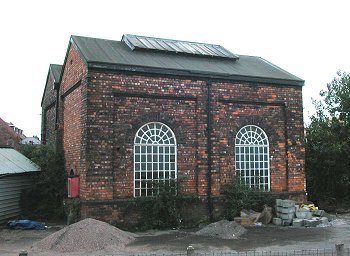
Listing: Hydraulic engine house.
C. 1890, built as part of the London and North Western Railway
Company's Wolverhampton High Level development. Flemish
Stretcher bond: double-gabled Welsh slate roof with rooflights.
Square plan, in two bays, with boiler end engine house in each
bay: hydraulic accumulator was located next to the engine house,
to the east elevation (north end), Single storey. All elevations
each have two recessed panels, the side elevations having
dog-tooth cornices in blue brick. West elevation, facing the Old
Steam Mill (Grade II), has semi-circular arches to double leaf
plank doors. North elevation has two similar arches cast-iron
multi-panelled windows, with centre hung top radial lights.
Infilled window to south elevation. Two segmental-arched
openings to former boilers in east elevation. Interior has
timber roof trusses.
History: An integral functional part of a
very fine grouping of industrial structures around Corn Hill.
The Interior housed two boilers and a cylinder steam engine, the
hydraulic power thus produced (as water pressure) powering the
cranes and ramps in the nearby Mill Street Goods Depot (listed
Grade II).
Comment: A standard London & North
Western Railway building designed at Crewe under Francis William
Webb. The L.N.W.R. were always willing to save money where
possible and self sufficiency was the byword. In the mid 19th
century bricks were often made on a building site, especially
when large buildings were under construction. In a large
enterprise like a railway new buildings were regularly required
throughout the country, all needing large numbers of bricks.
Large scale brick making began at Crewe in 1862 using clay from
the cutting between the south end of Crewe station and Whitmore.
The company had been paying 24 shillings per 1,000 for bricks
from outside suppliers whereas company-made bricks cost just
16s.2d per 1,000. The bricks were handmade and so a lot of
labour was involved.
In 1872 Webb realised that the L.N.W.R. could make
bricks more cheaply if the process was automated. At the time
Crewe works were expanding and the clay spoil from the building
site was dumped in a field where the clay sub-soil ran deep.
Webb gave his Indoor Assistant and Assistant Steel Works
Manager, John Aspinall, the task of building a 100ft diameter
Hoffman kiln with a 114ft chimney. Two Pinfold brick making
machines were driven by an old locomotive. Aspinall worked hard
on the project and in the first eleven months about 4.8 million
bricks were produced at the cost of 15 shillings per thousand.
The brick making plant cost just £5,000 and gave a saving of
1s.2d per thousand, using mass production techniques. Aspinall
described the final loading operation as follows:
Around the kiln is a line of rails, upon which
the ordinary railway trucks run, and the finished bricks are
loaded direct from the kiln into them, by two men who fill their
barrows, wheel them to the trucks, and pile the bricks carefully
inside, for 5.5 pence per thousand. One thousand bricks weigh
three tons, and considering that this weight has to be moved
twice and wheeled about fifteen yards, it is not a high rate.
Webb was so pleased with the success of the
venture that he doubled Aspinall's salary.
The multi-coloured bricks are an attractive
feature of most L.N.W.R buildings, and make them easily
recognisable. They were a common site up and down the L.N.W.R.
mainline, but most of the company's buildings are now long gone
and only two remain in Wolverhampton, this one and the adjacent Mill Street Goods Depot.
|