In 1891 Thomas became interested in a greatly
improved method of producing phosphorus, as can be seen
from the following article about phosphorus
production by electricity. This is copied from a
newspaper cutting that was in Thomas's cuttings book.
Unfortunately I don't know where the cutting came from. |
8th
June 1891
Phosphorus Making by Electricity.
In the late 19th century phosphorus
was used in several industries. It was used in matches,
in the production of saccharine, in weapons and as a
poison. It was usually produced by a labour-intensive
chemical means and so was relatively expensive to
manufacture, but this was all about to change.
Dr. Readman of Edinburgh took out a
patent for producing the substance using electricity and
his patent was bought by the E.C.C. Mr. Thomas Parker
and Mr. A. E. Robinson, F.C.S. (E.E.C.’s chemist) began
experimenting with the process and took out a patent for
a revised process, early in 1890. The resulting process
worked extremely well and the E.C.C. built a phosphorus
works at Wednesfield by the side of the Birmingham
canal, near to the railway station.
The process operated on a small scale
using several electric furnaces, which were driven by a
triple-expansion marine steam engine, delivering 700
horse power. Steam was fed from three Babcock and
Wilcock’s boilers, which were fed with heated water to
reduce the cost of producing steam. The engine drove an
alternator that was 8ft in diameter and produced 400
units of electricity. Intense heat for the furnaces was
produced by powerful carbon arcs, a technique that was
invented by Thomas Parker to produce a small and compact
design.
The furnaces were 8ft. square and
each was fitted with a hopper at the top which allowed
phosphates and coke to be poured in without any heat
vapour escaping. The furnaces were air-tight and so no
smoke was generated and the whole of the ingredients,
except for a little slag, produced the phosphorus, which
was drawn from the furnace using a tapping principle,
similar to that used in a blast furnace. The resulting
liquid was passed through pipes and condensers, where
extremely pure phosphorus was deposited. It required a
minimal amount of refining and was formed into circular
cakes.
The charge for the furnace was
carried in buckets and tipped into the hopper at the
top. It consisted of coke and an already calcined
mixture of Redonda stone and tar. Each furnace
operated from a single phase A.C. supply and was
constructed of firebricks mounted in a framework of
cast iron plates. The horizontal carbon electrodes
were 12" square and received 80KW through iron
connection forks. They were tamped everywhere with
carbon strip, ground coke and pitch.
Care had to be taken to ensure that there was
always enough material between the carbons to
maintain electrical contact. |
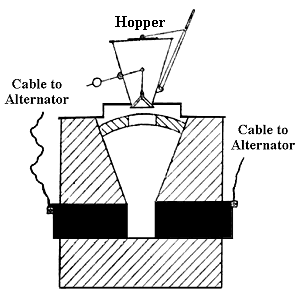
A Wednesfield furnace
|
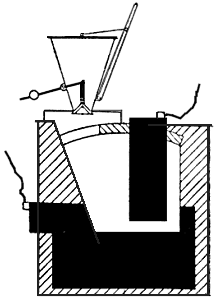
A
later type of furnace.
|
A circular furnace was also built
which performed better and was more reliable. The
firebrick hearth was replaced by a gas carbon retort
strip and it had a vertical electrode. The hopper
was moved to one side to make way for the vertical
electrode. This became the standard design and
remained unchanged for some time. |
The production costs were far less than with any
other system and the process was so successful that
after several month’s production, plans were made to
enlarge the works. The patents and the works were
acquired by the Phosphorus Company Limited and it was
hoped that they would be able to produce 1,000 tons a
year, which amounted to half the world’s production. |
|
The phosphorus furnace became known as "The Wednesfield
Furnace" and appeared in many school textbooks.
In the earlier
process, phosphorus was distilled in earthenware retorts and
handling these was extremely dangerous due to the fire hazard.
The Parker Robinson process eliminated this hazard, making the
manufacturing process much safer. The phosphorus was transported
from the works in 50lb. blocks placed in a tank of water.
