By the 1940s, Lincoln Works covered over seven acres,
and was the country's largest factory producing
electrical accessories. The company was also one of the
country's largest consumers of porcelain for electrical
purposes.
By 1946 the company employed around 1,800 people, who
were carefully selected for intelligence and initiative.
The firm had its own research laboratories, and
manufactured all of the component parts for the Crabtree
products, except the porcelain, which came from the
potteries at Stoke-on-Trent.. |
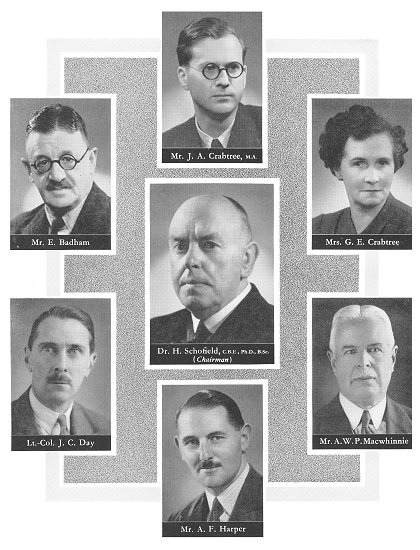
The company's directors in 1947. |
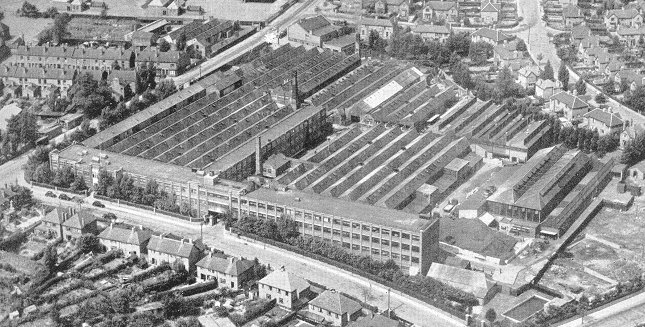
Lincoln Works in 1946. |
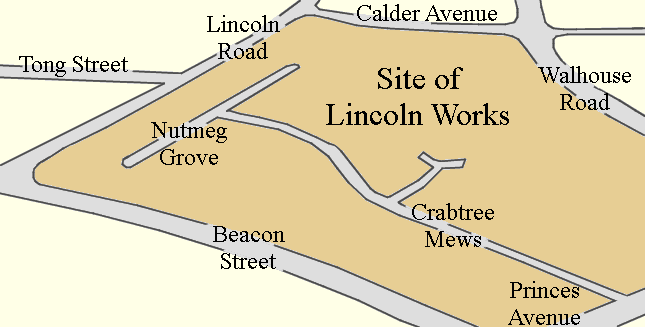
A map of the area today, showing
the site of Lincoln Works. |
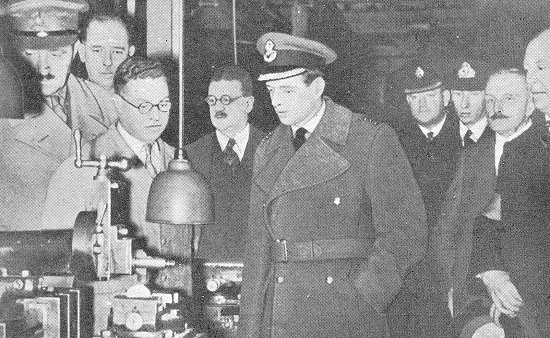
The Duke of Kent at the factory in
December 1940. |
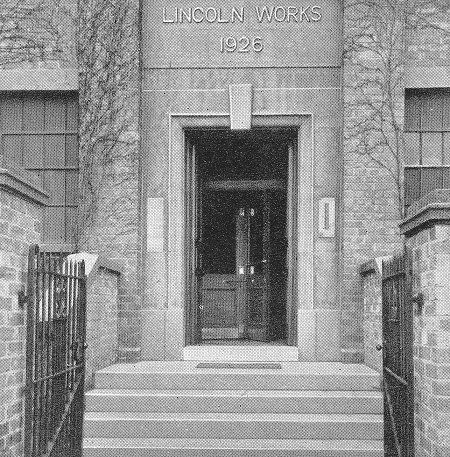 |
The entrance to the offices. |
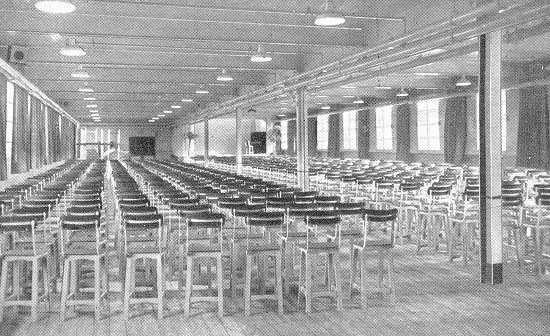
The canteen, laid-out for an
evening concert. |
The Laboratories All the raw
materials purchased by the company were tested and examined
before use in the factory. Samples were taken for chemical
analysis, microscopic examination, and physical testing. |
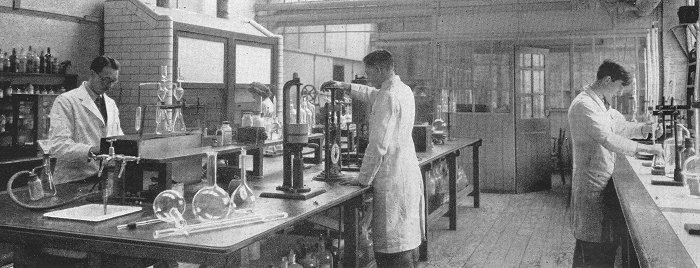
The chemical laboratory. |
During the manufacturing process, further tests were
carried out to ensure that all components would perform
correctly in use. Pressed items were examined for uniformity
