Trades and
Industries, up to the end of the 17th Century
It was inevitable that metalworking in one form
or another would be carried out in the area, because of the plentiful
supplies of coal, iron ore, and limestone. Work at this time was
carried out in little workshops, often in a yard behind the
craftsman’s house. In the 15th century the churchwardens accounts at
All Saints’ Church list the local trades and industries in three
categories:
1. Smiths, braziers,
carriers, lime burners.
2. Millers, shearmen,
tailors, mercers, drapers, glovers, sempsters, and
barbers.
3. Cobblers, bakers,
butchers, and carpenters. |
Mining
Much of Walsall lies in the South Staffordshire
and Cannock Chase coalfields, often outcropping close to the
surface. By the early 14th century, coal and iron ore was being
mined. The lords of the manor (then divided), Roger de Morteyn, and
Margery Ruffus made an agreement to share the profits of the coal
and ironstone mines in the manor. Margery’s son, Sir Thomas le Rous
reserved the right to license coal-mining on land at Birchills in
1326 and 1327. By the late 1380s, and 1390s, there were coal and
ironstone mines in Windmill field.
Coal was mined in the manorial park, because
the manorial accounts for 1490 to 1491 include a payment for
prospecting for a mine there. By the middle of the 16th century, the
town was supplying coal to Sutton Coldfield. A document from the Calendar of Deeds, dated
1597 records a sale by William Webb, Mayor of Walsall, and others,
of land in Bloxwich to George Whitehall. The document states that
the purchaser promises to serve all the inhabitants of Walsall with
coals, called “dassell coalles” at the rate of three pence
for each horse, mare, or gelding load, and with others called “bagge
coalles” at two pence per like load, and to refuse none so long
as there be any coals upon the bank.
Large quantities of iron ore, or ironstone as
it is known, were to be found alongside the coal seams. The ore
often outcropped near the surface, particularly in the south, and
south eastern parts of the town. As already mentioned, the ore was
mined in the town in the early 14th century, and in Windmill field
by the late 1380s. In 1537 Thomas Acton was leasing mines in the
‘Foreign’, from the Crown, and by the early 17th century the ore was
supplied to ironworks in the surrounding area, including (from 1561)
Lord Paget's blast furnace on Cannock Chase. His son Henry leased 8
open cast mines in Walsall in 1576, and soon many more were to be
found in the area.
The carboniferous coal and iron measures lie
above a layer of Silurian limestone, which in places outcrops near
the surface, and so is relatively simple to mine. It is first
mentioned in a document dated 1325 which states that Sir Thomas le
Rous grants Robert Bonde three acres of his waste land in Birchills,
on condition that he should not make any mines of limestone in the
same. |
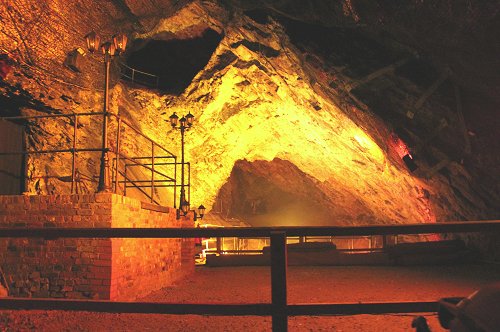
One of the limestone caverns
off the Dudley canal tunnel. It gives an impression
of the size of the caverns, and the vast amount of
limestone removed. |
It was mined in many areas around the town, from
the eastern edges, to Rushall, and in the town
centre itself, where the Arboretum now stands.
There were also mines at Townend Bank, and around
Church Hill, where the more valuable Upper and Lower
Wenlock Limestones are to be found.
The part of Church Hill around Ablewell Street
became known as Lime Pit Bank, as a result of the
extensive caverns that were dug under the hill. |
Much of the limestone was used
as building material, although it was also burnt to
produce lime, and used in agriculture as a
fertiliser. It became an essential ingredient for
tanners who soaked leather in a solution of lime to
remove any hairs. There is a list of trades in the
Staffordshire Record Office dating from around 1494
which includes a mention of lime burners in Walsall.
Cartloads of local limestone
were transported throughout the area. It became a
popular building material. Wenlock limestone was
favoured by ironmasters for use as a flux in the
smelting process. By 1569 it was being transported
to the ironworks at Middleton in Warwickshire. The
limestone on the eastern side of the town was known
as Barr Limestone, and mainly mined around Hay Head.
