E.C.C. Products from
the 1950's and 1960's
This section contains details of some of the company's later
products and notable installations. The E.C.C. installed purpose built
equipment for all kinds of industrial uses, much of which is probably still
in use today. The curators recently visited a Wolverhampton nail
manufacturer and noted that the whole factory was driven from E.C.C. motors.
We were told that one of the motors, which must be about 50 years old, and
is in daily use, was actually cleaned and oiled about 15 years ago, and
hasn't been touched since. This shows how well-made and reliable, the
company's products are.
The first transatlantic telephone cable between
Clarenville, Newfoundland and Oban was inaugurated on 25 September
1956. It was designed to link both the United States and Canada to
the U.K., with facilities for links to other European countries. It
provided 30 telephone circuits to America and 6 to Canada, as well
as a number of telegraph circuits to Canada.
E.C.C. designed and manufactured the power equipment for the Oban
terminal station, as is mentioned in the advert on the right. |
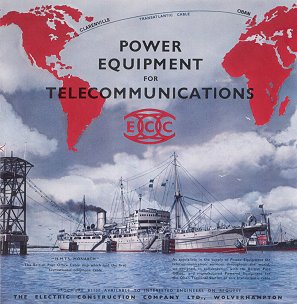 |
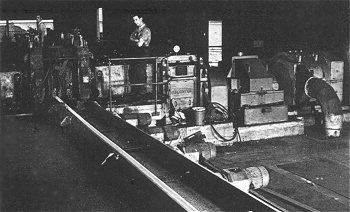
The finishing mill with 750h.p. E.C.C. drive
motors. |
When Bayliss, Jones & Bayliss Ltd., of Cable Street,
Wolverhampton, opened a new rolling mill, it was driven by E.C.C.
motors. More than two hundred motors were used in the system, the
main mill drives producing 3,150 hp. and 4,000 hp. The other four
main motors were housed in the motor room along with the rectifier
and switchboard. These provide the supply to the five variable
speed, 460 volt D.C. motors. |
The supply equipment consisted of four 580/832 KVA
rectifier transformers, feeding four mercury arc rectifiers, each
with an output of 500 kW, at 1135 amps. The E.C.C. Service
Department and the Electrical and Maintenance Department of Bayliss,
Jones & Bayliss, installed the equipment without substantially
effecting production. This was one of the most modern rolling mills
in the Midlands and specialised in the rolling of alloy steels and
carbon steels. |
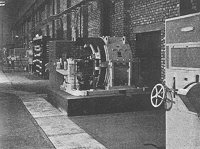
The motor room. |
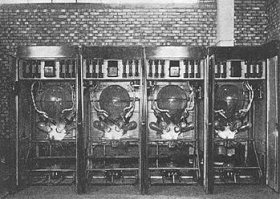
The four mercury arc rectifiers. |
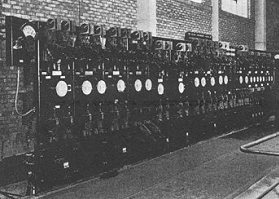
The D.C. Switchboard.
|
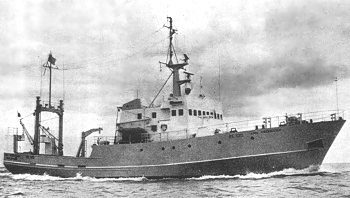 |
The Fisheries research vessell "Arni Fridriksson" was
built for the Icelandic Government, and launched on 1st March 1967.
The ship's electrical system was designed and built by the E.C.C. It
supplied 440 volts, 3 phase at 50 Hz. |
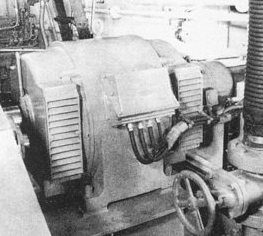
The main generator. |
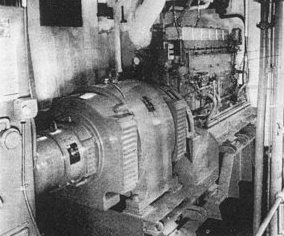
The auxiliary generator. |
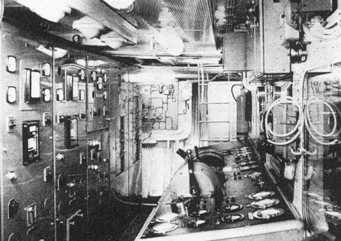
The main control switchboard.
