The Industrial Town
Locks and Keys
|
Willenhall's manufacturers, like those in the neighbouring
towns, originally worked in small workshops, often in a small
yard behind a family home, where at times the whole family would
be involved in the manufacturing process. As time progressed,
the town's industry was dominated by the lock and key makers. By
the 1850s when lock factories began to appear, there were more than
300 lock makers, 90 key makers, and a dozen or so key stampers,
working in small workshops throughout the town.
As the number of manufacturing firms increased, and the local
transport network improved, large factories were built,
completely changing the Black Country landscape. The factories
increased in size and number. By the Second World War there were
around 200 factories in the town, both large and small, along
with 40 or so workshops.
An important development happened in 1830 when James
Carpenter and John Young designed a door rimlock with a perpendicular action,
which led to the development of the modern mortice lock.
Carpenter and Young had a joint patent which they agreed to
divide into two halves, giving Young the right to make mortice
locks, and Carpenter the right to produce a perpendicular action
rim lock, which became known as "Carpenters lift up lock". His
business grew and he built a large factory in New Road, known as
Summerford Works. James' daughter, Harriet married James Tildesley.
When James Carpenter died in 1844, John Carpenter
and James Tildesley inherited
the business, Carpenter and Company, which in 1851
became Carpenter and Tildesley. James dissolved his
partnership with John Carpenter and became the sole
owner of the company. |
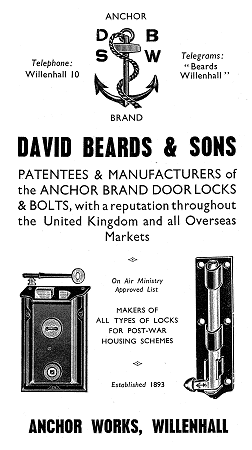
An advert from 1938. |
James Carpenter was an ardent church goer who
became a Wesleyan Methodist due to the antics of the
Rev. William Moreton, curate of St. Giles' Church.
He was a keen supporter of Wolverhampton's Member of
Parliament, C. P. Villiers, and is buried in a vault
on the east side of Union Street Methodist Church. |
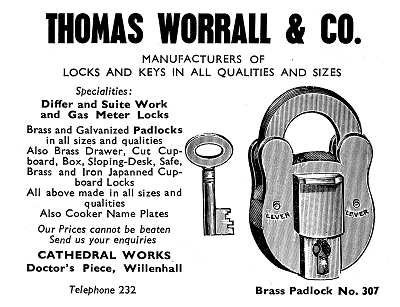
An advert from 1938. |
All kinds of locks were produced in the town, including
padlocks, lever locks, and Bramah locks; but another form of
lock, the cylinder pin tumbler lock, would revolutionise the
local industry, leading to several large factories, and greatly
increased production. |
|
|
Read a report about a
Willenhall keymaker and his wife in 1841 |
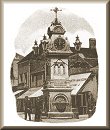 |
|
|
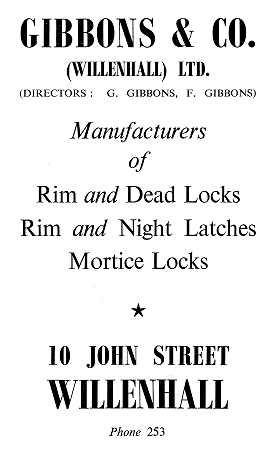 |
|
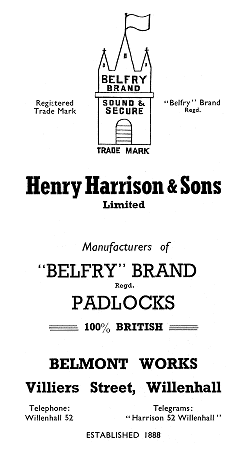 |
Two adverts from 1938. |
|
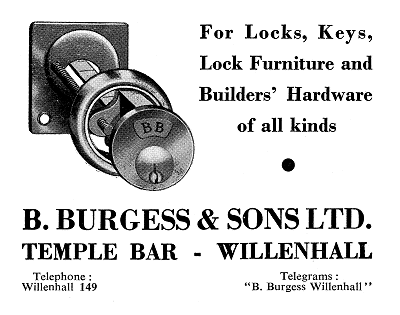
An advert showing a pin
tumbler lock, from 1938. |
One of the town's largest lock factories, which stood in Wood
Street, was originally built by H. and T. Vaughan, a business established
in 1856 by Henry, William and Thomas Vaughan, the sons of lockmaker
Able Vaughan. On
6th December, 1869 Willenhall Local Board approved plans for the
factory in Wood Street, and in 1872 approved plans for a second
factory in Union Street.
Around 1910 the company extensively
developed the cylinder pin
tumbler lock which had been invented in America by Linus Yale,
and improved by his son Linus junior. The lock became extremely
popular, and few houses were without them. |
H. and T. Vaughan became the largest
manufacturer of door locks in the world.
Henry Vaughan, son of Abel
Vaughan. He was educated at Wolverhampton Grammar
School, and became a Justice of the Peace for
Staffordshire, and President of the Wolverhampton
Chamber of Commerce. He was also a County Councillor,
and a member of Willenhall School Board. |
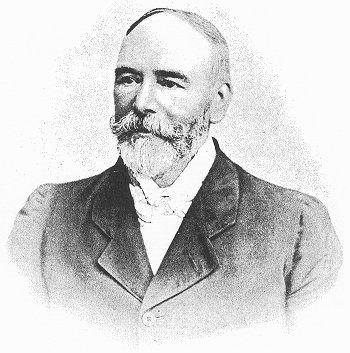 |
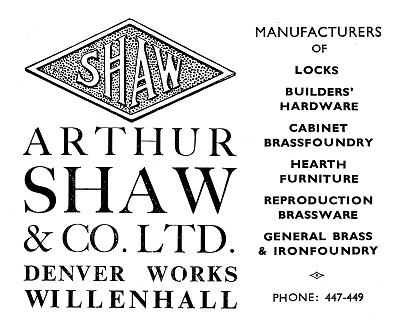
An advert from 1938. |
Thomas Vaughan also became a Justice of the
Peace for Staffordshire.
In 1935 two bells were given to St. Giles' Church
as a memorial to Mr. and Mrs Henry Vaughan.
In 1928, when Vaughan's managing director,
Joseph Starkey died, the family decided to sell
their business to the American firm, Yale and Towne
Manufacturing Company, the original inventors of the
lock.
|
This allowed the American company to begin
producing the 'Yale' cylinder pin tumbler lock in
the UK with a ready made factory and workforce. Cylinder pin tumbler locks were also made in
Willenhall by Josiah Parkes & Sons, Enoch Tonks & Sons, Arthur Shaw &
Company Limited, Century Locks Limited, and J. Legge. |
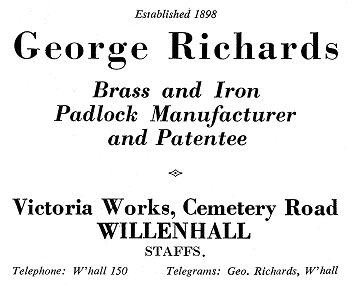 |
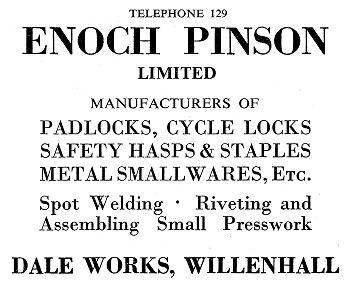 |
Two adverts for padlock manufacturers,
from 1938. |
|
|
Read Samuel
Griffiths' description of Willenhall and
its industries in the early 1870s |
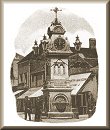 |
|
|
|
Originally
all lock parts were hand made, often being filed from square or
round iron bars. Other parts were forged on the anvil then filed
to final size and shape. Holes were punched-in on a vice, or
anvil, and drilled with a bow and stock. A file was one of the
most important tools used by the lockmaker. Children of only 9
or 10 years old were taught to file, which they did
for many hours each day, continually bending over their work. As
a result of starting at such an early age, many of them
developed humped backs, twisted shoulders, and even bent legs,
which led to the town's nickname "Humpshire".
Some public houses
even had hollows in the wall behind the bench seats, so that
customers could sit upright, with their hump in the hollow. |
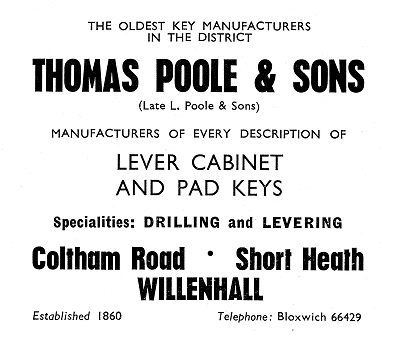
An advert from 1938. |
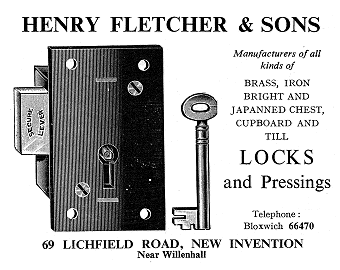 |
|
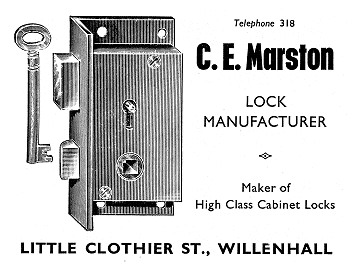 |
Two adverts for cabinet lock
manufacturers, from 1938. |
|
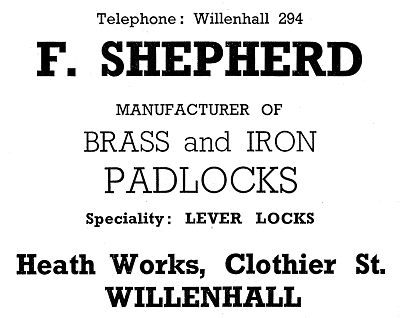
An advert from 1938. |
It took a long time for the lock industry to be
mechanised. Low wages meant that large numbers of
people could be employed in the industry, turning
out vast numbers of locks by hand.
The manufacturing
process was speeded-up in the late 1830s when cheap
malleable iron castings became available. The cast
parts were accurately produced and only needed a
little filing to clean them up, and finish them off.
This process also simplified key making with the
introduction of key castings.