of hardness and thickness, and if annealing was necessary,
the most suitable temperature for the annealing ovens would
be chosen. Tests were carried out on every metal part
that had to be heat-treated, to make sure that no
deterioration took place. |
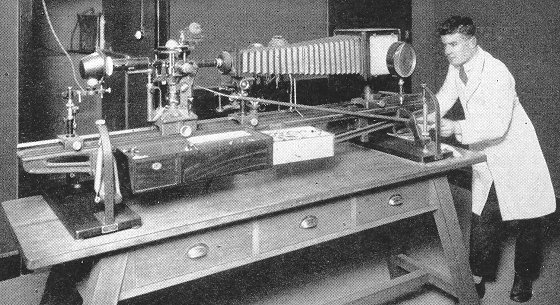
Microscopic examination of grain
structures. |
A close eye was kept on the raw materials that went into
the cupola furnaces in the foundry, to make sure that cast iron
was produced to
the correct specification, and to determine the optimum
casting temperature. The laboratories also ensured that the
paint and enamels used in the factory were of the highest
quality.
Tests were carried out on their resistance to corrosion
and abrasion, and also to the organic acids that are present
in certain foodstuffs, which could damage the finish of cooker control units.
The iron cases that were used on some of the switchgear
cases were tested for their resistance to corrosion in an
open area on the roof, where they were exposed to the elements
for periods of time. |
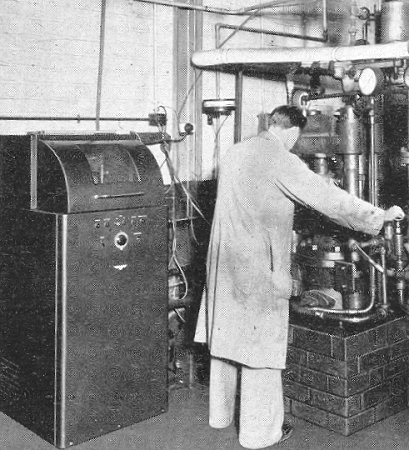
High frequency pre-heating equipment. |
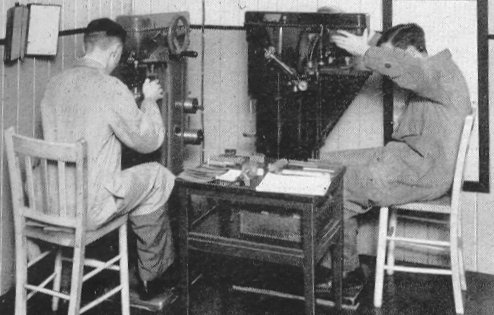 |
Testing metal specimens for
hardness. |
The Electrical Laboratory The
laboratory had electrical plant to produce AC and DC
voltages for a wide range of tests. The AC supply came from
the mains supply, which was also used for a motor-generator
set that provided the DC supply. There were also two banks
of rechargeable batteries, each providing a 250 volt DC
