In the first half of the 19th century, town gas,
initially for street lighting, was in great demand. Gas
pipes were originally hand-wrought in short lengths that
were expensive and slow to produce. This all changed
thanks to Cornelius Whitehouse, who invented a quick,
accurate and reliable method of cheaply producing tubes
that could cope with higher pressures. His work
revolutionised the tube-making industry. Widespread gas
distribution now became a practicality, but
unfortunately he received little in the way of financial
reward, for his efforts.
Luckily for us, Frederick William Hackwood, Wednesbury's
late19th century historian, wrote several articles
chronicling Whitehouse's life. This short version is
based on his article in the 1898 Ryders Annual, and his
"Wednesbury Workshops" from 1889.
Cornelius Whitehouse was born in Oldbury on 22nd July,
1795. His father Edward became an expert sword maker,
producing high quality swords at a time of high demand
during the Napoleonic Wars. One day his products were
inspected by a corrupt War Office inspector who said
they were not up to standard. Edward lost his temper
with the man and forced him to hold an approved sword at
arm's length. He then cut the sword in two with a single
blow from one of his own swords. From then on they were
Government approved.
Cornelius and his brother worked for their father in his
Birmingham workshop and became expert sword makers and
gunsmiths in their own right. Cornelius became a
recognised craftsman and was offered a job as a
Government sword inspector, but turned it down.
After the Napoleonic Wars the demand for guns and swords
fell and so the family moved to Wyrley where they worked
for Gilpin, the edge tool maker. Four years later
Cornelius moved to Wednesbury Forge to work for Edward
Elwell making edge tools.
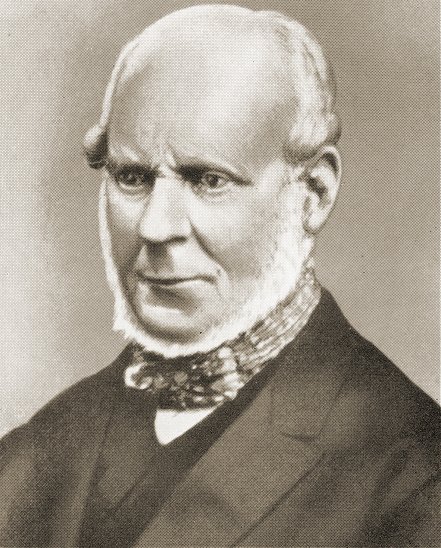
Cornelius Whitehouse.
While working at the forge his thoughts turned to tubes,
and he began experimenting with new ways of producing
them. At the time there was a great demand for gas
pipes, which were made by an expensive and labour
intensive process requiring very skilled workmen. Tubes
were formed from an iron strip, or skelp, which was
heated in small sections, a few inches at a time, in a
conventional open hearth forge. After hammering each
section into shape, each side of the seam was overlapped
and hammered to form a weld. Many heatings were required
for each length of tube which had a maximum length of 4
feet. The industry couldn’t keep up with the demand and
so there was a lot of interest in increasing
productivity and also reducing the manufacturing costs.
Cornelius's solution, developed in 1824 and 1825
consisted of heating the whole strip in one go, in a
hollow fire of the type used by the edge tool makers at
the forge. The strip was then shaped and welded in one
operation by drawing it out of the furnace by a chain
attached to a drawer bench, and passed through a pair of
semi-circular dies. The process produced an accurately
shaped tube with smooth inside and outside surfaces. It
is believed that he first offered it to Edward Elwell
who suggested that he should take it to James Russell.
With Russell's help he took out a patent for the process
which was granted on 26th February, 1825.
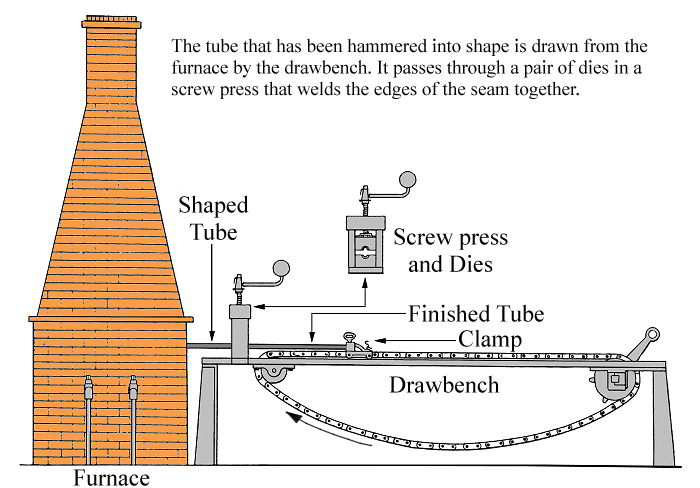
A drawing based on the 1825
patent.