Another
manufacturing aid came in the form of the fly-press developed by
Isaac Mason. The press allowed large numbers of parts to be
quickly and accurately pressed out from a die, saving much time
and labour. |
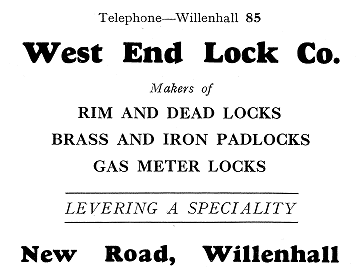 |
|
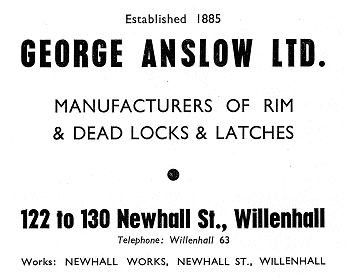 |
Two adverts for rim and dead lock
manufacturers, from 1938. |
|
The most important lockmakers in the town in the late 1800s
included:
Beddows & Sturmey
Carpenter & Tildesley
John Harper and Company Limited
William Harper
Joseph Legge
and Company
John Miners & Sons
Enoch Tonks & Sons
J. Waine &
Sons
H & T. Vaughan |
|
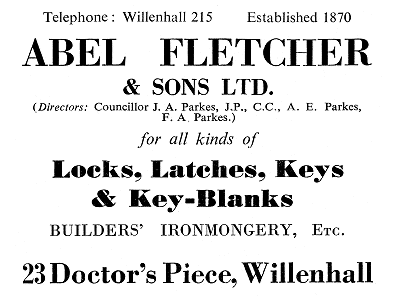
An advert from 1938. |
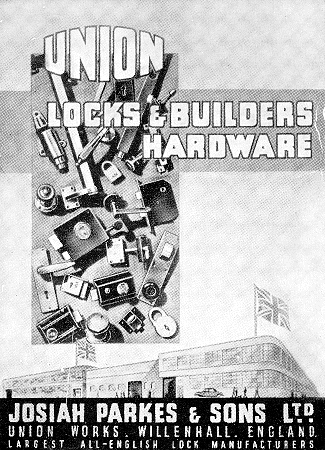 |
|
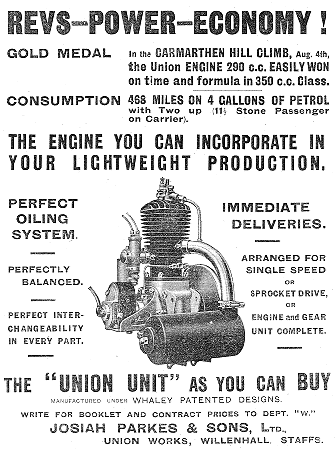 |
Two very different adverts from Josiah Parkes,
the one on the left from 1938, the other
from 1919. |
|
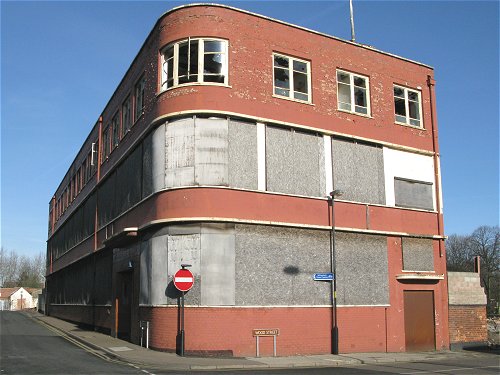
The former offices of Josiah Parkes &
Sons Limited, demolished some years ago.

An advert from 1974.
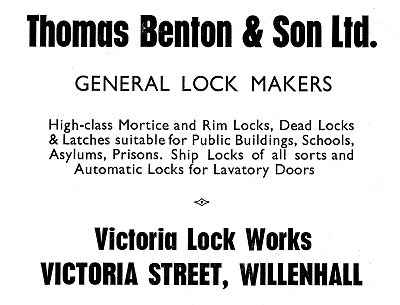
An advert from 1938. |
Eventually the industry did become more mechanised, often with
special-purpose machines that were tended by female workers. The various
components were made by machine, with the final assembly and
finishing carried out by skilled locksmiths. As a result, the
manufacturers produced a vast array of different locks, for
almost every use, and supplied many industries such as
shipbuilding, aircraft building, military vehicle makers, and
the railways, both at home and abroad. Willenhall greatly
prospered thanks to the lock industry, which
survived until recent times. Sadly it began to
decline in the late 1980s, due in the main to
cheap foreign imports. Many businesses were
taken over, or amalgamated, and many others soon
disappeared.
|
In its heyday there were over 4,000 people
employed in the town's lockmaking
industry, but this number rapidly reduced in the 1990s, until
today only a handful of skilled lock makers remain. |
If you want to read more about the local lock making firms,
please look at the Gazetteer of lock and Key Makers, which is
also on this website. Because of this, I have deliberately kept
the description of the industry short, rather than duplicate
what is already there.
View the Gazetteer of
lock and Key Makers |
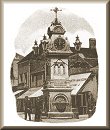 |
|
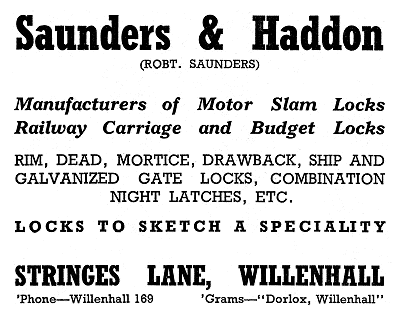
An advert from 1938. |
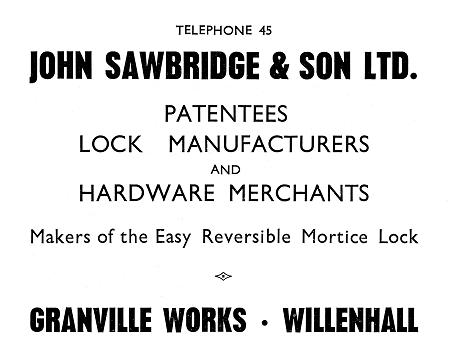
An advert from 1938.
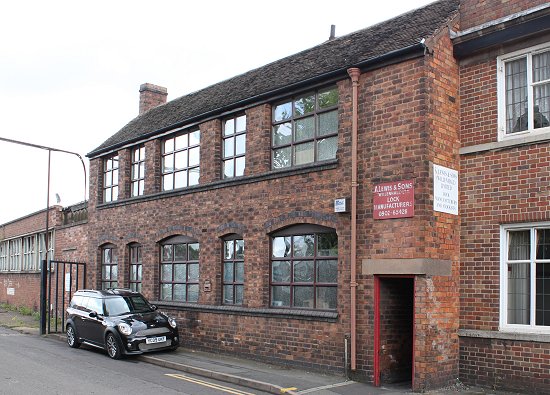 |
One of the last
workshops in the town where locks are still
made. It belongs to A. Lewis & Sons.
The company still
manufactures high quality brass cabinet locks. |
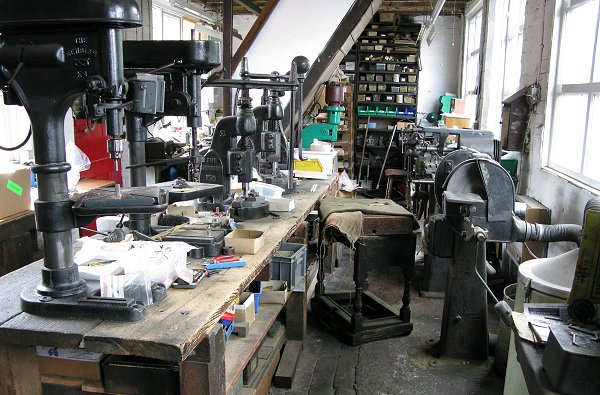
Part of A. Lewis & Sons workshop.
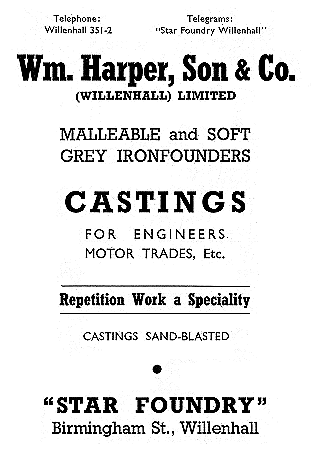
An advert from 1938. |
Like its neighbours, Willenhall had a wide variety of
manufacturers, producing all kinds of metal goods.
There were
brass foundries, die sinkers, drop forgers, grey iron and
malleable iron foundries, bolt manufacturers, and companies
producing all kinds of presswork.
Willenhall became famous throughout the Black Country for its
grey iron castings produced by such firms as John Harper,
William Harper, Charles Perks, William Horton, and Thomas Pedley.
Large numbers of malleable iron castings were
also made in
the town.
Malleable iron was cheaper than steel, and just as
good for many applications. Castings were produced by Charles
Perks, Star Foundry, John Harper, William Horton, and at many
other local foundries.
|
In 1917 Josiah Parkes & Sons Limited acquired Wolverhampton
based Crane Foundry, where large numbers of castings of all
kinds were produced. Crane Foundry remained in their hands until
1945 when it was sold to Qualcast.
There were also foundries producing non-ferrous castings,
including C. & L. Hills, J. Parkes junior, Pioneer Castings,
Wye Foundry, and Knowles Foundry.
|
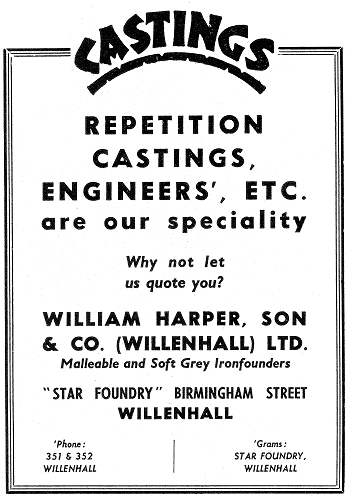
An advert from 1958. |
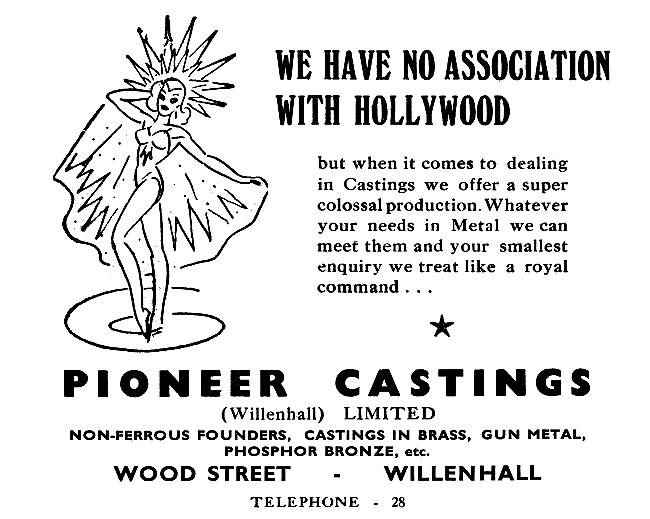
An advert from 1953.
