|
|
Read about Coal and
Ironstone Mining |
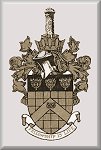 |
|
|
The
following local manufacturers are listed in
William White's 1851 ‘History, Gazetteer and
Directory of Staffordshire’:
James Bailey,
Willingsworth
William Banks.
Ettingshall
William Barrow, Quarry
Hall
Bennett & Pemberton,
Deepfield
Colbourn & Groucutt,
Bankfield
Josiah Cresswell,
Woodsetton
Haines Brothers, Willingsworth
Round Daniel George,
Daisy bank
Samuel Smith. Rookery
Hall
Joseph and Thomas
Turley, Coseley Furnaces
Henry Bickerston
Whitehouse, Wallbrook
Philip Williams and
Sons, Wednesbury Oak
Ironfounders:
David Green, Coseley
Foundry
James Johnson, Broad
Lane
Edward Sheldon |
|
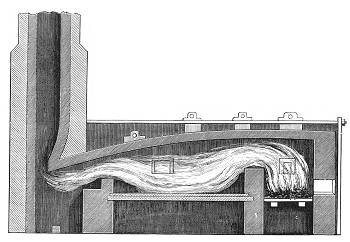
A section
through a puddling furnace. |
The most common method
of producing wrought iron from pig iron in
the 19th century was puddling, invented by
Henry Cort in 1784. Pig iron or scrap cast
iron was melted in a puddling furnace and
stirred with a long pole, which reduced the
carbon content by bringing it into contact
with air, in which it burned. The puddling
furnace heated the iron by reflecting the
exhaust gases from the fire down onto it. In the drawing
opposite, the iron would be placed in the
central section. Because it was not in
contact with the fire, cheaper, poor quality
fuel could be used. After puddling, the iron
was hammered and rolled to remove the slag. |
The large furnaces at
Willingsworth, operated by the Willingsworth
Iron Company Limited, were founded in 1827 by the
Yates Family. The firm was later run by Sir
Horace St. Paul, and then the Willingsworth
Iron Company. The principal partner was
David Kenrick, of Wolverhampton. In 1902 the
firm was incorporated into the newly formed
Metropolitan Amalgamated Railway Carriage
and Wagon Company, which in 1912 became the
Metropolitan Carriage, Wagon and Finance
Company Limited. In 1939, the ironworks was
absorbed into the Patent Shaft and Axletree
Company of Wednesbury, then liquidated.
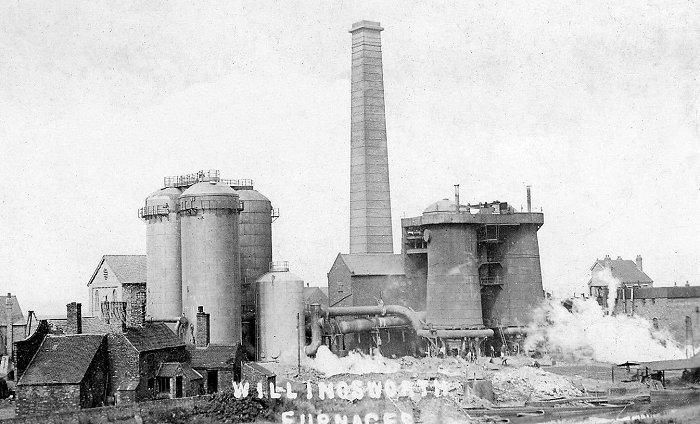
Willingsworth
Ironworks. From an old postcard.
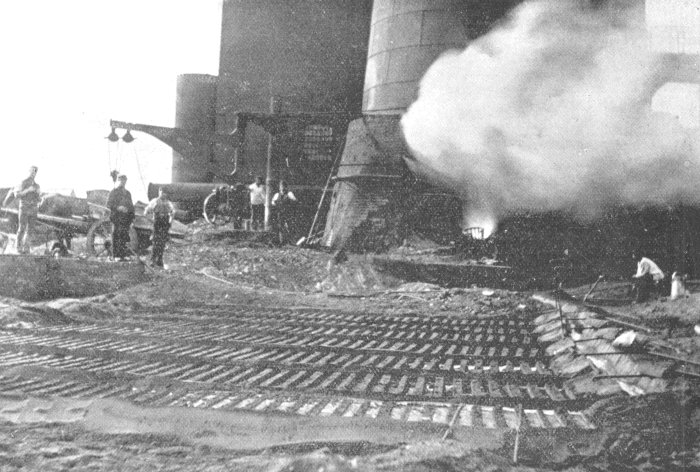
Tapping
one of the furnaces at
Willingsworth Ironworks. The
molten iron was run into
channels cut into sand to
produce iron ingots. This was
known as a pig bed. The iron was
called pig iron because during
casting, the ingots were likened
to a piglet suckling milk from a
sow. |
Next to the ironworks
were large slag heaps and spoil heaps from
the adjoining Willingsworth Colliery. The
slag heap was known as ‘Elephant Rock’
because the end that faced the nearby G.W.R.
