Expansion Several important changes
took place in 1920. The Fencing Department closed, and
the Metal Aircraft Department was formed. At the same
time the Roofing Department became the Structural
Department, and on April 14th the name Rubery, Owen &
Company Limited was registered. The company was
registered at the suggestion of the Midland Bank and
Alfred Owen's accountant, in order to look after his
investments, the assets of which would be transferred to
the new company. By that time he had invested in the
Darlaston & District Housing Association, Chains Limited
at Moxley, Nuts & Bolts (Darlaston) Limited, A. G.
Sutherland Limited in Birmingham, and Rogers & Jackson
of Wrexham.
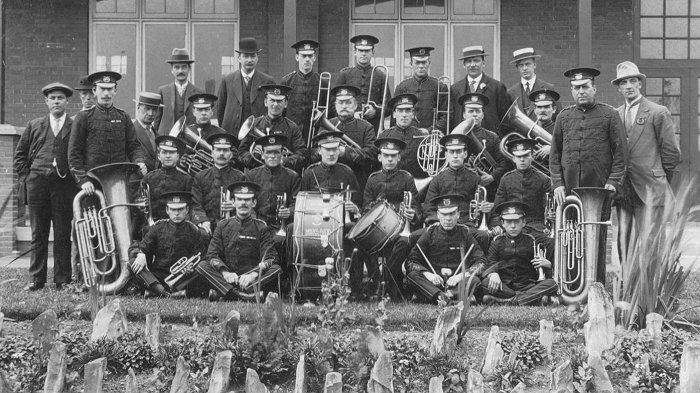
The company's brass band, the
Victoria Brass Band. From an old postcard.
The 1920s were a time of ups and downs. The post-war
recession in the early 1920s caused severe financial
problems in a rapidly declining market. There were
difficulties in reducing costs in order the keep the
firm competitive. The departmental managers were not
able to achieve the necessary cost reductions, and so
drastic action was necessary. In 1923 all factory
employees were given a week's notice, and only essential
staff were re-employed, at rates of pay the firm could afford.
This was organised by the Company Secretary, George
Buckley, who ran the Central Office, and the Accountant,
Charles Partridge who was in charge of the Financial
Department. In order to carry out their task they were
appointed as Joint General Managers. |
The product range was extended to include the
manufacture of metal aircraft propellers, pressed steel
shafting pulleys, for overhead line shafting, and the
opening the Motor Wheel Department to produce vast
numbers of disc and wire wheels. In 1923 Alfred Owen
bought New Hall Manor in Sutton Coldfield as his family
home. The house, claimed to be one of the oldest
inhabited moated houses in the country, had a sizeable
estate, which was run by his wife Florence.
In the next year, Alfred underwent an operation for an
internal complaint from which he had suffered for
sometime. During his absence the firm was ably managed
by the Joint General Managers, George Buckley and
Charles Partridge, both long serving employees. The
operation was a great success and he resumed to his
labours with renewed vigour.
By the late 1920s the business had fully recovered
from the recession and the future looked bright.
Unfortunately, in November 1929, Alfred Owen suffered a
recurrence of his illness, from which he never
recovered. He sadly died on 29th December, 1929, in his
sixtieth year, and was buried at Sutton Coldfield
Cemetery. |
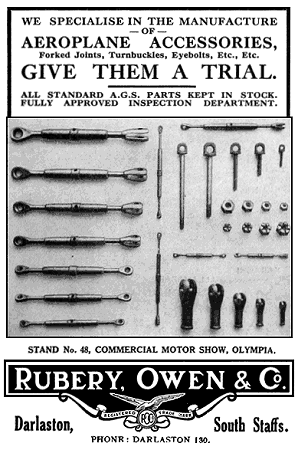
An advert from 1927. |
It was now time for his two sons to take over. His
eldest son, Alfred George Beech Owen, a 21 years old
engineering student at Emmanuel College, Cambridge took
over the business on 2nd January, 1930. At the time the
firm had 1,600 employees. In 1934 A. G. B.
Owen and his younger brother, Ernest William Beech Owen
became joint managing directors.
The Structural Steel
Department |
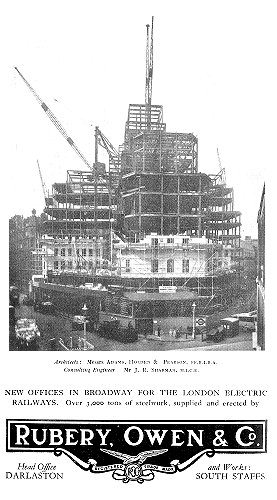
An advert
from 1930. Courtesy of Mike Ashworth. |
In the 1930s the Structural Department provided the
structural steel for a number of stands for some of the
country's leading football teams including Derby County,
Manchester United, Millwall, Twickenham, and
Wolverhampton Wanderers.
Steel structures were designed and made for
all types of single and multi-storey buildings, and erected by Rubery Owen in conjunction with the customer's architect or
civil engineer.
The firm’s structural department was responsible
for a number of well-known buildings such as the London
Passenger Transport Offices at Westminster (the tallest building
in London at the time); the Palace Court Hotel, Bournemouth; Rootes
Securities building; Speke aircraft factory; the Castle
Bromwich aircraft works; Tube Investments factory;
British Celanese factory; the Austin factory; and the
Bush Radio factory.