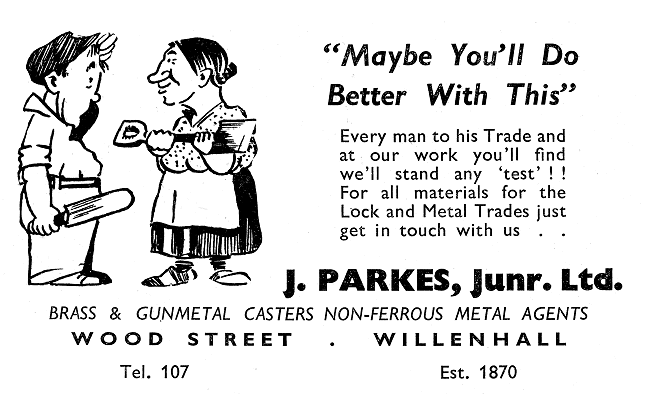
An advert from 1953.
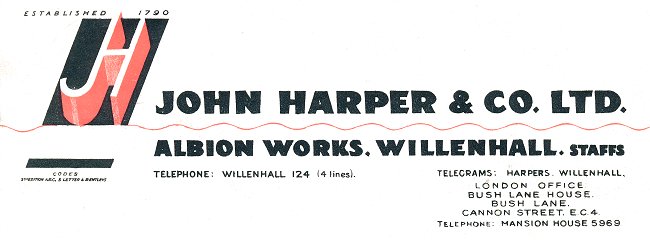
A company letterhead from 1936.
John Harper was second son of John Harper
senior, a hardware merchant in Willenhall. John
Harper junior became a Justice of the Peace for
Staffordshire, County Councillor for North Bilston,
and served on the Willenhall School Board. He was a
staunch Liberal, and close friend of C. P. Villiers,
M.P.
He was a prominent Wesleyan and a lifelong
teetotaller. As well as being the principal
shareholder, chairman of the directors, and general
manager of John Harper & Company, he was proprietor
of the Bilston Windmill Cement and Plaster Company,
and a Fellow of the Imperial Institute.
He extensively travelled throughout the world. |
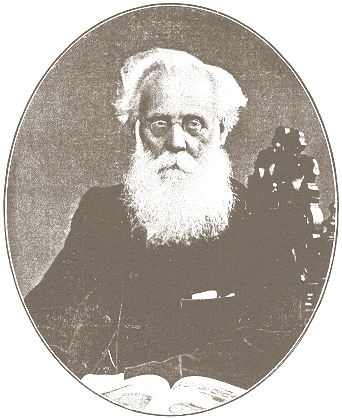
John Harper junior. |
|
|
Albion Works, one of the oldest factories in
Willenhall, run by John Harper & Company Limited,
was founded in 1790. The firm not only
produced locks, but also a wide range of
products.
Read a history of the
company |
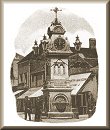 |
|
|
|
|
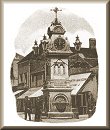 |
Read the story of 'The Old Works', produced
by John Harper & Company Limited in 1950. |
|
|
|
|
Read an
Albion Works Bulletin from John Harper &
Company Limited
for June 1951. |
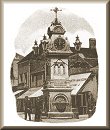 |
|
|
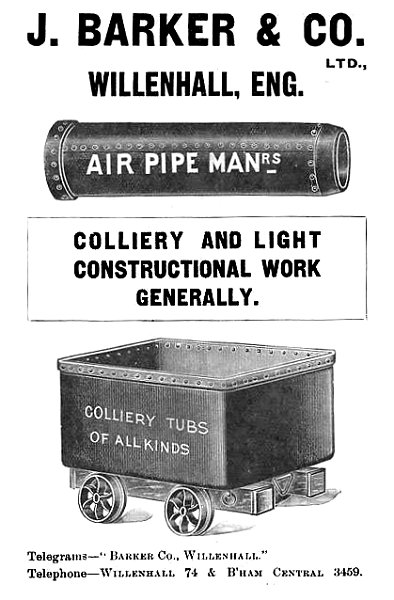 |
Another once-well-known Willenhall company
was Ash Foundries Limited in Wood Street,
founded in 1908. The firm originally traded as
Arthur Ash & Company until 1948 when it became a
limited company. All kinds of small repetition
grey iron castings were produced for many
industries, particularly the local lock trade
which required small thin-section machineable
parts.
In the late 1940s the foundry was
rebuilt and new machines were added to widen the
product range to include castings for textile
and agricultural engineers. There was also a
jobbing section where larger castings could be
produced, and an up-to-date pattern shop. The
larger castings included press beds for machine
tool manufacturers. |
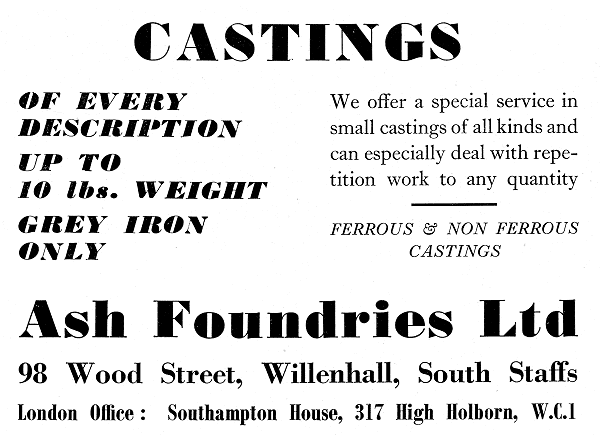
An advert from 1954.
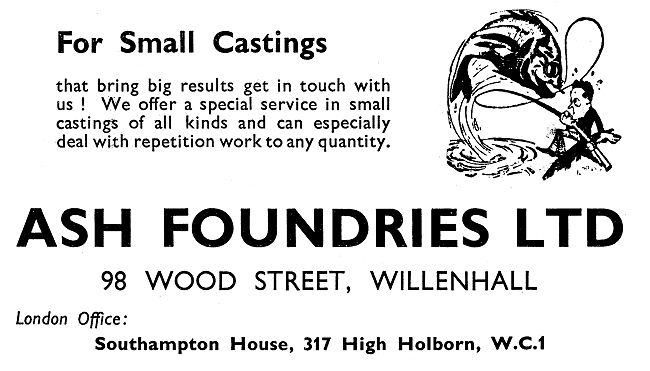
An advert from 1953.
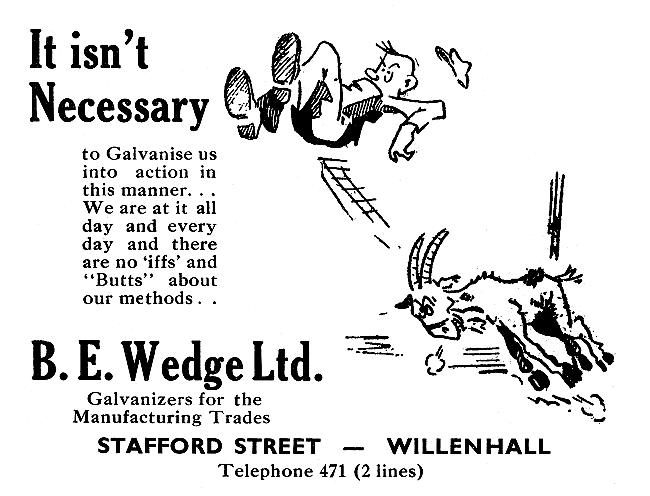
An advert from 1953.

From the 1976 edition of the
Walsall Official Handbook.
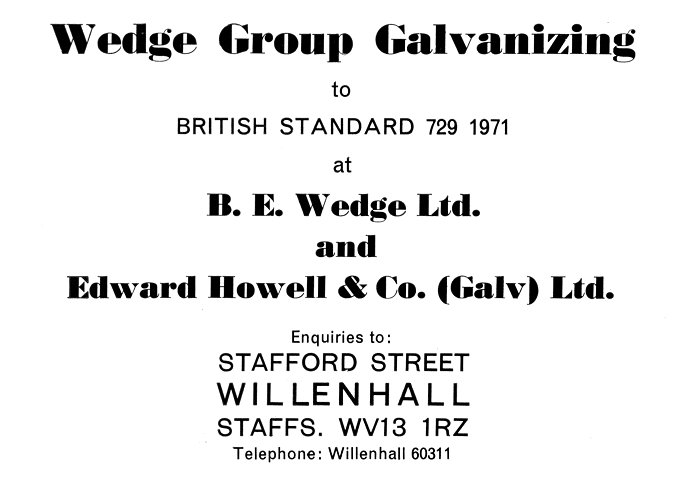
An advert from 1976.
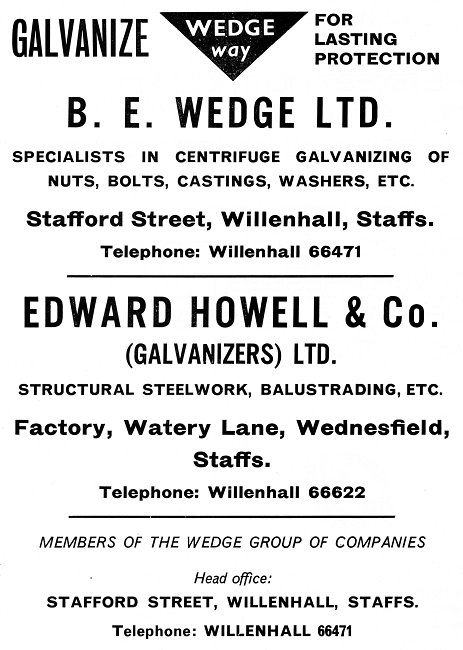
An advert from 1974.
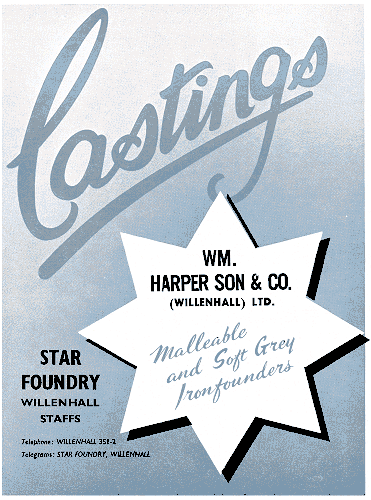
An advert from 1954. |
William Harper Son & Company were another
firm, specialising in repetition work,
particularly for engineering firms, and the
motor trade. The business was based at Star
Foundry in Birmingham Street, where castings
were produced in malleable and soft iron.
Many of Willenhall's foundries were great
innovators, constantly developing new techniques
to keep ahead of the competition. One such
company, A. Fryer & Sons Limited, founded in
1903, produced castings using the Shell method,
which were cleaner and more accurate than
castings made using traditional techniques. The
castings had such a fine finish, and were so
accurate that machining was often unnecessary.
