to evaporate and
superheat 280,000 lb. or 125 tons of water per hour.
There is a legend that on one
occasion 41 of the staff of 42 took a twenty-fours’
holiday, and that, in consequence of their taking the
precaution to chain with a sufficiently free tether the
master control switchboard man to his gallery, neither
the board of directors nor anyone else outside the staff
ever heard of the incident. The chief engineer however,
denies that there is any basis founded in truth for this
legend. He says that if it had been fact he would
certainly have heard them-through the telephone - coming
home again.
Seriously, this generating station
is an important example of the important dictum that the
best commercially economic results are obtained when
there is no excessive straining after the last possible
fraction in the percentage of physical efficiency. The
most skilful engineering is not that yielding the exact
maximum of physical efficiency, but that that gives
maximum commercial economy - reliability and freedom
from breakdown being a very influential factor in this
economy - which is always obtained at the sacrifice of
some small degree of physical efficiency. |