Local structures include the
steel frame for Wolverhampton's Civic Hall, and Birmingham
Tramways and Omnibus Department's bus garage. Many
steel structures were built during the Second World War,
including shadow factories, aircraft hangars, and store
depots, which were built to the requirements of the War
Office, while during the months previous to the Second
Front, contracts for Bailey bridges, frigate components,
tank landing craft, lock gates for Flanders canals,
steel lifeboats, and components for Mulberry Harbours
were carried out in strict secrecy. |
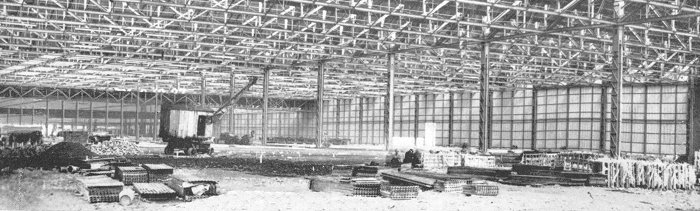
An inside view of a large aircraft
factory built by Rubery Owen in the late 1930s, which
used over 12,000 tons of steelwork. |
In 1945 Hudson Brown Limited in Oldbury, became part
of the Owen Organisation. The company, which had been
founded in 1937, manufactured structural steelwork, and
carried out the same kind of work as the structural
steel department. They became part of the department,
and produced steelwork for garage buildings, bridges, and
specialised plant equipment. |
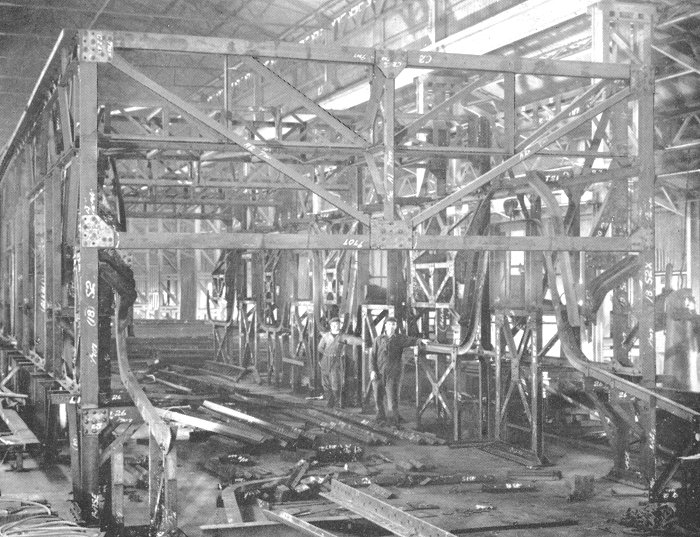
A view inside the Hudson Brown
factory, showing the construction of structural steelwork
for a roto-dip plant that was built for Volvo, and
exported to the Volvo factory in Sweden. |
Assembling the steelwork was
both a difficult and dangerous job.
In the 1950s there were no
helmets, harnesses, or safety ropes available. |
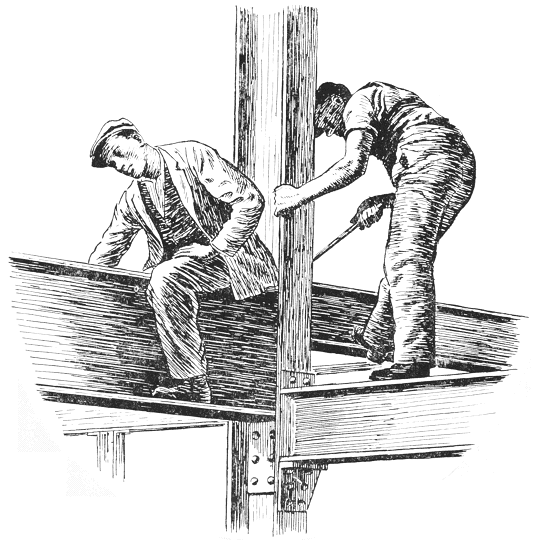 |
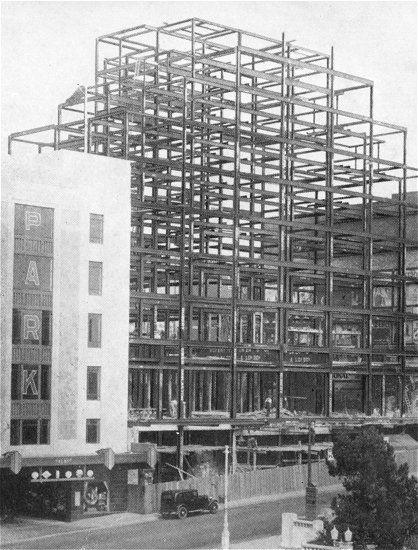
A modern hotel at Bournemouth. |
Some of the many other welded structures
fabricated at the Darlaston factory included single and
multi-storey buildings of all kinds, such as hotels,
cinemas, hospitals, banks, blocks of flats, offices,
complete factory buildings, warehouses, power stations,
bus depots, garages, and bridges.
Members of the design staff also
operated in London, Birmingham, Coventry and
Southampton, to assist architects, engineers, municipal
authorities and other clients.
|
The headquarters of the London
Passenger Transport Board, over St. James's Park
Underground Station. It has changed little today.
At the time, the 14 story building
was the tallest building in London.
Over 3,000 tons of structural
steelwork were used in the construction of the building. |
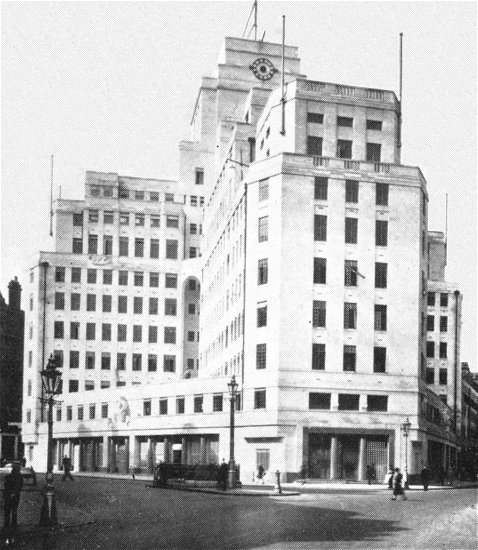 |
After the war, houses were in short supply, and local
authorities had to start vast council house building
programs to meet the demand. The Structural Department
produced a range of pre-fabricated houses to be
sold to local authorities. They were designed by A. T. &
Bertram Butler of Wolverhampton. |
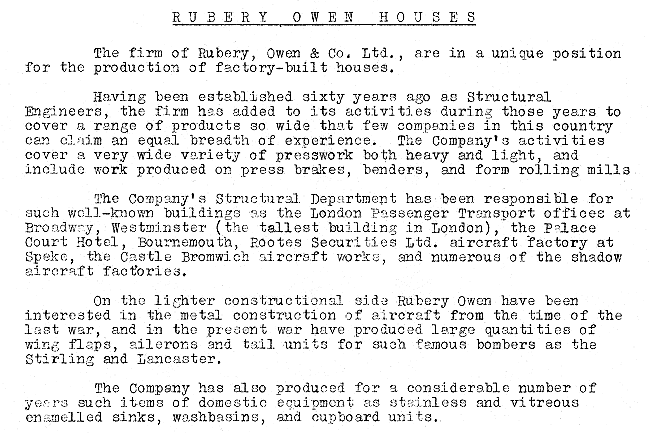
The first page of the Rubery Owen
catalogue.
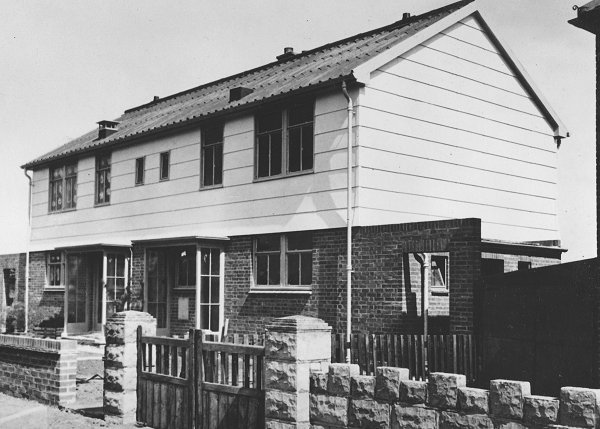
A Rubery Owen house. From the firm's
catalogue.