Castings were produced for a wide range of
industries, in particular electrical
engineering, building and the motor trades.
The factory had a modern shot blast plant
where work was done for outside companies, and a
large stock was kept of chill cast phosphor
bronze rods, both solid and cored, for sale to
the trade. |
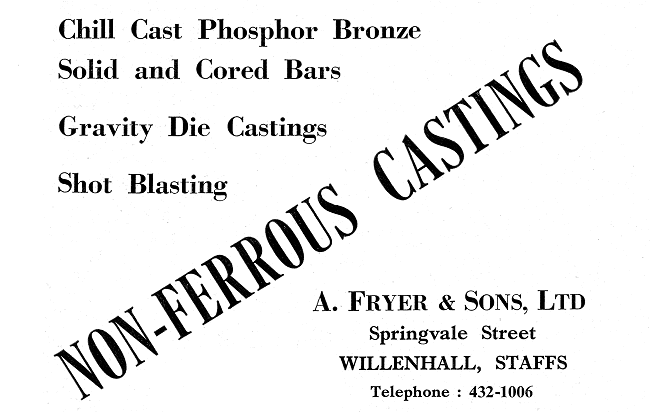
An advert from 1954.
H. & J. Hill were based in Walsall Street on
a site purchased from John Harper & Company
Limited. The firm specialised in malleable and
soft grey iron castings for all trades, and
produced annealing pans and hardening pots.
The business went into liquidation on 5th
May, 1981. |
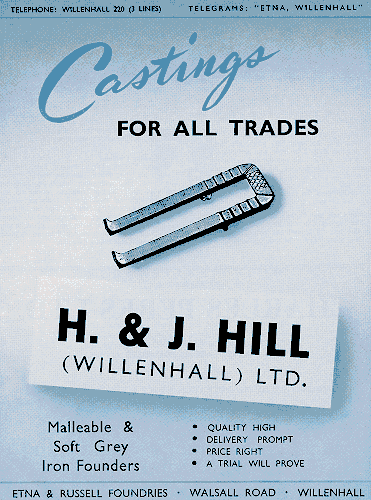
An advert from 1954. |
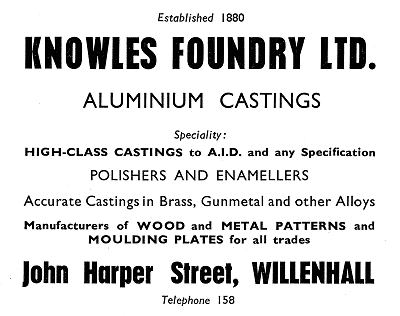 |
Knowles Foundry in John Harper Street was
founded in 1880 to produce small brass castings
for the local lock trade. The firm's product
range greatly changed in the intervening years
to include castings in aluminium alloy,
gunmetal, phosphor bronze etc., for many
industries including electrical engineering,
shipbuilding, and textiles. Aluminium alloy
castings were produced up to two hundredweights,
particularly for petrol and diesel engines, fire
engine-fittings, textile and machine tools,
emulsifiers, traffic signs, bus and coach
fittings, electrical switchgear, lighting
fittings, and outboard engines. Aluminium
gravity die castings were also made. The pattern
shop produced numerous patterns of all kinds for
the trade. |
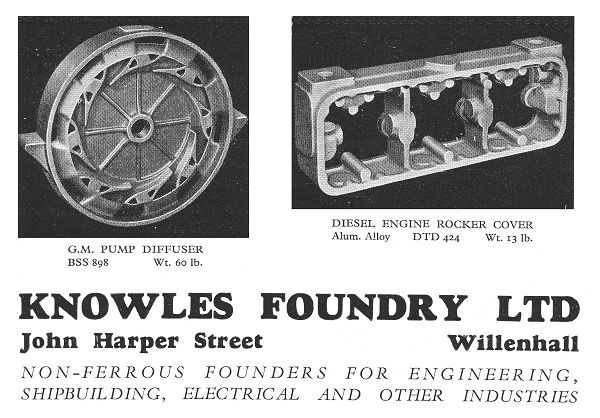
An advert from 1954.
|
|
Read about C. & L.
Hill Limited brass, non-ferrous, and iron
founders |
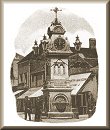 |
|
|
One of Willenhall's notable foundries was
Victoria Foundry in Stringes Lane, run by Arthur
Tipper Limited, grey and malleable ironfounders,
producers of conduit tubes and fittings, and
makers of a vast range of builders ironmongery. |
The firm produced almost every kind of
builders' fittings including door and gate
bolts, shelf brackets, Suffolk and Gothic
latches, axle pulleys, tee and butt hinges, hat
and coat hooks, shelf brackets, letter plates,
sash fasteners, fanlight stays and catches, and
casement stays and fasteners. Their delivery
vans operated over most of the Midlands, and
their London office and warehouse supplied
London and places as far afield as the south and
east coasts.
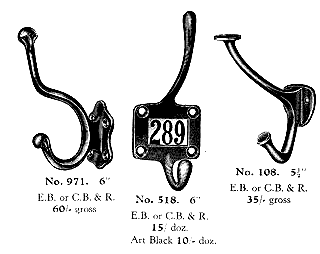
Some of Tipper's coat
hooks. |
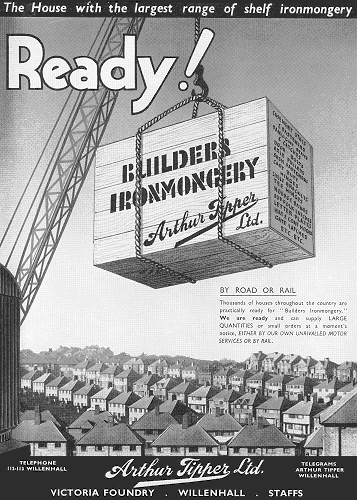
An advert from 1954. |
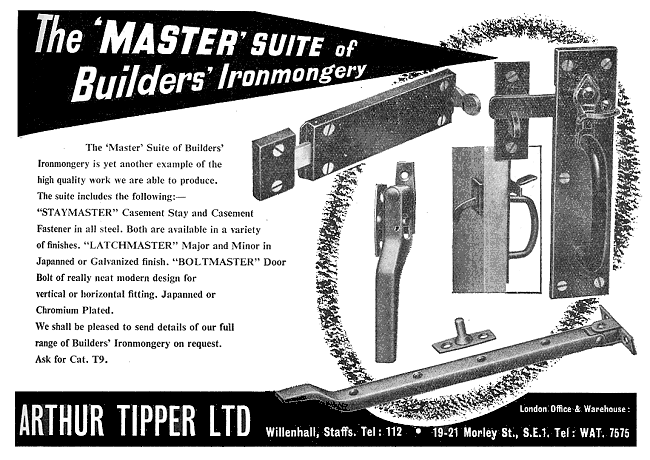
An advert from 1958. |
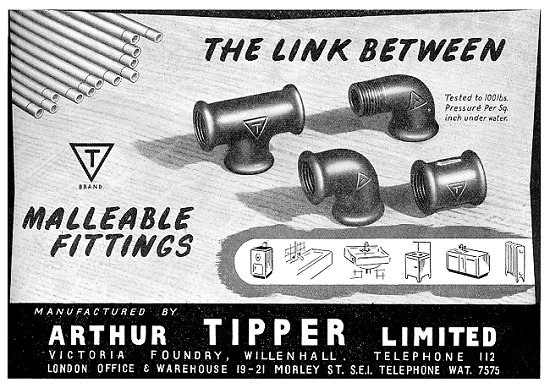
An advert from 1958. |
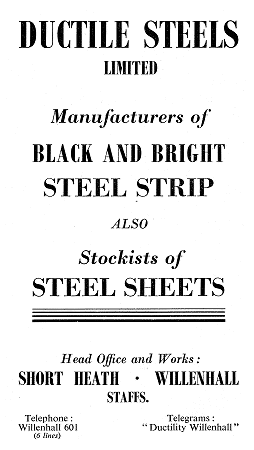 |
One of the many local industrial success
stories is that of the Ductile Steels Group,
which started in 1915 when Mr. Frank Hall
acquired a fifty percent stake in Stanley &
Hawker, a steel merchandising firm. He became
sole proprietor in the early 1920s after the
death of his partner. In 1924 Mr. C. H. Batten
joined the firm, and became a partner in 1931.
The business became the largest stockholder of
cold-rolled steel strip in the country,
importing over 6,000 tons per year. In the early
1930s Frank Hall foresaw the coming of the 33⅓
percent tariff that was to be imposed on all
imported steel, and so he decided that the
company should produce its own steel. He purchased two
second-hand cold rolling mills, and had a
'coffin-pot' annealing furnace built in a small
factory on a levelled dirt tip in Stringes Lane.
Within a short time cold rolled steel strip was
in production.
Ductile Steels Limited was formed as a
private company, and two further cold rolling
mills, and a hot rolling mill were installed at
the factory. The business prospered and became a
public company in 1936 incorporating Starkey &
Hawker, whose stock and machinery were moved to
the Stringes Lane site. Although the stocks of
steel strip were gradually
reduced, the stocking and shearing of steel
sheets continued, and became an important part of
the business.
|
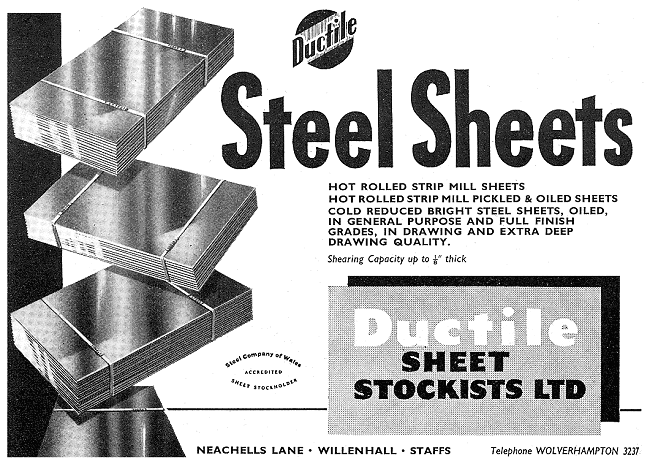
An advert from 1958.