Much of the limestone at
Rushall was extracted from around 200 feet below
the surface. It was highly prized because when
polished it looked like marble.

Walsall Wood Colliery. From an
old postcard.
Metal Working
Although iron ore was plentiful
in the area, it seems likely that little smelting
was done in the town until the 14th century. By the
16th century several bloomeries producing iron were
operating in the town.
Around 1300 the lord of the
manor, Sir Roger de Morteyn granted Adam the bloomer
an acre of waste at Bloxwich, presumably on which to
set up a bloomery. It may be that iron was being
smelted in the Birchfields area in 1333, because by
that time the name Cinder Hill Field had appeared. |
In the late 14th century the
lord of the manor sold iron ore, and purchased the
finished metal from Robert Grubbere, an iron smith
working in his local bloomery. In 1528 an area near
the River Tame called Bloomsmithy meadow was sold to
Martin Pemerton, which suggests that a bloomery was
there before that date, presumably water-powered.
In the late 1570s, trees were
felled in Bentley to provide timber for charcoal
making. The trees were cut down by William Gorwey,
John Stone, and Richard Worthington to provide
charcoal for their ‘smithmills’.
There would have been many
smiths in the area who would have produced all the
different kinds of metal items that were in everyday
use, from household utensils and fittings, to tools,
agricultural implements, horseshoes, and weapons. In
1362 Robert Grubbere had a forge in the town, as did
Richard Marchal who made nails at his forge on
Church Hill. William Marshall had a forge in Rushall
Street, and William Mercer ran a forge in Bloxwich.
By the end of the 17th century
the many goods manufactured in the town included
awl-blades, buckles, chains, locks, nails, brass and
pewter holloware. |
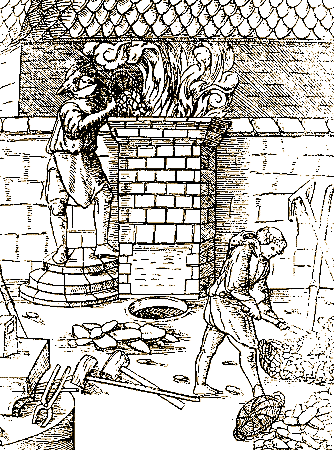
An impression of an early
bloomery. |
Nails were made in Walsall by the late 14th
century. There were three nail makers in the town in 1603, and
several in Bloxwich. By the end of the century there were many more.
Locks were made in small numbers from the 16th century, and awl
blades were made in Bloxwich. They were used for boring holes in
wood and leather.
Horse Furniture
Walsall has been well known for a long time as
a centre for the production of horse-riding products such as
bridles, spurs, and stirrups etc. The industry had begun by the
start of the 15th century. The Burgess Roll includes the name of
John Sporior, listed as a spur maker. By 1435 Walsall had three makers of lorinery,
consisting of saddler’s ironmongery, bits, spurs, and other metal
objects.
Around 1540 the well known antiquary John
Leland visited the town. He had been authorised to examine, and use
the libraries of all religious houses in England by the king. He
compiled numerous lists of significant or unusual books, and
recorded evidence relating to the history of England and Wales. His
description of Walsall is as follows:
Walleshaul, a little market towne in
Stafordshir, a mile by north from Weddesbyrie. Ther be many smithes
and bytte makers yn the towne. It longgith now to the King, and
there is a parke of that name scant half a mile from the towne, yn
the way to Wolverhampton. At Walleshaul be pyttes of se cole, pyttes
of lyme, that serve also South Town (Sutton Coldfield) 4 miles off.
The William Salt Library has another
contemporary description of the town, possibly written by William
Wyrley towards the end of the 16th century:
Walsale is a fayre village, and although it
inivyneth (enjoys) a maior and priviledges, yet it hath no market,
but in it be good store of lorrimers, making bridle bitts, spurs,
and such like. This town was sometime belonging to the familie of
Hyllarie, but nowe doth acknowledge for lord Th. Wilbrome, of
Woodhey, in co. Chester, Esquier; near unto this is the head of
Thame, and in the church be these armes.
The description is followed by a series of drawings, made in the
church.
Horse furniture was being produced in Bloxwich
by the 16th century. In 1561, John Baily, a lorimer of Bloxwich,
died, and by the turn of the century there were at least two
others.
Locally made horse furniture was sold far and
wide. In 1542 Richard Hopkes of Walsall was owed money for stirrups,
'odd bits', fine bits, and snaffles, sold at Exeter, and Bristol, and
in Devonshire, Somerset, Dorset, and the West Riding of Yorkshire.