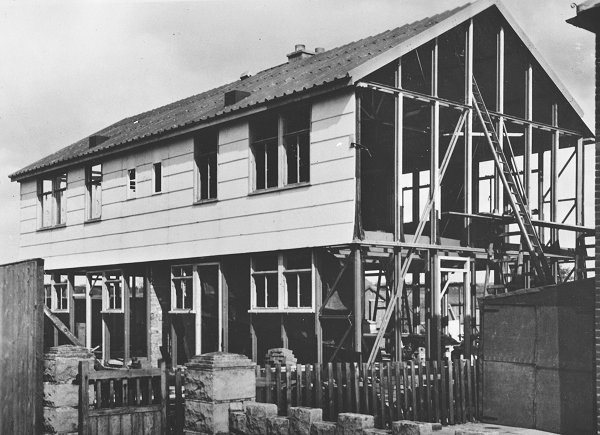
The same house under construction. From
the firm's catalogue.
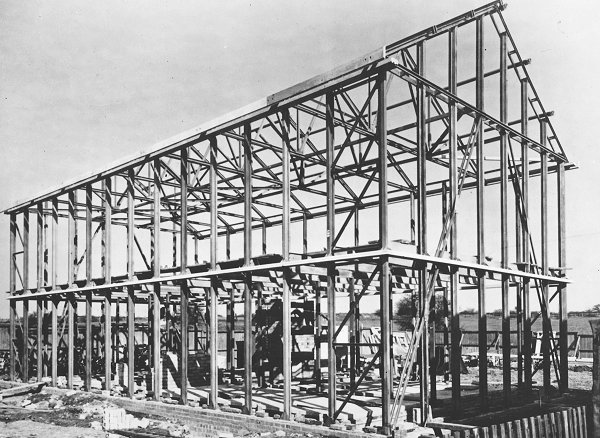
The steel framework. From the firm's
catalogue.
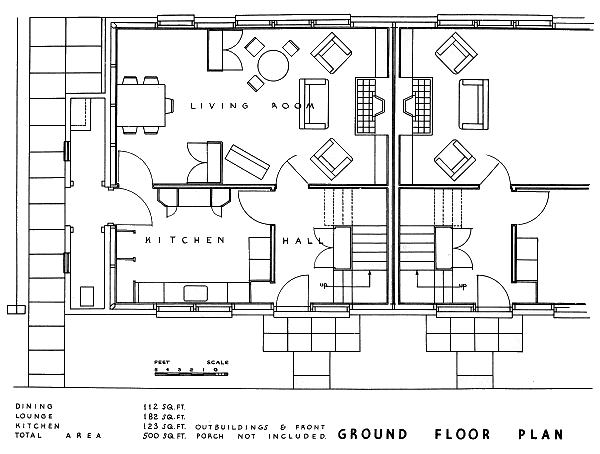
From the firm's catalogue.
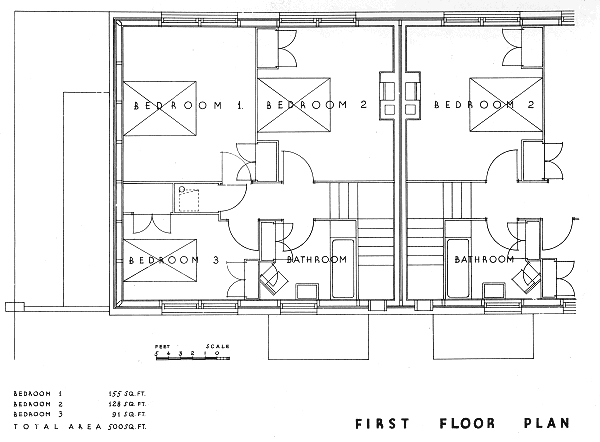
From the firm's catalogue.
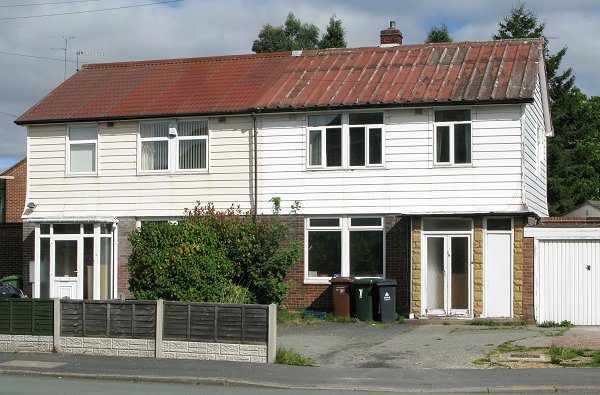
A Rubery Owen house today.
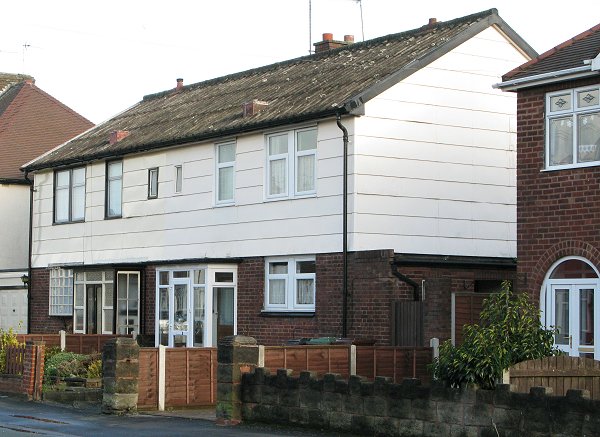
Another Rubery Owen house.
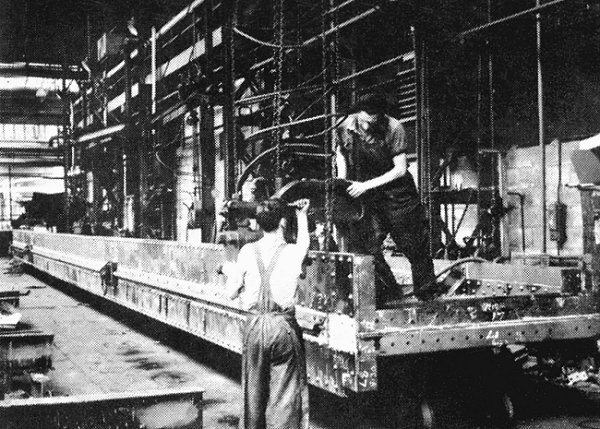 |
Working on an 84 ft. long
steel girder in the Structural Department in the 1950s.