The Willenhall factory expanded again in 1945
when the manufacture of cold-formed sections was
added to the product list. The firm purchased
Sections & Mouldings (Birmingham) Limited and
transferred its plant to the Stringes Lane
site. In the same year the firm purchased The Monmore Green Rolling Mills Company (1924)
Limited at Wolverhampton, which was in
liquidation. The name was changed to Monmore
Conduits Limited, and the factory began to
produce electrical conduits made from Ductile's
hot rolled steel strip. In order to improve
the sales of electrical conduit, the firm
purchased the conduit fittings supplier, Seal
Conduit Company Limited in 1946 and moved the
business to the Monmore Green site. A warehouse
was also opened in Coventry to stock the firm's
conduits, along with fittings, certain
electrical goods, and a quantity of Ductile
steel flats and sheets. 1946 also saw the
formation of Metalon Steels Limited at Jubilee
Works, Short Heath to turn Ductile steel strip
into galvanised coils. In 1947 the firm acquired
press maker Samuel Griffiths (Willenhall)
Limited, based in John Harper Street,
Willenhall to make all of the machinery for the
mechanisation and development of the Ductile
group. |
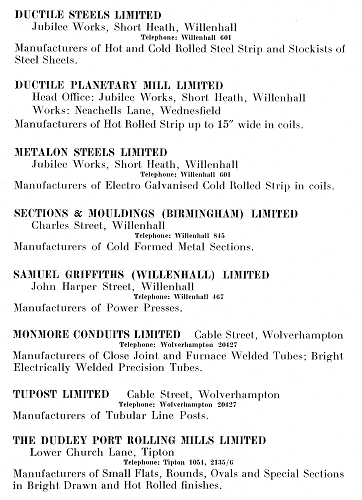 |
Expansion continued in 1948 with the
acquisition of Dudley Port Rolling Mills
Limited, of Lower Church Lane, Tipton. This was
one of the most up-to-date and efficient rolling
mills of its kind in the country. The firm
produced rolls, small flats, strip, rounds,
ovals, and special sections in bright drawn and
hot rolled finishes.
This operation was expanded
by the purchase of Shropshire Steels whose
entire operation was transferred to Dudley Port.
In 1953 Ductile formed Ductile Planetary Mill
Limited in Planetary Road, Wednesfield to
operate a newly installed hot steel rolling
mill, the first of its kind.
The new process
called "Planetary Rolling" was named after
Planetary Road. In 1963 the group moved its head
office there. |
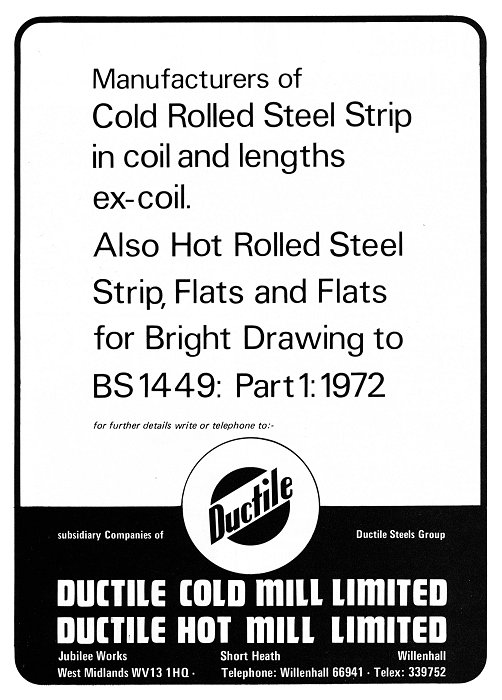
An advert from 1976. |
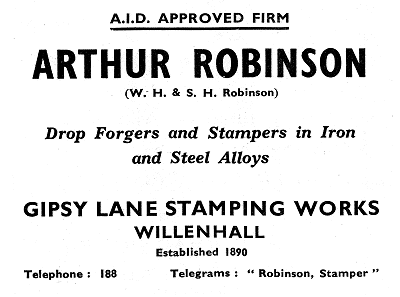
An advert from 1938. |
Another important local industry, which still survives today is
drop forging. It began in Willenhall in 1812 when John Grimley
moved here from Birmingham and began to produce
keys, using a drop hammer. The industry rapidly
grew to become an important part of local
manufacturing. A vast range of products were
produced, including bolts, hinges, letter boxes,
staples, and every kind of ironmongery. Parts
were also produced for the shipbuilding industry, cycle
manufacturing, and vehicle manufacturing. |
Some of the main companies were:
Armstrong Stevens
Criterion Stampings
Vaughan
Brothers
A. Vaughan,
E. Nicklin & Sons
Platts Forgings
Victoria Drop Forgings
G. A. Tildesley & Co. Ltd. |
The thud of the drop hammers would have been a familiar sound in
the town.
It could be heard until recently around the premises of
George Dyke Limited in Doctors Piece, now closed, and can
still be heard at W. H. Tildesley
Limited in Bow Street. |
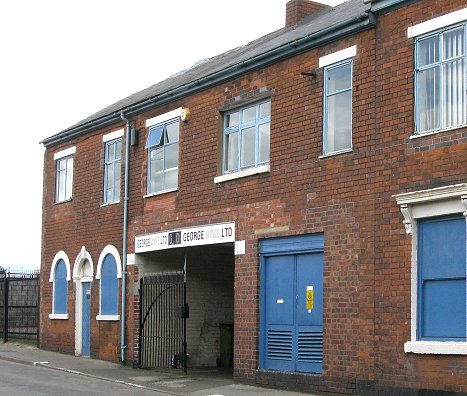
George Dyke Limited in
Doctors Piece, now derelict. |
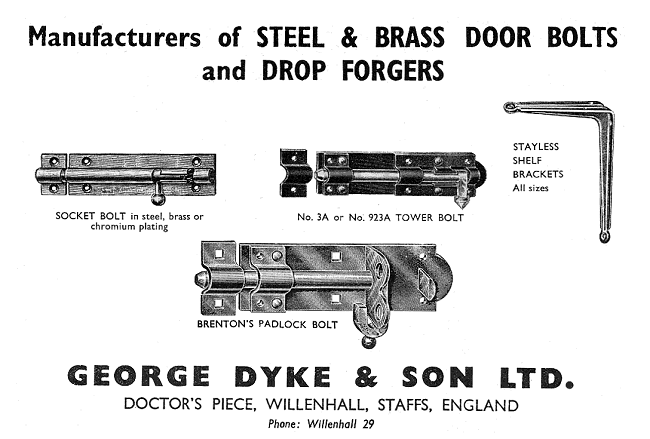
An advert from 1958.

The stone panel on the
side of the derelict factory built by E. Nicklin
& Sons, dropforgers, in 1894. |
~
E. Nicklin & Sons'
factory, now derelict, on the corner of Field
Street, and Round Croft. It was later occupied
by Henry Ellard and Sons Limited. |
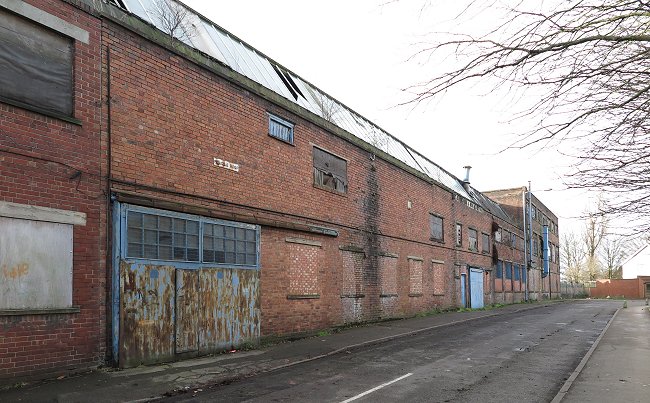
A final view of the
factory, as seen from Round Croft in January
2015. |
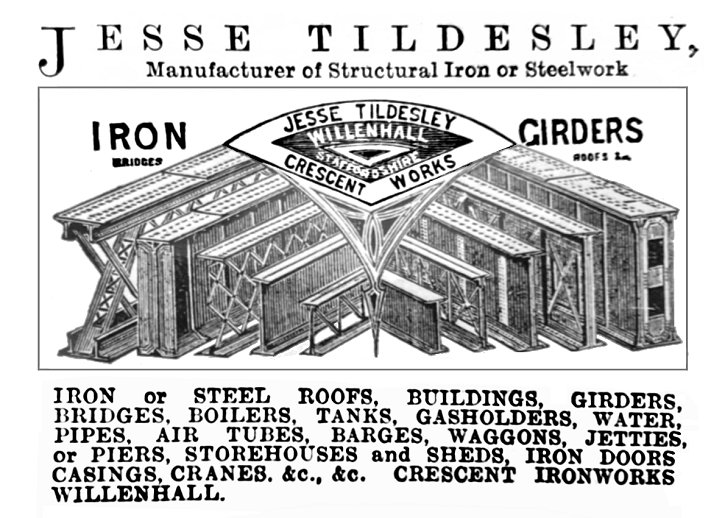
An advert from 1892.
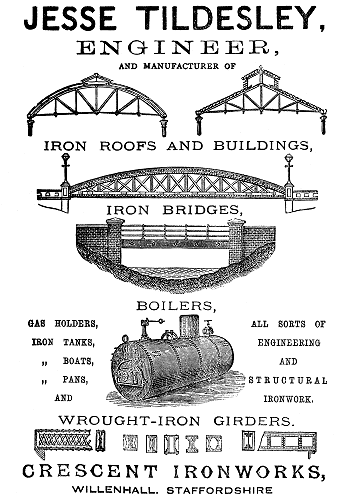 |
An advert from 1884. |
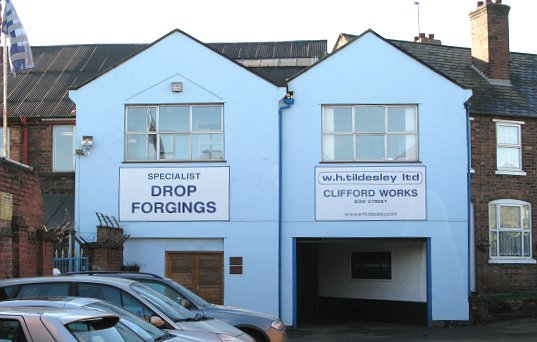
W. H. Tildesley's Clifford Works in
Bow Street.
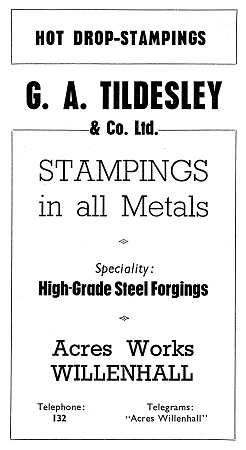 |
G. A. Tildesley and
Company Limited were one of the larger drop
forging companies in the town.
There were also a number
of patternmakers, such as the Central
Patternmaking Company, catering for the numerous
foundries in the area.