He was probably a dealer rather than a manufacturer, and also sold
locally made buckles. Another Walsall dealer, Nicholas Jackson died
in 1560. Half of his possessions consisted of bits, stirrups, spurs,
and buckles.
By the late 17th century shoe and garter
buckles were made locally, but most buckles were produced for
saddles.
In the 14th century, pewter and brassware
products were made in the town. There were many pewterers and
braziers making household utensils such as bottles, candlesticks,
chamber pots, dishes, kettles, pots and pans, plates, salt-cellars,
saucers, spoons, and warming-pans. There were also bell-founders,
and brass foundries casting window casements. Copper was also worked
in the town by the late 16th century. Copper smiths produced a wide
range of products including holloware, nails, and studs.
Leather
Walsall has become well known for its leather
goods, and saddles. By the middle of the 15th century there were
tanneries in the town, by the stream at Digbeth, and in Caldmore.
Finished leather goods were not produced until the 16th century, and
only in small quantities.
Weaving
By 1300 there was a fulling mill in the town,
and by the middle of the 15th century cloth was being produced.
William Staunton was a clothier who made an agreement with the
corporation in 1620 to teach 20 or 30 children the art of 'spinning,
twisting, doubling, and quilling' worsted, woollen, and linen yarn. |
When Dr. Robert Plot
visited Walsall in 1680 he described the
local industries as follows:
Nor are they less
curious in their ironworks at the town of
Walsall, which chiefly relate to somewhat of
horsemanship, such as spurs, bridles,
stirrups etc.” He mentions that the natives
were then skilled in the making of every
article connected with saddlery, and of all
kinds of buckles. Walsall men were familiar
with the arts of tinning metals, and the
casting of iron, copper, and brass pots.
Ironstone was raised at
this time, both at Walsall and at Rushall,
opposite the church, and was divided into
six different varieties:
1. |
Black Bothum |
2. |
Gray Bothum |
3. |
Chatterpye, being the colour
of a magpie |
4. |
Gray measure |
5. |
Mush |
6. |
White measure |
The two first are
seldom made use of, they are so very mean;
the two middle sorts but indifferent; the
two last, the principal sorts, but Mush the
best of all, a small comby-stone, othersome
round and hollow, and many times filled with
a briske sweet liquor, which the workmen
drink greedily, so very rich an ore that
they say it may be made into iron in a
common forge.
I think that the sweet
liquor that attends some of the iron ore,
deserves a little further consideration,
whereof I received a most accurate account
from the Worshipful Henry Leigh, of Rushall,
Esq., in whose lands, particularly in the
Mill Meadow, near the furnace in the Park;
in the Moss Close, near the old Vicarage
house; and in the furnace piece or Lesow, it
is frequently met with amongst the best sort
of Ironstone called Mush, in round or oval,
blackish and redish stones, sometimes as big
as the crown of ones hat, hollow and like a
honeycomb within, and holding a pint of this
matter, of a sweet sharp taste, very cold
and cutting, yet greedily drank by the
workmen.
After many enquiries
from old miners in the district, I have been
unable to find out anything definite
respecting this liquor. The ironstone is now
practically extinct, but traces of its
former existence are still to be found. The
ore from Rushall and Walsall - which latter,
however, was not quite so good, was used for
making tough iron, out of which the best
wares were made.
Limestone was dug all
about Walsall, particularly in the lands of
the learned Henry Leigh, Esq., where it lies
in beds for the most part horizontally. The
lime burners here were much more adroit than
those of other neighbourhoods.
The Ladypool Furnace at
Rushall supplied some excellent tough iron,
but softer iron, tin, copper, brass, lead,
resin and sal-ammoniac had to be imported
into the locality. |
|
During the next two hundred years, Walsall would grow into an
affluent manufacturing town, greatly helped by the canal, and
improvements to the roads, and transport. The industries so far
mentioned were small businesses, employing relatively few people,
but that would all change with the coming of factories, and mass
production. |
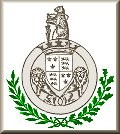 |
|
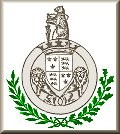 |
|
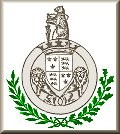 |
Return to 16th, 17th centuries |
|
Return to
the beginning |
|
Proceed
to The 18th Century |
|