mainline was shaped a little like an
elephant’s head. The other large spoil heap
was known as ‘Tiger Rock’ because of the
different colours in the layers that it was
made of. The heaps were destroyed by
blasting in the 1980s and a housing estate
was built on the site.
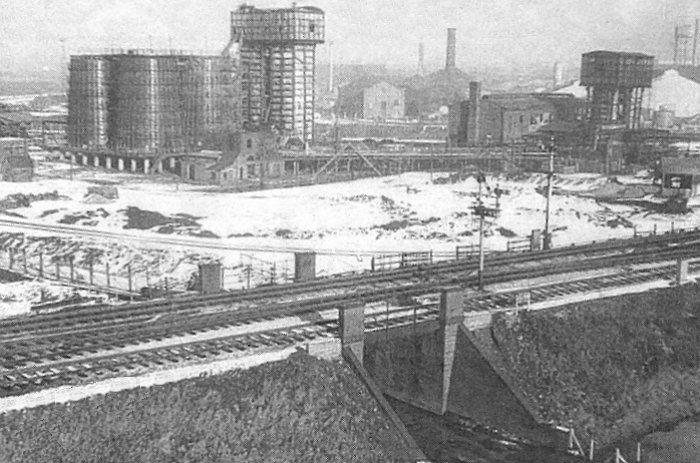
The view
from the top of 'Elephant Rock',
looking across the Great Western
Railway line, where the Midland
Metro now runs, towards Chance
and Hunt's acid works. |
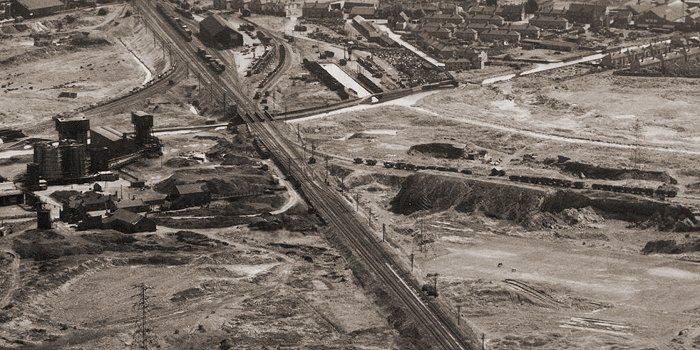
An aerial view of
Chance and Hunt's acid works with 'Elephant
Rock' to the right.
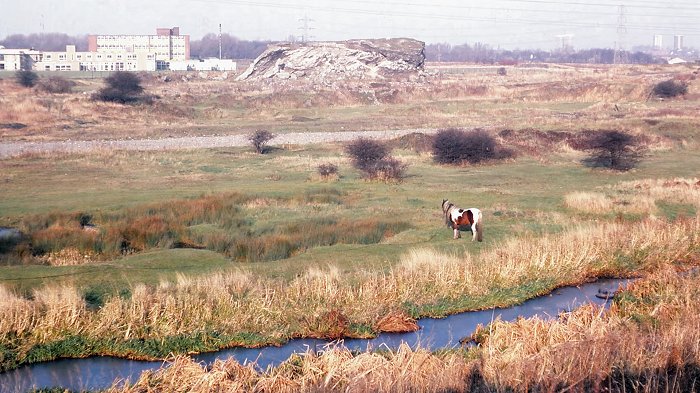
Tiger Rock.
Another early industry
was nail making. At the Coppice, many
nailers' cottages were built, along with a
nail warehouse. The nail makers relied on
the ironmonger, the middle-man who supplied
them with bundles of iron rods, weighing
some fifty or sixty pounds each. He then
purchased the finished nails from them,
often for tokens instead of cash. The
nailers mainly worked in outbuildings next
to their cottages and were self-employed,
usually working long hours for little
reward. The whole family, husband, wife and
children could be producing nails. They were
totally dependant upon the ironmaster who
gave them work when it suited him, and could
also delay payment for finished nails until
he saw fit.
The nailers were
amongst the poorer members of society, often
with an irregular income, working extremely
hard for many hours at a time, before being
idle until more work came along. The
industry rapidly declined in the nineteenth
century when machine-made nails began to be
produced in the Black Country, from about
1830.
