Introduction
To the north east of Penn Common,
on the slopes of the Colton Hills, is an area of open
countryside known as The Seven Cornfields. Although it
is now associated with Pennwood Farm, and has a long
agricultural past, it was once the site of an important
local industry, brick making.
Large numbers of bricks were needed
for new housing developments, as Wolverhampton expanded
to cater for its growing population. The Black Country
changed dramatically as industrialisation began to
dominate the landscape, and people moved into the area
to find employment in the new factories. During the 19th
century the UK population almost trebled, but the
increase in the local population was far greater.
Population increases of up to 8 fold occurred in some
areas, as the proportion of people living in towns
increased from 20% to 80%.
The fine glacial clay deposits on
the southern side of Wolverhampton were ideal for brick
making, and so several brickworks were built in the
area. Most Black Country towns had at least one
brick-maker who took full advantage of the locally mined
coal and the excellent canal and road network that
covered the area. Brickkiln Street in Wolverhampton is
named after the brick kilns that once stood there, and
others could be found on the southern boundary of the
old town. |
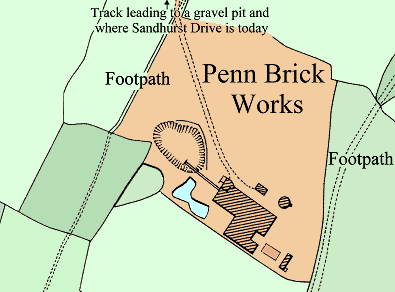
The location of Penn Brickworks. |
On the eastern side of Dudley Road stood the Elm
Farm Brickworks, and Pheonix Brickworks, along with
several others around Ettingshall Park.
There were also a number of brickworks around Himley
and in Gornal Wood, and in more recent times the one at
Baggeridge.
It is possible that a brickworks once occupied part
of the site of Windsor Avenue playing fields, in Penn, because
the old meadow that once stood along the northern side
of Linton Road was called Near Brickkiln. |
Penn Brickworks
Penn brickworks has long
disappeared, but the site has never been redeveloped,
and today is scattered with remains from the demolished
buildings and the old spoil heaps.
No documentary information about
the works has so far been discovered, but it is marked
on old maps, and is remembered by the descendants of the
last owner, Samuel Flavell. Unfortunately the
descendants of the original owners, the Lakin family,
know nothing about the business, other than that it was
owned by the family. What follows is based on evidence
from old maps, remains from the site, and standard 19th
century brick-making techniques. Luckily the remnants of
the spoil heaps, which have now almost disappeared, gave
an insight into what was made at the works, and possibly
when. |
Local landowners, the Lakin family, lived in Carlton
House, which stood where Sandhurst Drive is today. The
house stood on the Colton Hills, near the top of
Sandhurst Drive, just below the summit ridge. The family
is listed in the Wolverhampton Red books, as living in
Carlton House, until the 1930 edition, but is not listed
afterwards. By 1951 the house was occupied by the Gough
family, who were poulterers. They
appear to have occupied the house until its demolition
in the late 1960s when the current houses in Sandhurst
Drive were built. |
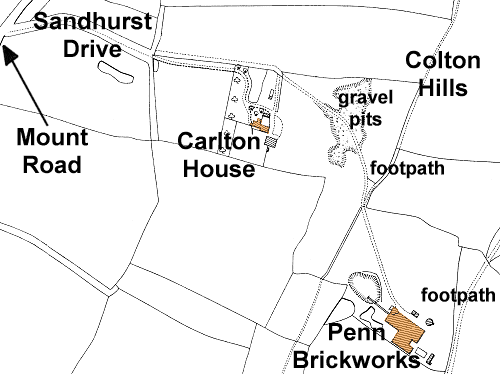
The location of the brickworks, the gravel pits,
and Carlton House. |
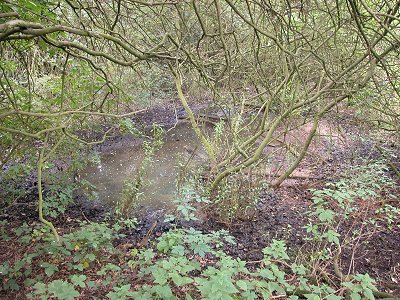
A filled-in clay hole, now only a
few inches deep. |
The last ice age glacier to cross the site,
deposited gravels at the top of the ridge, and clay on
the far eastern side.