supply. The batteries were designed to withstand large
short-circuit currents. |
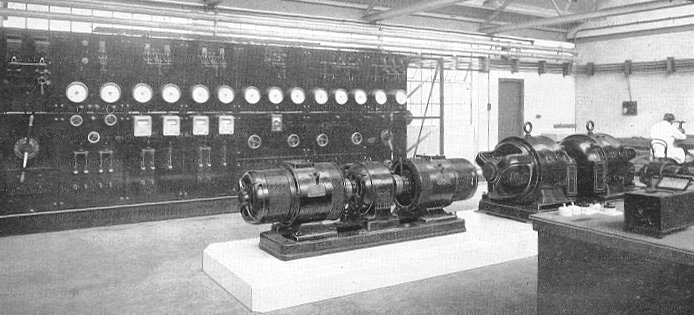
The generating plant and
switchboard. |
A corner of the electrical
laboratory, showing some of the test equipment. |
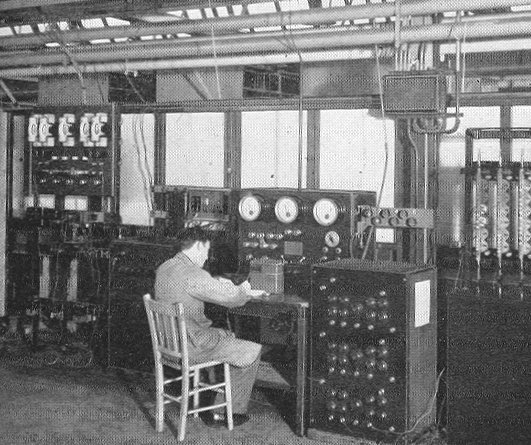 |
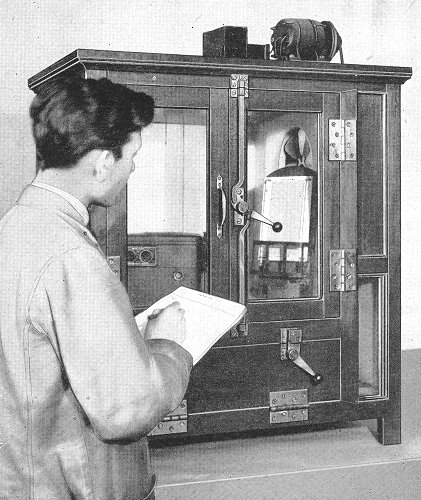
Carrying out a humidity test. |
The laboratory had an extensive range of meters,
oscillographs, and resistance bridges. All incoming
materials were examined for their electrical characteristics
to ensure that they were suitable for purpose.
Finished products were also inspected and thoroughly
tested to make sure that they operated within their
specification. Overload characteristics were also tested.
Efforts were continually made to improve existing
products, both in the materials used, and construction. |
The Foundry Lincoln Works'
foundry used the latest and most up-to-date machinery
including hydraulic and pneumatic moulding machines that
were fed mechanically by hoppers. They were encircled by a
slowly moving conveyor. |
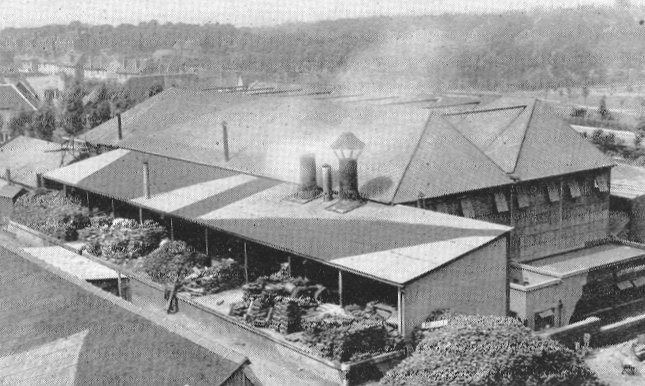
The foundry, showing piles of pig
iron. |
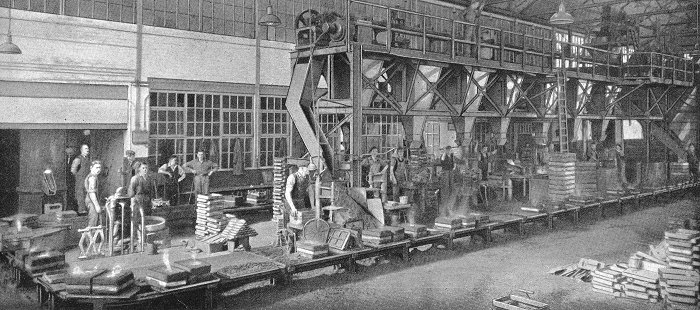
The production plant, and the
conveyor, loaded with moulds. |
The foundry had siphon type cupolas that provided
molten iron for most of each working day. |
The conveyor carried the moulds from the moulding
machines to the pouring point, then on to the knock-out
point, a journey of about fifteen minutes.