The drawing opposite is from the American patent for the
furnace which was granted on 13th September, 1892. It shows a
modified, and presumably improved form of the furnace. |
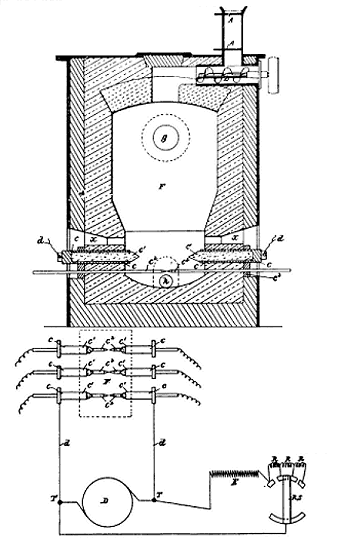 |
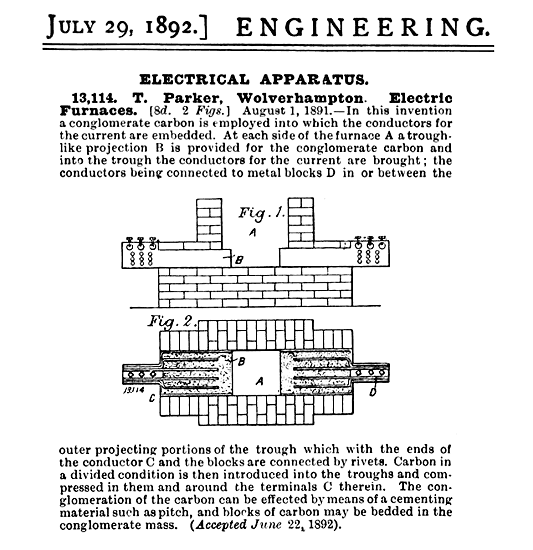 |
Details of one of Thomas Parker's
furnace patents. From
'Engineering' magazine. |
Another of Thomas's many patents, also
from 'Engineering' magazine. |
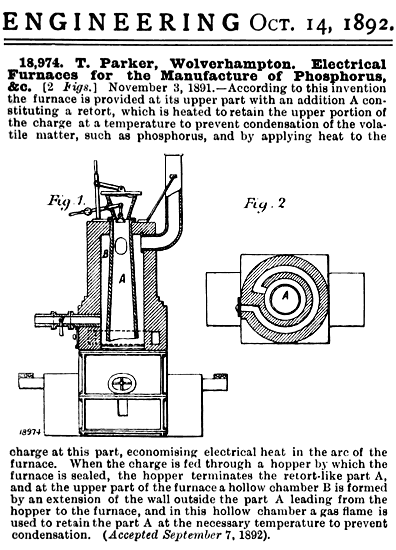 |
The patents and the factory were later sold to Albright and Wilson of Oldbury for £16,000. Certain conditions were applied to the sale
including a guaranteed consumption of not more than 8 units of
electricity for every pound of phosphorus produced, and a
minimum yield of 75 per cent. At that time the measurement of
electric current was in its infancy and so it was difficult to
verify the consumption of the furnaces. Sir Alexander Kennedy,
an eminent engineer, was appointed as assessor and he brought in
the greatest electrical engineer of the day, Lord Kelvin. The
most accurate instrument at the time for measuring electric
current was the Kelvin balance and Lord Kelvin applied this
apparatus to the task in hand.
The sale conditions were duly met
and the sale went ahead. The Wednesfield works continued in
operation for a further two years until a new factory was built
at Oldbury, which opened in 1893. After transferring production
to Oldbury, the Wednesfield factory was gradually shut down, and
soon closed.
Albright and Wilson Limited went from
strength to strength using improved versions of the Wednesfield
furnace. In the early years of the First World War the company
developed a range of munitions for the army including
phosphorus-filled shells, hand and rifle grenades, and 'Chinese
tumblers', and 'plum puddings' for trench warfare. On detonation
they liberated phosphorus which produced phosphorus pentoxide, a
non-poisonous gas that acted as an extremely efficient smoke
screen to mask the enemy's fire.
The army initially thought that
phosphorus-based munitions were far too dangerous for troops to
handle, and so little interest was shown. After much persuasion
the devices were accepted, and in a short space of time large
numbers were being produced. The other armed services also used
phosphorus devices. The Royal Navy and Mercantile Marine
frequently used phosphorus smoke screens, and the Royal Flying
Corps used wind-direction indicators called candles, which
continuously burned phosphorus. They also used 'toffee' bombs
which contained a mixture of white phosphorus and amorphous
phosphorus against Zeppelins and kite balloons.
Phosphorus for smoke screens was needed in
large quantities, which Albright and Wilson Limited could not
hope to manufacture. The furnaces were already working beyond
their safe limits producing large amounts of phosphorus for
shells. To overcome the supply problem the Trench Warfare Supply
Department under Sir Alexander Roger, decided, with Government
assistance, to build a new factory for the production of
phosphorus on the six and a half acre site at Heath Town, which
had been purchased towards the end of 1915 from Lord Barnard.