Russell agreed to employ Whitehouse and pay him the sum
of £25 annually for 14 years, the life of the patent. He
soon increased the sum to £50 when Whitehouse assigned
the patent rights to him.
The new tubes were twice as long and half the price of
the older ones, and could withstand a higher pressure.
Russell built a new factory at a cost of £14,000 and
invented a way of screwing tubes together.
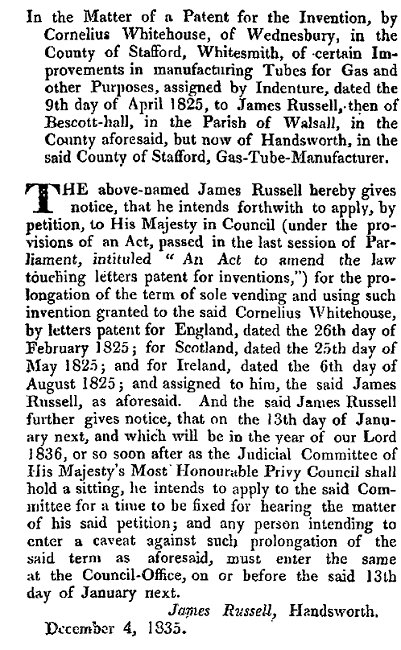
From the London
Gazette, 11th December, 1835. |
Large numbers of tubes were produced, but success came
at a price. From 1830 until 1845 Russell was constantly
in litigation with rival manufacturers who tried to
infringe his patent. By 1838 the legal expenses amounted
to approximately £4,000.
The new revolutionary process was seen as a threat by
the traditional tube makers and Russell and Whitehouse
went in fear of their lives. On one occasion Whitehouse
even shot at the legs of a gang of men who were about to
attack his house.
In 1842 he took out a patent for an improved process
with one of Russell's sons; Thomas Henry Russell.
Unfortunately Whitehouse had a disagreement with one of
the sons which resulted in him leaving the company.
From then on he entered into a number of
unsuccessful business ventures. The first,
in partnership with a Mr. Chubb was a tube
making factory at Globe Works, Wednesbury
Bridge.
In Pigot & Company's 1842 National and
Commercial Directory, Cornelius Whitehouse
is listed under gun barrel manufacturers and
gun manufacturers in the Wednesbury section. |
In 1845 he took out another patent,
this time for the construction of welding and hammering
machines for the manufacture of tubes and gun barrels.
By 1849 he was also manufacturing lathe and press tools. Unfortunately the business at Globe Works was not
successful and resulted in Whitehouse loosing much of
his capital. He then moved to Wolverhampton and went into partnership with Edwin
Dixon, who had a tube factory at Monmore Green. Although
the partnership lasted for 20 years it was not
financially successful.
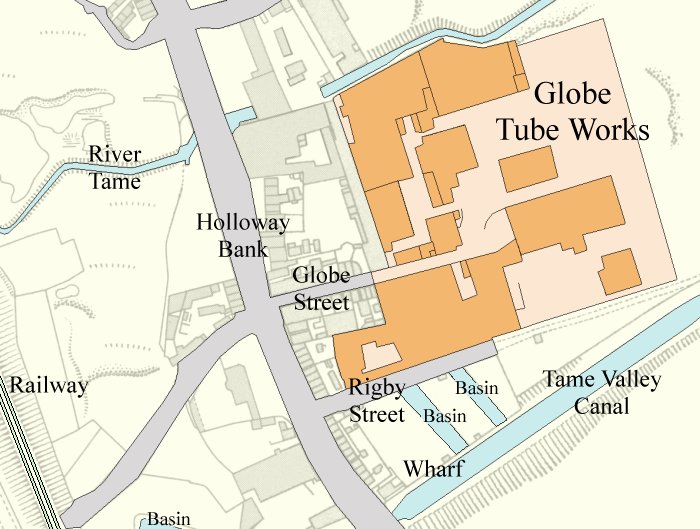
The location of Globe Tube Works.