At the knock-out point the casting was removed from the
mould, which was then broken up. The sand fell through an
open grid in the floor to an underground conveyor which
carried it to an area where it was screened, cooled, and
milled.
Any remaining scrap iron was removed by a
magnetic field. Flight conveyors then transported the
refined sand to the hoppers for re-use. |
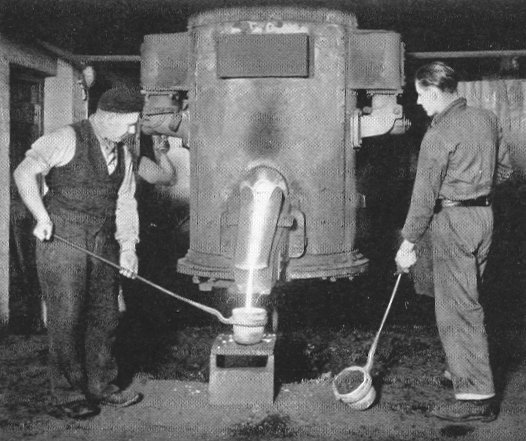
Pouring molten iron from one of the
cupolas. |
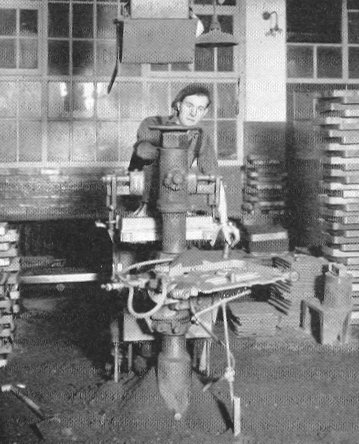
A moulding machine in operation. |
The castings were sand-blasted to remove any remaining
sand, and to show-up any surface defects. They were then
transported to the grinding and bobbing machines for
cleaning-up, before going to the mechanical enamelling plant,
to be given a heavy stove-enamelled finish.
Some hand moulding was still employed for castings that
were unsuitable for mechanical production. For this work, a
few highly skilled moulders worked in the traditional way,
carrying out floor and stump moulding.
The company had its own patternmaking section where
patterns were produced in wood, white metal, aluminium, and
gunmetal.
The cast-iron components were carefully monitored by a
metallurgical chemist, who ensured that the highest standards
of quality and accuracy were maintained. |
Moulding Department The moulded
cases and covers used in Crabtree products were produced in
the factory's moulding department, on hydraulically-operated presses.
Hydraulic pressure was supplied by an eighty ton hydraulic
ram, mounted high on the building. Components were moulded
in 'Jacelite' (phenol formaldehyde), and P.V.C. The dies for
the mouldings were produced in the toolroom to a very high
standard. The quality of the finished product depended
entirely on the quality of the die. The presses had
steam-heated platens, which were maintained at a precise
temperature.
The high quality finish achieved relied upon the close
cooperation of many members of staff, including the artist,
the draughtsman, the research chemist, the toolmaker, and
the plastics production engineer. At every stage of
production, the process was carefully monitored.
