The Early Years
Alfred Owen was passionate about anything mechanical, and
always kept an eye open for new possibilities and products,
especially items that were not produced in any quantity
elsewhere. In the late years of the nineteenth century, a
revolution in transport in the form of the motor car was
just starting. |
Within a few years the early prototypes had evolved
into useable and reliable machines. As more manufacturers
appeared, it became certain that the new form of transport would
soon dominate the roads. Alfred Owen realised what the future
had in store, and decided that the firm should get
involved in the transport revolution as a parts supplier
to the many up and coming vehicle builders. In the
factory yard he made a prototype chassis framework from
rolled channel and tubing, which greatly interested the
growing motor trade.
The vehicle chassis began to sell,
and the list of customers grew. Alfred could often be
seen at the bench, with sleeves rolled-up, helping to
put the finishing touches to urgently needed frame
assemblies. He was delighted with the idea that his Darlaston-made chassis would be
travelling up and down the country in all kinds of vehicles.
He was an early motorist himself, and was the first man
to drive a car into Aberdovey,
North Wales.
Other than the early factory building and the partly
covered yard, there was a small two-roomed office where
the partners did their clerical work. |
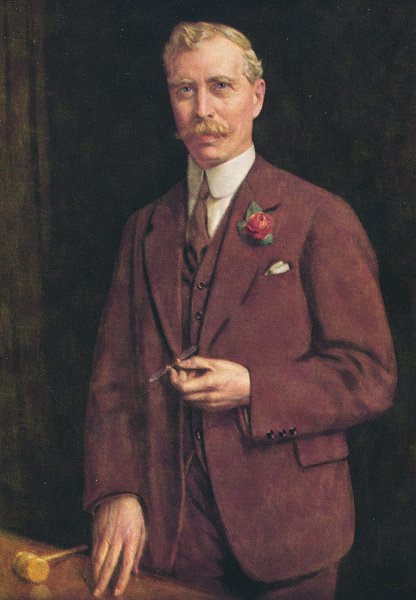
Alfred Ernest Owen. (1869 to 1929) |
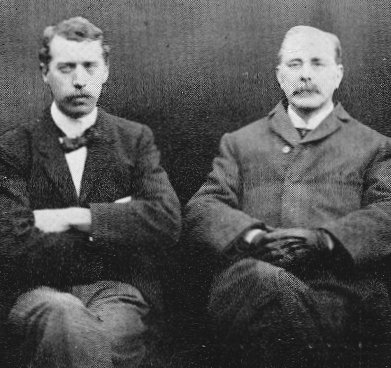
Mr. A. E. Owen (left) and Mr, J.
T. Rubery in 1899. From the April 1947 edition of the
staff magazine "Goodwill". |
They were assisted
in the office by three employees. The first, Charles Guy, the
firm’s draughtsman, also produced the technical specifications.
The second, John Jeavons, the cashier, also helped with the
bookwork and general routine. The third member of the office
staff, young George Buckley, was an eager office junior. At
the side of the factory was a large pool, said to be at
least twenty five feet deep. It occasionally rose
and fell as if it had a tidal system of its own. The extent of
rising and falling was registered by an upright piece of
tee-iron at the water's edge, with markers at every foot. In
warm weather some of the employees would cool-off by taking a
swim. There were many fish including perch, two fine preserved
specimens of which, could be seen for many years in one of the
firm’s offices in Booth Street. |
Hard factory work, particularly in the
summer, would bring-on a great thirst, so workers often flocked
to one of the many public houses in the area. Sometimes workers
would be late returning from their lunch break, so someone had
to be sent out from the factory to order them back to work.
This task was occasionally performed by Alfred Owen himself, who on
discovering the culprits, simply took out his watch, and gave
them a time limit to empty their tankards and get back to work.
The factory had its own guard dog in the
form of Leo, Mr. Rubery’s mastiff. In work hours it resided in a
large cage by the factory entrance, but at night it lay in a
sheltered spot in the yard, ready to pounce at the faintest
sound.