The Lakins fully exploited their mineral rights by
opening a gravel pit at the top of the ridge, and the
brickworks on the eastern side above the clay.
Both sites were conveniently situated next to a
relatively flat dirt track which led to Goldthorn Hill,
and allowed the gravel and finished bricks to be easily
transported from the site by horse and cart. |
Until a few years ago the site of the brickworks was
quite open, and much could be seen. During the last two
or three years the site has changed beyond recognition.
It is now completely overgrown, and in places is two
metres deep in weeds and saplings. Many of the bricks
lying around the site, both in the spoil heaps, and in
the base of the factory walls, have been removed, as
have many of the tiles from the floor of the kiln. It
now looks almost identical to the other overgrown fields
in the area. Parts of a smaller flooded clay pit still
survive, but have been filled-in, and are well fenced.
The main clay pit was situated at the north eastern end
of the site and is still remembered by the older members
of the local community. It was deep, with steep sides,
and like other clay pits, eventually filled with water.
It became known as “The Danger Pool”, and people often
tell the story of a horse and cart that fell into the
pool, and also a young child who drowned there. In the
mid 1930s the buildings were demolished, and in the
1970s, the pool
was filled-in with rubble from the site. All traces of
it are now gone. |
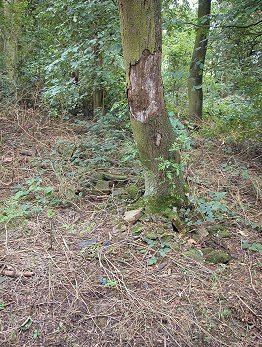
The site of Penn Brickworks. |
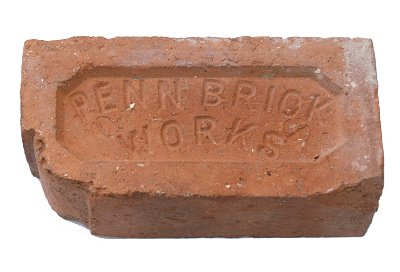
A Penn brick. |
Evidence from the
site
Until a few years ago, there was
much to see. Remains of the buildings could be seen in
the wooded area on the northern side of the site, along
with old floor tiles, and the base of the kiln.
The lower courses of the outer
factory walls were visible, as was the brick base of the
steam engine.
There were some slate roof tiles,
the top of the well, the remains of kiln fire holes, and
parts from the curved kiln roof. |
The main building was rectangular in plan, as could
be seen from the base of the outer walls. It was built
of brick and had a slate roof. There were two thick,
heavy duty walls just inside the northern corner of the
building, and what seemed to be a filled-in pit.
This appeared to be the base of a steam engine and
boiler, with a pit for the flywheel. Locals sometimes
referred to this part of the building as the engine
house. The steam engine would have powered a pug mill
for mixing the clay, and possibly driven a brick-making
machine. It provided steam for drying the bricks, and
probably powered a winch to lift the clay from the
bottom of the deep clay hole. |
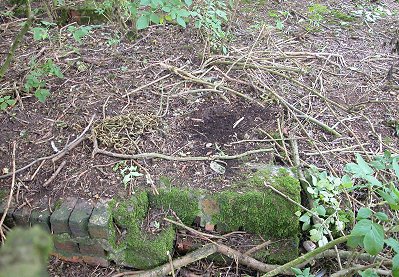
What remains of the outer walls. |
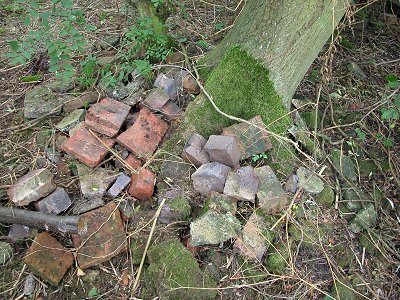
Some of the old bricks and tiles,
pushed up by tree roots. |
It is likely that most of the building would have
been occupied by a steam-heated drying room, which was
usually the largest part of any late 19th century
brickworks. There was also an office, possibly situated
at the northern end of the building near the entrance.
Some of the old bricks and tiles were pushed up by tree
roots, and many others were still in the old spoil
heaps, which consisted of the inevitable rejects that
occurred thanks to the vagaries of the firing process.