Courtesy of Christine and John Ashmore. |
A. G. B. Owen was as
much a businessman as his late father, and soon plans
were made to expand production. In 1932 he opened the
Metal Storage Equipment Department. In 1937, as war with Germany
seemed more likely, and rearmament began, he opened the
Armour Plate Department, to produce armour plate
assemblies for tanks and gun turrets, and also the Metal
Aircraft Department in 1939 to produce parts for air
frames. The Metal
Aircraft Department
Metal components of all kinds were produced in
the Metal Aircraft Department. Initially aircraft
propellers were made, but the project range eventually
expanded to parts for the company's vast range of
products. During the Second World War, special petrol
containers known as 'Jerricans' were produced along with
steel helmets, smoke containers, ballistic caps,
incendiaries, mortar shells, anti-tank ammunition, and
shell carriers. |
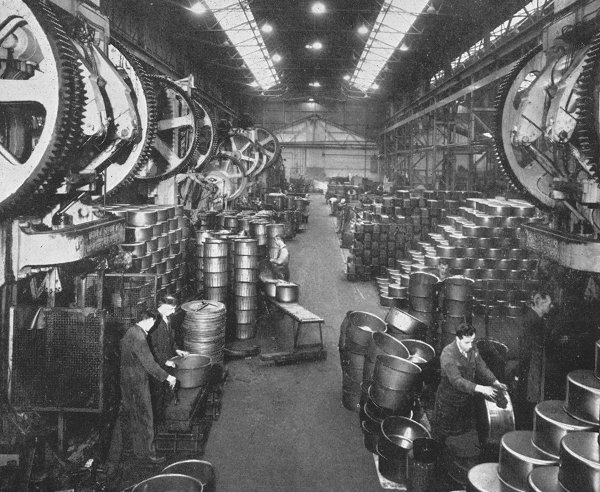 |
One of the large press shops
in the Metal Aircraft Department. |
Stove enamelling fluorescent
light fittings. |
 |
In 1946 the Metal
Aircraft Department became the Metal Assemblies
Department and used its deep-drawn presswork for a
variety of products, including brake drums, engine sumps,
valve covers, sheet metal products in aluminium, dural,
alclad and stainless steel, and an extensive range of
components for domestic appliances, cookers and
refrigerators.
Other products
included sink units, washbasins and flushing cisterns,
all produced in enamelled steel in one of the finest
vitreous enamelling plants in the country. Sinks,
washbowls, milk churns and dairy equipment were also
made from stainless steel, and thousands of fluorescent
lighting units were made to customers' designs. The
department also made propane and butane gas cylinders
for the petroleum industry, at a branch factory in West
Bromwich. |
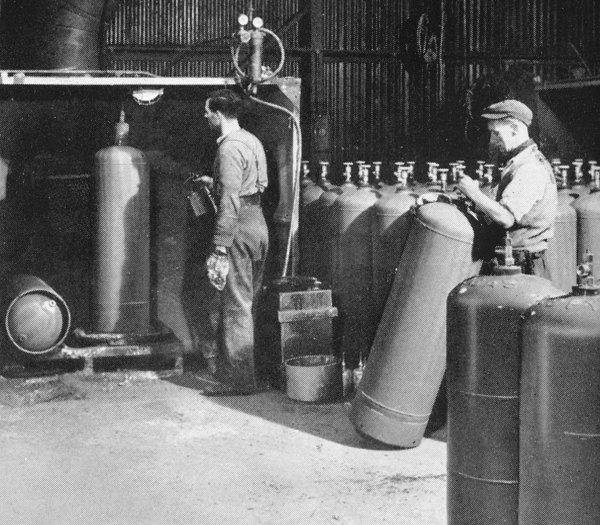 |
Producing large industrial
propane and butane gas cylinders. |
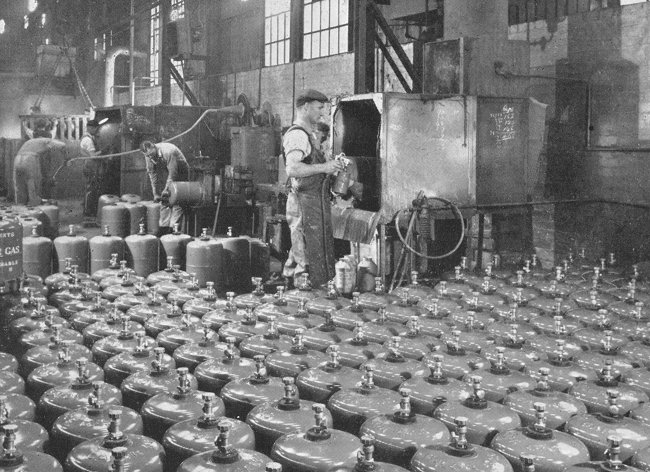
Producing smaller domestic propane
and butane gas cylinders. |
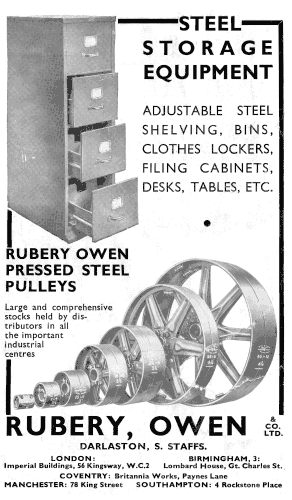 |
|
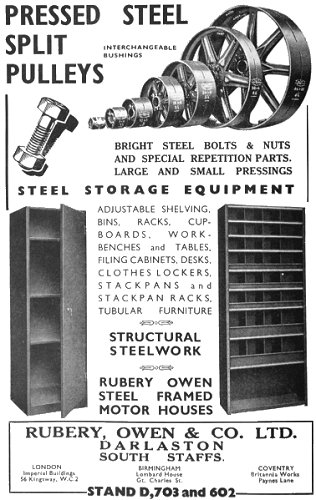 |
Two
adverts from 1938. |
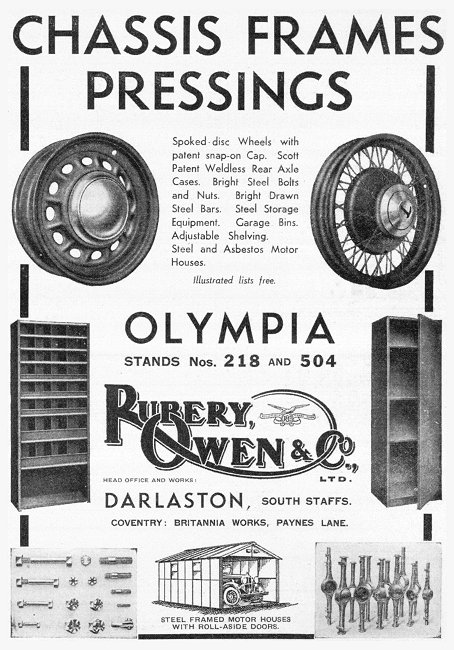
An advert from
1936. |
In 1938 A. G. B. Owen became Chairman, and acquired Easiclene Porcelain-Enamel (1938)
Limited, which had been in liquidation, and also opened
a Cooker Department in Coventry. In the
following year Rubery, Owen & Company Limited obtained
control of Aviation Engineering (Messier) Company
Limited at Warrington where the undercarriages for the
Handley Page Halifax Bomber were made. Its name was
changed to Rubery Owen Messier Limited on 17th July,
1939.