Both adverts are from
1938. |
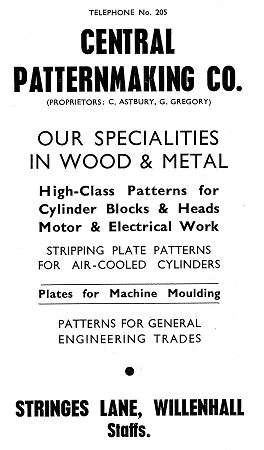 |
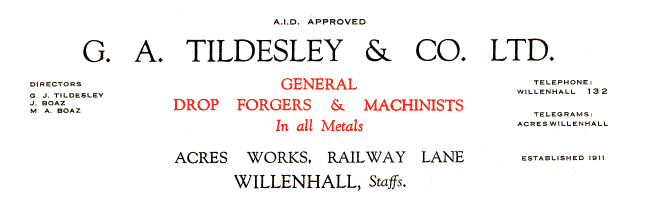
A company letterhead from the mid
1960s.
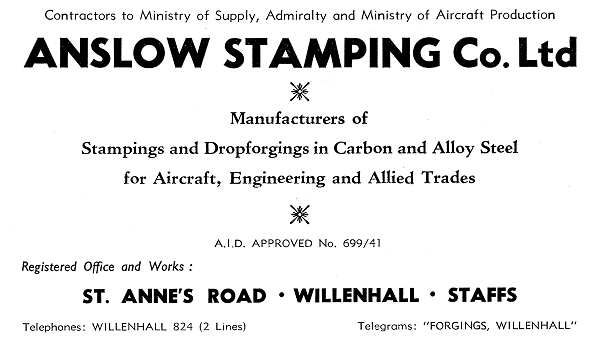
An advert from 1954.
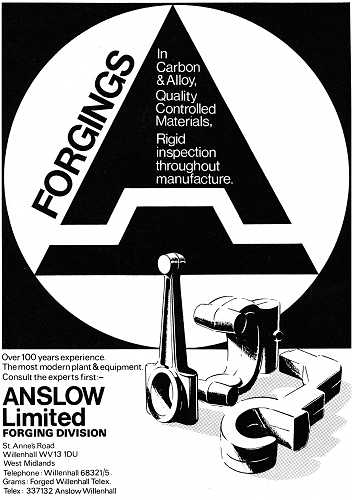 |
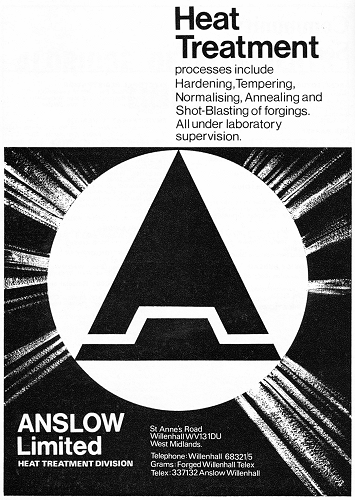 |
Two adverts
from 1976. |
|
Vaughan Brothers (Drop forgings) Limited of
Eagle Works, Somerford Place, Willenhall was founded
in 1874. It became a private limited company in
1936, and went public a year later. All kinds of
drop forgings were produced including parts for
vehicle manufacturers, railway companies, aircraft
manufacturers, aircraft engine manufacturers,
fittings for ships, and parts for agricultural
machinery.
The firm also carried out machining and produced
a number of finished products including jacks, gear
boxes, and many tools. Another product was Eagle
brand spanners.
By the 1960s the company employed over 300
people.
The Firm closed in the recession which began in
the late 1980s. The business was taken over by a
company called Shakespeare, which only lasted for a
short time.
Eagle Works has since been acquired by the
Middleton Paper Company
Limited, paper merchants and convertors,
specialising in paper sheeting, rewinding,
rewrapping, and recycling. |
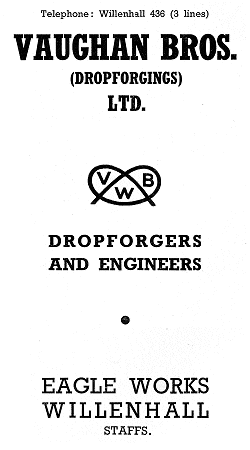
An advert from the late 1930s. |
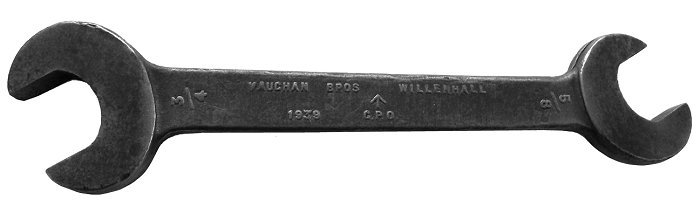
A Vaughan Brothers spanner, made for
the GPO in 1939.
The Middleton Paper Company moved to a new
site and so for several years Eagle Works was
unused. Walsall Council's planning committee
gave permission for the site to be redeveloped
into 1 and 2 bedroom apartments and 2, 3 and 4
bedroom houses. Demolition of the old factory
began at the end of 2022.
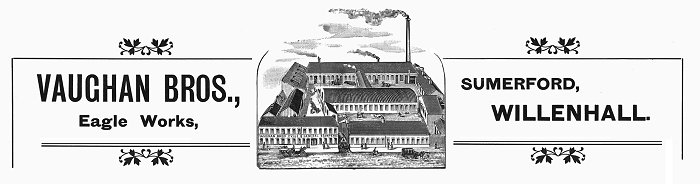
An old letterhead. |
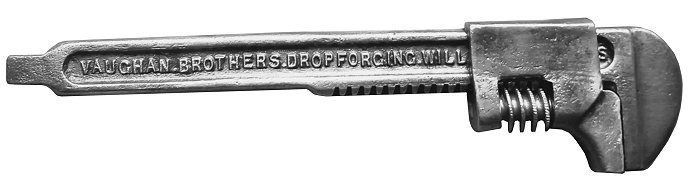
A Vaughan Brothers adjustable spanner.
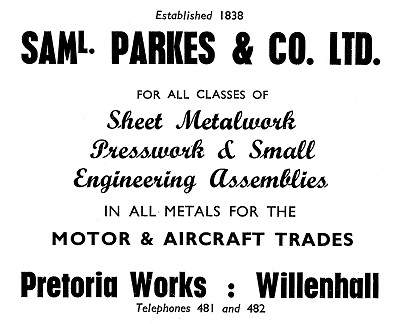
One of the local firms that made parts for vehicle
manufacturers. An advert from 1938. |
Vehicle manufacturers were supplied with all
kinds of pressings from several locally based
firms including Thomas Herbert and Company, George
Carter and Sons, and the Willenhall Motor Radiator Company,
founded in 1919. During World War 2 the company manufactured
parts for the De Havilland Mosquito, and in 1951 began to
produce steel cabs for ERF trucks. In the late 1950s DKR
scooters were built at the factory, and in the 1960s sheet metal
motor components including wings, bonnets, petrol tanks, and
shields were supplied to vehicle manufacturers. Body pressings
and assemblies were also supplied to Ford. The company still
exists today as part of Caparo Modular Systems Limited, a
steel engineering and automotive group, based in the UK, India
and the USA. |
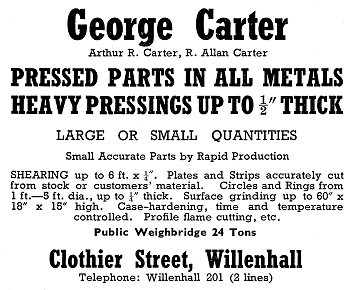 |
|
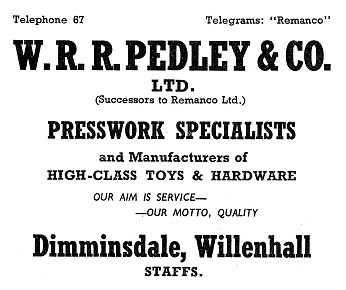 |
Two of the
many local firms producing
presswork in the late 1930s. |
George Carter (Pressings)
Limited was founded by
George Carter in 1830. He
was a general smith,
specialising in hand-forged
vices and hand and power
presses.
He was succeeded by his
son, also George Carter, who
specialised in hand-forged
press tools.
The firm was then taken
over by the founder's
grandson, Robert Carter, who
improved the firm's
manufacturing processes.
On his death in 1925, his
two sons Arthur and Allan
Carter took over. The firm
became a private limited
company in 1946 and by the
1960s employed around 180
people, producing general
presswork for the motor
trade.
Sadly
George Carter (Pressings) Limited
closed in May, 2009. |
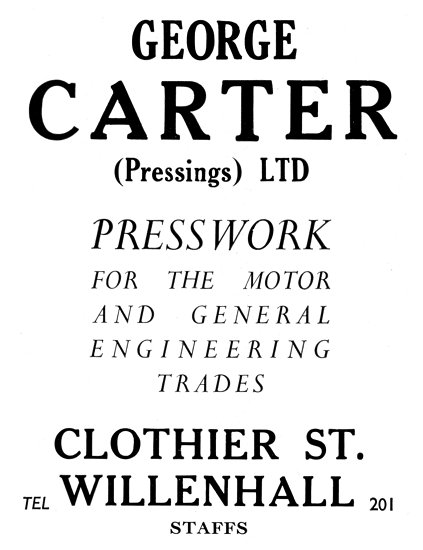 |

An advert from 1958.
|
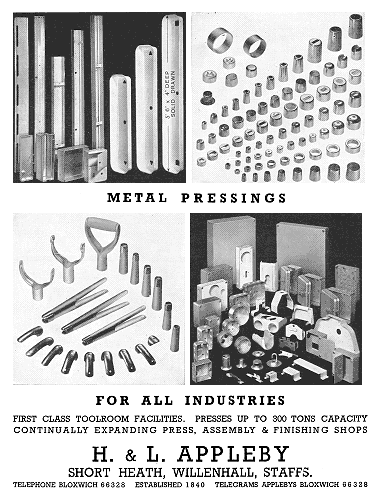
An advert from 1954. |
Another firm, once-well known for high grade
metal pressings was H. & L. Appleby in Forge
Road, Short Heath. The business, founded in
1840 had a well-equipped factory with a toolroom
complete with the latest machine tools, a
jig-boring facility, and a large press shop
housing thirty five power presses with
capacities up to three hundred tons.
A large extension, built in the early 1950s,
was used for the assembly and finishing of the
firm's products, including welding, riveting,
painting, enamelling, and machining.
The firm survived for over one hundred and
fifty years. It was dissolved on 6th October,
1998. |
Willenhall firms produced component parts for almost every
industry.