The remains of the spoil heaps contained a wide variety
of bricks and tiles that were made over a long period of
time. |
The earliest examples were crude, hand-made products
that contained a small percentage of gravel, presumably
from the two nearby gravel pits, owned by the Lakin
family. The gravel helped to lessen shrinkage during the
firing process and so would have reduced the number of
rejects.
There were many well-made standard bricks, facing
bricks, bricks with scroll work or a motif, and also
some high quality examples that look like terracotta.
The more recent bricks were machine made, indicating
that a degree of automation was later introduced.
Some of the bricks were of a lighter colour, and
blistered, suggesting that crushed lime had been added.
Many of the tiles scattered around the site are of a
heavy industrial type. They are unusual in that they
slot together and so would ensure an even surface and
share a heavy load. |
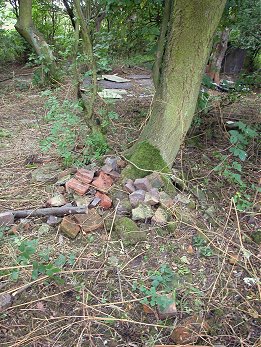
Another view of the bricks and
tiles. |
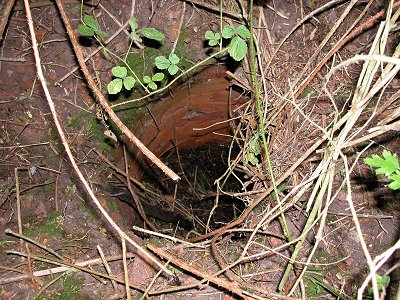
The well. |
A good water supply was essential. Water would have
been added to soften the freshly dug clay to give it the
right consistency for moulding. The water came from a
well, the top of which could be seen on the north
eastern side of the main building. The works had one
kiln, about thirty feet in diameter, which could have
had a capacity of up to 20,000 bricks, depending upon
the height of the kiln and the stacking density. Much of
the tiled base remained until recently. Sections of it
were pushed-up by the small trees that grow in the area.
|
The circular kiln, with a chimney on one side, can
be seen on old ordnance survey maps. It appears to be a
downdraught kiln which would have been fired from eight
or so fire holes. One of the spoil heaps contained
parts of the curved arches that formed the top of the
fire holes, and another contained some of the tiles that
formed the kiln roof.
The bricks for the kiln must have been made on the
site. The base was built using the company’s heavy duty
interlocking floor tiles, which were extremely strong
and hard wearing. |
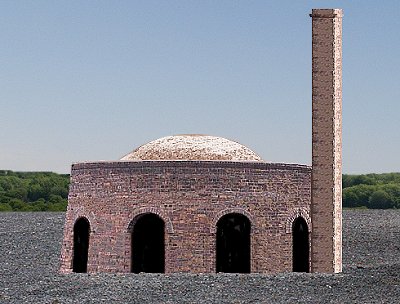
An impression of how the kiln
might have looked. |
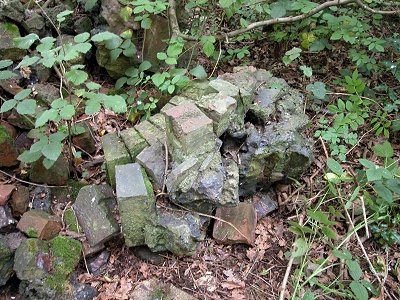
Part of the curved top of one of
the kiln's fire holes. |
The Brickworks in
Operation
In the early days the clay would
probably have been dug out by hand, in lumps, placed in
a soak pit, and left overnight to soften.
Roughly three cubic yards of clay
produced about 1,000 bricks. It could then be mixed with
water to form a suitable consistency for moulding.