During World War II the company turned out all kinds
of products to assist in the war effort, including wing
flaps, ailerons and tail units for Lancaster bombers,
parts for the De Havilland Mosquito, aircraft propeller
hubs, aircraft wings, lifeboats, sea mines, bombs,
armoured car bodies, Bofors guns and howitzers, Bailey
bridges, 'jerricans', and even large quantities of steel
helmets. |
|
In January 1943, the Duke and
Duchess of Gloucester paid a visit to the Darlaston
factory, as did Sir Stafford Cripps, Minister of
Aircraft Production, in February, 1944.
In order to fulfil orders for the Admiralty,
the Warrington company's engineering department was
turned into a separate company. By the end of the war
the firm employed around 16,000 people and the future
for peacetime products looked extremely bright.
The Motor Frame
Department Since its opening in 1904, the Motor
Frame Department became one of the company's most
important sections, providing the county's ever
expanding motor industry with pressed steel chassis, and
pressed automotive parts. During the Second World War,
the department produced a wide range of components for
military vehicles, carriages for 2 to 25 pounder guns,
carriages for 4.5 to 95 mm guns, Bofors gun platforms,
armoured car turrets, Bailey Bridge parts, ammunition
boxes, searchlight gear track units, and sand channels,
all for the Ministry of Supply. The department also
supplied the Admiralty with mines, powder cases, and
projectiles; and the Ministry of Aircraft Production
with storage racks, universal jacking trestles, bomb
trolleys, and 250 lb. bombs. After the war, pressed
steel chassis were produced in many forms, for cars,
light commercial vehicles, and buses. They could be up
to 36 feet in length. Another product was 'Scott' patent
rear axle casings for light commercial vehicles and
cars. Hundreds of thousands of them were produced
directly from steel tube, on special hydraulic machines,
so that they were entirely weldless. |
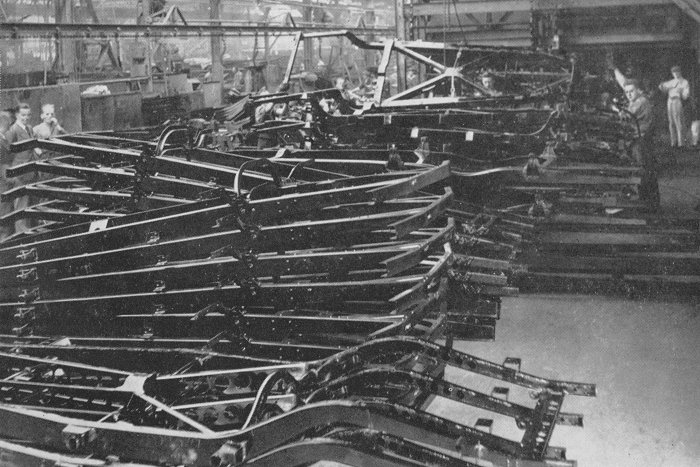
Completed chassis frames. |
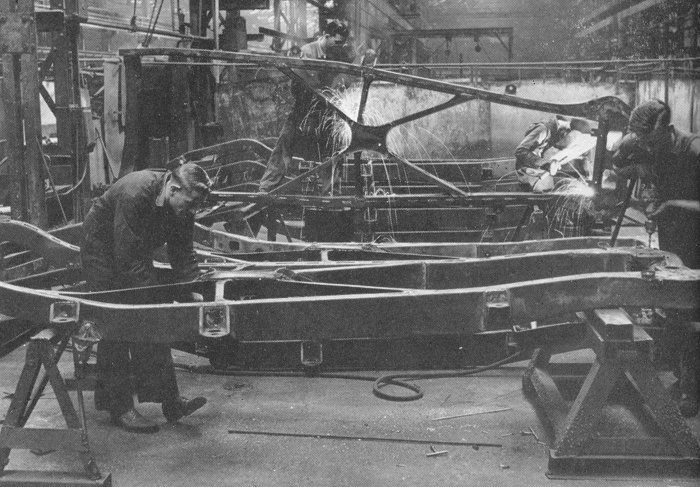
Building chassis frames in one of
the large erecting shops. |
The department had two large press shops, one for
cold pressings up to ¼ inch
thick, and one for hot pressings up to ⅝ inch thick.