|
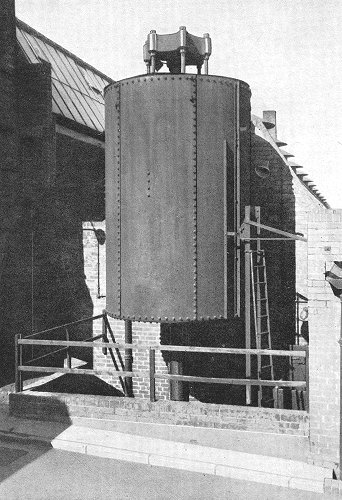 |
|
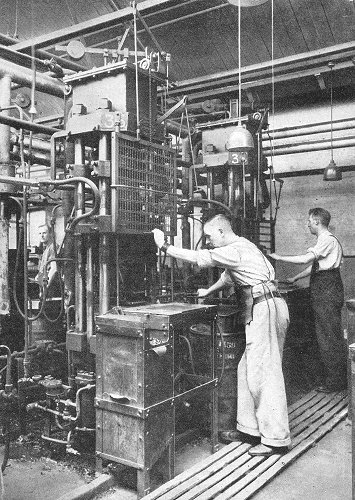 |
The eighty ton hydraulic ram. |
|
Some of the hydraulic presses. |
|
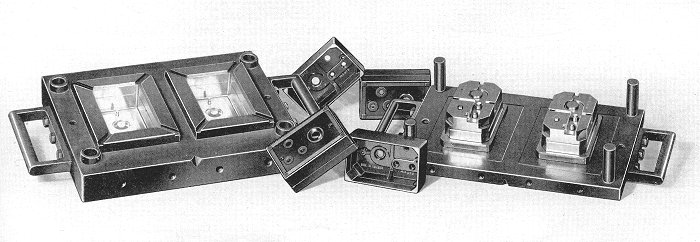
The steel dies for a switch socket
outlet cover, together with some of the mouldings. |
Machines Used in Production The
production process was automated as far as possible. In the
late 1940s the company always used machines made in the UK.
Millions of small component parts were produced each week
for the wide range of Crabtree products.
Many high speed machines were used, such as . drilling
machines that ran at speeds from 5,000 to 10,000
revolutions per minute.
High speed machines were used in the automatic turning
department where millions of small screws and terminals etc.
were made.
Some of the smaller components such as switch contacts
went through a sequence of delicate bending operations which
had to be carried out by hand, using the old-fashioned fly
press.
The firm's power presses were equipped with multiple
tools and could produce between three to four hundred parts
a minute. |
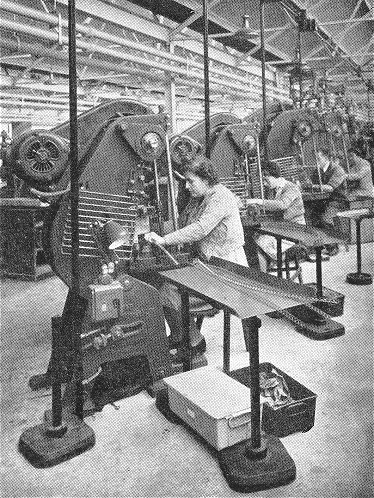
Stamping blanks from metal strip. |
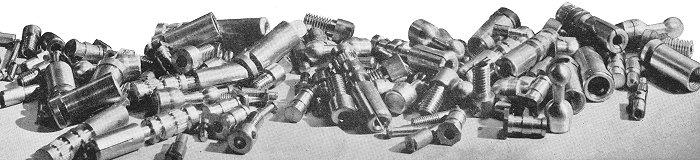
A few of the large number of
turned brass parts used in the company's products. |
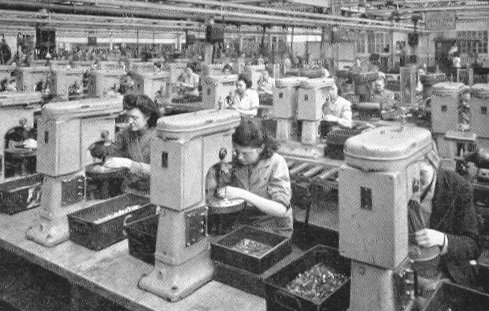 |
Part of the power drilling bay. |
Machining components to close
tolerances. |
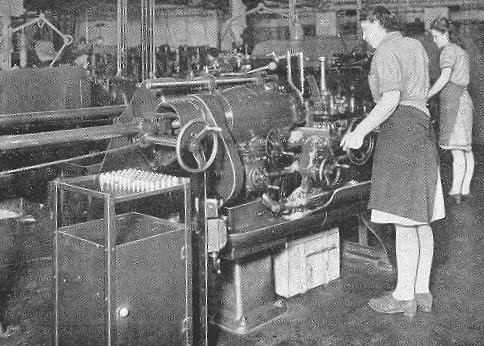 |
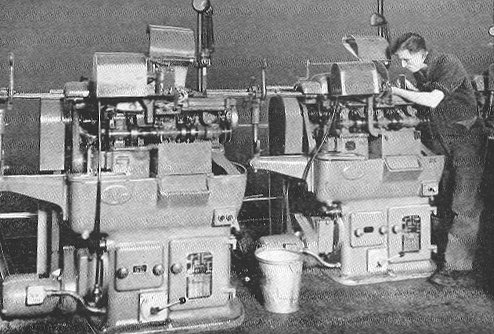 |
Adjusting a high speed automatic
machine. |
Packaging The company moved away
from multiple cartons to separate cartons for each product,
made of strong cardboard, printed in a distinctive red and
black design. The individual cartons were placed in strong
outer boxes made of corrugated cardboard, holding six or
twelve of the cartons.