Castings and pressings were made for lockmakers (in
grey iron, malleable iron, brass, bronze, and gunmetal), and for
gas stove and cooker manufacturers, bedstead makers, the
electrical industry, tool manufacturers, fittings for travel goods,
vehicle manufacturers, etc., etc. |
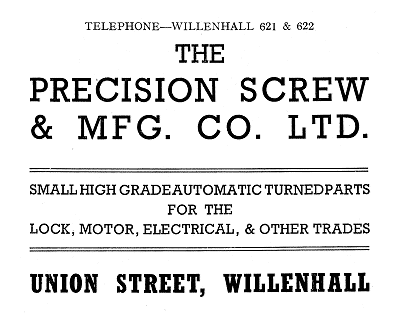
One of the few screw
manufacturers in the town. |
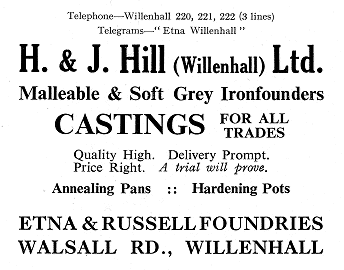 |
|
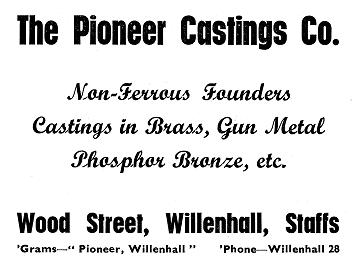 |
Two of the
many foundries in the area. |
|
An advert from 1861.
Another metal working company was the Metal
Products Company (Willenhall) Limited, based in
Neachells Lane. The firm was founded by James W.
Whitehouse in 1908 to reclaim and refine metal.
It originally traded as J. W. Whitehouse & Sons.
The factory included a ferrous foundry, a brass
foundry, and a non-ferrous foundry which
produced metal ingots. The brass foundry closed
in 1914 in order to make space for the refining
part of the business. During the First World War
hot metal pressings were produced for shell
fuses, and the company became the first in the
country to make chilled brass bars for
stampings. After the war the firm developed a
process for hardening alloys in ingots,
including manganese copper, silicon copper,
ferro copper, and phosphor copper. In the 1950s
the product range included metal alloys for the
aircraft industry, particularly for jet engines.
In later years development continued with a
range of alloys for use in nuclear power
stations.
The factory grew to cover over 76,000 square
feet, and included an up-to-date and well
equipped research laboratory. The firm had a
large export business and sold products to
almost every country in the world. |
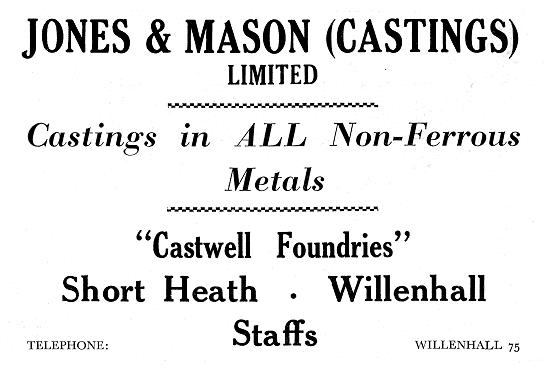
Another non-ferrous
foundry.
Another of Willenhall's diverse industries
was the production of arc welding electrodes at
Invicta Electrodes Limited in Bilston Lane. The
firm, a member of the Owen Organisation,
produced a wide range of electrodes suitable for
welding mild steel, medium high tensile cast
iron, steel reinforcing, and stainless steel.
The electrodes were marketed using the trade
name "Wey", including "Speedway" and "Deepway",
and were produced on machinery built by
companies within the Owen organisation. The
factory was extended during the Second World War
to enable the firm to fulfil a number of
Government contracts which resulted in the
production of millions of feet of
electrodes. The factory had all of the latest
facilities including chemical and mechanical
laboratories, X-ray machines, and microscopy, to
ensure that the products were of the highest
quality. |
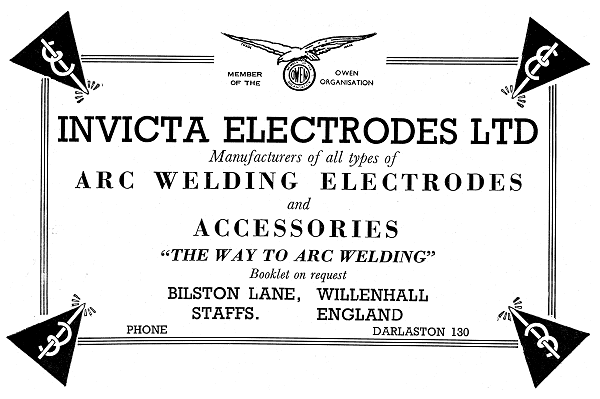
An advert from 1954.
Although the town was dominated by factories working on metal
goods, and known for its lockmaking, there were many other manufacturers and producers of a
wide variety of products, such as those that follow: Presswork specialists W. R. R. Pedley & Company produced high
class toys, the Willenhall Box Company made cardboard boxes of
every kind, Harris & Sheldon Limited made distinctive display
fittings for shops etc., B. E. Wedge Limited galvanised all
kinds of products, H. A. Birch & Company Limited manufactured
electrical resistances, rheostats, and elements, and Grant's
Bakery produced bread and confectionery.
|
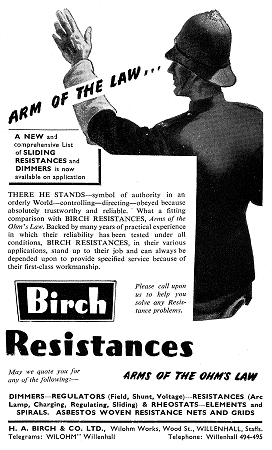 |
|
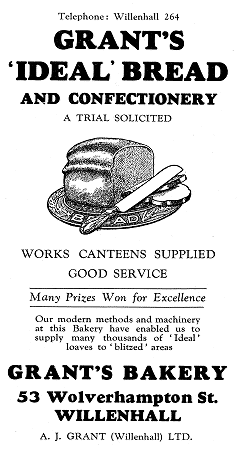 |
Two more
adverts from the late 1930s. |
|
The Union Mill which stood on the corner of Union Street
and Stafford Street, was run by John Austin. He was a miller, baker,
and grocer, who became famous for something quite different.
In
1844 he introduced copper farthing tokens, which were known
as Austin Farthings. In 1853 Austin left Willenhall and moved to Allscott near Wellington, where he founded an artificial manure
works.
He sold his business in Willenhall to Joshua Rushbrooke
who had previously worked at Birchills Mill in Walsall. |
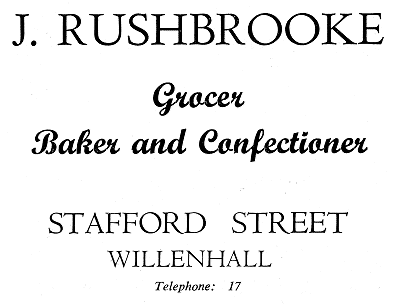 |
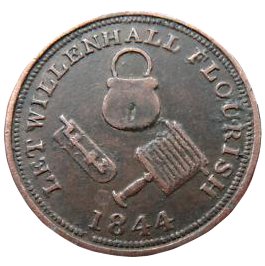 |
|
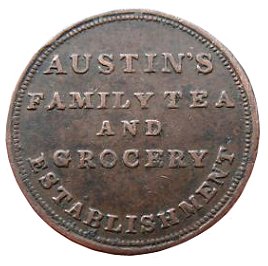 |
Both
sides of an Austin token. |
|
Rushbrooke continued to produce the farthings which still
carried the 1844 date. Although the front remained unchanged,
the reverse side of the token now carried Rushbrooke's name. The
farthing tokens were sold to local traders at the rate of 5
shillings worth of tokens for 4 shillings and ninepence in cash. The tokens continued in circulation until 1860 when new and
smaller bronze pennies, halfpennies, and farthings were
introduced. At the same time severe penalties
were imposed on people using tokens, and so Rushbrooke
immediately called-in his tokens, which cost him a considerable
amount of money, and melted them down. He managed to sell the
copper, and completely recuperate his loss. He married the
eldest daughter of Richard Tildesley in 1849 and they had 11
children. In 1863 he retired, and went to live in Sutton
Coldfield. He was succeeded in the business by his son
Joshua. The family-run concern survived until after the Second
World War, when the building was demolished, as part of the town
centre development scheme. The Rushbrooke farthing name is still
remembered today, because the name of 'The Spring Vale Tavern' in
St. Anne's Road has been changed to 'The Rushbrooke Farthing' in
commemoration of the once well known tokens. |
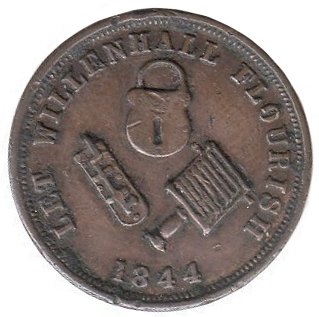 |
|
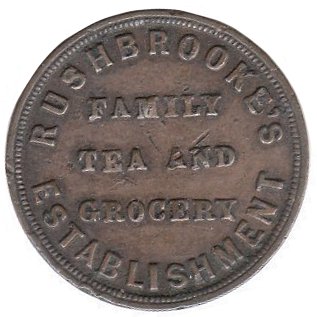 |
Both
sides of a Rushbrooke token. |
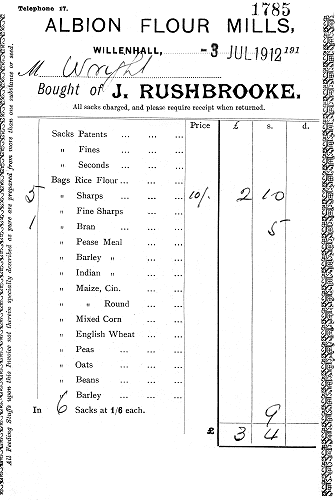
|
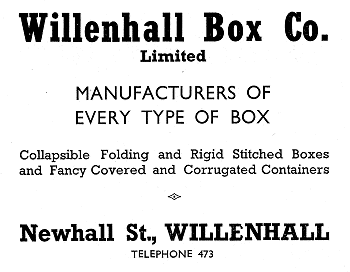 |
Willenhall had its own packaging producer in the
form of the Willenhall Box Company Limited, founded in
1934 to make rigid and folding boxes for Willenhall's
lock makers and hardware trades.
The product range was extended in 1938 when a new
department was formed for the manufacture of fancy
covered boxes and shoe boxes.