In 1899,
Rubery and Co. were awarded a Gold Medal at the
Richmond Exhibition for a chassis frame assembled from rolled
sections and solid round steel bars.
|
On 27th June, 1900, Alfred Owen married
Miss Florence Lucy Beech, and they moved into their first home at
Bescot. In August the employees celebrated the event with a
Saturday trip to Codsall Wood, travelling the eight or so miles
on horse-brakes. The celebration, including dinner, was held in
a large tent. Mr. Rubery toasted the newlyweds, and the
afternoon was spent in a series of games and races organised by
the more athletic members of the party. |

Mr. & Mrs. Alfred Owen. From the
summer 1954 edition of the staff magazine "Goodwill". |
Alfred Owen was an excellent salesman and
company ambassador. He often visited manufacturers to offer them
his company’s services, and gained an excellent reputation by
scrupulously fulfilling their orders. He realised that motorcar
production would become a national industry and so pursued his
ideas on improving the manufacture of chassis frames. In 1902 he
installed a hydraulic press to produce the first pressed steel
chassis made in this country, and two years later new workshops
were built to house the Motor Frame Department, under the
management of Mr. Albert F. Wilkes. In the same year the Fencing
Department opened.
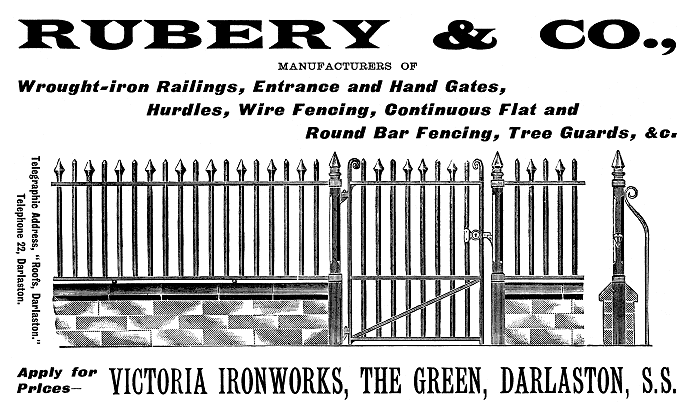
An advert from 1905, just before the name
change.
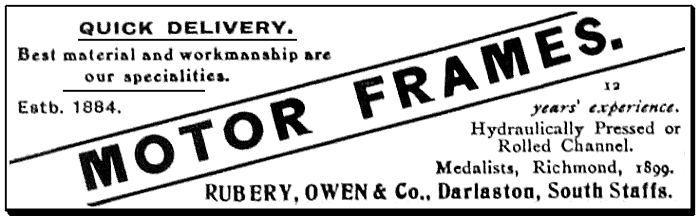
An advert from 1908.
Alfred Owen was far more active in
the business than his partner. He clearly felt it was
time to renegotiate the terms of the deed of
partnership, and so talks between the two partners began
on the matter in 1903. After two years an agreement was
reached, and on 7th September, 1905 a new deed of
partnership was signed, and the firm changed its name to Rubery,
Owen & Company. In 1910, John Tunner Rubery, who was getting-on in
years decided to retire. He had no son to follow him
into the business, and so he resigned from the
partnership and sold his interest in the company to his
partner. It took Alfred Owen five years to pay what he
owed. John Tunner Rubery died in Walsall in 1920.
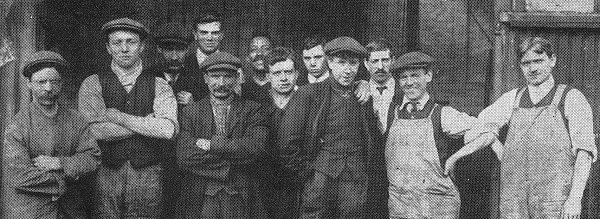
Some employees in 1910. From the
spring 1948 edition of the staff magazine "Goodwill".