Wilson Lovatt & Company of Wolverhampton
were given the contract to build the factory, and work got
underway in January 1916. Extra plots of land covering around
six acres were also purchased, mainly from the adjacent London
and North Western Railway. The factory had twelve 500kW, single
electrode furnaces and condensers, with wooden tops that were
lifted by mechanical gear, and filters in a separate building,
similar to the ones in use at Oldbury. There were also four
resistance mud furnaces, a fitting shop, carbon shop,
electrician's shop, a time office, and a bungalow for the
foreman. Power was purchased from the Wolverhampton Electricity
Department, and production got underway in May 1917.
|
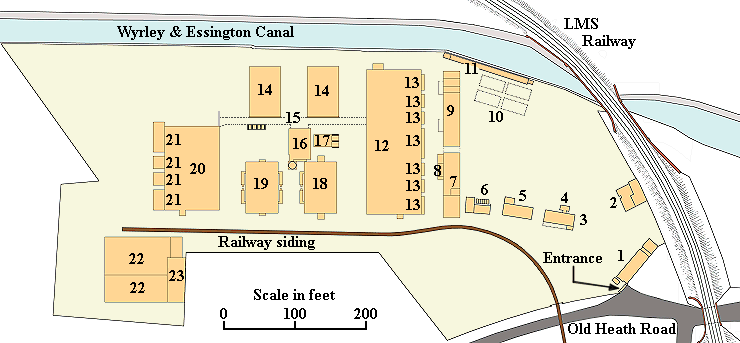
A plan of the factory based on a plan of
the works from the 1925 sales catalogue.
Ref.
number |
|
Description |
1. |
|
Offices -
single storey brick building
with four offices and a
toilet. slate roofed with
granolithic paving outside. |
2. |
|
Foreman's
bungalow - containing an
entrance hall, 2 bedrooms,
sitting room, kitchen,
pantry, outside coal place,
and paved yard. |
3. |
|
Canteen -
built of wood and galvanised
iron, with three rooms and a
toilet. |
4. |
|
Kitchen |
5. |
|
Store -
built of wood and galvanised
iron, with lean-to stable. |
6. |
|
Bath house
and toilets - brick built,
slate roof, granolithic
floor. Including 4 bath
rooms, and 6 toilets. |
7. |
|
Fitting
Shop - brick walls, Belfast
roof, granolithic floor,
divided into two sections. |
8. |
|
Test rooms
- brick built, concrete
roof, granolithic floor, and
a toilet. |
9. |
|
Mixing
house - brick built with
walls 3 feet wide at the
base, Belfast roof covered
with ruberoid, granolithic
floor, divided into 3
sections. |
10. |
|
Four
storage tanks - 3 concrete,
40 ft. by 18 ft., and 1
partly formed. |
11. |
|
Canal
loading deck - covered by a
roof, and having open sides.
The roof extends over the
canal to provide shelter
when loading or unloading. |
12. |
|
Furnace
house number 1- built
of brick up to 10 feet, with
corrugated iron above. Slate
roof, granolithic floor, and
7 concrete tanks. |
13. |
|
Transformer
house - brick built, single
storey lean-to, with slate
roof and granolithic floor. |
14. |
|
Filter
house - brick wall at each
end, open sides with brick
piers, Belfast roof,
granolithic floor, concrete
tank. |
15. |
|
Concrete
gantry - 12 feet wide,
connecting the surrounding
buildings. |
16. |
|
Boiler room
- brick built, with flue and
chimney stack. |
17. |
|
Pump house
- brick walls, Belfast roof,
concrete floor, with a well
for the water. |
18. |
|
Bleaching
house - brick wall at each
end, open sides with brick
piers, Belfast roof,
granolithic floor, concrete
tank. |
19. |
|
Mud
furnaces - brick wall at
each end, open sides with
brick piers, Belfast roof,
granolithic floor, concrete
tank, transformer houses
attached. |
20. |
|
Furnace
house number 2 - brick side
walls, one brick end wall,
one corrugated iron end
wall, slate roof,
granolithic floor, and 4
blocks of concrete tanks. |
21. |
|
Transformer
house - brick built, slate
roof, and granolithic floor. |
22. |
|
Anthracite
and chip store - brick wall,
Belfast roof, with a loading
shed. |
23. |
|
Mixing
house - brick walls, 3 feet
thick at base, Belfast roof,
concrete floor. |
|
|
During the first year of operation, a
further twelve furnaces and condensers were built, along with
filters and four more mud furnaces. A railway siding and mixing
house were added because the quantity of furnace mixture
required for the plant was too great for Oldbury to supply.
Initially it had been brought from Oldbury, shovelled out of the
boats and put on conveyors which loaded the bins above the
furnaces.
The phosphorus was moulded into 50lb.
blocks which were put into open tanks on wheels, and carried to
the Oldbury works by canal boat.
After the war had ended, and the orders for
munitions ceased, the factory was of no further use to Albright
and Wilson, and so in 1920 the plant was sold for £6,000 and
scrapped. The land and buildings remained derelict until the mid
1920s when the site was sold by order of the Surplus Stores of
the Liquidation Department of H.M. Treasury. It was put-up
for sale by public auction at the Victoria Hotel in
Wolverhampton on 22nd July, 1925. It did not sell on that
occasion but was soon acquired by Mander Brothers, along with
some adjacent land for the building of a new factory. |
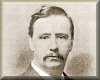 |
Return
to the
previous page |
|