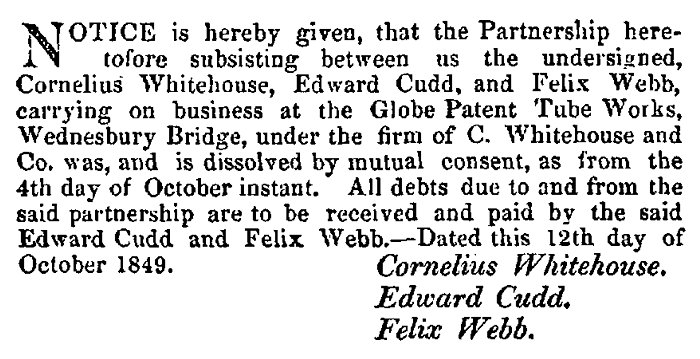
From the London Gazette, 16th
October, 1849.
Jones
Mercantile Directory
of the Iron
District, 1865:
Wednesbury
Whitehouse &
Company, gas tube
and gas fitting
manufacturers, Globe
Works. |
|
|
Cornelius continued to run Globe Tube Works until the
business closed in the depression that started in the
mid 1870s. The factory closed and was acquired by
John Spencer, who reopened it in
1882.
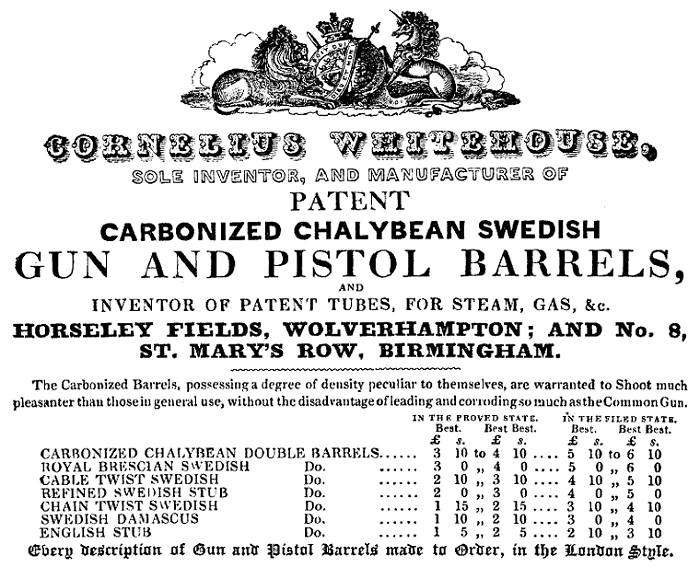
An advert from 1847.
Melville & Company's 1851 Wolverhampton Directory has
the following listing:
Cornelius Whitehouse and Company,
manufacturers of patent iron tubes for
gas, water, and steam locomotive and
marine, of any diameter or thickness,
Monmore green. Whitehouse Cornelius,
patent gas tube manufacturer, Mount
Pleasant, house Monmore Green Cottage. |
|
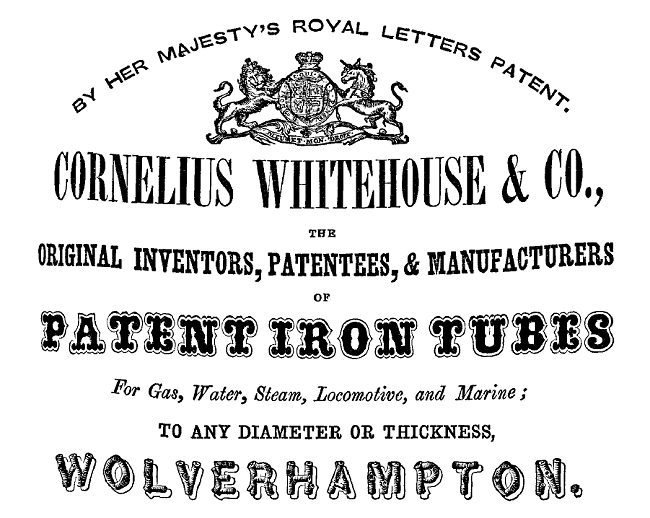
An advert from 1861.
Whitehouse's final venture, in a holloware manufacturing
business at Birmingham ended prematurely in 1863 when a
workman was crushed by a falling piston.
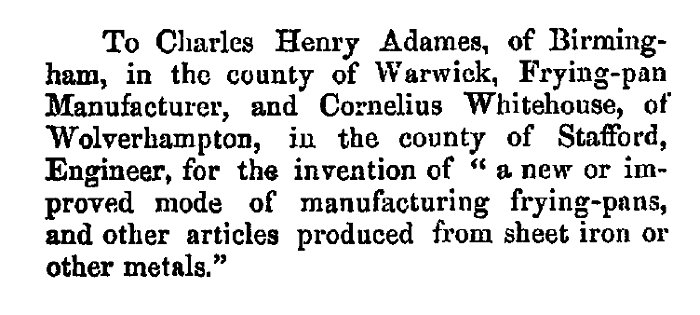
From the London Gazette, 4th
January, 1861.