Alfred soon began to expand the
business and extend the product range. Because he saw an
increasing demand for bright bolts and nuts, and turned parts
for vehicle manufacturers, he added new machinery and plant for
their production, and employed both male and female workers in
the new section. |
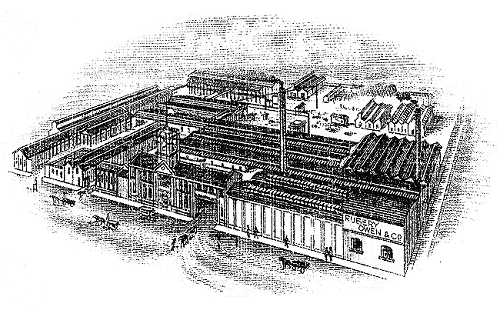
The early factory. From a 1914
letterhead. |
He also foresaw the development and growth of
the aeroplane, and so opened an Aviation Department to supply
manufacturers with parts. By 1911 the firm had issued a
small catalogue of metal aircraft components. In 1910 the product range included
structural steelwork, motor car and aircraft components,
pressings and fabrications, agricultural products, propane gas
cylinders, and nuts and bolts. |
Many of the larger machines at Victoria
Ironworks were made by a local Darlaston firm, Wilkins and
Mitchell. Alfred Owen was a friend of Walter Wilkins, the clever
engineer who designed the Wilkins and Mitchell machines. |
|
|
Read about slightly unusual
Rubery Owen products from 1911, for water treatment. |
 |
|
|
In 1911 Walter and Alfred conceived the
idea of a massive forming press to cold press vehicle chassis
frames, so revolutionising production. Chassis frames were made
from around 10 gauge steel, and until that time had been pressed
hot. Although several similar presses were in use in the U.S.A.
nothing on this scale had been attempted here. The 1,500 ton "upstroking"
hydraulically operated press, costing £2,000, was installed at
Rubery Owen’s Darlaston factory in August 1913 and became an
immediate success. It worked so well that it continued in
operation until 1970, and can be seen today in the car park at
the Black Country Living Museum. Plant was also installed for
the production of larger vehicle chassis, and for components
such as brake drums and rear axle casings.
In 1912 the success of the huge press, and the close
relationship between Walter Wilkins and Alfred Owen led them to
go on a fact finding tour of the U.S.A. to explore the latest
developments in machine tools. Walter had always been impressed
with American engineering and their seven week tour would
provide plentiful opportunities to examine the latest machines.
It nearly ended in disaster because they
booked their passage on a brand new luxury ship, RMS Titanic,
but luckily last minute business commitments forced them to
delay their departure. Had they not done so, the history of
manufacturing in Darlaston would have been very different, with
the possible loss of two of the town’s most important
manufacturers.
|
Thanks to the delay, they sailed on RMS
Lusitania and after arriving safely, visited many of the leading
American machine tool manufacturers. They also inspected some of
the factories belonging to the largest vehicle manufacturers
including Ford, General Motors, and Studebaker.
As a result of
their successful tour, Alfred Owen conceived the idea of
producing vehicle chassis and other motor components for British
vehicle manufacturers at highly competitive prices. Similarly
Wilkins and Mitchell would go on to build competitively priced,
state of the art machines for the same manufacturers. |
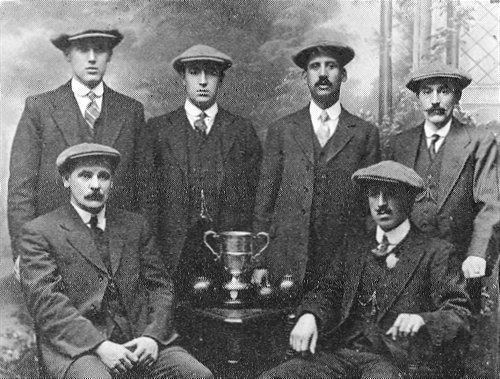
One of the works bowling teams in
1915 with the A. E. Owen Bowling Cup. From the spring 1950
edition of the staff magazine "Goodwill". |
By 1912 there were five departments, each
treated as a separate profit centre:
Aviation, which included the
production of straining screws, eyebolts, clamps, bolts and
nuts, and engine housings.
Engineering where excavating machinery, steam and
electrically powered navvies, and conveyors were made.
Fencing, for fences, gates, railings, balustrades, signs,
etc.
Motor
Frames which produced chassis and pressed steel parts for
motor cars.
Roofing where steel roofs, railway station buildings,
railway bridges, aeroplane sheds, and buildings for all kinds of
industrial uses were produced.
