JEREMIAH SMITH AND SON LTD, 9 NEWBRIDGE STREET, WOLVERHAMPTON
The Memories of A.J.V. Whitehouse
Tony Whitehouse provided the following memories of this
firm in 1999. All the photos were taken in 2002. Thanks to Neil
Turner for cheerfully allowing entry to take photographs.
My mother was Mabel Helen Whitehouse, nee
Jones. Her father was Jeremiah William Jones who was the Working Director
and Manager of Jeremiah Smith & Sons circa 1920.
He lived at 9 Newbridge Street until the mid 1930s, when he
moved to a new semi detached house at Pendeford Lane, Wolverhampton. The
other directors of Jeremiah Smith & Sons Limited were Fred and Ernie Smith;
but I have no recollection of where they lived or their background.
|
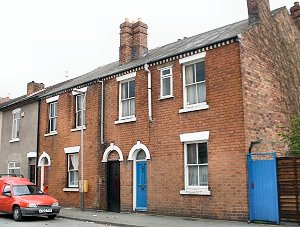 |
Numbers 9 & 10 Newbridge
Street. A pair of late 19th century houses with an access way
between them which once lead to the lockworks. |
I was born on 31 January 1925 at 87 Newbridge Street,
which is almost opposite to number 9.
Number 87 was at that time owned by J. W. Jones. We
certainly paid rent to him right up to his death during World War II, when
it was willed to my mother.
|
From an early age, once I had become
mobile, probably from 4 years onwards, I was a frequent visitor to the
lockworks and often played in the comparative safety of the yard.
Number nine itself was the home of J. W. Jones, thought eventually it
came to serve as an office building.
In the yard behind the house there were four distinct
buildings. All the buildings were of typical early/mid Victorian
industry style with arched metal framed windows.
The manufacturing
interiors were brick or earth ground floors, solid wooden stairs and
floors at first floor. There were no ceilings. All the beams and roof
structure were exposed. |
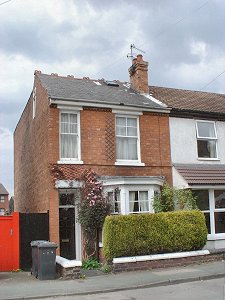
87 Newbridge Street
|
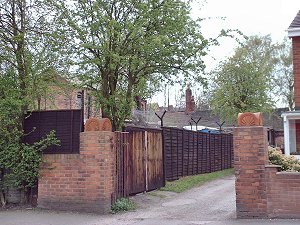 |
The works seen from
Newbridge Street. The gate piers to the right gave access to
the works but were not generally used.
Mr. Hill's house would have
been to the right of them but is has now been replaced by modern houses. |
The lockworks of Jeremiah Smith & Sons Ltd., circa 1930.
1: the warehouse, with the office at the
Newbridge Street end.
2: the main workshop,
3A: the casting shop
3B: the machine shop
3C: derelict workshop, originally
with internal stairs to the upper floor. Disused before 1925.
Demolished by 1999.
Behind No.10 is its garden. Behind that,
next to the main workshop, was the garden area for No.9. The area
between the warehouse and the derelict workshop was rough, disused
garden ground. The house on the right was that of Mr. Hill, the
Secretary. |
|
|
Detail of buildings
2, 3A and 3B above. 1: coke and
sand store
2: casting shop sand tray; there was a
plinth on the other two sides.
3: machine shop bellows forge.
4: line shafts, with drive from -
5: gas engine
6: The main workshop, of two storeys.
There were work benches round all sides of both floors, with stairs in
the centre.
|
A particular feature, which I well remember, was the
gas engine, which was a single cylinder and crank machine driven from the
town gas supply. It had a large flywheel about 6/7 ft in diameter which had
to be swung, rather like an aircraft propeller, to start the engine. There
was a pilot jet to fire the gas, which was admitted and regulated by a set
of rotating governors half linked to the output drive. When running, the
intermittent thump thump of the engine was a workday feature of the
neighbourhood. But I cannot recall anyone complaining about it. |
On the side of the crank support frame
opposite to the flywheel was the main drive pulley for the belt driven
machinery. This extended through the machine shop wall and through to
the main workshop where there were line shafts and belts everywhere.
I was never encouraged to get too near because of the particles flying
from the grinders etc. and the belts coming off.
There was also a typical bellows coke forge at one end
of the machine shop. |
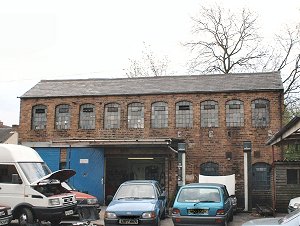
The main workshop |
Even with the machinery, files were very much a work
tool and I remember small sacks of files going out for re-cutting and into
the works as new. Where they went or came from I never knew. |
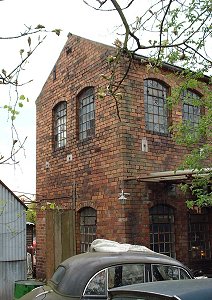
The main workshop seen from the St. Jude's
School end. |
The real place of interest was always the
casting shop, where there was a hand bellows operated coke furnace in
the corner. Brass would come in as either small ingots or scrap and be
dropped into what looked like a grey graphite crucible pot nestled into
the hot coke.