Both press shops had a range of presses from 30 to 2,000
tons, and produced products for the automotive and
general engineering industries, as well as complete
fabrications, and large deep drawn pressings. |
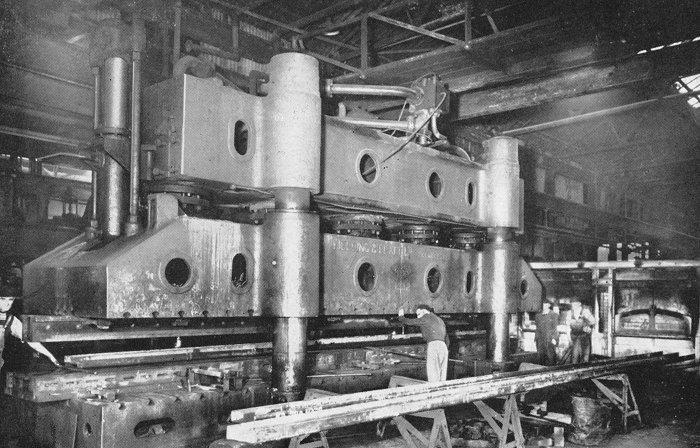
A hydraulic press, turning out
parts of bus and lorry chassis. |
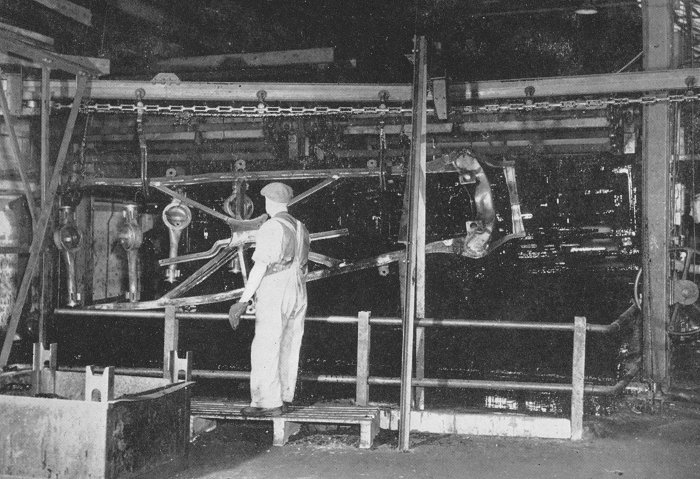
Dipping chassis frames as part
of the enamelling process. |
The department's toolroom was one of the largest
in the Midlands. It produced all of the large press
tools and jigs for the press shops, which were
designed in-house. There was also a motor repair
section in Meeting Street, Wednesbury, which undertook repairs to
chassis and rear axle casings. It catered for local
garages and service stations. |
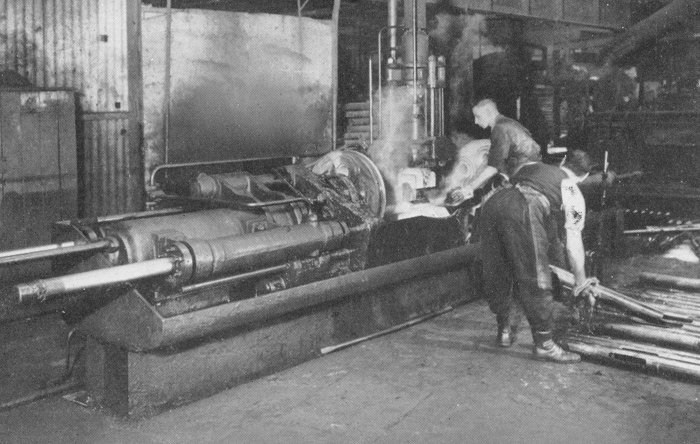
Making 'Scott' rear axle
casings on one of the special hydraulic machines. |
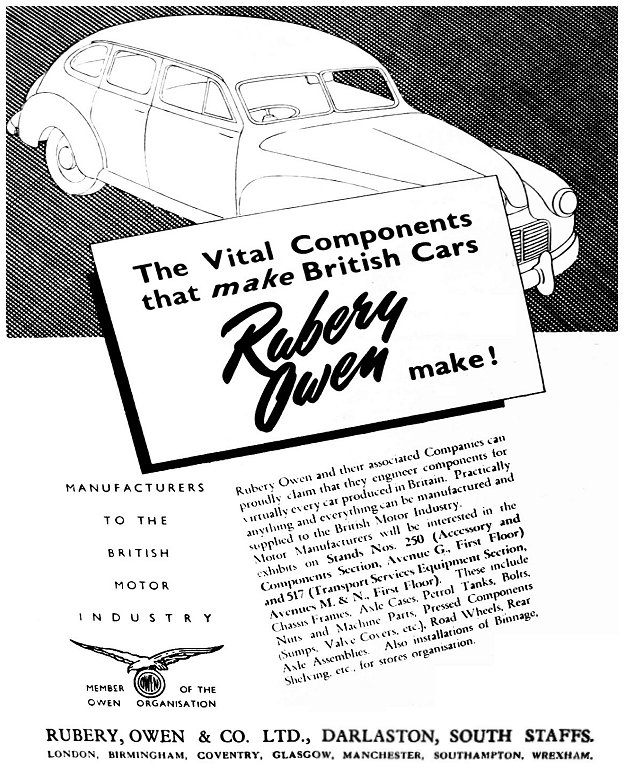
An advert from 1949. |
The Motor Wheel
Department The Motor Wheel Department
supplied pressed steel wheels and wheel discs for
the motor industry, and supplied over one third of
the British vehicle manufacturers with disc and
spoked disc wheels for private cars. Wheels for
caravans and agricultural trailers were also
produced, along with 400 types of steel split
pulleys, ranging from 3 to 48 inches in diameter.
During the Second World War, the department
produced charge cases for demolition purposes, instrument
containers, sea mine trigger mechanisms, aircraft
bomb carriers, ant-aircraft weapon equipment, steel
helmets, and ammunition boxes. |
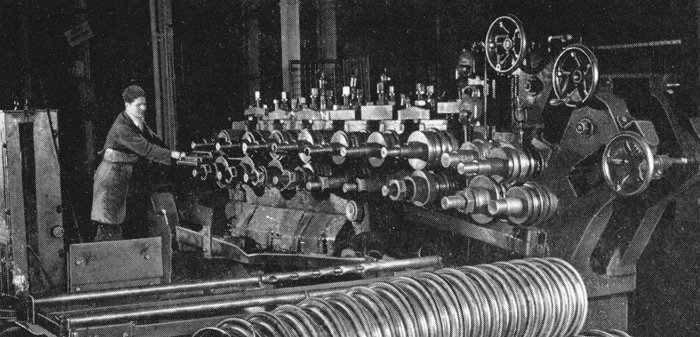
Large scale wheel production. |
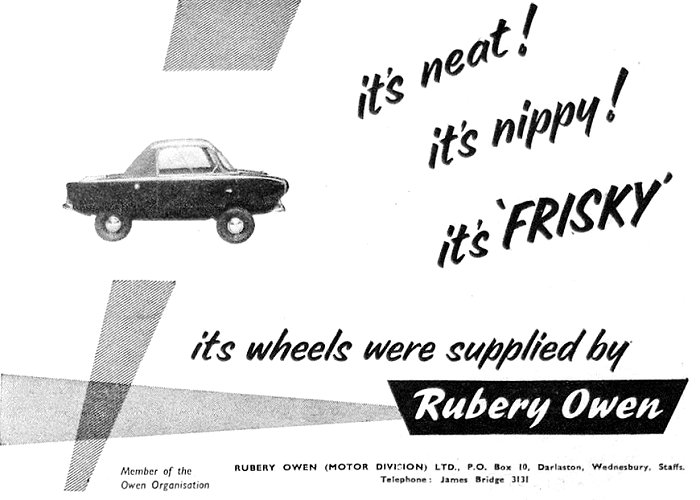
An advert from October 1958.
The Air Frame
Department This department opened in the
Second World War to produce air frame units, wing
flaps, tail planes, assemblies for the Stirling and
Lancaster bombers, 50 gallon jettison tanks for
Spitfires, and light alloy radar reflectors.