In 1946 the factory was re-equipped with the latest
machinery including semi-automatic fed machines which
could efficiently produce boxes in either small or large
quantities. |
Products included rigid, folding, collapsible, and
fancy covered boxes, cartons, and containers for almost
every trade, including boots and shoes, clothing,
electrical goods, plastics, hardware, locks, and buttons
etc. A considerable number of boxes were made for the
aircraft industry and the Ministry of Supply. The firm's
boxes were made to a high standard at an economical
price and so were extremely attractive to manufacturers
of all kinds. |
|
|
|
View some of the products
made in St. Anne's Road by William & H. H. James Limited |
|
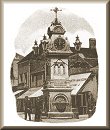 |
|
|
|
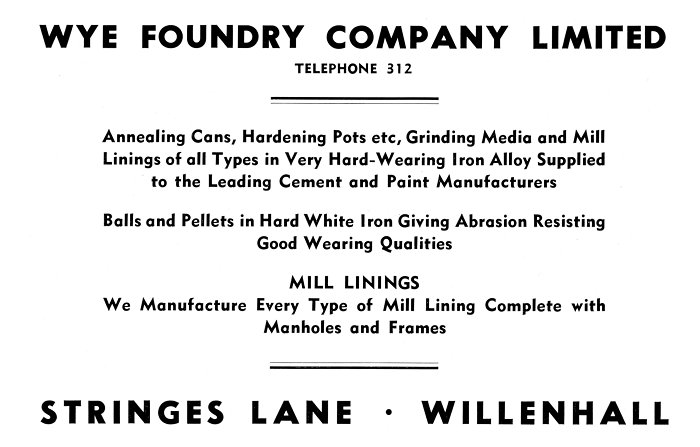
An advert from 1954.
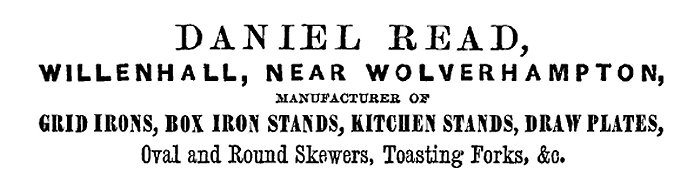
An advert from 1865.
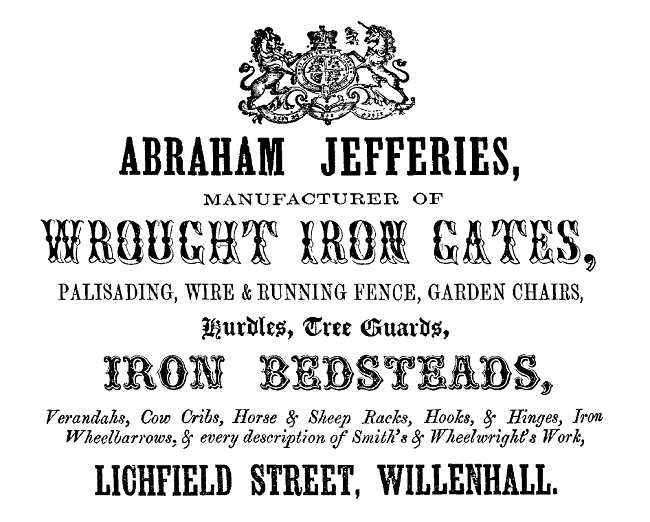
An advert from 1851.
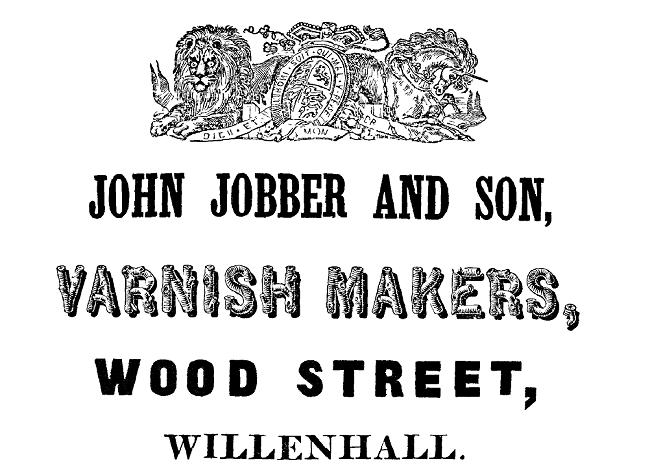
An advert from 1851.
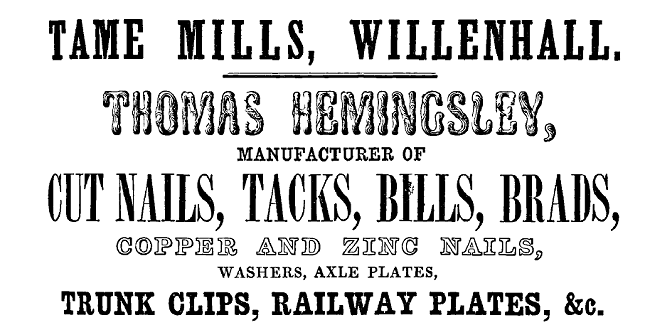
An advert from 1851. 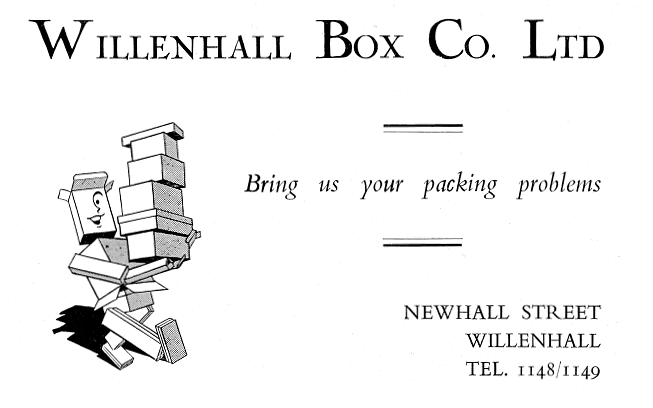
An advert from 1954.
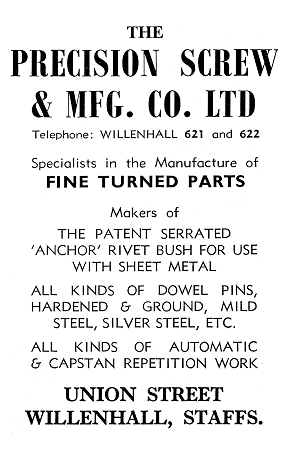 |
|
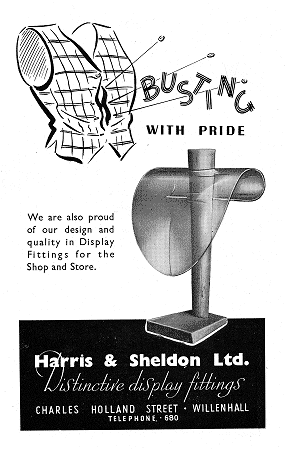 |
Two
of the many and varied industries in the
town. |
|
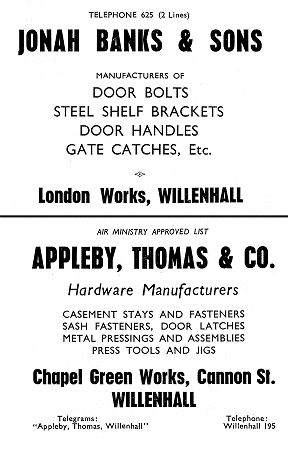 |
|
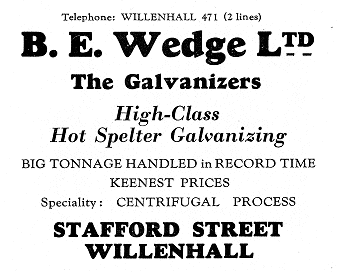 |
Adverts from
the late 1930s. |
|
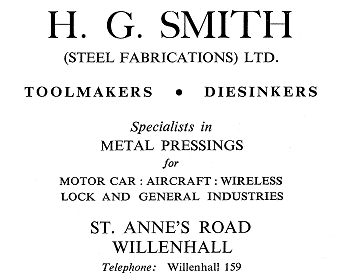 |
|
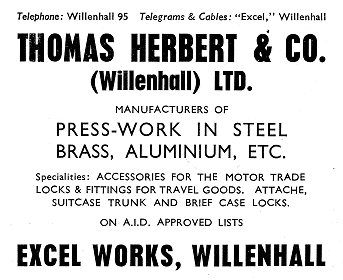 |
More
adverts from the late 1930s. |
|
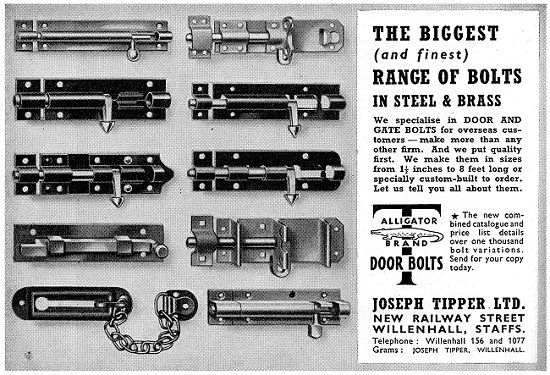
An advert from 1958. |
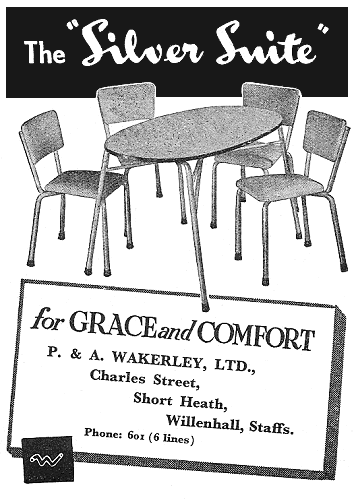 |
An advert from 1958. |
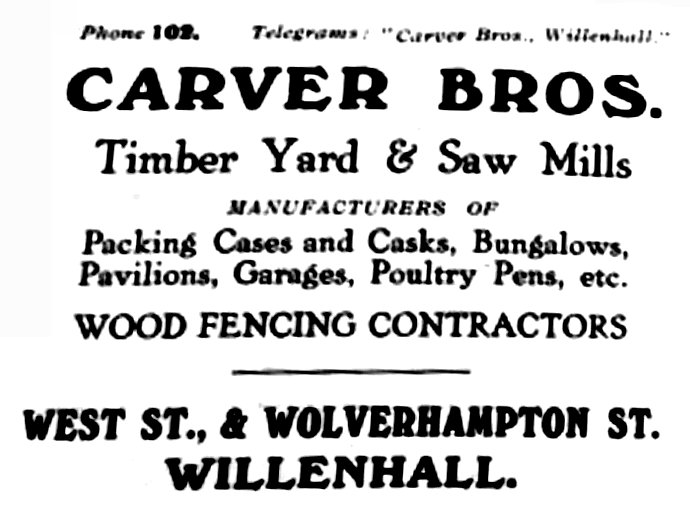
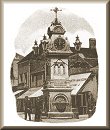 |
|
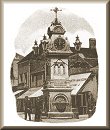 |
|
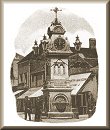 |
Return to
Religion
and Churches |
|
Return to
the contents |
|
Proceed to
Personalities |
|