There would have been at least one moulding table
where bricks were moulded by hand, using four-sided
wooden moulds with no top or bottom. |
The wooden mould was placed over a rectangular piece
of wood on the table, to form the frog, and the clay
would be firmly pushed in. Finally the excess clay was
cut from the top to form the completed brick, which
would be removed from the mould and left to dry. Moulds
were often lined with a dusting of sand to prevent the
clay sticking. The moulding tables would have been
replaced by moulding machines, which must have produced
the later, higher quality bricks. Mechanisation had several advantages over
traditional methods. The pressure applied to the clay in
the mould was much greater, leading to a denser and more
uniform brick, which gave more consistent results,
leading to fewer rejects. The machines would also have
increased the number of bricks made. |
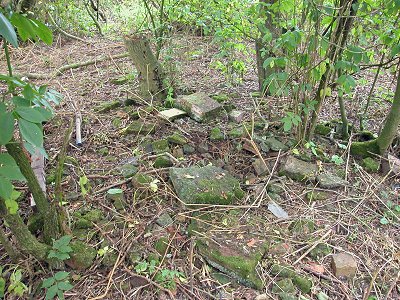
The site of the kiln, showing
floor tiles and bricks that have
been pushed to the surface by tree roots. The kiln base
is made of the company's interlocking floor tiles,
several of which can be seen above. |
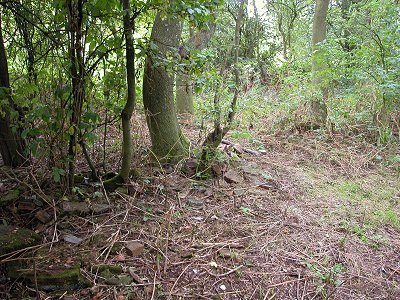
Trees growing through the base of
the kiln. |
The moulded bricks would be stacked
on racks to dry, where each brick could loose as much as
half a pint of water.
Before the steam engine was
installed, this would be a lengthy process because the
bricks would take a considerable time to dry, possibly
never fully drying in the winter months.
If this was the case, the
brick-making would have been seasonal. |
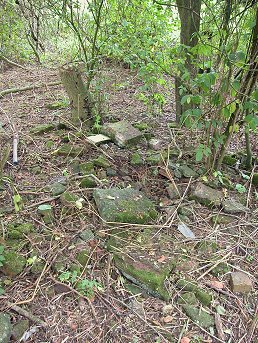
Another view of the site of the
kiln. |
The dried bricks would have been carefully stacked
in the kiln, and coal in the fire hole grates would be
lit to produce the hot gases that were directed upwards
from baffles to the underside of the domed roof. The
gases would then flow downwards through the stacked
bricks and out through the chimney. The floor would be
perforated for this purpose. Once fired, the kiln
would be fed with coal through the fire holes, and
stoked every half an hour, both day and night. The kiln
had to be constantly attended for around two days until
it had reached a temperature of possibly 1,000 degrees
centigrade. The firing then continued for a further day
to maintain the temperature, while the bricks baked.
Three or four days later the kiln would have cooled
down sufficiently for the bricks to be removed. The
whole process took just over a week. Great care was
needed to reduce the number of rejects. Some were to be
expected, but a whole kiln-full would be disastrous. Two
ruined kiln-fulls in a row could lead to bankruptcy. |
Emptying the kiln must have been one of the most
unpleasant tasks. It would have been emptied as soon as
possible after the firing process, to maintain
production. This meant that the kiln would still be
quite warm, and the bricks would not have fully cooled.
Although all of the bricks in the kiln were made from
the same clay, their final colour would depend upon
their position in the kiln. The ones in the centre would
reach a higher temperature and so could be darker and
much harder than the others. |
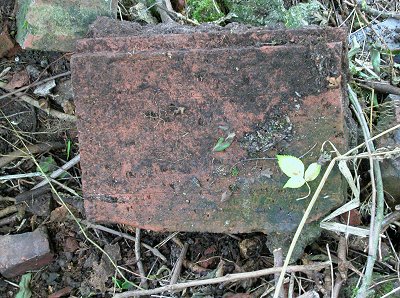
One of the floor tiles from the
kiln. |
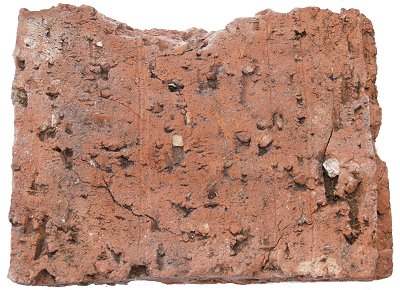
The underside of a floor tile
showing the clay-gravel mixture. |
On the 1901 map there appears to be a ramp leading
from the main building, down into the large clay pit, so
the clay would have been hauled into the building on
some kind of trolley, before being placed in the pug
mill, which was probably near to the steam engine at the
northern end of the building.
The map also shows two small outbuildings on the
site. These could have been stables, coal bunkers, or
coverings for the straw that would have been used for
packing. |
A number of people would have been
employed on the site, mostly doing dirty and unpleasant
work for little pay. Some would be digging clay, or
operating the pug mill. Others would be operating the
moulding machines or stacking the moulded bricks in the
drying room.