After the war the department concentrated on
large scale production of petrol tanks for cars,
commercial vehicles, and agricultural vehicles.
Department No. 11
Another wartime department, Department No. 11,
produced propeller hubs by a new process developed
in conjunction with Messrs. Rotol of Gloucester, and
the Ministry of Aircraft Production. The hubs were
pressed in two halves, direct from steel plate, over
on inch thick, using presses of up to 2,000 tons
capacity. After the war, the department produced two
piece, pressed steel, rear axle casings, for
commercial vehicles. |
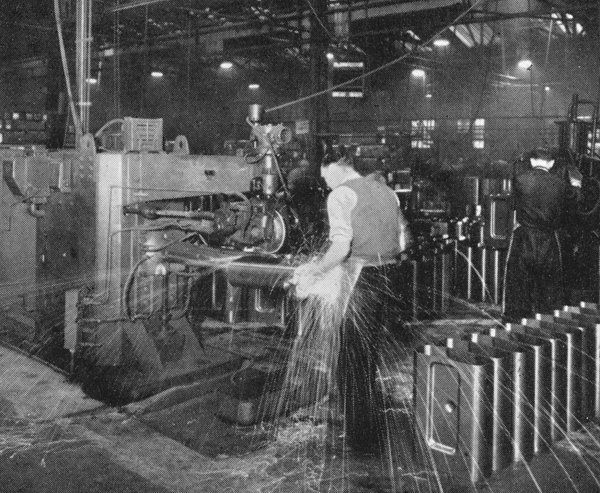 |
Flash welding petrol
tanks. 5,000 types
were produced each week, all fully assembled and
tested. |
Aviation
Department The Aviation Department opened
before the First World War for the production of
repetition components machined to fine tolerances,
in all metals. Bright drawn steel bars of various
sections were also produced. By the 1940s, around
five million parts were manufactured in the
department, each week.
After the Second World War, the department was
manufacturing bright bolts and nuts up to one inch
in diameter, eye bolts, turn buckles, shackle pins,
and tension rods for the motor, aircraft, and
general engineering industries. They were produced
in mild steel, high tensile steel, and alloys, and
were available in a wide range of finishes,
including cadmium, and zinc, and could be Parkerised,
or anodised.
Cold-headed, heat treated bolts were also
produced, and were available in mild steel, high
tensile steel, or nickel steel, in sizes from 2BA up
to half an inch in diameter, and six inches long.
Bright steel bars up to 2¼
inches diameter were also produced. |
Part of the production
area, where precision aircraft parts, and bright
bolts and nuts were made. |
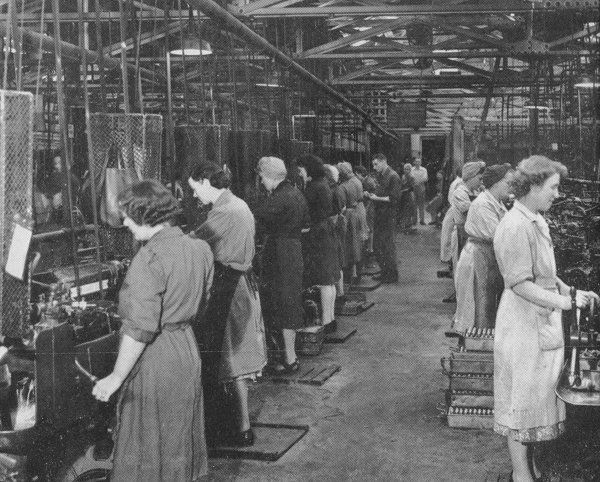 |
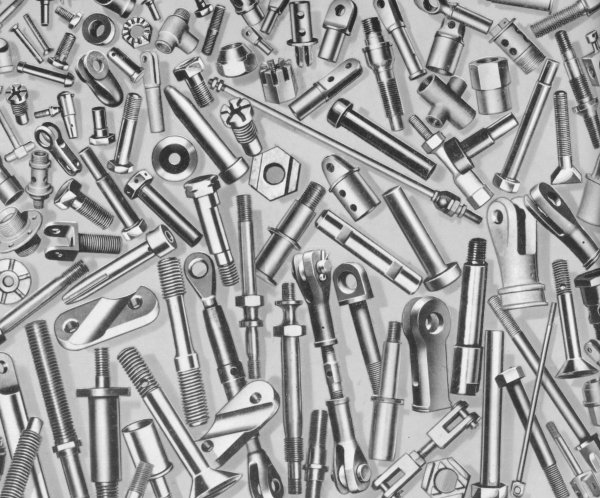 |
A few of the many small
components manufactured in the department. |
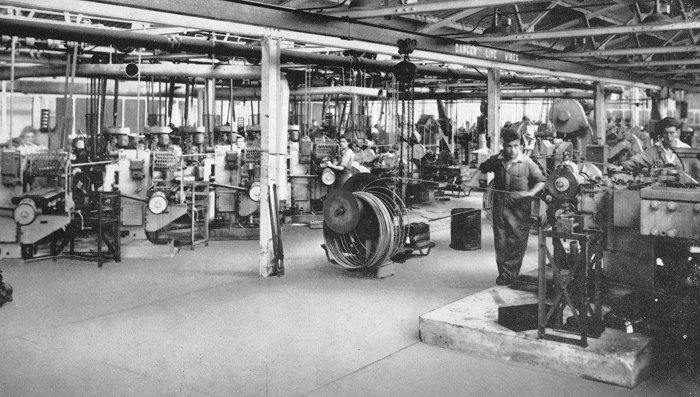
The department's other factory
at Moxley, where cold headed bolts were produced by
the million. |
The Aircraft
Components Department This department
opened in 1939 to manufacture precision sub
assemblies, and small accessories for aircraft
manufacturers. Products included control columns,
seats for pilots, rudder bar assemblies, and
hydraulic feed systems. The product range later
widened to include valves for propane and butane gas
containers, valves for small hydraulic rotary pumps,
and valves for petrol nozzles, and hydraulic jacks.
New production lines were laid down to manufacture
agricultural components, particularly the hydraulic
implement lift for the Fordson 'Major' tractor.