When the moulds had been prepared and all was ready,
the caster would lift out the pot of molten brass with hand tongs,
scrape off floating dross and then pour the liquid metal into three
separate holes in each mould block until they were just full, then move
on. Usually there would be four, perhaps five, mould frames.
When pouring was going on the small casting shop
filled with grey sulphurous fumes, with bits floating in the air like
snowflakes. |
The next process was to allow the brass to set and then
to break open the mould blocks to reveal the still hot and smoking raw
castings, looking rough and blackened, attached to the main mould feeds. The
useful castings, usually the lock casings, were then broken off, quenched
and sent as a batch to the workshop. |
The sand from the casting would be fine
riddled and the lumps discarded. New red sand was added to make up as
needed. The caster would then fill half of the mould block with damp
sand, level off and carefully insert the mould patterns into the sand. A
few deft taps and the patterns were removed. Filling channels were
pressed in, then the prepared mould surface was given a light dusting of
pounded up soft brick dust from a shaker bag. The mould halves were
brought together and the process repeated.
The previous mould cores were of course recycled into
the pot for re-melting.
I have no idea of the method employed to determine the
correct copper/zinc alloy proportions (should it have been deemed
necessary). |
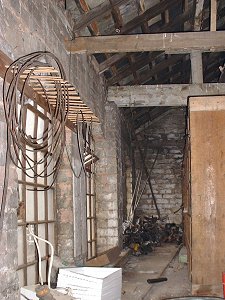
The upper floor of the main
workshop
showing the open roof.
|
In the machine shop and workshop there followed all
the drilling, filing and finishing processes which resulted in the finished
product. |
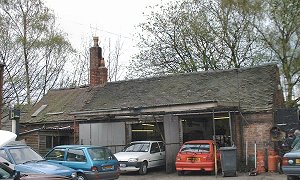
The casting shop on the left and the machine
shop on the right. The gas engine shed has been demolished. |
The lock levers were made from strip
brass, pressed out to shape using hand fly presses. The lever
combinations could be altered by using different fly press tools.
I
cannot remember seeing any of the final processes which matched the
shaped keys to the levers.
From the workshop the finished locks went
into the warehouse where they were impressed with the maker's name etc
by hand fly press, lacquered, dried and then wrapped in tissue and boxed
in cartons ready for dispatch. |
The warehouse walls were covered in a multitude of open
fronted small wood box storage compartments to act as stores for all the
various bit and pieces for manufacture and as storage for some finished
locks. |
The office area comprised of a Dickensian
long desk with a couple of tall stools and the usual record file racks.
I cannot remember any closed filing cabinets but I think there was a
small safe. During the mid 1930s the common line shaft and belt drive
machinery was replaced by individual electric motors.
Transport of materials to and from the lockworks in the 1920/1930s
was almost entirely by horse drawn, iron wheeled wagons (mostly LMS).
One dare by us lads was to creep under the horse whilst it was waiting
for the delivery driver. The horses never seemed to mind.
During this time there would have been about 30 people employed at
the works but this number gradually reduced until the works closed.
|
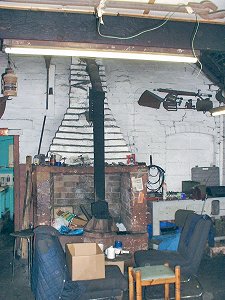
The chimney to the machine shop bellows
forge is still in place.
|
In my teenage years and later, although I continued to
live at 87 Newbridge Street until 1948 (3 1/2 years war service in Royal
Navy included), my interest in the lockworks waned, particularly after my
grandfather vacated 9 Newbridge Street. In the mid 1950s I was once asked to
represent my mother (who had shares left to her) at a shareholders meeting,
one item of which was to consider appointment of Mr Hill, the secretary who
had served Jeremiah Smith in an executive capacity for many years, to
position of Director. This was voted out.
In keeping with the tradition of the time my grandfather,
Jeremiah Smith, was also an active Methodist supporter and regularly
attended Cranmer Methodist Church, where I also attended and was married in
July 1948.
In May of 1999, out of curiosity, I visited the lockworks
site, part of which is now occupied by a car repair business. The present
occupants were very helpful. Their car repair business is on the area of the
old lockworks machine shop and ground floor of the lock workshop. The
buildings are still existing pretty much as I remember them but now seem
remarkably small compared with how I recollected them. I did not enquire
whether the old warehouse or Number 9 were still accessible.
One possibility that has occurred to me is that the works of
Jeremiah Smith & Sons probably represent the western limits of lockmaking in
the Wolverhampton/Willenhall area.
|
 |
Return to the
list of makers |
|