Steel pen nibs were
another early product being produced both in
Coseley and in Sedgley. Each town lays claim
to have been the first in England to
manufacture pen nibs. Thomas Sheldon, a
forerunner of the Sheldons who later owned
the Cannon Iron Foundries at Coseley, was
making them for Mr. Daniel Fellows of
Sedgley, as early as 1806. They were sold by Beilby and Knott, a Birmingham firm of
stationers, until about 1828.
Local industries
flourished because of improved transport
facilities. The local canals made a great
difference, as did better roads, thanks to
the turnpike trusts. The local railways
which came along in the 1850s allowed goods
to be rapidly transported over much greater
distances, all of which led to the opening
of many factories and workshops. Deepfields
was ideally situated to take advantage of
the new transport facilities. The canal, the
railway, and turnpiked roads were close at
hand, which led to the opening of furnaces,
iron foundries, brick yards and collieries
in the near vicinity. One such firm, Edward
Sheldon and Company, would later become
Cannon Iron Foundries Limited, and Priorfield
Furnaces, built for H. B. Whitehouse, which would
become one of the largest of their kind in
this part of the country. Henry Bickerton
Whitehouse was a well-known local ironmaster
who was later joined in the business by his
son, Benjamin. Samuel Griffiths, in his
'Guide to the Iron Trade of Great Britain'
published in 1873, had this to say about the
firm:
At Deepfields they
have facilities for
making sheets and
boiler plates equal
to any other works
in the
neighbourhood. The
quality of the
plates here is good,
the sheets are well
annealed, and the
shears being of the
most modern type.
Plates and sheets
are turned out at
Deepfields, not only
of good quality, but
in a clean and
handsome condition.
|
|
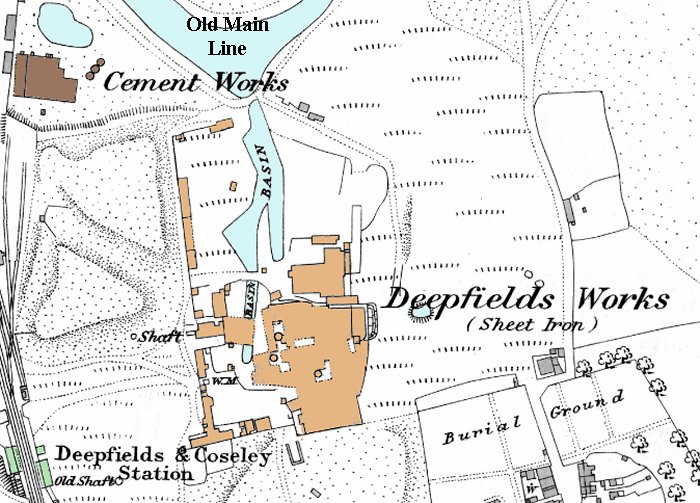
Wednesbury Oak
Ironworks to the north of Wednesbury Oak
Road were built in 1820 and operated for 100
years. The firm was called Philip Williams &
Sons, whose 'Mitre Brand' of best quality
iron had a high reputation throughout the
world.
In 1833 there were at
least 20 screw makers and screw forgers in
Upper Ettingshall and wood screw makers,
including Enoch Allen, Simeon Allen, William
Saunders and Bennett Waterhouse. Fire iron
manufacturers established themselves in
Coseley and Woodsetton including the
Wolverston brothers and Stephen Hipkins of
Princes End.
A firm of whitesmiths was founded in
Woodsetton and locks were made locally by
William Bowyer, William Lowe, and John
Newton. There were at least five
wheelwrights: T. R. Bennett, George Church,
Joseph Cooper, John Peacock, and Edward
Weaver.
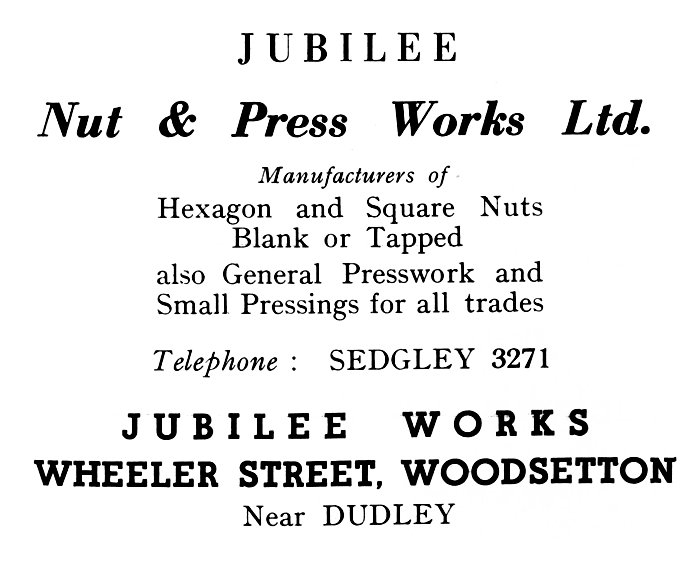
An advert from 1965.