The kiln would have a number of
attendants who stacked the bricks, controlled the fires,
and then emptied the kiln at the end of each firing.
There would have been a person in charge of the boiler,
and someone to look after the horses and carts that were
used for transportation. |
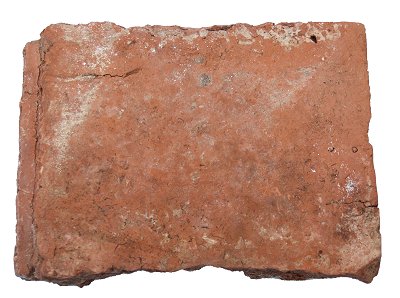
The top view of one of the unusual
floor tiles. |
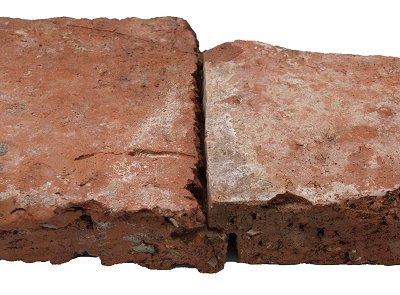
Many of the tiles scattered around
the site are of a heavy industrial
type like the two above. They are unusual in that they
slot together and so would ensure an even surface and
share a heavy load. |
If a quantity of bricks was
ordered, the customer’s name could be stamped on the top
of each brick. "Beacon View" cottage, owned by Len
Collins, was built from Penn bricks, and the Collins
name is on each brick. The cottage was built around 1890
by Len's grandfather, who was a milkman.
Around 1900, Samuel Flavell purchased the brickworks,
which he ran for a number of years. He was born around
1836, and at the age of 24 married Rachel at Sedgley
Parish Church. He was the underground Manager at Corbyns
Hall Colliery, Dudley, where he gained an
award for his handling of a pit fall. In the 1901 census
he is listed as a brick manufacturer. His son Arthur,
aged 20 is listed as a clerk in the office at the
brickworks. |
Samuel lived at 10 New Street,
Gornalwood, and was proud of one of the large orders,
which was for bricks for the building of Queen Victoria
School in Bilston Street, Sedgley.
The transportation of the bricks
became increasingly more expensive, and so Samuel
decided call it a day. It appears that he tried to sell
the business, but without success.
By this time Samuel lived at 12a
Gospel End Street, Sedgley, not far from the old
brickworks. Samuel and his son Arthur, and other members
of the Flavell family would go for walks across Penn
Common to see the works, and no doubt reminisce about
‘the good old days’. Samuel died in November 1927.
After closure, the buildings
remained empty for some time, and were demolished in the
mid 1930s.
|
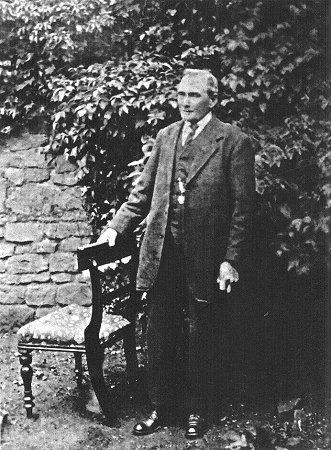
Samuel Flavell. Courtesy of
Cheryl Nicholls. |
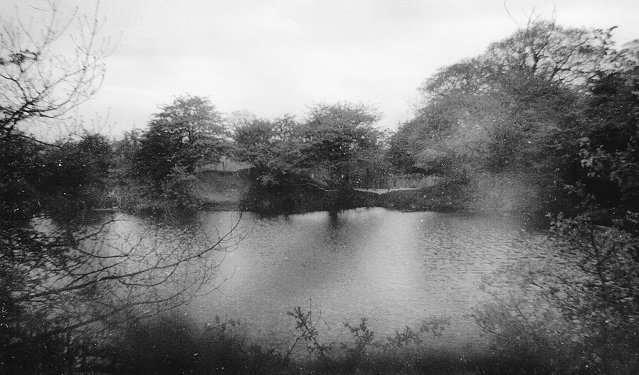
What remained of The Danger Pool
in later years. Courtesy of Lawson Cartwright. |
I would like to thank
Cheryl Nicholls for information about the Flavell family
and their involvement at the brickworks, and
|
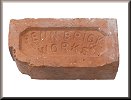 |
Return to
the
Penn Menu |
|