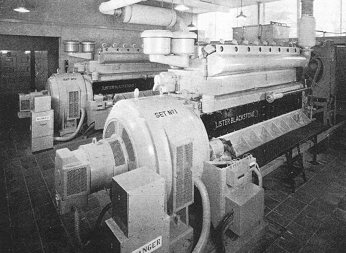
A view of the engine room showing the two main
generators. |
On Friday 9th July 1965 the 2.5 million pound
telephone trunk centre at Woodcroft, Edinburgh, was formally opened
by the Director General of the Post Office. The standby and
continuity power equipment was designed and built by E.C.C. It
consisted of two 300 KVA, 415 volt A.C. generators. They were of the
self-aligning bearing type with overhung exciters. The output
voltage was automatically regulated to within plus or minus 1.5%.
Each generator was driven by a Lister/Blackstone diesel engine at
750 r.p.m. |
The company also supplied a 35 KVA 415 volt, 3 phase
generator, for the uninterrupted supply for essential services. On
mains failure, a battery automatically provides power for a D.C.
motor, which drives the generator until the main diesel engines and
generators are up and running.
The 35 KVA generator. |
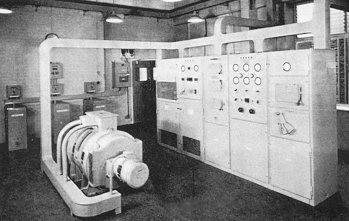 |
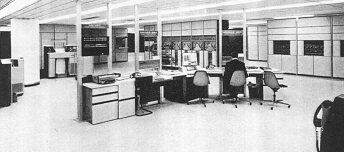 |
In 1965 a Univac 490 computer system was installed at
the British European Airways West London Air Terminal. The E.C.C.
provided the continuity power equipment and associated control gear. |
It consisted of two motor-generator sets, each of
which provided 208 volts, 3-phase, at 60 Hz. Each unit consisted of a
350b.h.p., 400 volt steel yoke D.C. motor which was coupled to a
300 KVA, 240 kW A.C. generator. The output voltage was automatically
controlled to within plus or minus 1% and separate control panels
were provided for each generator. Solenoid operated, air-break
circuit-breakers were included in the output circuitry. |
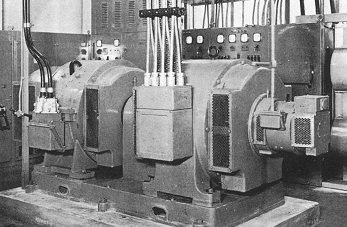
One of the motor-generator sets. |
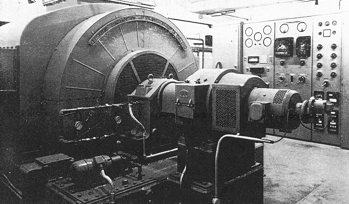
The E.C.C. generator, exciter and
control switchboard. |
English Clays, Lovering, Pochin & Co. Ltd.
commissioned an unmanned, remotely controlled 5 Megawatt
Turbo-Generator, to supplement its existing electricity supply.