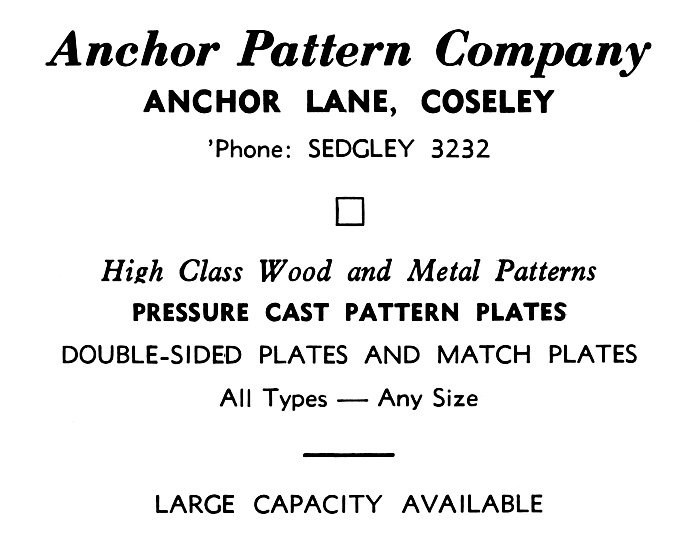
An advert from 1965.
The local clay deposits
led to the formation of brick and tile
making works. Brick makers in the 1850s
included James Bates, Edward Cartwright,
George Church, Job Elwell, and Benjamin
Gibbons. Some brick makers, including Thomas
Hinton, Benjamin Johnson, John Mellard, and
William Waterfield produced
fire-bricks. Many of the bricks and tiles
were used to line some of the Staffordshire canals.
Much of the locally
quarried limestone was used to produce lime
fertiliser. Lime burners included Joseph
Baker, Thomas Baker, John Ellis, James
Johnson, and Wade Smith. Quarry owners
included John Parker and Samuel Saunders.
In the 1850s there were
still many farms. Farmers included William
Ashcroft, Thomas Barrs, John and Joseph
Beddard, Samuel Brown, John and Benjamin
Caswell, William Clarke, James Deeley,
Samuel Finch, Abel and William Fletcher,
John Gibbons, John Hodson, John Jukes,
Thomas King, Prudence Law, Benjamin Marsh,
William Perry, William Reade, Thomas Rhodes,
John Ritson, Henry Smith, Isaac Thompson,
and Mrs. Titley.
There must have been a
great contrast between the farms and the
heavily industrialised areas, which were
like almost any other Black Country town.
There were many spoil heaps, some emitting
smoke from hot furnace droppings, which
competed with an overall pall of smoke from
the many chimneys and furnaces. Much like
the saying about the Black Country; ‘Black
by day and red by night’.
This is what the Vicar
of Coseley, the Rev. William Ford Vance, had
to say on his arrival here in 1850:
Black, in truth, it
now is, alike in its appearance, and in the
character of a large section of its
inhabitants. Black in its rugged and dreary
aspect, diversified with heaps of molten ore
and smouldering dross, and with those dark
piles of brickwork ever emitting smoke or
flame - black in regard to the minerals
extracted from its caverns - black from the
dense clouds of sooty vapour which blight
its vegetation, and shroud its sky with a
funereal pall - black with dilapidated and ruined habitations,
strewn in all directions, like the ravages
of a general earthquake or volcano eruption,
but many of which, melancholy to reflect,
are yet tenanted by whole families of human
beings - black as to the unwashed and
dejected faces of those miserable drudges,
who seem to have toiled all their lives in
dirt and darkness.
He also stated that in
Coseley alone, there were over 800 widows
and orphans; their state due solely to fatal
accidents in the mines or the factories.
|
|
Many of the locals were
paid, or partly paid with tokens, which had
to be exchanged for goods, often overpriced,
in the so called Tommy shops, as part of the
notorious truck system, which exploited much
of the workforce. The invidious practice was
not outlawed until Parliament passed the
Truck Act 1831, which made the practice
illegal in many trades, followed by the
Truck Act 1887, which outlawed it
completely.
|