This technique eliminated breakages during transit, and
allowed the individual products to be easily identified. |
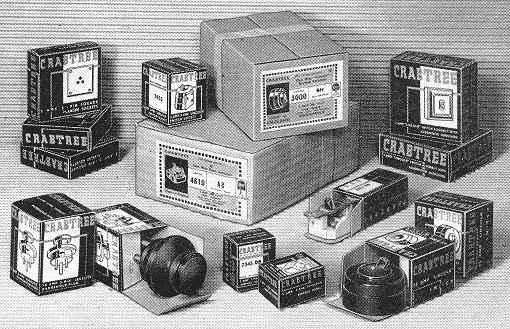
Crabtree cartons. |
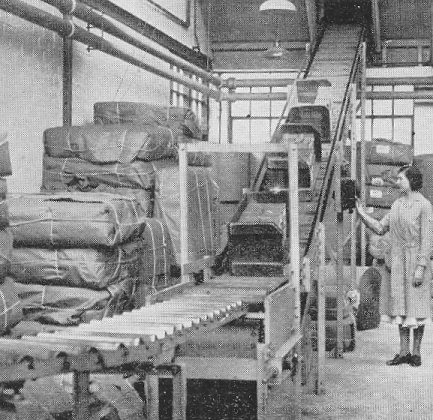
A corner of one of the packaging
rooms. |
The company's ironclad switchgear, and the larger
automatic control units were packed individually in
corrugated cardboard cartons.
The cartons were transferred from the stock bins and
placed in conveyor trucks. After checking against the
customer's order, they were placed on a roller-conveyor belt
to be carried to the packing room, where they were placed in
suitable boxes or cases.
The completed cases were transferred from the packing
room to one of the company's lorries or trucks for delivery. |
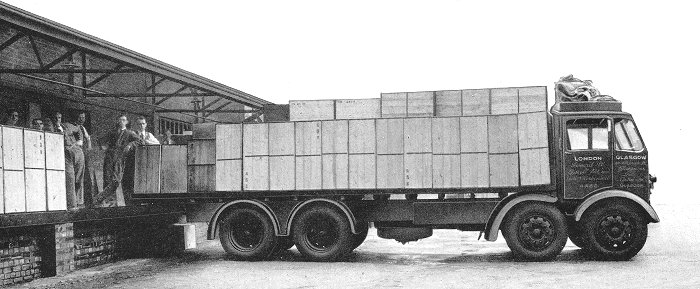
Part of an export order being
loaded onto one of the company's lorries. |
World-Wide Distribution Crabtree
products were sold throughout much of the world. The company
had agencies in Argentina, Australia, Barbados, Belgium,
Brazil, British Columbia, Burma, Ceylon, China, Columbia,
Cyprus, Egypt, Ireland, Ethiopia, Faroes, Fiji, Finland,
France, Gold Coast, Greece, Iceland, India, Iraq, Italy,
Kenya, Malaya, Malta, Mauritius, Mexico, New Zealand,
Norway, Palestine, Peru, Portugal, Seychelles, Siam, South
Africa, Sudan, Sweden, Switzerland, Tanganyika, Trinidad,
Turkey, Uruguay, and Zanzibar.
There were also distributors in Afghanistan, Algeria,
Chile, Costa Rica, Denmark, Hong Kong, Indonesia, Libya,
Madeira, Morocco, Tangier, and Uganda. |
|
|
View some of the company's
many products from the late 1940s |
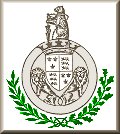 |
|
|
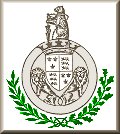 |
Return to
the
previous page |
|