Cornelius married three times, first to Mary Peters in
June 1821, who sadly died in 1822. They had a son who
died at the age of three. Cornelius married again in
January 1826, to Lucy Aston the widow of Richmond Aston
of Bescot Hall. They had a son, Edward Searl Whitehouse,
born in 1826. He became a gunmaker. Cornelius's last
marriage in 1831 was to Charlotte Powers. Their son,
Denham Whitehouse, born around 1840, is listed in the
1881 census as a window pulley maker, employing 16 men,
14 boys, 3 girls, and living with his family at 15 Great
Brickkiln Street, Wolverhampton. Their other children
were Emma Whitehouse, Charlotte Whitehouse, and
Elizabeth Whitehouse.
Cornelius died on 7th August, 1883. At the time he was
living at his son's house in Great Brickkiln Street. Two of his nephews worked in tube
manufacturing. They both worked for him at Russells and
at Monmore Green, and one of them, John Brotherton,
founded Brotherton Tubes at the Imperial Tube Works in
Wolverhampton and later became the town's mayor. The
other, Thomas Pritchard, founded the South Staffordshire
Tube Works at Wednesbury.
His obituary in The Engineer:
The Engineer. 24th
August, 1883.
Cornelius Whitehouse
Those who remember
the great patent of Russell v. Ledsam,
which for many years dragged its slow
length through the various courts up to
the House of Lords, where it was finally
decided in the year 1848, will regret to
learn that Mr. Cornelius Whitehouse, one
of the inventors whose patent was in
dispute, died on the 7th
inst. in the eighty-ninth year of his
age. The invention was of the greatest
importance, and may be said to have laid
the foundation of the welded tube trade.
Whitehouse was originally a workman in
the employ of James Russell, tube
manufacturer, of Wednesbury. As far back
as the year 1825 he took out a patent
for making tubes, according to which the
skelp, previously bent up, was heated in
a furnace, and was welded by being
drawn, without a mandril, through a pair
of semicircular dies; or through
pincers, each jaw of which had a
semicircular groove or aperture. It
created quite a revolution in the trade,
the price of tubes being reduced to
one-half and for some sorts to two
thirds, and a much longer length could
be made.
The tubes were of
greater uniformity, both internally and
externally, and the trade came very soon
almost entirely into the hands of
Russell, to whom the patent had been
assigned, the inventor receiving an
annual sum of £300, together with a
house and certain other advantages.
Ledsam, the defendant in the action, was
the assignee of a patent taken out by
the late Richard Prosser, of Birmingham,
according to which tubes were welded by
drawing them through grooved rollers.
This was decided by
the court to be an infringement of
Whitehouse’s patent, the grooved rollers
being regarded as the mechanical
equivalent of Whitehouse's die, but the
litigation which was commenced in 1830
was not totally set at rest until 1848,
long after the patent and its extension
had expired. It was extended for six
years in 1839, on condition that an
annuity of £500 should be secured to the
inventor. The defendants contended that
the Crown had no power to insert such a
proviso, and they further alleged that
the application for extension had not
been made in time, and that the annuity
had not been duly paid.
Amongst the
testimony to the great value of the
invention given before the Privy Council
was that of Perkins, the patentee of a
well known system of warming buildings,
who stated that no other tubes would
have enabled him to carry out his
invention. They would bear bending cold,
and would stand a pressure of 5,000 lb.
on the inch. Francis Bramah, son of the
great inventor, also stated that the
introduction of the improved pipe
enabled him to dispense with the very
expensive copper tubing formerly used in
connection with hydraulic presses, which
cost 10s. per foot, whilst Russell's
pipe could be obtained of sufficient
strength at 1s. 3d. per foot.
Mr. Whitehouse
commenced business on his own account at
the Globe Tube Works, Wednesbury, in
1845, which, however, he relinquished to
Mr. John Spencer last year, as we
reported at the time. He also took out
several other patents in connection with
the manufacture of lap-welded tubes, but
none of such importance as his original
invention. No one will be surprised,
though it is much to be regretted, that
in common with many other patentees, the
benefits Mr. Whitehouse conferred upon
all countries through his invention did
not leave his latter days with such
substantial means as the importance of
the industry he created ought to have
afforded him. |
|
I would like to thank
|