The business had greatly expanded since the
early days, and so Alfred Owen now had to manage the business as
a whole, rather than look after the day-to-day management of the
individual departments. He also had his other business interests
to consider, having invested in other companies. He set-up a
staff council consisting of the various departmental heads, with
himself as Chairman. The members were:
Charles Guy (Roofing), Henry
S. Price (Engineering), William Slater (Fencing),
William S. Stambridge appointed in October 1913
(Aviation), and Albert Wilkes (Motor Frames). |
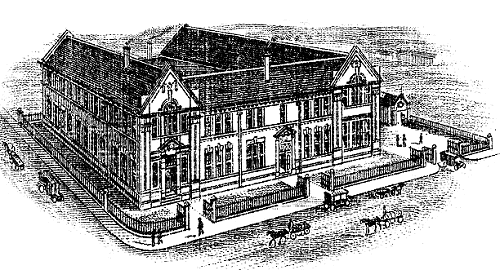
The new offices. From a 1914
letterhead. |
Also in 1912, new offices were opened, with a
canteen and Works Institute, and also a new factory entrance,
complete with clock tower.
A recreation ground also opened on
a nearby piece of land, with bowling greens and tennis
courts to provide relaxation and
enjoyment for the workers at midday or in the evening. |
The
institute included a billiards room, a reading room and a
concert room, which were greatly appreciated by the employees.
By 1914 the firm's main products
were:
Structural steelwork,
bridges, buildings, roofs, tanks, girders, etc. |
Excavating and conveying machinery,
steam and electrically driven navvies. |
Water purification plants,
bacterial treatment for town supplies, filtration and softening
for industrial purposes. |
Electric steel castings. |
Fencing and gates
(ornamental and plain),
tree guards, garden seats, etc. |
Black washers and light presswork. |
Motor car and wagon frames
(hydraulically pressed and rolled channel),
hydraulically pressed axle casings,
brake drums, clutch drums, etc. |
Aeroplane framework,
engine housings, cold drawn steel tubing, tighteners, eye bolts,
and all accessories. |
During the First World War
manufacturers were required to concentrate on the war
effort by fulfilling ministry contracts. Rubery Owen was
in a unique position, being the only firm capable of
producing large quantities of small aircraft parts for the Government.
|
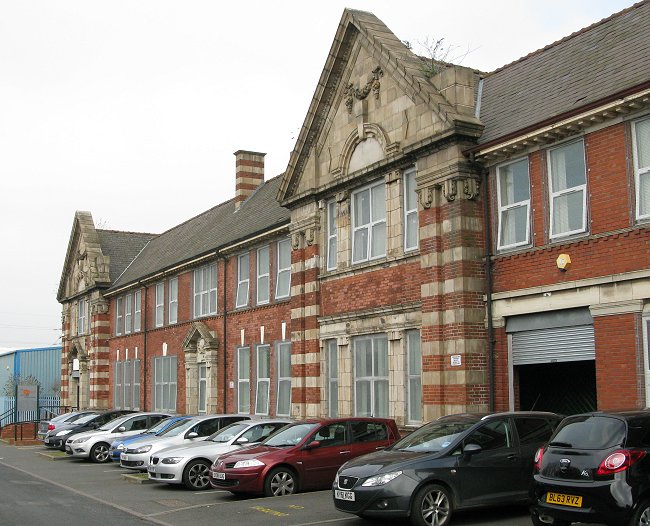
The Rubery Owen office building in 2014.
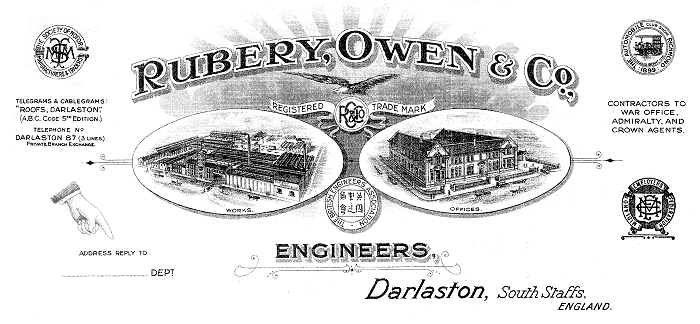
A letterhead from 1914.
At the end of hostilities, the wartime ministry
contracts were terminated and the factory returned to
normality. In April 1919 the staff council, which was
set up seven years earlier became the Committee of
Management. In the same year the firm built a very large
steam excavator, designed by A. R. Grossmith for J. B.
Forder & Son's Pillange Brickworks, and the Engineering
Department was sold to the Wellman, Smith, Owen
Engineering Corporation. On Saturday 16th August, 1919 a
new Canteen and Works Institute opened on part of the
original recreation ground. |
 |
|
 |
Return to
the contents |
|
Proceed to
Expansion |
|