The E.C.C. provided the turbo-generator and the associated
control gear. The generating station was located at Bugle in
Cornwall and produced electricity during peak periods and at
times of power failure. |
The generator was powered by a land version of
the Proteus Turbo-prop aero engine that was built by
Bristol-Siddeley. The engine ran on class 'A' diesel fuel and
full electrical power was available within five minutes, after
the engine started. The station produced 11,000 volts and
storage was provided for 24,000 gallons of diesel fuel, which
was enough to run the generator for 80 hours at maximum power. |
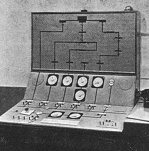
The control desk. |
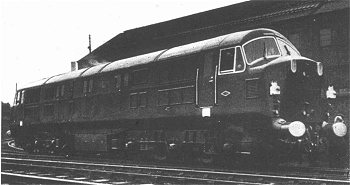
One of the 2,000 hp. diesel hydraulic
locomotives. |
In 1958 the E.C.C. produced a number of
Dynostarters, which were used to start up locomotive
diesel engines. They were used in Type 4, 2,000 hp. diesel
hydraulic locomotives that were built by the North British
Locomotive Company Limited, at Glasgow. The locomotives were
65ft. long and weighed 116 tons. They had a maximum tractive
effort of 50,000 lbs. |
An E.C.C. Dynostarter. |
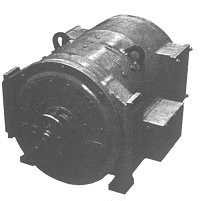 |
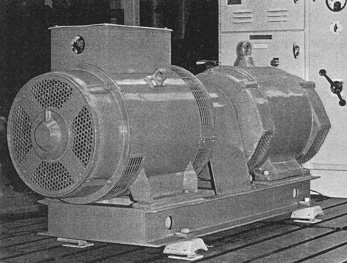 |
In the 1960's the company started to produce
synchronous reluctance motors. These were much smaller and
cheaper to build than traditional A.C. motors. They were simple
to start, requiring no starting gear. Direct on-line starting or
star-delta starting was used.
The photograph shows a C350
reluctance motor driving a BRF 250 brushless generator. |
Comparing one of the new synchronous reluctance
motors, on the left, with the traditional type of A.C. motor on
the right. Both motors deliver the same output power. |
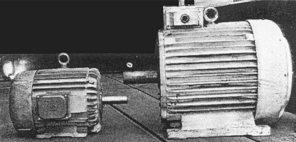 |
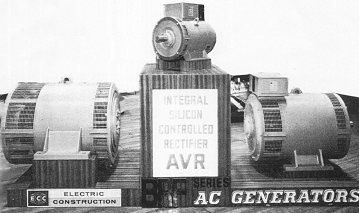 |
E.C.C.'s exhibit at the
1968 Electrical Engineers Exhibition. |
BRF generators were designed for use as standby
power A.C. supplies. They were brushless, A.C. generators with a
built-in static voltage regulator that was designed by the
Static Plant Division. The output voltage was regulated to
within 2.5% of its rating and the generator was only about three
quarters of the size of a traditional unit.
A BRF generator. |
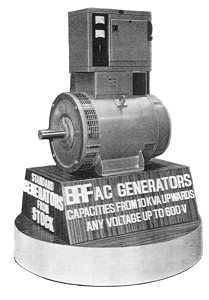 |
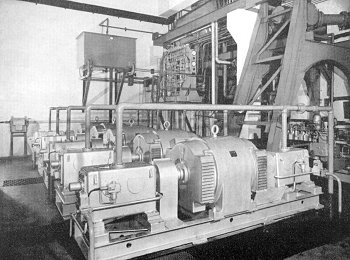 |
Control valves and
pumping equipment that is driven by E.C.C. 1,500 r.p.m. and
3,000 r.p.m. squirrel cage motors.
This is part of an installation at the Hereford forging
works of Henry Wiggin. The equipment was installed early in
1963. |
The following is a list of some of the company's
other products. This demonstrates the wide range of items that
were produced by the company. The E.C.C. had a reputation of
being able to design and manufacture almost any piece of
electrical equipment.
a) |
Remote control by
injecting signals into mains power lines |
b) |
High frequency
alternators up to 100 kW at 10 kHz |
c) |
60,000 volt
precipitator supplies with rotating switch rectifiers |
d) |
400 Hz generators for
radar supplies |
e) |
servo control systems |
f) |
tyre heating machinery
for railway wheels |
g) |
Electronic moisture
control systems for fabric and paper manufacture |
h) |
Lift motors and
control systems providing controlled acceleration |
i) |
High current
rectifiers |
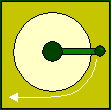
|
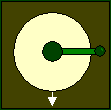
|
|
Return to the
Company's Products |
|
Proceed to Final
Expansion |
|