Other products included axles for caravans and
agricultural trailers, with a loading capacity of 12
to 60 cwt. |
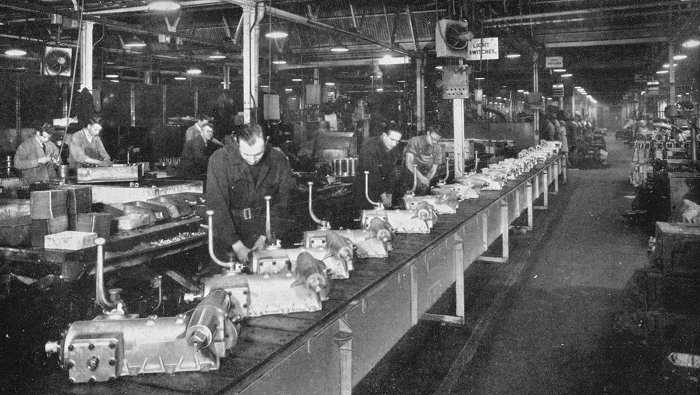
Assembling hydraulic implement
lifts for the Fordson 'Major' tractor. |
Agricultural Plough Department This was
originally established in 1937, as the Armour Plate
Department, to manufacture armour
plate assemblies for tanks. After the war,
production turned to implements for the Ferguson
tractor, including the Ferguson plough, the Ferguson
universal grain drill, the International
Harvester manure spreader, and beet hoppers. Accessories and
components were also produced for various types of
agricultural implements. |
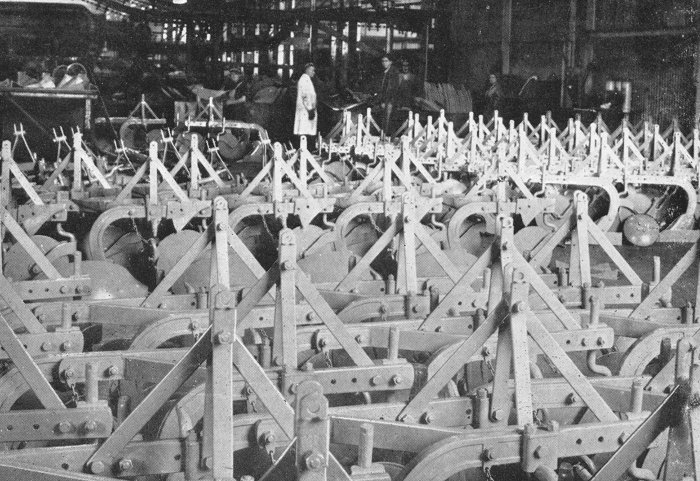
Completed ploughs. |
The Metal
Equipment Department |
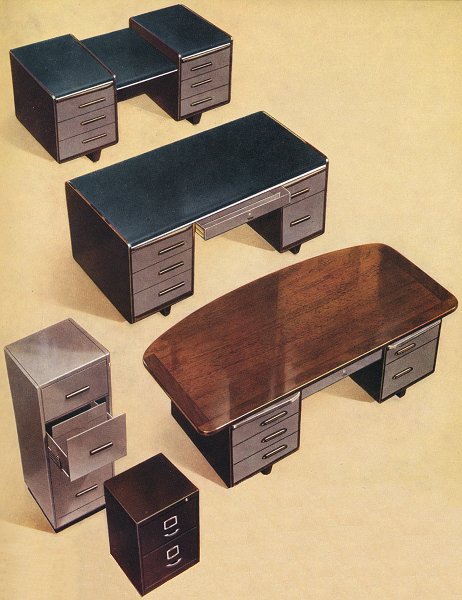 |
The department opened in 1929 to manufacture all
kinds of metal storage units and steel office
furniture. They were supplied to factories, and
government departments at home and abroad, The
department rapidly expanded, and a new factory, The Whitegate Factory, was acquired at Wrexham in order
to increase production.
The Wrexham factory concentrated on storage
equipment, and the department at Darlaston
concentrated on office furniture.
The office furniture included filing cabinets,
and a wide range of desks and tables. The desks
could have a lino top, or one made of oak, or
mahogany.
There were also wardrobes, typists' desks and
tables, cupboards, and plan files for design
offices,. The department also manufactured kitchen
cabinets, refrigerators, and special purpose control
equipment. |
An example of the special
purpose control equipment that was manufactured at
Darlaston.
A piece of flight control
equipment that was supplied to the Ministry of
Civil Aviation. |
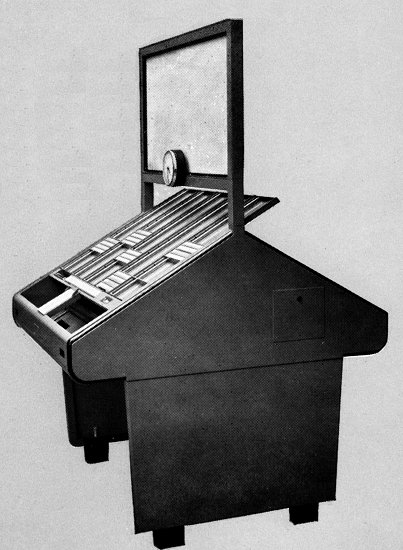 |
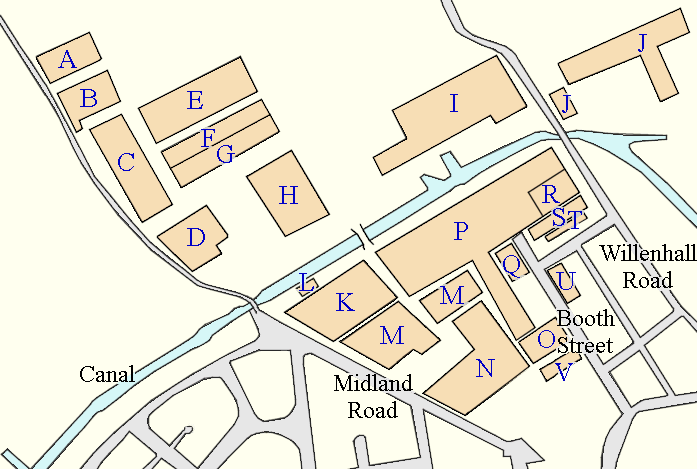
The Darlaston Factory. |
A. |
Invicta Electrodes Limited |
|
L. |
Laboratory |
B. |
Apprentice Training Centre |
|
M. |
Aviation Department |
C. |
Aircraft Components Department |
|
N. |
Structural Steel Department |
D. |
Air Frame Department |
|
O. |
Metal Aircraft Department (Press Plant) |
E. |
Vitreous Enamelling Department, and
Easiclene |
|
P. |
Motor Frame Department |
F. |
Department No. 15 |
|
Q. |
Axle Case Department |
G. |
Heavy Press Plant |
|
R. |
Agricultural Implement Department |
H. |
Motor Wheel Department |
|
S. |
Transport Services |
I. |
Metal Equipment Department |
|
T. |
Technical Administration |
J. |
Department No. 46 |
|
U. |
Central Administration |
K. |
Motor Frame Department, Hot Pressing
Plant |
|
V. |
Sheet Metalwork Department |
 |
|
 |
|
 |
Return to
The
Early Years |
|
Return to
the contents |
|
Proceed to
Easiclene |
|